基于单片机的工业电阻炉智能温度控制系统设计毕业设计论文.docx
《基于单片机的工业电阻炉智能温度控制系统设计毕业设计论文.docx》由会员分享,可在线阅读,更多相关《基于单片机的工业电阻炉智能温度控制系统设计毕业设计论文.docx(48页珍藏版)》请在冰豆网上搜索。
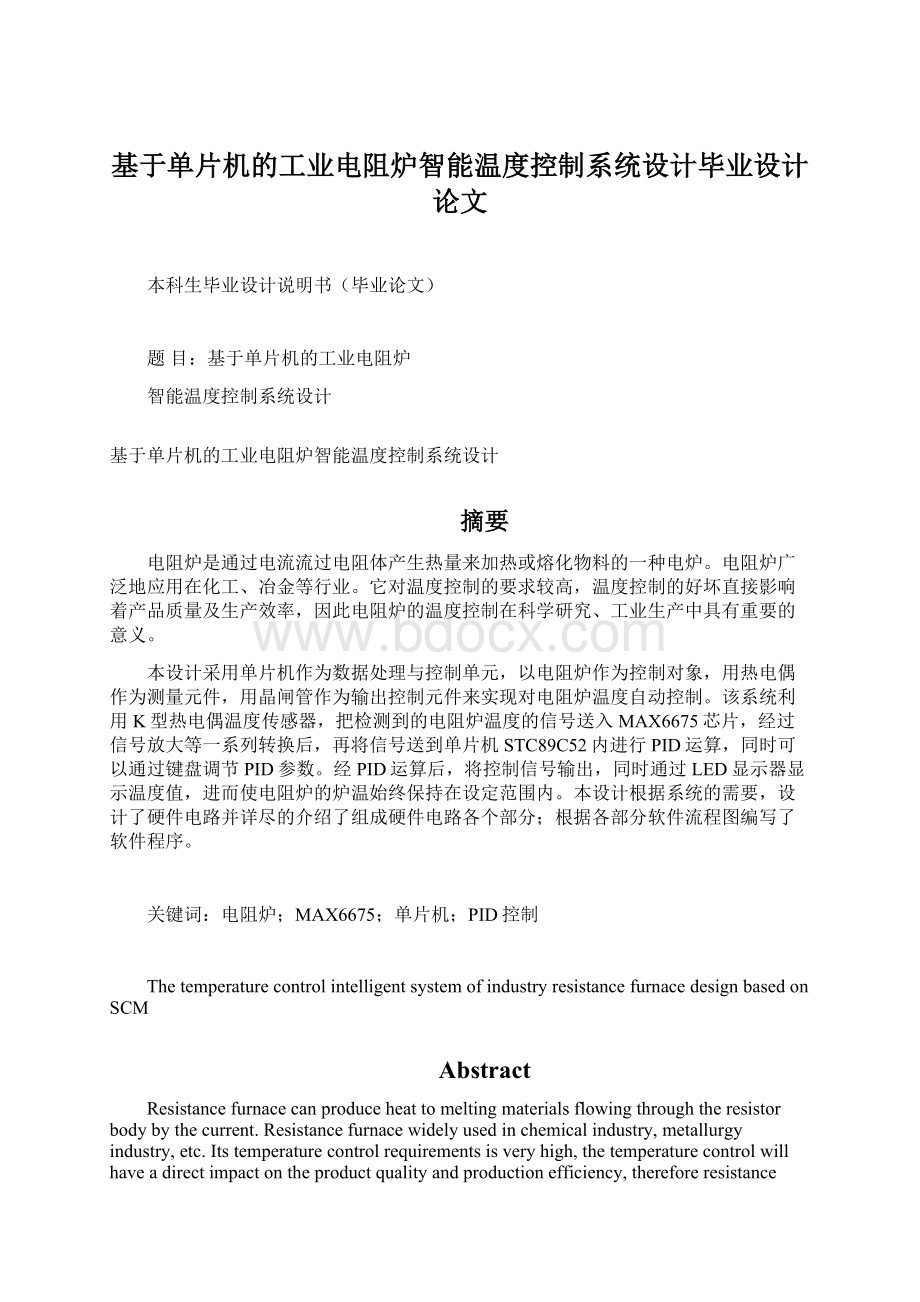
基于单片机的工业电阻炉智能温度控制系统设计毕业设计论文
本科生毕业设计说明书(毕业论文)
题目:
基于单片机的工业电阻炉
智能温度控制系统设计
基于单片机的工业电阻炉智能温度控制系统设计
摘要
电阻炉是通过电流流过电阻体产生热量来加热或熔化物料的一种电炉。
电阻炉广泛地应用在化工、冶金等行业。
它对温度控制的要求较高,温度控制的好坏直接影响着产品质量及生产效率,因此电阻炉的温度控制在科学研究、工业生产中具有重要的意义。
本设计采用单片机作为数据处理与控制单元,以电阻炉作为控制对象,用热电偶作为测量元件,用晶闸管作为输出控制元件来实现对电阻炉温度自动控制。
该系统利用K型热电偶温度传感器,把检测到的电阻炉温度的信号送入MAX6675芯片,经过信号放大等一系列转换后,再将信号送到单片机STC89C52内进行PID运算,同时可以通过键盘调节PID参数。
经PID运算后,将控制信号输出,同时通过LED显示器显示温度值,进而使电阻炉的炉温始终保持在设定范围内。
本设计根据系统的需要,设计了硬件电路并详尽的介绍了组成硬件电路各个部分;根据各部分软件流程图编写了软件程序。
关键词:
电阻炉;MAX6675;单片机;PID控制
ThetemperaturecontrolintelligentsystemofindustryresistancefurnacedesignbasedonSCM
Abstract
Resistancefurnacecanproduceheattomeltingmaterialsflowingthroughtheresistorbodybythecurrent.Resistancefurnacewidelyusedinchemicalindustry,metallurgyindustry,etc.Itstemperaturecontrolrequirementsisveryhigh,thetemperaturecontrolwillhaveadirectimpactontheproductqualityandproductionefficiency,thereforeresistancefurnacetemperaturecontrolhasanimportantmeaninginscientificresearchandindustrialproduction.
Thisdesignusesthesinglechipmicrocomputerasthedataprocessingandcontrolunit,theresistancefurnaceascontrolobject;thethermocouplesusedasmeasuringelement,SCRastheoutputcontrolelementstoachieveresistancefurnacetemperatureautomaticcontrol.ThesystemusesKthermocoupletemperaturesensortype;itsenttheexaminationoftheresistancefurnacetemperaturesignalintoMAX6675chip,throughaseriesofamplificationafterconversion,thereforesendasignaltoSTC89C52microcontrollerwithinthePIDoperation,butalsoregulationPIDparametersthroughthekeyboard.AfterthePIDoperation,sentthesignalofcontroloutput,andshowstemperaturethroughLEDdisplayatthesametime,andremainsthetemperatureofresistancefurnaceinsetrange.Thisdesignaccordingtotheneedsofthesystem,designthehardwarecircuitanddetailedintroducesthehardwarecircuitofeachpart;thisdesignwritesoftwareprogramaccordingtoeachpartofthesoftwareflowchart.
Keywords:
Theresistancefurnace;MAX6675;Single-chipmicrocomputer;PIDcontrol
第一章绪论
1.1课题研究的背景及意义
20世纪20年代以来,电阻炉就在工业生产中得到了广泛地应用。
随着社会的发展,科学技术的进步,电阻炉被大量的应用在电力、冶金、机械、石油化工等工业生产中。
在这些工业生产中,温度的测量及控制影响着生产安全、产品质量、生产效率等重要的技术经济指标,电阻炉温度控制的稳定性、精度、可靠性等要求也逐步提高。
而在各个领域测温仪器的实际应用表明,智能化仪器已经是现代电阻炉温度控制系统发展的主要方向[1]。
基于此,设计一种智能化的电阻炉温度控制系统有广泛的应用前景及实际意义。
电阻炉是利用电流流过电阻体,使其产生热量来加热或熔化物料的一类电炉。
它的特点是:
①电路简单;
②对炉料种类的限制较少;(小型电阻炉可用来加热食品、干燥木材);
③炉温控制精度高;
④容易在真空中加热等特点。
它主要作用于:
①机械零件的淬火、退火、渗碳等热处理;
②各种材料的干燥、加热、烧结、熔化等。
电阻炉的参数有工作空间尺寸、额定温度、额定电压、额定功率。
电阻炉按炉温不同可分为低温电阻炉(600~700℃以下)、中温电阻炉(700℃~1200℃)、高温电阻炉(1200℃以上)[2]。
电阻炉的温度控制主要有:
1、传统PID控制;2、智能控制。
PID控制温度系统的效果,主要取决于P、I、D三个参数。
PID控制对于确定了的温度系统控制效果较好,但是对控制大惯性、大滞后、时变性温度系统则难以保证其控制品质。
电阻炉大多是经电阻丝加热升温,自然冷却降温的,当电阻炉的温度超调时,无法靠控制手段降温,所以电阻炉温度的控制具有滞后性、非线性、惯性、不确定性等特点。
目前国内较成熟的电阻炉温度控制系统中,以PID控制器为主。
PID控制器对小型实验用的电阻炉控制效果良好,但对于大型工业用电阻炉,就难以保证电阻炉温度控制系统的稳定性及精度等问题。
智能控制是一种不需要人操作就能驱动智能机械来实现其目标的自动控制。
随着科学技术、控制理论的发展,国外的温度控制系统发展很迅速,基本实现对温度的智能控制。
被广泛应用的温度智能控制方法有:
模糊控制、神经网络控制、专家系统等。
具有自适应、自协调、自学习等能力,使控制系统的控制精度、稳定性、抗干扰能力等性能得到保证[4]。
本文以电阻炉为控制对象,以单片机STC89C52为硬件核心元件,采用PID控制,该系统硬件电路设计简单、控制算法成熟稳定、系统性能优良。
1.2电阻炉的应用与发展
整体上,我国的电阻炉控制系统比国外发达国家要落后四、五十年,占主导地位的是模拟仪表控制,这种系统的控制参数由人工选择,需要配置专门的仪表调试人员,费时、费力且不准确。
控制精度依赖于试验者的调节,控制精度不高,一旦生产环境发生变化就需要重新设置,操作不方便,控制数据无法保存。
因而,对生产工艺的研究很困难,造成产品质量低、废品率高、工作人员的劳动强度大、劳动效率低、这些都缩减了企业的效益[3]。
目前在控制领域,电阻炉控制系统的水平在很大程度上取决于测控水平的高低。
由于现代工业生产规模的不断扩大和生产工艺的日益复杂,对生产过程的自动控制提出了越来越高的要求,不但要求自动控制系统有优越的控制性能、良好的性能价格比、良好的可维护性等,还要求高可靠性、灵活的构成方式和简易的操作方法。
这也使得生产过程自动控制技术得到了不断的发展。
近年来,随着计算机技术、超大规模集成电路技术、网络通信技术的进步,工业控制已逐步从单机监控、直接数字控制发展到以新型工业控制网络、智能化仪表和控制器为主要支撑技术的过程自动化与信息管理自动化相结合的计算机综合型控制系统,其本质是利用计算机技术对生产过程进行监视、操作和管理。
从控制系统的角度讲,计算机控制系统经历了直接数字控制系统(DDC)、分散控制系统(DCS)、现场总线控制系统(FCS)三个阶段。
而在过程控制系统中采用分散控制系统己经成为主流。
分散控制系统中有以可编程序控制器为中心或以微型计算机为中心的两种主要形式,二者的设计思想及方法均有较大差别。
国外先进电阻炉的控制系统普遍采用了以PC、PLC、PCC等为核心的可编程系统,并在一些高精度生产装备上采用了模糊控制、统计过程控制(SPC),以及基于网络的远程监控、故障诊断和控制系统。
而我国在先进测量系统方面,基本上依赖进口。
因此利用现有技术改造原有生产系统势在必行。
而单片机以其功能强、性价比高、小巧灵活、可靠性好、适应温度范围宽而成为工业控制系统的首选。
目前国内大多数电阻炉的温度控制系统正逐步由传统分离式仪表控制转变为PID控制和简单的模糊控制。
由生产实践可知电阻炉温度控制系统的时间常数大、纯滞后长。
温度控制过程所具有的高度非线性、动态突变性、多时间尺度性、信息复杂性、传感元件与执行元件的分散性以及决策机构的分层分散性等,决定了其难以用精确的数学模型(微分方程或差分方程)来表征。
PID控制器简单、稳定性好、可靠性高,普通PID控制器常用于一些线性定常系统的控制,但对于非线性、时变系统难以取得预期的效果[3]。
目前电阻炉温度控制主要问题是:
由于电阻炉是一个特性参数随炉温变化而变化的被控对象,常规PID控制方法难以满足工艺温度在大范围变化时的控制要求。
另外采用常规PID控制,使得系统的动态品质差,超调量大、调节时间长,系统的跟踪性差。
随着现代工业技术的发展,对热处理温度控制提出了越来越高的要求。
为了适应工业要求,己有不少公司研究了一些先进控制策略,实现了许多相对复杂的高级控制算法。
第二章系统总体设计方案
2.1设计总体思路
本设计是对工业电阻炉温度进行实时监测与控制,主要的温度控制系统能实现基本的温度控制功能:
当电阻炉炉内温度低于设定的下限温度时,系统就会对电阻炉发出加热信号,使其温度上升;当电阻炉炉内温度高于设定的上限温度时,系统将停止加热电阻炉,使炉内温度下降。
通过PID调节不断重复该过程,使温度值始终保持在上下限温度之间,并且使LED显示器即时显示温度。
2.2系统技术指标
本系统的技术指标要求如下:
1.测量温度和控制温度均可以数字显示;
2.被测温度范围为0~1000℃,精度为±0.5℃;
3.控制温度可连续可调,精度为±1℃;
4.温度超过限时,产生声、光报警信号。
2.3设计方案选择
在选择控制器的时候,有下面几种方案。
方案一:
控制核心采用8031。
使用最为常用的器件ADC0809作模数转换,使用对电阻丝加电使炉升温。
此方案理论上是可行的,所选元件的价格便宜,但8031内部没有设置存储器,需要内存扩展,加大了电路的复杂性,且ADC0809是8位模数转换器,转换的精度较低,所以不能满足控制的要求。
方案二:
采用比较流行的STC