设计组合机床.docx
《设计组合机床.docx》由会员分享,可在线阅读,更多相关《设计组合机床.docx(18页珍藏版)》请在冰豆网上搜索。
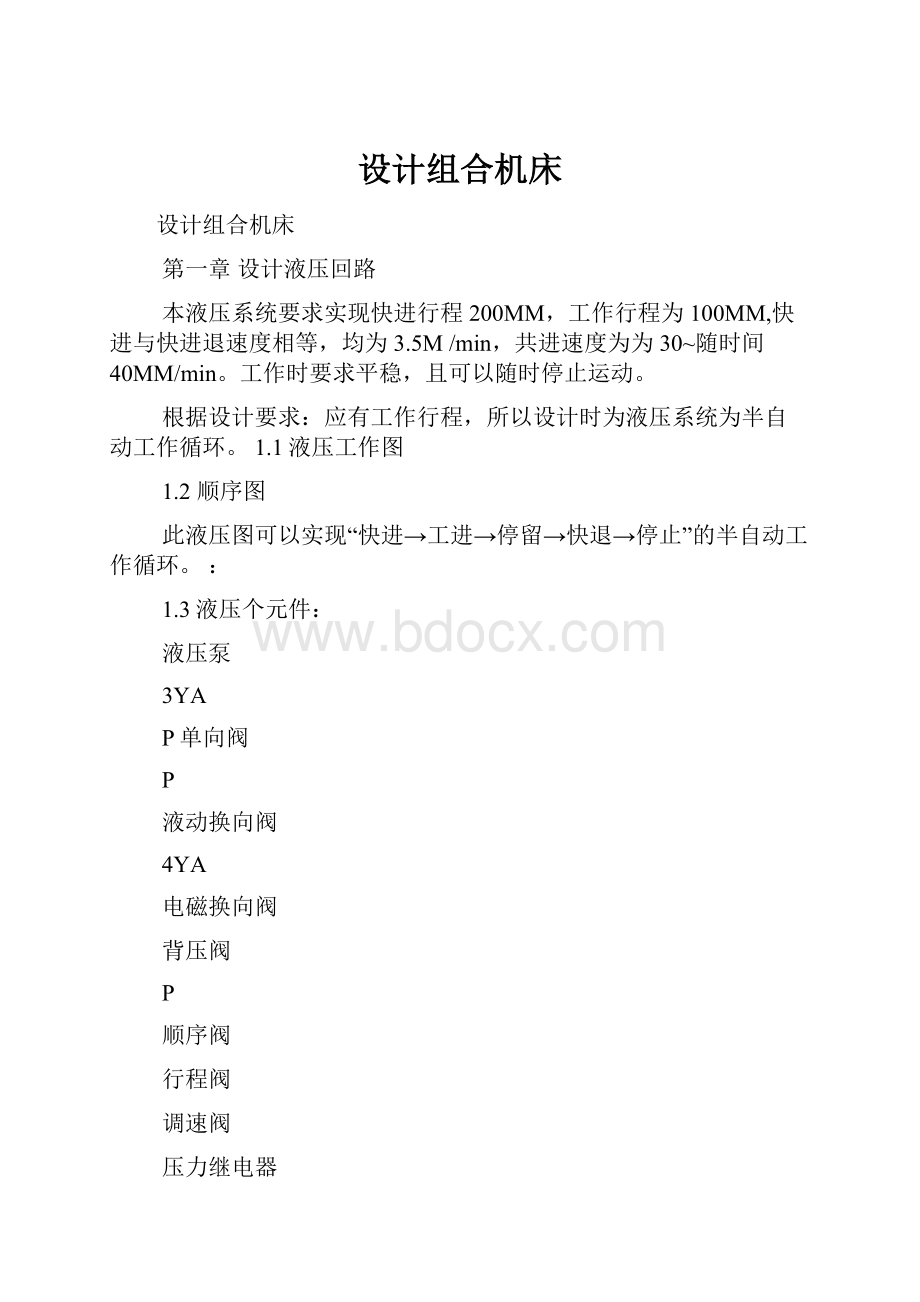
设计组合机床
设计组合机床
第一章设计液压回路
本液压系统要求实现快进行程200MM,工作行程为100MM,快进与快进退速度相等,均为3.5M/min,共进速度为为30~随时间40MM/min。
工作时要求平稳,且可以随时停止运动。
根据设计要求:
应有工作行程,所以设计时为液压系统为半自动工作循环。
1.1液压工作图
1.2顺序图
此液压图可以实现“快进→工进→停留→快退→停止”的半自动工作循环。
:
1.3液压个元件:
液压泵
3YA
P单向阀
P
液动换向阀
4YA
电磁换向阀
背压阀
P
顺序阀
行程阀
调速阀
压力继电器
1.4电磁阀和行程阀工作顺序图:
液压缸工作循环
型号来源
电磁铁
行程阀
1YA2YA3YA4YA
+-+-+-+-+
快进工进止位丁停留快退原位停止暂停
启动按钮行程阀
-
压力继电器:
止位丁时间继电器挡块压终点开关换向阀
1.5电器回路图.
SB1为开始开关SB2为暂停开关SB3暂停恢复
第二章组合机床液压系统的工况分析
2.1负载分析
系统的负载包括切削负载、惯性负载及摩擦阻力负载。
由设计书给出,轴向切削力为24000N;滑台移动部件总质量为510KG;加,减速时间为0.2S;采用平导轨,静摩擦系数为0.2,动摩擦系数为0.1。
2.1.1切削负载
由机械切削加工方面的知识可知,用高速钢钻头(单个)钻铸铁孔时轴向切削力Ft(单位为N)为:
Ft=25.5Ds0.8(HBS)0.6
式中:
D—钻头直径,单位为mm;
s—每转进给量,单位为mm/r;HBS—铸件硬度。
根据组合机床加工特点,钻孔时主轴转速n和每转进给量s按“组合机床设计手册”取:
对φ13.9mm的孔:
n1=360r/min,s1=0.147mm/r;对φ8.5mm的孔:
n2=550r/min,s2=0.096mm/r;所以,系统总的切削负载Fq为:
Fq=10⨯25.5⨯13.9⨯0.147
0.8
⨯260
0.6
+2⨯25.5⨯8.5⨯0.096
0.8
⨯260
0.6
=27667.069N
2.1.2惯性负载Fm=m
∆v
5
=120=66.6N67∆t60⨯0.15
阻力负载
机床工作部件对动力滑台导轨的法向力为:
Fn
=mg=120⨯9.8=1176N
2.1.3静摩擦阻力
6Ftf=fsFn=0.2⨯117=
23N5.
2.1.4动摩擦阻力
6Ffd=fdFn=0.1⨯117=
11N7.
由此得出液压缸在各工作阶段的负载,液压缸在各工作阶段的负载FL:
按表数值绘制的动力滑台负载图:
组合机床液压缸负载图
2.2液压系统主要参数的确定
根据表2、表3可知,当组合机床在最大负载约为24000N时,取液压系统工作压力p1=4MPa。
表2按负载选择系统工作压力
表3按主机类型选择系统工作压力
鉴于要求动力滑台快进、快退速度相等,液压缸可选用双作用单活塞杆式,并在快进时作差动连接。
在此情况下,通常液压缸无杆腔的工作面积A1为有杆腔工作面积A2的两倍,即速比ϕ
=A1/A2=2。
在钻孔加工时,液压缸回油路上必须具有背压p2,以防止孔钻通时滑台突然前冲。
在液压缸结构参数尚未确定之前,一般按经验数据估计一个数值。
系统背压的一般经验数据为:
回油路有调速阀或背压阀的系统取0.5MPa~1.5MPa,现取液压缸回油背压推荐值取p2=0.6MPa。
快进时,液压缸作差动连接,管路中有压力损失,有杆腔的压力应略大于无杆腔,但其差值较小,可先按0.3MPa考虑。
快退时回油腔中也应具有背压,这时p2也可按0.6MPa估算。
用工进时的负载值计算液压缸面积(取液压缸的机械效率ηm=0.96):
A2=
FL
ηm(p1ϕ-p2)
=
23485.121
0.96⨯(4⨯2-0.6)⨯10
-3
6
=3.306⨯10m
-32
A1=ϕA2=2A2=6.612⨯10
m
2
D=
=0.0918m
d=0.707D=0.065m
将直径按GB/T2348-1993(2001)圆整得:
D=0.10m
;d
=0.08m
由此求得液压缸两腔的实际有效面积为:
A1=πD/4=7.85⨯10
2
-3
m
2
根据上述液压缸两腔的实际有效面积值,可估算出液压缸在各个工作阶段中的压力、流量和功率,如表4所示,并据此绘出工况图4(a)所示:
表4液压缸在不同工作阶段的压力、流量和功率值
工况图
图4(a)组合机床液压系统工况图
第三章动力滑台液压系统工作原理
3.1快进
快进时压力低,顺序阀6关闭,变量泵1输出最大流量。
按下启动按钮,电磁铁1YA通电,电磁换向阀4左位接入系统,液动换向阀3在压力油作用下也将左位接入系统工作,其油路为:
控制油路
进油路:
﹛泵1→阀4(左)→I1→阀3左端﹜使阀3换为左位回油路:
﹛阀3右端→L2→阀4(左)→油箱﹜换向时间由L2调整主油路
进油路:
﹛泵1→单向阀2→阀3(左)→行程阀11→缸左腔﹜差动快进回油路:
﹛缸右腔→阀3(左)→单向阀7→油箱﹜差动快进
这时液压缸两杠连通,滑台差动快进。
节流阀L2可用以调节液动换向阀阀芯移动速度,也调节主换向阀的换向时间,以减小换向冲击。
3.2工进进给
当滑台快进终了时,滑台下的挡块压下行程阀11,切断了快速运动的进油路.其控油了未变,而主油路中,压力油只能通过调速阀8进入液压缸左腔.由于油液流经调速阀而使系统压力升高,液压顺序阀6开启,单向阀7关闭,液压缸右腔的油液经阀6和背压阀5流回油箱.同时,泵的流量也自动减小.滑台实现由调速阀的工进进给,其主油路为:
进油路:
﹛泵1→阀2→阀3(左)→调速阀8→缸左腔﹜回油路:
﹛缸右腔→阀3(左)→阀6→背压阀5→油箱﹜
3.3止位钉停留
滑台完成第二次工作进给后,液压缸碰到滑台座前端的止位钉(可调节滑
台行程的螺钉)后停止运动。
这时液压缸左腔压力升高,当压力升高到压力继电器12的开启压力时,压力继电器动作,向时间继电器发出电信号,由时问继电器延时控制滑台停留时间。
这时的油路同第二次工作进给的油路,但实际上,系统内油液已停止流动,液压泵的流量已减至很小,仅用于补充泄漏油。
设置止位钉可提高滑台工作进给终点的位置精度及实现压力控制。
3.4快退
滑台停留时间结束时,时间继电器发出信号,使电磁铁2YA通电,lYA、
3YA断电。
这时电磁换向阀4右位接人系统,液动换向阀3也换为右位工作,主油路换向。
因滑台返回时为空载,系统压力低,变量泵的流量又自动恢复到最大值,故滑台快速退回,其油路为控制油路
进油路:
﹛泵1→阀4(右)→工2→阀3右端﹜使阀3换为右位回油路:
﹛阀3左端→L1→阀4(右)一油箱﹜(换向时间由L1调节)主油路
进油路﹛泵1→阀2(右)→阀2(右)→缸右腔﹜快退回油路:
﹛缸左腔→阀13→阀3(右)→油箱﹜快退
当滑台退至第一次工进起点位置时,行程阀11复位。
由于液压缸无杆腔有效面积为有杆腔有效面积的二倍,故快退速度与快进速度基本相等。
3.5原位停止
当滑台快速退回到其原始位置时,挡块压下原位行程开关,使电磁铁2YA
断电,电磁换向阀4恢复中位,液动换向阀3也恢复中位,液压缸两腔油路被封
闭,滑台被锁紧在起始位置上。
这时液压泵则经单向阀2及阀3的中位卸荷,其油路为控制油路
回油路:
﹛阀3(左)→L1﹜→阀4(中)→油箱
﹛阀3(右)→L1﹜→阀4(中)→油箱
主油路
进油路:
泵1→阀2→阀3(中)→油箱
回油路:
﹛液压缸左腔→阀13→(液压缸停止并被锁住)﹛液压缸右腔→阀13→(液压缸停止并被锁住)
单向阀2的作用是使滑台在原位停止时,控制油路仍保持一定的控制压力
(低压),以便能迅速启动。
3.6暂停
电磁阀14转换
第四章选择液压元件
4.1液压泵
在整个工作循环中液压缸的最大工作压力为3.687MPa。
假设进油路上的压力损失为0.8MPa,为使压力继电器能可靠地工作,取其调整压力高出系统最大工作压力0.5MPa,则液压泵的最大工作压力应为:
pp1=3.687+0.8+0.5=4.987MPa
液压泵在快进、快速运动时才向液压缸输油,由工况图可知,快退时液压缸的工作压力比快进时大,假设油路上的压力损失为0.5MPa(因此时进油不经调速阀,故压力损失减少),则液压泵的最高工作压力为:
p
p2
=0.434+0.5=0.934MPa
由图4(a)工况图可知,液压泵应向液压缸提供的最大流量为25.14L/min,因该系统较简单,取泄漏系数KL
=1.05,则两个液压泵的实际流量应为:
qp=1.05⨯25.14=26.397L/min
工进时输入液压缸的流量为0.392L/min,则由泵单独供油时,其流量规格最少应为3.392L/min。
根据以上压力和流量的数值查阅产品样本,最后确定选取最后确定选取PV2R12-6/26型双联叶片液压泵,其小泵和大泵的排量分别为6mL/r和26mL/r。
当液压泵的转速n若取液压泵的容积效率ηv
p
=940r/min
时该液压泵的理论流量为30.08L/min,
=0.9,则液压泵的实际输出流量为:
qp=(6+26)⨯940⨯0.9/1000=5.1+22=27.1L/min>26.397L/min
即所选液压泵的实际流量满足设计要求。
且由于液压缸在快退时输入功率最大,这时液压泵工作压力为0.934MPa、流量为27.1L/min。
取液压泵的总效率η动机所需的功率为:
P=
ppqp
=
0.934⨯27.160⨯0.75
≈0.6kW
p
=0.75,则液压泵驱动电
ηp
根据此数值查阅电动机产品样本选取Y100L-6型
电动机,其额定功率Pn
4.2阀类元件及辅助元件
根据阀类及辅助元件所在油路的最大工作压力和通过该元件的最大实际流量,可选出这些液压元件的型号及规格,如表10所列:
表10液压元件和液压辅助元件的型号及规格
=1.5kW
,额定转速nn
=940r/min
。
4.3油管
各元件间连接管道的规格按液压元件接口处的尺寸决定,液压缸进、出油管则按输入、
排出的最大流量计算。
由于液压泵选定之后液压缸在各个工作阶段的进、出流量已与原定数值不同,所以要重新计算,如表11所列:
表11液压缸的进、出流量及运动速度
由表11可以看出,液压缸在各个工作阶段的实际运动速度符合设计要求。
根据表11中的数值,取推荐流速v=3m/s,计算得与液压缸无杆腔及有杆腔相连的油管内径分别为:
dw=2⨯
=2⨯=17.31mm
dy=2⨯
=2⨯=13.85mm
液压缸进、出两根油管都选用内径φ15mm、外径φ18.2mm的15号冷拔无缝钢管。
4.4油箱取经验数据α
=7
,则油箱估算容积为:
V=αqV=7⨯27.1=189.7L
按GB2876―1981规定,取最靠近的标准值V4.5密封件的选择
=250L
。
液压系统中密封件的作用是防止工作介质的内外泄漏,以及防止灰尘,金属屑等异物侵入液压系统。
能实现上述作用的装置称为密封装置,其中起密封作用的关键元件密封元件,简称密封件。
系统的内外泄漏均会使液压系统容积效率下降,或达不到要求的工作压力,甚至使液压系统不能正常工作。
外泄漏还会造成工作介质的浪费,污染环境。
异物的侵入会加剧液压元件的磨损,或使液压元件堵塞,卡死甚至损坏,造成系统失灵。
一般的液压系统对密封件的主要要求是:
(1)在一定的压力,温度范围内具有良好的密封性能;
(2)有相对运动时,因密封件引起的摩擦应尽量小,摩擦系数应尽量稳
定;
(3)耐腐蚀、耐摩性能好,不易老化,工作寿命长,磨损后能在一定程
度上自动补偿;
(4)结构简单,装拆方便,成本低廉。
第五章验算液压系统性能
5.1验算系统压力损失:
由于系统的管路布置尚未确定,整个系统的压力损失无法全面估算,故只
能先估算阀类元件的压力损失,对压力损失的验算按一个工作循环中不同阶段分别进行。
5.1.1快进时:
滑台快进时,液压缸差动连接,由表10和表11可知,进油路上油液通过单向阀2的流量是22L/min、通过电液换向阀4的流量是27.1L/min,然后与液压缸有杆腔的回油汇合,以流量42.34L/min通过行程阀11并进入无杆腔。
因此进油路上的总压降为:
⎛22⎫⎛27.1⎫⎛42.34⎫
∑∆pV=0.2⨯+0.5⨯+0.3⨯⎪⎪⎪=0.22MPa
⎝63⎭⎝80⎭⎝63⎭
2
2
2
回油路上,液压缸有杆腔中的油液通过电液换向阀4和单向阀7的流量都是
15.242L/min,然后与液压泵的供油合并,经行程阀11流入无杆腔。
由此可算出快进时有杆腔压力p2与无杆腔压力p1之差:
⎛15.242⎫⎛15.242⎫⎛42.34⎫
∆p=p2-p1=0.5⨯+0.2⨯+0.3⨯⎪⎪⎪=0.165MPa
806363⎝⎭⎝⎭⎝⎭
2
2
2
此值小于设计估计值0.3MPa,符合要求。
5.1.2工进时:
工进时,油液在进油路上通过电液换向阀4的流量为0.392L/min,在调速阀8处的压力损失为0.5MPa;油液在回路上通过换向阀4的流量是0.14L/min,在背压阀5处的压力损失为0.6MPa,通过顺序阀6的流量为(0.14+22)L/min=22.14L/min,折算到进油路上因阀类元件造成的总压力损失为:
⎛0.392⎫∑∆pV=0.5⨯⎪+0.5+
⎝80⎭
2
22
⎡⎛0.14⎫⎛22.14⎫⎤⎛28.26⎫⎢0.5⨯⎪+0.6+0.3⨯⎪⎥⨯⎪=0.73MPa
⎝80⎭⎝63⎭⎥⎢⎣⎦⎝78.5⎭
液压缸回油腔的压力p2为:
⎛0.14⎫⎛22.14⎫
p2=0.5⨯+0.6+0.3⨯⎪⎪=0.637MPa
8063⎝⎭⎝⎭
2
2
此值略大于原估计值。
重新计算工进时液压缸进油腔压力p1,即:
Fp1=
ηam
+p2A2A1
=
23485.121+0.637⨯10⨯28.26⨯1078.5⨯10
-4
6-4
⨯10
6
=3.92MPa
考虑到压力继电器可靠动作需要压差∆pe值p应为:
y
=0.5MPa
,故工进时溢流阀9的调压
⎛0.392⎫
py>p1+∑∆p1+∆pe=3.92+0.5⨯⎪+0.5+0.5=4.92MPa
⎝80⎭
2
5.1.3快退时:
快退时,油液在进油路上通过单向阀2的流量为22L/min、通过换向阀4的流量为27.1L/min;油液在回油路上通过单向阀7、换向阀4和单向阀13的流量都是75.28L/min。
因此进油路上总压降为:
∑∆pV1
⎛22⎫⎛27.1⎫
=0.2⨯+0.5⨯⎪⎪=0.082MPa
6380⎝⎭⎝⎭
22
此值小于原估计值,所以液压泵驱动电动机的功率是足够的。
回油路上总压降为:
∑∆pV2
⎛75.28⎫⎛75.28⎫⎛75.28⎫
=0.2⨯+0.5⨯+0.2⨯⎪⎪⎪=0.1014MPa
638063⎝⎭⎝⎭⎝⎭
p
222
所以,快退时液压泵的工作压力p应为:
pp=p1+∑∆pV1+∑∆pV2=0.434+0.082+0.1014=0.6174MPa
因此大流量液压泵卸荷时顺序阀7的调定压力应大于0.6174MPa。
5.2验算油液温升
工进在整个工作循环过程中所占的时间比例达95﹪,所以系统发热和油液温升应按工进时的工况来计算。
工进时液压缸的有效功率为:
Pe=Fv2=
23485.121⨯0.0499
60
=0.02kW
这时大流量液压泵经顺序阀7卸荷,小流量泵在高压下供油。
大流量液压泵通过顺序阀7的流量为q2
2
=22L/min,故此阀在工进时的压力损失为:
2
⎛q2⎫⎛22⎫
∆p=∆pn⎪=0.3⨯⎪=0.037MPa
⎝63⎭⎝qn⎭
小液压泵工进时的工作压力p压泵的总输入功率为:
pp1q1+∆pq2
4.92⨯10⨯=
6
p1
=4.92MPa
,流量q1=5.1L/min,所以两个液
5.160
⨯10+0.037⨯10⨯
0.75
-36
2260
⨯10
-3
Pp=
ηp
=0.5757kW
液压系统的发热功率为:
∆P=Pp-Pe=0.5757-0.02=0.5557kW
为使温升不超过允许的∆T(∆T
可按下式计算油箱的最小有效容积:
=30C)值,
Vmin=10
--2
=10=0.074m
油箱总容积:
Va=1.25V=1.25⨯0.074=0.0925m=92.5L
2
所以该系统不必设置冷却器。
第六章动力滑台液压系统的特点
动力滑台的液压系统是能完成较复杂工作循环的典型的单缸中压系统,
其有如下特点。
(1)采用容积节流调速回路该系统采用了“双联叶片液压泵+调速阀+背压阀”式容积节流调速回路。
用变量泵供油可使空载时获得快速(泵的流量最大),工进时,负载增加,泵的流量会自动减小,且无溢流损失,因而功率的利用合理。
用调速阀凋速可保证工作进给时获得稳定的低速,有较好的速度刚性。
调速阀设在进油路上,便于利用压力继电器发信号实现动作顺序的自动控制。
回油路上加背压阀能防止负载突然减小时产生前冲现象,并能使工进速度平稳。
(2)采用电液动换向阀的换向回路采用反应灵敏的小规格电磁换向阀作为先导阀控制能通过大流量的液动换向阀实现主油路的换向,发挥了电液联合控制的优点。
而且由于液动换向阀芯移动的速度可由节流阀L1、L2调节,因此能使流量较大、速度较快的主油路换向平稳,无冲击。
(3)采用液压缸差动连接的快速回路主换向阀采用了三位五通阀,因此换向阀左位工作时能使缸右腔的回油又返回缸的左腔,从而使液压缸两腔同时通压力油,实现差动快进。
这种回路简便可靠。
(4)采用行程控制的速度转换回路系统采用行程阀和液控顺序阀配合动作实现快进与工作进给速度的转换,使速度转换平稳、可靠、且位置准确。
采用两个串联的调速阀及用行程开关控制的电磁换向阀实现两种工进速度的转换。
由于进给速度较低,故亦能保证换接精度和平稳性的要求。
(5)采用压力继电器控制动作顺序滑台工进结束时液压缸碰到止位钉时,缸内工作压力升高,因而采用压力继电器发信号,使滑台反向退回方便可靠。
止位钉的采用还能提高滑台工进结束时的位置精度及进行刮端面、锪孔、镗台阶孔等工序的加工。
第七章设计总结
随着毕业日子的到来,毕业设计也接近了尾声。
经过几周的奋战我的毕业设计终于完成了。
在没有做毕业设计以前觉得毕业设计只是对这几年来所学知识的单纯总结,但是通过这次做毕业设计发现自己的看法有点太片面。
毕业设计不仅是对前面所学知识的一种检验,而且也是对自己能力的一种提高。
通过这次毕业设计使我明白了自己原来知识还比较欠缺。
自己要学习的东西还太多,以前老是觉得自己什么东西都会,什么东西都懂,有点眼高手低。
通过这次毕业设计,我才明白学习是一个长期积累的过程,在以后的工作、生活中都应该不断的学习,努力提高自己知识和综合素质。
在这次毕业设计中也使我们的同学关系更进一步了,同学之间互相帮助,有什么不懂的大家在一起商量,听听不同的看法对我们更好的理解知识,所以在这里非常感谢帮助我的同学。
致谢
在此要感谢我的指导老师赵亚英对我悉心的指导,感谢老师给我的帮助。
在设计过程中,我通过查阅大量有关资料,与同学交流经验和自学,并向老师请教等方式,使自己学到了不少知识,也经历了不少艰辛,但收获同样巨大。
在整个设计中我懂得了许多东西,也培养了我独立工作的能力,树立了对自己工作能力的信心,相信会对今后的学习工作生活有非常重要的影响。
而且大大提高了动手的能力,使我充分体会到了在创造过程中探索的艰难和成功时的喜悦。
虽然这个设计做的也不太好,但是在设计过程中所学到的东西,这次毕业设计的最大收获和财富,使我终身受益。
参考文献
主要参考资料:
1.李芝主编液压传动机械工业出版社2.沈兴全吴秀玲主编液压传动与控制国防工业出版社3.陈鼎宁主编4.王守城段俊勇主编5.张利平主编
机械设备控制技术液压元件及选用液压气动技术速查手册机械工业出版社化学工业出版社化学工业出版社