第五章并条.docx
《第五章并条.docx》由会员分享,可在线阅读,更多相关《第五章并条.docx(21页珍藏版)》请在冰豆网上搜索。
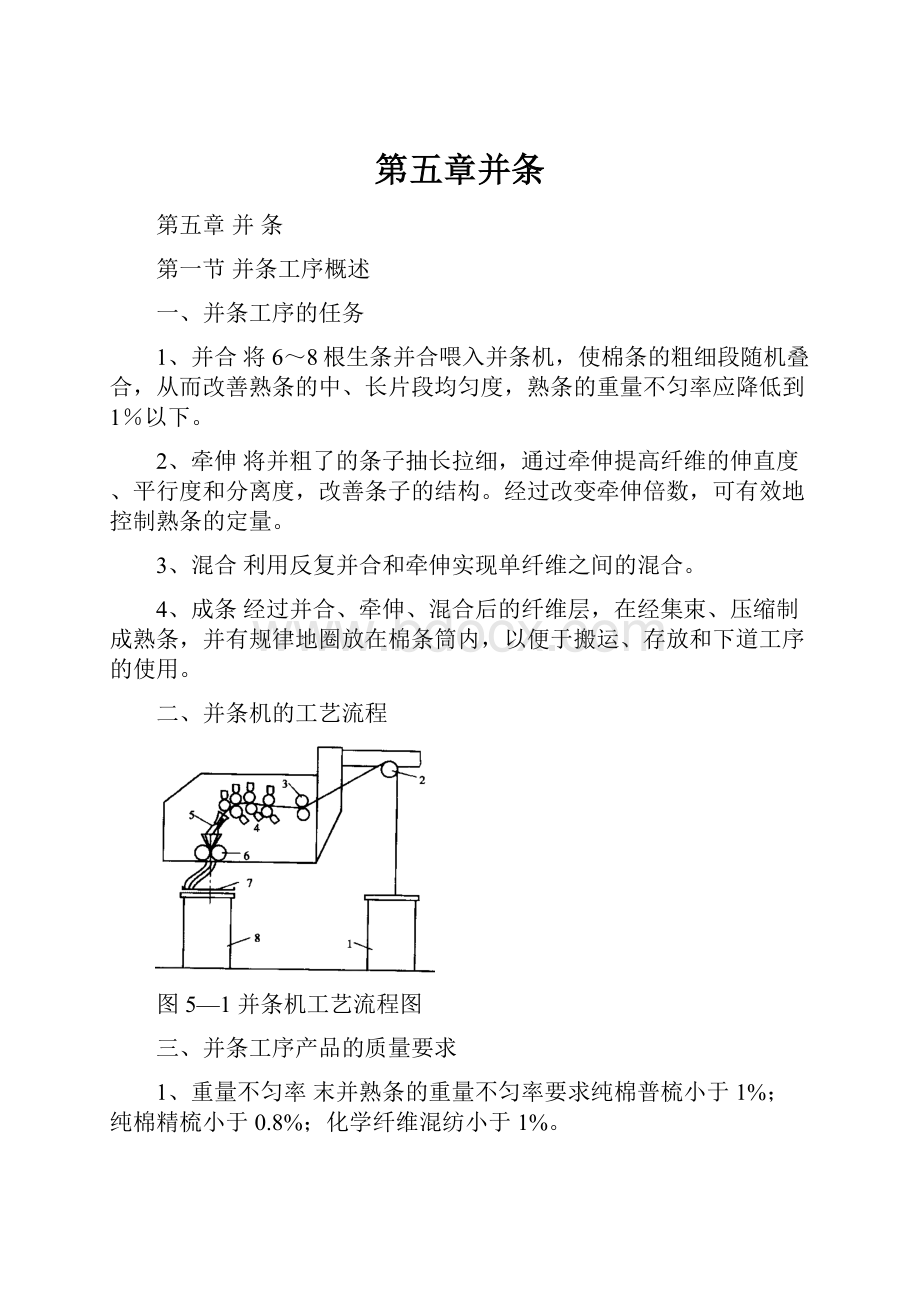
第五章并条
第五章并条
第一节并条工序概述
一、并条工序的任务
1、并合将6~8根生条并合喂入并条机,使棉条的粗细段随机叠合,从而改善熟条的中、长片段均匀度,熟条的重量不匀率应降低到1%以下。
2、牵伸将并粗了的条子抽长拉细,通过牵伸提高纤维的伸直度、平行度和分离度,改善条子的结构。
经过改变牵伸倍数,可有效地控制熟条的定量。
3、混合利用反复并合和牵伸实现单纤维之间的混合。
4、成条经过并合、牵伸、混合后的纤维层,在经集束、压缩制成熟条,并有规律地圈放在棉条筒内,以便于搬运、存放和下道工序的使用。
二、并条机的工艺流程
图5—1并条机工艺流程图
三、并条工序产品的质量要求
1、重量不匀率末并熟条的重量不匀率要求纯棉普梳小于1%;纯棉精梳小于0.8%;化学纤维混纺小于1%。
2、重量偏差单机台熟条干重的差异率控制在±1%左右,全机台熟条干重的差异率可控制在±0.5%左右。
3、条干不匀率
纱线类别
萨氏条干不匀率(%)
乌斯特CV值(%)
细特纱
20
3.5~3.6
中粗特纱
22
4.1~4.3
化学纤维纱
15
3.2~3.8
第二节条子的并合
一、并合的均匀作用
将多个同一品种的棉条或不同品种的棉条平行地喂入牵伸装置,经牵伸后合并为一体的过程,称为并合。
图中
(1)最粗与最细相并合,均匀效果最好;图中
(2)最粗与粗细适中相并合,图中(3)最细与粗细适中相并合,虽然没有图中
(1)理想,但也改善了棉条的均匀度;图中(4)最粗与最粗、最细与最细相并合,棉条的均匀度虽未得到改善,但也没有恶化。
棉条的并合数越多粗段与粗段、细段与细段相遇的机会就越少,其他情况相遇的机会就越多,因此,改善产品均匀度的效果就越好。
图5—2并合的均匀效果
根据数理统计原理,当n根条子并合时,并合后的不匀率为:
式中:
——并合前各根喂入条子的不匀率,%;
C——并合后条子的不匀率,%。
上式也可写为:
,据此式绘制n根条子不匀率变化曲线。
从图中可看出:
1、并合根数越多,并合后须条不匀率越低。
2、当并合根数较小时,增加根数,不匀率降低程度大;当并合根数较多时,不匀率降低程度小。
而且当根数达到一定数值后,不匀率的降低已很小,均匀效果使不显著。
3、棉纺中一般都采用两道并合,当生条重量不匀率
=4%时,若要熟条重量不匀率达到
=1%,那么并合总根数n=16,两道并条采用4×4相并合即可满足要求。
但考虑到牵伸和机台间差异,两道并条一般采用6×6(36)根或8×8(64)根并合。
图5—3并合效果与并合根数的关系
二、不匀率类型及改善途径
(一)重量不匀率的种类:
CZ2=CN2+CW2
内不匀CN:
同一眼或同一卷装内单位长度重量之间的不匀。
它反应棉条的重量随时间变化关系。
外不匀CW:
不同卷装的棉条各取一段称重计算出的不匀。
它反应不同卷装之间的重量差异。
总不匀CZ:
对不同卷装连续取样,分段称重后计算得出的不匀。
它是内不匀及外不匀综合反应。
内、外不匀率有一定的联系,但又不是完全相关的。
当内不匀率大时,外不匀率一般也比较大;当内不匀率小时,外不匀率却不一定小。
(二)改善棉条重量不匀率的途径
1、轻重条搭配
2、积极式喂入
3、断条自停
4、使用自调匀整
第三节罗拉牵伸的基本理论
一、罗拉牵伸的概念
(一)牵伸的条件
对于罗拉牵伸来说,实现牵伸的条件有以下三个:
1、须条上必须具有积极握持的两点,且两握持点之间有一定的距离;
2、积极握持的两点必须进行相对运动,输出端的线速度大于喂入端的线速度;
3、握持点上必须具有一定的握持力。
(二)实际牵伸与机械牵伸
牵伸倍数是须条拉细的程度,通常用
来表示。
式中:
、
——牵伸前、后单位长度须条的长度,m;
图5-4牵伸作用示意图
、
——牵伸前、后单位长度须条的重量,g/m;
、
——牵伸前、后须条的持数,tex。
若牵伸过程中罗拉与须条间无滑溜,即
,则有:
式中:
、
——喂入罗拉和输出罗拉的表面速度。
牵伸倍数
称为机械牵伸倍数或计算牵伸倍数。
则由
所得的牵伸倍数
不等于
。
称为实际牵伸倍数。
实际牵伸倍数与机械牵伸倍数之比称为牵伸效率
,即:
在纺纱上艺中,常使用一个经验数值——牵伸配合率,它相当于牵伸效率的倒数
。
(三)总牵伸倍数与部分牵伸倍数
各部分牵伸倍数分别是:
E1=v1/v2,E2=v2/v3,E3=v3/v4,总牵伸倍数E=v1/v4。
将三个部分牵伸倍数连乘,则:
E1×E2×E3=(v1/v2)×(v2/v3)×(v3/v4)=v1/v4=E
即总牵伸倍数等于各部分牵伸倍数的乘积。
二、牵伸过程中纤维的运动
在牵伸过程中,从熟条到成纱的产品条干均匀度总是变差的。
如熟条的条干CV%一般为3%-6%;粗纱的条干CV%一般为8%-9%;细纱条干CV%一般为13%-18%。
为会么在牵伸过程中条干会变差呢?
实践证明是由牵伸造成的。
图5-5牵伸后纤维的正常移距
(一)牵伸后纤维的正常移距
为了研究牵伸区内纤维的运动需作以下假设:
1、所有纤维都是等长的;2、所有纤维都是伸直平行的;3、牵伸区内的纤维只有两种运动状态,即快速纤维与慢速纤维。
如图,假若纤维头端都在前钳口变速,a0为牵伸前纤维头端距离,a1为牵伸后纤维头端的距离。
当纤维A头端到达前钳口时以快速运动,当纤维B到达前钳所用的时间t为:
t=a0/v2
在t时间内,A纤维前进的距离a为:
a=v1×t=E×a0
由此可知:
须条牵伸后与牵伸前相比,纤维头端拉长了E倍,因此按照此规律牵伸,牵伸前后的均匀度没有变化。
(二)移距偏差
设1-1截面为A纤维头端的变速点,2-2为B纤维头端的变速点,X为两变速截面的距离。
1、当A纤维开始变速时,B纤维距变速点的距离为:
X+a0;
2、B纤维到达2-2的时间为:
t=(X+a0)/V2;
3、在t时间内,A纤维前进的距离为:
V1×t=a+X;
4、牵伸后纤维头端距离为:
a=V1(X+a0)/V2-X=Ea0+X(E-1)
X(E-1)为移距偏差。
如图所须条牵伸后在A与B纤维之间形成明显的细节。
移距偏差越大,牵伸后形成的细节越长。
如果1-1为B纤维的变速截面、2-2为A纤维的变速点,则牵伸后纤维的头端移距为:
a=V1(X+a0)/V2-X=Ea0-X(E-1)
按此种模式,在A与B纤维之间形成粗节。
由此可知:
(1)X(E-1)越大,则牵伸后产生的粗细节越明显;
(2)X越大,则移距偏差越大;(3)E越大,移距偏差越大。
因此提高纱条的均匀度的思路是:
尽可能使X及E小。
图5—6纤维头端在不同界面变速的移距图5—8简单罗拉牵伸区内纤维变速点分布
(三)牵伸区内纤维变速点分布求
1、牵伸内纤维变速点的分布在牵伸过程中,纤维头端的变速界面xi(变速点至前钳口距离)有大有小,各个变速界面上变速纤维的数量也不相等,因而形成一种分布,即为纤维变速点分布(曲线1)。
2、牵伸内纤维变速点的分布状态的影响因素
(1)同样长度的纤维其头端也不在同一位置变速,呈现一种分布。
(2)长纤维变速点分布较集中且向前钳口靠近(曲线2);短纤维变速点分布较分散且距前钳口较远(曲线3)。
(3)牵伸形式不同,纤维变速点的分布曲线不同。
(4)牵伸工艺不同,纤维变速点分布曲线不同。
为了获得均匀的产品应使纤维头端变速点分布尽可能向前钳口处集中而稳定。
三、牵伸区内纤维数量的分布
(一)牵伸区内纤维的分类
1、按握持钳口分:
前纤维、后纤维
2、按速度分:
快速纤维、慢速纤维、浮游纤维
(二)纤维的数量分布
1、牵伸区内纤维的数量分布2、前纤维的数量分布
3、后纤维的数量分布4、快速纤维的数分布
5、慢速纤维的数量分布
(三)影响牵伸区内纤维数量分布的因素
1、牵伸倍数2、罗拉隔距
图5-9简单罗拉牵伸区纤维数量分布
四、牵伸区内须条摩擦力界分布
纤维在牵伸过程中的运动决定于牵伸过程中作用于纤维上的外力。
(一)定义:
在牵伸区中,纤维与纤维间、纤维与牵伸装置部件之间的摩擦力所作用的空间称为摩擦力界。
(二)影响摩擦力界的因素
1、加压量:
加压大,摩擦力界的峰值增高、范围扩展;
2、罗拉直径:
直径增大,峰值降低、范围扩展;
3、棉条定量增加:
棉条定量增大,峰值降低、范围扩展;
(三)牵伸区内的摩擦力界分布
在一个牵伸区中,两对罗拉各自形成的摩擦力界连贯起来,就组成了简单罗拉牵伸区中整个摩擦力界分布。
中部摩擦力界的强度较弱,所保持的只是纤维间的抱合力,因而控制纤维的能力较差,致使较短的纤维变速点不稳定,恶化产品条干。
图5—10罗拉钳口下摩擦力界分布图5—11简单罗拉牵伸区摩擦力界分布
五、浮游纤维的变速条件及牵伸过程中纤维运动的控制
(一)浮游纤维的变速条件
1、概念:
牵伸区内任意一根浮游纤维都被周围的快速纤维和慢速纤维所包围。
快速纤维对浮游纤维的摩擦力fa称为引导力。
慢速纤维对浮游纤维的摩擦力fv称为控制力
2、影响控制力与引导力的因素
(1)牵伸区内的纤维数量分布
(2)牵伸区内的摩擦力界分布
3、浮游纤维的变速条件:
fa>fv
(二)牵伸过程中纤维运动的控制
1、牵伸区内摩擦力界布置的要求
对后钳口和前钳口的摩擦力界分布要求如下:
(1)后钳口的摩擦力界应尽量向前扩展,并使其向前逐渐减弱,以便加强慢速纤维对浮游纤维的控制,同时又能让比例逐渐加大的快速纤维从须条中顺利滑出,而不影响其他纤维的运动。
(2)前钳口摩擦力界在纵向分布的状态应高而狭,以便稳定地发挥其对浮游纤维的引导作用,保证纤维变速点分布向前钳口附近集中且相对稳定,对整个牵伸须条来说,牵伸力应有适当数值,并保持稳定。
2、附加摩擦力界的应用
根据摩擦力界分布的理论要求,仅有两对罗拉组成的摩擦力界分布是不能满足要求的。
在牵伸区域中,由于两对罗拉之间有一定的隔距,且隔距主要适应加工纤维长度的需要,因此由两对罗拉所建立的摩擦力界,其扩展到中部时强度已经很弱,甚至在中部很长一段距离上,摩擦力界主要依靠纤维之间的抱合力来维持,因此引导力和控制力不稳定,波动较大。
此时,浮游纤维的运动很难得到控制,变速点分布分散且不稳定。
因此,需要在牵伸区中增设附加摩擦力界,以加强牵伸区中部摩擦力界强度,达到既控制浮游纤维运动,又不阻碍快速纤维运动的作用。
目前,常用的附加摩擦力界机构为胶圈、压力棒、轻质辊、多皮辊曲线牵伸形式等,改善对纤维运动的控制。
六、牵伸过程中罗拉钳口的受力
(一)概念
1、牵伸力:
牵伸过程中,以前罗拉速度运动的快速纤维从周围的慢速纤维中抽出时,所受到的摩擦阻力的总和,称为牵伸力。
2、握持力:
罗拉钳口对须条作用力。
3、正常牵伸的条件:
握持力大于牵伸力。
(二)罗拉钳口的受力分析
设前、后罗拉作对须条的摩擦力F1、F2,前、后皮辊对须条的摩擦力f1、f2;牵伸力为T,如图所示:
图5—13罗拉钳口下须条受力
则须条不在前钳口下打滑的条件是:
F1-f2>T
须条不在前钳口下打滑的条件是:
T>F2-f2
由以上分析可知,前后钳口的实际握持力分别为(F1-f1)及(F2+f2)。
因此欲使前后钳口同样达到与牵伸力相适应的握持力,则F1>F2,故前皮辊上的压力P1应大于后皮辊上的压力P2。
(三)影响握持力和牵伸力的因素
1、影响握持力的因素
(1)皮辊加压;
(2)纤维与罗拉间的摩擦系数;(3)皮辊与罗拉的状态:
皮辊的硬度、罗拉表面沟槽的形态及槽数、皮辊磨损中凹、皮辊芯子缺油而回转不灵活一。
2、影响牵伸力的因素
(1)牵伸倍数
当喂入棉条的线密度一定时,随牵伸倍数的增大,牵伸力先增大后减小。
棉条临界牵伸倍数Ec=1.2~1.3。
当输出棉条线密度维持不变,喂入棉条的线密度增大,牵伸倍数增大,牵伸力增大。
(2)罗拉握持距:
罗拉隔距增大,牵伸力减小。
(3)皮辊加压:
牵伸区中后钳口皮辊压力增大,后摩擦力界强度、范围增大,牵伸力也随之增大。
(4)附加摩擦力界:
由于曲线牵伸机构的后摩擦力界扩展,因此,即使后钳口处压力与简单罗拉牵伸相同,牵伸力也较大。
如牵伸机构中采用集合器,压力棒等都会使牵伸区内附加摩擦力界增大,牵伸力增大。
(5)喂入棉条的厚度和密度:
当喂入棉条厚度增大时,摩擦力界分布长度扩展,牵伸力变大。
实验证明,当其他条件不变时,两根棉条并列喂入,其牵伸力为单根棉条的两倍;两根棉条上下重叠喂入,牵伸力为单根棉条的3.2倍。
(6)纤维性质等的影响:
纤维长度长,细度细,则同样号数的须条的截面中纤维根数多,且纤维在较大的长度上受到摩擦阻力,所以牵伸力大,同时接触的纤维数量较多,抱合力一般较大,因而增加了牵伸力。
此外,纤维的平行伸直度愈差,纤维相互交叉纠缠摩擦力较大,牵伸力增大。
(7)温湿度:
温湿度与牵伸力密切相关。
温度增高时,纤维间摩擦系数小,牵伸力降低。
一般情况下,相对湿度增大,纤维摩擦系数增加,但相对湿度在34%~76%时,相对湿度增加,牵伸过程中纤维易于平行伸直,牵伸力反而降低。
图5—14牵伸倍数与牵伸力图5—15罗拉隔距与牵伸力
七、牵伸过程中纤维的伸直平行作用
通过牵伸可以提高须条中纤维的伸直平行度,改善须条中纤维的弯钩状态,提高成纱质量。
(一)伸直度与平行度
如图5—16所示,
为纤维在空间的真实长度(原始长度),
为
向任意平面
的最大投影长度,则纤维的伸直度(伸直系数)
及平行度
为:
=
=
图5—16单纤维伸直度与平行度
牵伸过程中纤维的伸直过程,就是纤维自身各部分间发生相对运动的过程。
在须条中纤维的形态分为三类,即无弯钩的卷曲纤维、前弯钩纤维和后弯钩纤维。
通常将弯钩纤维的较长部分称为“主体”,较短部分称为“弯钩”,弯钩与主体相连处称为弯曲点。
弯钩的消除过程,即弯钩纤维的伸直过程,因此应使弯钩和主体产生相对运动,否则不能消除弯钩。
弯钩纤维能否伸直,必须具备三个条件,即弯钩与主体部分必须有相对运动即速度差;伸直延续时间即速度差必须保持一定的时间;作用力即弯钩纤维所受到的引导力和控制力应相适应。
(二)纤维伸直过程的延续时间
图5—17纤维的伸直效果
(三)影响纤维伸直平行效果的主要因素
实践证明,影响纤维伸直平行效果的主要因素有牵伸倍数、牵伸分配、牵伸型式、罗拉握持距和罗拉加压及工艺道数等。
1、牵伸倍数及牵伸分配牵伸倍数的大小对于弯钩纤维的伸直效果有直接关系。
弯钩纤维的伸直度可以用伸直系数来表示:
=主体部分的长度/纤维的实际长度
图5—18前弯钩纤维伸直效果图5—19后弯钩纤维伸直效果
由以上分析可见,牵伸对伸直后弯钩有利,且牵伸倍数越大,对后弯钩纤维的伸直效果越好;而对于前弯钩纤维,伸直效果仅在牵伸倍数较小(E<3)时,才有一定的伸直作用。
2、牵伸型式不同的牵伸型式,其牵伸区具有不同的摩擦力界分布,对须条牵伸能力和弯钩伸直作用不同。
曲线牵伸和压力棒牵伸,由于加强了牵伸区中后部的摩擦力界,对纤维的控制力加强,且主牵伸区牵伸倍数增大,对纤维伸直作用较好。
3、工艺道数由于细纱机是伸直纤维的最后一道工序,且牵伸倍数最大,有利于消除后弯钩,因此为了使喂入细纱机的粗纱中后弯钩纤维为主,在普梳纺纱工艺中,梳棉与细纱之间的工艺道数应遵循“奇数原则”,这样有利于弯钩的伸直。
第四节并条机的牵伸型式及牵伸工艺
一、并条机的牵伸型式
(一)三上四下曲线牵伸
(二)压力棒曲线牵伸
1、下压式压力棒
2、上托式压力棒
图5—20三上四下曲线牵伸图5—21压力棒曲线牵伸
3、压力棒曲线牵伸的特点
(1)由于压力棒的存在,加强了主牵伸区中后部摩擦力界,使纤维变速点向前钳口靠近且集中。
(2)由于压力棒可以调节,容易做到须条沿前罗拉握持点切线喂入,有利于高速。
(3)适应性强,适纺纤维长度约为25—80mm。
(4)压力棒对须条的法向压力具有自调作用,它相当于一个弹性钳口的作用。
图5—23三上三下压力棒曲线牵伸
4、三上三下、三上三下附导向辊压力棒曲线牵伸
5、四上四下附导向辊压力棒曲线牵伸
(三)多皮辊曲线牵伸
1、五上三下曲线牵伸
2、五上四下曲线牵伸
图5-24FA311型并条机的牵伸型式
图5—25五上三下并条机牵伸型式图5—26五上四下并条机牵伸型式
二、并条机的牵伸工艺
(一)并条机的工艺道数
并条工艺道数确定的依据是:
由牵伸过程中纤维的伸直理论可知,牵伸倍数越大,对伸直后弯钩的效果越好;因细纱机的牵伸倍数最大,应保证喂入细纱机的纤维弯钩为后弯钩。
根据这一理论,从梳棉到细纱的工序道数应为“奇数”;即并条机为二道。
(二)并条机的速度
确定速度时应考虑以下因素:
1、并条机的机型;2、所纺纤维的类型,如纺化纤时应比棉低10-20%;3、并条机产量供应;4、纺纱的质量要求。
(三)熟条定量
应根据纺纱特数、纺纱品种、设备情况等因素而定,一般为12-25克/5米。
见下表:
纺纱特数
定量(克/5米)
纺纱特数
定量(克/5米)
9以下
12-17
20-30
17-23
9-19
15-21
32以上
19-25
(四)牵伸倍数
1、总牵伸倍数根据经验一般为(1-1.15)×并合数
2、牵伸分配
(1)各牵伸区的牵伸分配:
方法是先确定后区牵伸倍数,根据总牵伸倍数计算前区牵伸倍数。
头道并条机的后区牵伸倍数偏大掌握,一般为1.7-2.0倍;原因是加大后区牵伸倍数,可使前区牵伸倍数减小,有于前弯钩纤维的伸直(因喂入头道并条机的大多为前弯钩纤维),前区一般为3倍左右。
二道并条机的后区牵伸倍数1.16-1.1倍,前区在7倍以上。
因喂入二道并条机的大多为后弯钩纤维。
(2)头二道并条机的牵伸分配有以下两种方法:
一是头道大于二道,称为倒牵伸;此种方式有利于熟条的条干均匀度,但对前弯钩的伸直不利。
二是头道小于二道,称为顺牵伸;此种方式有利于弯钩纤维的伸直,但对熟条的条干不利。
(五)罗拉握持距
1、罗拉握持的大小对牵伸的影响
(1)过大时,易出现牵伸波;
(2)过小时,须条在钳口中打滑。
2、握持距的确定
(1)纤维长度与性能;
(2)牵伸区内的摩擦力界大小;(3)须条的定量等。
前区:
S=LP+5-10mm
后区:
S=LP+10-14mm
(六)加压
三上三下压力棒加导向皮辊:
(118、294、314、294)×2