插床机构综合设计说明书.docx
《插床机构综合设计说明书.docx》由会员分享,可在线阅读,更多相关《插床机构综合设计说明书.docx(29页珍藏版)》请在冰豆网上搜索。
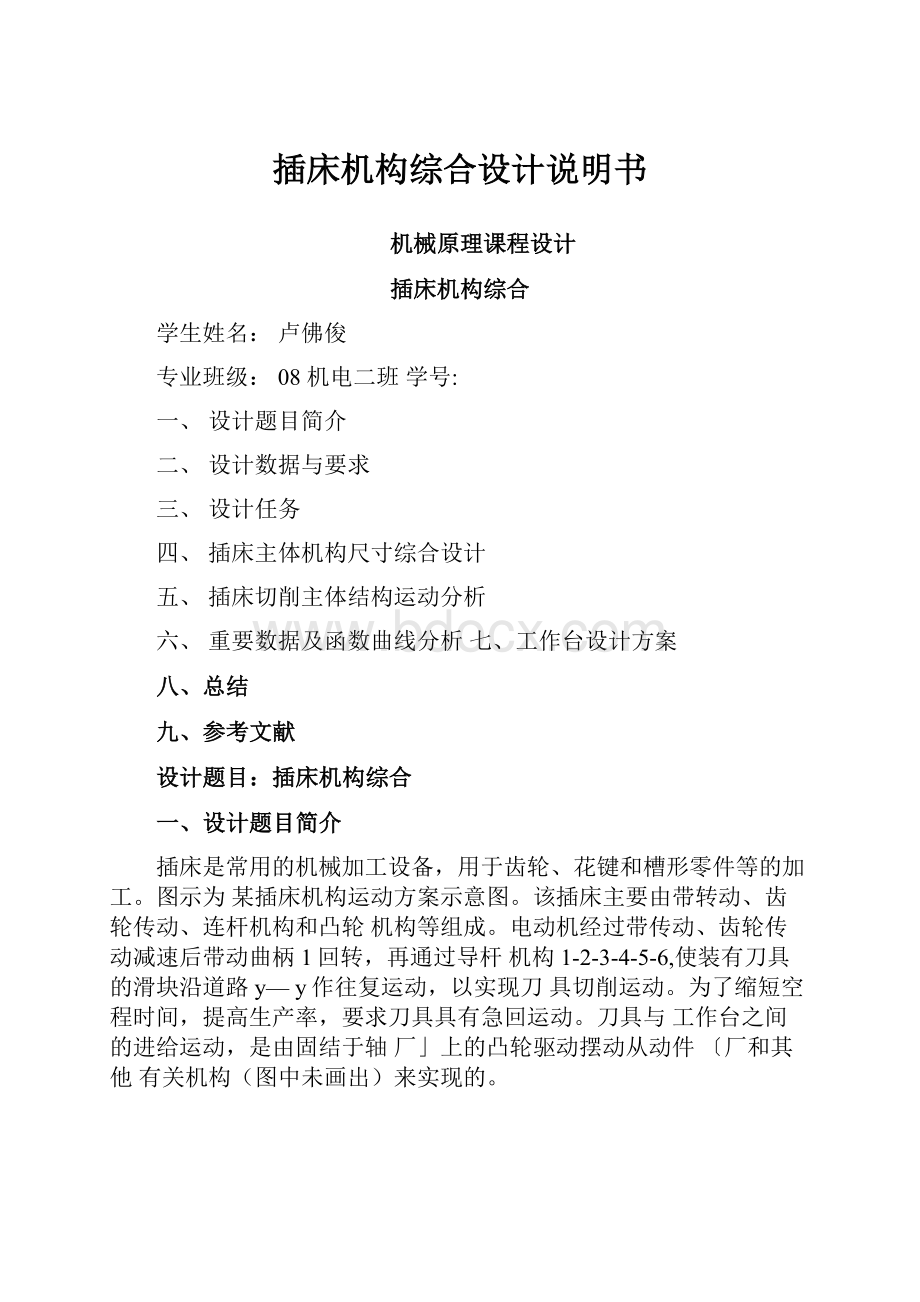
插床机构综合设计说明书
机械原理课程设计
插床机构综合
学生姓名:
卢佛俊
专业班级:
08机电二班学号:
一、设计题目简介
二、设计数据与要求
三、设计任务
四、插床主体机构尺寸综合设计
五、插床切削主体结构运动分析
六、重要数据及函数曲线分析七、工作台设计方案
八、总结
九、参考文献
设计题目:
插床机构综合
一、设计题目简介
插床是常用的机械加工设备,用于齿轮、花键和槽形零件等的加工。
图示为某插床机构运动方案示意图。
该插床主要由带转动、齿轮传动、连杆机构和凸轮机构等组成。
电动机经过带传动、齿轮传动减速后带动曲柄1回转,再通过导杆机构1-2-3-4-5-6,使装有刀具的滑块沿道路y—y作往复运动,以实现刀具切削运动。
为了缩短空程时间,提高生产率,要求刀具具有急回运动。
刀具与工作台之间的进给运动,是由固结于轴厂」上的凸轮驱动摆动从动件〔厂和其他有关机构(图中未画出)来实现的。
插床机构运动方案示意图
针对图所示的插床机构运动方案,进行执行机构的综合与分析。
二、设计数据与要求
依据插床工况条件的限制,预先确定了有关几何尺寸和力学参数,如表6-4所示。
要求所设计的插床结构紧凑,机械效率高。
插床机构设计数据
插刀往复次数占(次/min)
60
插刀往复行程H(mm
100
插削机构行程速比系数疋
2
中心距S金(mm
150
杆长之比41g
1
质心坐标金(mm
50
质心坐标色(mm
50
质心坐标亡(mm
120
凸轮摆杆长度心(mm
120
凸轮摆杆行程角曹(0)
15
推程许用压力角[口](0)
45
推程运动角4(0)
90
回程运动角耳(0)
60
远程休止角戌(0)
15
推程运动规律
3-4-5次多项式
回程运动规律
等速
速度不均匀系数占
最大切削阻力Q(N
1000
阻力力臂川(mm
120
滑块5重力Q(N
320
构件3重力4(n
160
构件3转动惯量’工(kgm2)
三、设计任务
1.针对图所示的插床的执行机构(插削机构和送料机构)方案,依据设计要求和已知参数,确定各构件的运动尺寸,绘制机构运动简图;
2.假设曲柄1等速转动,画出滑块C的位移和速度的变化规律曲
线;
3.在插床工作过程中,插刀所受的阻力变化曲线如图所示,在不考虑各处摩擦、其他构件重力和惯性力的条件下,分析曲柄所需的驱动力矩;
4.取曲柄轴为等效构件,确定应加于曲柄轴上的飞轮转动惯量;
5.用软件(VBMATLABADAM或SOLIDWORKS均可)对执行机构进
行运动仿真,并画出输出机构的位移、速度、和加速度线图。
6.图纸上绘出最终方案的机构运动简图(可以是计算机图)并编写说明书。
四、插床主体机构尺寸综合设计
方案选择:
方案一:
结构简图如下
方案二:
机构简图如下:
经过对方案一和方案二的比较,我们发现方案一的优点是结构简单,易于实现。
方案二的优点是可承受的力要大。
考虑到插床需要较大的进给里用已加工零件,所以我们选择方案二,下面我们就相对于方案二进行进一步的计算和设计。
y
已知OQzilSOmmBC/BO21,行程H=100m,行程比系数K=2,
根据以上信息确定曲柄O1A,BC,BO2长度,以及O2到YY轴的距离
1.OiA长度的确定
图1极限位置
由K(180°)/(1800),得极为夹角:
6O0,
首先做出曲柄的运动轨迹,以Oj为圆心,0小为半径做圆,随着曲柄的转动,有图知道,当O2A转到O2A1,于圆相切于上面时,刀具处于下极限位置;当O2A转到O2A2,与圆相切于下面时,刀具处于上极限位置。
于是可得到O2A1与O2A2得夹角即为极为夹角600。
由几何关系知,A1O1O2A2O1O2,于是可得,
OjAj
cos
?
OiO2
A1O1O2A2O1O2600。
由几何关系可得:
代入数据,O1O2=150mrn600,得
O1A75mm
即曲柄长度为75mm
2.
刀具上极限
AO护月2是等边三角形
刀具下极限
是平行四边形
杆BC、BO2的长度的确定
图2杆BC,BO2长度确定
由图2知道,刀具处于上极限位置C2和下极限位置Ci时,C1C2长度即
为最大行程H=100mm,即有C1C2=100mrm
在确定曲柄长度过程中,我们得到A1O1O2A2O1O2600,那么可得
到B1O2B2600,那么可知道三角形B1B2O2等边三角形。
又有几何关系知道四边形B1B2C2G是平行四边形,那么B2B1C2C1,又
上面讨论知B1B2O2为等边三角形,于是有B1O2B2B1,那么可得到
B2O2100mm,即BO2100mm
又已知BC/B021,
于是可得到
BCB02100mm
即杆BC,B02的100mm
3.O2到丫丫轴的距离的确定
冏I|乃为
图302到丫丫轴的距离
有图我们看到,丫丫轴由y1y1移动到z过程中,同一点的压力角先减小,后又增大,那么在中间某处必有一个最佳位置,使得每个位置的压力角最佳。
考虑两个位置:
1当丫丫轴与圆弧B2B1刚相接触时,即图3中左边的那条点化线,与圆弧B2B1
相切与B1点时,当B点转到B2,B1,将会出现最大压力角
2.当丫丫轴与B2B1重合时,即图中右边的那条点化线时,B点转到B1时将出现最大压力角
为了使每一点的压力角都为最佳,我们可以选取丫丫轴通过CB1中点(C点为O2B1与B2B1得交点)。
又几何关系知道:
IO2B?
cosB2O2C(O2B2O2B?
cosB2O2C)/2
由上面的讨论容易知道B2O2C300,再代入其他数据,得:
I93.3mm
即02到丫丫轴的距离为93.3mm
综上,插床主体设计所要求的尺寸已经设计完成已知O1O2=150mm
BC/BO21,行程H=100mm行程比系数K=2,
根据以上信息确定曲柄o1a,bc,bo2长度,以及02到丫丫轴的距离
图4极限位置
由K(180°)/(1800),得极为夹角:
60°,
首先做出曲柄的运动轨迹,以O,为圆心,O,A为半径做圆,随着曲柄的转动,有图知道,当O2A转到02几,于圆相切于上面时,刀具处于下极限位置;当O2A转到O2A2,与圆相切于下面时,刀具处于上极限位置。
于是可得到O2A与O2A2得夹角即为极为夹角60°。
由几何关系知,AQQ2A2OQ2,于是可得,
O1A1
cos
?
OQ2
A1O1O2A2O1O2600。
由几何关系可得:
代入数据,OCzM^Omm600,得
O1A75mm
即曲柄长度为75mm
2.杆BC、BO2的长度的确定
刀員上极限
△0月屮2是等边三角形
刀具下极限
\f
B1B2c2c1是平行四边形
图5杆BC,BO2长度确定
由图2知道,刀具处于上极限位置C2和下极限位置Ci时,CO长度即为最大行程H=100mm,即有C1C2=100mm
在确定曲柄长度过程中,我们得到A1O1O2A2O1O2600,那么可得
到B1O2B2600,那么可知道三角形B1B2O2等边三角形。
又有几何关系知道四边形B1B2C2C1是平行四边形,那么B2B1C2C1,又上面讨论知B1B2O2为等边三角形,于是有B1O2B2B1,那么可得到B2O2100mm,即BO2100mm
又已知BC/BO21,
于是可得到
BCBO2100mm
即杆BC,BO2的100mm
3.O2到丫丫轴的距离的确定
冏I[升沟
图6O2到丫丫轴的距离
有图我们看到,丫丫轴由y°i移动到丫3丫3过程中,同一点的压力角先减小,后又增大,那么在中间某处必有一个最佳位置,使得每个位置的压力角最佳。
考虑两个位置:
1当丫丫轴与圆弧B2B1刚相接触时,即图3中左边的那条点化线,与圆弧B2B1相切与B1点时,当B点转到B2,Bi,将会出现最大压力角。
2.当丫丫轴与B2B1重合时,即图中右边的那条点化线时,B点转到B1时将出现最大压力角为了使每一点的压力角都为最佳,我们可以选取丫丫轴通过CB1中点(C点为0?
B1与B2B1得交点)。
又几何关系知道:
l02B?
cosB202C(02B202B?
cosB202C)/2由上面的讨论容易知道B202C300,再代入其他数据,得:
l93.3mm
即02到丫丫轴的距离为93.3mm
综上,插床主体设计所要求的尺寸已经设计完成。
五、插床切削主体结构运动分析
用图解法作机构的运动分析和动态静力分析
已知w60r/m,逆时针旋转,由作图法求解位移,速度,加速度。
规定位移,速度,加速度向下为正,插刀处于上极限位置时位移为0.
(1)位移
在1:
的基础上,量的位移为79.5mm,即曲柄转过175°时位移为79.5mm
(2)速度
由已知从图中可知,Va2与O,A垂直,Va3A2与O2A平行,Va3与O2A垂直,由理论力学中不同构件重合点地方法可得
VA3VA3A2VA2
大小?
?
方向
其中,Va2是滑块上与A点重合的点的速度,Va3A2是杆AOB±与A点重合的点相对于滑块的速度,Va3是杆AOBt与A点重合的速度。
又由图知,Vb与O2B垂直,Vcb与BC垂直,Vc与YY轴平行,有理论力学同一构件不同点的方法可得:
大小
vc
?
VB
VCB
?
方向
其中,Vc是C点,即插刀速度,Vbc是C点相对于B点转动速度,Vb是B点速度
又B点是杆件3上的一点,,杆件3围绕02转动,且B点和杆件与A点重合
的点在。
2的两侧,于是可得:
Vb
100
220
由已知可得vA2wO1A2
7547lmm/s,规定选取比例尺
由图量的O2A3220mm,则可到
1]”t
u15mms/mm,则可的矢量图如下:
最后量出代表vC的矢量长度为12mm,
于是,可得vC=0.174m/s
即曲柄转过175°时,插刀的速度为0.174m/s
(3)加速度
k
r
A2
A3A2
A3A2?
由理论力学知识可得矢量方程:
A3
大小?
方向?
A2
OiA44
752957.88mm/s2,方向由A4指向01;
A3A2
是科氏
加速度,A3A22
A2是滑块上与A点重合点的加速度
3vA3A21080mm/s2(其中g,VA3A2大小均
从速度多边形中量得),q方向垂直O2A4向下;;3A2是A4相对于滑块的加速
度,大小位置,方向与O2A4平行;A3A2是C点相对于B点转动的向心加速
度,2302皿3亦993.43mm/s2,方向过由C指向B;;302是C点相对
于B点转动的切向加速度,大小位置,方向垂直BC次矢量方程可解,从而得
到A3。
B时杆AOB上的一点,构AOB围绕02转动,又A4与B点在O2的两侧,由
tR,n2R(是角加速度)可得
O?
B
BO2A3a3
量出O2A4则可得到a的大小和方向
B
又由理论力学,结合图可得到;
nt
cBCBCB
大小?
?
方向
其中,B在上一步中大小方向都能求得;Cb是C相对于B点转动的向心加速度CbvBc/BC36mm/s2,方向由C点指向B点;Cb是C相对于B点转动的切向加速度,大小未知,方向与BC垂直。
次矢量方程可解,从而可得到C点,即插刀的加速度。
取比例尺u36mms2/mm,可得加速度矢量图如下:
最后由直尺量的ac长度为12mn,于是,可得ac0.432m/s2
当355°
(1)位移
在1:
的基础上,滑块的位移为1.5mm,即卩曲柄转过355°时位移为1.5mm
(2)速度
由已知从图中可知,VA2与°1A垂直,Va3A2与O2A平行,VA3与°2A垂直,由理论力学中不同构件重合点地方法可得
VA3VA3A2VA2
大小?
?
方向
其中,Va2是滑块上与A点重合的点的速度,VA3A2是杆AOB±与A点重合的点
相对于滑块的速度,Va3是杆AOBt与A点重合的速度。
又由图知,Vb与O2B垂直,Vcb与BC垂直,Vc与YY轴平行,有理论力学同一构件不同点的方法可得:
VcVbVcb
大小?
?
方向
其中,Vc是C点,即插刀速度,Vbc是C点相对于B点转动速度,Vb是B点速度。
又B点是杆件3上的一点,,杆件3围绕02转动,且B点和杆件与A点重合的点在。
2的两侧,于是可得:
O2B
VBO2XVA3
由图量的O2A5123.5mm,则可到
100
vBVA3
由已知可得VA2w01A2
75471mm/s,规定选取比
123.5
u10ms1/mm,则可的矢量图如下:
最后量出代表vc的矢量长度为2.16mm于是,可得:
vC0.0216m/s
即曲柄转过355°时,插刀的速度为0.0216m/s方向沿YY轴向上。
(3)加速度
由理论力学知识可得矢量方程:
A2
752957.88mm/s2,方向由A5指向01;
忙"是哥氏
A3A2
2
°iA24
小均从速度多边形中量得),方向垂直O2A5向下;A3A2是A相对于滑块的加
O2B5
BO2A5a3
量出O2A5则可得到a的大小和方向
B
又由理论力学,结合图可得到;
nt
cBCBCB
大小?
?
其中,B在上一步中大小方向都能求得;
Cb是C相对于B点转动的向心加速
方向
度CbvBc/B5C51.44mm/s2,方向由C点指向B点;Cb是C相对于B点转
动的切向加速度,大小未知,方向与BC垂直。
次矢量方程可解,从而可得到C点,即插刀的加速度。
取比例尺u50ms2/mm,可得加速度矢量图如下
六、重要数据及函数曲线分析
角度
位移S(mm)
速度
V(m/s)
加速度
a(m/s2)
S,V,a数据表
143
214
25
30
31
41
45
55
57
73
76
83
42
49
56
63
70
77
84
91
98
105
112
119
126
133
140
147
154
161
168
175
180
187
90
92
95
98
99
99
98
97
90
73
66
194
201
208
215
222
229
236
243
250
257
264
271
278
285
292
299
306
313
320
327
334
341
355
36000
1、S()图的分析:
随着曲柄OiA,逆时针转动角度的增大,滑块C位移由0开始增大,大约在240度时达到最大,然后开始减少,易知滑块C进程与回程时,曲柄0!
A,转动的角度并不相等,这说明了曲柄01A,转动时存在急回运动。
2、V()图的分析
随着曲柄OiA,逆时针转动角度的增大,即的增加,速度V正向增大,大约在120度时达到最大,然后呈现下降趋势,在240度时下降为0,表明位移以增大到最大,即滑块C达到最下端,由曲线看出,滑块C的正向平均速度比负向平均速度小,进一步表明了急回运动的存在。
进程时,速度比较小,更有利于进刀;回程时,速度较快,有利于提高工作效率,充分证明了此机构设计的合理性。
下面对特殊点作一下分析:
转角为0度时,V=0;曲柄转动至120度,正向速度到达最大值0.22m/s,此时滑块C具有最大速度,当曲柄继续转动至240度时正向速度减少至0,此时由速度是位移的变化率可知,其位移达到最大值。
当曲柄继续转动时,滑块C速度反向,变为负向速度,随着转角增大而增大,曲柄转至240度,速度达到负向最大值0.63m/s之后,当滑块继续由摇杆带动时,却曲柄由300度转至360度时,其速度由负向最大值变为0.
3、a()图的分析:
随着曲柄OiA,逆时针转动角度的增大,滑块C先向下作加速运动,但加速度越来越小,但是加速度越来越小,然后反向增大知道位移达到最大,接着滑块进入空回程,由于存在急回运动,加速度迅速正向增大,达到最大后又开始减小,直到滑块C进入工作行程。
下面对一些特殊点进行分析:
进程时,滑块C具有正向加速度,由开始减少,在102度时达到0,当角度继续增大时,加速度反向增大,大约在240度时滑块位移达到最大值,但是加速度还是在反向增大,而且增长率明显比前段更大,当角度达到270度时加速度增大到5.2m/s2时到达峰值,开始减少,在300度左右是达到0,然后正向增长,表明了滑块将要向上减速运动,最后回到0位移,然
后往复运动。
我们可以看出,在0至240度区间内,加速度都很平缓,而在240至360度内,加速度变化很快,都说明了急回运动的存在。
七、工作台设计方案
方案的选择:
方案一:
凸轮连杆机构(题目中给的方案)
方案讨论:
①运动怎样从电动机引下来;
2工作台的运动情况及相对位置;
3怎样确定凸轮的安装角,怎样让整个机构协调工作
第一个问题:
由于插床机身高度较高,所选择的机构传动方案必须能够实现长距离传动,且保证定传动比,长距离传动方案多种多样,如:
齿轮系传动;带传动;链传动;平行四边形机构传动等。
齿轮系传动会使整个机器结构变得复杂;带传动本身具有个缺点:
会产生弹性滑动,且其精度不高;链传动则会产生冲击,并伴随着很大的噪声;平行四边形机构传动效率高,结构简单,完全复制了原动件的运动,且其刚度较高,故选取平行四边形机构这个方案来进行长距离传动。
第二个问题:
工作台最终可实现前后、左右作间歇直线送进运动和作间歇回转送进运动。
送进运动必须与主切削运动协调配合,即进给运动必须在刀具非切削期时间即上超阶段以内完成,以防止刀具的切削运动与工作台的送进运动发生干涉。
要实现工作台的三个间歇运动,即将原动件的连续往复摆动转化为从动件的单向间歇运动,根据机构的这个运动特性,知可选取棘轮机构,实现预期运动。
同时,机构中添加复合锥齿轮,可实现改变锥齿轮的旋转方向,从而改变工作台的运动方向;同时加上离合器机构,以实现动力的传递或断开。
这样,当机械运动传递到棘轮时,棘轮作有规律的单向间歇运动,同时将摆动转化为沿轴的自转运动,再通过复合锥齿轮传递给工作台。
除了靠各机械构件带动工作台运动外,还可用手柄操作,此时与棘轮连接的离合器处于断开状态,棘轮的运动及动力不继续传递,不影响手柄对工作台的操纵。
要保证送进运动与主切削运动协调配合,即进入上超工作台开始运动,结束上超工作台停止运动,直到下一个上超阶段才重新运动,则必须保证推程运动角小于等于上超区间的角度。
第三个问题:
由于工作台的进给运动只能发生在上超阶段,故我们所选择的机构传动方案中机构的运动只有在上超阶段才能传递给工作台,其它时间工作台
都是处于静止状态,故选择凸轮式间歇运动机构,同时为了保证机构协调工作,凸轮的安装角必须在上超区间的角度范围内。
方案简图
方案二:
不完全齿轮间歇旋转机构
该机构中不完全齿轮的旋转运动由连杆机构和锥轮从主动齿轮引导下来,然后由
不完全齿轮推动工作台运动,设计的不完全齿轮的主动轮旋转一周时从动轮旋转1/10周。
HJwi
■■■■■
万案简图
方案比较:
比较两个方案,可以发现方案一比方案二要多设计凸轮,由于凸轮设
计比较麻烦且精度不高,所以我们选择方案二,下面就方案二做进一步计算:
齿轮传动计算:
取Zi22,Z25Zi225110。
按照要求取m8,压力角200则
d1z1m=228=176mm
d2z2m1108880mm
中心距采用标准中心距则am(Z1Z2)/2=8(22+110)2=528mm
不完全齿轮的计算:
设计的不完全齿轮的主动轮旋转一周时从动轮旋转1/10周。
齿轮部分取参数为z=120,m=8法面压力角取20°
则中心距azm1208960
分度圆直径dmz8120960
基圆直径dbdcos8120902.11
齿顶圆直径dad2ham960218976
齿根圆直径dfd2h「c*m960210.258940
凸轮止弧和凹轮止弧则按照基圆的圆弧来配合
八、总结
这次设计课程不仅让我加深了对机械原理理论课程的理解和认识,更培养了我用理论知识去解决实际问题的能力。
作为初次接触设计的我,对未来的设计充满了信心。
当我们遇到一个问题时,首先不能畏惧,而是要对自己有信心,相信通过自己的努力一定能解决的。
就象人们常说的在战略上藐视它。
但是在战术上的重视它。
通过慎重的考虑认真的分析,脚踏实地去完成它,克服重重困难,当你成功实现目标时,那种成就感一定会成为你成长的动力。
还有就是经过这次的课程设计,我在绘图方面和三维仿真方面的知识也得到进一步的加强,让我受益匪浅。
九、参考文献
冯鉴、何俊、雷志翔.机械原理.西南交大出版社
裘建新.机械原理课程设计指导书.北京:
高等教育出版社