变频器技术及PLC实训报告.docx
《变频器技术及PLC实训报告.docx》由会员分享,可在线阅读,更多相关《变频器技术及PLC实训报告.docx(27页珍藏版)》请在冰豆网上搜索。
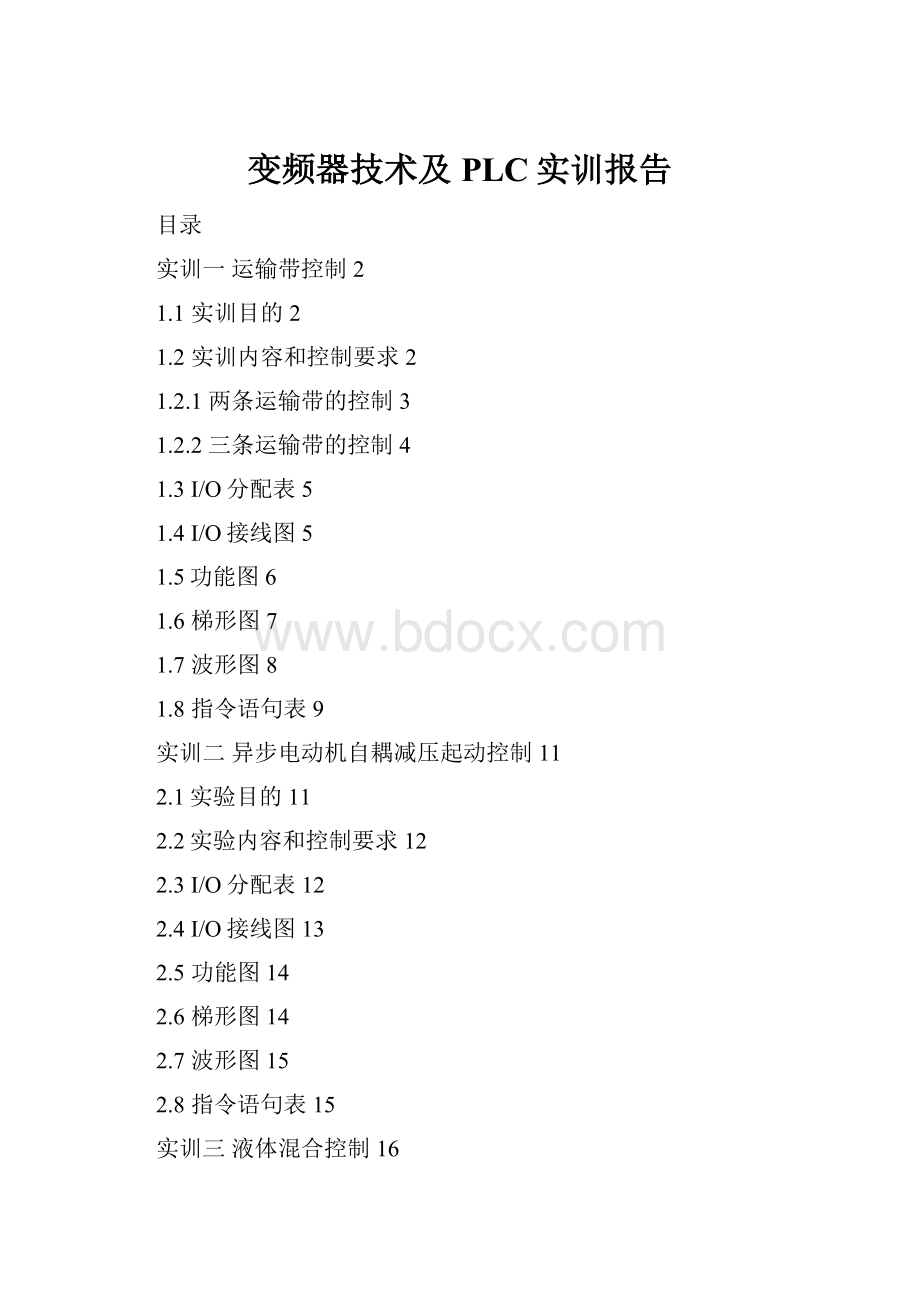
变频器技术及PLC实训报告
目录
实训一运输带控制2
1.1实训目的2
1.2实训内容和控制要求2
1.2.1两条运输带的控制3
1.2.2三条运输带的控制4
1.3I/O分配表5
1.4I/O接线图5
1.5功能图6
1.6梯形图7
1.7波形图8
1.8指令语句表9
实训二异步电动机自耦减压起动控制11
2.1实验目的11
2.2实验内容和控制要求12
2.3I/O分配表12
2.4I/O接线图13
2.5功能图14
2.6梯形图14
2.7波形图15
2.8指令语句表15
实训三液体混合控制16
3.1实训目的16
3.2实训内容和控制要求16
3.2.1液体混合控制程序的调试A16
3.2.2液体混合控制程序的调试B17
3.3I/O分配表18
3.4I/O接线图19
3.5功能图20
3.6梯形图21
3.7指令语句表22
实训总结25
参考文献27
实训一运输带控制
1.1实训目的
熟悉S7-200系列PLC的指令,用经验设计法编写简单的梯形图程序。
1.2实训内容和控制要求
两条运输带循序相连(见图1-1)为了避免运送的物料在1号运输带上堆积,按下起动按钮I0.0,1号运输带开始运行,5s后2号运输带自动起动。
停机的顺序与起动的顺序刚好相反,即按了停止按钮I0.1后,先停2号运输带,5s后停1号运输带。
PLC通过交流接触器KM1和KM2控制两台电动机M1和M2。
图1-3是PLC的外部接线图,SB1和SB2分别是起动按钮和停止按钮。
梯形图程序如图1-7所示,图1-9是程序中各变量的波形图。
将程序下载到PLC后运行程序。
用接在输入端子I0.0的小开关发出起动信号,观察Q0.0是否变为1状态,5s后Q0.1是否能自动变为1状态。
用接在输入端子I0.1的小开关发出停止信号,观察Q0.1是否马上变为0状态,5s后Q0.0是否自动变为0状态。
1.2.1两条运输带的控制
图1-1两条运输带的示意图
1.2.2三条运输带的控制
图1-2三条运输带的示意图
3条运输带顺序相连(见图1-2),为了避免运送的物料在1号和2号运输带上堆积,按下起动按钮I0.0,1号运输带开始运行,5s后2号运输带自动起动,再过5s后3号运输带自动起动。
停机的顺序与起动的顺序刚好相反,即按了停止按钮I0.1后,先停3号运输带,5s后停2号运输带,再过5s停1号运输带。
PLC通过交流接触器KM1,KM2和KM3控制3台电动机M1,M2和M3。
图1-4是PLC的外部接线图。
图1-10中的波形图给出了程序设计的思路。
T37的常开触点与M0.1的常触点串联,控制Q0.1的线圈。
T38的常开触点与M0.0的常闭触点串联,控制Q0.2的线圈。
参考图1-7中的程序,根据图1-10中的波形图,设计出控制3条运输带的梯形图。
将程序下载到PLC后运行该程序。
用接在输入端子I0.0的小开关发出起动信号,观察Q0.0是否变为1状态,5s后Q0.1是否能自动变为1状态,再过5s后Q0.2是否能自动变为1状态。
用接在输入端子I0.1的小开关发出信号,观察Q0.2是否马上变为0状态,5s后Q0.1是否能自动变为0状态,再过5s后Q0.0是否能自动变为0状态。
1.3I/O分配表
表1-1两条运输带的I/O分配表
I/O分配表
I
O
启动按钮I0.0-SB1
1号电动机Q0.0-KM1
停止按钮I0.1-SB2
2号电动机Q0.1-KM2
表1-2三条运输带的I/O分配表
I/O分配表
I
O
启动按钮I0.0-SB1
1号电动机Q0.0-KM1
停止按钮I0.1-SB2
2号电动机Q0.1-KM2
3号电动机Q0.2-KM3
1.4I/O接线图
图1-3两条运输带的I/O接线图
图1-4三条运输带的I/O接线图
1.5功能图
图1-5两条运输带的顺序功能图图1-6三条运输带的顺序功能图
1.6梯形图
图1-7两条运输带的梯形图
图1-8三条运输带的梯形图
1.7波形图
图1-9两条运输带的波形图
图1-10三条运输带的波形图
1.8指令语句表
表1-3两条运输带的指令语句表
指令语句表
1
LD
I0.0
8
═
Q0.1
2
O
Q0.0
9
LD
I0.1
3
AN
T38
10
O
M0.0
4
═
Q0.0
11
AN
T38
5
TON
T37,50
12
═
M0.0
6
LD
T37
13
TON
T38,50
7
AN
M0.0
表1-4三条运输带的指令语句表
语句指令表
1
LD
SM0.1
24
A
T40
2
═
M0.0
25
═
M0.0
3
LD
M0.0
26
═
M0.5
4
A
I0.0
27
LD
M0.1
5
═
M0.1
28
O
M0.2
6
═
M0.0
29
O
M0.3
7
LD
M0.1
30
O
M0.4
8
A
T37
31
O
M0.5
9
═
M0.2
32
═
Q0.0
10
═
M0.1
33
LD
M0.2
11
LD
M0.2
34
O
M0.3
12
A
T38
35
O
M0.4
13
═
M0.3
36
═
Q0.1
14
═
M0.2
37
LD
M0.3
15
LD
M0.3
38
═
Q0.2
16
A
I0.1
39
LD
M0.1
17
═
M0.4
40
TON
T37,50
18
═
M0.3
41
LD
M0.2
19
LD
M0.4
42
TON
T38,50
20
A
T39
43
LD
M0.4
21
═
M0.5
44
TON
T39,50
22
═
M0.4
45
LD
M0.5
23
LD
M0.5
46
TON
T40,50
实训二异步电动机自耦减压起动控制
2.1实验目的
熟悉S7-200系列PLC的指令,以及将继电器控制电路转换为梯形图的方法。
2.2实验内容和控制要求
了解自耦减压起动电路的工作原理,以及将继电器控制电路转换为梯形图的方法。
在调试继电器控制电路转换的梯形图时,建议根据继电器控制系统的工作原理和工作过程,画出PLC有关输入,输出点的波形图,供调试时使用。
图2-4是自耦减压起动控制中PLC输入点,输出点的波形图。
如果有必要,还需要画出某些定时器,计数器和存储器位M的波形图,在调试时用程序状态功能或状态表示监控它们。
在编程软件中新建一个项目,将梯形图程序写入OB1,将程序下载到PLC后运行该程序。
接通I0.2对应的小开关,模拟热继电器FR常闭触点闭合。
用接在I0.0输入端的小开关模拟起动按钮,将开关接通后马上断开,观察Q0.1和Q0.2是否同时变为1状态,8s后Q0.1是否自动变为0状态。
再过7s后,Q0.2应变为0状态,同时Q0.3变为1状态。
用接在I0.1输入端的开关模拟停止按钮,将开关接通后马上断开,观察Q0.3是否变为0状态。
梯形图是否正确,用程序状态或状态表等监控功能来监控程序的运行情况,找到出错的原因,修改程序后继续调试,直到合乎图2-4中的波形图。
在电动机起动之前或起动,运行过程中断开I0.2对应的小开关的触点,观察PLC外接的FR的常闭触点的作用。
2.3I/O分配表
表2-1异步电动机自耦减压起动控制的I/O分配表
I/O分配表
I
O
启动按钮I0.0-SB1
Q0.1-KM1
停止按钮I0.1-SB2
Q0.2-KM2
Q0.3-KM3
2.4I/O接线图
图2-1异步电动机自耦减压起动控制的I/O接线图
2.5功能图
图2-2异步电动机自耦减压起动控制的顺序功能图
2.6梯形图
图2-3异步电动机自耦减压起动控制的梯形图
2.7波形图
图2-4异步电动机自耦减压起动控制的波形图
2.8指令语句表
表2-2异步电动机自耦减压起动控制的语句指令表
语句指令表
1
LD
SM0.1
15
LD
M0.3
2
═
M0.0
16
A
I0.1
3
LD
M0.0
17
═
M0.0
4
A
I0.0
18
═
M0.3
5
═
M0.1
19
LD
M0.1
6
═
M0.0
20
═
Q0.1
7
LD
M0.1
21
TON
T37,80
8
A
T37
22
LD
M0.1
9
═
M0.2
23
O
M0.2
10
═
M0.1
24
═
Q0.2
11
LD
M0.2
25
LD
M0.2
12
A
T38
26
═
T38,70
13
═
M0.3
27
LD
M0.3
14
═
M0.2
28
═
Q0.3
实训三液体混合控制
3.1实训目的
熟悉以转换为中心的顺序控制程序的设计和调试方法。
3.2实训内容和控制要求
3.2.1液体混合控制程序的调试A
将图3-6中的液体混合控制系统的梯形图程序写入PLC,根据图3-4中的顺序功能图,从初始步开始调试。
用状态表监视T37,T38,C0,C1,VW10和VW12的当前值,格式均为“有符号”,在VW10和VW12中写入C0和C1的设定值。
为了节约调试的时间,C0和C1的设定值不要太大。
用二进制格式监视MB0,QB0,IB0和M1.0。
调试步骤简述如下:
1)用I0.0对应的小开关发出信号后,观察M0.1,M0.3和连续标志M1.0是否变为1状态。
2)步M0.1为活动步时,用I0.3对应的小开关模拟计量泵的计数脉冲信号,在C0的当前值等于设定值时,观察是否能转换到下一步,C0的当前值是否被复位为0。
3)步M0.3为活动步时,用I0.4对应的小开关模拟计量泵的计数脉冲信号,在C1的当前值等于设定值时,观察是否能转换到下一步,C1的当前值是否被复位为0。
4)M0.2和M0.4均为活动步时,观察是否能转换到步M0.5。
5)步M0.5为活动步时,观察经过T37的延时后,是否能自动转换到步M0.6。
6)步M0.6为活动步时,用外接的小开关使下限位信号I0.1为1状态,观察是否能转换到步M0.7。
7)步M0.7为活动步,且T38的定时时间到时,观察是否能返回步M0.1和步M0.3。
8)在运行过程中,用I0.2对应的小开关产生停止信号,观察连续标志M1.0是否变为0状态,在步M0.7结束时(T38的定时时间到)是否能返回初始步。
3.2.2液体混合控制程序的调试B
图3-5是图3-1中的液体混合控制系统的顺序功能图,根据它编写出梯形图程序。
在编程软件中创建一个项目,将梯形图程序写入OB1,仔细检查和编译后下载到PLC。
用状态表监视T37~T40和C0的当前值,格式为“有符号”。
用二进制制格式监视IB0,QB0,MB0和M1.0。
调试步骤简述如下:
1)进入初始步M0.0后,观察C0是否被复位,其当前值是否为0.
2)在初始步用I0.0对应的小开关发出起动信号,观察M0.1和M0.4是否同时变为1状态。
3)用I0.1和I0.3对应的小开关模拟上限位开关信号,观察是否能转换到下一步。
4)M0.2或M0.5为活动步时,观察在定时器设定的时间到时,是否能转换到下一步。
5)M0.3和M0.6同时为活动步时,观察是否能转换到步M0.7,C0的当前值是否加1。
6)步M0.7为活动步时,观察在T39的定时时间到时,是否能转换到步M1.0。
7)步M1.0为活动步时,观察在T40的定时时间到时,是否能返回步M0.1和步M0.4。
8)继续步骤3~步骤7的操作,在步M1.0,当C0的当前值小于3且T40的定时时间到时,观察是否能返回步M0.1和步M0.4。
当C0的当前值等于设定值3且T40的定时时间到时,观察是否能返回初始步。
图3-1液体混合控制程序A的I/O接线图
3.3I/O分配表
表3-1液体混合控制程序A的I/O分配表
I/O分配表
I
O
启动按钮I0.0-SB1
1号电动机Q0.0-KM1
停止按钮I0.1-SB2
2号电动机Q0.1-KM2
表3-2液体混合控制程序B的I/O分配表
I/O分配表
I
O
启动按钮I0.0-SB1
Q0.0-KM1
I0.1-上限位
Q0.1-KM2
I0.3-上限位
Q0.2-KM3
Q0.3-KM4
Q0.4-KM5
Q0.5-KM6
3.4I/O接线图
图3-2液体混合控制程序A的I/O接线图
图3-3液体混合控制程序B的I/O接线图
3.5功能图
图3-4液体混合控制程序A的顺序功能图
图3-5液体混合控制程序B的顺序功能图
3.6梯形图
图3-6液体混合控制程序A的梯形图
图3-7液体混合控制程序B的梯形图
3.7指令语句表
表3-3液体混合控制程序A的指令语句表
语句指令表
1
LD
I0.0
32
═
M0.6
2
O
M1.0
33
LD
M0.7
3
AN
I0.2
34
A
T38
4
═
M1.0
35
A
M1.0
5
LD
SM0.1
36
═
M0.1
6
═
M0.0
37
═
M0.3
7
LD
M0.0
38
═
M0.7
8
A
I0.0
39
LD
M0.7
9
═
M0.1
40
A
T38
10
═
M0.3
41
AN
M1.0
11
═
M0.0
42
═
M0.0
12
LD
M0.1
43
═
M0.7
13
A
C0
44
LD
M0.1
14
═
M0.2
45
═
Q0.0
15
═
M0.1
46
LD
M0.3
16
LD
M0.2
47
═
Q0.1
17
A
M0.4
48
LD
M0.5
18
═
M0.5
49
═
Q0.2
19
═
M0.2
50
TON
T37,600
20
═
M0.4
51
LD
M0.6
21
LD
M0.3
52
O
M0.7
22
A
C1
53
═
Q0.3
23
═
M0.4
54
LD
M0.7
24
═
M0.3
55
TON
T38,100
25
LD
M0.5
56
LD
I0.3
26
A
T37
57
LD
M0.2
27
═
M0.6
58
CTU
C0,VW10
28
═
M0.5
59
LD
I0.4
29
LD
M0.6
60
LD
M0.4
30
A
I0.1
61
CTU
C1,VW12
31
═
M0.7
表3-4液体混合控制程序B的指令语句表
语句指令表
1
LD
SM0.1
32
═
M0.6
2
═
M0.0
33
LD
M0.7
3
LD
M0.0
34
A
T39
4
A
I0.0
35
═
M1.0
5
═
M0.1
36
═
M0.7
6
═
M0.0
37
LD
M1.0
7
LD
M0.0
38
A
C0
8
A
I0.0
39
A
T40
9
═
M0.4
40
═
M0.0
10
═
M0.0
41
═
M1.0
11
LD
M0.1
42
LD
M1.0
12
A
I0.1
43
AN
C0
13
═
M0.2
44
A
T40
14
═
M0.1
45
═
M0.1
15
LD
M0.4
46
═
M1.0
16
A
I0.3
47
LD
M0.1
17
═
M0.5
48
═
Q0.0
18
═
M0.4
49
LD
M0.4
19
LD
M0.2
50
═
Q0.1
20
A
T37
51
LD
M0.2
21
═
M0.3
52
═
Q0.2
22
═
M0.2
53
TON
T37,50
23
LD
M0.5
54
LD
M0.5
24
A
T38
55
═
Q0.3
25
═
M0.6
56
TON
T38,50
26
═
M0.5
57
LD
M0.6
27
LD
M0.3
58
LD
M0.0
28
A
M0.6
59
CTU
C0,3
29
A
═1
60
LD
M0.7
30
═
M0.7
61
═
Q0.4
31
═
M0.3
62
TON
T39,50
实训总结
经过了为期一周的时间,我们小组的同学共同努力,完成了这次课程设计。
在这一次课程设计中让我更加深入的学习了有关PLC方面的知识,使我感触良多,收获颇丰。
在这次PLC实训中我们学习了画图等一些与自己专业相关联的知识。
我在实训的过程中,让我学到了许多东西,其中最主要的是PLC设计方法与应用。
设计步骤是首先是我们要弄清楚设备的顺序运作,然后结合PLC知识在图纸上画出顺序功能图,将顺序功能图转变为梯形图,之后利用PLC软件编程。
在这次课程实训中,我较好的完成了既定任务。
还有不时去帮助其他同学解决一些问题。
PLC实训让我更加深入的了解了PLC顺序功能图、梯形图、语句指令表、外部接线图,也让我更加了解了关于PLC设计原理与方法。
按我的想法来看,有很多设计理念来源于实际,从中找出最适合的设计方法。
总之,这次通过这次设计实践。
我学会了PLC的基本编程方法,对PLC的工作原理和使用方法也有了更深刻的理解。
在对理论的运用中,提高了我们的工程素质,在没有做实践设计以前,我们对知道的撑握都是思想上的,对一些细节不加重视,当我们把自己想出来的程序用到PLC中的时候,问题出现了,不是不能运行,就是运行的结果和要求的结果不相符合。
能过解决一个个在调试中出现的问题,我们对PLC的理解得到加强,看到了实践与理论的差距。
通过这次PLC设计,我们的合作意识得到加强。
合作能力得到提高。
上大学后,很多同学都没有过深入的交流,在设计的过程中,我们用了分工与合作的方式,每个人互责一定的部分,同时在一定的阶段共同讨论,以解决分工中个人不能解决的问题,在交流中大家积极发言,和提出意见,同时我们还向别的同学请教。
在此过程中,每个人都想自己的方案得到实现,积极向同学说明自己的想法。
能过比较选出最好的方案。
而且通过这次实训过程也提高了我们的表过能力。
为期一周的实训就这样结束了,这次实训让我明白了作为一名设计师的辛苦。
此次的实训是以班级为主体,以小组为单位而开展的一次综合的实践,老师也给予我们足够的空间让我们完成此次的实训,这让我觉得压力减轻了不少。
这次的实训从程序上面看起来很复杂,我们组进行了任务性分工,一下子就变得简单化了。
自己选择了画图,在老师的指导下,自己慢慢开始学会了如何用相应的软件去画图,并且也让我更好地理解了PLC各种图的含义,从而更好的应用到实训中。
PLC实训让我收获了很多,给我弥补了很多我欠缺的知识和原先没有学习的知识以及巩固了之前所学的知识点等等。
在今后的学习过程中,我要更加努力的学习自己的专业知识,多多与同学和老师交流,相信在以后的学习里面会有所作用,并且通过这次实训让我深刻的理解了团队精神的重要所在。
在此,我要很感谢刘光辉老师的指导和同学的帮助,因为他们使我的设计完成得更加顺利。
通过这实训让我受益匪浅,本次实训脱离不了集体的力量,遇到问题和同学互相讨论交流。
多和同学讨论。
我们在做实训项目的过程中要不停的讨论问题,这样,我们组员可以尽可能的统一思想,这样就不会使在做的过程中没有方向,并且这样也是为了方便最后设计和在一起。
讨论不仅是一些思想的问题,还可以深入的讨论一些技术上的问题,这样可以使自己的处理问题要快一些,少走弯路。
多改变自己设计的方法,在设计的过程中最好要不停的改善自己解决问题的方法,这样可以方便自己解决问题。
总之,这次的实训给予了我不同的学习方法和体验,让我深切的认识到实践的重要性。
在以后的学习过程中,我会更加注重自己的操作能力和应变能力,多与这个社会进行接触,让自己更早适应这个陌生的环境,相信在不久的将来,可以打造一片属于自己的天地。
参考文献
[1]SIEMENSAG.SIMATICS7-200ProgrammableControllerSystem
Manual.2007.
[2]西门子(中国)有限公司.S7-200可编程序控制器系统手册.2007.
[3]西门子(中国)有限公司.S7-200可编程序控制器系统手册.2006.
[4]廖长初.PLC编程及应用[M].3版.北京:
机械工业出版社,2008.
[5]廖长初.S7-200PLC编程及应用[M].北京:
机械工业出版社,2007.
[6]廖长初.S7-300/400PLC应用技术[M].2版.北京:
机械工业出版社,
2008.
[7]廖长初,陈晓东.西门子人机界面(触摸屏)组态与应用技术[M].2
版.北京:
机械工业出版社,2008.
[8]廖长初.PLC基础及应用[M].2版.北京:
机械工业出版社,2007.
[9]廖长初.FX系列PLC编程及应用[M].北京:
机械工业出版社,2005.
[10]阳宪惠.工业数据通信与控制网络[M].北京:
清华大学出版社,
2003.
[11]徐昌荣.对国产PLC产业化的几点思考[J].自动化博览.2005
(3):
18-20.
致谢词
在我的实训完成之际,我要向为我提供过帮助的刘光辉老师表达我最真挚的感谢,在论文的写作过程中,他无比耐心,无私无求的给予我持续的帮助,没有刘老师的帮助我无法顺利完成此次的课程设计。
还有我的同窗,朋友们,是他们用最真挚的情感和最实际的援助,帮我渡过了一处处的难关。
感谢宿舍好友王珍珍,同我一块探讨可行性研究的内容,还有同组的其他同学,也一并感谢,谢谢你们。
在这次设计里我学会了好多东西,也学会了感恩其他同学和孜孜不倦的老师,让我明白了人多力量大的团队精神。