通用机械零部件检验规范.docx
《通用机械零部件检验规范.docx》由会员分享,可在线阅读,更多相关《通用机械零部件检验规范.docx(21页珍藏版)》请在冰豆网上搜索。
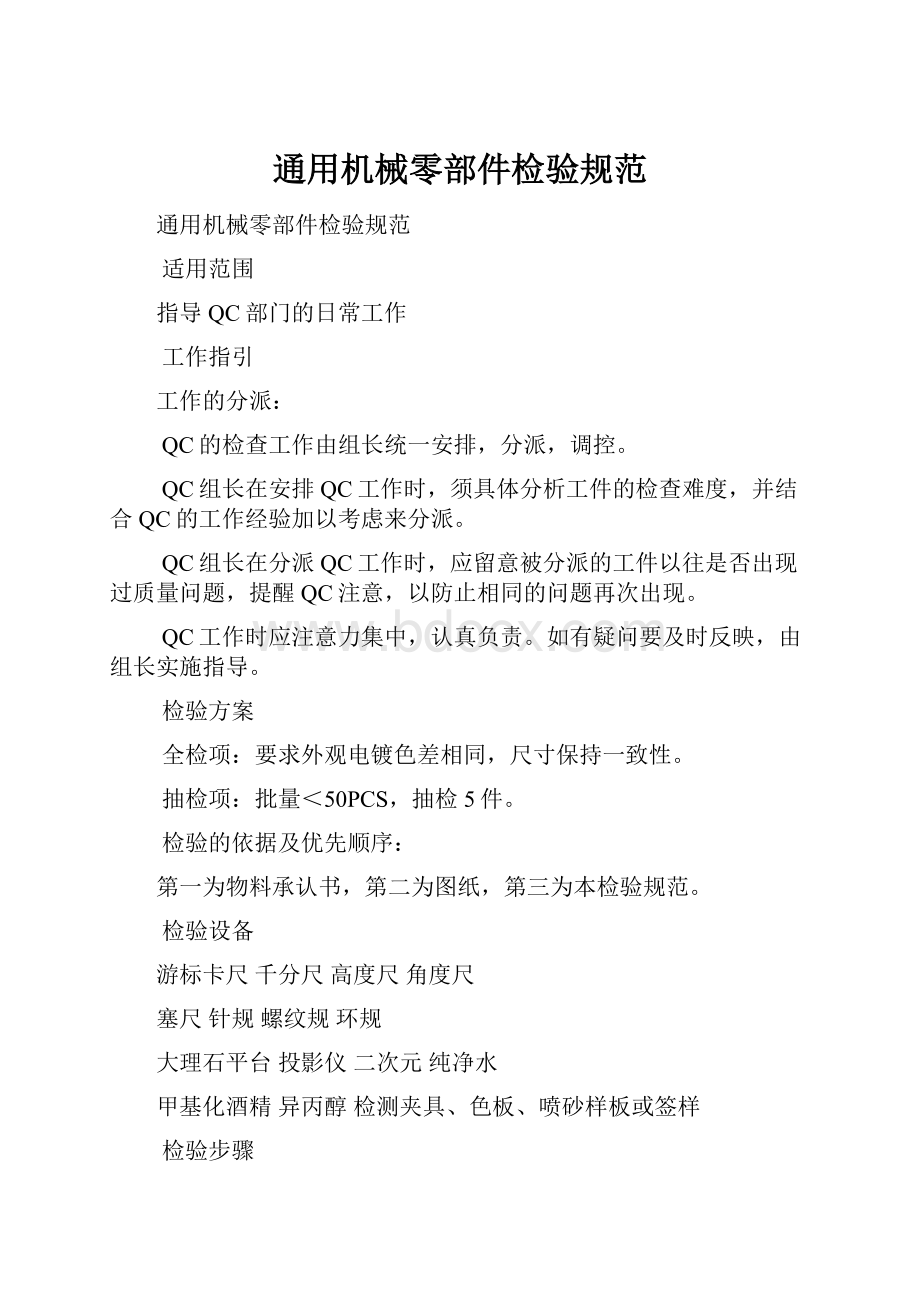
通用机械零部件检验规范
通用机械零部件检验规范
适用范围
指导QC部门的日常工作
工作指引
工作的分派:
QC的检查工作由组长统一安排,分派,调控。
QC组长在安排QC工作时,须具体分析工件的检查难度,并结合QC的工作经验加以考虑来分派。
QC组长在分派QC工作时,应留意被分派的工件以往是否出现过质量问题,提醒QC注意,以防止相同的问题再次出现。
QC工作时应注意力集中,认真负责。
如有疑问要及时反映,由组长实施指导。
检验方案
全检项:
要求外观电镀色差相同,尺寸保持一致性。
抽检项:
批量<50PCS,抽检5件。
检验的依据及优先顺序:
第一为物料承认书,第二为图纸,第三为本检验规范。
检验设备
游标卡尺千分尺高度尺角度尺
塞尺针规螺纹规环规
大理石平台投影仪二次元纯净水
甲基化酒精异丙醇检测夹具、色板、喷砂样板或签样
检验步骤
1)对照图纸要求之版本,是否与实物一致。
2)清点图纸要求之数量,是否与实际相符
3)识别图纸要求之材料,是否与实物相符。
4)审查技术说明。
留意:
是否有对称件。
不同类型的热处理、光洁度等对加工的要求。
英文/日文的注解说明。
5)审核图纸的尺寸、形位公差、外观要求、光洁度等,决定检查方法,合理选用量具,保证检测质量。
6)QC按次序对工件进行检验,检完一个尺寸,作一个记号,不能漏检。
7)检出不良品,由组长或厂部确认是否返修,报废。
8)检验完毕签署检验记录,工件按要求进行清洗,清点包装,粘贴标识。
9)入库/出货。
注意事项
1)审图时注意图纸是否模糊不清、是否漏盖工艺章。
2)图纸数量理论上只许多不能少。
3)审核所有材料,避免错料,混料。
4)检查是否有漏加工之处。
5)图纸要求热处理,氧化的,关注是否除锈,留量,堵孔,氧化淬火前的攻牙加工等。
6)留意零件与图纸其它不符之处,比如方向相反等。
常用材料;
铝:
AL6061、LY12、A5052、7075、2014
黄铜:
C3604、C2801P、PTFE、H62青铜:
C5241,BC6
不锈钢:
SUS303、SUS304、SUS301、SUS302可热处理不锈钢:
SUS440C
白赛钢:
白POM、Dtrlin黑赛钢:
黑POM铁弗龙:
PT铁(热轧板):
SPHC铁(冷轧板):
SPCC
铬钢:
SKD、NAK55、NAK8045#钢:
SS400、SGD400-D
外观检视
1)外观检视条件
——视力:
校正视力以上
——目视距离:
检查物距眼睛A级面40㎝,B、C距眼睛一臂远。
——目视角度:
45度~90度(检查时产品应转动)
——目视时间:
A级面15秒/面,B、C面10秒/面
——灯光:
大于500LUX的照明度
2)术语和定义
A级表面:
在使用过程中总能被客户看见的部分(如:
面壳的正面和顶面,后壳的顶面,手柄,透镜,按键及键盘正面,探头整个表面等)。
B级表面:
在使用过程中常常被客户看见的部分(如:
面壳的左右侧面,底壳或后壳的左右侧面及背面等)。
这些表面允许有轻微不良,但是不致引起挑剔客户不购买产品。
C级表面:
在使用过程中很少被客户注意到的表面部分(如:
面壳的底面,底壳或后壳的底面,内部零件表面)。
此表面的外观缺陷应合理而且不至于给客户觉得该产品质量不佳。
D级表面:
在使用过程中几乎不被客户看到部分(如:
产品的内部件表面)。
此表面的缺陷合理,不能影响零件使用性能。
金属表面:
包括电镀、氧化、钝化等表现为金属质感的表面,非喷涂表面。
拉丝:
是一种砂带磨削加工,通过砂带对金属表面进行磨削加工,去除表面缺陷,并形成具有一定粗糙度、纹路均匀的装饰表面。
基材花斑:
电镀或氧化前因基体材料腐蚀、材料中的杂质、材料微孔等原因所造成的、与周围材质表面不同光泽或粗糙度的斑块状花纹外观。
抛光区:
对基材上的腐蚀、划伤、焊接区、铆接区等部位进行机械打磨抛光后表现出的局部高光泽、光亮区域。
镀前划痕:
指材料划痕、电镀或氧化之前因操作不当,或对明显缺陷进行粗打磨等人为造成的基体材料上的划伤或局部磨擦痕迹,一般呈细线型。
浅划痕:
膜层表面划伤,但未伤及底层(即底层未暴露);对其它无膜层表面则为:
目测不明显、手指甲触摸无凹凸感、未伤及材料本体的伤痕。
深划痕:
膜层表面划伤,且已伤至底层(即底层已暴露出来);对其它无膜层表面则为:
目测明显、手指甲触摸有凹凸感、伤及材料本体的伤痕。
凹坑:
由于基体材料缺陷,或加工过程中操作不当等原因而在材料表面留下的小坑状痕迹。
凹凸痕:
因基材受撞击或校形不良等而呈现出的明显变形、凹凸不平的现象,手摸时有不平感觉。
烧伤:
拉丝处理时因操作不当造成零件表面过热留下的烧蚀痕迹。
水印:
电镀或氧化后因清洗水未及时干燥或干燥不彻底所形成的斑纹印迹。
露白:
镀锌彩色钝化膜因磨擦而去除,露出新层,或因缝隙截留溶液导致的无钝化膜现象,呈现为区别于周围彩色的白色。
雾状:
镀铬、镀镍表面上的模糊、不清晰、不光亮的现象。
颗粒:
因材料夹杂物或外来物(如焊渣)的影响而在表面形成的,颜色与正常表面一致的凸起现象。
挂具印:
指电镀、氧化、喷涂等表面处理生产过程中,因装挂用辅助工具的遮挡而使其与零件相接触的部位产生局部无膜层的现象。
图文损伤:
印刷图文因局部脱落或擦伤、附着不良、污染等所造成的图形、字迹不完整不清晰的现象。
气孔:
焊接时熔池中的气泡在焊液凝固时未能逸出而残留下来形成的空穴。
夹渣:
焊后残留在焊缝中的焊渣。
焊瘤:
焊接过程中,熔化金属流淌焊缝外未熔化的母材上形成的金属瘤。
3)外观检验方法
使用材料应符合有效版本图纸的要求,材料本身应无变形、划伤、氧化变色
表面光滑、平整、无毛刺、变形、锈蚀、裂纹、压折、夹渣、气孔等;预埋件、铆件应牢靠、无松动,螺纹无缺损、无腐蚀等;不允许有加工遗留物;
零件的喷塑、喷漆层应均匀、连续,无缩孔、起泡、开裂、剥落、粉化、流挂、露底(局部无涂层或涂料覆盖不严)、指印等缺陷;
热处理方法应符合有效版本图纸要求,热处理后不应有过烧、氧化、脱碳、热裂、变形、斑点、翘曲、及表面晶粒不均不良现象;
表面处理方法应符合有效版本图纸要求,处理后表面光滑平整、无斑点、烧焦、起泡、水纹、镀层脱落、镀层不全以及电镀酸性渗渣物等
表面处理后,零件表面允许有不可避免的轻微夹具印痕和轻微的水印;在不影响装配的情况下,边、棱角处允许有轻微的粗糙;非重要表面允许有轻微的水纹或个别的斑点;
去毛刺要求:
用手沿零件加工边角的任何位置及方向触摸均无刮卡现象。
对工件的非喷漆表面可允许下列缺陷:
外观缺陷类型
缺陷所处表面类型
允许范围
A级表面
B级表面
C级表面
基材花班
金属表面
不允许
不允许
S总≤被测面积的5%
浅划痕
所有表面
不允许
L≤50×,P≤2
P≤5
深划痕
所有表面
不允许
不允许
不允许
凹坑
非拉丝和喷砂面
不允许
直径≤,P≤2
不限制
凹凸
所有表面
不允许
不允许
直径≤,P≤5
抛光区
金属表面
不允许
不允许
S总≤被测面积的5%
烧伤
拉丝面
不允许
不允许
不限制
水印
电镀、氧化
不允许
S≤,P≤1
不限制
露白
镀彩锌
不允许
不允许
S≤,P≤3
修补
喷塑、电泳漆
不允许
S≤,P≤2
S总≤被测面积的5%
颗粒
所有表面
不允许
直径≤,P≤2
直径≤,P≤5
挂具印
所有表面
不允许
不允许
不限制
图文损伤
印刷图文
不允许
不允许
不允许
色点
所有表面
S≤,P≤2
L≤50
S≤,P≤3
L≤50
S总≤被测面积的2%
露底
电镀
不允许
不允许
不允许
注
S为单个缺陷面积(mm2),P为缺陷数量(个),L为缺陷长度或间距(mm)
尺寸检验
1.标注公差尺寸检验方法及标准:
用游标卡尺,高度尺,角度尺,百分表,平台,投影仪,高度测量仪或检测夹具等进行检验:
标准:
实测尺寸偏差应符合图纸公差要求。
2.未标注公差尺寸检验方法及标准:
用游标卡尺,高度尺,角度尺,百分表,平台,投影仪,高度测量仪或检测夹具等进行检验:
标准:
实测尺寸偏差应符合以下公差要求。
3.螺纹检验方法及标准:
使用符合6g(外螺纹)或6H(内螺纹)公差要求的螺纹规。
标准:
符合通止规要求。
线性尺寸要求
1)线性尺寸的极限偏差数值(外尺寸按负差;槽、孔按正差)单位mmGB/T1804-92
尺寸范围
~3
﹥3~6
﹥6~30
﹥30~120
﹥120~400
﹥400~1000
﹥1000~2000
﹥2000~4000
公差
±
±
±
±
±
±
±
±2
2)未注公差角度的极限偏差长度单位:
mmGB11335-89
长度
0~10
10~50
50~120
120~400
﹥400
公差
±1°
±30′
±20′
±10′
±5′
3)直线度和平面度的未注公差儿单位:
mmGB1184-96
长度
≦10
﹥10~30
﹥30~100
﹥100~300
﹥300~1000
﹥1000~3000
公差
4)垂直度未注公差值单位:
mmGB/T1184-96
长度
≦100
﹥100~300
﹥300~1000
﹥1000~3000
公差
0.2
0.2
0.4
0.5
5)对称度未注公差值单位:
mmGB/T1184-96
长度
≦100
﹥100~300
﹥300~1000
﹥1000~3000
公差
0.5
铝件、钢件表面处理后的尺寸变化:
序号
表面处理
面单边增厚范围
孔单边小范围
1
铝发白
~
~
2
铝发黑
~
~
3
镀镍
一般要根据客户要求,可以控制~
大于φ10的~,小于φ10的忽略不计
4
镀铬
~
大于φ10的~,小于φ10的忽略不计
5
镀锌
~
~
6
铝硬白
~
~
常用形位公差项目及符号:
分类
项目
符号
说明
形状公差
直线度
直线度是用来限制母线、棱线、轴线及平面上某一直线加工后的形状误差。
平面度
平面度是用来限制零件上一平面,加工后不平程度的形状误差。
圆度
圆度是用来限制回转表面上某一垂轴截面的圆形误差。
圆柱度
圆柱度是用来限制所给整个圆柱表面,加工后的实际形状对理想形状的偏离。
线轮廓度
线轮廓用来限制零件上任一曲或曲面任一正截曲线,加工后的实际形状对其理想形状的变动量。
面轮廓度
面轮廓度是用来限制零件上任一曲面,加工后的实际形状误差。
位置公差
定向
平行度
平行度用来限制零件上一直线或平面对基准直线或平面,加工后所产生的不垂直程度的误差。
垂直度
垂直度用来限制零件上一直线或平面对基准直线或平面,加工后所产生的不垂直程度的误差。
倾斜度
倾斜度用来限制零件上一斜面或斜直线,对基准平面倾斜角度的误差。
定位
同轴度
同轴度用来限制共轴表面中被测表面轴线对基准轴线歪斜程度。
对称度
对称度用来限制加工表面的对称平面对基准平面或轴线歪斜的程度。
位置度
位置度用来限制零件加工后的一些实际点、线、面、对其理想位置的最大偏离量。
跳动
圆跳动
圆跳动用来限制零件上圆柱面、圆锥(任意回转曲面)及端面上,某一横截面(或直径位置上)上,回转一周测得对基准轴线(或平面)的最大偏离量。
全跳动
全跳动用来限制零件上回转面或端面,整个表面对基准轴线(或平面)的最大偏离量。
形位公差代号标注示例及其文字说明:
项目
示例
图解
说明
直线度
圆柱表面上任一素线必须位于轴向平面内,距离为公差的两平行直线之间。
Φ30圆柱体的轴线必须位于直径为公差值的圆柱面内。
整个零件的轴线必须位于直径为公差值的圆柱面内。
平面度
上表面必须位于距离为公差值的两平行平面内。
圆度
在垂直于轴线的任一正截面上,该圆必须位于半径差为公差值的两同心之间。
圆柱度
圆柱面必须位于半径差为公差值的两同轴圆柱面之间。
线轮廓度
实际曲线必须位于包络以理想曲线为中心的一系列直径为圆的两包络线之间。
面轮廓度
实际曲面线必须位于包络以理想曲面线为中心的一系列直径为圆的两包络之间。
平行度
实际平面必须位于距离为公差值,且平行垂直于基准平面的两平行平面之间。
垂直度
左侧端面必须位于距离为公差值,且垂直于基准轴线的两平行平面之间。
Φ30的轴线必须位于直径的公差值,且垂直于基准平面A的圆柱面内。
倾斜度
实际斜面必须位于距离公差值为㎜,且与基准面A呈45度的两个平行平面之间。
同轴度
Φ20的轴线必须位于直径为公差值,且与Φ30基准轴线同轴的圆柱面内。
对称度
键槽的实际中心平面必须位于距离公差为㎜的两个平行平面之间。
该两平面对称的位于通过基准轴线A的辅助中心平面两侧。
位置度
三个Φ10的孔实际轴线必须位于直径㎜且以30理想位置为轴线的诸圆柱面内。
圆跳动
Φ50圆柱面绕Φ30基准轴线作无轴向移动回转进,在任一测量平面内的径向跳动量均不得大于公差值
当零件绕Φ20基准轴线作无轴向移动回转时,在左端面上任一测量直径处的轴向跳动量均不得大于公差值
圆锥表面绕基准轴线作无轴向移动回转时,在任一测量圆锥面上的跳动量均不得大于公差值
全跳动
Φ35表面绕Φ20基准轴线作无轴向移动地连续回转,同时,指示器作平行于基准轴线的直线移动;在Φ35表面上任一点跳动量不得大于公差值
端面绕Φ20基准轴线作无轴向移动地连续回转,同时,指示器作垂直于基准轴线的直线移动;在端面上任意一点的轴向跳动量不得大于
形位公差测量
1.平面度的简单测量:
①把工件被测面放在平板上用目测法观察工件与平板之间缝隙的大小进行测量;
②把工件被测面放在平板上用厚薄规(塞尺)进行测量;
③用三个千斤顶(可调支撑顶尖)把被测面朝上支撑好,用高度尺装上杠杆百分表(千分表)校正好三个基准点后进行测量。
2.平行度的简单测量:
把工件基准面朝下放在平板上,用百分表(千分表)对到被测面并使指针偏摆过半圈左右,紧贴平板轻轻推动工件,从百分表(千分表)上读出指针变动量;
把工件基准面朝下放在平板上,用高度尺装上杠杆百分表(千分表)对到被测面并使指针偏摆过半圈左右,紧贴平板轻轻推动高度尺,从杠杆百分表(千分表)上读出指针变动量。
3.跳动或同轴度的简单测量:
把轴类零件相同尺寸的部位(基准圆)放在一个或两个V型槽内,与带百分表或千分表的高度规一起放在平板上,把表头对准被测部位,慢慢转动零件,读出表上的指针变动量就可得到圆跳动或同轴度。
4.对称度的简单测量
轴上的键槽的对称度,一般是放在平台上,使用V型铁和百分表(带座),先测一边的槽面,固定表头,然后旋转180度再测另外的一边,差值既是.
5.垂直度的简单测量
把工件基准面朝下压住紧贴在平板上,用高度计的百分表(千分表)对到被测垂面并使指针偏摆过半圈左右,摇动高度计上手柄,使百分表头在工件被测垂面上下移动,从百分表(千分表)上读出指针变动量;
6.螺纹位置度的简单测量
螺纹孔相对于外径的位置度。
因为是螺纹孔,所以很难测量,可在螺纹加工前--即测量加工光孔的位置度
除此外,各形位公差测量可利用投影仪,高度仪,检测工装等进行准确测量。
附:
质检人员检验误差的特点及防止措施
一、检验误差的概念
1.真值(Y):
被测量(可以是几何量,也可以是其他物理量)的真实值。
2.检验误差:
被测量的测得值与被测量真值之差。
即定义为△Y=y-Y
△Y为检验误差:
y为检验测得值
*任何检验都不能检验出真值,因为检验误差不可避免。
*几何量的测量准确度常用绝对误差表示,电子量用相对误差。
3.产生检验误差的因素
(l)测量器具的固有误差
(2)测量标准带来的误差于
(3)被测对象本身造成的误差
(4)环境因素影响的误差
(5)测量方法引入的误差
(6)操作者的人为过失误差
二、检验人员产生检验误差的特点以及防止措施
检验人员的检验误差主要是错检和漏检。
其产生的种类有:
1.技术性误差 2.粗心大意误差 3.程序性误差 4.明知故犯误差
技术性误差
首先检验人员的技术性误差可用四种方法来发现
1.复核检验:
由技术水平较高的检验员来复检其他检验人员已检过的合格品。
2.循环检验:
对同一件产品先后有几个检验员各自进行检验,看谁发现的缺陷多。
3.重复检验:
由检验人员对本人已检过的产品再检验一次,(不告诉他先前检验的结果)、二次检验结果是否一致。
4.建立标准样品:
把标准样品排列在被检的产品一起作比较。
(-)什么叫做技术性误差
所谓技术性误差,是指检验人员缺乏判断产品合格与否的能力、技能和技术知识而造成的误差。
(二)技术性误差的特点是:
1.非有意的。
2.一贯性、不可避免的。
这是由于检验人员缺乏技术能力造成的,如检验技术不熟练;不会正确使用量、器具;或看不懂图纸;或没有工作经验和技巧(通常所称的诀窍)。
3.特殊性。
检验人员有生理缺陷,如色盲、视力过低等。
(三)防止技术性误差的措施。
技术性误差是可以防止的,其主要措施有:
1.进行技术培训。
内容可包括基本知识和操作技能的方面,同时应注意让他们了解和掌握与新的标准相适应的新的检测技术,实现知识与技能的不断更新。
2.总结、推广误差较少的检验人员的经验和技巧,对所出现的错检,漏检及时分析原因,吸取教训,引以为戒。
3.对有生理缺陷等不宜做检验工作的人,应另行分配做其他适当工作。
4.对检验人员、竞争上岗。
进行应知、应会考核,以及错、漏检率的考核,或持证上岗。
粗心大意误差
(一)什么叫做粗心大意误差
所谓粗心大意误差,顾名思义是一种由于检验人员粗心大意而造成的差错。
(二)粗心大意造成误差的特点是:
1.非有意的。
检验人员不希望产生误差。
2.不知不觉的。
检验人员往往没有意识到自己,正在或已经造成误差。
3.不可预测的。
误差的类型、时间、人员、原因都表现出随机性。
(三)防止粗心大意误差的措施
1.进行工作调整。
特别是对于需要保持注意力高度集中的复杂检验项目,检验人员工作时间一长,因疲劳容易发生误差。
因此,要定时休息或者轮换去检验较简单的工作等。
2.采用先进的自动化检测仪器,以弥补检验人员感觉器官、鉴别能力的缺陷,提高鉴别能力。
3.建立标准样品。
采用比较法。
即提供一个实物标准品,作为判断产品质量的依据。
如:
有的厂把国内外的先进产品或零部件作样品,进行对比检验,都可以大大提高质量检验的准确性。
4.简化检验操作,如在判断尺寸大小或位置时,可提供样板、卡板或塞规等。
5.产品的重新设计。
有些情况下,产品设计会使检验工作难于开展或对检验人员增加了不必要的负担,在这种情况下,产品的重新设计将有助于减少检验人员的误差以及操作工的误差。
总之,防止粗心大意误差的原则是使检验人员能够较好地保持自己的注意力,减少质量检验对人注意力的依赖程度。
程序性误差
除了由于粗心大意而未能检出缺陷以外,还有一种叫做程序性误差。
这是由于程序或管理制度不健全造成的。
如,运送出未经检验的产品;或者甚至送出被剔除的产品;不合格的半成品流入下道工序;不同批号、不同规格甚至不同品种的产品混装出厂等等,对这样的差错,只要通过严格管理,建立健全工作程序使之减少到最低限度。
其措施有:
1.检验人员对检验过的产品必须按规定做好标记、采取分区堆放。
各工序的搬运人员应会识别标记,按规定线路搬运,不搬运无标记的制品。
2.制造部门在更换品种(或不同规格)时,应做好场地清理工作,检验人员对清场工作同样要进行检查验收,经确认合格后,转入另一种规格或品种的生产。
明知故犯误差
明知故犯的误差是检验人员在各种各样的压力之下,放弃原则而造成的误差。
其原因是错综复杂的,可能是由管理部门引起的,也可能由检验人员本身引起的,或者是多方原因引起的。
(一)管理上引起的误差
以下几种形式,都是导致检验人员明知故犯误差的原因。
1.不坚持原则。
检验人员屈服于生产部门或操作人员重产量、赶进度(赶工期)、轻质量,对检出的不合格品请求放行的压力;或为了切身利益,不汇报、不干涉、甚至回避此事。
2.对检验人员反映的正确意见和要求,管理部门因某些原因,不理不睬,不支持。
与检验人员反映质量标准或工位器具不合理,测试设备不健全等问题得不到明确答复时,检验人员限于条件、无奈了事。
3.领导的欺骗行为。
某经理、厂长为了达到某种目的而需在质量上作假时,有的检验人员为了迎合、讨好领导自愿参与,也有的怕不参与将遭打击报复,从而被动参与了弄虚作假行为。
(二)检验人员本身引起的误差
1.工作马虎,不负责任。
有的检验人员利用由于领导不重视检验工作,因此工作时漫不经心,产品是否合格,心中根本无数,检验制品只是过个手,盖了检验合格章放行了事。
2.对质量认识不足,私自放宽检验标准。
对小毛病认为超差一点不会出现大问题;或者是上一次超差比这次还多,有关领导照样同意处理,而且用户也没退货,甚至为此讨好领导等。
3.讲义气,和为贵,不轻易得罪人。
与同事相处多年了,低头不见抬头见,和和气气关系好,犯不着得罪人;或者同事说上几句好听的,因而这次破例,下不为例,也就过关。
4.偷工作弊。
私自减少抽检数量;一次检验不合格,因怕费事,不作再次抽检或全数检验,对脏、累的检验工作马虎从事,造成检验数据不可靠。
(三)防止明知故犯误差的措施
1.加强“质量第一”思想教育和职业道德教育,以增强检验人员的质量意识。
2.企业领导以身作则。
从管理上消除引起明知故犯误差的弊端。
3.明确检验人员责任。
明确每个检验人员的工号,并在检验过的制品上或检验记录上打印、签字,以示负责,保证质量的可跟踪性。
4.采用复核检验的方法,定期进行质量检验审核,查出欺骗行为时要给予严肃处理。
对敢于坚持原则,如实反映质量情况的检验人员则应给予表彰和奖励。
5.选用经证明是作风正派,能坚持原则的人员从事检验工作,对弄虚作假的检验人员应调离岗位。
以上所述,在检验过程中作为人的因素,检验人员造成了大部分的检验误差。
不言而喻,要想真正做好检验工作,把总的检验误差减至最小,必须要在防止检验人员的检验误差的同时,尤其要重视造成检验误差的这些原因,才能取得更好的效果。