超声波纳米表面改性的微凹表面及其摩擦学效应1.docx
《超声波纳米表面改性的微凹表面及其摩擦学效应1.docx》由会员分享,可在线阅读,更多相关《超声波纳米表面改性的微凹表面及其摩擦学效应1.docx(18页珍藏版)》请在冰豆网上搜索。
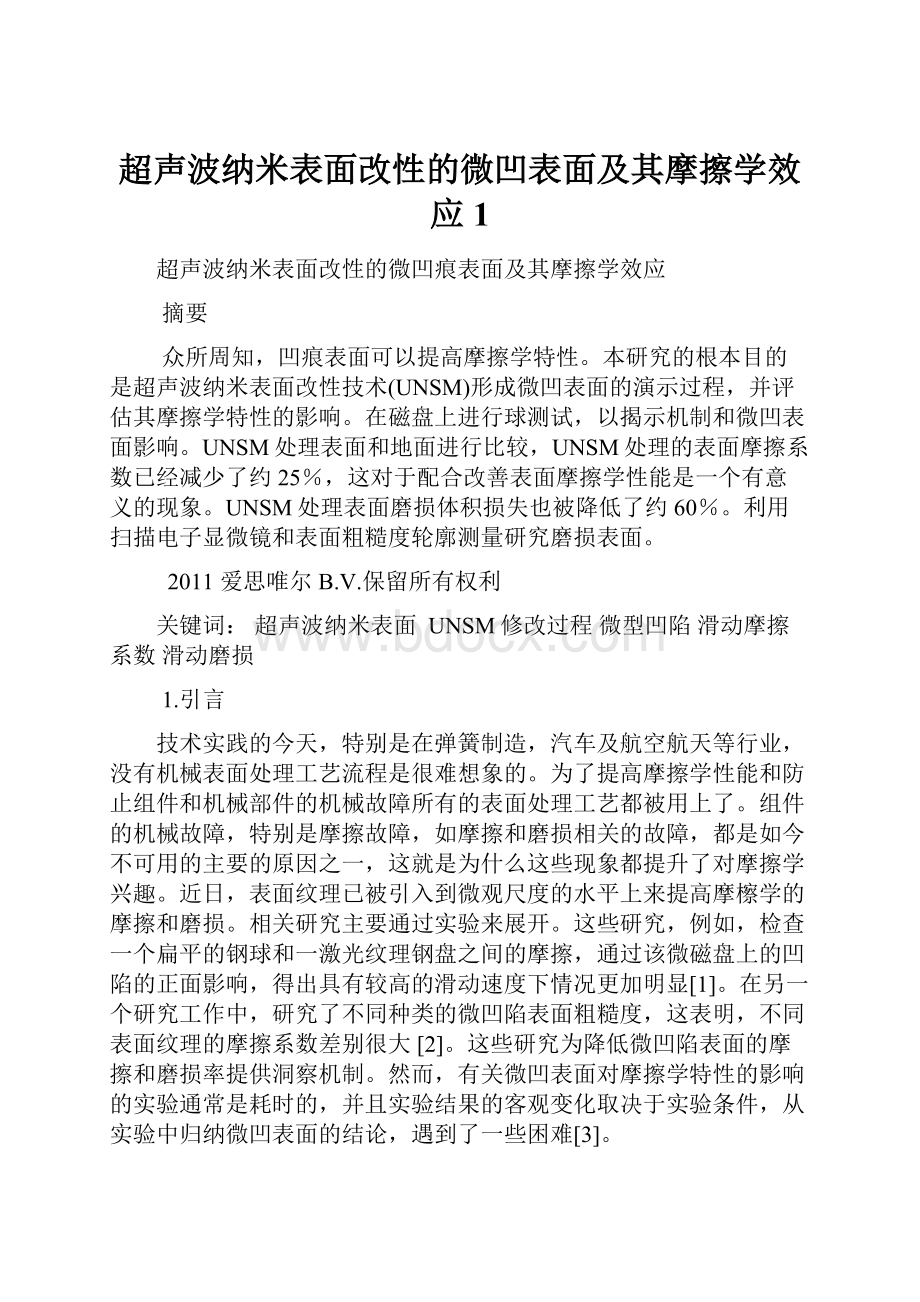
超声波纳米表面改性的微凹表面及其摩擦学效应1
超声波纳米表面改性的微凹痕表面及其摩擦学效应
摘要
众所周知,凹痕表面可以提高摩擦学特性。
本研究的根本目的是超声波纳米表面改性技术(UNSM)形成微凹表面的演示过程,并评估其摩擦学特性的影响。
在磁盘上进行球测试,以揭示机制和微凹表面影响。
UNSM处理表面和地面进行比较,UNSM处理的表面摩擦系数已经减少了约25%,这对于配合改善表面摩擦学性能是一个有意义的现象。
UNSM处理表面磨损体积损失也被降低了约60%。
利用扫描电子显微镜和表面粗糙度轮廓测量研究磨损表面。
2011爱思唯尔B.V.保留所有权利
关键词:
超声波纳米表面UNSM修改过程微型凹陷滑动摩擦系数滑动磨损
1.引言
技术实践的今天,特别是在弹簧制造,汽车及航空航天等行业,没有机械表面处理工艺流程是很难想象的。
为了提高摩擦学性能和防止组件和机械部件的机械故障所有的表面处理工艺都被用上了。
组件的机械故障,特别是摩擦故障,如摩擦和磨损相关的故障,都是如今不可用的主要的原因之一,这就是为什么这些现象都提升了对摩擦学兴趣。
近日,表面纹理已被引入到微观尺度的水平上来提高摩檫学的摩擦和磨损。
相关研究主要通过实验来展开。
这些研究,例如,检查一个扁平的钢球和一激光纹理钢盘之间的摩擦,通过该微磁盘上的凹陷的正面影响,得出具有较高的滑动速度下情况更加明显[1]。
在另一个研究工作中,研究了不同种类的微凹陷表面粗糙度,这表明,不同表面纹理的摩擦系数差别很大[2]。
这些研究为降低微凹陷表面的摩擦和磨损率提供洞察机制。
然而,有关微凹表面对摩擦学特性的影响的实验通常是耗时的,并且实验结果的客观变化取决于实验条件,从实验中归纳微凹表面的结论,遇到了一些困难[3]。
表面纹理对机械部件的摩擦特性的改善是一个有吸引力的方法。
微凹配合表面的摩擦学以各种形式,大小和形状的研究工作已经在世界各地用各种方法使微凹表面技术开展开来,如喷丸,离子束纹理,激光表面纹理等等。
今后,除了这些技术,UNSM技术已被应用于各种机械部件[4-6]。
Nakano等。
[7]报道的摩擦系数增加或减少取决于微观纹理图案的几何形状,凹坑图案纹理导致比其他图案纹理摩擦系数低,如槽和网格图案纹理。
相关的结果表明,较低的摩擦系数可以被获得,因为微凹坑的影响导致更大的配合面之间的分离。
微凹陷性能的提高主要归因于UNSM处理表面的微凹陷扮演了润滑剂水库和帮助促进保留配合面之间的润滑薄膜的重要角色,从而降低摩擦和磨损率。
值得称道的作品,以及前面提到的研究,对于提高配合面的摩擦学和机械性能的改善有很大帮助。
2.超声波纳米表面改性处理
2.1UNSM处理的概念
UNSM技术是由DesignMecha有限公司开发和商业化的一项专利技术[4]。
UNSM是利用超声波能量改善金属的一种方法。
由于其经济效果,对工件的效果可以很好的调节,并因为它在生产机器零件及各种用途的机器中是一种安全,简单和有效的方法,这项技术已引起了人们相当大的兴趣。
UNSM技术掌握着工件表面的质量、性质和特性,在改造领域修改材料的性能,提高了疲劳和耐腐蚀性以及抗磨损性,并减少了接触故障,诱导表面层的残余应力和严重的塑性变形以及稳定性,在机械工业领域提高了静止质量和可靠性的特点。
UNSM技术已经说明了对各种金属和合金,如铝,青铜,钢,钛,铜等的有效性,这种UNSM技术也被应用到高温结构材料。
UNSM技术的主要优点之一是它可用于在表面上创建微凹陷,并且这种生产成功率是极高的。
2.2微凹表面形成的理论和过程
在UNSM技术工艺过程中,工件表面不仅受静载荷(聚苯乙烯)作用,而且还受动态负载(Pdy=Psin2πft)的作用,如图1所示[5]。
图2所示的发电机和压电转换器发射超声波为20kHz。
当波穿越声学助推器时,会被放大。
尺寸在10-100微米范围的震动振幅才可以通过接触面。
均匀的处理可以在处理后的表面获得。
UNSM的原理是基于仪器的超声波频率共振的声学调节体的谐波振荡转换。
通电的超声波换能器给声学调节体的本体带来了共振。
从这些工件表面为20,000-40,000平方毫米的高频脉冲的总的力(F=Pst+Pdy)中产生能量[6]。
与此同时,撞击在工件表面上产生无数的微凹面,表面上产生严重的塑性变形,从而诱导纳米结构。
这些微凹表面既可以作为充满条件下的微流体动压轴承也可以作为润滑条件下的混合润滑和碎屑的微型水库。
通常的氮化硅陶瓷(氮化硅)或碳化钨球和销具有球形精度高和表面光滑的特性被作为敲击介质如表1中所示,这些球和销还可以连接到介质中。
使用硬度为2300HV的氮化硅制成不同尺寸的球和硬度为1700HV的碳化钨制成不同尺寸的销。
典型的销和球的大小是直径在1.2-6毫米的范围内,这些可以根据工件选材目的和力学性能的不用来选择。
在应用中根据想要得到的效果来处理不同的球和销。
备注:
F=Pst+Pamsin2π英尺;其中:
F是总的撞击力;Pst是工具正常静态负载;Pam是动载荷的振幅;A为振幅;V是主轴转速(rpm);S是进给速度(mm/rev);r是球半径;D为试样直径。
假设微凹面积为1-10平方微米,深度小于0.1微米。
微凹的数量,n用公式
(1)计算。
n—f/2πR(V×S)
(1)
其中f是频率[1/s],V是该机器主轴的速度[r/s],S为进给速率[m/r],从而使(V×S)[m/s]和f/(V×S)为[1/m],而n是[1/m²],r为要处理的球或销表面的半径。
采用原子力显微镜测定微凹陷表面的确切尺寸[8]。
图1(a)微凹陷的制作工艺(b)微凹陷的表面
图2UNSM处理技术的主要装置
2.3设置和应用
UNSM技术可能在不同的所需位置上设置数控机和计算机数控机。
在这项研究中,UNSM工艺过程是在一个标准的加装压电驱动工具的数控车床上进行的。
UNSM技术的主要实验设置如图2所示。
有很多基本参数影响UNSM的实验过程。
这些参数可能是精确的并被NC/CNC机床高度控制和优化的,为了UNSM技术能够获得每个应用程序的最佳效益,它们的设置必须是简单容易的。
本研究实验的基本参数示于表2。
UNSM技术抑制裂纹产生的性能,主要受两方面的影响。
打击的影响导致严重的工作表面硬化,同时增加了工作表面的疲劳强度。
此外,UNSM技术在表面层中产生的残余压应力。
通常情况下,这些压应力的量和深度明显高于标准的制造方法,如车削、钻孔或切割。
通过压缩残余应力提高疲劳寿命来影响裂纹萌生和扩展。
表面硬度的增加依赖于物质的硬化潜力以及物质条件。
UNSM技术的便利和经济也适用于大面积制造微凹陷表面。
它表明,UNSM技术是一种多用途、准确的技术,对于机械部件表面纹理的处理是一种潜在的成本效益方法。
经验及多项研究已经证明了UNSM技术工艺导致的进步,它被广泛用于提高工作在高应力环境和其它关键部件的机械部件的使用寿命。
尽管UNSM技术在理解过程中具有重要的进展,但是一些地方没有完全掌握和开发,生产率和有效性还有待开发。
能够预测设置条件过程中的效果确实是完成控制过程并使其可靠的关键。
3.纳米化机制
纳米晶体材料吸引了人们相当大的兴趣,因为它们的大晶界体积分数新性能[9,10]。
自从Gleiter等人。
[11]通过惰性气体冷凝和合并成功地合成了第一块块体纳米晶试样,各种合成技术已经被开发用来生产纳米材料,如球磨[12],无定形固体结晶[10],电镀[13,14]和严重塑性变形[15]等等。
然而,在技术应用中制备纳米晶体材料,仍然是一个挑战[16]。
纳米晶体材料的摩擦学特性是非常重要的,因为它们具有潜在的工程学应用程序潜能。
在知名的Hall-Petch关系之后,组织的细化预计将提高硬度[17,18]。
在纳米晶体材料的许多实验研究中,已证明了晶粒细化耐磨性的显著增强。
在纳米硬质合金复合材料的情况下,例如,WC晶粒大小减少到70纳米时其磨粒耐磨性比常规金属陶增长近一倍。
纳米铝合金也比常规合金表现出更好耐磨性[20]。
纯纳米金属磨损的系统研究是罕见的,这可能是由于生产批量的适合摩擦和的磨损测试的纯纳米样品很困难[21-23]。
其实,工程材料的失败,如摩擦、磨损、腐蚀和疲劳经常发生材料表面上[24]。
这些材料的表面决定于材料的工作属性。
常规金属和材料其纳米晶表面层是,它不仅可以解决块体纳米材料制造的难度,还提高了常规材料的性能同时也节省了成本[25]。
了解纳米晶体在UNSM技术中的形成过程是发展UNSM技术的关键。
梯度大小的分布从几纳米(顶部表面层)到几微米取决于UNSM处理的试样表面,它提供了一个独特的机会来研究不同级别的表面层的微型结构特性。
因此,可以推断出微米纳米制度中变形引起的晶粒细化的基本原理[26]。
图5展现了UNSM处理试样横截面的表面层的微观结构特征和分布的示意图。
纳米结构表面层的厚度(以及精细的结构层)非常依赖材料和UNSM技术工艺参数(如球的大小,振幅,负载,NC/CNC机床的进给速率和主轴转速)。
在52100轴承钢横截面样本中,沿着地面和UNSM处理表面的深度方向的显微硬度的变化是确定,如图3(a)所示。
顶面层的纳米晶的硬度大约是840HV且随深度增大逐渐减小。
很显然,UNSM处理的轴承钢的硬度显着增加,而不会对其他性质造成任何损害。
图3(b)表示的是地面和UNSM处理的标本从顶面沿深度方向残余应力的分布。
利用
放射线获得的晶面衍射模式,古典
方法可被应用于测定沿试样的长轴方向的残余应力。
对试样进行UNSM处理,当压力达到负900兆帕时塑性变形的压缩残余应力有增加的趋势。
很明显,UNSM处理表面的残余压应力高于未经处理的表面。
压缩残余应力随着离表面的距离增加而不断减少。
电子背散射衍射显微照片表明,与未经处理的表面相比较,在UNSM处理的表面层观察到了更多的表面塑性变形,如图4所示。
如图4所示的黑点的显微图像,指出了EBSD算法无法重建模糊的菊池线方向上的点。
使用TSLOIM分析5程序(EBSD数据采集和处理软件)分析EBSD来测定晶粒尺寸。
图3(a)从顶面层开始测量地面和UNSM处理试样的显微硬度,
图3(b)从顶面层开始测量地面和UNSM处理试样的残余应力。
图4:
(a)EBSD观察下的地面横截面图(b)UNSM处理过标本。
图5UNSM处理的表面层结构特点及分布示意图
金属表面的粒面层的塑性变形层的变化显著提高了金属表面层的强度和硬度。
由于在表面层中的塑性变形引起了UNSM,在不改变的化学成分的情况下表面层中的粗粒结构被精制成纳米尺度。
如图5所示,UNSM技术已成功地应用于轴承钢它已获得了达100微米厚的三层纳米结构表面层。
50nm到500nm范围的成品粒度在最顶端三层中产生,而且它的尺寸随着距离顶部的深度的增加而增加,它和图3(a)所示的硬度值有密切的关联。
表面层加工硬化后的Hall-Petch关系如式
(2)所示。
材料的硬度H,是依赖于晶粒直径d,以类似的众所周知的Hall-Petch关系方式来表示,晶粒尺寸越小,材料越硬。
其中k是给定的材料常数,
为硬度测量与适当的相关常数,d是平均颗粒尺寸。
这种关系被在许多微米尺度晶粒尺寸的金属材料的理论和实践中证实[27]。
实现批量材料表面纳米化的关键点是在表面层中引入晶界,以便它的微型结构转化为纳米尺寸的微晶。
UNSM是一种在金属材料上实现表面纳米晶的有效技术。
4.摩擦学测试
在这个实验中,上部环的推力球轴承(第51306号)被用来作为盘标本(直径60毫米,厚度5毫米),作为一个球--盘试验台。
在本研究中所用的盘和球材料由SAE52100轴承钢制成,都是在热处理状态完成的(淬火和回火)。
利用球--盘试验台的几何相切来进行摩擦学实验测试。
对将要进行连续的滚动/滑动的材料和为了使用一个来自推力球轴承的直径为11毫米的球模拟相同的推力球轴承条件是一个很好的筛选试验。
表3列出了球--盘测试的实验条件。
试验后,进行了盘试样的接触面的评估来确定应用正常负载的影响程度。
此外,对摩擦学性能进行了详细的分析。
通过摩擦力确定摩擦系数,并根据滑动过程中产生的磨痕的表面粗糙度对磨损量进行定量。
在这项研究中使用的所有试样,具有相同的表面粗糙度(Ra=0.10um),以排除表面粗糙度的影响。
微凹陷的初期形状是球形。
凹陷初期直径和深度分别为约1.25um和0.07um。
图6摩擦系数在载重条件下UNSM图7摩擦体积在载重条件下UNSM
处理与地面实验的变化曲线。
处理与地面实验的变化曲线。
图8摩擦系数的变化作为地面和图9摩擦体积的变化作为地面和
UNSM处理的滑动距离的函数。
UNSM处理的滑动距离的函数。
图10单个微凹陷的放大3D图和轮廓图
5.结果和讨论
5.1摩擦和磨损
在平面上有微型凹陷的存在能够很明显的减小摩擦系数就像是一个更小的膜厚度与粗糙度之比(h/Rq的),小的表面粗糙度,或较大的负载。
对于较大的膜厚度比粗糙度(h/Rq的),较大的表面粗糙度,或更小的负载的情况下,在平面上摩擦系数的变化由于微凹坑的效果取决于这些综合影响因素[28]。
图6和图7曲线分别描述了摩擦系数和磨损体积损失在滑动距离为100米,转速为100rpm下UNSM处理和地面标本的函数。
此外,增进的摩擦和磨损性能归于较强的纳米尺寸晶粒表面层和从顶表面沿深度方向的微细构造和性能的梯度变化。
图8和图9分别显示了明显不同的摩擦系数和磨损量以及UNSM在同样的100N负载和100rpm下作为滑动距离的函数。
图10显示了微凹陷在初始状态下的放大3D图和轮廓图。
图10(b)提供证据表明,微凹陷(初始状态)的膨胀在500m左右滑动,滑动摩擦距离500m后趋于稳定,一直到膨胀充满为止。
Rapoport等人[29]报告说,相互重叠的一半膨胀表面透露着最小的摩擦系数和亏损量。
分别如图8和图9所示当摩擦和磨损稳定之后,UNSM应快速穿脱,示于图10(b)线条的尖锐突起。
该UNSM不会是一个绝对的光滑表面,直到球状物撞击到工件表面。
图11随着3D地形试验后的型材表面粗糙度。
(a)图地面表面粗糙度,
(b)图UNSM处理的表面粗糙度。
图12地面和UNSM处理试样滑动距离为50米的表面粗糙度分布的中断测试。
(a)图为地面表面粗糙度,
(b)图为UNSM处理表面粗糙度。
图13(a)图测试后UNSM处理的磨损表面形貌
(b)图测试后地面处理的磨损表面形貌
图14在扫描式电子显微镜放图15滑动距离变化时微
大观察UNSM处理试验表面凹陷消除百分比的函数。
从对表面轮廓曲线的学习中发现磨损体积损失与结束表面有关,标本表面的硬度是预测穿行为的重要参数[30]。
纳米晶体表面层的UNSM处理表面,以及由于晶粒细化而增加硬度耐磨性提高。
地面盘试样的表面硬度为720HV,但由于UNSM技术的支持它提高到840HV。
评估磨损的表面轮廓曲线如图11所示的地面试验后的磨损体积损失。
正如前面提到的,表面粗糙度的UNSM处理和研磨(抛光)试验前的表面具有相同的表面粗糙度(Ra=0.10um),目的是消除表面粗糙度的影响。
然而,试验后的粗糙度值是不同的,是由于如图11所示的UNSM试样的表面硬度的改进。
观察滑动距离50米的中间阶段之后,进行了UNSM处理过的表面和接地表面的表面粗糙度的中断实验。
两个试样的表面粗糙度测量,如图12所示。
摩擦随时间变化的图,如上图所示,作为时间的函数关系进行调查摩擦系数性能。
UNSM处理标本的中断测试揭示了一个有趣的事情是磨损轨迹在某种程度上填补了球磨损碎片,因为UNSM转化处理后的表面硬度(约840HV)比球硬度(约720HV)更硬。
然而,这个结果并没有发生在同一滑动距离为50米的地面上。
所以,UNSM处理的试样表面略有磨损较软的球,相反于地面。
其结果是,可以说,当球和圆盘(圆盘标本是UNSM处理)的材料相同并且彼此相对运动和相互作用,由于提高了表面硬度和圆盘试样的残余应力,在一个短距离滑动之后UNSM的磨损效果会很明显。
虽然反部分(球)的磨损性能是重要的,但是去量化的球的磨损性能是不可能的,因为球表面上出现轻微的磨损。
5.2磨损表面和磨损机理
图13显示了UNSM处理和地面试验后的磨损表面的SEM显微图像。
经UNSM处理过的磨损表面标本,图13(a),和图13(b)显示的地面表面形态相比具有不同的表面形态。
显然,地面形态包含了磨损疤痕和斑点,而经UNSM处理过表面形貌几乎是平坦的,这表明了地面试验后磨损表面有微凹陷残留。
图14和图13(a)相辅相成,为了更清楚地看到测试后所剩下的表面微凹陷。
使用原子力显微镜(AFM)对滑动磨损距离函数的微凹痕的百分比也进行了研究,结果如图15。
原子力显微镜的观测显示,在滑动距离为1000m,负载为100N,滑动速度为100rpm时微凹陷几乎磨损。
实验对200-1000N范围内的不同负载进行了测试,以确定在哪一级的负载下圆盘试件表面发生损伤。
图16显示出在更高的负载下脱氨剥落和氧化物出现,但与地面实验进行对比UNSM处理的表面磨损较少。
另一个显着的特点是,观察了UNSM处理试验,表面的微凹陷没有穿。
然而,UNSM处理的表面比地面具有相当的低摩擦系数和磨损体积损失。
归因于微凹陷定期对试件表面面积的接触,从而能够表现为集成局部压力确保较高的水动升力。
随着负载的增加,滑动引起重复的加工硬化,在磨损表面产生分层裂纹传播随后导致在表面层中的材料剥落形成沉重的塑性变形。
纳米晶结构,在UNSM处理过的试样表面层中获得。
通过对表面层横截面图的观察,由塑性变形引起的晶粒细化在UNSM技术的基础上被提出。
UNSM表面处理的实验证据和分析表明,微凹陷和改进摩擦学特性对于减少摩擦和磨损是必要的。
摩擦系数最小和最大的耐磨性以及机械部件的优化设计和材料开发是重要的科学因素。
材料表面纳米化为大宗材料的纳米化过程提供了一个互补的过程。
因此,增加硬度和促使压缩残余应力、具有优良的抗磨损保护以及微凹陷的表面提供升降机本身作为微流体动压轴承可以用来降低摩擦系数。
6.结论
在这项研究中,微凹陷和纳米晶表面层已成功成为SAE52100轴承钢UNSM生产技术。
微凹陷的过程已进行了介绍,对他们的摩擦学特性的影响也进行了评估。
微凹陷和使它们达到了预期结果的进程。
总结得出以下结论:
-纳米晶体表面层的试件通过UNSM技术制造,随着研究深度的增加被处理的表面上的晶粒尺寸也会跟着增加。
-与地面相比,UNSM表面处理的摩擦和磨损性能显着提高。
-UNSM表面处理耐磨性的提高与高硬度的纳米晶结构有关。
-在UNSM技术的过程中,超声波影响是技术效果的主要载体。
-原子力显微镜观测显示在100N的负荷下,滑动距离为1000m后,微凹陷几乎破损。
-随着UNSM技术在处理、性能、工业应用方面调查的增加,可以预期,在不久的将来UNSM将成为升级工程材料。
UNSM过程适用于在工件表面产生大量微凹陷。
据预计,随着持续的研究和开发,基于UNSM技术的更多新应用可能会在未来诞生。
致谢
这项研究得到了韩国21世纪教育、科学和技术前沿研发项目部旗下纳米材料技术中心的授予(代码#2010K000290)。
参考文献
[1]Z.B.Wang,N.R.Tao,S.Li,W.Wang,G.Lui,J.Lu,K.Lu,Effectofsurfacenanocrys-tallizationonfrictionandwearpropertiesinlowcarbonsteel,Mater.Sci.Eng.A352(2003)144–149.
[2]B.Bhushan,HandbookofMicro/NanoTribology,CRCPressLLC,1999,ISBN0-8493-8402-8.
[3]H.Haefke,Y.Gerbig,G.Dumitri,V.Romano,Microtexturingoffunctionalsurfacesforimprovingtheirtribologicalperformances,ProceedingsoftheInternationalTribologyConference,Nagasaki,2000,pp.217–221.
[4]DesignMechaCo.,Ltd.Informationon:
www.designmecha.co.kr.
[5]A.Amanov,Y.S.Pyoun,I.S.Cho,C.S.Lee,I.G.Park,Theevaluationofthemicrotracksandmicrodimplesontribologicalcharacteristicsofthrustballbearings,Int.J.Nanosci.Nanotechnol.11
(1)(2011)701–705.
[6]Y.S.Pyoun,J.H.Park,C.M.Suh,I.H.Cho,C.S.Lee,I.G.Park,A.Amanov,J.Park,Tribologicalcharacteristicsofradialjournalbearingsbyultrasonicnanocrys-tallinesurfacemodificationtechnology,Int.J.Mod.Phys.B15–16(2010)3011–3016.
[7]M.Nakano,A.Korenaga,A.Korenaga,K.Miyake,T.Murakami,Y.Ando,H.Usami,S.Sasaki,Applyingmicro-texturetocastironsurfacestoreducethefrictioncoefficientunderlubricatedconditions,Tribol.Lett.28(2007)131–137.
[8]A.Amanov,Y.S.Pyoun,B.Zhang,J.H.Park,J.Nohava,Preliminarystudyoftheeffectofmicro-scaledimplesizeonfrictionandwearunderoil-lubricatedslidingcontact,in:
ProceedingsofASIATRIB2010,Australia,2010,p.18.
[9]H.Gleiter,Nanocrystallinematerials,Prog.Mater.Sci.33(1989)223–315.
[10]K.Lu,Nanocrystallinemetalscrystallizedfromamorphoussolids:
nanocrystal-lization,structure,andproperties,Mater.Sci.Eng.R16(1996)161–221.
[11]R.Birringer,H.Gleiter,H.P.