键合技术 引线键合的失效机理.docx
《键合技术 引线键合的失效机理.docx》由会员分享,可在线阅读,更多相关《键合技术 引线键合的失效机理.docx(16页珍藏版)》请在冰豆网上搜索。
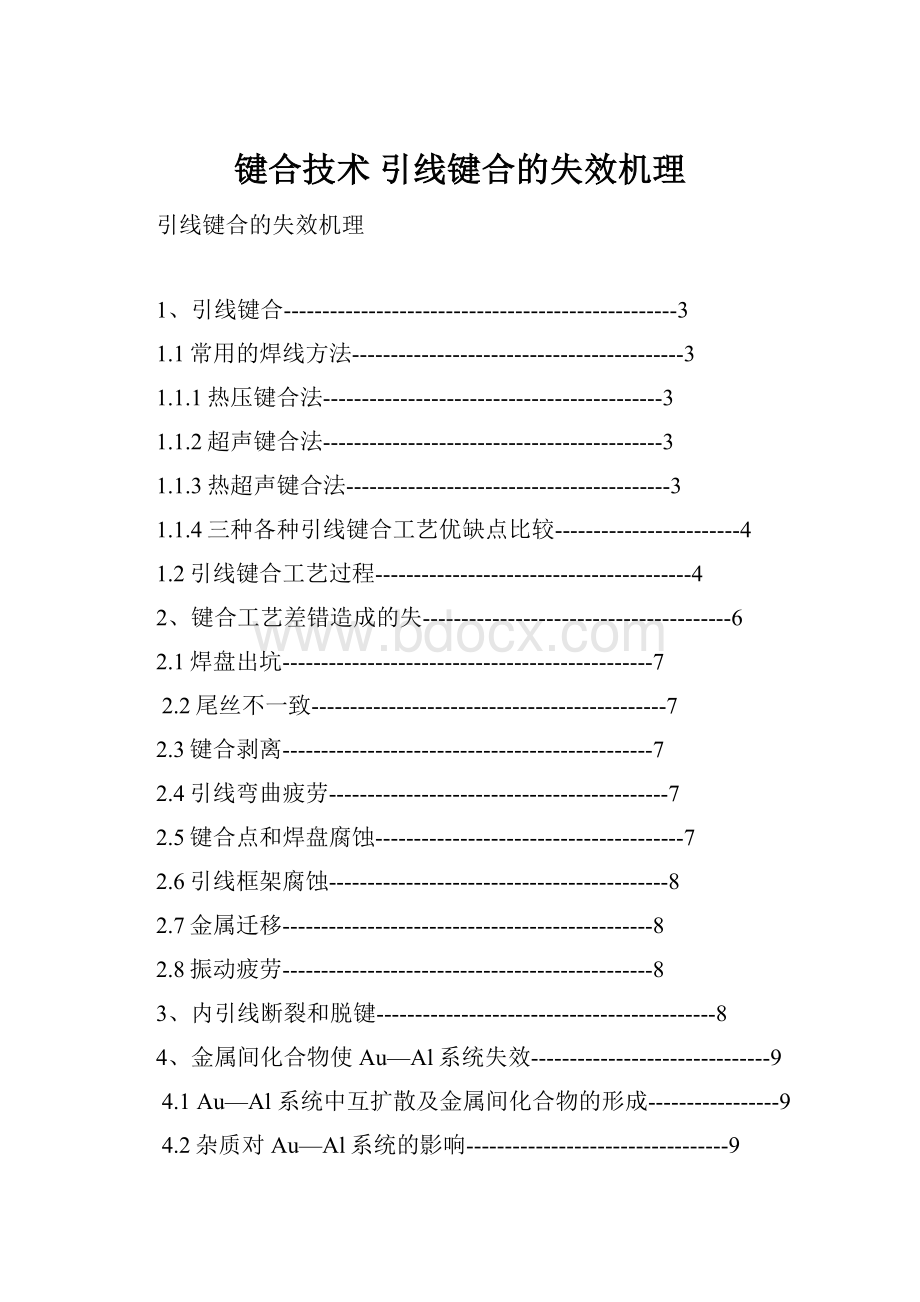
键合技术引线键合的失效机理
引线键合的失效机理
1、引线键合---------------------------------------------------3
1.1常用的焊线方法-------------------------------------------3
1.1.1热压键合法--------------------------------------------3
1.1.2超声键合法--------------------------------------------3
1.1.3热超声键合法------------------------------------------3
1.1.4三种各种引线键合工艺优缺点比较------------------------4
1.2引线键合工艺过程-----------------------------------------4
2、键合工艺差错造成的失----------------------------------------6
2.1焊盘出坑------------------------------------------------7
2.2尾丝不一致----------------------------------------------7
2.3键合剥离------------------------------------------------7
2.4引线弯曲疲劳--------------------------------------------7
2.5键合点和焊盘腐蚀----------------------------------------7
2.6引线框架腐蚀--------------------------------------------8
2.7金属迁移------------------------------------------------8
2.8振动疲劳------------------------------------------------8
3、内引线断裂和脱键--------------------------------------------8
4、金属间化合物使Au—Al系统失效-------------------------------9
4.1Au—Al系统中互扩散及金属间化合物的形成-----------------9
4.2杂质对Au—Al系统的影响----------------------------------9
4.3改善方法------------------------------------------------10
5、热循环使引线疲劳而失效-------------------------------------10
5.1热循环峰值温度对金相组织的影响--------------------------10
5.2热循环峰值温度对冲击功的影响----------------------------10
5.3引线疲劳------------------------------------------------11
6、键合应力过大造成的失效-------------------------------------11
参考文献-------------------------------------------------------12
1、引线键合
引线键合是芯片和外部封装体之间互连最常见和最有效的连接工艺。
—1、1常用的焊线方法
—1、1、1热压键合法:
热压键合法的机制是低温扩散和塑性流动(PlasticFlow)的结合,使原子发生接触,导致固体扩散键合。
键合时承受压力的部位,在一定的时间、温度和压力的周期中,接触的表面就会发生塑性变形(PlasticDeformation)和扩散。
塑性变形是破坏任何接触表面所必需的,这样才能使金属的表面之间融合。
在键合中,焊丝的变形就是塑性流动。
该方法主要用于金丝键合。
压头下降,焊球被锁定在端部中央在压力、温度的作用下形成连接
压头上升压头高速运动到第二键合点形成弧形
在压力、温度作用下形成第二点连接压头上升至一定位置,送出尾丝
夹住引线,拉断尾丝引燃电弧,形成焊球进入下一键合循环
—1、1、2超声键合法:
焊丝超声键合是塑性流动与摩擦的结合。
通过石英晶体或磁力控制,把摩擦的动作传送到一个金属传感器(Metal“HORN”)上。
当石英晶体上通电时,金属传感器就会伸延;当断开电压时,传感器就会相应收缩。
这些动作通过超声发生器发生,振幅一般在4-5个微米。
在传感器的末端装上焊具,当焊具随着传感器伸缩前后振动时,焊丝就在键合点上摩擦,通过由上而下的压力发生塑性变形。
大部分塑性变形在键合点承受超声能后发生,压力所致的塑变只是极小的一部分,这是因为超声波在键合点上产生作用时,键合点的硬度就会变弱,使同样的压力产生较大的塑变。
该键合方法可用金丝或铝丝键合。
定位(第一次键合)键合
定位(第二次键合)键合——切断
—1、1、3热超声键合法:
这是同时利用高温和超声能进行键合的方法,用于金丝键合。
—1、1、4三种各种引线键合工艺优缺点比较:
特性
热压键合法
超声键合法
热超声键合法
可用的丝质及直径
Au丝
φ15~φ100um
Au丝,Al丝
Φ10~φ500um
Au丝
Φ15~φ100um
键合丝的切断方法
高电压(电弧)
拉断
拉断(超声压头)
拉断(送丝压头)
高电压(电弧)
高电压(电弧)
拉断
优点
键合牢固,强度高;在略粗糙的表面上也能键合;键合工艺简单
无需加热;对表面洁净度不十分敏感;
与热压键合法相比,可以在较低温度、较低压力下实现键合
缺点
对表面清洁度很敏感;应注意温度对元件的影响
对表面粗糙度敏感;工艺控制复杂
需要加热;与热压法相比工艺控制要复杂些
其他
适用于单片式LSI
最适合采用Al丝
适用于多芯片LSI的内部布线连接
—1、2引线键合工艺过程
引线键合的工艺过程包括:
焊盘和外壳清洁、引线键合机的调整、引线键合、检查。
外壳清洁方法现在普遍采用分子清洁方法即等离子清洁或紫外线臭氧清洁。
(1)等离子清洁——该方法采用大功率RF源将气体转变为等离子体,高速气体离子轰击键合区表面,通过与污染物分子结合或使其物理分裂而将污染物溅射除去。
所采用的气体一般为O2、Ar、N2、80%Ar+20%O2,或80%O2+20%Ar。
另外O2/N2等离子也有应用,它是有效去除环氧树脂的除气材料。
(2)外线臭氧清洁通过发射184.9mm和253.7mm波长的辐射线进行清洁。
过程如下:
184.9nm波长的紫外线能打破O2分子链使之成原子态(O+O),原子态氧又与其它氧分子结合形成臭氧O3。
在253.7nm波长紫外线作用下臭氧可以再次分解为原子氧和分子氧。
水分子可以被打破形成自由的OH-根。
所有这些均可以与碳氢化合物反应以生成CO2+H2O,并最终以气体形式离开键合表面。
253.7nm波长紫外线还能够打破碳氢化合物的分子键以加速氧化过程。
尽管上述两种方法可以去除焊盘表面的有机物污染,但其有效性强烈取决于特定的污染物。
例如,氧等离子清洁不能提高Au厚膜的可焊性,其最好的清洁方法是O2+Ar等离子或溶液清洗方法。
另外某些污染物,如Cl离子和F离子不能用上述方法去除,因为可形成化学束缚。
因此在某些情况还需要采用溶液清洗,如汽相碳氟化合物、去离子水等。
(3)引线键合工艺有球键合工艺和楔键合工艺两种。
球键合一般采用D75μm以下的细Au丝。
主要是因为其在高温受压状态下容易变形、抗氧化性能好、成球性好。
球键合一般用于焊盘间距大于100μm的情况下。
目前也有用于50μm焊盘间距的例子。
楔键合工艺既适用于Au丝,也适用于Al丝。
二者的区别在于Al丝采用室温下的超声波键合,而Au丝采用150℃下的热超声键合。
楔键合的一个主要优点是适用于精细尺寸,如50um以下的焊盘间距。
但由于键合工具的旋转运动,其总体速度低于热超声球键合。
最常见的楔键合工艺是Al丝超声波键合,其成本和键合温度较低。
而Au丝楔键合的主要优点是键合后不需要密闭封装,由于楔键合形成的焊点小于球键合,特别适用于微波器件。
(6)键合的方式有两种。
正焊键合:
第一点键合在芯片上,第二点键合在封装外壳上;反焊键合:
第一点键合在外壳上,第二点键合在芯片上。
采用正焊键合时,芯片上键合点一般有尾丝;采用反焊键合时,芯片上一般是无尾丝的。
究竟采用何种键合方式键合电路,要根据具体情况确定。
2、键合工艺差错造成的失效
—2、1焊盘出坑
出坑通常出现于超声波键合中,是指对焊盘金属化层下面半导体材料层的损伤。
这种损伤有时是肉眼可见的凹痕,更多是不可见的材料结构损伤。
这种损伤将降低器件性能并引发电损伤。
其产生原因如下:
(1)超声波能量过高导致Si晶格层错;
(2)楔键合时键合力过高或过低:
(3)键合工具对基板的冲击速度过大,一般不会导致Si器件出坑,但会导致、
GaAs器件出坑;
(4)球键合时焊球太小致使坚硬的键合工具接触到了焊盘金属化层;
(5)焊盘厚度太薄。
1~3μm厚的焊盘损伤比较小,但0.6μm以下厚度的焊盘可能存在问题;
(6)焊盘金属和引线金属的硬度匹配时键合质量最好,也可以最小化出坑现象;
(7)Al丝超声波键合时金属丝太硬可能导致Si片出坑。
—2、2尾丝不一致
这是楔键合时最容易发生的问题,而且也是最难克服的。
可能的产生原因如下:
(1)引线表面肮脏;
(2)金属丝传送角度不对;
(3)楔通孔中部分堵塞;
(4)用于夹断引线的工具肮脏;
(5)夹具间隙不正确;
(6)夹具所施加的压力不对;
(7)金属丝拉伸错误。
尾丝太短意味着作用在第1个键合点上的力分布在一个很小的面积上,这将导致过量变形。
而尾丝太长可能导致焊盘间短路。
—2、3键合剥离
剥离是指拉脱时键合点跟部部分或完全脱离键合表面,断口光滑。
剥离主要是由工艺参数选择错误或键合工具质量下降引起。
它是键合相关失效的一个很好的早期信号。
—2、4引线弯曲疲劳
这种失效的起因在于引线键合点跟部出现裂纹。
原因可能是键合操作中机械疲劳,也可能是温度循环导致热应力疲劳。
已有的试验结果表明:
(1)温度循环条件下,Al丝超声波键合比Al丝热压键合更为可靠;
(2)含0.1%Mg的Al丝要好于含1%Si的Al丝;
(3)引线闭环的高度至少应该是键合点间距的25%以减轻弯曲。
—2、5键合点和焊盘腐蚀
腐蚀可导致引线一端或两端完全断开,从而使引线在封装内自由活动并造成短路。
潮湿和污物是造成腐蚀的主要原因。
例如,键合位置上存在Cl或Br将导致形成氯化物或溴化物,腐蚀键合点。
腐蚀将导致键合点电阻增加直至器件失效。
绝大多数情况下,封装材料在芯片表面和相邻键合点施加了一个压力,只有腐蚀非常严重才会出现电连接问题。
—2、6引线框架腐蚀
起因是残余应力过大,或者在为防止引线框架基体金属(42合金或Cu)腐蚀而进行的表面镀层(如Ni)工艺中引入了过多的表面污染。
最敏感的区域是密封化合物材料与引线框架的界面处。
—2、7金属迁移
是指从键合焊盘处开始的金属枝晶生长。
这是一个金属离子从阳极区向阴极区迁移的电解过程,与金属的可获得性、离子种类、电势差等相关。
金属迁移将导致桥连区的泄露电流增加,如果桥连完全形成则造成短路。
最为广泛报道的是Ag迁移。
其它金属,如Pb、Sn、Ni、Au和Cu也存在迁移现象。
因为与失效相关,这是一种逐渐失效现象。
—2、8振动疲劳
可能产生谐振并因此损伤键合点的最小频率,
对于Au丝为3~5kHz,Al丝为10kHz。
一般而言,
引线键合的振动疲劳失效发生于超声波清洗过程,
因此超声波清洗设备的谐振频率应在20~100kHz
以内。
3、内引线断裂和脱键
内引线断裂的方式一般分为三类:
引线中间断裂;引线在近键合点的根部裂;脱键。
(1)引线中间断裂
引线中间断裂不一定在早期失效中出现,因为它和内引线存在损伤的程度和由损伤诱发的机理有关。
键合丝的损伤使引线损伤部位面积变小,将导致:
电流密度加大,使损伤部位易被烧毁;抗机械应力的能力降低,会造成内引线损伤处断裂。
产生损伤的原因:
一是键合丝受到机械损伤,二是键合丝受到了化学腐蚀的侵蚀
(2)键合丝在近键合点的根部断裂
这种现象的发生主要是由工艺所引入的。
存在铊(Tl)污染源,Tl可以与
Au形成低熔点的共晶相并从镀Au的引线框架传输到Au丝中。
键合点形
成过程中,Tl可以快速扩散并在球颈以上的晶界处富集形成共晶相。
在塑
性密封或温度循环时,球颈断裂,器件失效。
(3)键合点脱键隐患
自动引线键合技术中,半导体器件键合点脱落是最常见的失效模式。
这种失效模式用常规筛选和测试很难剔除,只有在强烈振动下才可能暴露出来,因此对半导体器件的可靠性危害极大。
可能影响内引线键合可靠性的因素主要有:
<1>界面上绝缘层的形成在芯片上键合区光刻胶或窗口钝化膜未去除干净,可形成绝缘层。
管壳镀金层质量低劣,会造成表面疏松、发红、鼓泡、起皮等。
金属间键合接触时,在有氧、氯、硫、水汽的环境下,金属往往与这些气体反应生成氧化物、硫化物等绝缘夹层,或受氯的腐蚀,导致接触电阻增加,从而使键合可靠性降低。
<2>金属化层缺陷,金属化层缺陷主要有:
芯片金属化层过薄,使得键合时无缓冲作用,芯片金属化层出现合金点,在键合处形成缺陷;芯片金属化层粘附不牢,最易掉压点。
<3>表面沾污,原子不能互扩散包括芯片、管壳、劈刀、金丝、镊子、钨针,各个环节均可能造成沾污。
外界环境净化度不够,可造成灰尘沾污;人体净化不良,可造成有机物沾污及钠沾污等;芯片、管壳等未及时处理干净,残留镀金液,可造成钾沾污及碳沾污等,这种沾污属于批次性问题,可造成一批管壳报废,或引起键合点腐蚀,造成失效;金丝、管壳存放过久,不但易沾污,而且易老化,金丝硬度和延展率也会发生变化。
<4>材料间的接触应力不当,键合应力包括热应力、机械应力和超声应力。
键合应力过小会造成键合不牢,但键合应力过大同样会影响键合点的机械性能。
应力大不仅会造成键合点根部损伤,引起键合点根部断裂失效,而且还会损伤键合点下的芯片材料,甚至出现裂缝。
4、金属间化合物使Au—Al系统失效
—4、1Au—Al系统中互扩散及金属间化合物的形成
Au-Al系统中互扩散及金属间化合物的形成过程如下:
(1)在键合的早期阶段,Au-Al之间形成一很薄的扩散层,其成分为AuAl2(紫斑);
(2)进一步受热导致Au-Al扩散继续,随着Au不断向Al薄膜中扩散,纯Al层消失。
与此同时,在Au丝球一侧形成Au5Al2化合物层;
(3)扩散层厚度不会无限增加,这是因为Al的来源有限而且二者之间互扩散速度存在差别。
定义D为扩散速度,DAu→Al>DAl→Au。
假设初始Al薄膜厚度为1μm,总的扩散层厚度约为4~5μm。
进一步受热则Au向扩
散层中扩散并在Au丝球一侧形成Au4Al,并向半导体芯片一侧生长;
(4)进一步受热则Au向扩散层中的扩散继续,并最终使扩散层成分仅为Au5Al2和Au4Al。
同时由于kirkendall效应,扩散层周围将有空洞产生;
(5)如果继续受热,无空洞位置的Au的扩散进一步加强,导致在中央部位形成Au4Al层;
(6)对于塑封IC,由于树脂材料中的阻燃剂含溴化物,它将成为Au4Al层中Al氧化的催化剂。
溴化物穿过空洞进入键合点并氧化Au4Al层中的Al,
从而在Au球中央和化合物层之间的界面处形成一高电阻层,这将导致一种断开失效。
—4、2杂质对Au—Al系统的影响
在引线开发的最初阶段,其主要目的是为了增强机械强度例如引线结构和引线长度的控制,因此没有太多考虑金属间的断裂问题。
但是随着焊盘间距的不断减小和控制窗口的不断变窄,引线键合技术的发展开始受到金属间相问题的束缚。
迄今为止,引线掺杂效应还没有得到深入的研究。
通过添加掺杂杂质和减缓金属间相的扩散速度被认为是减少金属间失效的唯一手段。
实际上,掺杂浓度为100ppm时掺杂杂质并不能有效地阻止金属间相的生长。
为此,一些常用引线中掺杂杂质的含量被提高到1%,此时掺杂杂质能够阻止Au和Al的扩散。
但是其效果没有我们预期的那么好,而且还会降低引线的电导率。
因此,我们需要能够更加有效地解决这些问题的新方法,而且不能影响电导率性能。
—4、3改善方法
金属间失效的主要原因有很多,因此很难通过控制一个因素将其降低到最小程度。
我们能做的是选择最佳EMC以减小封装应力、选择最佳毛细管劈刀类型以形成更致密的金属间相,以及优化工艺参数以尽量减小不规则生长程度和提高初始金属间相覆盖率。
研究结果显示最有效的影响因素是引线类型。
毛细管劈刀类型也会影响金属间相的形成。
但是,当金属间相覆盖率大于70%时,金属间相覆盖率不再是主要因素。
当我们将焊盘间距为70um的毛细管劈刀和引线类型用于40um时,我们将遇到HTS和温度循环失效问题。
但是,通过选择最佳毛细管劈刀类型、引线类型和EMC,我们可以在可靠性性能上取得很好的改善效果。
5、热循环使引线疲劳而失效
—5、1 热循环峰值温度对金相组织的影响
热循环不同峰值温度条件下的金相组织如图1所示。
由图1可看出,当热循环峰值温度为1350℃时,冷却后转变成粗大的低碳马氏体+少量的侧板条贝氏体组织。
当热循环峰值温度为950℃时,冷却后组织明显细化。
当热循环峰值温度为750℃时,对应于热影响区的部分淬火区,因高温停留时间短,奥氏体成分均匀化很不充分,使该区组织为铁素体+粒状贝氏体组织。
峰值温度为600℃时,未超过调质处理时的高温回火温度,组织以回火索氏体为主。
—5、2热循环峰值温度对冲击功的影响
经不同峰值温度热循环作用下,随着热循环峰值温度的提高,冲击功下降。
当热循环峰值温度超过1100℃后,冲击功已降低到较低水平。
由此可以看出,随着热循环峰值温度的增加,晶粒长大倾向增大,当热循环峰值温度为1350℃时,奥氏体晶粒严重长大,致使该区冲击功最低。
—5、3引线疲劳
在Au纳米引线的热疲劳测试中,将正弦交变电压(Vpp=10V)输入引线,从而在引线中产生交变热应力。
实验中交变电压信号的频率为50Hz-100Hz。
如设由于交变电信号在引线中产生的温度变化为ΔT,则引线中产生的热应变为Δε=(αAu-αSi)ΔT,其中(αAu-αSi)为Au和Si的热膨胀系数之
(αAu=1.42×10-5/oC;αSi=3×10-6/oC)。
这一应变将导致Au引线经历压-压疲劳循环。
在实验中,记录每一试件的疲劳失效寿命(指引线开路时的疲劳循环次数),并同时通过SEM观察引线表面的形貌变化。
表给出了长度为20μm,三种不同宽度Au引线在相同交变电压信号(Vpp=10V),不同电压频率作用下的疲劳失效结果。
对于同样的输入电压随着引线线宽的减小,其失效循环次数明显减少。
产生这一结果有两个原因,其一是由于引线宽度的减少,导致其横截面积相应地减少,这样在相同的电压作用下,较窄的引线中将形成较大的电流,而随着电流的增加,将在导线中引起较高的温度及较大的热应力,从而加速了引线的疲劳失效;其二是由于本文的纳米引线厚度仅35nm,宽度从500nm到150nm,引线材料中晶粒在厚度方向将小于35nm,在宽度方向小于100nm。
和以往研究者所利用的微米到亚微米晶粒相比,细化后的晶粒能够拟制位错的运动,因而导致引线失效的原因可能是由局部界面损伤引起引线在宽度方向的破坏所控制。
因此较宽和较薄的引线将具有更长的疲劳寿命。
结合中引线失效时的显微图片可以看到,在纳米引线的表面并没有发现类似于体材料疲劳时由于往复的位错运动导致的滑移在薄膜表面形成平行的起皱图案(体材料在机械疲劳载荷作用下的挤出和挤入机制,在这些起皱位置由于引线横截面积的突然减少将会导致局部电流过载引起焦耳热而导致引线熔断失效)。
显然,较大尺寸的引线(含有较大的晶粒)破坏过程由位错作用控制。
而在本文的实验中由于引线细而薄,使得引线结构中晶粒尺度减小,其疲劳行为受扩散机制以及界面特性控制,而不是位错滑移机制控制。
即损伤可能在膜基界面形核(由于纳米晶粒的高强度很难在纳米晶薄膜上形成裂纹,且金薄膜和SiO2界面为弱结合界面),一旦局部界面脱粘,由电流诱导的边界或界面扩散将进一步加速界面脱粘,最终将在压-压疲劳驱动下形成局部跨线宽损伤区域,导致焦耳热熔断引线形成开路失效。
另外从引线失效显微图看到,三个线宽的引线疲劳损伤失效机制一致。
在焦耳热导致的高温区晶界消失成流动状态。
由于失效过程为瞬态行为,失效区域由于高温熔融,实验还无法观察损伤前该区域的形貌特性。
6、键合应力过大造成的失效
键合应力过小会造成键合不牢,键合应力过大会影响键合点的机械性能。
应力大不仅会造成键合点根部损伤,引起键合点根部断裂失效,而且还会损伤键合点下的芯片材料,甚至出现裂缝等情况。
这种损伤有时是肉眼可见的凹痕,更多是不可见的材料结构损伤,这种损伤将降低器件性能并引发电损伤。
其产生原因如下:
(1)声波能量过高导致Si晶格层错;
(2)楔键合时键合力过高或过低;
(3)球键合时焊球太小致使坚硬的键合工具接触到了焊盘金属化层;
(4)焊盘厚度太薄;
(5)Al丝超声波键合时金属丝太硬可能导致Si片出坑。
参考文献
1、关东旭.《硅集成电路工艺基础》.北京大学出版社,2003年10月
2、Dong-JinJeong,AmkorTechnologyKorea.《半导体制造》.2006年10月刊
3、潘峰.顔向乙.郑轩《全自动键合机工艺调试方法》(期刊).2009年5月
4、刘恩科朱秉升罗晋升.《半导体物理》.国防出版社.2008年4月
5、晁宇晴.杨兆建.乔海灵《引线键合技术进展》(期刊).2007年04