丝杠加工工艺.docx
《丝杠加工工艺.docx》由会员分享,可在线阅读,更多相关《丝杠加工工艺.docx(16页珍藏版)》请在冰豆网上搜索。
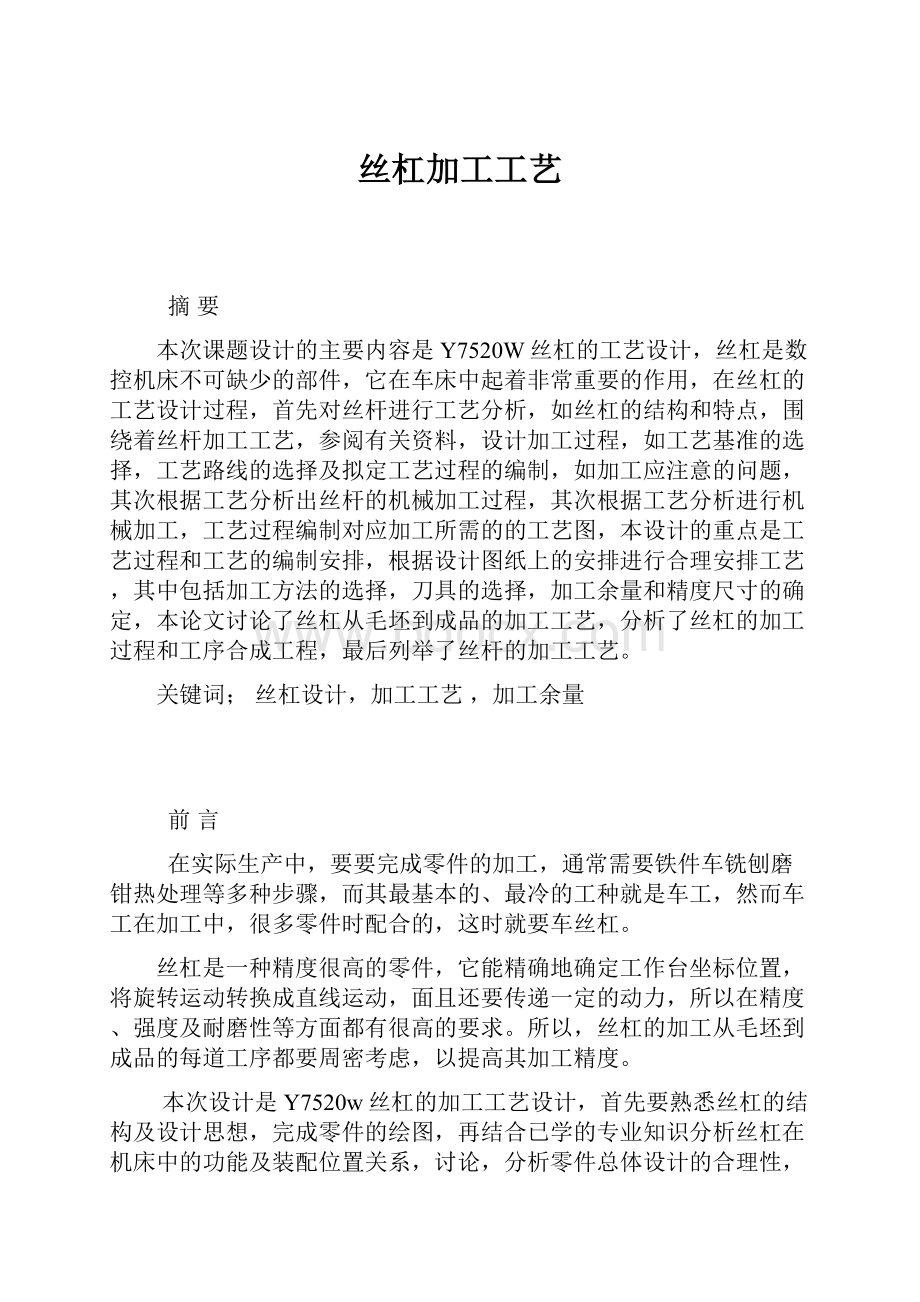
丝杠加工工艺
摘要
本次课题设计的主要内容是Y7520W丝杠的工艺设计,丝杠是数控机床不可缺少的部件,它在车床中起着非常重要的作用,在丝杠的工艺设计过程,首先对丝杆进行工艺分析,如丝杠的结构和特点,围绕着丝杆加工工艺,参阅有关资料,设计加工过程,如工艺基准的选择,工艺路线的选择及拟定工艺过程的编制,如加工应注意的问题,其次根据工艺分析出丝杆的机械加工过程,其次根据工艺分析进行机械加工,工艺过程编制对应加工所需的的工艺图,本设计的重点是工艺过程和工艺的编制安排,根据设计图纸上的安排进行合理安排工艺,其中包括加工方法的选择,刀具的选择,加工余量和精度尺寸的确定,本论文讨论了丝杠从毛坯到成品的加工工艺,分析了丝杠的加工过程和工序合成工程,最后列举了丝杆的加工工艺。
关键词;丝杠设计,加工工艺,加工余量
前言
在实际生产中,要要完成零件的加工,通常需要铁件车铣刨磨钳热处理等多种步骤,而其最基本的、最冷的工种就是车工,然而车工在加工中,很多零件时配合的,这时就要车丝杠。
丝杠是一种精度很高的零件,它能精确地确定工作台坐标位置,将旋转运动转换成直线运动,面且还要传递一定的动力,所以在精度、强度及耐磨性等方面都有很高的要求。
所以,丝杠的加工从毛坯到成品的每道工序都要周密考虑,以提高其加工精度。
本次设计是Y7520w丝杠的加工工艺设计,首先要熟悉丝杠的结构及设计思想,完成零件的绘图,再结合已学的专业知识分析丝杠在机床中的功能及装配位置关系,讨论,分析零件总体设计的合理性,经济性,加工性能,所需采用的热处理工艺和装配的合理性等,根据所给零件的技术要求,选择合理的毛坯形式,进行工艺分析,对总体工艺过程进行合理的规划,在老师指导下,编制工艺的、分析文件,查阅加工所需设备信息,选用加工设备,在工艺分析的基础上制定合理的工艺路线,编制加工工艺过程,编制详细到底加工工序并绘制加工零件图,最后编写设计说明书。
通过本次设计,使我们对机械加工工艺有了更加深刻的了解和认识,把以前学过的理论知识初步与实际结合,为毕业以后从事工艺方案设计及零件机械加工打下坚实的基础,并且进一步了解机床的组成,结构,为以后工作打下一定基础。
毕业设计是集理论知识与实际技能训练于一体的一次全面性的应用,通过此次设计,应达到如下要求:
1..掌握各种丝杠车削的方法.
2.掌握丝杠的组成结构、工作原理.
3.能够熟练的掌握丝杠加工过程中有关计算的方法,并能正确查找有关的技术手册和资料.
4.能合理的选择零件的定位基准;掌握工件的定位,夹紧的基本原理和方法.
5.能分析零件的加工工艺,尽可能采用选的工艺.
6.能独立地制定丝杠的加工工艺.
第1章零件的分析
1.1零件的作用
丝杠是一种精度很高的零件,它能精确地确定工作台坐标位置,将旋转运动转换成直线运动,面且还要传递一定的动力,所以在精度、强度及耐磨性等方面都有很高的要求。
所以,丝杠的加工从毛坯到成品的每道工序都要周密考虑,以提高其加工精度。
1.2零件的结构简介
1.2.1丝杠的分类
机床丝杠按其摩擦特性可分为三类:
即滑动丝杠、滚动丝杠及静压丝杠。
由于滑动丝杠结构简单,制造方便,所以在机床上应用比较广泛。
滑动丝杠的牙型多为梯形。
这种牙型比三角形牙酬具有效果高,传动性能好,
精度高,加工方便等优点。
滚动丝杠义分为滚珠丝杠和滚柱丝杠两大类。
滚珠丝杠与滚柱丝杠相比而言摩擦力小,传动效率高,精度也高,因而比较常用,但是其制造工艺比较复杂。
静压丝杠有许多的优点,常被用于精密机床和数控机床的进给机构中。
其纹牙与标准梯形螺纹牙形相同。
但牙形高于同规格标准螺纹1.5~2倍,目的在于获得好油封及提高承载能力。
但是调整比较麻烦,而且需要一套液压系统,工艺复杂,成本较高。
1.2.2丝杠的结构特点及技术要求
(1)丝杠结构的工艺特点
丝杠是细长柔性轴,它的长度L与直径d的比值很大,一般为20~50,刚性较差。
结构形状复杂,有很高的螺纹表面要求,还有阶梯、沟槽等,所以,在加工过程中易出现变形。
(2)精度等级
在国家标准GB785-65中,对普通梯形螺纹精度是按中径公差划分的。
共有五项基本参数:
即外径d、内径d1、中径d2、螺距t及牙形半角α/2。
由于丝杠要传递准确运动,因此,按JB2886-81规定,丝杠及螺距的精度,根据使用要求分为6个等级:
4、5、6、7、8、9(精度依次降低)。
各级精度丝杠应用范围如下:
4级为目前最高级,一般很少应用;5级用于精密仪器及机密机床,如坐标镗床、螺纹磨床等;6级用于精密仪器、精密机床和数控机床;7级用于精密螺纹车床、齿轮加工机床及数控机床;8级用于一般机床,如卧式车床、铣床;9级用于刨床、钻床及一般机床的进给机构。
一般所说的精密丝杠是指5、6、7级丝杠。
精密丝杠有淬硬丝杠和不淬硬丝杠两种。
前者的耐磨性较好,能较长时间保持加工精度,但加工工艺复杂,必须有高精度的螺纹磨床和专门的热处理设备,而后者只需要精密丝杠车床。
滚珠丝杠副和滚珠丝杠的精度等级也分为六个等级。
(3)技术要求
对于丝杠的技术要求可分为如下几项:
①精度等级;
②表面粗糙度;
③单个螺距允差和定长上的累积允差;
④中径圆度允差;
⑤外径相等性允差;
⑥外径圆跳动允差;
⑦牙形半角允差;
⑧中、外、内径允差等项。
1.2.3零件的加工工艺分析
丝杠加工中,中心孔是定位基准,但由于丝杠是柔性件,刚性很差,极易产生变形,出现直线度、圆柱度等加工误差,不易达到图样上的形位精度和表面质量等技术要求,加工时还须增加辅助支承。
将外圆表面与跟刀架相接触,防止因切削力造成的工件弯曲变形。
同时,为了确保定位基准的精度,在工艺过程中先后安排了三次研磨中心孔工序。
由于丝杠螺纹是关键部位,为防止因淬火应力集中所引起的裂纹和避免螺纹在全长上的变形而使磨削余量不均等弊病,螺纹加工加工采用“全磨”加工方法,即在热处理后直接采用磨削螺纹工艺,以确保螺纹加工精度。
由于该丝杠为单件生产,要求较高,故加工工艺过程严格按照工序划分阶段的原则,将整个工艺过程分为五个阶段:
准备和预先热处理阶段,粗加工阶段),半精加工阶段,精加工阶段,终加工阶段。
为了消除残余应力,整个工艺过程安排了四次消除残余应力的热处理,并严格规定机械加工和热处理后不准冷校直,以防止产生残余应力。
为了消除加工过程中的变形,每次加工后工件应垂直吊放,并采用留加工余量分层加工的方法,经过多道工序逐步消除加工过程中引起的变形
第2章工艺规程的设计
2.1确定毛坯材料
丝杠材料的选择是保证丝杠质量的关键,一般要求是:
(1)具有优良的加工性能,磨削时不易产生裂纹,能得到良好的表面光洁度和较小的残余内应力,对刀具磨损作用较小。
(2)抗拉极限强度一般不低于588MPa。
(3)有良好的热处理工艺性,淬透性好,不易淬裂,组织均匀,热处理变形小,能获得较高的硬度,从而保证丝杠的耐磨性和尺寸的稳定性。
(4)材料硬度均匀,金相组织符合标准。
常用的材料有:
不淬硬丝杠常用T10A,T12A及45等;淬硬丝杠常选用9Mn2V,CrWMn等。
其中9Mn2V有较好的工艺性和稳定性,但淬透性差,常用于直径≤50mm的精密丝杠;CrWMn钢的优点是热处理后变形小,适用于制作高精度零件,但其容易开裂,磨削工艺性差。
丝杠的硬度越高越耐磨,但制造时不易磨削。
丝杠材料要有足够的强度,以保证传递一定的动力;应具有良好的热处理工艺性(淬透性好、热处理变形小、不易产生裂纹),并能获得较高的硬度、良好的耐磨性。
丝杠螺母材料一般采用GCrl5、CrWMn、9CrSi、9Mn2V,热处理硬度为60~62HRC。
整体淬火在热处理和磨削过程中变形较大,工艺性差,应尽可能采用表面硬化处理。
上述滚珠丝杠材料为9Mn2V热轧圆钢,调质硬度为250HRS,除螺纹外,其余高频淬硬60HRC。
材料加工前须经球化处理,并进行严按的切试样检查。
为了消除由于金相组织不稳定而引起的残余应力,安排了冰冷处理工序,使淬火后的残余奥氏体转变为马氏体。
为了保证质量,毛坯热处理后进行磁性探伤,检查零件是否有微观裂纹。
2.2基面选择
由于热处理使丝杠产生变形,而义不允许有冷直法校直,必须用切削方法纠止。
如果仍采用原来的中心孔就会使加工余量过大。
另外,中心孔本身也会有变形,因此对于不淬硬丝杠采用切去原中心孔,重新打中心孔(最后一次修正中心孔工序除外)的方法。
在重新打中心孔之前,找出丝杠径向圆跳动量为最大的圆跳动量的一半的两点,而后用中心支架支撑在这两点上并按外圆找正,切去原米的中心孔,重新打中心孔,这样就可使总加工余量减少很多。
对于淬硬丝杠只能采用每次研磨中心孔的方法进行修正。
加工丝杠时,理论上是以中心孔为主要基面,外圆为辅助基面。
实际上,在加工螺纹时,外圆本身的圆柱度和圆度,跟刀套与丝杠的配合精度,跟刀套与两顶尖连线的同轴度都成为影响螺纹加工精度的因素。
因此工艺过程应为:
在热处理后先加工外圆,再加工螺纹,以加工后的外圆定位。
这样,终磨时外圆精度要求也相应地提高。
2.3拟定丝杆的工艺路线
丝杠加工中,中心孔是定位基准,但由于丝杠是柔性件,刚性很差,极易产生变形,出现直线度、圆柱度等加工误差,不易达到图样上的形位精度和表面质量等技术要求,加工时还须增加辅助支承。
将外圆表面与跟刀架相接触,防止因切削力造成的工件弯曲变形。
同时,为了确保定位基准的精度,在工艺过程中先后安排了三次研磨中心孔工序。
由于丝杠螺纹是关键部位,为防止因淬火应力集中所引起的裂纹和避免螺纹在全长上的变形而使磨削余量不均等弊病,螺纹加工加工采用“全磨”加工方法,即在热处理后直接采用磨削螺纹工艺,以确保螺纹加工精度。
由于该丝杠为单件生产,要求较高,故加工工艺过程严格按照工序划分阶段的原则,将整个工艺过程分为五个阶段:
准备和预先热处理阶段(工序1—6),粗加工阶段(工序7—13),半精加工阶段(工序14—23),精加工阶段(工序24—25),终加工阶段(工序26—28)。
为了消除残余应力,整个工艺过程安排了四次消除残余应力的热处理,并严格规定机械加工和热处理后不准冷校直,以防止产生残余应力。
为了消除加工过程中的变形,每次加工后工件应垂直吊放,并采用留加工余量分层加工的方法,经过多道工序逐步消除加工过程中引起的变形。
2.4填写工艺卡片
工序号
工种
工序内容
设备
1
备料
热轧圆钢65mmх920mm
2
热处理
球化退火
3
车
车削试样,试样尺寸为Φ45×8mm,车削后应保证零件总长为908mm
车床CA6140
4
磨
在平面磨床上磨试样两平面(磨出即可),表面粗糙度Ra值为1.6μm
平面磨床
M820
5
检验
检验试样,要求试样球化等级1.5~4级,网状组织小于3级,待试样合格后方可转入下道工序
6
热处理
调质,调质后硬度250HBS,校直
7
粗车
粗车各外圆,均留加工余量6mm
车床CA6140
8
钳
划线,钻Φ7mm起吊通孔
9
热处理
时效处理,除应力,要求全长弯曲小于1.5mm,不得冷校直;
10
车
(1)车两端面取总长902mm,修正两端面中心孔。
(2)车外圆Φ64.5处到Φ64.5+0.40+0.30,滚珠螺纹大径Φ44处车至Φ44+0.40+0.20,留磨量1.1~1.2mm;
车床CA6140
11
粗磨
粗磨滚珠螺纹大径至Φ440-0.20,磨其他各外圆,均留磨量1.1~1.2mm
万能外圆磨床M1432A
12
热处理
按图样技术要求淬硬,中温回火,冰冷处理,工艺要求:
全长弯曲小于0.5mm,两端中心孔硬度达50~56HRC,不得冷校直
13
检验
检验硬度,磁性探伤,去磁
14
研
研磨两端中心孔,表面粗糙度Ra值为1.25μm
车床CA6140
15
粗磨
磨Φ64.5外圆至Φ64.5+0.20+0.10,磨滚珠螺纹大径Φ44+0.10+0,磨其余各外圆,均留磨量0.65~0.75mm,磨出两端垂直度为0.005mm及表面粗糙度Ra值为1.6μm的肩面,完工后垂直吊放
万能外圆磨床M1432A
16
检验
磁性探伤,去磁
17
粗磨
磨滚珠丝杠底槽至尺寸,粗磨滚珠丝杠螺纹,留磨量(三针测量仪),齿形用样板透光检查,去不完整牙,完工后垂直吊放
丝杆磨床
S7432
18
检验
磁性探伤,去磁
19
热处理
低温回火除应力,要求变形不大于0.15mm,不准冷校直
20
研
修研两端中心孔,要求表面粗糙度Ra值为0.63μm,完工后垂直吊放
车床CA6140
21
粗磨
磨Φ64.5外圆至Φ64.50-0.20,磨
外圆至
,磨其他各外圆,均留磨量0.3~0.4mm
万能外圆磨床M1432A
22
半精磨
半精磨滚珠螺纹,留精磨余量(三针测量仪),齿形用样板透光检查,完工后垂直吊放
丝杆磨床
S7432
23
热处理
低温回火,消除磨削应力,要求全长弯曲小于0.10mm,不得冷校直
24
研
修研两端中心孔,表面粗糙度Ra值为0.32μm,完工后垂直吊放
车床CA6140
25
半精磨
磨Φ64.5外圆(磨出即可),磨滚珠螺纹大径至图样要求,全长圆柱度0.02mm,磨
外圆至图样要求
万能外圆磨床M1432A
26
精磨
粗磨滚珠丝杠螺纹
丝杆磨床
S7432
27
精磨
精磨滚珠丝杠螺纹至图样要求,齿尖倒圆R0.2mm,要求:
齿形按样,透光检查,完工后垂直吊放
丝杆磨床
S7432
28
终磨
终磨各外圆,及肩面至图样要求,完工后垂直吊放,并涂防锈油
万能外圆磨床M1432A
2.5确定工序尺寸
下料尺寸:
65mm×920mm
粗车尺寸:
各外圆均留加工余量6mm
半精车尺寸:
总长902mm,各外圆留加工余量1.4~1.5mm,外圆中心Φ64.5到Φ64.5+0.40+0.30,Φ44处车至Φ44+0.40+0.20
粗磨尺寸:
各外圆均留磨量0.3~0.4mm(分三次),磨锥度留磨量0.35~0.45mm,Φ64.5外圆到Φ64.50-0.20分二次),Φ45+0.40+0.30外圆至Φ450-0.05(分二次)
半精磨尺寸:
磨Φ64.5外圆(磨出即可),磨滚珠螺纹大径,磨Φ450-0.05外圆至图样要求,外圆均留余量0.12~0.15mm
精磨尺寸:
各部分尺寸至图纸要求
2.6细长轴工件安装
2.6.1在双顶尖间或一夹一顶安装工件
一夹一顶安装:
即轴的一端外圆用卡盘夹紧,一端用尾座顶尖顶住中心孔的工件安装方式。
这种安装方式可提高轴的装夹刚度,此时轴的外圆和中心孔同作为定位基面,常用于长轴加工及粗车加工中。
双顶尖间安装:
在实心轴两端钻中心孔,在空心轴两端安装带中心孔的锥堵或锥套心轴,用车床主轴和尾座顶尖轴两端中心孔的工件安装方式。
2.6.2用中心架加工工件时装夹和找正
用中心架加工工件时将打好中心孔的工件装夹好,并用尾座支持尖支持好。
用较小的切削用量支持车一段光径,其直径必须大于工件的成活直径,然后将中心架的三个支承爪卡装在光径上。
在使用中心架时,应先将架体固定在床面上,压紧上盖,然后调整三个支承爪,使它轻轻地、均匀地接触在光径上,再紧固螺钉。
在切削过程中,要不断加上润滑油,并随时注意发热情况和支承的松紧。
如果毛坯件没有预制中心孔,或者工件在中心架上装夹的部分是已经加工好的表面,不允许擦伤的情况下,便需要使用定心套筒进行装夹,如果9-2所示。
先将工件装夹在卡盘和尾座支持减之间,并校正夹固,然后退出尾座支持尖,将定心套筒固定在工件的适当位置上,用安装在小刀架上的百分表,分别在水平方向和垂直方向校正定心套筒与工件轴线的同轴度,然后再架上中心架。
定心套筒如果夹固在已经精加工的表明上,必需在夹固螺钉和工作表面垫上纯铜皮,防止压伤工件。
在确定中心架位置时,要考虑到公件加工时要有足够的刚度。
如果用后支持尖支支持,最好选取工件和中部作为忠心加支承的位置。
又如加工端面或内孔时,则在接近工件端部作为中心架支承位置。
中心架位置的确定,除考虑到工件装夹应有足够的刚度以外,还应该保证不会由于中心架的位置不合理而影响加工
2.7机床、刀具、夹具、量具的选择
2.7.1机床的选择
车削:
车床CA6140
平面磨削:
平面磨床M820
外圆磨削:
万能外圆磨床M1432A
丝杠磨削:
丝杆磨床S7432
1)机床的主要规格尺寸应与加工零件的外廓尺寸相适应。
2)机床的精度应与工序要求的加工精度相适应。
3)机床的生产率与加工零件的生产类型相适应。
4)机床选择应结合现场的实际情况
2.7.2刀具的选择
数控车床上用的刀具应满足安装调试方便,刚性好,精度高,耐用度好等要求,根据零件的外形结构,加工需要如下刀具:
45°硬质合金端面车刀,菱形外圆车刀,外切槽刀,外螺纹刀,中心钻,键槽铣刀。
2.7.3夹具的选择
单件小批生产,应尽量选用通用夹具;大批大量生产,应采用高生产率的气液传动的专用夹具。
夹具的精度应与加工精度相适应。
2.7.4量具的选择
(1)单件小批生产应选用通用量具;大批大量生产应采用各种量规和一些高生产率的专用检具。
量具的精度应与加工精度相适应。
(2)工时定额与劳动生产率
工时定额(To)是指在一定的生产条件下制订出来的完成单件产品(如一个零件)或某项工作(如一个工序)所必须消耗的时间。
包括基本时间(Tb)、辅助时间(Ta)、技术服务时间(Tc)、组织服务时间(Tg)、休息和生理需要时间(Tn)。
其中:
Tc+Tg+Tn=(Tb+Ta)хβ
则工时定额To=(Tb+Ta)х(1+β)
劳动生产率是指工人在单位时间内制造的合格品数量,或者指制造单件产品所消耗的劳动时间。
劳动生产率一般通过时间定额来衡量。
(3)切削用量的选择
1)主轴转速的确定
①车外圆是主轴转速
主轴转速应根据允许的切削速度和工件的直径来选择。
计算公式为:
n=1000v/ITd。
②车螺纹是主轴转速
在车削螺纹时,车床的主轴转速将受到螺纹的螺距P大小,驱动电机的升降频特性,以及螺纹插补运算速度等外种因素影响对于不同的数控系统,推荐不同的主轴转速选择范围。
公式为N≤(1200/P)-K式中,P—被加工螺纹螺距,K—保险系数,一般取80.
2)进给速度的确定
进给速度是数控机床切削用量中的主要参数。
确定进给速度的原则:
当工件的质量要求能得到保障时,为提高生产率,可选择较高的进给
速度,一般在100~200mm/min范围内选取。
再切断加工深孔或用高速钢刀具加工时,宜选择较低的进给速度,一
般在20~50mm/min范围内选取。
当加工精度,表面粗糙度要求较高时,进给量应选小一些,一般在
20~50mm/min范围内选取。
3)背吃刀量的选择
背吃刀量根据机床,工件,刀具的刚度来决定,在刚度允许的条件下
应尽可能使背吃刀等于工件的加工余量,这样就可以减少走刀次数,提高
生产率,为了保证加工表面质量,可以留少许加工余量,一般为0.2~0.5
mm。
车削用量的具体规划如下:
精车时,首先尽可能大的背吃刀量,其次
选择一个较大的进给量,最后确定一个合适的切削速度,精车时,加工表
面要求较高,加工余量不大且均匀,因此选择较小的背吃刀量和进给量。
刨削和铣削加工切削用量包括主轴转速(切削速度)进给速度,被吃刀量和侧吃刀量。
切削用量的大小对切削力,切削功率,刀具磨损,加工质量和加工成品均有显著的影响。
为了保证刀具的耐磨度,切削用量的选择方法是:
先选择被吃刀量或侧吃到量,其次确定进给速度,最后确定切削速度。
设计小结
随着毕业日子的到来,课程设计也接近了尾声。
经过几周的奋战我的课程设计终于完成了。
在没有做课程设计以前觉得课程设计只是对这几年来所学知识的单纯总结,但是通过这次做课程设计发现自己的看法有点太片面。
课程设计不仅是对前面所学知识的一种检验,而且也是对自己能力的一种提高。
通过这次课程设计使我明白了自己原来知识还比较欠缺。
自己要学习的东西还太多,以前老是觉得自己什么东西都会,什么东西都懂,有点眼高手低。
通过这次课程设计,我才明白学习是一个长期积累的过程,在以后的工作、生活中都应该不断的学习,努力提高自己知识和综合素质。
在这次课程设计中也使我们的同学关系更进一步了,同学之间互相帮助,有什么不懂的大家在一起商量,听听不同的看法对我们更好的理解知识,所以在这里非常感谢帮助我的同学。
我的心得也就这么多了,总之,不管学会的还是学不会的的确觉得困难比较多,真是万事开头难,不知道如何入手。
最后终于做完了有种如释重负的感觉。
此外,还得出一个结论:
知识必须通过应用才能实现其价值!
有些东西以为学会了,但真正到用的时候才发现是两回事,所以我认为只有到真正会用的时候才是真的学会了。
在此要感谢我们的指导曹玉君老师对我们悉心的指导,感谢老师给我们的帮助。
在设计过程中,我通过查阅大量有关资料,与同学交流经验和自学,并向老师请教等方式,使自己学到了不少知识,也经历了不少艰辛,但收获同样巨大。
在整个设计中我懂得了许多东西,也培养了我独立工作的能力,树立了对自己工作能力的信心,相信会对今后的学习工作生活有非常重要的影响。
而且大大提高了动手的能力,使我充分体会到了在创造过程中探索的艰难和成功时的喜悦。
虽然这个设计做的也不太好,但是在设计过程中所学到的东西是这次课程设计的最大收获和财富,使我终身受益。
致谢
天下没有不散的宴席,虽然大三的生活多半时间还是呆在学校里,但是论文致谢语写就的那一刻也真正标志着我与这所学校就此别离了,没有伤感,更多的是遗憾,但是总归不如意事十有八九,过去的不能挽回,人应该大胆向前看,所以这段文字应该像它的标题一样充满感恩和致谢,感谢三年来在我的成长道路上扶持过我,指点过我的人。
论文得以顺利完成,要感谢的人实在太多了。
首先要衷心地感谢我的指导老师曹老师,您严谨的治学态度,开阔的思维,循循善诱的指导一直给我很大的帮助。
当我对论文的思路感到迷茫时,您为我理清思路,指导我往一条比较清晰的思路上进行修改。
在论文的不断修改中,我也努力做到及时积极地跟曹老师交流,因为我觉得这样可以使得我的论文更加完善。
在这里还要深深的对您说上一句抱歉,因为我的懒散和懈怠,令您费尽苦心并且几近失望。
论文的最终完成,也是一波三折。
在不断完善和修改的过程中,也让我更加懂得“一分耕耘才有一分收获”的道理。
再次对您表示感谢,师恩伟大,无以回报。
参考文献
[1]《机修手册》<设备零件的修复及加工工艺>北京:
中国机械工程学会第一机械工业部.主编,机械工业出版社,1981.4北京第一版
[2]《机械零件》徐振宇北京:
高等教育出版社,1983
[3]《机械工程基础》雷红哈尔滨:
黑龙江出版社,2002
[4]《机械制造基础》唐宗军大连:
机械工业出版社,1997
[5]《数控机床》吴祖育,秦鹏飞上海:
上海科技技术出版社,2003
[6]《机械工程学》张树森辽宁:
东北大学出版社,2001
[7]《数控加工工艺》徐宏涛北京:
中央广播电视大学出版社,2007
[8]《数控编程技术》张超英北京:
中央广播电视大学出版社,2007
[9]《机械制造技术》李华北京:
高等教育出版社2006
[10]《机械设计课程设计》巩云鹏、田万禄.沈阳:
东北大学出版社2000