离合齿轮的工艺规程与专用夹具设计教材.docx
《离合齿轮的工艺规程与专用夹具设计教材.docx》由会员分享,可在线阅读,更多相关《离合齿轮的工艺规程与专用夹具设计教材.docx(15页珍藏版)》请在冰豆网上搜索。
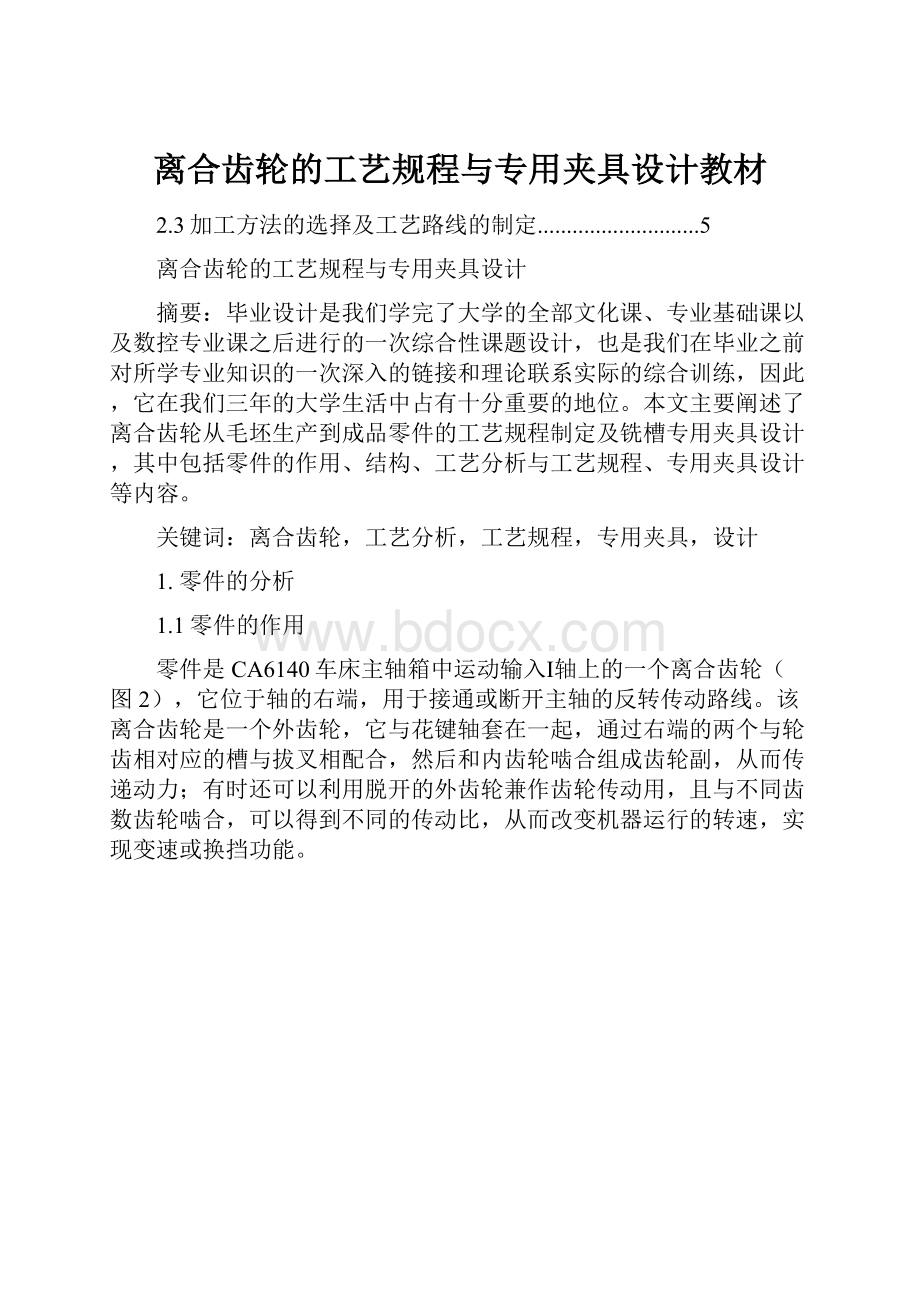
离合齿轮的工艺规程与专用夹具设计教材
2.3加工方法的选择及工艺路线的制定............................5
离合齿轮的工艺规程与专用夹具设计
摘要:
毕业设计是我们学完了大学的全部文化课、专业基础课以及数控专业课之后进行的一次综合性课题设计,也是我们在毕业之前对所学专业知识的一次深入的链接和理论联系实际的综合训练,因此,它在我们三年的大学生活中占有十分重要的地位。
本文主要阐述了离合齿轮从毛坯生产到成品零件的工艺规程制定及铣槽专用夹具设计,其中包括零件的作用、结构、工艺分析与工艺规程、专用夹具设计等内容。
关键词:
离合齿轮,工艺分析,工艺规程,专用夹具,设计
1.零件的分析
1.1零件的作用
零件是CA6140车床主轴箱中运动输入Ⅰ轴上的一个离合齿轮(图2),它位于轴的右端,用于接通或断开主轴的反转传动路线。
该离合齿轮是一个外齿轮,它与花键轴套在一起,通过右端的两个与轮齿相对应的槽与拔叉相配合,然后和内齿轮啮合组成齿轮副,从而传递动力;有时还可以利用脱开的外齿轮兼作齿轮传动用,且与不同齿数齿轮啮合,可以得到不同的传动比,从而改变机器运行的转速,实现变速或换挡功能。
图1离合齿轮三维图
图2离合齿轮零件图
1.2零件的工艺分析
该零件属盘套类回转体零件,它的所有表面均需切削加工,各表面的加工精度和表面粗糙度都不难获得。
4个16mm槽口相对φ68K7mm孔的轴线互成90°垂直分布,其径向设计基准是φ68K7mm孔的轴线,轴向设计基准是φ90mm外圆柱的右端面。
4-φ5mm孔在6X1.5mm沟槽内,孔中心线距沟槽一侧面的距离为3mm,由于加工是不能选用沟槽的侧面为定位基准,要精确地保证上述要求是比较困难的,但这些小孔为油孔,位置要求不高,只要钻到沟槽之内接通油路即可,加工没问题。
1.3零件的生产类型
零件年产量Q=200台/年,n=1件/台;结合生产实际,备用率α和废品率β分别取为10%和1%。
代入公式得该零件的生产纲领
N=Qn(1+10%)X(1-1%)=2000X1X(1+10%)X(1-1%)=2178
零件是机床上的齿轮,质量为1.36kg,属轻型零件,生产类型为中批生产。
2.工艺规程设计
2.1确定毛坯的制造形式
由生产计划可知,该零件为中批生产。
零件材料为45钢,由于零件本身的作用,考虑到其在运行过程中会经常的正、反向行驶,并经常“离”、“合”,故零件在工作过程中经常承受交变及冲击性载荷,齿轮面也应该有较强的硬度,因此应该选用锻件,以便金属纤维不被切断,保证零件的工作可靠性。
由于零件为大批生产,而且零件的尺寸不大,可以采用模锻成型,从而提高生产率,保证加工精度。
2.2设计毛坯图
2.2.1确定圆角半径
本锻件各部分的H/B<2。
为化简起见,本锻件的内、外圆角半径分别取相同数值,以台阶高度H=16~25进行确定。
外圆角半径r=6
内圆角半径R=3
以上所取的圆角半径数值能保证各表面的加工余量
2.2.2确定模锻斜度
本锻件由于上、下模镗深度不相等,模锻斜度应以模镗较深一侧计算。
L/B=110/110=1,H/B=32/110=0.291
查阅相关手册可以确定外模锻斜度α=5°,内模锻斜度加大,取β=7°
2.2.3确定分模位置
由于毛坯是H<D的圆盘类锻件,应采用轴向分模,这样可冲内孔,使材料利用率得到提高。
为了便于起模及便于发现上、下模在模锻过程中错移,选择最大直径即齿轮处的对称平面为分模面,分模线为直线,属平直分模线。
2.2.4确定毛坯的热处理方式
钢质齿轮毛坯经锻造后应安排正火,以消除残余的锻造应力,使不均匀的金相组织通过重新结晶而得到细化、均匀的组织,从而改善加工性。
图3所示为本零件的毛坯图
图3离合齿轮毛坯图
2.3加工方法的选择及工艺路线的制定
2.3.1定位基准的选择
本零件是带孔的盘状齿轮,孔是设计基准(也是装配基准和测量基准),为避免由于基准不重合而产生的误差,应选孔为定位基准,即遵循“基准重合”的原则。
具体点,就是选φ68K7mm孔及一端面作为精基准。
由于本齿轮全部表面都需加工,而孔作为精基准应先进行加工,因此应选外圆及一端面为粗基准。
最大外圆上有分模面,表示不平整,有飞边等缺陷,定位不可靠,所以不能选为粗基准。
2.3.2零件表面加工方法的选择
本零件的加工面有外圆,内孔,端面,齿面,槽及小孔等,材料为45钢。
以公差等级和表面粗糙度要求,查阅工艺手册中零件表面加工方法、加工经济精度与表面粗糙度相关内容,其加工方法如下:
(1)φ90mm外圆面。
为未注公差尺寸,根据GB1800-79规定其公差等级按IT14,表面粗糙度Ra3.2μm,需进行粗车和半精车。
(2)齿圈外圆面。
公差等级为IT11,表面粗糙度为Ra3.2μm,需粗车和半精车。
(3)φ106.5mm外圆面。
公差等级为IT12,表面粗糙度为Ra6.3μm,粗车即可。
(4)φ68K7mm内孔。
公差等级IT7,表面粗糙度为Ra0.8μm,毛坯孔已锻出,为未淬火钢,加工方法可采取粗镗,半精镗之后用精镗,拉孔或磨孔都能满足加工要求。
由于拉孔用于大批生产,磨孔适用于单位小批量生产,所以本零件适合采用粗镗,半精镗和精镗。
(5)φ94mm内孔。
未标注公差尺寸,公差等级按IT14,表面粗糙度为Ra6.3μm,毛坯已锻出,只需粗镗就可。
(6)端面。
本零件的端面为回转体端面,尺寸精度要求不高,表面粗糙度为Ra3.2μm及Ra6.3μm两种要求。
要求Ra3.2μm的端面可粗车和半精车,要求Ra6.3μm的端面,经粗车就可。
(7)齿面。
齿轮模数为2.25,齿数为50,精度8FL,表面粗糙度为Ra1.6μm,采用A级单头滚刀滚齿就能达到要求。
(8)槽。
槽宽和槽深的公差等级分别为IT13和IT14,表面粗糙度分别为Ra3.2μm和Ra6.3μm,需采用三面刃铣刀,粗铣,半精铣。
(9)φ5mm小孔。
采用复合钻头一次就可以钻出。
2.3.3制订工艺路线
齿轮的加工工艺路线一般是先进行齿坯的加工,再进行齿面加工。
齿坯加工包括各圆柱表面及端面的加工。
按照先加工基准面及先粗后精的原则,可以按照如下的工艺路线进行:
工序Ⅰ:
以φ106.5mm处外圆及端面定位,粗车另一端面,粗车外圆φ90mm及台阶面,粗车外圆φ117mm,粗镗孔φ68mm。
工序Ⅱ:
以粗车后的φ90mm外圆及端面定位粗车另一端面,粗车外圆φ106mm及台阶面,车6mmX1.5mm沟槽,粗镗φ94mm孔,倒角。
工序Ⅲ:
以粗车后的φ106mm外圆及端面定位,半精车另一端面,半精车外圆φ90mm及台阶面,半精车外圆φ117mm,半精镗φ68mm孔,倒角。
加工齿面是以孔φ68K7mm为定位基准,为了更好地保证他们之间的位置精度,齿面加工之前,先精镗孔。
工序Ⅳ:
以φ90mm以外圆及端面定位,精镗φ68K7mm孔,镗孔内的沟槽,倒角。
工序Ⅴ:
以φ68K7mm孔及端面定位,滚齿。
4个沟槽与4个小孔为次要表面,加工应安排在最后。
考虑定位方便,应该先铣槽后钻孔。
工序Ⅵ:
以φ68K7mm孔及端面定位,粗铣4个槽。
工序Ⅶ:
以φ68K7mm孔、端面及粗铣后的一个槽定位,半精铣4个槽。
工序Ⅷ:
以φ68K7mm孔、端面及一个槽定位,钻4个小孔。
工序Ⅸ:
钳工去毛刺。
工序Ⅹ:
终检。
2.4工序设计
2.4.1选择加工设备与工艺装备
1)选择机床
①工序Ⅰ、Ⅱ、Ⅲ是粗车和半精车。
各工序的工步数不多,成批生产不要求很高的生产率,所以选用卧式车床就能满足要求。
本零件外廓尺寸不大,精度要求不是很高,选用最常用的C620-1型卧式车床就可以了。
②工序Ⅳ为精镗孔。
由于加工的零件外廓尺寸不大,又是回转体,可以在车床上镗孔。
由于要求的精度较高,表面粗糙度值较小,需选用较精密的车床才能满足要求,因此选用C646A型卧式车床。
③工序Ⅴ滚齿。
从加工要求及尺寸大小考虑,选Y3150型滚齿比较合适。
④工序Ⅵ和Ⅶ是用三面刃铣刀粗铣及半精铣槽,应采用卧式车床。
考虑到本零件属成批生产,所以机床选用比较广泛,选最常用的X62型铣床就能满足要求。
⑤工序Ⅷ钻4个φ5mm的小孔,可采用专用的分度夹具在立式钻床上加工,所以选Z525型立式钻床。
2)选择夹具
本零件粗铣、半精铣槽和钻小孔工序需要专用夹具外,其它工序实用通用夹具即可。
前4道车床工序用三爪自定心卡盘,滚齿工序用心轴。
3)选择刀具
根据不同的工序选择刀具:
①在车床上加工的工序,一般都选用硬质合金车刀和镗刀。
加工钢质零件采用YT类硬质合金,粗加工用YT5,半精车用YT15,精加工用YT30。
为提高生产率及经济性,应该选用可转位车刀。
切槽刀选用高速钢。
②关于滚齿,查阅相关资料采用A级单头滚刀能达到8级精度。
滚刀选用模数为2.25mm的Ⅱ型A级精度滚刀。
③铣刀选镶齿三面刃铣刀。
零件要求铣切深度为15mm,查阅资料可知铣刀的直径为100mm~160mm。
因此所选铣刀:
半精铣工序铣刀直径d=125mm,宽L=16mm,孔径D=32mm,齿数z=20;粗铣由于留有双面余量3mm,槽宽加工到13mm,该标准铣刀无此宽度需特殊订制,铣刀规格为d=125mm,L=13mm,D=32mm,z=20.
④钻φ5mm小孔,由于带有90°的倒角,可采用复合钻一次钻出。
4)选择量具
本零件属成批生产,一般情况下尽量采用通用量具。
根据零件表面的精度要求,尺寸和形状特点,选择如下:
1选择各外圆加工面的量具。
本零件各外圆加工面的量具见表1
表1外圆加工面所用量具单位:
mm
工序
加工面尺寸
尺寸公差
量具
Ⅰ
φ118.5
0.54
读数值为0.02,测量范围0~150游标卡尺
φ91.5
0.87
Ⅱ
φ106.5
0.4
Ⅲ
φ90
0.87
读数值为0.05,测量范围0~150游标卡尺
φ117
0.22
读数值为0.01,测量范围100~150外径千分尺
加工φ91.5mm外圆面可用分度值0.05mm的游标卡尺进行测量,但由于与加工φ118.5mm外圆面是在同一工序中进行,所以就用表中的一种量具就可以了。
②选择加工孔用量具。
φ68K7mm孔经粗镗,半精镗,精镗3次加工。
粗镗至φ65+0.19mm,半精镗φ67+0.09mm.
粗镗孔φ65+0.19mm,公差等级为IT11,选读数值0.01mm、测量范围50mm~125mm内径千分尺。
半精镗φ67+0.09mm,公差等级为IT9,选读数值0.01mm、测量范围50mm~100mm的内径百分表。
精镗φ68K7mm孔,由于精度要求高,加工时每个工件都需进行测量,宜选用极限量规。
3选择加工轴向尺寸所用量具,加工轴向尺寸所用量具见表2
加工轴向尺寸所用量具单位:
mm
工序
尺寸及公差
量具
Ⅰ
66.4-0.34
读数值0.02、测量范围0~150游标卡尺
20+0.21
Ⅱ
64.7-0.34
32+0.25
31+0.52
Ⅲ
20+0.08
读数值0.01、测量范围0~25游标卡尺
64-0.4
读数值0.01、测量范围50~75外径千分尺
④选择加工槽所用量具。
槽经粗铣、半精铣2次加工。
槽宽及槽深的尺寸公差的等级为:
粗铣时均为IT14;半精铣时,槽宽IT13,槽深为IT14,均可选用读数值为0.02mm,测量范围0~150mm的游标卡尺进行测量。
⑤选择滚齿工序所用量具。
滚齿工序在加工是测量公法线长度就可以。
根据手册可选分度值0.01mm测量范围25~50mm的公法线千分尺。
2.4.2确定工序尺寸
以圆柱面的工序尺寸确定为例:
圆柱表面多次加工的工序尺寸与加工余量有关。
前面已确定圆柱面的总加工余量,应将毛坯余量分为各工序加工余量,然后由后往前计算工序尺寸。
中间工序尺寸的公差按加工方法的经济精度确定。
本零件各圆柱表面的工序加工余量,工序尺寸,公差和表面粗糙度见表3
表3圆柱表面的工序加工余量,工序尺寸,公差和表面粗糙度单位:
mm
加工表面
工序双边余量
工序尺寸公差
表面粗糙度/μm
粗
半精
精
粗
半精
精
粗
半精
精
φ117h11外圆
2.5
1.5
φ118.5-0.54
φ117-0.22
Ra6.3
Ra3.2
φ106.2-0.4外圆
3.5
φ106.5-0.4
Ra6.3
φ90外圆
2.5
1.5
φ91.5
φ90
Ra6.3
Ra3.2
φ94孔
5
φ94
Ra6.3
φ68K7孔
3
2
1
φ65+0.19
φ67+0.074
φ68-0.021
Ra6.3
Ra1.6
Ra0.8
2.4.3选工序Ⅱ切削用量及基本时间的确定
本工序仍为粗车(车断面,外圆,台阶面。
镗孔,车沟槽及倒角)已知条件与工序Ⅰ相同。
车断面、外圆及台阶面可采用工序Ⅰ相同的可转位车刀。
镗刀选YT5硬质合金、主偏角kr=90°、直径为20mm的圆形镗刀。
车沟槽采用高速钢成形切槽刀。
采用工序Ⅰ确定切削用量的方法,得本工序的切削用量及基本时间见表4
表4工序Ⅱ切削用量及基本时间
工步
ap/mm
f/mm·r-1
v/m·s-1
n/r·s-1
Ti/s
粗车端面
1.7
0.52
0.69
2
16
粗车外圆φ106.5mm
1.75
0.65
0.69
2
25
粗车台阶面
1.7
0.52
0.74
2
8
镗孔及台阶面
2.5及1.7
0.2
1.13
3.83
69
车沟槽
手动
0.17
0.5
倒角
手动
0.69
2
2.4.4选工序Ⅳ切削用量及基本时间确定
本工序为精镗φ68
mm孔、镗沟槽及倒角。
1)确定精镗φ68mm孔的切削用量。
所选刀具为YT30硬质合金、主偏角Kr=45°、直径为20mm的圆形镗刀。
其耐用度T=60min.
①
②f=0.04mm/r
③v=0.9X1.4X291/(600.2X0.50.15X0.040.2)=5.52m/min
④n=(1000X5.52)/(πx68)=1598.6r/min
根据C616A车床的转速表,选择n=1400r/min=23.3r/s,则实际切削速度v=4.98m/s.
确定镗沟槽的切削用量。
选用高速钢切槽刀,采用手动进给,主轴转速n=40r/min=0.67r/s,切削速度v=0.14m/s.
2)基本时间
精镗φ68mm孔的基本时间为
Tj=(33+3.5+4)/(0.04X23.3)=44s
3.专用夹具设计
本夹具是工序Ⅵ用三面刃铣刀纵向进给粗铣4X16mm槽口的专用夹具,在X62W卧式铣床升加工离合齿轮一个端面上的两条互成90°的十字槽。
有关说明如下:
1)定位方案
工件以另一端面及φ68K7mm孔为定位基准,采用平面与定位销组合定位方案,在定位盘10的短圆柱面及台阶面上定位,其中台阶平面限制3各自由度,短圆柱面限制2个自由度,共限制了5各自由度。
槽口在原周上无位置要求,该自由度不需限制。
2)加紧机构
根据生产率要求,运用手动夹紧可以满足。
采用二位螺旋压板联动加紧机构,通过拧紧右侧夹紧螺母15使一对压板同事压紧工件,实现夹紧,有效提高了工作效率。
压板夹紧力主要作用是防止工件在铣削作用力下产生倾覆和震动,手动螺旋夹紧是可靠的,可免除夹紧力计算。
3)对刀装置
采用直角对刀块及平面塞尺对刀。
选用JB/T8031.3—1999直角对刀块17通过拧紧对刀座21固定在夹具体上保证对刀块工作面始终处在平行于走刀路线的方向上,这样便不受工件转位的影响。
确定对刀块的对刀面与定位元件定位表面之间的尺寸,水平方向尺寸为13/2(槽宽一半尺寸)+5(塞尺厚度)=15mm,其公差取工件相应尺寸公差的1/3。
由于槽宽尺寸为自由公差,查标准公差表IT14等级公差值为0.43mm则水平尺寸公差取0.43X1/3=0.14mm,对称标注为(11.5±0.07)mm,同理确定垂直方向的尺寸为(44±0.1)mm(塞尺厚度也为5mm)。
4)夹具与机床连接元件
采用两个标准定位键A18h8JB/T8016—1999,固定在夹具体底面的同一直线位置的键槽中,用于确定铣床夹具相对于机床进给方向的正确位置,并保证定位键的宽度与机床工作台T形槽相匹配的要求。
5)夹具体
工件的定位元件和夹紧元件由连接座6连接起来,连接座定位固定在分度盘23上,而分度装置和对刀装置均定位固定在夹具体1上,这样该夹具便有机连接起来,实现定位、夹紧、对刀和分度等功能。
夹具体零件图见图3
6)使用说明
安装工件时,松开右边铰链螺栓上的螺母15,,将两块压板16后撤,把工件装在定位盘10上,再将两块压板16前移,然后旋紧螺母15,通过杠杆8联动使两块压板16同时夹紧工件。
为了使压板和走刀路线在4个工位不发生干涉,压板与走刀路线成45°角布置。
当一条槽加工完毕后,扳手30顺时针转动,使分度盘23与夹具体1之间松开。
分度盘下端沿圆周方向分布有4条长度1/4周长的斜槽。
然后逆时针转动分度盘,在斜槽面的推压下,使对定销24逐步退入夹具体的衬套孔中,当分度盘转过90°位置时,对定位销依靠弹簧力量弹出,落入第二条斜槽中,再反靠分度盘使对定销与槽壁贴紧,逆时针转动扳手30把分度盘紧定在夹具体上,就可以加工另一条槽。
由于分度盘上4条槽为单向升降,所以分度盘也只能单向旋转分度。
7)结构特点
该夹具结构简单,操作方便。
但分度精确受到4条斜槽制造精度的限制,适用于加工要求不高的场合。
夹具上有直角对刀块17,可使夹具在一批零件的加工之前很好的对刀(与塞尺配合使用);同时,夹具体底面上的一对定位键可使整个夹具在机床工作台上有一正确的安装位置,以利于铣削加工。
本夹具调整对刀块位置、增添周向定位机构,就可以用于下一道工序,成为在X62W卧式铣床上精铣槽口的专用夹具,使离合齿轮的十字槽最终成形。
图4专用夹具装配图
4.毕业设计心得体会
三年的大学学习,让我对数控技术与应用方面的知识有了一个系统而又全新的的认识,也对计算机方面的知识有了深入的了解。
毕业设计是我们学习中最后一个重要的实践性环节,是一个综合性较强的设计任务,它为我们以后从事技术工作打下了一个良好的基础,对我们掌握所学知识情况进行了全面而又直观的检测。
为了能够较好的完成这次毕业设计,我投入了万分的精力做了充分的准备工作。
首先,我先针对毕业课题来考虑,在指导老师缪飞军的指点和帮助下,对所需的资料进行搜集和整理,根据设计的要求,再对资料做一个简单的归类。
其次,依据指导老师给出的设计任务要求,先制定设计的总体方案,按照指导老师要求的设计进度,一步步的完成此次的设计任务。
毕业设计虽已结束,但想想我在其中所学到的知识,所遇到的困难,仍记忆犹新。
它让我明白了无论是设计新产品,还是改造原先的老产品,都是一个复杂的技术过程,容不得半点含糊。
设计人员应先明白设计的目的,了解产品的价值和实用性,其次要对设计的产品进行构思,确定总体方案,查阅资料。
本次设计也暴露了我们不少的缺点和问题:
对于所学知识还没有做到仔细、认真消化,许多方面还是只有一个大概的认识,没有深入探讨,对实际事物没有深刻得了解,没有做到理论联系实际,没有达到对所学的知识熟练运用的水平。
这也从一个侧面反映出我们设计经验不足,思维不够开拓,不够灵活。
从而我得出一个结论:
无论是现在还是以后走上工作岗位,还是再深造,都应该虚心向老师和前辈们学习,从而不断完善自我,提高自我水平。
参考文献
[1]赵家奇.机械制造工艺学课程设计指导书(第2版)[M].北京:
机械工业出版社,2000[2]李云.机械制造及设备指导手册[M].北京:
机械工业出版社,1997.8
[3]孟少农.机械加工工艺手册[M].北京:
机械工业出版社,1991.9
[4]徐圣群.简明加工工艺手册[M].上海:
科学技术出版社,1991.2
[5]徐圣群.简明加工工艺手册(第2版)[M].北京:
机械工业出版社,2003.1