机械制造工艺课程设计凸轮杆机械加工工艺规程设计doc.docx
《机械制造工艺课程设计凸轮杆机械加工工艺规程设计doc.docx》由会员分享,可在线阅读,更多相关《机械制造工艺课程设计凸轮杆机械加工工艺规程设计doc.docx(20页珍藏版)》请在冰豆网上搜索。
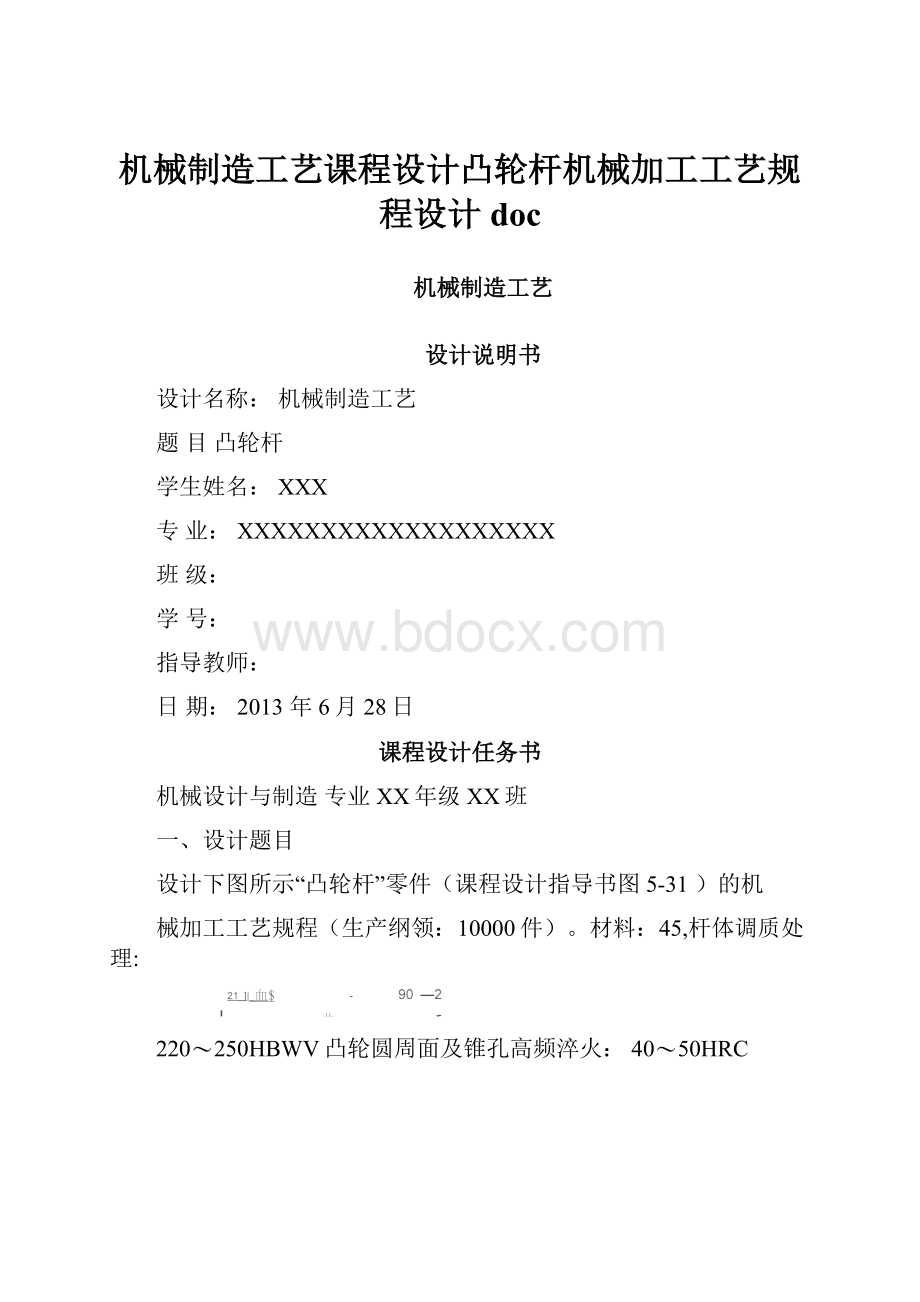
机械制造工艺课程设计凸轮杆机械加工工艺规程设计doc
机械制造工艺
设计说明书
设计名称:
机械制造工艺
题目凸轮杆
学生姓名:
XXX
专业:
XXXXXXXXXXXXXXXXXXX
班级:
学号:
指导教师:
日期:
2013年6月28日
课程设计任务书
机械设计与制造专业XX年级XX班
一、设计题目
设计下图所示“凸轮杆”零件(课程设计指导书图5-31)的机
械加工工艺规程(生产纲领:
10000件)。
材料:
45,杆体调质处理:
220〜250HBWV凸轮圆周面及锥孔高频淬火:
40〜50HRC
二、主要内容
1.绘制产品零件图,了解零件的结构特点和技术要求,对零件进行结构分析和工艺分析。
2.确定毛坯的种类及制造方法。
3•拟定零件的机械加工工艺过程,选择各工序的加工设备和工艺装备,确定各工序的加工余量和工序尺寸及其公差,计算各工序的切削用量和工时定额。
4.填写机械加工工艺过程卡片、机械加工工序卡片。
撰写设计说明书。
三、具体要求
产品零件图1
产品毛坯图1
机械加工工艺过程卡片1
机械加工工序卡片1
课程设计说明书1
四、进度安排
张
张
份
套
份
第一阶段:
绘制零件图,工艺卡片(2天)
第二阶段:
查阅资料,工艺方案比较,确定加工路线(2天)
第三阶段:
确定各工序的加工余量和工序尺寸,计算各工序的切
削用量和工时定额(3天)
第四阶段:
整理说明书,填写工艺卡片(3天)五、成绩评定
指导教师签名日期年—月—日
系主任审核日期年月日
序言
一、零件的分析6
1.1、零件的结构特点6
1.2、加工工艺性7
1.3、确定零件毛胚7
二、基准的选择8
2.1、有关基准的选择说明8
三、凸轮杆的材料、毛坯及热处理9
3.1、凸轮杆的材料9
3.2、凸轮杆毛坯9
3.3、凸轮杆的热处理9
四、制定加工工艺路线9
4.1凸轮杆加工工艺过程分析9
4.2、工艺路线的拟定1..0..
4.3、凸轮杆机械加工工艺过程卡1..2.
4.4、加工余量的确定1..2..
五、凸轮杆零件的检验1...7..
5.1、加工中的检验1...7..
5.2、加工后的检验1...7..
总结1...9
机械制造工艺及设备毕业设计是我们完成本专业教学计划的一个极为重要的实践性教学环节,是使我们综合运用所学过的基本课程,基本知识与基本技能去解决专业范围内的工程技术问题而进行的一次基本训练。
我们在完成课程设计的同时,也培养了我们正确使用技术资料,国家标准,有关手册,图册等工具书,进行设计计算,数据处理,编写技术文件等方面的工作能力,也为我们以后的工作打下坚实的基础,所以我们要认真对待这次综合能力运用的机会!
其主要目的是:
1.培养学生综合分析和解决本专业的一般工程问题的独立能力,拓宽和深化
所学的知识。
2.培养学生树立正确的设计思想,设计思维,掌握工程设计的一般程序,
规范和方法。
3.培养学生正确的使用技术知识,国家标准,有关手册,图册等工具书,进行设计计算,数据处理,编写技术文件等方面的工作能力和技巧。
4.培养学生进行调整研究,面向实际,面向生产,向工人和工程技术人员
学习的基本工作态度,工作作风和工作方法。
一、零件的分析
根据轴套类零件的功用和工作条件,其技术要求主要在以下方面:
⑴尺寸精度轴类零件的主要表面常为两类:
一类是与轴承的内圈配合的外圆轴颈,即支承轴颈,用于确定轴的位置并支承轴,尺寸精度要求较高,通常为IT5-IT7;另一类为与各类传动件配合的轴颈,即配合轴颈,其精度稍低,常为IT6-IT9。
⑵几何形状精度主要指轴颈表面、外圆锥面、锥孔等重要表面的圆度、
圆柱度。
其误差一般应限制在尺寸公差范围内,对于精密轴,需在零件图上另行
规定其几何形状精度。
⑶相互位置精度包括内、外表面、重要轴面的同轴度、圆的径向跳动、重要端面对轴心线的垂直度、端面间的平行度等。
⑷表面粗糙度轴的加工表面都有粗糙度的要求,一般根据加工的可能性和经济性来确定。
支承轴颈常为0.2~1.6卩m传动件配合轴颈为0.4~3.2卩m
⑸其他热处理及外观修饰等要求。
1.1、零件的结构特点
图1凸轮杆
如图所示零件是凸轮杆,它属于台阶型轴套类零件,由圆柱面、轴肩、螺纹、退刀槽等组成。
轴肩一般用来确定安装在其他零件的轴向位置,起定位作用。
螺纹用于安装各种锁紧螺母和调整螺母。
女口图所示的车床主轴零件的支撑轴颈A是装配基准,故对A段外圆的加工提出了很高的要求。
主轴的支撑轴颈、配合轴颈、锥孔、前端圆锥面及端面、锁紧螺纹等表面是轴的主要加工表面。
其中支撑轴颈本身的尺寸精度、几何形状精度、相互位置精度和表面粗糙度尤为重要。
1.2、加工工艺性
零件的技术要求不高,用车床、铣床和钻床就可以加工出来,精度要求一般是7到8级,而且表面粗糙度要求也不太高,是一个较好加工的零件。
1.3、确定零件毛胚
考虑到零件的经济性和综合性能要求,零件材料为45钢。
凸轮杆大毛坯图
如下:
•
一寸光阴不可轻
二、基准的选择
2.1、有关基准的选择说明
1、粗基准的选用原则
1、保证不加工表面与加工表面相互位置要求原则。
当有些不加工表面与加工表面之间有相互位置要求时,一般不选择加工表面作为粗基准。
2、保证各加工表面的加工余量合理分配的原则。
应选择重要加工表面为粗基准。
3、粗基准不重复使用的原则。
粗基准的精度低,粗糙度数值大,重复使用会造成较大的定位误差,因此,同一尺寸方向的粗基准,通常只允许使用一次。
2、精基准的选用原则
1、基准重合原则。
尽可能使设计基准和定位基准重合,以减少定位误差。
2、基准统一原则。
尽可能使用同一定位基准加工个表面,以保证各表面的位置精度。
如轴类零件常用两端顶尖孔作为统一的定位基准。
3、互为基准原则。
当两个加工表面间的位置精度要求比较高的时候,可用互为基准的原则反复加工。
4、自为基准的原则。
当要求加工余量小而均匀时,可选择加工表面作为自身的定位基准。
2.2、确定零件的定位基准
凸轮杆加工中,为了保证各主要表面的相互位置精度,选择定位基准时,应遵循基准重合、基准统一和互为基准等重要原则,并能在一次装夹中尽可能加工出较多的表面。
由于凸轮杆外圆表面的设计基准是主轴轴心线,根据基准重合的原则考虑应选择凸轮杆右端的顶尖孔作为精基准面。
用顶尖孔定位,还能在一次装夹中将许多外圆表面及其端面加工出来,有利于保证加工面间的位置精度。
所以主轴在粗车之前应先加工顶尖孔。
三、凸轮杆的材料、毛坯及热处理
3.1、凸轮杆的材料
选用45钢,精度较高的轴可选用40Cr、轴承钢GCr15弹簧钢65Mn也可选用球墨铸铁;对高速、重载的轴,选用20CrMnTi、20Mn2B20Cr等低碳合金钢或38CrMoAI氮化钢。
3.2、凸轮杆毛坯
常用圆棒料和锻件;大型轴或结构复杂的轴采用铸件。
毛坯经过加热锻造后,可使金属内部纤维组织沿表面均匀分布,获得较高的抗拉、抗弯及抗扭强度。
3.3、凸轮杆的热处理
锻造毛坯在加工前,均需安排正火或退火处理,使钢材内部晶粒细化,消除锻造应力,降低材料硬度,改善切削加工性能。
调质一般安排在粗车之后、半精车之前,以获得良好的物理力学性能。
表面淬火一般安排在精加工之前,这样可以纠正因淬火引起的局部变形。
精度要求高的轴,在局部淬火或粗磨之后,还需进行低温时效处理。
四、制定加工工艺路线
拟订零件的加工路线是制定工艺规程的总体布局,主要任务是选择各表面的
加工方法,及定位基准,确定加工顺序,各工序采用的机床设备和工艺装备等。
4.1凸轮杆加工工艺过程分析
凸轮杆加工工艺过程可划分为两个加工阶段,即粗加工阶段(包括车端面、
加工顶尖孔、粗车外圆等);精加工阶段(包括精铣端面,粗、精加工外圆、锥孔等)。
在机械加工工序中间尚需插入必要的热处理工序,这就决定了主轴加工各主
要表面总是循着以下顺序的进行,即粗车f调质(预备热处理)f半精车f精车一淬火-回火(最终热处理)f粗磨f精磨。
综上所述,主轴主要表面的加工顺序安排如下:
外圆表面粗加工(以三夹一顶定位)一外圆表面精加工(以三夹一顶定位)
T钻通孔(以精加工过的外圆表面和端面定位)T左端面的铣削(以精加工过的外圆表面和端面定位)一锥孔粗加工(以半精加工过的外圆表面定位,加工后配锥堵)一外圆表面精加工(以锥堵顶尖孔定位)-锥孔精加工(以精加工外圆面定位)。
凸轮杆的加工技术要求:
加工表面
尺寸及技术要求/mm
公差及精度等级
表面粗糙度Ra/m
①50外圆面
50mm
IT9
0.8
①74.5外圆端面
21mm
IT9
0.8
孔外侧面
64mm
IT12
6.3
锥度孔
20mm
IT9
0.8
开口槽
3mm
IT12
6.3
4.2、工艺路线的拟定
为保证几何形状、尺寸精度、位置精度及各项技术要求,必须判定合理的工艺路线。
制定工艺路线的出发点,应当是使零件的几何形状、尺寸精度及位置精度等技术要求能得到合理的保证。
在生产纲领已确定为中批生产的条件下,可以考虑采用万能性机床配以专用夹具,并尽量使工序集中来提高生产率。
除此以外,还应当考虑经济效果,以便使生产成本尽量下降。
1、工艺路线方案一:
工序一:
车外圆①45,①50,车螺纹M45X1.5
工序二:
开槽3X0.5
工序三:
车外圆①74.5,①105
工序四:
钻孔两次并扩孔①20
工序五:
铣削①64的深3mm断平面
工序六:
铣削最大的圆弧面
工序七:
精铣圆弧面
工序八:
车锥度为MorseNo3的锥面
工序九:
精车①50和锥度为MorseNo3的锥面
工序十:
终检
上面的工序可以是中批生产,但是其效率不高,并且工序四中的钻孔方法在钻孔是可能会偏离中心。
2、工艺路线方案二:
工序一:
粗、精铣①70mm①125mm的下表面。
工序二:
钻①20的孔(不到尺寸)
工序三:
镗①20的孔(不到尺寸)工序四:
精镗①20两孔,锥度孔,倒角1.5X45°工序五:
车外圆①45,①50,车螺纹M45X1.5工序六:
开槽3X0.5
工序七:
车外圆①74.5,①105
工序八:
铣削①64的深3mm断平面
工序九:
铣削最大的圆弧面
工序十:
精铣圆弧面
工序十一:
终检
上述两个方案的特点在于:
方案一是先加工外圆,然后以此为基准加工①20的孔。
而方案二则与其相反,先加工①20的孔。
经比较可见先加工外圆定位加工①20的孔,这时的位置精度较易保证,并且定位及装夹都较为方便。
综上所诉,具体工艺过程如下:
3、工艺路线方案:
工序一:
车端面及外圆①45,①50,并车螺纹M45X1.5,倒角C1,以
①125外圆为粗基准,选用GSK980TD卧式车床。
工序二:
开槽3X0.5,选用刀宽为3mm的切刀。
工序三:
车端面及外圆①74.5,①105,以①50外圆为粗基准,保证①
74.5的右端面满足技术条件,选用GSK980TD卧式车床。
工序四:
钻孔两次并扩孔①20,以①45的外圆为基准,选用立式加工中心。
工序五:
铣削最大直径为①105的圆弧面,以①45的端面和①50的外
圆为基准定位,选用三爪卡盘和铣床。
工序六:
精铣最大直径为①105的圆弧面,保证其外圆表面粗造的为
0.8o
工序七:
铣削①64的深3mn端平面,并倒角3X45°,以①45的端面和①50的外圆为基准,选用三爪卡盘和铣床。
工序八:
车锥度为MorseNo3的锥面,选用GSK980TD卧式车床。
工序九:
精车①50的外圆面和锥度为MorseNo3的锥面。
保证表面粗
造的为0.8,选用GSK980TD卧式车床。
工序十:
终检
4.3、凸轮杆机械加工工艺过程卡
附件,凸轮杆的机械加工工艺过程卡、机械加工工艺卡。
4.4、加工余量的确定
工序1:
下料
毛坯选择铸造毛坯,材料为45号钢。
毛坯直径D=60mm毛坯长度L=230mm.
工序4:
车外圆①45,①50,车螺纹M45X1.5,倒角C1
1.加工条件
工件材料:
45#,
加工要求:
车毛坯两头端面,各加工余量2mm;
机床:
数控车床;
刀具:
YT15硬质合金车刀。
尺寸:
宽度B=16mm高度H=25m刀杆长度L=125,选择刀具前角丫o=20°后角ao=10°,副后角ao=1O°,刃倾角入S=—8°,主偏角Kr=90°,,副偏角Kr'=5°。
2.切削用量
(1)确定背吃刀量:
轴线长度方向的端面的加工余量为2mm,需全部加工,因为
余量较小,故可一次加工,选择背吃刀量asp2mm。
故选择:
fz=0.18mm/z。
故:
丄(55_°0234)/5600.50.12min
bnf2
(6)车螺纹M45错误!
未找到引用源。
1.5机床:
数控车床
刀具:
螺纹车刀
根据《切削手册》查得,进给量为
0.18〜0.22mm/z,现取f=0.22mm/z,v=17m/min,
则:
工序5、6:
开槽3X0.5,车外圆①74.5,①105
1.加工条件
工件材料:
45#,(Tb=630-700MPa锻件;
加工要求:
粗车-半精车©74.5和©105,长度为21mm表面粗糙度为6.3。
刀具:
YT15硬质合金车刀。
尺寸:
宽度B=16mm高度H=25mr刀杆长度L=125,选择刀具前角丫o=20°后角ao=10°,副后角ao=1O°,刃倾角入S=—8°,主偏角Kr=60°,,副偏角Kr'=5°。
2.确定切削用量
粗车-半精车©74.5和©105,开槽3X0.5
(1)确定背吃刀量
粗车©74.5和©105外圆,加工余量为2mm两次走刀,则背吃刀量asp2.5mm
(2)确定进给量
进给量f0.5mm/r(查表得)
(3)选择刀具磨钝标准及耐用度
由刀具磨顿标准参考值表查取硬质合金外圆车刀磨损部位为后刀面且粗加工时的后
刀面磨损最大限度为0.6-0.8,焊接耐用度T=60mino
(4)确定切削速度Vc
查表取:
Vc=1.5m/s(由asp2.5mm、f=0.5mm/r、车刀为YG硬质合金)由公式
n1000Vc/d有n(10001.560)/(3.1455)521r/min
根据C6140车床速度表选择车床速度N=560r/min
、,dN3.1455560…,
则实际的切削速度
Vc1.62m/s
1000100060
综上,此工步的切削用量为:
asp2.5mm,f=0.5mm/r,
n=560r/min,Vc1.62m/s
tb—i(2060234)/5600.50.76min
nf
工序7、8:
钻、镗①20孔以及镗①64孔,以①45外圆基准
机床:
T68卧式镗床
单边余量z2.5mm,a2.5mm
p
1.选择钻头
根据《切削手册》表2.1.2.2,选择高速钢麻花钻钻头,粗钻时do=15mm钻头采用
双锥后磨横刀,后角ao=12°,二重刃长度b£=3.5mm横刀长b=2mm宽l=4mm,棱带长
度l11.5mm,2100°,30
2.选择切削用量
0.43~0.53mm/r,1d30181.673,
(1)确定进给量
按加工要求确定进给量:
查《切削手册》由《切削手册》表2.7,系数为0.5,则:
f(0.43~0.53)0.5(0.215~0.265)mm/r
按钻头强度选择:
查《切削手册》表2.8,钻头允许进给量为:
f2.0mm/r;
按机床进给机构强度选择:
查《切削手册》表2.9,机床进给机构允许轴向力为8330N时,进给量为f0.93mm/r。
以上三个进给量比较得出,受限制的进给量是工艺要求,其值为:
0.215~0.265mm/r。
根据《简明手册》表4.2-16,最终选择进给量f0.22mm/r。
由于是通孔加工,为避免即将钻穿时钻头折断,故应在即将钻穿时停止自动进给而改为手动进给。
根据《切削手册》表2.19查出,钻孔时轴向力Ff=2500N轴向力修正系数为1.0,故Ff=2500N根据Z525立式钻床使用说明书,机床进给机构允许的最大轴向力为8830N
>Ff,故所选进给量可用。
(2)确定钻头磨钝标准及寿命
后刀面最大磨损限度(查《简明手册》)为0.6mm,寿命T45min.
(3)切削速度
(4)
查《切削手册》表2.30,切削速度计算公式为:
3、计算工时
4、镗孔至①18
查《切削手册》表2.10,镗孔进给量为:
f0.7〜0.8mm/r,并由机床使用说明书最
终选定进给量为:
f0.81mm/r。
根据资料,切削速度v0.4v钻,其中v钻为用钻头钻同样尺寸实心孔时的切削速度,
故v0.49.53.8m/min
根据机床使用说明书选取nw97r/min
基本工时t-y3^-80.48min
970.81970.81
工序9:
铣削最大直径为①105的圆弧面
刀具:
硬质合金三面刃铣刀
机床:
X51立式铣床
根据《简明手册》查得:
dw63mm,Z16。
根据《切削手册》查得:
fz0.10mm/z,
因此:
1000vnsdw
100027
136r/min
63
现采用X51立式铣床,取:
nw100r/min,故实际切削速度为:
当nw300r/min时,工作台每分钟进给量应为:
根据《切削手册》表4.2-37查得,取:
fm165mm/min
12.52537.5mm
计算切削基本工时:
因此:
L375
tm0.0.227min
fm165
lly
工序10:
磨削最大直径为①105的圆弧面
机床:
X51立式铣床
刀具:
硬质合金立铣刀(镶螺旋形刀片),由《切削手册》表3.6查得:
d40,z6,fz0.08mm/min,v0.45m/s即27m/min,因此,
钟进给量fm应为:
fmfzznw0.08
6210
100.8mm/min
查机床使用说明书,
取fm
100mm/min
磨削基本工时:
tm
7212
0.84min
100
2tm0.8421.68min
工艺路线拟定以后,应确定每道工序的加工余量、工序尺寸及其公差。
工序尺寸是工件加工过程中,每个工序加工应保证的尺寸,工序尺寸允许的变动范围就是工序尺寸的公差。
工序尺寸的确定与加工余量有着密切的关系。
零件图上的尺寸和公差就是最终的加工工序尺寸和公差。
将此尺寸加上加工余量就是上一工序的工序尺寸。
五、凸轮杆零件的检验
5.1、加工中的检验
自动测量装置,作为辅助装置安装在机床上。
这种检验方式能在不影响加工的情况下,根据测量结果,主动地控制机床的工作过程,如改变进给量,自动补偿刀具磨损,自动退刀、停车等,使之适应加工条件的变化,防止产生废品,故又称为主动检验。
主动检验属在线检测,即在设备运行,生产不停顿的情况下,根据信号处理的基本原理,掌握设备运行状况,对生产过程进行预测预报及必要调整。
在线检测在机械制造中的应用越来越广。
5.2、加工后的检验
单件小批生产中,尺寸精度一般用外径千分尺检验;大批大量生产时,常采用光滑极限量规检验,长度大而精度高的工件可用比较仪检验。
表面粗糙度可用粗糙度样板进行检验;要求较高时则用光学显微镜或轮廓仪检验。
圆度误差可用千分尺测出的工件同一截面内直径的最大差值之半来确定,也可用千分表借助V
形铁来测量,若条件许可,可用圆度仪检验。
圆柱度误差通常用千分尺测出同一轴向剖面内最大与最小值之差的方法来确定。
主轴相互位置精度检验一般以轴两端顶尖孔或工艺锥堵上的顶尖孔为定位基准,在两支承轴颈上方分别用千分表测量。
一寸光阴不可轻
总结
时光飞逝,在这次设计过程中,使我真正的认识到自己的不足之处,以前上课没有学到的知识,在这次设计当中也涉及到了。
使我真正感受到了知识的重要性。
这次设计将我以前学过的机械制造工艺与装备、公差与配合、机械制图、工程材料与热处理工艺等知识很好的串联了起来,起到了穿针引线的作用,巩固了所学知识的作用。
在机械制造工艺课程设计中,首先是对工件机械加工工艺规程的制定,这样在加工工件就可以知道用什么机床加工,怎样加工,加工工艺装备及设备等,因此,工件机械加工工艺规程的制定是至关重要的。
在这次械制造工艺课程设计中,对我来说有所收获也存在着不足之处。
本次课程设计我们学会了很多,也收获了很多,进一步巩固了Word、AutoCAD、Proe的基础学习;在今后的工作中我们会将本次课程设计中所学到的知识、品质和精神一同带进去,发挥其作用。
收获:
1)能把以前所学的各种知识,综合的运用的这次设计中,巩固了以前所学的知识。
2)学会了参阅各种资料及查各种余量、切削用量等手册。
3)学会了,分析问题,解决问题的能力。
不足之处:
1)有些步骤,问题解决的方法不是很好,需在以后的学习、实践中进一步改进。
2)有些工艺路线制定的不是太好,而且余量、切削用量设计不是很精确,需在以后的实践中积累经验,进一步改进。
综上所述:
这次的械制造工艺课程设计对我以后的工作起了很大的帮助,我认识到,无论是工作还是学习都必须做到认真、谨慎,时时处处细心。
参考文献
1、顾崇衍等编著。
机械制造工艺学。
陕西:
科技技术出版社,1981。
2、姜敏凤主编。
工程材料及热成型工艺。
高等教育出版社,2003。
3、机械制造工艺及设备设计手册编写组编。
机械制造工艺及设备设计手册。
机械工业出版社,1989。
4、倪森寿主编。
机械制造工艺与装备习题集和课程设计指导书。
化学工业出版社,2001。
5、刘越主编。
机械制造技术。
化学工业出版社,2001。
6、赵如福主编。
金属机械加工工艺人员手册(第三版)。
上海科技技术出版社,1981。
7、南京工程学院陈于萍主编沈阳大学周兆元副主编。
互换性与测量技术基础。
机械工业出版社,2004。