褐煤干燥项目采用的工艺.docx
《褐煤干燥项目采用的工艺.docx》由会员分享,可在线阅读,更多相关《褐煤干燥项目采用的工艺.docx(34页珍藏版)》请在冰豆网上搜索。
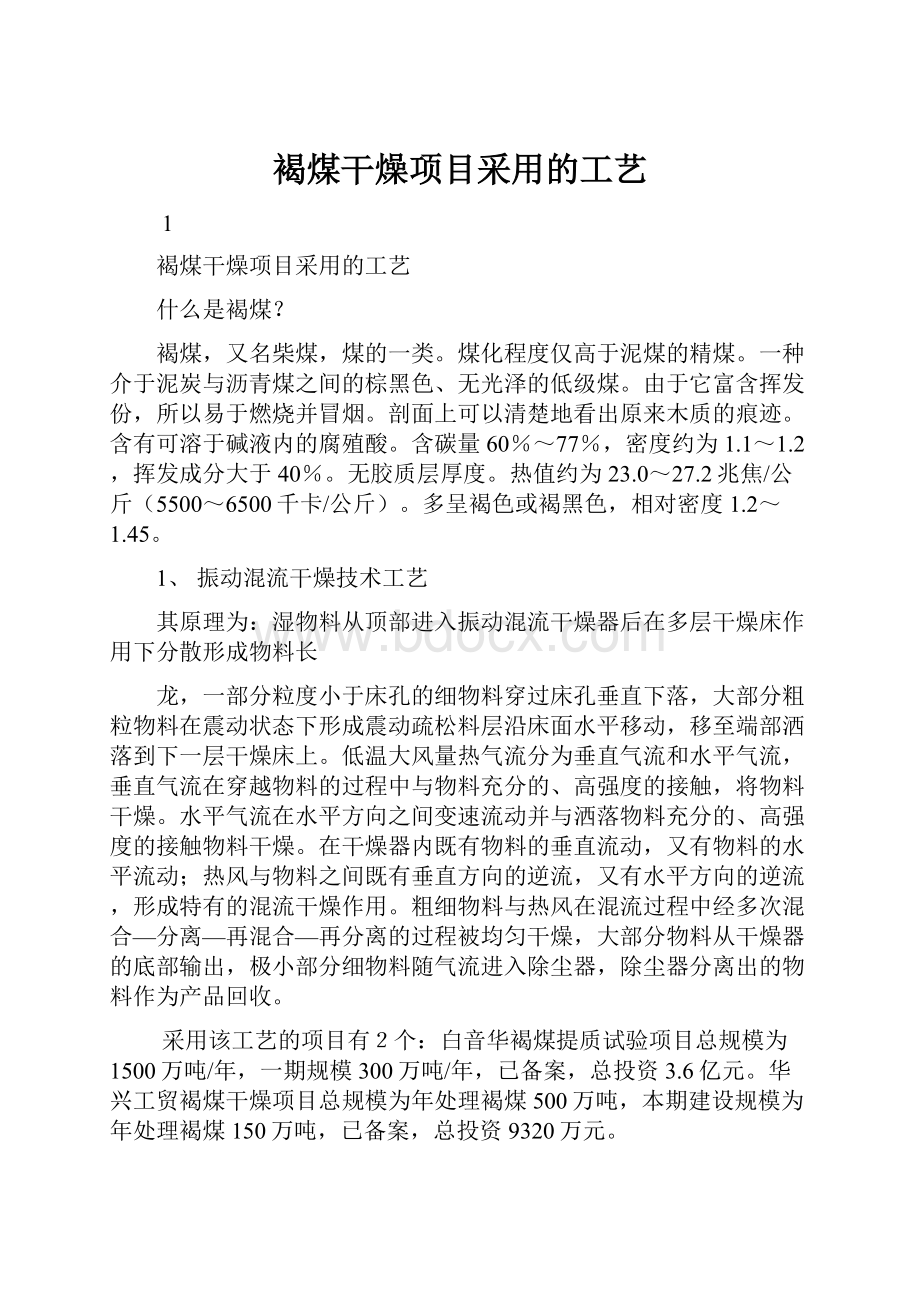
褐煤干燥项目采用的工艺
1
褐煤干燥项目采用的工艺
什么是褐煤?
褐煤,又名柴煤,煤的一类。
煤化程度仅高于泥煤的精煤。
一种介于泥炭与沥青煤之间的棕黑色、无光泽的低级煤。
由于它富含挥发份,所以易于燃烧并冒烟。
剖面上可以清楚地看出原来木质的痕迹。
含有可溶于碱液内的腐殖酸。
含碳量60%~77%,密度约为1.1~1.2,挥发成分大于40%。
无胶质层厚度。
热值约为23.0~27.2兆焦/公斤(5500~6500千卡/公斤)。
多呈褐色或褐黑色,相对密度1.2~1.45。
1、振动混流干燥技术工艺
其原理为:
湿物料从顶部进入振动混流干燥器后在多层干燥床作用下分散形成物料长
龙,一部分粒度小于床孔的细物料穿过床孔垂直下落,大部分粗粒物料在震动状态下形成震动疏松料层沿床面水平移动,移至端部洒落到下一层干燥床上。
低温大风量热气流分为垂直气流和水平气流,垂直气流在穿越物料的过程中与物料充分的、高强度的接触,将物料干燥。
水平气流在水平方向之间变速流动并与洒落物料充分的、高强度的接触物料干燥。
在干燥器内既有物料的垂直流动,又有物料的水平流动;热风与物料之间既有垂直方向的逆流,又有水平方向的逆流,形成特有的混流干燥作用。
粗细物料与热风在混流过程中经多次混合—分离—再混合—再分离的过程被均匀干燥,大部分物料从干燥器的底部输出,极小部分细物料随气流进入除尘器,除尘器分离出的物料作为产品回收。
采用该工艺的项目有2个:
白音华褐煤提质试验项目总规模为1500万吨/年,一期规模300万吨/年,已备案,总投资3.6亿元。
华兴工贸褐煤干燥项目总规模为年处理褐煤500万吨,本期建设规模为年处理褐煤150万吨,已备案,总投资9320万元。
评论:
唐山市神州机械有限公司的SZ振动混流干燥系统设备入口烟气温度低于200度,应该是安全的。
但是产量太小,能耗和设备投资太高,因为温差太小。
并且只能脱除表面水,无法脱除结合水。
以最大流化面积40平米,处理量为200吨每小时,而最大脱水量为15吨每小时。
如果初水分为35%,而干燥后的水分至少为30%。
2、滚筒干燥工艺
其原理为:
原煤仓中的原煤(常温)通过给料机进入干燥机的滚筒,在干燥滚筒入口与
热风炉提供的烟气混合(约650℃)。
在转动的滚筒内,有滚筒壁上的扬料板使物料在干燥筒体内行程稳定的全断面料幕,使烟气与原煤充分交换热量,交换时间在25~35分钟左右。
2
滚筒末端的干燥煤温度上升为60℃,烟气温度下降到120℃左右。
采用该工艺的项目有2个:
东苏旗褐煤干燥项目总规模为年处理褐煤450万吨。
已备案。
春成集团褐煤干燥项目总规模为年处理褐煤500万吨。
已备案,总投资9961.11万元。
评论:
见图片,与海拉尔的工艺一样。
海拉尔的设备在调试时发生爆炸。
3、SJ—Ⅳ低温干馏炉工艺
其原理为:
从备料工段供煤到SJ—Ⅳ低温干馏方炉炉顶布料皮带机,布料皮带机将煤料
加入炉顶煤仓中,煤料通过辅助煤箱进入干馏方炉内,煤料下移经过干燥段逐渐进入干馏段完成煤干燥,干馏后的煤继续下移到冷却段,最后由炉底推焦机、刮板机排出。
采用该工艺的项目有:
北方电力褐煤提质项目。
该项目由北方联合电力公司投资建设,总规模为年处理褐煤400万吨,已备案,总投资6亿元。
4、美国褐煤轻度热解干燥提质(LFC)工艺
其原理为:
经过破碎和筛分后的原煤(启水量约33.87%wt)送入干燥炉中,
用来自干燥热风炉的热气流加热脱水,出干燥炉的原煤含水量降到约4%(wt)。
干燥热风炉的燃料为热解气,补充燃料来自LNG。
干燥炉入口加热气体在干燥器内的停留时间和温度的必须严格控制,以满足如下要求:
能够脱除煤炭中水分且不会引起化学变化。
原煤温度也需严格控制以确保不会释放大量的甲烷、二氧化碳和二氧化碳。
离开干燥炉的褐煤进入热解炉。
在热解炉中,用来自热解燃炉的热循环气流(温度约527℃)作为加热介质。
褐煤固体的加热速率、温度和热循环气流的流速都需严格控制,因为这些参数将直接影响固体和液体质量的质量和组成。
煤中的剩余水分被完全脱除,并在热解炉中发生了轻度的气体反应,煤中的挥发性气体物质被释放出来。
从热解炉中出来的固体先在激冷盘中用工艺水快速冷却以中止热解反应,然后输送到PDF冷却和精制系统。
采用该工艺的项目有:
大唐华银东乌褐煤干燥示范装置项目。
年处理褐煤30万吨,已备案,总投资3.44亿元。
5、北京柯林斯达技术工艺
其原理为:
入场原料煤首先进入一级破碎机,将其破碎至150mm一下,经过一级破碎
3
的
原煤进入手选胶带输送机进行拣矸,经过拣矸的煤进入二级破碎机,将其破碎至25mm一下,二级破碎后的原煤进入分机筛(筛孔为13mm)进行分级,小于13mm的末煤进入燃料仓,13~25mm的块煤进入块煤仓。
块煤经电子皮带称定量给料机给入布料机,布料机将块煤均匀分布到改性炉带体,依次经过升温、改性、冷却后运出炉外形成产品。
末煤由电子皮带称定量给料机给入热风炉,燃烧后的热风进入改性炉作为改性热煤。
采用该工艺的项目有:
蒙元煤炭褐煤改性提质加工项目总规模为年处理褐煤270万吨。
已备案。
总投资9984万元。
评论:
这种工艺着火和爆炸的可能性比滚筒干燥工艺更大
6、鲁奇三段炉工艺
其原理为:
由备煤工段运来的合格装炉煤首先装入炉顶最上部的煤仓内,再经进料口和
辅助煤箱装入炭化室内。
加入炉内的块煤向下移动,与送入炉内的加热气体逆向接触,并逐渐加热升温,煤气经上升管从炉顶导出,炉顶温度应控制在80~100℃。
自炉内出来的荒煤气,经过冷却洗涤,冷却后气液分离,冷却下来的液体经管道流到循环水池,通过静置沉淀油水分离,焦油由泵打到焦油贮槽,循环水经管壳式换热器换热冷却后循环使用,循环水池封闭运行。
从干馏炉炉底排出的半焦,因半焦水分较高需要进行干燥,烘干所需热量由干馏炉自产剩余煤气燃烧供给。
烘干后的半焦进行筛分,成品焦由皮带运输机送到焦场堆放储存。
采用该工艺的项目有:
锡林河褐煤提质项目总规模为年处理褐煤90万吨,已备案,总投资9800万元。
7、国能富通干燥炉工艺
其原理为:
原煤从储煤斗经过布煤器进入预热干燥段,被自下而上的干燥气预热至170℃左右,将原煤中的外在水分降至1%以下。
干燥段温度必须严格控制;能够脱除煤中水分且不会发生化学反应。
干燥煤经过中间段进入深度干燥段,和自下而上的热载体换热,达到500℃,去除煤中的内在水、结晶和化合水,并降低干燥煤的挥发分,将煤深度干燥成
4
提质煤。
深度干燥生成的煤气随热载体一起从集气降伞引出。
提质煤下降到冷却段,被冷烟气冷却到150℃。
提质煤在进入输煤皮带时,用深度干燥段生成的废水对提质进行喷淋降温,使成品煤中水分含量与大气水分含量达到平衡,有效防止提质煤返水,同时煤的温度降到50~60℃。
另外喷淋还防止了提质煤输出过程中粉尘气扬;提质煤送到矿区成品煤堆放场。
采用该工艺的项目有:
大唐国能褐煤干燥项目年处理褐煤250万吨,已备案。
总投资9735万元。
煤炭液化
煤炭是一种碳含量高、但氢含量只有5%的固体。
与液体燃料(从原油中提取的)相比,煤炭不便于处理和运输。
通过脱碳和加氢,煤炭可以直接或间接转化成适于运输的液体燃料,其中一种方法是焦化或热解,另外一种方法是液化。
由于将煤炭转化成液体燃料的成本比提炼原油的成本高,但原煤本身的价格比较低廉,这是煤炭液化技术能够付诸实施的一个主要激励因素。
随着石油储量的逐渐减少,可以预见在未来的一定时期,将需要替代性液体燃料。
由于全球的煤炭储量极其丰富,煤炭液化是其中之一。
早在70年代初,由于国际油价暴涨,美国、英国和日本等国家就开始进行大量的煤炭液化技术研究和开发。
从80年代开始,大部分煤炭液化项目被搁置起来,但南非例外。
原因是南非没有石油和天然气资源,仅有丰富的煤炭资源,另外,到80年代中期为止,南非受到了30年的贸易禁运,这些因素促使南非大规模采用煤炭液化产品。
目前,南非60%的运输燃料是由煤炭提供的。
许多不同的直接液化工艺已被开发出来,但就所进行的化学反应而言,它们密切相关。
这些液化工艺的共同特征是,先将大量的煤粉放入溶剂中,在高温高压的条件下进行溶解,然后将溶解的煤炭在氢气和催化剂的作用下进行加氢过程。
5
直接液化是目前可采用的最有效的液化方法。
在合适的条件下,液化油收率超过70%(干燥无矿物质煤)。
如果允许热量损失和其它非煤能量输入的话,现代液化工艺总热效率(即转化成最终产品的输入原料的热值比例,%)一般为60~70%。
这些工艺一般发展到工艺开发单元(processdevelopmentunit)或试验性阶段,并且主要的技术问题已得到解决。
但是,目前没有示范厂或商业化厂建成运转。
煤炭间接液化的唯一正在运转工艺是南非的Sasol工艺,目前已经建成了三座生产厂。
间接液化的唯一核心技术是合成反应段,因此最近的主要工作集中在开发先进的催化剂上,催化剂不限于某一具体工艺。
从1985年以后,由于石油的价格较低,人们对用于生产运输燃料的煤炭液化的兴趣下降。
目前,只有日本还在积极进行大规模的煤炭液化工艺的研究,并且还有一座150t/d规模的装置正在运转。
由于中国目前逐渐成为一个净石油进口国,而且潜在的产油区地理位置偏僻,因此中国有发展煤炭液化的强烈愿望。
中国正在分别与美国、日本和德国合作进行煤炭液化的可行性研究。
焦化和热解作用
高温焦化技术是一种最原始的生产液体的方法,烃类液体作为炼焦过程的副产品。
由于高温焦化过程生产的液体含量较低(<5%),且液化成本高,因此传统的高温焦化工艺不能满足商业化生产液体燃料的需要。
温和热解也是一种焦化技术,但操作条件相对不太苛刻。
温和热解工艺包括:
将煤加热到450~650℃的高温(高温焦化工艺中的温度高达950℃),在热分解的过程中赶出原煤中的挥发性物质,在处理过程中,通过热分解生成其它挥发性有机化合物。
温和热解工艺中的液体燃料产量比高温焦化工艺要高,但至多仍不超过总产量的15~20%。
主要产物中降低了氢和杂原子的含量。
美国在这一工艺的研究处于世界领先水平,主要是通过将煤
6
中的氧以二氧化碳的形式脱除,并减少硫含量的途径提高低阶次烟煤和褐煤的性能,提高其发热量。
目前至少有一种液化工艺已经达到半商业化生产的规模。
考虑到这些技术对燃料加工所带来的巨大市场前景,我们可以认为,尽管这些工艺的液体燃料产率较低,但它们必将对全球液体燃料的供应产生重大的贡献。
通过快速热解的途径可以获得较高的液体燃料产率。
这些工艺的操作温度可达到1200℃,但煤的停留时间大大缩短,至多为几秒钟。
快速热解工艺主要是为了生产化工原料而不是液体燃料,原因是从经济上讲生产液体燃料是不合算的。
快速热解工艺可能还存在未解决的工程问题。
所有的热解和焦化工艺都存在这样一个缺点,如果原料煤中的氢含量提高到可蒸馏液体的程度时,残留固体中的氢含量必须被减少。
所生产的液体燃料的质量仍然比较低,需要采取专门的处理措施来清除固体杂质和水分。
经这样处理后的液体产品可以掺合生产加热燃料和固定式涡轮机用的燃料。
如果原产品不混合来使用,或者被用作运输燃料,仍需要进一步的处理。
需要混合和传统的精制加工使液体产品经济可行。
但目前这一设想还没有成功地付诸实施。
最近,人们的兴趣集中在美国开发的煤的提质加工工艺上。
至少有三项技术已经达到了中试规模。
这些工艺的主要不同之处在于热解反应器的设计上。
其中煤炭制取液体燃料(LiquidsfromCoal,LFC)工艺自1992年已经投入商业化生产。
LFC工艺是由SGI国际公司研制的一种旨在改善煤炭性能的温和热解方法。
可生产两种可销售产品:
一种是被称为工艺衍生燃料(process-derivedfuel,PDF)的低硫、高热值固体;另一种是被称为煤炭衍生液体
7
(coal-derivedliquid,CDL)的烃类液体。
PDF的产量远远大于CDL的产量。
图2Encoal公司开发的LFC工艺
Encoal公司拥有的第一座示范厂建在怀俄明州Gillette附近,该示范厂得到了美国能源部洁净煤技术示范项目的支持。
示范厂于1992年投产,原料煤是波德河煤田生产的低硫高水分次烟煤,最大日处理能力为1000t。
煤炭被粉碎和筛选,然后在一个旋转的篦式干燥器上被热气加热。
对这些固体原料的温度控制非常重要,因为加热的目的就是为了减少原料中的水分,而不能导致其结构的改变,从而尽量把早期气产率降为最低限度。
被干燥后的煤随后进入主旋转篦式热解器,被循环的高温气流加热到540℃。
此时,精确控制固体原料的加热速度和停留时间至关重要,因为这些参数影响着产品性能。
固体原料被从热解器中排出之后,进行冷却,然后经过钝化处理,其中包括经过振动流化床,被含有固定氧含量的气流处理。
PDF产品经过轻度的氧化之后便稳定下来,避免了随后发生自燃现象的危险。
离开热解器的气流被在一个急冷塔中冷却,CDL冷凝,水分留在气相中。
经过冷却的大部分气体被重新循环进入热解器中,一部分气体被在热解燃烧
8
器中进行燃烧,产生工艺过程所需要的热量。
剩余的气体进入干燥燃烧器中被燃烧,加入干燥器的气体循环过程中。
气体中的颗粒杂质和硫氧化物被使用湿式涤气方式从气体循环过程中除去。
涤气器中吹扫液体被排到池中蒸发。
经过适度氧化之后,生成的PDF产品是一种低硫反应性燃料,适合用于粉煤喷吹燃烧锅炉,因此将经过铁路运到各电站;另外生成的CDL性能相当于6号燃料油,也被经过铁路运到燃料油销售商。
1996年,SGI公司与印度尼西亚、日本和中国签定合同,准备在这些国家建立商业化LFC示范厂。
1997年,该公司宣称将在美国建立一座600万t/年规模的工厂。
1、直接液化
直接液化工艺旨在向煤的有机结构中加氢,破坏煤结构产生可蒸馏液体。
目前已经开发出多种直接液化工艺,但就基本化学反应而言,它们非常接近,共同特征是:
在高温和高压的条件下在溶剂中将较高比例的煤溶解,然后加入氢气和催化剂进行加氢裂化过程。
直接液化是目前可使用的最有效的液化方式。
在合适的条件下,液体产率超过70%(以干燥、无矿物质煤计)。
如果允许热量损失和其它非煤能量输入的话,采用现代化的液化工艺时总热效率(即转化成最终产品的输入原料的热值比例,%)一般为60~70%。
直接液化工艺的液体产品比热解工艺的产品质量要好得多,可以不与其它产品混合直接用作大部分固定式燃料。
但是,直接液化产品在被直接用作运输燃料之前需要进行提质加工,采用标准的石油工业技术,让从液化厂生产出来的产品与石油冶炼厂的原料混合进行处理。
根据煤的溶解步骤是否与溶解后的煤再转化成可蒸馏的液体产品步骤分开,直接液化工艺可被分为以下两类:
·单段直接液化工艺该工艺是通过一个主反应器或一系列反应器来生产蒸馏组分
9
的。
这种工艺包括一个合在一起的在线加氢反应器,对原始馏分提质,而不能直接提高总转化率。
·两段直接液化工艺该工艺是通过两个反应器或一系列反应器来生产馏分的。
其中第一段的主要目的是进行煤的溶解,不加催化剂或只加入低活性的可弃催化剂。
第一段生产的重质煤液体在第二段中在高活性催化剂的作用下加氢,生产出馏分。
另外,有些工艺专门设计用于煤和石油衍生油共处理,也可以划到这两种工艺中去。
同样,上述两种液化工艺都可改进用来共处理。
1.1单段液化工艺
60年代中后期,煤炭液化技术得到了人们的重视,全部的液化工艺均为单段液化工艺,大部分的液化研究项目也集中在单阶段液化工艺上。
70年代发生了世界范围的石油危机,一些研究人员增加了第二段的研究工作,以提高轻质油的产量。
单段液化工艺主要包括:
·Kohleoel液化工艺(德国鲁尔煤炭公司)·NEDOL液化工艺(日本新能源产业技术开发
·H-煤液化工艺(美国HRI公司)·Exxon供氢溶剂液化工艺(即EDS工艺,美国Exxon)
·SRC-I和II液化工艺(美国海湾石油公司)·Imhausen高压液化工艺(德国)
·Conoco氯化锌液化工艺(美国Conoco公司)
上述大部分液化工艺已经被淘汰,但Kohleoel和NEDOL液化工艺目前仍被广泛采用,开发商准备对这两种液化工艺进行商业性生产。
另外,美国目前还研制了其它几种较小规模的液化工艺。
俄罗斯和波兰等其它国家也进行了大量的单段煤炭液化工艺的研发工作,所采用的方法在许多方面与Kohleoel液化工艺类似。
10
1.1.1Kohleoel液化工艺
Kohleoel液化工艺(见图3)联合原油精炼工艺(IntegratedGrossOilRefining,IGOR+)在1945年德国商业化规模工艺基础上,由RuhrkohleAG和VEBAOELAG公司近期开发而成。
开发经历了Bergbau-Forschung(目前的DMT)0.5t/d、0.2t/d连续运转和到Bottrop的200t/d规模。
其中在Bottrop的液化厂生产期间为1981~1987年,设备运转时间2.2万小时,处理了17万t煤,生产了8.5万t馏出产品。
因此,该液化技术被认为完全可行。
图3Kohleoel液化工艺
1997年,中国煤炭科学研究总院(CCRI)与德国签定了两年的合作协议,进行一项5000t/d的示范厂可行性研究。
研究人员在云南省考察了液化厂址,并对液化产品的市场前景进行了调查。
煤与工艺衍生循环溶剂和赤泥可弃铁催化剂配成煤浆,并进行加压和预热。
随后加入氢气。
然后,混合物进入一个液体向上流动的管式反应器,煤加料速度为0.5~0.65t/h·m3,反应器内的压力为300br,温度为470℃。
从反应器顶部出来的产品进入到一个高温分离器中。
分离器顶部的馏分保留在气相中,在一个固定床反应器中进行加氢,固定床的压力与主反应器的压力一样,温度为350~420℃。
加氢处理后的产品分两段进行减
11
压和冷却。
其中第一段的液体产品被循环到煤浆段,作为溶剂使用。
第二段生产的液体产品在常压下进行蒸馏,可生产轻质油(C5~200℃,沸点)和中质油(200~325℃,沸点)。
高温分离器底部产品进入减压蒸馏塔,以回收可蒸馏的液体。
这些液体被作为加氢反应器的原料,大部分被循环作为溶剂。
减压蒸馏塔底部的残余物含有沥青、矿物质、未反应的煤和催化剂。
在商业化运转中,这些残余物可以作为气化器的原料,用来生产氢气。
当对烟煤进行液化时,煤的转化率可大于90%,液体收率为50~60%(干基无灰煤)。
表1列出了德国的Prosper次烟煤进行液化的产量和质量。
表1Kohleoel液化工艺产率和产品质量(Prosper煤为原料)
产品种类产率(%)
烃类气体(C1~C4)19.0轻质油(C5-200°C)25.3中质油(200~325°C)32.6未反应的煤和沥青22.1
产品质量轻质油中质油
氢含量(%)13.611.9氮(ppm)39174氧(ppm)15384硫(ppm)12
<5
12密度kgm-772912
1.1.2NEDOL液化工艺
从1978~1983年,在日本政府的倡导下,日本钢管公司、住友金属工业公司和三菱重工业公司分别开发了三种直接液化工艺。
所有的项目是由新能源产业技术机构(NEDO)负责实施的。
1983年,所有的液化工艺以日产0.1~2.4t不同的规模进行了试验。
NEDO不再对每个工艺单独支持,相反将这三种工艺合并成NEDOL液化工艺(见图4),主要对次烟煤和低阶烟煤进行液化。
有20家公司合并组成了日本煤油有限公司,负责设计、建造和经营一座250t/d规模的小型试验厂。
但是,该项目于1987年由于资金问题被迫搁置。
一座1t/d的工艺支持单元(PSU)按计划于1988年安装投产,项目总投资3000万美元,由于各种原因该项目进展得断断续续。
1988年,该项目被重新规划,中试规模液化厂的生产能力被重新设计为150t/d。
新厂于1991年10月在鹿岛开工,于1996年初完工。
从1997年3月~1998年12月,日本又建成了5座液化厂。
这5座液化厂对三种不同品种的煤(印度尼西亚的TanitoHarum煤和Adaro煤以及日本的Ikeshima煤)进行了液化,没有太大问题。
液化过程获得了许多数据和结果,如80天连续加煤成功运转,液化油的收率达到58wt%(干基无灰煤),煤浆的浓度达50%,累计生产时间为6200小时。
13
图4NEDOL液化工艺
中国煤炭科学研究总院与日本新能源产业技术开发机构和煤炭利用中心签定了合作协议,准备进行一座5000t/d的液化示范厂建设的可行性研究。
利用依兰煤进行了实验室和PSU装置上完成了几个试验。
据预测,油收率将达到62%。
产自黑龙江省的一种黄铁矿被作为催化剂。
项目的下一阶段将进行工艺评价、环境影响评价和经济效益分析,按计划于2000年完成。
在合成的铁系催化剂的重量比为2~4%的条件下,煤被研磨,并与循环溶剂配成煤浆。
煤浆与氢气混合,预热,然后进入主反应器中。
该主反应器是一个简单的管式液体向上流动的反应器,操作温度为430~465℃,压力为150~200bar。
煤浆标称平均停留时间为1个小时,而实际的液相煤浆平均停留时间为90~150分钟。
从主反应器中出来的产品被冷却、减压后至常压蒸馏塔,除去轻质产品。
常压蒸馏后的残余物经过减压蒸馏塔,此时中质馏分和重质馏分被除去。
大部分的中质油和全部的重质油经加氢后被循环作为溶剂。
减压塔底部的残余物中包括未发生反应的煤、矿物质和催化剂,这些残余物被排除掉。
在商业化运转中,这些残余物可以作为气化器的原料,用来生产氢气。
在最终产品中固体含量可达到50%,一般情况下为35%。
由于沥青与固体一起排放会导致产品的损失,因此该液化工艺限制在灰分含量较低的煤种。
14
从减压蒸馏塔中生产出的中质和重质油被混合之后,进入溶剂再加氢反应器。
这些反应器是流体向下流动的催化剂填充床反应器,其中的温度为320~400℃,压力为100~150bar。
所使用的催化剂是传统石油工业加氢脱硫催化剂的变种。
标称的停留时间为1小时。
从反应器中出来的产品被减压后进入闪蒸塔中,此时加氢后的石脑油将被除去。
闪蒸产生的液体产品将被作为溶剂循环到煤浆混合段。
使用不同的煤进行液化时,产品的收率将发生变化,通过调整主反应器中的工作条件尽量减小这种变化。
对所有煤种而言,馏出产品的收率为50~55%(干基无灰煤)。
与其它液化工艺相比,该液化工艺的液体产品的质量较低,需要进一步的提质加工,但这并不表示出现了新的技术难题。
H-煤液化工艺
H-煤液化工艺(见图5)是由HRI公司(即目前的Hydrocarbon技术公司,HTI)根据商业化的用于改善重质油性能的H-油工艺研制的。
根据H-煤液化工艺,美国于1980年在肯塔基州的Catlettsburg建造了一座200t/d的中试厂。
该试验厂一直生产到1983年。
随后,美国设计了一座可进行商业化生产的液化厂,准备建在肯塔基州的Breckinridge。
美国能源部资助的大部分液化项目是以H-煤液化工艺为基础的,该工艺也被有效地应用到催化两段液化(CTSL)工艺中。
15
图5H-煤液化工艺的流程简图
煤与循环溶剂混合配成煤浆,循环溶剂中包括加氢反应器中产生的含有固体的产品以及蒸馏时产生的重质和中质馏分。
然后加入氢气,混合物被预热后进入沸腾床加氢反应器,反应器是该液化工艺的一个独特之处。
反应器的工作温度为425~455℃,工作压力为200bar。
该反应器使用常规的载体加氢催化剂,可以使用以铝为载体的