奥氏体晶粒度测定.docx
《奥氏体晶粒度测定.docx》由会员分享,可在线阅读,更多相关《奥氏体晶粒度测定.docx(18页珍藏版)》请在冰豆网上搜索。
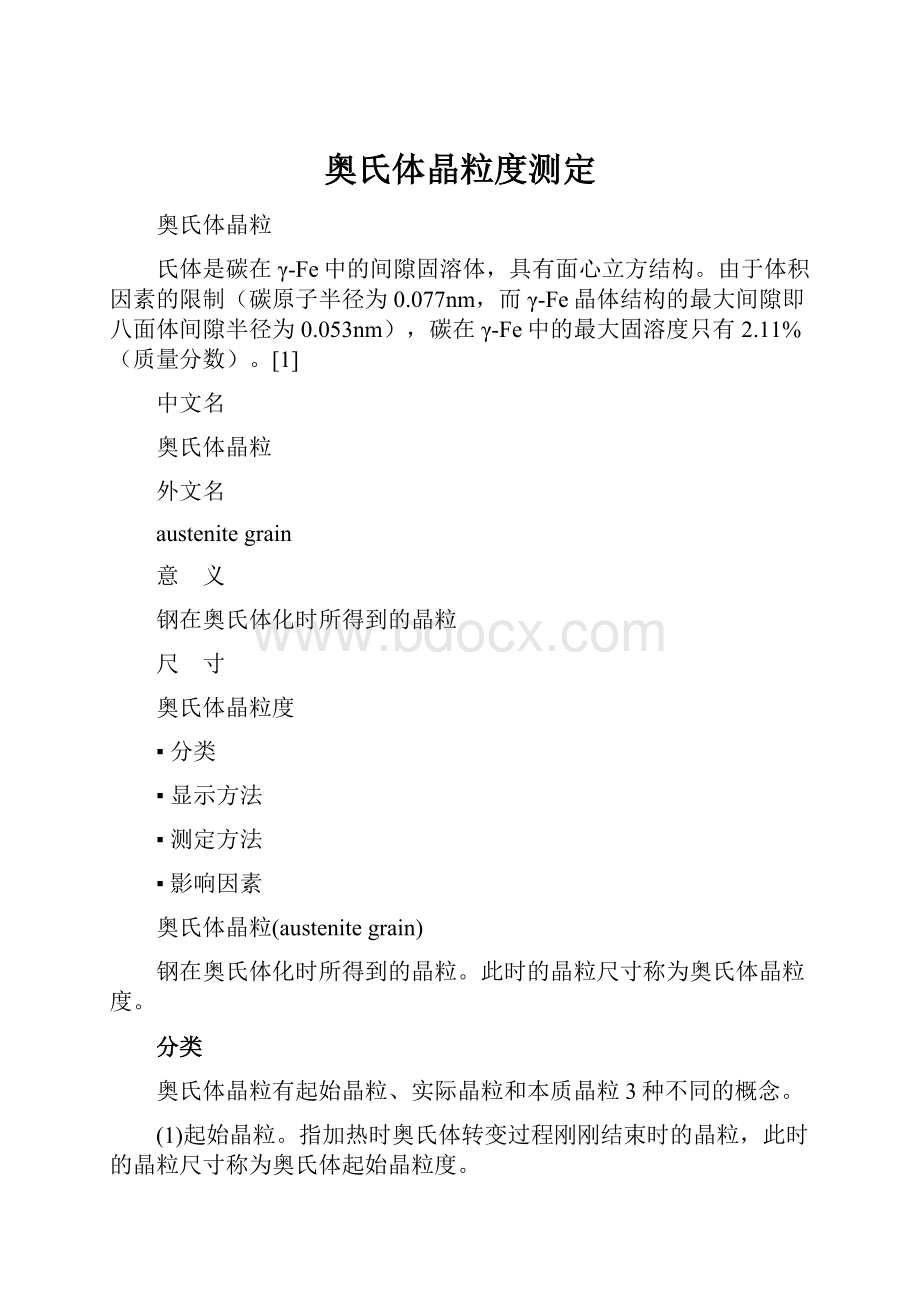
奥氏体晶粒度测定
奥氏体晶粒
氏体是碳在γ-Fe中的间隙固溶体,具有面心立方结构。
由于体积因素的限制(碳原子半径为0.077nm,而γ-Fe晶体结构的最大间隙即八面体间隙半径为0.053nm),碳在γ-Fe中的最大固溶度只有2.11%(质量分数)。
[1]
中文名
奥氏体晶粒
外文名
austenitegrain
意 义
钢在奥氏体化时所得到的晶粒
尺 寸
奥氏体晶粒度
▪ 分类
▪ 显示方法
▪ 测定方法
▪ 影响因素
奥氏体晶粒(austenitegrain)
钢在奥氏体化时所得到的晶粒。
此时的晶粒尺寸称为奥氏体晶粒度。
分类
奥氏体晶粒有起始晶粒、实际晶粒和本质晶粒3种不同的概念。
(1)起始晶粒。
指加热时奥氏体转变过程刚刚结束时的晶粒,此时的晶粒尺寸称为奥氏体起始晶粒度。
(2)实际晶粒。
指在热处理时某一具体加热条件下最终所得的奥氏体晶粒,其尺寸大小即为奥氏体实际晶粒度。
(3)本质晶粒。
指各种钢加热时奥氏体晶粒长大的倾向,晶粒容易长大的称本质粗晶粒,晶粒不易长大的称本质细晶粒。
通常在实际金属热处理条件下所得到的奥氏体晶粒大小,即为该条件下的实际晶粒度,而一系列实际晶粒度的测得即表示出该钢材的本质晶粒度。
据中国原冶金工业部标准YB27—77规定,测定奥氏体本质晶粒度是将钢加热到930℃,保温3~8h后进行。
因此温度略高于一般热处理加热温度,而相当于钢的渗碳温度,经此正常处理后,奥氏体晶粒不过分长大者,即称此钢为本质细晶粒钢。
显示方法
绝大部分钢的奥氏体只是在高温下才是稳定的。
因此欲测定奥氏体晶粒就得设法将高温状态奥氏体轮廓的痕迹在室温下显示出来,常用的显示奥氏体晶粒的方法可归纳为渗入外来元素法、化学试剂腐蚀法和控制冷却速度法3种。
(1)渗入外来元素法。
如渗碳法和氧化法,是利用奥氏体晶界优先形成渗碳体和氧化亚铁等组成物,形成网络显示出奥氏体轮廓。
渗碳法一般适用于不高于0.3%c的渗碳钢和含不高于0.6%c而含碳化物元素较多的其他类型钢。
氧化法却适用于任何结构钢和工具钢。
(2)化学试剂腐蚀法。
钢材经不同温度的淬火一回火处理后,磨光并用饱和苦味酸水溶液和新洁尔灭几滴浸蚀能抑制马氏体组织,促使奥氏体晶界的显示。
或者直接用盐酸1~5mL、苦味酸(饱和的)和乙醇浸蚀,使马氏体直接显示出来,利用马氏体深浅不同和颜色的差异而显示出奥氏体的晶粒大小,此法适用于合金化程度高的能直接淬硬的钢。
(3)控制冷却速度法。
低碳钢、亚共析钢、共析钢、过共析钢可控制冷却速度使钢的奥氏体周围先共析析出网状铁素体、网状渗碳体,或使屈氏体沿晶界少量析出以显示出奥氏体晶粒。
测定方法
测定奥氏体晶粒度常用比较法和统计法。
比较法测定奥氏体晶粒度是根据YB27—77级别图与之相比较。
标准晶粒度分8级,1~4级属粗晶粒,5~8级属细晶粒,8级以上的10~13级为超细晶粒。
此法均在100倍显微镜下观察。
晶粒度级别N与晶粒大小之间符合n=2或n’=2的关系,式中n为在放大100倍下观察时,每6.45mm视野中的平均晶粒数;n’为实际每1mm面积中平均晶粒数。
若出现过粗或过细晶粒,需在50倍或大于100倍的显微镜下观察进行换算。
表1为换算为100倍的晶粒度表。
统计法实际为测定晶粒的平均直径法。
表2为晶粒度与其他晶粒大小表示法的比较。
①为了避免在晶粒号前出现“—”号,有人把—3、—2、—1等晶粒号改为0000、000、00号。
影响因素
首先,奥氏体起始晶粒度取决于形核率N和长大速度G的比值N/G,此值愈大,奥氏体起始晶粒就愈小。
其次,在起始晶粒形成之后,钢的实际晶粒则取决于奥氏体在继续保温或升温过程中的长大倾向,而奥氏体晶粒长大倾向又与起始晶粒的大小、均匀性以及晶界能有关。
晶粒大小愈不均匀、曲率半径愈小、表面弯曲度愈大,则界面能愈大,晶粒长大的倾向性就愈大。
此外,奥氏体的实际晶粒度还受加热温度、保温时间、钢的成分以及第二相颗粒的大小、多少、性质、原始组织和加热速度等的影响。
(1)加热速度和保温时间的影响。
晶粒长大和原子的扩散密切相关,温度愈高,相应的保温时间愈长,原子的活动能力愈大,扩散愈容易进行,奥氏体晶粒亦将愈粗大。
(2)加热速度的影响。
加热速度实质上是过热度问题,过热度愈大,即成核率与成长速度之比越大,将获得细小的起始晶粒。
虽然如此,但高温下奥氏体晶粒极易长大,因此,在高温下不能有长的保温时间。
(3)钢中含碳量的影响。
在钢中含碳量不足以形成未溶解的碳化物时,含碳量增高,奥氏体的晶粒容易长大而粗化。
当形成未溶解的二次渗碳体时,因奥氏体晶粒长大受第二相的阻碍作用,使奥氏体晶粒长大的倾向反而减小。
(4)脱氧剂及合金化元素的影响。
用铝脱氧的钢,晶粒长大的倾向小,属本质细晶粒钢。
这是因为钢中含有大量难溶的六方点阵结构的A1N、机械地阻碍奥氏体长大。
用硅和锰脱氧的钢,晶粒长大的倾向大,一般属于本质粗晶粒钢。
其他合金元素按阻碍奥氏体晶粒长大程度的不同,可以分为:
有强烈阻碍晶粒长大作用的,如铌、锆、钛、钽、钒和铝等;有中等阻碍作用的,如钨、钼和铬等;稍有阻碍或无阻碍作用的,如铜、镍、钴和硅等;有增大晶粒长大倾向的,如碳(指溶入奥氏体中的)、磷、锰等。
(5)原始组织的影响。
钢的原始组织愈细、碳化物分散度愈大,所得到的奥氏体起始晶粒愈细小。
但从晶粒长大的原理可知,起始晶粒愈细小,则钢的晶粒长大倾向性愈大,即钢的过热敏感性增大,生产上难于控制。
所以原始组织极细的钢,不可用过高的加热温度和长的保温时间,而宜采用快速加热、短时保温的热处理工艺。
晶粒度的作用加热时所得到的奥氏体实际晶粒的大小,对冷却后钢的组织和性能有很大的影响。
一般地说,粗大的奥氏体实际晶粒往往导致冷却后获得粗大的组织,而粗大的组织又往往相应地具有较低的塑性和韧性。
就冲击韧性而言,普通碳钢和低合金钢的奥氏体晶粒度每细化一级,冲击韧性值能提高19.6~39.2J/cm,同时冷脆转化温度可降低10℃以上。
因此,在热处理时应严格控制奥氏体晶粒大小,以获得良好的综合性能。
细化晶粒已成为强化金属材料的重要手段之一。
通过多次反复奥氏体化处理,或用交变冷变形及在(α+γ)两相区退火等方法,获得超细化奥氏体晶粒,可以同时提高钢的强度和韧性。
特别是低温下使用的高强度合金,经此类处理后可使其断裂韧性大幅度提高,例如将40crNiMo钢的奥氏体晶粒度由5~6级细化到12~13级时,其KIc值可由1.382kPa·m。
(138.2×10N/cm)提高到2.607kPa·m(260.7×10N/cm)。
实验钢的奥氏体晶粒度的测定
在钢铁等多晶体金属中,晶粒的大小用晶粒度来衡量,其数值可由下式求出:
式中:
n—显微镜放大100倍时,6.45cm2(1in2)面积内晶粒的个数。
N—晶粒度
奥氏体晶粒的大小称奥氏体晶粒度。
钢中奥氏体晶粒度,一般分为1~8等8个等级。
其中1级晶粒度晶粒最粗大,8级最细小(参看YB27—64)。
奥氏体晶粒的大小对以后冷却过程中所发生的转变以及转变所得的组织与性能都有极大的影响。
因此,研究奥氏体晶粒度的测定及其变化规律在科学研究及工业生产中都有着重要的意义。
一、奥氏体晶粒度的一般概念
奥氏体晶粒按其形成条件不同,通常可分为起始晶粒、实际晶粒与本质晶粒三种,它们的大小分别以起始晶粒度,实际晶粒度与本质晶粒度等表示。
1、起始晶粒度
在临界温度以上,奥氏体形成刚刚结束时的晶粒尺寸,称起始晶粒度。
起始晶粒度决定于奥氏体转变的形核率(n)及线生长速度(c)。
每一平方毫米面积内奥氏体晶粒的数目N与n及c的关系为
由上式可知,若n大而c小,则起始晶粒就细小。
若n小而c大则起始晶粒就粗大。
在一般情况下n及c的数值决定于原始组织的形态和弥散程度以及加热时的加热速度等因素。
由于在珠光体中存在着大量奥氏体形核部位,n极大。
故奥氏体的起始晶粒总是比较细小的。
如果加热速度快,则转变被推向高温,奥氏体起始晶粒将更加细化。
这是因为,随着加热速度的增大和转变温度的升高,虽然形核n和c都增大,但n比c增加的幅度更大。
表1—6示出钢在加热时,奥氏体的n与c数值与加热温度的关系,由表1—6中的数据可知。
相变温度从740℃提高到800℃时n增大280倍而c仅增加40倍。
表1—6奥氏体形核(n)和线生长速度(c)与温度的关系
温度
740℃
750℃
760℃
780℃
800℃
形核率(n)(个/毫米3•秒)
2280
——
11000
51500
61600
线生长速度(c)(毫米/秒)
0.001
0.004
0.01
0.026
0.041
应当指出,奥氏体起始晶粒随加热速度的增大而细化的现象,只是在加热速度不太大时比较明显。
当加热速度很大时起始晶粒不再随之细化(见表1—7)
表1—7加热速度对起始奥氏体晶粒大小的影响
加热方法
加热速度℃/秒
加热温度(淬火后铁
素体消失的温度)
起始奥氏体晶粒的平均面积μm2
炉内加热
0.03℃
825℃
60
2℃
825℃
40
8℃
830℃
30
感应加热
200℃
870℃
28
1000℃
900℃
29
这可能是由于在快速加热时,转变被推向高温(大于800℃),奥氏体的核不仅可以在铁素体与渗碳体的交界面上形成,而且可以在铁素体晶粒内嵌镶块的边界上形成。
铁素体的含碳量虽然很低,但铁素内碳的分布是不均匀的,碳原子大都集中在嵌镶块边界。
实验测定嵌镶块边界上的碳浓度或达0.2—0.3% 。
由Fe—Fe3C状态图可知,这样的地区,对应的奥氏体形成温度为800~840℃(实验证明嵌镶块边界的厚度亦远大于该温度下临界晶核的尺寸)。
因此,只要加热速度足以把转变温度提高到上述范围,则奥氏体的核除了在铁素体与渗碳体的分界面上形成外,还将在铁素体嵌镶块边界上大量形成,增加了形核率,因而使奥氏体晶粒进一步细化。
但是,当加热速度继续增大,使转变温度超过840℃,因不能继续出现新的形核部位,奥氏体晶粒也将不能继续细化。
上述关于加热速度的影响,是限制在常用的普通加热速度范围之内。
近几年来,随着科学技术的发展,出现了加热速度高于1000℃/秒的所谓“超快速加热淬火法”,如超高频脉冲加热,激光加热或电子束加热等方法。
经过这些方法加热后以极快的令速淬火,得到的组织极细,甚至在30万倍的电子显微镜下观察,仍看不清楚该种组织的细节。
2、实际晶粒度
在热处理(或热加工)的某一具体加热条件下所得到的奥氏体晶粒的大小称为实际晶粒度。
奥氏体转变终了后,若不立即冷却而在高温停留,或者继续升高加热温度,则奥氏体将长大。
因为上述过程在热处理时是不可避免的,所以奥氏体开始冷却时的晶粒(实际晶粒度)总要比起始晶粒大。
实际晶粒度除了与起始晶粒度有关外,还与钢在奥氏体状态停留的温度及时间有关,在快速加热时,与加热速度和最终的加热温度有关。
当加热温度相同时,加热速度越大,实际奥氏体晶粒越细小。
奥氏体晶粒的长大是自发的,因为减少晶界可以降低表面能。
如果不存在阴碍晶粒长大的因素而又给以足够的时间,则从原则上说应该能长成一单晶奥氏体。
但是由于存在着一些阻碍奥氏体晶粒长大的因素,所以当达到一定尺寸后就不再长大了。
奥氏体晶粒的长大是通过大晶粒吞并小晶粒进行的。
在长大阶段晶粒大小是不均匀的。
等到各个晶粒都趋向同一大小时,晶粒不再长大。
要使晶粒进一步长大,必须提高温度。
实验证明,加热温度越高,晶粒长大越快,最后得到的晶粒也越粗大。
显然,快速加热时,虽然起始晶粒较细小,但如控制不好(加热温度过高或保温时间过长),则由于所处的温度较高,奥氏体极易长大。
为什么温度一定时,奥氏体晶粒长大到一定大小就不再继续长大了呢?
为什么有的钢种奥氏体晶粒容易长大,而有的不易长大?
对于这些问题目前一般都用机械阻碍理论来解释。
认为钢中存在一些难溶的化合物,分布在奥氏体晶界上,阻碍了奥氏体晶粒的长大。
只有当温度进一步提高,一部分化合物溶入奥氏体后,奥氏体才能继续长大。
长大到一定程度后以被尚未溶解的化合物所阻碍,不能再长大。
只有再提高温度才能进一步长大。
由于不同钢的化学成份及冶炼方法不同,这样就导致了有的钢种奥氏体晶粒容易长大,而另一些钢种奥氏体晶粒不易长大。
3、本质晶粒度
图1-29奥氏体晶粒尺寸变化示意图
1.本质细晶粒钢2.本质粗晶粒钢
把钢材加热到超过临界点以上的某一特定温度,并保温一定时间(通常规定为930℃保温8小时),奥氏体所具有晶粒大小称为奥氏体本质晶粒度。
之所以选用930℃,是因为对于一般钢材来讲,不论进行何种热处理,如淬火、退火、正火、渗碳等,加热温度都在930℃以下。
如果在930℃保温8小时后,奥氏体晶粒几乎不长大,则在热处理过程中就不会出现粗大的奥氏体晶粒。
本质晶粒度即标志着上述特定温度范围内,随着温度的升高奥氏体晶粒的长大倾向:
奥氏体晶粒显著长大的钢(得到奥氏体晶粒为1—4级),定为本质粗晶粒钢;奥氏体晶粒长大不显著的钢(得到的奥氏体晶粒度为5—8级),定为本质细晶粒钢。
必须指出,本质晶粒度只是反映了930℃以下奥氏体晶粒长大的倾向。
超过930℃以后,本质细晶粒钢的奥氏体实际晶粒度可能比本质粗晶粒钢的实际晶粒度还粗(参看图1—29所示)。
二、研究奥氏体晶粒度的意义
奥氏体晶粒度对钢的性能有着重要的影响。
通常认为,本质晶粒度对钢的工艺性能影响很大,对其使用性能的影响常常是间接的,而实际晶粒度则对钢的使用性能有着更直接的影响。
1、实际晶粒度
实际晶粒度粗大往往使钢的机械性能特别是冲击韧性、疲劳性能降低,实际晶粒度细小可以提高钢的屈服强度、正断强度、疲劳强度,同时使钢材具有较高的塑性和冲击韧性,并能降低钢的脆性转变温度。
因此在制定热处理工艺时,在一般情况下应尽量设法获得细小的奥氏体晶粒。
按目前常用的生产工艺,对结构钢来说仅能使奥氏体晶粒细化到8级,很难再进一步细化。
晶粒细化到10级以上(d<10—2毫米)则称为超细晶粒。
用来获得这种超细晶粒的特殊的加工处理方法称为超细化处理。
近年的研究工作表明,采用超细晶粒化处理方法,可以使奥氏体晶粒细化到15级使铁素体细到16级。
从实验数据还知道,将合金结构钢的奥氏体晶粒度从9级细化到15级后钢的屈服强度(调质状态)从115kg/mm2提高到142kg/mm2,并使它的脆化转变温度从—50℃下降到—150℃;将低碳钢的铁素体晶粒从8级细化到16级后钢的屈服强度(退火状态)从20kg/mm2提高到55kg/mm2, 将碳素工具钢的奥氏体晶粒度从8级细化到15级后,钢的硬度(低温回火状态)从HRC63.5提高到HRC65。
晶粒细化能提高钢的综合力学性能,这是当前热处理中能使钢的强度和韧性同时得到提高的方法之一。
现有使奥氏体晶粒超细化的工艺方法很多,如快速循环加热淬火、循环加热回火、快速加热及形变热处理等。
它们的工艺曲线分别示于图1—30,图1—31,图1—32,图1—33,图1—34。
图1—30钢的超细晶粒化处理工艺
(多次快速加热冷却法)
图1—31循环加热正火法
图1—32摆锤式循环处理
图1—33加热速度、重复次数对奥氏体晶粒度的影响
重复处理次数
图1—34钢的超晶粒处理工艺(形变热处理)
放大100倍后一平方英寸视域内奥氏体晶粒数
下面将较为典型的奥氏体晶粒超细化处理方法介绍如下:
根据α→γ→α多次循环相变,可使奥氏体晶粒细化的原理,将40Cr钢加工成φ20×3的薄片试样进行了超细化处理,为了便于比较晶粒的大小,其热处理工艺选了三种,如图1—35(a)、(b)、(c)所示。
根据图1—35(a)的热处理工艺曲线将试样用盐炉加热到840℃保温2分钟后立即水冷至室温,经测定晶粒度为7~8级之间,如图1—36(a)所示,其硬度为HRC60。
图1—35(b)所示工艺将试样加热到840℃保温2分钟后立即淬入水中冷至室温,然后再放入760℃的盐炉中加热保温2分钟立即淬入水中冷至室温,再放入840℃的盐炉中加热保温2分钟
a)
b)
c)
图1—351次,3次和5次循环热处理工艺图
a.1次加热冷却,b.3次加热冷却,c.5次加热冷却
图1—36(a)40Cr1次加热冷却
奥氏体晶粒大小×400(4/5)
图1—36(b)40Cr3次加热冷却
奥氏体晶粒大小×400(4/5)
图1—36(c)40Cr5次加热冷却
奥氏体晶粒大小×400(4/5)
时间分
时间分
时间分
温度
水冷至室温。
经过测定奥氏体的晶粒度为9~10级,如图1—36(b)所示,其硬度为HRC60.5。
按图1—35(c)工艺曲线处理试样比图1—35(b)多循环了两次,测得的奥氏体晶粒度达到11~12级如图1—36(c)所示,其硬度为HRC61。
从实验的结果看出经过循环处理后晶粒得到细化,硬度略有提高,而且循环次数越多效果越显著。
2、本质晶粒度
本质晶粒度对钢的性能的影响,主要表现在工艺性能方面,而且涉及面也比较广泛,从成型热加工,预备热处理到最终热处理,从普通热处理到复杂的化学热处理等,本质晶粒度都显示了它的作用。
表1—8即示出本质晶粒度对钢的各种工艺性能的影响。
从表1—8可以清楚地看出本质晶粒度对钢的工艺性能的影响是非常复杂的。
为了保证钢材的工艺性能与机械零件的使用性能必须对晶粒度进行研究,掌握它的变化规律及测量方法的技能,这样可以挖掘出钢材的潜力,提高零件使用寿命。
三、奥氏体本质晶粒度的显示方法
钢在临界温度以上直接测量奥氏体晶粒大小一般是比较困难的,而奥氏体在冷却过程中又将发生相变。
因此如何在室温下(即在冷却转变后)显现奥氏体晶粒的大小,就是需要解决的问题。
通常可采用以下几种方法来测定钢的晶粒度。
1、渗碳法
适用于测定渗碳钢的本质晶粒度。
测定时试样需经特定规范的热处理,其过程为表面无氧化脱碳的渗碳钢试样装入40%BaCO3+60%木炭的渗碳箱中密封之并置入930℃±10℃的炉中,保温8小时,然后随炉以50℃/小时速度缓慢冷至600℃以下,再空冷或缓冷至室温。
表1—8本质晶粒度对钢的性能的影响
钢的状态
本质粗晶粒
本质细晶粒
锻造
在监界温度
以上加热
倾向于粗化
倾向于保留细晶粒
高温正火
冲击韧性较低;较好的切削加工性,但表面粗糙,弹性极限较低
冲击韧性较高;切削性能差,但表面光洁度好;有较高的弹性极限
工具钢退火
比较容易球化
淬火加热
允许温度范围窄
允许温度范围宽
淬火冷却
淬透性大,软点倾向小易于变形及开裂
淬透性较低,形成软点倾向性大;不易变形及开裂
渗碳时
渗碳速度快,层较深
渗碳速度慢,层较浅
渗碳后
中心易脆,需重新细化中心处理;表面硬度均匀
中心韧性好,可直接从渗碳箱中取出淬火,有产生软点的可能性
处理后试样表面层含碳量达到过共析成份,经磨制(标准规定至少磨去2毫米深)、抛光和浸蚀(浸蚀剂可用4%硝酸酒精溶液或4%苦味酸酒精溶液)后,即可得到如图1—37所示珠光体+网状渗碳体组织。
图1—37中渗碳网所包括的面积可反映出奥氏体的晶粒。
在操作中,渗碳剂应严格干燥,渗碳箱须仔细密封,渗碳后必须缓慢冷却。
当渗碳浓度不足时磨面打磨深度可浅些。
虽然渗碳法适于测量渗碳钢的本质晶粒度,但在实践中沿晶界析出的碳化物网有时不连续,也有时会出现奇异的“大晶粒”、或大晶粒套小晶粒的混合等问题,给正确确定奥氏体晶粒带来了不少困难,同时渗碳所需时间长,耗费人力,电力较多。
2、氧化法
适用于测定各种钢的本质晶粒度。
这种方法需将试样进行如下处理:
将磨光、抛光后的试样放入硼砂槽或其他盐浴中,加热至930℃±10℃,保温3小时后再放入930℃±10℃的
的盐浴热腐蚀2分钟,随之在煤油中冷却;再进行短时间抛光,腐蚀(可用4%苦味酸酒精溶液)以显示奥氏体晶粒度。
生产实践中也常用一种更简单的方法,即将磨光(可用03~04号细砂纸)的试样埋入生铁屑中并在930℃±10℃的炉中保温3小时后取出在空气中氧化瞬间(几秒钟),随之淬入水中,再用细砂纸磨光、抛光和腐蚀以显示晶粒度。
所得结果如图1—38所示。
图1-37经浸蚀后晶界上呈黑色的碳化物×100
图1-38T7钢用氧化法所得奥氏体晶粒的
大小×100
采用氧化法显示晶粒时,经常因氧化过重或磨掉深度过浅使奥氏体晶内的嵌镶块边界也与晶间一同被氧化后并显示,同时试样也容易受奥氏体化前期低温氧化的影响,因此往往在试样表层遗留下细晶的假相。
若加热时保护不当产生全脱碳区,也要出现假的大晶粒。
因此,在氧化法操作中,应严防加热及保温过程中的氧化与脱碳。
3、网状铁素体法
图1-3945钢加热至930℃±10℃保温3小时
空冷所得奥氏体晶粒大小×100
图1-40T8钢经腐蚀后晶界上呈黑色的屈氏体组织×400
网状铁素体法适用于测定亚共析钢的奥氏体晶粒。
其过程是将试样加热到930℃±10℃,保温3小时后再根据钢种不同,选择适当的冷却方法(可直接水冷、油冷、空冷、炉冷或等温冷却等),将试样冷却。
试样处理后,用硝酸或苦味酸酒精溶液腐蚀,以便显示出围拢在腐蚀变黑的组织(珠光体、贝氏体或马氏体)周围的网状铁素体(见图1—39所示);铁素体所环挠面积的尺寸即为原奥氏体晶粒的大小。
4、网状珠光体(屈氏体)法
网状珠光体法适用于淬透性不大的碳素钢及低合金钢。
奥氏体晶粒的测量,将试样在930℃±10℃炉内加热,保温3小时后,将试样一端淬入水中。
冷却后在试样过渡带可清晰地看到围绕在马氏体周围的黑色屈氏体组织,它所环绕的面积,即为原奥氏体晶粒。
如图1—40所示。
试样热处理后,磨去脱碳层,抛光后用硝酸或苦味酸酒精溶液腐蚀。
5、加热缓冷法
适用于测定过共析钢的奥氏体晶粒度。
试验时将试样加热至930℃±10℃,保温3小时后冷却到600℃(冷却速度为80~100℃/小时),使碳化物沿奥氏体晶界析出以显示晶粒大小。
经上述热处理的试样抛光后,应使用硝酸或苦味酸酒精溶液腐蚀。
6、直接腐蚀法
直接腐蚀法也叫晶粒边界腐蚀法。
此法适用于测定淬火得到的马氏体或贝氏体组织的钢的奥氏体晶粒度。
试样不经磨制即可进行热处理:
将试样加热至930℃±10℃,保温3小时后水冷,然后磨去脱碳层制成金相试样,用含有0.5~1%烷基磺酸盐的100克苦味酸饱和水溶液腐蚀。
由于晶粒边界被腐蚀变黑即可用以测定奥氏体的晶粒度。
所得结果如图1—41所示。
为了得到更清晰的组织,试样可经二次或三次腐蚀、抛光重复操作;或将腐蚀剂加热到50℃±10℃后进行热腐蚀。
也可先将试样在烷基苯磺酸钠饱和苦味酸水溶液中浸蚀,经抛光去掉表面黑膜,再用饱和苦味酸洒精溶液腐蚀再次轻微抛光后即可进行观察。
7、真空法
图1-41轴承钢用直接腐蚀法所得奥氏体晶粒大小×400
图1-42用真空法所得奥氏体晶粒大小
将试样磨制、抛光后装入真空炉炉中,当真空度达10—5毫米汞柱时,加热至930℃±10℃,保温3小时随炉冷至200℃以下,停止扩散泵,继续随炉冷至室温。
出炉后可在显微镜下直接观察(见图1—42所示)。
抛光试样在高温高真空下,由于晶界上晶格畸变,并浓聚着大量杂质便发生了选择性的挥发,因而在晶界上开成了明显的凹沟。
一般认为这种方法是最可靠的。
但由于设备条件限制,生产中很少使用。
当炉子真空度不够时也有可能因晶界杂质挥发受影响而出现假相。
在上述几种测定奥氏体晶粒度的方法中,直接腐蚀法和真空法在试验中钢表面的化学成份不发生变化(相对于渗碳法和氧化法),也不受晶界处过剩相(铁素体或渗碳体)或组织(屈氏体)的干扰,因而所显示的晶粒度较接近实际尺寸。
另外,直接腐蚀法对实验用的设备没有特殊要求,是值得推广的一种方法。
上述