注塑模课程设计说明书DOC.docx
《注塑模课程设计说明书DOC.docx》由会员分享,可在线阅读,更多相关《注塑模课程设计说明书DOC.docx(18页珍藏版)》请在冰豆网上搜索。
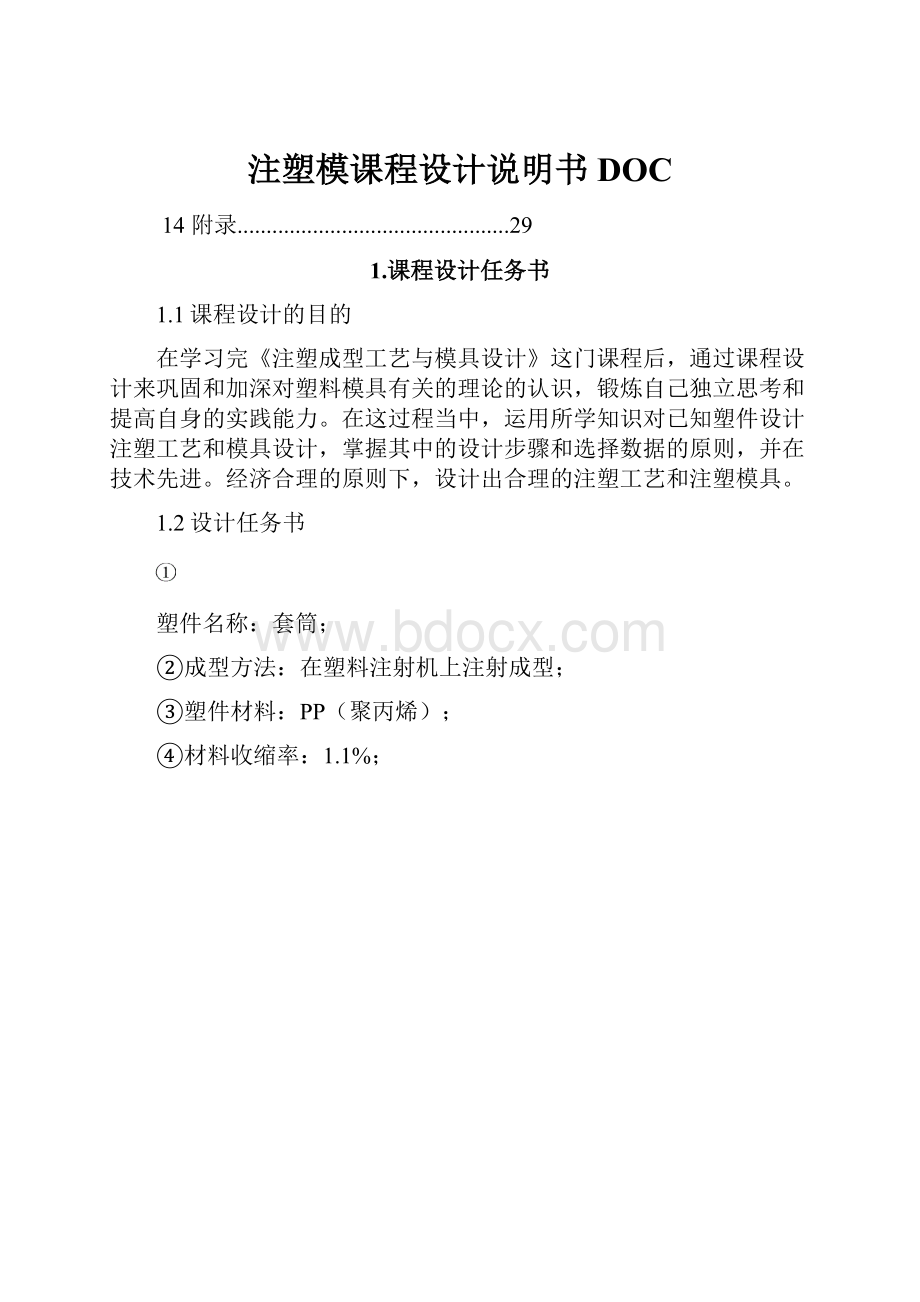
注塑模课程设计说明书DOC
14附录...............................................29
1.课程设计任务书
1.1课程设计的目的
在学习完《注塑成型工艺与模具设计》这门课程后,通过课程设计来巩固和加深对塑料模具有关的理论的认识,锻炼自己独立思考和提高自身的实践能力。
在这过程当中,运用所学知识对已知塑件设计注塑工艺和模具设计,掌握其中的设计步骤和选择数据的原则,并在技术先进。
经济合理的原则下,设计出合理的注塑工艺和注塑模具。
1.2设计任务书
塑件名称:
套筒;
②成型方法:
在塑料注射机上注射成型;
③塑件材料:
PP(聚丙烯);
④材料收缩率:
1.1%;
⑤塑件图:
如下
2.塑件工艺性分析
2.1塑件图
图2-1塑件三维图
套筒,材料PP(聚丙烯),单个塑件体积V=1685.5280mm3=1.6855cm3,质量m=1.5170g,一模四腔注射成型。
2.2材料性能分析
2.2.1适用范围
适于制作一般机械零件,耐腐蚀零件和绝缘零件。
2.2.2成形性能
密度小,强度,刚性,硬度,耐热性,均优于低压聚乙烯,可在100℃左右。
具有优良的耐腐蚀性和高频绝缘性,不受湿度影响,但低温时变脆,不耐磨,易老化。
适于制作一般机械零件、耐腐蚀零件和绝缘零件。
2.2.3成型性能
①结晶料,吸湿性小,易发生熔体破裂,长期与热金属接触易分解。
②流动性好,但收缩范围和收缩值大,易发生缩孔、凹痕、变形。
③冷却速度快,浇注系统及冷却系统应缓慢散热,并注意控制成形温度。
模具温度低于50℃时,塑件不光泽,易产生熔接不良、流痕,90%以上易发生翘曲变形。
④塑件壁厚需均匀,避免缺口、尖角,以防应力集中。
2.2.4主要技术指标
表2-1PP技术指标
密度
克/厘米3
0.90~0.91
比容
厘米3/克
1.10~1.11
吸水性(24小时)
%
0.01~0.03
收缩率
%
1.1
熔点
℃
170~175
热变形温度(0.45Mpa)
℃
102~115
热变形温度(1.82Mpa)
℃
56~67
弯曲强度
Mpa
68
硬度
HB
8.65
抗拉屈服强度
Mpa
37
冲击强度
KJ/㎡
78(无缺口)/3.5~4.8(有缺口)
2.2.5材料推荐工艺参数
聚丙烯(PP)查《模具设计与制造简明手册(第二版)》P371表2-36得
预热:
70~80℃1h
料筒温度(℃):
后段:
160~180
中段:
180~200
前段:
200~220
喷嘴温度(℃):
170~190
模具温度(℃):
80~90
注射压力(MPa):
70~100
成型时间(s):
高压时间:
0~3
保压时间:
20~60
冷却时间:
20~90
成形周期:
50~160
螺杆转速(r/min):
48
干燥:
料斗干燥
后处理:
无
2.3结构工艺性分析
2.3.1塑件尺寸精度分析
该塑件尺寸精度无特殊要求,查《模具设计与制造简明手册(第二版)》P357表2-18,聚丙烯(PP)一般精度按MT6查取公差。
其主要尺寸公差要求查P356表2-17塑件尺寸公差,如下所示:
表2-3塑件尺寸
塑件标注尺寸
塑件尺寸公差(按MT6级精度)
模具尺寸精度(按IT12级精度)
A类尺寸
Φ23
Φ23-0.44
Φ23-0.21
Φ14
Φ14-0.36
Φ14-0.18
Φ9
Φ9-0.32
Φ9-0.15
B类尺寸
10
10±0.26
10±0.075
7
7±0.26
7±0.075
2.3.2壁厚分析
聚丙烯(PP)最小壁厚及推荐壁厚
制件流程50mm的最小壁厚
一般制件壁厚
大型制件壁厚
0.85
2.45~2.75
>2.4~3.2
设计合理,壁厚相对均匀,塑件最小壁厚2.5mm,查《塑料成型工艺与模具设计》第三版P80表3-13,符合要求。
CAE分析塑件图如下:
图2-2零件CAE分析图
2.3.3圆角过渡
从分型面的位置、型芯、型腔结构来分析过渡圆角的设置。
塑件转角处一般采取圆弧过度,其半径为塑件壁厚的1/3以上,最小不宜小于0.5mm。
2.3.34脱模斜度
为便于塑件从模腔中取出,塑件的内外壁需要足够的脱模斜度。
外型尺寸以大端为基准,斜度往小处取;内型尺寸以小端为基准,斜度往大处取。
查《塑料成型工艺与模具设计》第三版P80表3-11,聚丙烯的脱模斜度如下:
表3-11聚丙烯脱模斜度
材料名称
型腔
型芯
聚丙烯(PP)
25~45’
20~45’
考虑到塑件的小,型腔采用30’脱模斜度,型芯采用35’脱模斜度。
3成型设备的选择
3.1计算塑件的体积
根据塑件的三维模型,利用三维软件直接求得塑件的体积为:
V=1.6855cm3,质量m=1.5170g
3.2计算塑件及分流道的总体积
已知单个塑件体积V=1.6855cm3,一模四腔成型。
m2=m1。
n=4,4m1+4m2=12.136g。
则V总=9.7356cm3。
3.3选择注射机
选择原则:
V注≥1.5V件=14.6034cm3。
凹模采用镶拼组合式,查《模具设计与制造简明手册(第二版)》P498表2-99,S1=5,S2=15;矩形布置,一模四腔;根据计算公式:
L=(2S1+S2+d)×2=96mm
b==(2S1+S2+d)×2=96mm
根据L×b及塑件容量等因素,查《塑料成型工艺与模具设计(第三版)》P111表4-1初选型号为XS-ZY-125型注射机,其主要参数如下:
XS-ZY-125型注射机参数
型号
单位
XS-ZY-125
螺杆(柱塞)直径
(mm)
Φ42
额定注射容量
(cm3)
125
注射压力
(MPa)
120
注射行程
(mm)
115
锁模力
(KN)
900
最大成型面积
(cm2)
320
模具厚度
最大
(mm)
300
最小
(mm)
200
最大开(合)模行程
(mm)
300
喷嘴
球半径
(mm)
Φ12
孔直径
(mm)
Φ4
定位孔直径
(mm)
Φ100
表3-1注射机主要参数
4分型面的选择
4.1分型面选择原则
分型面应选择在制品的最大截面处,无论塑件以何形式布置,都应将此作为首要原则。
便于塑件顺利脱模,尽量使塑件开模时留在动模一边。
有利于保证塑件的精度要求。
尽量满足塑件的外观质量要求。
分型面上型腔壁面稍有间隙,就会产生飞边。
便于模具加工制造,在选择非平面分型面时,应有利于型腔加工和制品的脱模方便。
对成型面积的影响,尽量减少制品在合模方向上的投影面积,以减小所需锁模力。
对排气效果的影响,尽可能有利于排气。
对侧向抽芯的影响(本塑件没有抽芯)。
4.2分型面方案确定
根据分型面选择原则,分型面应选在塑件的最大截面处,由于塑件有两个最大截面,同时塑件在成型的过程中会冷却收缩,为了使塑件能够紧紧包在动模上,塑件的分型面有如下两种选择:
图4-1
方案一:
图4-1该塑件采用水平分型,型腔在定模,型芯在动模分型面取在底部平面最大处,分型后塑件包紧在型芯上,随型芯一起留在动模,然后由动模的推管作用将塑件从动模中脱出,这种分型方式,首先,塑件的外形由定模的型腔成型,这样不仅能够保正塑件的外观质量,成型后由而且型腔采用镶块式更加节省材料,便于加工;其次,分型后由动模的推管作用于塑件内部将塑件从动模的脱出,这样就不会影响塑件的外观质量,而且模具的结构简单,加工方便。
无论从成型性能上看,还是从经济性看此方案都较为合理。
图4-2
方案二:
图4-2该塑件采用水平分型,定模部分成型塑件的内部结构,将型芯装在定模上,型腔做在动模,当开模后塑件包紧在型芯,随型芯留在定模,这样的分型方式对于推出机构要求大,且容易产生飞边的现象,因此此方案不是很好。
综上所述,分型面的方案选取应采用方案一。
5模架的选择
5.1确定模板尺寸
根据塑件外形尺寸b×l,查《模具设计与制造简明手册(第二版)》P481表2-95,选择B=270,L=300,塑件采用推件板顶出,选用BI型组合,定二动三,如图5-1所示:
图5-1BI型
模具上所有的螺钉尽量采用内六角螺钉;模具外表面尽量不要有突出部分;模具外表面应光洁,加涂防锈油。
两模板之间应有分模间隙,即在装配、调试、维修过程中,可以方便地分开两块模板。
定模座板:
300mm×320mm,厚度25mm
定模板:
270mm×300mm,厚度40mm
推件板:
270mm×300mm,厚度25mm
动模板:
270mm×300mm,厚度35mm
支撑板:
270mm×300mm,厚度40mm
垫块:
63mm×450mm,厚度80mm
推杆固定板:
160mm×300mm,厚度15mm
推板:
160mm×300mm,厚度20mm
动模座板:
270mm×300mm,厚度25mm
6浇注系统的设计
6.1浇注系统设计原则
(1)浇注系统与塑件一起在分型面上,应有压降,流量和温度的分布的均衡布置;
(2)结合型腔布置考虑,尽可能采用平衡式分流道布置;
(3)尽量缩短熔体的流程,以便降低压力损失、缩短充模时间;
(4)浇口尺寸、位置和数量的选择十分关键,应有利于熔体流动、避免产生湍流、涡流、喷射和蛇形流动,有利于排气和补缩,且应设在塑件较厚的部位,以使熔料从后断面移入薄断面,以利于补料;
(5)避免高压熔体对模具型芯和嵌件产生冲击,防止变形和位移的产生;
(6)浇注系统凝料脱出应方便可靠,凝料应易于和制品分离或者易于切除和整修;
(7)熔接痕部位与浇口尺寸、数量及位置有直接关系,设计浇注系统时要预先考虑到熔接痕的部位、形态,以及对制品质量的影响;
(8)尽量减少因开设浇注系统而造成的塑料凝料用量;
(9)浇注系统的模具工作表面应达到所需的硬度、精度和表面粗糙度,其中浇口应有IT8以上的精度要求;
(10)设计浇注系统时应考虑储存冷料的措施;
(11)尽可能使主流道中心与模板中心重合,若无法重合应使两者的偏离距离尽可能小。
6.2主流道设计
主流道通常位于模具中心塑料熔体的入口处,它将注射机喷射出的熔体导入分流道或型腔中。
主流道的形状为圆锥形,以便于熔体的流动和开模时主流道凝料的顺利拔出。
6.2.1主流道尺寸
(1)主流道小端直径d
主流道小端直径d=注射机喷嘴直径+(0.5~1)
=4+(0.5~1)
取d=5mm这样便于喷嘴和主流道能同轴对准,也能使的主流道凝料能顺利脱出
(2)主流道球面半径
主流道入口的凹坑球面半径SR,应该大于注射机喷嘴球头半径的1~2mm。
反之,两者不能很好的贴合,会让塑件熔体反喷,出现溢边致使脱模困难.
SR=注射机喷嘴球头半径+1~2;
SR=12+1~2;
取d=13mm,经查表,取d=13mm。
(3)主流道长度L
一般按模板厚度确定,但为了减小充模时压力降和减少物料损耗,以短为好,小模具控制在50之内。
在出现过长流道时,可以将主流道衬套挖出深凹坑,让喷嘴伸入模具。
本设计中结合该模具的结构,取l=59.2mm。
(4)主流道大端直径
D=d+2ltanα(半锥角α为1°~2°)≈6mm
6.2.2主流道衬套
主流道小端入口处与注射机喷嘴反复接触,属易损件,对材料要求较严,因而模具主流道部分常设计成可拆卸更换的主流道衬套形式,即浇口套。
6.3分流道的设计
分流道设计:
根据《模具设计与制造简明手册(第一版)》P299表2-40,选择梯形分流道,查《模具设计与制造简明手册(第一版)》P299表2-40,选择H=8;如图6-1:
图6-1分浇道截面形状和尺寸
分流道布局如下:
6.4浇口的设计
浇口可分为限制性和非限制性浇口两种。
我们将采用限制性浇口。
限制性浇口一方面通过截面积的突然变化,使分流道输送来的塑料熔体的流速产生加速度,提高剪切速率,使其成为理想的流动状态,迅速面均衡地充满型腔,另一方面改善塑料熔体进入型腔时的流动特性,调节浇口尺寸,可使多型腔同时充满,可控制填充时间、冷却时间及塑件表面质量,同时还起着封闭型腔防止塑料熔体倒流,并便于浇口凝料与塑件分离的作用。
模具设计时,浇口的位置及尺寸要求比较严格,初步试模后还需进一步修改浇口尺寸,无论采用何种浇口,其开设位置对塑件成型性能及质量影响很大,因此合理选择浇口的开设位置是提高质量的重要环节,同时浇口位置的不同还影响模具结构。
总之要使塑件具有良好的性能与外表,一定要认真考虑浇口位置的选择。
通常要考虑以下几项原则:
a.尽量缩短流动距离。
b.浇口应开设在塑件壁厚最大处。
c.必须尽量减少熔接痕。
d.应有利于型腔中气体排出。
e.考虑分子定向影响。
f.避免产生喷射和蠕动。
g.浇口处避免弯曲和受冲击载荷。
h.注意对外观质量的影响。
从模具的制造及结构考虑,该注塑模具采用矩形侧浇口。
矩形侧浇口一般开设在模具的分型面上,从塑件的边缘进料。
矩形侧浇口广泛应用于中小型塑件的多型腔注塑模,截面形状简单、易于加工、便于试模后修正。
6.5分流道CAE分析
图6-1充填时间图
图6-2流动前沿温度图
6.5相关零件
6.5.1浇口套
查《模具设计与制造简明手册(第二版)》P513表2-118I型浇口套,P=5mm;
图6-5浇口套
表6-1浇口套数据
D
h
A
SR
P
L
10
3
1°
13
5
44.2
6.5.2定位圈
查《机械设计》P137表13-19,得D=100.
图6-6定位圈
表6-2定位圈数据
D
T
B
d2
d1
A
100
15
35
6.6
11
85
7冷却系统的设计
综合分析查《模具设计与制造简明手册(第二版)》表2-151型腔采用直流式,水孔直径为8mm,型芯水孔直径4mm,水路如图7-1:
图7-1冷却水道
8顶出-推出机构设计
8.1顶出机构
8.1.1推杆尺寸
塑件为圆形件,采用推件板顶出,推件板的尺寸为270×300,另外推件板还要使用推杆推动,综合分析查《模具设计与制造简明手册(第二版)》P519表2-126推杆标准尺寸,形状尺寸如下:
D
L
s
25
130
4
8.2推出元件
推板尺寸
推板(160mm×300mm);
推板固定板尺寸
推杆固定板(160mm×300mm);
推板导柱
查《模具设计与制造简明手册(第二版)》P508页,注塑模带头导柱标准尺寸,尺寸如下:
d
d1
D
s
L
12
12
16
4
80
9支撑零件
查网络得支撑柱相关尺寸如下:
M
D
L
6
20
64
10注射机校核
10.1注射量校核
经计算,工件与浇注系统总的注射体积V注=29.75cm3,远小于理论注射量125cm3,符合注射机要求。
10.2压力校核
根据注射压力条件:
P成≤P注。
查《模具设计与制造简明手册(第二版)》p371,PP注射压力为70~100MPa。
注射机压力120MPa,符合要求。
10.3锁模力校核
查《模具设计与制造简明手册(第一版)》p396,根据锁模力要求:
p腔F≤P锁。
取p腔=50Mpa,F=60cm2,P锁=900KN,锁模力符合要求。
10.4开模行程校核
H1=45,H2=10,H1+H2+10=65mm,小于300mm,符合要求。
10.5模具厚度校核
由装配图可知模具的闭合高度H闭=270mm而注射机的最大模具厚度Hmax=300mm满足安装要求。
综上所述:
选取XS-ZY-125型注射成型机完全符合本模具的使用要求。
11型芯型腔尺寸计算
收缩率Scp=1.1%,查《模具设计与制造简明手册(第二版)》P356表2-17,取塑料制件公差等级为MT6,对应的模具制造公差等级为IT12;
(1)型腔尺寸计算
Φ23-0.21:
LM1=[(1+1.1%)*23-0.75*0.21]+0.07=23.0995+0.07
14-0.18:
LM2=[(1+1.1%)*14-0.75*0.18]+0.06=14.019+0.06
16-0.18:
LM3=[(1+1.1%)*16-0.75*0.18]+0.06=16.041+0.06
7±0.075:
HM1=[(1+1.1%)*7+2/3*0.15]+0.05=7.177+0.05
3±0.075:
HM2=[(1+1.1%)*3+2/3*0.1]+0.03=3.1+0.03
(2)型芯尺寸计算
9-0.15:
lM1=[(1+1.1%)*9+0.75*0.15]-0.05=9.211-0.05
11-0.06:
lM2=[(1+1.1%)*11+0.75*0.18]-0.06=11.256-0.06
10±0.075:
hM=[(1+1.1%)*10+2/3*0.15]-0.05=10.21-0.05
1结论
(1)注射机选择为XS-ZY-125。
(2)塑件一模四腔成型,梯形浇道,侧浇口。
(3)模架形式为定二动三。
(4)模具闭合高度为270mm。
(5)采用导柱导套进行模具导向。
(6)推出机构为推件板顶出。
(7)排气方式为零件间隙排气。
(8)冷却水道采用直通式水道。
12心得体会
通过这次注塑模具课程设计,让我对如何完整的设计一套注塑模具有了一个较为体统的了解,设计过程中综合运用以前学习的各种相关知识,也让让我对模具专业知识有了一个很好的串联,复习。
这次课程设计,由于理论知识的遗忘、不熟练,加之没有设计经验,一开始的时候一头雾水,不知从何入手。
开始大量的查阅资料数据,这个过程是很辛苦的,也正是这个过程锻炼了我查阅资料文献的能力。
现在想想其实课程设计当中的每一天都是很累的,其实正向老师说得一样,模具设计的课程设计没有那么简单,每一个数据都要精确计算,考虑很多因素。
设计过程中老师给与我很多帮助,教会我很多设计技巧经验,教育我们作为技术设计人员要有严谨的思维,每一步设计都要有理有据,校核。
总之这次注塑模具收获还是很多的,巩固了自己专业知识,锻炼了动手能力,提高查阅资料能力,培养了严谨的思维意识,巩固和扩充了注塑模具课程的专业知识和视野,掌握了怎样分析零件的工艺性,熟悉了注塑模具的规范和标准。
纸上得来终觉浅,这次动手实践学习到很多课本学不到的知识,也对自己以前的学习有了一次检验。
参考文献
[1]冯炳尧,等.模具设计与制造简明手册[M].上海科学技术出版社,1985.
[2]池成忠.注塑成型工艺与模具设计[M].化学工艺出版社,2010.7.
[3]杨占尧.塑料模具课程设计指导与范例[M].北京:
北京高等教育出版社,2009.6.
附录
CAE分析报告
1.浇口位置
经过MoldFlow软件的分析提供了如下的最佳浇口位置:
图1-1MoldFlow最佳浇口位置
如图1-1所示,Moldflow提供的最佳浇口位置基本位于型芯附近,如果采用软件提供的浇口位置,则浇口形式需采用点浇口或改变分型面,而采用点浇口则模具必须采用三板式模具,这对于设计成本和设计难度都有提高。
经过小组分析、讨论之后重新选定的浇口如下:
重新选定的浇口位置
采取这种浇口位置对于充填质量并没有什么不利的影响而且这种浇口不仅利于分型,模具精度得以保障,模具结构也变得简洁方便,所以选择图1-1的浇口是可行的。
2.注塑工艺参数:
经过重新选定浇口后对塑件进行MoldFlow分析后工艺参数如下:
气穴位置图
图中显示的是一模四腔的气穴位置图,在进行浇注是途中红圈处易产生气穴,反应出塑件发生烧焦,短射等问题。
锁模力变化图
锁模力是压力分布在整个制品上的结果值。
它是对从填充和保压到开模的压力记录。
锁模力是注射压力和制品投影面积的函数。
投影面积是模型投影到XY平面的面积
熔接痕位置图
熔接线产生在填充分析的末端,分析显示可能发生熔接线的地方,在模型上沿着流动前沿聚合形成熔接线。
熔接线发生在两个或者更多个流动前沿聚合处。
熔接线的存在指示了结构缺点或者表面缺陷。
上图所示的熔接痕表示的是该塑件可能发生的熔接痕位置,熔接痕的产生可能导致产品结构发生问题。