PCB生产过程与技术.docx
《PCB生产过程与技术.docx》由会员分享,可在线阅读,更多相关《PCB生产过程与技术.docx(15页珍藏版)》请在冰豆网上搜索。
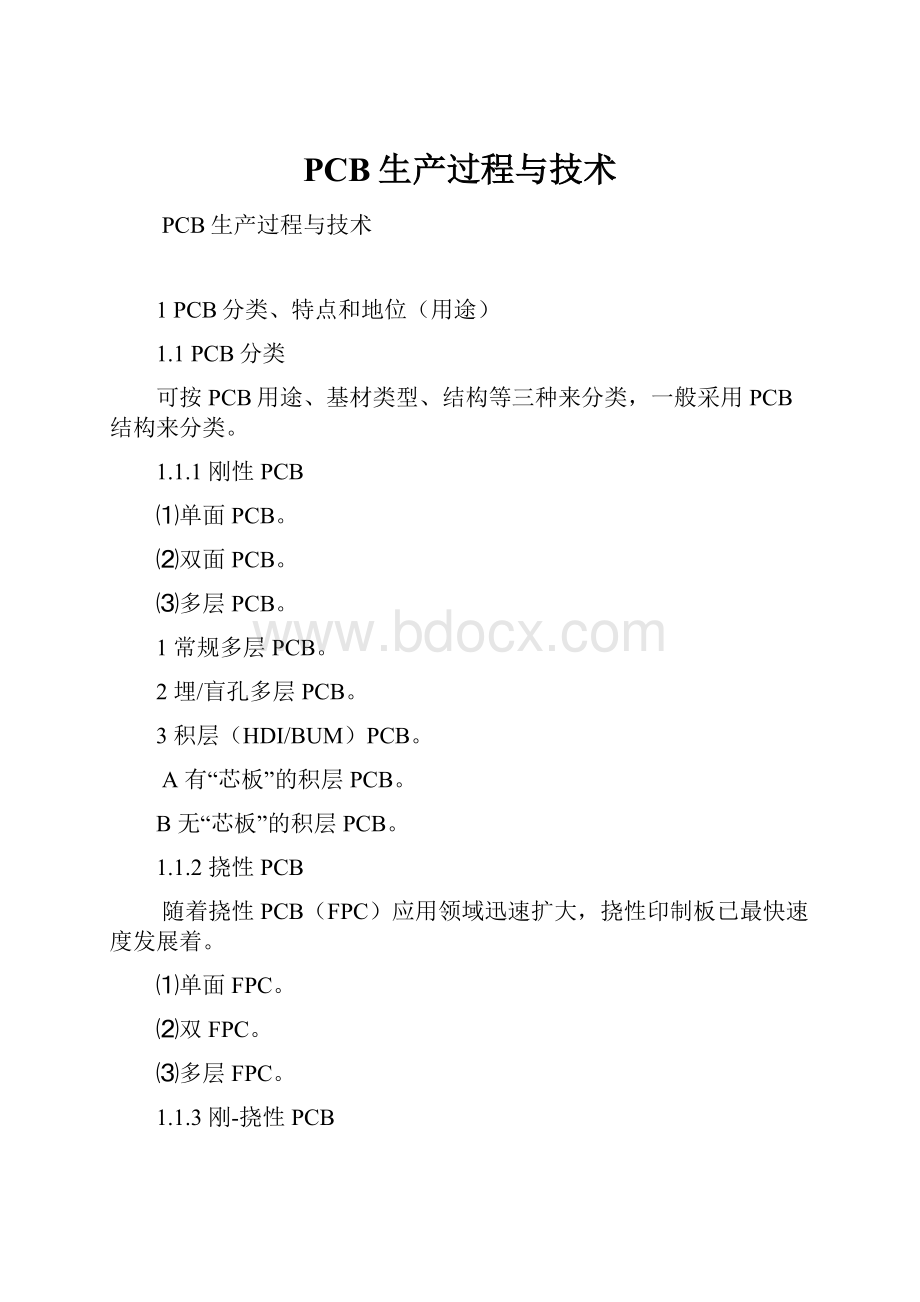
PCB生产过程与技术
PCB生产过程与技术
1PCB分类、特点和地位(用途)
1.1PCB分类
可按PCB用途、基材类型、结构等三种来分类,一般采用PCB结构来分类。
1.1.1刚性PCB
⑴单面PCB。
⑵双面PCB。
⑶多层PCB。
1常规多层PCB。
2埋/盲孔多层PCB。
3积层(HDI/BUM)PCB。
A有“芯板”的积层PCB。
B无“芯板”的积层PCB。
1.1.2挠性PCB
随着挠性PCB(FPC)应用领域迅速扩大,挠性印制板已最快速度发展着。
⑴单面FPC。
⑵双FPC。
⑶多层FPC。
1.1.3刚-挠性PCB
这是指由刚性部分和挠性部分共同组成的PCB。
刚性部分主要用于焊接或组装元器件,而挠性部分主要起着刚性部分之间的连接、信号传输和可挠曲性机械安装的作用。
⑴刚性部分主要为刚性多层板结构,但中间夹入挠性部分,通过层压、钻孔和孔化与电镀等形成刚性部分与挠性部分之间连接。
⑵挠性部分由挠性板组成。
为了保持可挠曲性机械安装,挠性部分大多为单、双面挠性板或多组的单、双面挠性板等组成。
1.1.4特种PCB
这是指高频微波PCB、金属基(芯)PCB和某些特殊PCB而言的。
⑴高频微波PCB。
这是指应用于高频(频率大于300MHZ或波长小于1米)与微波(频率大于3G或波长小于0.1米)领域的PCB。
其主要要求如下。
1低介电常数εr的基材。
A聚四氟已烯(PTFE)又称Teflon,其εr=2.1,形成CCL的εr为2.6左右。
B“空气珠”或“微泡”结构的CCL材料,其εr为1.15∽1.35之间(Arlon公司)。
2低介质损耗角正切tanδ。
PTFE基材的tanδ为0.002,仅为FR-4的1/10。
⑵金属基(芯)PCB。
在组装有大功率组件的PCB埋入金属板,以提高导热或散热为主要目的(还有改善CTE和尺寸稳定性等)的PCB。
所采用的金属材料有:
薄Al板;薄Fe板;薄Cu板;殷钢;钨钼合金。
还有非金属的炭素板等。
⑶其它特殊PCB。
如厚铜箔PCB、复合材料PCB和特大尺寸(面积或厚度等)PCB。
1厚铜箔PCB。
这是指镀通孔和导线的铜厚度35∽200µm之间的PCB。
主要应用于大电流通过的场合,如电源用的PCB等。
2复合材料PCB。
这是指不同材料压合在一起的PCB,如把PTFE材料和FR-4材料压合在一起的PCB。
既解决了高频信号传输问题,又解决了使用时的刚性与尺寸稳定性问题。
3特大尺寸PCB。
这是指厚度很厚、面积很大的PCB,如600X800X5∽800X1800X12(mm)的背板或底板(又称母板)。
1.1.5集成元件PCB。
这是指把无源元件(电阻、电容和电感等)、有源元件(各种集成电路等)分别或复合埋入到PCB部的产品。
由于目前技术水平和发展过程的原因,目前主要是埋入无源元件的PCB为主,其工艺也比较成熟。
⑴埋入无源元件PCB。
1为何要埋入无源元件到PCB部去呢?
A无源元件数量与有源元件数量比率越来越大。
由(6∽15):
1上升到(15∽33):
1,如手机的无源元件的数量已超过500只,而台式电脑主板(奔腾Ⅱ)的无源元件数量已达2000只以上。
这种增加趋势还在继续。
B促进PCB高密度化发展。
如能埋入50%数量的无源元件,则可使PCB板面缩小25%以上。
C提高PCB组装的可靠性。
减少了大量的焊接。
埋入无源元件受到“保护”,避免大气中的湿气、有害气体、尘粒等侵蚀,性能稳定。
D提高了PCB组装件的电气性能。
消除了无源元件焊接所形成的大量回路,及其引起的寄生效应。
减少无源元件功能失效率,提高无源元件功能稳定性。
2埋入电阻PCB。
把电阻以平面形式埋入到PCB部的方法,以CCL电阻、网印油墨电阻、喷墨打印和烧结等工艺来形成。
3埋入电容PCB。
把电容以平面形式埋入到PCB部的方法,同样以CCL电容、网印油墨电容、喷墨打印和烧结等工艺来形成。
4埋入电感PCB。
把电感以平面形式埋入到PCB部的方法。
由于数量很少,加上电感较大,埋入效果不理想。
5复合埋入无源元件PCB。
即同时埋入电阻和电容等的PCB。
1.1PCB特点
过去、现在和未来,PCB之所以能越来越得到广泛地应用,这是因为它有好多独特的优点,概括如下。
⑴可高密度化。
100多年来,PCB的高密度化是随着集成电路集成度的提高和安装技术的进步而发展着。
⑵可靠性。
通过一系列标准和规定的检查、测试和老化试验等可保证PCB产品长期(使用期,一般为20年)而可靠地工作着。
⑶可设计性。
对PCB产品的各种性能(电气、物理、化学、机械等)的要求,可以通过设计标准化、规化等来实现PCB设计,时间短、效率高。
⑷可生产性。
可采用现代化生产管理,可进行标准化、规模(量产)化、自动化生产,保证产品质量一致性。
⑸可测试性。
建立了比较完整的测试方法、测试标准、各种测试设备与仪器等来检验,并鉴定PCB产品的合格性和使用寿命。
⑹可组装性PCB产品既便于各种元件进行标准化组装,又可以进行自动化、规模化的组装生产。
同时,PCB和各种元件组装的部件还可以组装形成更大的部件、系统,直至整机产品。
⑺可维护性。
由于PCB产品和各种元件组装形成的部件是以标准化设计与规模化生产的,因而,这些部件也是标准化的。
所以,一旦系统或整机发生故障,可以快速、方便、灵活地进行更换,迅速恢复工作。
当然,还可以举例说得更多些。
如系统小型化、轻量化,消息传输高速化等。
1.3PCB地位
在所有的电子工业领域中都离不开PCB产品,PCB产品已成为三大电子元件一。
其应用领域有五大方面。
⑴家用电子产品方面。
如电视机、洗衣机、VCD等。
①基板材料。
主要采用纸基酚醛树脂的单面板,少量采用纸基或玻纤布基环氧树脂的单、双面板。
②主要特点:
利润低;靠量产。
⑵便携式电子产品方面。
如手机(移动)、摄象机、录象机等。
1基板材料:
刚性材料FR-4、CEM-3;挠性材料PI、PE等。
2主要特点:
高密度化(HDI);量产化。
⑶高性能电子产品方面。
如电脑、游戏机等
1基板材料:
FR-4(或高Tg的FR-4)、CEM-3等。
2主要特点:
高密度化(HDI);量产化。
⑷超高性能电子产品方面。
如超级(巨型)计算机、大型工作站等。
1基板材料:
BT树脂基材;PI树脂基材。
2主要特点:
高密度化高层化;技术与工艺难度大,量少,昂贵(附加值高)。
⑸汽车领域电子产品方面。
1基板材料:
刚性材料FR-4、CEM-3,挠性材料PI、PE等。
2主要特点:
安全、可靠。
2PCB生产工艺与技术
2.1PCB原材料
⑴薄铜箔材料。
1FPC用铜箔材料。
采用高延展性铜箔,如冷轧的铜箔等,其厚度为35µm(1OZ)、18µm(1/2OZ)、12µm(3/8OZ)、9µm(1/40Z)、……等。
2刚性PCB用铜箔材料。
采用电镀高延展性铜箔,其厚度为35µm、18µm、12µm、9µm……等。
⑵半固化片(粘结片)材料。
一般是由玻纤布或纸和树脂来组成的。
1常规半固化片。
它是由常规玻纤布与树脂形成的半固化片。
2扁平或特种半固化片。
它是由扁平玻纤布(玻纤与树脂均匀分布)与树脂形成的,主要用于钻微、激光蚀孔,精细导线制作等。
⑶刚性覆铜板(CCL)材料。
它是由铜箔和半固化片于高温高压下而形成的,可以形成不同类型与不同厚度的系列产品供客户选用。
1FR-4材料。
这是由玻纤布(可用不同类型与活动厚度)与环氧树脂形成的CCL材料,是目前PCB工业应用最广泛的材料。
2CEM-3材料。
芯料为玻纤纸半固化片、面料为玻纤布半固化片,然后在与铜箔形成的材料。
它有利于机械冲切加工,价格也便宜些,但某些性能(如弯曲强度)比FR-4稍差。
3RCC(涂树脂铜箔)材料。
在处理过的铜箔表面上涂覆一定厚度树脂形成(半固化状态)的材料。
应用于HDI/BUM板的激光形成微孔方面。
4其它方面材料。
如CEM-1材料(芯料为纤维纸,面料为玻纤布),FR-1与FR-2(纸基酚醛树脂)材料,FR-3(纸基环氧树脂)材料,还有BT,PI,PTFE等等形成的CCL材料。
5特种基板材料。
如金属基覆铜箔材料,瓷基覆铜板材料等。
⑷挠性覆铜板材料。
挠性CCL的最大特点是介质层中没有增强材料,可成卷订货。
主要有PI和PE两种类型CCL。
其中PI的结构有两种。
1三层法。
即由铜箔、粘结剂和PI(或PE)膜形成的挠性CCL。
其优点是价格便宜。
缺点是由于粘结剂层存在使结合力低,同时由于粘结剂往往是非阻燃性的而形成不阻燃的挠性CCL。
2两层法。
即由铜箔和PI膜形成的挠性CCL。
2.2PCB工艺流程与技术
印制电路板的工艺流程与技术可分为单面、双面和多层印制板。
现以双面板和最复杂的多层板为例。
⑴常规双面板工艺流程和技术。
1开料---钻孔---孔化与全板电镀---图形转移(成膜、曝光、显影)---蚀刻与退膜---阻焊膜与字符---HAL或OSP等---外形加工---检验---成品
2开料---钻孔---孔化---图形转移---电镀---退膜与蚀刻---退抗蚀膜(Sn,或Sn/pb)---镀插头---阻焊膜与字符---HAL或OSP等---外形加工---检验---成品
⑵常规多层板工艺流程与技术。
开料---层制作---氧化处理---层压---钻孔---孔化电镀(可分全板和图形电镀)---外层制作---表面涂覆---外形加工---检验---成品
(注1):
层制作是指开料后的在制板---图形转移(成膜、曝光、显影)---蚀刻与退膜---检验等的过程。
(注2):
外层制作是指经孔化电镀的在制板---图形转移(成膜、曝光、显影)---蚀刻与退膜等过程。
(注3):
表面涂(镀)覆是指外层制作后---阻焊膜与字符---涂(镀)层(如HAL、OSP、化学Ni/Au、化学Ag、化学Sn等等)。
⑶埋/盲孔多层板工艺流程与技术。
一般采用顺序层压方法。
即:
开料---形成芯板(相当于常规的双面板或多层板)---层压---以下流程同常规多层板。
(注1):
形成芯板是指按常规方法造成的双面板或多层板后,按结构要求组成埋/盲孔多层板。
如果芯板的孔的厚径比大时,则应进行堵孔处理,才能保证其可靠性。
⑷积层多层板工艺流程与技术。
芯板制作---层压RCC---激光钻孔---孔化电镀---图形转移---蚀刻与退膜---层压RCC---反复进行形成a+n+b结构的集成印制板(HDI/BUM板)。
(注1):
此处的芯板是指各种各样的板,如常规的双面、多层板,埋/盲孔多层板等等。
但这些芯板必须经过堵孔和表面磨平处理,才能进行积层制作。
(注2):
积层(HDI/BUM)多层板结构可用下式表示。
a+n+b
a—为一边积层的层数,n—为芯板,b—为另一边积层的层数。
⑸集成元件多层板工艺流程与技术。
开料---层制作---平面元件制作---以下流程同多层板制作。
(注1):
平面元件以CCL或网印形式材料而采用。
2.3PCB检验与测试
PCB检验与测试是指PCB生产过程中质量控制、最终产品性能和使用期(寿命)可靠性等的检验与测试。
⑴PCB生产过程质量控制的检验。
1物理方面检验。
★目检:
采用人眼或2X、10X或更高倍数的工具显微镜以及其它工具(如检孔镜、背光装置等)来观测表面和孔表面质量。
★AOI(自动光学检查)和SEM(扫描电子显微镜)等的检查。
2化学方面检验。
★常规化学分析。
分析和控制各种溶液质量(主要是组成或成分方面)。
★各种化学仪器。
分析和控制各种溶液(主要是杂质或污染方面)。
⑵PCB产品性能的检测。
1外观检验。
通过目检(含放大倍数)来观测成品表面与尺寸的质量
2电气性能检验。
通过“通”、“断”测试,绝缘(电阻与电压)等来检测成品的电气性能情况。
3显微剖切检验。
通过剖切来检验成品部质量情况,如多层板的对位、镀层厚度分布、层间连接与缺陷等。
⑶PCB使用可靠性的检测。
热冲击试验(浮焊或焊接)、高低温循环试验、潮湿试验、高压蒸煮试验、互连应力试验等等。
然后通过电气性能(如电阻变化等)、显微剖切等来检查与分析成品的可靠性和使用寿命。
3PCB技术现状与发展
PCB技术的过去、现在和未来都是围绕着PCB的“孔”、“线”、“层”、“面”等而展开和发展着。
按电子组装技术的发展与进步可分为如下四个阶段。
3.1通孔插装技术(THT)的PCB概况
⑴通孔的作用。
1电气导通(连接)作用。
2支撑元器件作用。
即元器件的引脚是穿过通孔而焊接起来的,为了保证自动插装和焊接的可靠性,因而限制了元器件引脚尺寸和通孔直径尺寸不能太小,一般停留在φ0.8mm左右。
⑵高密度化方向。
1缩小线宽/间距(L/S)。
这一阶段L/S的高端产品达到0.1mm(但大多数为0.3∽0.2mm)。
2增加层数。
最多达到64层,计划为≥100层,但是孔化、特别是电镀十分困难。
⑶表面涂(镀)覆。
电镀Au或电镀Ni/Au,松香基助焊剂等。
3.2表面安装技术(SMT)的PCB概况
表面安装技术的出现,给PCB工业带来了天翻地覆的变化。
3.2.1主要特点。
⑴导通孔的作用。
它仅起电气互连作用,这意味着:
①只要保证电气互连质量,导通孔直径可尽量小;
②即使把导通孔堵塞起来也行。
⑵PCB成品共面性要求。
这意味着:
①PCB翘曲度应尽量小,要求由1%→0.7%或0.5%,甚至更小;
②连接盘(焊盘)的共面性高。
3.2.2高密度化方向。
主要是导通孔的迅速缩小和结构变化。
⑴导通孔迅速走向微小化,并由数控(机械)钻孔走向激光钻孔。
导通孔直径由0.8→0.5→0.3→0.2→0.15→0.10(mm)。
导通孔数控钻孔方法的改进:
①数控钻床主轴转速由6万转/分→8万转/分→10∽12万转/分→16∽18万转/分→25万转动/分等。
②由整个主轴转动改为夹钻头系统转动,动能大大减小,明显降低震动性,提高了钻孔定位精度和质量。
③台面由丝杠移动改为线性马达,移动更快速,既降低了磨损又提高了稳定性。
④改变了了钻头组成与结构,减小WC颗粒直径(由2∽3µm→0.2∽0.3µm,甚至更小)。
⑵激光钻孔的迅速发展。
①红外激光钻孔。
②UV激光钻孔。
③混合激光钻孔。
各种钻孔方法适用围如下:
钻孔直径Φ0.8→ф0.5→φ0.3→ф0.2→ф0.15→φ0.10→φ0.05mm
←------数控钻孔---------------→
←---红外激光-----→
←--UV激光---→
⑶埋/盲空孔结构的出现。
①埋/盲孔结构。
②不连接的层之间没有导通孔,不设隔离盘,缩短导线和孔深,提高布线自由度。
③PCB提高密度至少1/3以上。
④改善电气性能。
⑷盘孔(HIL或HIP)结构的诞生。
①由“狗骨”结构改为盘连接结构。
②达到缩短连线,提高密度,改善电气性能等。
3.2.3板面平整度
由于元器件是贴装在PCB表面上,不仅要求整体板面有平整度,而且连接盘(焊盘)这样共面性。
⑴PCB翘曲度要求越来越小,从1.0%→0.7%→0.5%,甚至更小。
⑵连接盘要有好的共面性。
由HAL(或HASL)→OSP、化学镀Ni/Au、Ag、Sn等。
3.2.4PCB表面涂(镀)覆
PCB表面涂(镀)覆是指保护性和可焊性涂(镀)覆两部分。
⑴保护性涂(镀)覆。
这是指PCB非焊接部分的常规性保护与字符。
1阻焊膜(剂)涂覆。
它起到“一阻三防”的作用:
“一阻”即阻(防)止PCB在焊接时焊料的污染与桥接作用;“三防”即在PCB长期使用过程中起到防污染、防霉变和防潮湿等作用。
2字符涂覆。
它起到元器件安装位置和便于维修的作用。
⑵可焊性涂(镀)覆。
这是指保持或形成PCB连接(焊接)盘表面可焊性的涂(镀)覆层。
如HAL、OSP、电镀Ni/Au、化学Ni/Au、化学Ag、化学Sn等。
1热风(焊料)整平。
它是把PCB在制板浸入熔化的Sn/Pb焊料中,然后拉出经热风吹去(控制厚度)多余的焊料。
由于可焊性好,它在PCB可焊性涂覆中曾达到90%以上。
但随着SMT技术和高密度化的发展,目前已下降到50%以下,还会继续下降下去。
主要原因有如下几个方面。
ⅰSn/Pb焊料表面力太大,随着焊盘直径缩小(即高密度化),涂覆的焊料表面形成“龟背”状态,从而影响焊接可靠性。
ⅱSn/Pb焊料很薄时,如≤2µm则会形成不可焊的Cu3Sn2表面层。
2有机可焊性保护剂(OSP)。
它是一种耐热有机(烷基苯并咪唑类)化合物,大约300℃才会分解,它能与连接盘新鲜铜表面络合形成厚度为0.3∽0.5µm的保护层,保护了铜的可焊性。
由于很薄,能保持原有的共面性,加上操作简便,成本低,因此得到了广泛应用,目前已达到30%左右的份额。
但易于划伤,生产操作应格外小心。
3电镀镍/金。
这是在焊盘表面先镀镍后再镀金的可焊性镀层。
ⅰ镍层为阻挡(隔离)层,其厚度为3∽5µm(原为5∽7µm),阻止铜/金之间互相扩散(影响可靠性)。
ⅱ电镀金层。
其厚度应由使用条件或特征来决定。
★插头(金手指)镀金。
由于是反复使用插拔,金层不仅要求耐磨(镀硬
金),而且要求有较大的厚度(目前规定应大于0.5µm)。
★焊接用镀金。
由于焊接是在镍表面进行,金层是为了保护新鲜镍表面(不
被氧化)的,所以金层在保证镍表面不氧化条件下,金层应越薄越好。
这不仅可降低成本问题,更重要的是保证焊点可靠性(焊点的焊料中金的含量≥3%时,焊点容易脆断)问题。
★金属丝(WB)焊接用镀金。
由于金属丝(金丝或Al丝等)是直接焊接
在金层上的,因此要求有较厚的金层,一般应≥0.5µm。
由于电镀镍/金的电镀分散能力差,镀层厚度不均匀,成本也高,所以采
用此方法越来越少了。
④化学镀镍/金。
利用氧化/还原的化学方法沉积镍层厚度3∽5µm,然后再沉积金层厚度(由应用条件来决定)。
由于采用化学沉积,因而镀层均匀。
目前化学镀镍/金已迅速取代电镀镍/金。
其中化学镀镍工艺控制较难,应特别注意。
⑤化学镀银。
由于“绿色”环保要求,无铅焊料与焊接便摆在日程上来了,因
此,与焊料相对应的化学镀银或化学镀锡等开发和使用起来了。
化学镀银是PCB连接盘上化学沉积一层厚度为0.05∽0.5µm。
为了防止银层
腐蚀和银迁移,在化学镀液中加入特种添加剂,使镀层中含有1∽3%的耐热有机物,可经得起多次焊接过程。
但化学镀液中Cl+离子含量应小于5ppm;避免与卤化物接触,否则会使表面发黄,影响外观与可焊性;防止与硫化物接触,否则会使表面呈黑色,同样影响外观与可焊性;成品应采用无硫纸包装。
所以化学镀银的PCB产品应优先与及时处理。
6化学镀锡。
由于所有焊料是以锡为主体的,所以锡镀层能与任何类型焊料相兼
容,化学镀锡是PCB表面涂(镀)覆技术最有发展前途的。
近几年来,由于镀锡溶液中加入新型添加剂,沉积锡层由树枝状结构变成含有
少量有机物的颗粒状结构,其厚度为0.8∽1.2µm之间。
由于它具有好的热稳定性,即使经过多次焊接过程,也不会形成不可焊结构化合物。
同时,它也不会形成锡丝和锡迁移问题。
3.3芯片级封装的PCB概况
3.3.1芯片级封装的PCB又可称封装基板。
它要求全面走向甚高的高密度化程度,主要特点是逐步而迅速走向HDI/BUM板和集成元件PCB。
⑴导通孔走向微孔化。
导通孔直径将≤150µm,并走向ф100→ф70→ф50→ф30→ф20(µm)。
全面走向激光钻孔,并以UV激光钻孔为主导。
⑵导线走向精细化。
如下表所示。
IC线宽和PCB线宽的进步与比较
年份
IC线宽(µm)
PCB线宽(µm)
比率
1970
3
300
1:
100
1985
1
200∽100
1:
200∽1:
100
2000
0.18
100∽30
1:
560∽1:
170
2005
0.10
50∽20
1:
500∽1:
200
2010
0.05
10(HDI/BUM板)
1:
200
要逐步走向采用激光直接成像(LDI)技术或集成电路加工技术来制造PCB,同时提高制作房间净化度也变得十分重要。
⑶介质层厚度走向超薄化。
由100→80→50→30→20→10(µm)。
同时由刚性(玻纤布增强的树脂材料)基材走向挠性(无增强的树脂)基材。
3.4系统封装(SIP)的PCB概况
系统封装(SIP)的PCB还处于明芽和试用的阶段。
它不仅把大量的无源元件埋入PCB部,而且也把有源元件装入到PCB部,从而具有独立系统功能的部件,因而具有密度更高、速度更快、功能更全(强)和可靠性更高的系统装置(有关这方面的较详细技术请参阅【印制电路信息】2004年2月第3∽11页)。