液压油缸检验规范详解.docx
《液压油缸检验规范详解.docx》由会员分享,可在线阅读,更多相关《液压油缸检验规范详解.docx(23页珍藏版)》请在冰豆网上搜索。
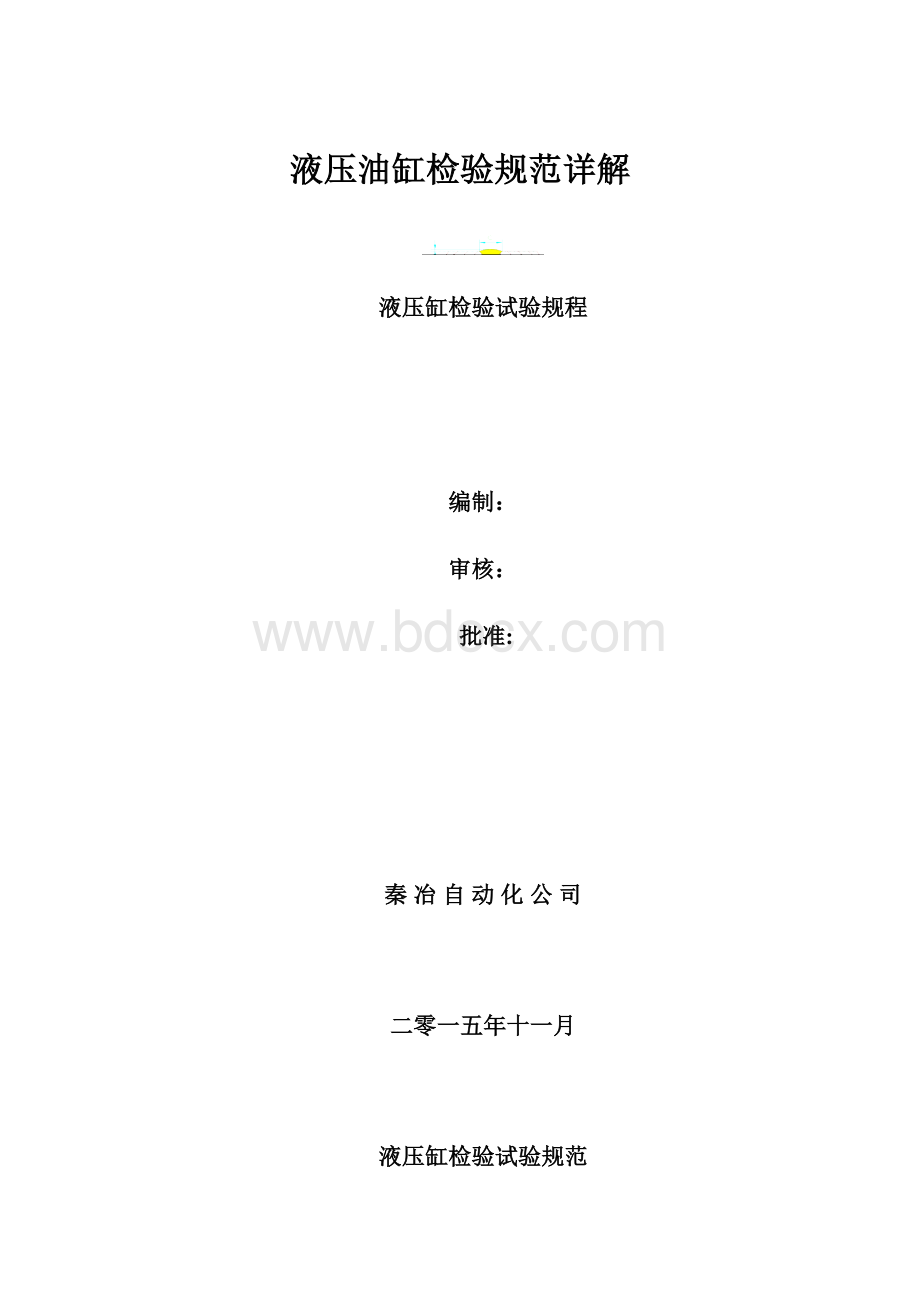
液压油缸检验规范详解
液压缸检验试验规程
编制:
审核:
批准:
秦冶自动化公司
二零一五年十一月
液压缸检验试验规范
1.0范围
适用于本公司液压缸的整个制作过程中的检验试验过程。
2.0检验试验流程(同液压缸的制作流程,图中棱形框为检验试验过程);
不合格不合格
不合格合格
合格
合格
不合格
合格
不合格
不合格不合格合格
不合格
合格合格
不合格不合格合格
不合格
合格
3.0液压缸检验试验
3.1总要求
3.1.1所有参与液压缸检验试验人员熟悉相应的生产图中要求的结构、尺寸和各项性能指标的要求;
3.1.2检验试验人员必须熟练掌握所使用的测量工具、仪表和设备的使用功能、适用范围和使用方法;
3.1.3所使用的测量工具、仪表必须定期检定和/或校准;
3.1.4在检验每个工件前,必须确认其标识号,并将该件的标识号记录在相应的检验试验表中相应栏内;
3.1.5质检部门确定:
3.1.5.1检验区域:
待检区;
检验区;
合格品区;
不合格品区;
3.1.5.2工件状态标识:
待检;
合格;
不合格;
3.1.6质检员在收到报检单、生产图和相关见证文件后,进行检验试验;
3.1.7质检员必须严格按图、有关技术文件和检验试验表的每一项要求,并记录在相应的检验试验表中;
3.1.8对于不合格品,质检人员做好“不合格”标识,并将不合格的工件放在不合格品区域,填写《不合格品评审单》,进入不合格品处理流程;
3.1.9产品检验试验合格后,质检人员做好“合格”标识,工件进入下一流程,所有质量见证文件在质检部门留存;待产品入库(出厂)后整理归档;
3.2检验试验使用的工具、仪器、仪表、设备
3.2.1尺寸测量:
卷尺,游标卡尺,内、外径千分尺,沟槽深度千分尺,沟槽宽度千分尺,角度千分尺,
塞尺,内、外圆角规,螺纹规;
3.2.2表面质量:
粗糙度仪或粗糙度样块;
3.2.3压力试验:
试验台,压力表;
3.2.4漆膜检验:
漆膜测厚仪;
3.3采购物品的检验
3.3.1密封元件
3.3.1.1合格供方定期(每年)提供每种类别的密封元件的检验报告;
3.3.1.2采购人员提供报检单和采购清单,按采购清单所示的规格进行检验;
用卡尺进行尺寸检验,检验的目的是确认符合采购要求的规格,不做精确尺寸测量;在检验时必须注意避免量具的尖锐部位挤压密封元件的表面,造成密封元件表面划伤和压痕;
3.3.1.3目视检查表面磕伤、撕裂、划伤、尖角、毛刺;
3.3.1.4发现不合格的退回到采购部门,在相关文件中进行记录;并跟踪处理结果;
3.3.1.5保留检验记录和质量见证文件;
3.3.2原材料
3.3.2.1采购人员提供报检单、材质单和采购清单,按采购清单所示的规格进行检验;
3.3.2.2按炉批号进行原材料的化学性能和力学性能的复验,复验结果符合材质单;
3.3.2.3检验规格尺寸
输送流体用无缝钢管:
外径允差为外径的±10%;壁厚允差为壁厚的+15%/-12.5%(最小+0.45/-0.40);
精密无缝钢管
精密无缝管参数及偏差
规格
外径mm
内径mm
壁厚mm
规格
外径mm
内径mm
壁厚mm
尺寸
允差
尺寸
允差
尺寸
允差
尺寸
允差
尺寸
允差
尺寸
允差
80×7
80
±0.35
62
±0.35
7
±10%
170×12.5
170
±0.85
145
±0.85
12.5
±10%
100×9
100
±0.45
82
±0.45
9
180×12.5
180
±0.9
155
±0.9
12.5
130×12.5
120
±0.65
105
±0.65
12.5
190×12.5
190
±0.95
165
±0.95
12.5
150×11
150
±0.75
125
±.75
9
圆钢
圆钢规格及偏差
公称直径mm
允许偏差mm
公称直径mm
允许偏差mm
>30~≥50
±0.6
>110~≥150
±1.40
>50~≥80
±0.8
>150~≥200
±2.00
>80~≥110
±1.10
>200~≥250
公称直径的±1.3%
3.3.2.4发现不合格的反馈到采购部门,由采购部门和相关部门联系协商,决定退货或让步接收;在相关文件中进行记录,并跟踪处理结果;
3.3.2.5保留检验记录和质量见证文件;
3.3.3外购(外协)件
3.3.3.1外购外协人员提供报检单、质量证明书、采购图、合同或技术协议,质检人员按前述文件进行检验;
3.3.3.2发现不合格的,填写不合格评审单,反馈到责任部门,由责任部门和相关部门和联系协商,决定让步接收、修复或报废;在相关文件中进行记录,并跟踪处理结果;
3.3.3.3保留检验记录和质量见证文件;
3.4零部件检验
3.4.1机加工
3.4.1.1操作者将自检合格的工件连同报检单和图纸及其他技术文件一起送达质检人员;质检人员按相关文件进行检验;
3.4.1.2检验内容:
尺寸及偏差;
表面粗糙度;
倒角和圆角;
棱边圆滑过渡;
3.4.1.3将检验内容记录在《检验记录表》中,并根据要求判定结果“合格”“不合格”;同时在报检单上签署判定结果的结论;在工件上对检验结果进行标识;
3.4.1.4对于不合格品进行跟踪;
8.0标识与记录
8.1、需报检的产品必须开具报检单,质检员接到报检单后应及时进行检验,对于报检时拒绝开具报检单的质检员有权拒绝检验。
8.1.1.检查合格的产品,认真填写报检单,注明日期、姓名并在产品上做好合格标识及在产品记录表上做好相应的记录。
8.1.2.检查不合格的产品,做好标识,及时找到有关人员进行维修或确认并在报检单和记录中写清不合格情况。
8.1.3.返修完的产品,经生产部门开具的返修报检单后,方可进行二次检验。
每道工序均编制工序卡,按工序卡要求进行各项制作任务;完成本道工序后,填报检单报检,经质检人员确认合格签字,制作人员本人签字后,该工序卡和制作的零部件一起转入到下一工序;各种检验和见证文件由质检部门收集,待油缸产品入库后整理归档;
3.1.3每个零部件在完成每道工序后,都要进行标识或标识移植,标识从原材料开始,标识号与炉批号和出厂编号形成一定的连带关系,在记录文件中体现;标识贯穿在整个制作过程,并保持同一性和连续性;
3.1.4所有密封件和外购件到厂检验合格后,包装完好,放置在安全、干净的场所,保证不受损害和脏污;
3.1.5所有机加工件在加工、转序、运输和仓储过程中,必须确定合适的运输工具和保护托架,确保加工表面不被碰伤、划伤;
3.1.6清洗、密封件安装和油缸装配前,必须确认所需零部件和元件是否齐全;
3.1.7事先计划好每天的油缸装配数量,清洗和密封件安装后,尽量争取当天完成装配工作;
3.2采购
3.2.1在合格供方内采购
3.2.2采购的物品到厂后,填报检单和采购清单及相关其他文件一起报检,经质检人员检验合格后进入下一工序;不合格的由采购部门反馈到供方进行更换或修复处理;
3.2.3采购的物品到厂后,做好相关标识(名称、规格和数量),且同一种物品标识是唯一的;
3.2.3密封件采购
3.2.3.1按物资采购申请表中型号、规格尺寸、材质、到货日期等要求进行采购;
3.2.3.2随密封元件一起供方提供产品合格证和检验报告(必要时);
3.2.3.3填写报检单,密封件和证件一起送检;
3.2.4原材料
3.2.4.1按物资采购申请表中材料类别、规格尺寸、材质、到货日期等要求进行采购;
3.2.4.2随原材料一起,供方按炉批号提供材质单;
3.2.4.3填写报检单,原材料和材质单一起送检;其中理化试验按批次进行;
3.2.5外购件
3.2.5.1按物资采购申请表和订货图(必要时签订技术协议和订货合同);
3.2.5.2外购件到货时,随机提供材质单(同一批次的提供一份)、检验报告和合格证;
3.2.5.3填写报检单,外购件和随机资料一起送检;
3.3零部件制作
3.3.1通用要求
3.3.1.1每道工序完成后,操作者将工件和工序卡一起转入下道工序;
3.3.1.2所有加工件在加工时,操作者必须注意倒角、圆角R的尺寸和粗糙度,严格满足生产图要求。
同时未注棱角倒钝和去除毛刺;
3.3.1.3在每道工序完成后,每个零部件都要做出相应的标识(标识移植),表示的内容为相应零件的图号;如为多件,则在图号后面加“—1(—2、—3···依次类推)”;
3.3.2下料
按每种零件的生产图中结构及尺寸选择合适的原材料,并留出足够的加工余量下料、标识;
3.3.3热处理调质
3.3.3.1有调质处理要求的料,按生产图要求进行调质处理;
3.3.3.2对于细长杆(活塞杆)在热处理时尽量减少在长度上的变形;
3.3.3.3处理后进行标识移植;
3.3.3.4处理后提供温度曲线和硬度检验报告;
3.3.4零部件制作
3.3.4.1活塞、导向套
a加工设备:
车床;
b按图加工外圆、内孔、端面、螺纹,尺寸达图;
c按图加工密封件用沟槽尺寸、倒角和倒圆角尺寸,尺寸达图
d粗糙度、图中标注的形状、位置要求达到图纸要求值;
磨削后
直径
性质
磨削长度
磨削前的加工偏差
100以下
100~250
250~500
500~800
800~1200
直径的磨削余量
18~30
不淬火
0.35
0.35
0.45
0.55
0.65
-0.14
淬火
0.40
0.45
0.55
0.65
0.75
30~50
不淬火
0.45
0.45
0.55
0.55
0.65
-0.17
淬火
0.50
0.60
0.60
0.70
0.80
50~80
不淬火
0.45
0.45
0.55
0.55
0.65
-0.20
淬火
0.50
0.60
0.70
0.75
0.80
80~120
不淬火
0.45
0.45
0.55
0.55
0.65
-0.23
淬火
0.65
0.75
0.80
0.85
0.85
120~180
不淬火
0.45
0.55
0.55
0.55
0.65
-0.23
淬火
0.65
0.75
0.85
0.85
0.85
e自检后报检、转序;
3.3.4.2活塞杆
a加工设备:
车床、磨床、淬火处理装置、镀铬装置;
b车削加工:
活塞杆标注“0.4”的表面的直径留磨削余量,根据具体直径按表1选取粗糙度为3.2;螺纹和外圆及长度尺寸加工达图;
表1外圆磨削加工余量
c感应加热表面淬火,淬火硬度和层深达图要求,提供温度曲线和硬度检验报告;淬火时其他表面做好保护;
d磨外圆,外圆尺寸10μm到20μm(视生产图镀铬层厚,满足最终尺寸而定),形位公差、粗糙度达图要求;磨削时做好螺纹的保护;填报检单报检;
e镀铬,镀铬层深达图要求,提供层深检验报告;
f抛光;
g做好表面磕碰划伤防护,转库存;
3.3.4.3间隔套、内半环、接头、缸筒体、缸底
a加工设备:
车床、钻床、丝锥、线切割
b间隔套:
车削加工尺寸、形位公差、粗糙度达图要求;报检转库存;
c内半环:
车削加工,尺寸、形位公差、粗糙度达图要求;
按图视位置线切割后报检转库存;
3.3.4.4缸体
a制作设备:
车床、珩磨设备、氩弧焊机、气保焊机
b接头:
车削加工,尺寸、形位公差、粗糙度达图要求;
钻孔、攻丝后报检转缸筒焊接;
c缸筒体:
车削加工,尺寸、粗糙度达图要求;
前油口钻孔,孔内侧棱角倒钝后报检转缸筒焊接;
d缸底:
车削加工,尺寸、形位公差、粗糙度达图要求;
后油口钻孔、攻丝后报检转缸筒焊接;
e缸筒:
缸筒体与中间耳轴和接头的焊接:
a)焊接前清理焊接区域即热影响区,达到焊接表面金属原色,保证该区域无杂物、粉尘及油污;
b)按图尺寸要求,中间耳轴和接头在缸筒体上找正位置定位;
c)焊接;
缸筒加工
a)内圆尺寸留珩磨余量,尺寸、粗糙度、形位公差达图要求;
b)车削加工两端面、沟槽及两端倒角,尺寸、粗糙度、形位公差达图要求;
缸筒的焊接、加工属外协加工,未作具体要求,验收时按订货图进行验收确认;
f缸体焊接:
缸体与缸底焊接:
焊接前清理焊接区域即热影响区,达到焊接表面金属原色,保证该区域无杂物、粉尘及油污;
按图尺寸要求找正位置定位;
焊前做好其他加工面的保护;
氩弧焊打底,焊后进行着色检验;如无焊接缺陷,焊缝表面清理干净后,气保焊焊接成型。
具体参数见表2;为减少缸筒变形,尽量采用小电流多道次的焊接方案,并在每道次之后;停留一段时间,自然冷却,再进行下一道次的焊接;
表2缸体与缸底焊接参数表
项目
焊接方式
焊丝牌号、规格
焊接电流(A)
保护气流量(l/min)
打底焊
氩弧焊
ER50-6Φ1.6
100~180
6~12
成型焊
气保焊
ER50-6Φ1.6
150~280
弧电压24~32V
焊缝断面尺寸
预留间隙b(mm)
焊缝宽度c(mm)
余高h(mm)
2
18±1
1~1.5
报检转库存;
3.4装配
3.4.1要求
3.4.1.1装配环境必须清洁,相对比较宽敞、明亮。
3.4.1.2液压缸装配三道工序(清洗、装密封元件、组装)在一个工位上完成,不存在中间转序;
3.4.1.3按照工作计划,将零部件(标识号要同一)和密封元件按计划装配台数准备齐全,核对密封元件的名称规格,做到当天清洗、装密封件,当天装配完成,封好油口;
3.4.1.4所有零部件、密封元件应按同一台液压缸的标识号,放置在铺有干净橡胶板的工作台上,不准落地;
3.4.1.5工作人员在每道工序前认真检查零部件和密封元件是否有表面磕伤、撕裂、划伤、尖角、毛刺;如发现及时更换;零件在装配前必须清理和清洗干净,不得有毛刺、飞边、锈蚀和氧化皮、切屑、砂粒、灰尘、油污、毛发和棉纱类等污物;
3.4.1.6整个过程使用的器械必须干净;
3.4.1.7整个装配过程的参与人员不允许带棉线类手套,被装配的零部件、密封元件不允许接触棉纱、毛发类物品;
3.4.1.8车间内使用的气源必须经过气动三大件将压缩空气中的水分去除,压力可进行调节;
3.4.2清洗
3.4.2.1使用器械:
清洗槽、煤油、自来水、压缩空气、风枪、铜丝刷、丝锥;
3.4.2.2自制件(含外协件)清洗:
a粗洗(主要是零部件外表面):
用水清洗掉表面污物,所有螺纹油口必须用丝锥重攻后清洗,保证油口内无杂物及污物,然后用压缩空气快速吹干;
b精洗:
在清洗槽内利用合适的辅助工具用煤油清洗,然后用压缩空气吹干
3.4.2.3密封元件直接在清洗槽中用煤油清洗后吹干;
34.2.4清洗液保持清洁,达到NAS9级;如果超出需进行过滤或更换;
3.4.2.5清洗后零部件的标识如果消失,务必采取措施(如同一油缸按区域放置或采用在存放器械上进行标识),保证标识的连续性和正确;且应保证各零部件不能接触碰撞;
3.4.2.6清洗后的零部件在组装前和组装过程中不得接触棉纱类物品;
3.4.3安装密封元件
3.4.3.1使用器械:
安装复原工具、润滑油
3.4.3.2安装前应确保密封元件、零部件及安装工具的清洁,与密封件接触的物件不允许有尖锐突出的部位,避免密封件表面出现划伤或撕裂;
3.4.3.3安装前在密封元件和密封元件经过的表面上涂抹干净的润滑油;螺纹部分加套,防止刮伤密封元件表面;
3.4.3.4密封件在安装时避免拉伸或压凹过大而造成强度破坏;
3.4.3.5活塞用密封元件安装:
aO型密封圈在安装前内径涂抹少许干净润滑脂,用手或工具推到密封槽内;O型密封圈安装后避免断面扭曲现象;
b组合密封件中的密封件,用工具推到密封槽内;
c组合密封件中的辅助件为开口的,安装时用手轻轻的掰开,放在合适的位置;
3.4.3.6导向套(活塞杆)密封件的安装:
a安装前密封件用手沿径向一点向内压凹,使得密封件直径小于孔的最小直径,然后送入到密封沟槽内,放正后,密封元件恢复到正常状态;
b对于硬度较高的密封件(如斯特封)在安装前用水或油加热到80°C~120°C,变软后压成凹形放入到沟槽内,用手理顺复原,然后用涂油的复原工具一边旋转一边推入孔内,保持一分钟后取出工具即可;
3.4.4液压缸装配
3.4.4.1使用器械:
安装架、安装套管、润滑油、风管、被减压的压缩空气、木锤或橡胶锤
安装前再次确认:
a缸筒内(包括油口孔内)清洁无污物;
b活塞组件清洁无污物;
c导向套组件清洁无污物;
3.4.4.2活塞组件缸体的安装:
a缸筒内表面均匀涂液压油;
b将钢筒找正位置后固定在安装架上;
c将活塞组件与缸筒组件找正位置,保证同心,向前送进到缸体端部;
d观察活塞组件的密封圈外圆是否与缸体端部有刮划现象,如有则采取措施,保证密封件表面不被划伤;
e保证缸体和活塞组件同心后用木锤或橡胶锤击打活塞杆端部,击打前对活塞杆端部螺纹做好保护,或者在活塞杆端部加垫板,将活塞组件缓慢推进到缸体内直到底端;
3.4.4.3安装导向套
a导向套外圆、内孔均匀涂液压油;
b将导向套找正位置后,同样观察导向套的密封圈外圆是否与缸体端部有刮划现象,如有则采取措施,保证密封件表面不被划伤;
c保证导向套与缸体通同心后,将安装套管放在导向套上端,用木槌击打装入到缸筒内,留出安装内半环的安装位置;
d将内半环装到缸筒的卡槽内并固定好;
e在缸底油口中通入经减压的压缩空气(压缩空气的压力由小到大调整,以活塞杆能缓慢升起为原则,切忌压力过大,造成各种可能的损伤),向前推动活塞,活塞推动导向套与内半环靠紧,然后将间隔套顶到内半环的外侧,最后将轴用弹性挡圈固定在导向套的沟槽内;
f将缸底油口的接头风管拆下保持自由开口状态,击打活塞端部或端部垫板,将活塞组件缓慢推进到缸体内直到底端
g将液压缸的两个油口用相应的封堵封住;
3.4.4.4连接端部耳环
a清理耳环的连接螺纹;
b将耳环和活塞杆端螺纹连接,调整到生产图要求的尺寸(此时,油缸活塞在油缸的底部);
c将耳环螺纹端的侧边紧定螺钉旋紧锁定尺寸;
3.4.5将带有出厂编号的产品铭牌钉在液压缸合适的或指定的位置,出厂编号必须和记录文件中的标识号相符;
3.4.5填报检单报检,合格转序;
4.0油缸出厂试验、检验
4.1试验项目
a试运转
b启动压力特性试验
c耐压试验
d泄露试验
e缓冲试验
f行程检验
4.2试验检验
4.2.1将液压缸油口的封堵打开,连接到试验台;
4.2.2按要求进行各项试验,试验步骤和方法详见《试验台操作规程》;
4.2.3质检员现场观察、记录试验检验数据;并记入检验试验相关的记录表;
4.2.4试验检验时应注意安全,以防连接件特别是螺纹连接件及高压油伤人,试验台周围严禁站人,特别是螺纹连接件正对面严禁站人;
4.2.5从实验台上拆下油缸,用经减压的压缩空气将液压缸内的油液排出回收,排除方法:
一端接压缩空气,另一端的软管直接放到回收桶;反向操作排出另一腔;然后油口用封堵封住;
4.2.6经质检员确认合格后转入下一工序;
5.0油缸表面防护处理
5.1在液压缸做好内部和配合表面的保护后,进行表面清理,可采用抹布或毛刷、铜丝刷蘸稀料进行清理;保证表面无锈蚀、粉尘和油污等;
5.2铭牌用不粘胶带覆盖,防止尤其涂抹到名牌表面上;
5.3清理后尽快进行表面喷漆,喷漆按《G/JL0705.05-2008喷漆技术条件》及《G/JL0705.04-2008A、G/JL0705.04-2008B喷漆作业指导书》执行;
5.4喷漆表面不得有漏喷、漆瘤、漆挂;漆膜厚度均匀,达到漆膜厚度要求;
6.0包装
6.1按公司有关规定进行,一般可有以下包装方式:
a放在底排固定;
b草绳捆扎
c包装箱
d真空包装后放包装箱;
6.2不管哪种包装方式,油口的封堵必须牢固,活塞杆裸露部位、缸头耳环、与设备连接部位的配合面做好防磕碰、划伤和防锈蚀的保护措施;
6.3包装后在包装的外部做液压缸的有效标识,并确保标识保留到开箱;
7.0入库(发货)
7.1按公司规定办理入库(发货);
7.2随机文件:
合格证和检验试验报告(需要时);
记录文件:
1.下料工序卡
2.零部件制作工序卡
3.液压缸装配工序卡
4.表面处理、包装工序卡
下料工序卡
设备名称
图号
生产编号
下达日期
序号
零件名称
图号
标识号
材质
下料要求
实际下料
下料
方式
操作者(签字)
设备
出厂编号
类别
规格尺寸
类别
规格尺寸
姓名
完成日期
编制:
审核:
批准:
零部件制作工序卡
设备名称
图号
生产编号
出厂编号
零部件名称
图号
标识号
下达日期
序号
工序
设备及工具
工艺要求
自检(签字)
操作者
完成日期
编制:
审核:
批准:
液压缸装配工序卡
设备名称
图号
生产编号
出厂编号
下达日期
序号
工序
装配内容、参数及技术要求
设备及工具
自检(签字)
操