高速铣削与数控编程技术.docx
《高速铣削与数控编程技术.docx》由会员分享,可在线阅读,更多相关《高速铣削与数控编程技术.docx(9页珍藏版)》请在冰豆网上搜索。
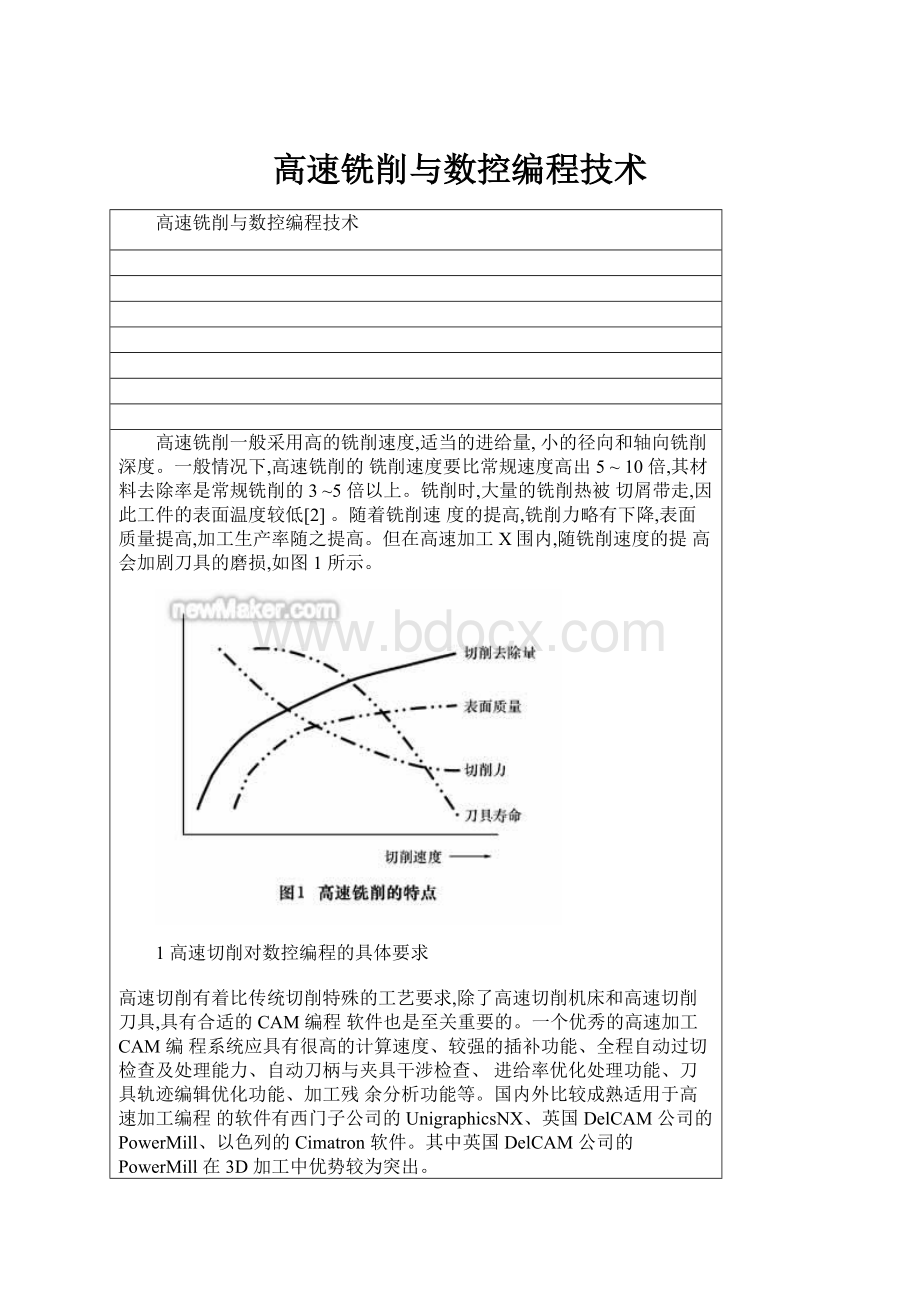
高速铣削与数控编程技术
高速铣削与数控编程技术
高速铣削一般采用高的铣削速度,适当的进给量,小的径向和轴向铣削深度。
一般情况下,高速铣削的铣削速度要比常规速度高出5~10倍,其材料去除率是常规铣削的3~5倍以上。
铣削时,大量的铣削热被切屑带走,因此工件的表面温度较低[2]。
随着铣削速度的提高,铣削力略有下降,表面质量提高,加工生产率随之提高。
但在高速加工X围内,随铣削速度的提高会加剧刀具的磨损,如图1所示。
1高速切削对数控编程的具体要求
高速切削有着比传统切削特殊的工艺要求,除了高速切削机床和高速切削刀具,具有合适的CAM编程软件也是至关重要的。
一个优秀的高速加工CAM编程系统应具有很高的计算速度、较强的插补功能、全程自动过切检查及处理能力、自动刀柄与夹具干涉检查、进给率优化处理功能、刀具轨迹编辑优化功能、加工残余分析功能等。
国内外比较成熟适用于高速加工编程的软件有西门子公司的UnigraphicsNX、英国DelCAM公司的PowerMill、以色列的Cimatron软件。
其中英国DelCAM公司的PowerMill在3D加工中优势较为突出。
高速切削中的NC代码并不仅仅局限于切削速度、切削深度和进给量的不同数值。
NC编程人员必须改变他们的全部加工策略,以创建有效、精确、安全的刀具路径,从而得到预期的表面精度[2]。
数控编程时首先要注意加工方法的安全性和有效性;其次要尽一切可能保证刀具轨迹光滑平稳,这会直接影响加工质量和机床主轴等零件的寿命;最后要尽量使刀具载荷均匀,这会直接影响刀具的寿命。
高速切削对数控编程的具体要求如下。
1.1保持恒定的切削载荷
高速铣削过程中保持恒定的切削载荷非常重要,这会直接影响工件的加工质量和机床主轴以及刀具等零件的寿命。
1.1.1保持金属的去除量恒定
在加工中恒定的金属去除量可以获得较好的加工质量,由于切削载荷均匀,从而可以延长刀具和机床的使用寿命。
为保持恒定的切削条件,主要采用顺铣方式进行粗加工。
在高速切削过程中采用顺铣铣削方式,可以产生较少的切削热,降低刀具的负载,降低甚至消除了工件的加工硬化,以及获得较好的表面质量等。
在工件余量不均匀的情况下,通常采用等高加工策略来保证恒定的金属去除量。
粗加工采用的方法通常是在Z方向切削连续的平面,又叫等高加工策略。
这种切削遵循了高速加工的理论,采用了比常规切削更小的切深,从而减小每齿切削去除量。
图2为Z方向切削连续平面示意图。
通常这种加工方式采用斜向或者螺旋切入,可以获得较平稳的切削路径。
在高速切削的粗加工过程中,保持恒定的金属去除率,可以获得以下的加工效果:
(1)保持恒定的切削负载;
(2)保持切削量的恒定;(3)较好的热转移;(4)刀具和工件均保持在较冷的状态;(5)延长刀具寿命;
(6)获得较好的加工质量等[1]。
1.1.2刀具要平滑地切入工件
如图3所示,在高速切削过程中,让刀具斜向或者沿螺旋线方向切入工件要优于让刀具沿Z向直接切入,这样可以保护刀具和机床,而且可以获得较好的加工质量。
1.1.3保证刀具轨迹的平滑过渡
刀具轨迹的平滑是保证切削负载恒定的重要条件。
如图4所示,螺旋曲线走刀是高速切削加工中一种较为有效的走刀方式。
在NC编程中应尽量避免刀具路径轨迹出现尖角,让轨迹尽可能的光顺,这样可以提高工件表面加工质量,从而降低模具数控加工后的后续研磨强度。
如图5中c图所示的刀具轨迹最好。
1.1.4尽量减少刀具的急速换向
由于进给量和切削速度非常高,编程人员必须预测刀具是如何切削材料的。
除了减小步距和切削深度以外,还要避免可能的加工方向的急剧改变。
急速换向的地方要减慢速度,急停或者急动会破坏表面精度,而且有可能因为过切而产生拉刀或者在外拐角处咬边[2]。
通常,切削过程越简单越好。
这是因为简单的切削过程可以允许最大的进给量,而不必因为数据点的密集或者方向的急剧改变而降低速度。
从一切削层等变率地降到另一层要好于直接跃迁,采用类似于圈状的路线将每一条连续的刀具路径连接起来,可以减小加速度的突变[6]。
实际的高速数控编程中,常常用圆弧连接来过渡切削移动以缓解这种急速换向的现象。
1.2保证工件的高精度
1.2.1减少刀具的切入次数
为了保证工件的高精度,最重要的一点就是尽量减少刀具的切入和切出次数。
在高速数控编程中常常选择回路或者单向路径切削。
这是因为在换向时,NC机床必须立即停止(紧急降速)然后再执行下一步操作。
由于机床的加速局限性,容易造成时间的浪费。
因此,许多人选择单向的路径切削模式来进行顺铣,尽可能地不中断切削过程和刀具路径,尽量减少刀具的切入次数,以获得相对稳定的切削过程。
图6显示了减少刀具切入次数的有效方法。
1.2.2精加工刀具的选择
高速精加工不同于粗加工与半精加工,高速精加工直接决定了所加工工件的加工质量的好坏,所以精加工选用适当的刀具也非常重要。
在同等条件下,刀具越长刚性越差,加工时让刀越严重。
所以精加工应尽量选用较短的刀具,可以减少让刀现象,保证加工质量。
但是由于3D加工往往形状复杂,较深的地方刀具会发生碰撞,这时就可以采用摆角加工,这样就可以保证使用较短的刀具保证加工时减小让刀,从而保证加工质量。
同样,精加工清角也可以采用这种方法进行加工。
1.3保证工件的表面加工质量
在通常情况下,除了单纯地通过控制程序的步距、公差和点分布等参数来提高工件的表面质量以外,还可以通过以下方法来保证工件的加工表面质量。
1.3.1分特征精加工
在精加工过程中,尤其在3D特征的加工过程中,要注意一些复杂的细节或者拐角处切削形貌的产生,而不是仅仅设法采用平行、“之冶字形切削、单向切削或其他的普通切削等方式来生成所有的形貌。
由于加工区域形状复杂不能单纯地用一种加工策略进行编程时,便需要针对不同的特征单独考虑进行编程,比较平缓的区域可以采用平行线精加工,比较陡峭的区域就需要单独考虑处理分区加工(如图7),这样的加工策略可以弥补单一加工策略的局限性,从而提高工件的表面加工质量。
分特征精加工是比较复杂的过程,要求编程员在对各种加工策略都非常了解的基础上,对工件进行详细分析,针对不同特征的区域采用不同的加工策略。
分区域的恰当与否直接影响了工件的表面加工质量,所以这也需要经验的积累。
分区域精加工有一定的原则:
(1)精加工不是分区越多越好,在允许的情况下,能不分区精加工就不要分,因为加工分区越多产生的加工对刀误差就越多,加工质量就越不容易保证;
(2)精加工刀路越简单越好,精加工应尽量减少刀路的连接时间,提高加工效率;(3)刀路中应尽量避免尖角的出现,因为刀路中存在尖角会影响整个工件表面的质量,会增加数控加工后的后续研磨时间;(4)陡壁面精加工时刀路应自上而下,这样可以避免加工过程中“拉刀冶现象的出现。
1.3.2采用较大的进给量
在高速切削过程中,过小的步进(进给量)会影响实际的进给速率,其往往会造成切削力的不稳定,产生切削振动,从而影响工件表面的完整性。
如图8所示,即为采用不同步进对工件加工表面质量的影响示意图。
可以看出,在高速切削条件下,采用较大的进给量,会产生较好的表面加工质量[2]。
1.3.3精加工前清角
在高速切削的精加工过程中,保证精加工余量的恒定至关重要。
为保证精加工余量恒定,通常在精加工之前要用比精加工使用的刀具小的刀具进行清角。
笔式清角采用的策略为,首先找到先前大尺寸刀具加工后有残留的拐角和凹槽区域,然后自动沿着这些拐角走刀。
其允许用户采用越来越小的刀具,直到刀具的半径与三维拐角或凹槽的半径相一致,如图9所示。
精加工前清角,在期望保持切屑去除率为常量的高速加工中是非常重要的。
精加工前缺少了清角,当精加工这些带有侧壁和腹板的部件时,刀具走到拐角处将产生较大的金属去除率,难以获得较好的表面加工质量。
清角后,拐角处的切削难度降低,减少了让刀量和噪声的产生。
所以3D精加工之前对工件进行行笔式清根可以有效地减小让刀量,使切削过程更稳定,减小噪声,从而获得较好的加工质量。
1.3.4采用f=P工艺来达到高速高精度工件表面
在高速铣削过程中,最好采用f=P的铣削方式(如图10所示)。
这样加工出来的表面粗糙度比较均匀,可以获得较好的表面加工质量[2]。
1.3.5退刀时采用进给速率
在高速数控精加工中采用进给速率退刀可以减小切削载荷的瞬间变化,使切削过程更平稳,从而获得较好的表面加工质量。
2结语
高速铣削技术以其卓越的加工优点被运用于各行各业。
高速切削的发展源于市场日益激烈的竞争,对时间和成本效率的要求越来越高,这便要求数控NC编程不断地优化加工策略,充分发挥高速铣削的优点。