产品包装生产线设计方案.docx
《产品包装生产线设计方案.docx》由会员分享,可在线阅读,更多相关《产品包装生产线设计方案.docx(35页珍藏版)》请在冰豆网上搜索。
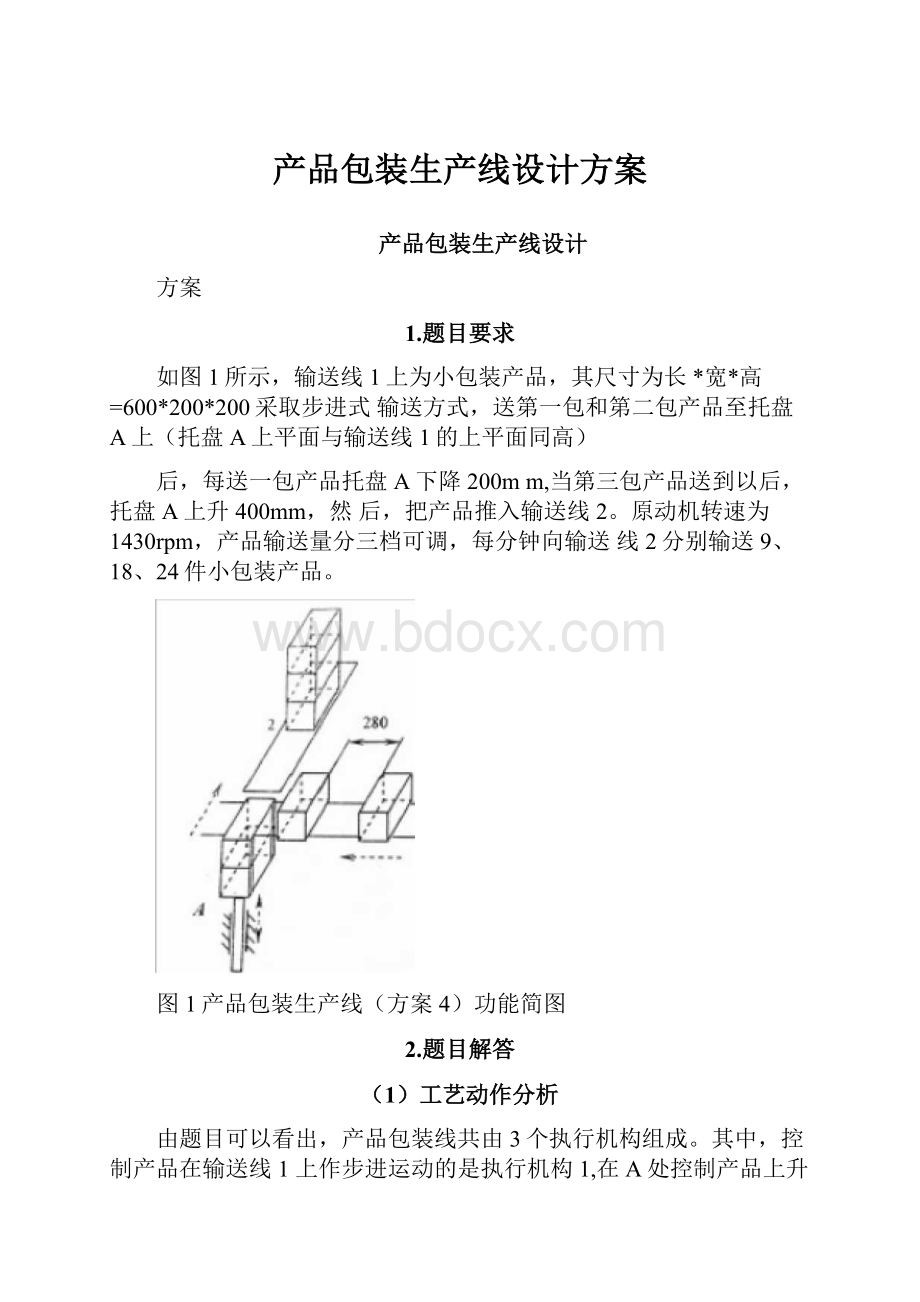
产品包装生产线设计方案
产品包装生产线设计
方案
1.题目要求
如图1所示,输送线1上为小包装产品,其尺寸为长*宽*高=600*200*200采取步进式输送方式,送第一包和第二包产品至托盘A上(托盘A上平面与输送线1的上平面同高)
后,每送一包产品托盘A下降200mm,当第三包产品送到以后,托盘A上升400mm,然后,把产品推入输送线2。
原动机转速为1430rpm,产品输送量分三档可调,每分钟向输送线2分别输送9、18、24件小包装产品。
图1产品包装生产线(方案4)功能简图
2.题目解答
(1)工艺动作分析
由题目可以看出,产品包装线共由3个执行机构组成。
其中,控制产品在输送线1上作步进运动的是执行机构1,在A处控制产品上升、下降的是执行机构2,在A处把产品推到输入线2的是执行机构3,三个执行构件的运动协调关系如图2所示。
下图中T1为执行构件1的工作周期,T2是执行构件2的工作周期,T3是执行构件3的工作周期,T3‘是执行构件3的动作周期。
由图2可以看出,执行构件1是作连续往复移动的,而执行构件2则有一个间歇往复运动,执行构件3作一个间歇往复运动。
三
T2
Ti
4
执行
构件
运动情况
执行
构件
1
进
退
进
退
进
退
进
执行
构件
2
休
降
休
降
休
升
休
休
执行
构件
3
停
进
退
停
T3
图2产品包装生产线运动循环图
(2)运动功能分析及运动功能系统图
根据前面的分析可知,驱动执行构件1工作的执行机构应该具有运动功能如图3所示。
该运动功能把一个连续的单向转动转换为连续的往复移动,主动件每转动一周,从动件(执
行构件1)往复运动一次,主动件的转速分别为9、18、24rpm。
9、18、24rpm
18、26rpm
iv1最大,iv3
图3执行构件1的运动功能
由于电动机转速为1430rpm,为了在执行机构1的主动件上分别得到12、
的转速,则由电动机到执行机构1之间的传动比iz有3种分别为:
iz1==158.89
iz2==79.4444
iz3==59.58
总传动比由定传动比ic与变传动比iv组成,满足以下关系式:
iz1=ic*iv1
iz2=ic*iv2
iz3=ic*iv3
三种传动比中izi最大,iz3最小。
由于定传动比ic是常数,因此3种传动比中最小。
若采用滑移齿轮变速,其最大传动比最好不要大于4,即:
iv1=4
则有:
ic==39.72
故定传动比的其他值为:
==2.00
==1.50
于是,有级变速单元如图4:
i=4,2.0,1.5
图4有级变速运动功能单元
在电动机和传动系统之间加一个过载保护环节。
这样,该运动功能单元不仅具有过载保护能力,
功能,如图5所示。
i=2.5
图5过载保护运动功能单元
整个传动系统仅靠过载保护功能单元的减速功能不能实现全部定传动比,因此,在传动系统
中还要另加减速运动功能单元,减速比为
i==15.9
减速运动功能单元如图6所示。
i=15.9
图6执行机构1的运动功能
根据上述运动功能分析,可以得到实现执行构件1运动的功能系统图,如图7所示。
1430rpmi=2.5i=4,2.0,1.5i=15.9
图7实现执行构件1运动的运动功能系统图
为了使用同一原动机驱动执行构件2,应该在图7所示的运动功能系统图加上个运动分
支功能单元,使其能够驱动分支执行构件2,该运动分支功能单元如图8所示。
执行构件2
有一个间歇单向转动。
执行构件3有一个执行运动,为间歇往复移动,其运动方向与执行构件1的运动方向垂直。
为了使执行构件2和执行构件3的运动和执行构件1的运动保持正确的空间关系,可以加一个运动传动方向转换功能单元,同时该运动单元具有减速的作用,传动比i=3,如图9所示。
图8运动分支功能单元1
i=3
图9运动传动方向转换的运动功能单元
经过运动传递方向转换功能单元输出的运动需要分成两个运动分支分别驱动执行构件
2的运动和执行构件3的一个运动。
因此,需要加一个运动分支功能分支单元,如图10所示。
图10运动分支功能单元2
执行构件2的一个运动是间歇往复移动,可以通过一个运动单元将连续转动转换成间歇往复移动。
如图11所示。
图11连续转动转换为间歇往复移动的运动功能单元
根据上述分析可以得出实现执行构件1和执行构件2运动功能的运动功能系统图,如图12
所示。
i=15.9
1430rpmi=2.5i=4,2.0,1.5
图12执行构件1、2的运动功能系统图
执行构件3需要进行间歇往复移动,为此,需要将连续转动转换为间歇转动。
由图2可以看出,执行构件3在一个工作周期内,其间歇时间很长,运动时间很短。
因此,需要采用一个间歇运动单元,再采用一个连续转动的放大单元,其运动功能单元如图13所示。
图13间歇运动和连续转动放大单元
然后,再把该运动功能单元输出地运动转换为往复移动,其运动功能单元如图14所示。
图14往复移动运动单元
根据上述分析,可以画出整个系统的运动功能系统图,如图
15所示。
图15产品包装生产线运动功能系统图
(3)系统运动方案拟定
根据图15所示的运动功能系统图,选择适当的机构替代运动功能系统图中的各个运动功能单元,便可拟定出机械系统运动方案。
图15中的运动功能单元1是原动机。
根据产品包装生产线的工作要求,可以选择电动机作为原动机。
如图16所示。
1430rpm
图16电动机替代运动功能单元1
图15中的运动功能单元
2是过载保护单元兼具减速功能,可以选择带传动实现,如图17所示。
/77~
图17带传动替代运动单元2
图15中的运动功能单元
3是有级变速功能单元,可以选择滑移齿轮变速传动替代,如
图18所示。
厶
■■
a
LI
Si_
IT
77777
图18滑移齿轮替代运动功能单元3
图15中的运动功能单元4是减速功能,可以选择2级齿轮传动代替,如图19所示。
rr
g
•77
m
图192级齿轮传动替代运动功能单元4
图15中运动功能单元5是运动分支功能单元,可以用运动功能单元7锥齿轮传动的主
动轮、运动功能单元6导杆滑块结构的曲柄与运动功能单元4的运动输出齿轮固连替代,如
图20所示。
:
吾却岀
1
z/z//
1
图202个运动功能单元的主动件固联替代运动功能单元5
图15中的运动功能单元
如图21所示。
6将连续传动转换为往复移动,可以选择导杆滑块机构替代,
图21导杆滑块机构替代运动功能单元6
图15中的运动功能单元7是运动传递方向转换功能和减速运动功能单元,可以用圆锥
齿轮传动替代,如图22所示。
图22圆锥齿轮传动替代减速运动功能单元7
运动单元8的类型与运动单元5相同。
图15中运动功能单元9将连续传动转换为间歇往复移动,可以选用凸轮机构固联来完成要求。
如图23所示。
图23凸轮机构固联替代功能单元9
图15中运动功能单元10是把连续转动转换为间歇转动的运动功能单元,可以用槽轮机
构替代。
该运动功能单元的运动系数为
由槽轮机构运动系数的计算公式有:
式中,
Z——槽轮的径向槽数。
则,槽轮的径向槽数为:
该槽轮机构如下图所示。
图24用槽轮传动替代运动功能单元10
图15中的运动功能单元11是运动放大功能单元,把运动功能单元10中槽轮在一个工作周期中输出的1/4周的转动转换为一周的运动,用圆柱齿轮机构替代,其传动比为i=1/4。
圆柱齿轮传动如图25所示。
i=0.25
图25用圆柱齿轮传动替代运动功能单元11
图15中运动功能单元12是把连续转动转换为连续往复移动的运动功能单元,可以用曲
柄滑块机构替代,如图所示。
图26用曲柄滑块机构替代运动功能单元12
根据上述分析,按照图15各个运动单元连接顺序把个运动功能单元的替代机构一次连
接便形成了产品包装生产线(方案4)的运动方案简图,如图所示。
(C)
(4)系统运动方案设计
1)执行机构1的设计
该执行机构是曲柄滑块机构,由曲柄,滑块,导杆,连杆和滑枕组成。
其中大滑块的行程h=480mm现对机构进行参数计算。
该机构具有急回特性,在导杆与曲柄的轨迹圆相切时候,从动件处于两个极限位置,
此时导杆的末端分别位于G和C位置。
取定CC2的长度,使其满足:
C1C2h
利用平行四边形的特点,由下图可知滑块移动的距离EiE2=CiC2=h,这样就利用了
机构急回运动特性,使滑块移动了指定的位移。
设极位夹角为显然导杆21的摆角就是取机构的行程速比系数K=1.4,由此可得极位夹角和导杆21的长度。
k100
18030
k1
l927.289mm
sin
2
图28导杆滑块机构设计
先随意选定一点为D,以D为圆心,I为半径做圆。
再过D作竖直线,以之为基础
线,左右各作射线,与之夹角15°,交圆与Ci和C点。
则弧CCa即为导杆顶部转过的
弧线,当导轨从CiD摆到CaD的时候,摆角为30°。
接着取最高点为C,在C和Ci之间做平行于GCa的直线m,该线为滑枕21的导路,距离D点的距离为
IIcos—
2
2
在Ci点有机构最大压力角,设导杆
21的长度为li,最大压力角的正弦等于
sin
max
要求最大压力角小于io0,所以有
IIsin
2
2sin
927.689
IIcos—
2
2Ii
1cosi50
2sini00
9i.02mm
Ii越大,压力角越小,取
Ii=200~400mm则取I=300mm
曲柄i5的回转中心在过
D点的竖直线上,曲柄越长,曲柄受力越小,可选
2ADI~I
23
max
取AD=600mm据此可以得到曲柄i9的长度
2)执行机构2的设计
如图27(b)所示,执行机构2的运动是将连续传动转换为间歇往复移动,可以选用齿
轮传动和直动平底从动件盘形凸轮机构固联来共同完成要求。
凸轮机构在一个工作周期的运动为
凸轮24:
第一次远休止角80,第一次回程运动角40°,第二次休止角80°,第二次回程运动角40°,近休止角80°,推程运动角30,远休止角10。
从动件推程50mm,推回程均采用无冲击的正弦加速度方式。
得到如下表格:
角度范围
S
0<0<
50
+sin(90)
+sin(90)
0
-sin(120--)
50
图29凸轮运动的位移图
根据凸轮的从动件运动规律,我们可以利用解析法设计出凸轮的轮廓。
具体设计流程:
做出-S图像,利用压力角的要求可以做出凸轮的基圆和偏距,这样,可以利用解析法求出凸
轮的形状。
由于电动机的转向是可以调整的,往右边看凸轮是顺时针转动的。
取凸轮偏距为
0,即设计成对心的滚子凸轮机构。
SI-I:
-:
iI:
隔孙
图30凸轮图
经查表许用压力角采用40°确定凸轮的基圆为353.17mm,滚子半径采用20mm的轴承。
理论轮廓坐标方程:
=(+s)cos0+ecos0;
y=(+s)sin0-esin0;
带上滚子半径的实际轮廓半径,滚子是在实际轮廓外部。
实际轮廓坐标:
X=x-X
Y=y+
理论轮廓和实际轮廓图如下图所示:
凸轮理论轮廊咲反基圆團
100
图31凸轮的理论轮廓和实际轮廓图
3)执行机构3的设计
执行机构3驱动构件2运动,由图可知,执行构件3由曲柄27,连杆29和滑块30组成。
由题可知,滑块30的行程是:
则曲柄的长度可以确定为
连杆29的长度与许用压力角有关,即
般,
则,=600mm
4)槽轮机构设计
1.确定槽轮槽数
在拨盘圆销数k=1时,槽轮槽数z=4。
2.槽轮槽间角
23=
3.槽轮每次转位时拨盘的转角2a=180°-23=90°
4.中心距
槽轮机构的中心距应该根据具体结构确定,在结构尚不确定的情况下暂定为a=150mm
5.
拨盘圆销的回转半径
入=
r=入*a=0.7071*150=106.065mm
6.
槽轮半径
E=
R=E*a=0.7071*150=106.065mm
7.锁止弧张角
Y=360°-2a=270
8.圆销半径
mm
圆整:
mm
9.槽轮槽深
h>(入+E-1)*a+=80.13mm
10.锁止弧半径
mm
取mm
5)齿轮机构设计
滑移齿轮传动设计
①确定齿轮齿数
如图18中齿轮5,6,7,8,9,10组成了滑移齿轮有级变速单元,其齿数分别为
Z5,Z6,Z7,Z8,Z9,Z10。
由前面分析可知,
iv1=4
==2.0
==1.5
按最小不根切齿数取Z9=17,则zio=iviZ9=4*17=68
为了改善传动性能应使相互啮合的齿轮齿数互为质数,取Z10=69。
其齿数和为Z9+Z10=17+69=86,
另外两对啮合齿轮的齿数和应大致相同,即
Z7+Z8~86,Z5+Z6~86
==2.0
=86-=57
同理可取,
②计算齿轮几何尺寸
取模数m=2mm,则5,6,9,10这两对齿轮的标准中心距相同
a=
这两对齿轮为标准齿轮,其几何尺寸可按标准齿轮计算。
由上面知齿轮7,8的齿数和比9,10的齿数和小,为了使齿轮5,6的实际中心距与齿轮7,8的标准中心距相同,齿轮5,6应采用正变位。
齿轮5,6为正传动,其几何尺寸按变位齿轮计算。
圆柱齿轮传动设计
由图可知,齿轮11、12、13、14实现运动功能单元4的减速功能,它所实现的传动比为15.89。
由于齿轮11、12、13、14是2级齿轮传动,这2级齿轮传动的传动比可如此确定
于是
为使传动比更接近于运动功能单元4的传动比11.9167,取
取模数m=2mm,按标准齿轮计算。
由图34-(b)可知,齿轮32、33实现运动功能单元15的放大功能,它所实现的
传动比为可按最小不根切齿数确定,即
则齿轮36的齿数为17/i=68
齿轮36、37的几何尺寸,取模数m=2mm,按标准齿轮计算。
如图所示,齿轮是为了实现凸轮输出的传动比的扩大,26,27,28总传动比为8,,齿
轮按不根切的最小齿数算,即=17,则齿轮27的齿数为17,又让,=4,则=4*17=68。
齿轮的几何尺寸,取模数m=2mm,按标准齿轮计算。
由图34-(a)可知,齿轮29,30图18中的运动功能单元12减速运动功能,其传动比为6,则
各个齿轮的具体参数如下
序
号
项目
代号
齿轮5,6
齿轮7,8
齿轮9,10
(11,12)
齿轮13,14
1
齿数
齿轮
z
34
29
17
17
齿轮
51
57
69
67
2
模数
2
2
2
2
3
压力角
20
20
20
20
4
齿顶咼系数
1
1
1
1
5
顶隙系数
0.25
0.25
0.25
0.25
6
标准中心距
85
86
86
84
7
实际中心距
86
86
86
84
8
啮合角
21.76
20
20
20
9
变位系数
齿轮
0.4
0
0
0
齿轮
0.12
0
0
0
10
齿顶咼
齿轮
2.76
2
2
2
齿轮
2.2
2
2
2
11
齿根高
齿轮
1.7
2.5
2.5
2.5
齿轮
2.25
2.5
2.5
2.5
12
分度圆直径
齿轮
68
58
34
34
齿轮
102
114
138
134
13
齿顶圆直径
齿轮
73.51
62
38
38
齿轮
106.4
118
142
138
14
齿根圆直径
齿轮
64.6
53
29
29
齿轮
97.49
109
133
129
15
齿顶圆压力角
齿轮
29.63
28.47
32.78
32.78
齿轮
25.73
24.79
24.046
24.15
16
重合度
1.59
1.71
1.66
1.66
序
号
项目
代号
齿轮32,33(26,27)
齿轮29,30
1
齿数
齿轮5
17
17
齿轮6
68
51
2
模数
2
2
3
压力角
20
20
4
齿顶咼系数
1
1
5
顶隙系数
0.25
0.25
6
标准中心距
85
68
7
实际中心距
85
68
8
啮合角
20
20
9
变位系数
齿轮
0
0
齿轮
0
0
10
齿顶咼
齿轮
2
2
齿轮
2
2
11
齿根高
齿轮
2.5
2.5
齿轮
2.5
2.5
12
分度圆直径
齿轮
34
34
齿轮
136
102
13
齿顶圆直径
齿轮
38
38
齿轮
140
106
14
齿根圆直径
齿轮
29
29
齿轮
131
97
15
齿顶圆压力角
齿轮
32.78
32.78
齿轮
24.10
25.27
16
重合度
1.67
1.64
圆锥齿轮传动设计
由图34-(a)可知,圆锥齿轮16、17实现图18中的运动功能单元7的减速运动功能,它所实现的传动比为3,两圆锥的齿轮的轴交角为
工=90
圆锥齿轮17的分度圆锥角为
圆锥齿轮16的分度圆锥角为
圆锥齿轮的最小不根切当量齿数为
圆锥齿轮16的齿数可按最小不根切齿数确定,即
则圆锥齿轮17的齿数为,
齿轮16、17的几何尺寸,取模数m=2mm,按标准直齿锥齿轮传动计算,其计算结果如下表
所示。
序号
项目
代号
计算公式及计算结果
1
齿数
齿轮16
16
齿轮17
48
2
模数
3
3
压力角
20°
4
齿顶咼系数
1
5
顶隙系数
0.25
6
分度圆锥角
齿轮15
71.57°
齿轮16
18.43°
7
分度圆直径
齿轮15
48.000mm
齿轮16
144.000mm
8
锥距
75.895mm
9
齿顶咼
齿轮15
3.000mm
齿轮16
3.000mm
10
齿根高
齿轮15
3.7500mm
齿轮16
3.750mm
11
齿顶圆直径
齿轮15
249.90mm
齿轮16
2149.69mm
12
齿根圆直径
齿轮15
45.63mm
齿轮16
136.885mm
13
当量齿数
齿轮15
50.610
齿轮16
151.785
14
当里齿轮
齿顶圆压力角
齿轮15
=39.19
齿轮16
27.526
15
重合度
/2n=3.195
6)
传送带设计
d160mmd2150mm
7)运动方案执行构件的运动时序分析
1.曲柄19的初始位置
如图33所示,曲柄19顺时针转动时的初始位置由角确定。
由于该曲柄导杆机构的
19与水平轴的夹角。
极位夹角B=30。
,因此,当导杆21处于左侧极限位置时,曲柄
图33系统运动示意图
2.凸轮的初始位置
意图,右图为凸轮的轮廓图。
图34凸轮转动方向示意图
3.曲柄27的初始位置
如图35所示,曲柄27逆时针转动时的初始位置由角确定。
滑块30的起始极限位
置在左侧,因此,曲柄27与水平轴的夹角。
4.拨盘34的起始位置
如图35所示,拨盘33逆时针转动时的初始位置由角确定,拨盘33逆时针转
动时的初始位置处于槽轮由动变停的分界位置,因此,拨盘33与水平轴的夹角
(5)设计课题运动方案分析
推料的曲柄滑块机构的位移,速度以及加速度随角度的变化如图所示:
F面三个图依次是滑块的位移,速度,加速度随时间的变化曲线:
本题中,有三种送料方式,由原动机转速为1430rpm,产品输送量分三档可调,每分钟
向输送线2分别输送9、18、24件小包装产品。
则输出的转速为则输出的角速度为0.942rad/s,
同理另外两种的角速度分别为1.885rad/s,2.513rad/s,经过的减速以及中间一系列的传动后
曲柄19的角速度依次为:
0.628rad/s,1.26rad/s,1.67rad/s,则图形曲线与上图大致相同,这里仅仅贴出当角速度为0.628rad/s时的图:
F面分析凸轮的位移速度,加速度的变化曲线:
位移:
00P讳轄口胃节'-11^61-:
;7--AS厂斤“斤"Y;-
融
速度:
加速度:
位移曲线
2000
1500
1000
誓5OQ
0'
-500
00.523A.0472.6702.09412.61S3.1413.&66S1888.712423ffi75Ml283SX轴
-1000
a0523004735703094^61®.1418665818S&712«236675962832
)(轴
以曲柄19的角速度为2.541rad/s时为例,画出滑枕20的加速度,速度以及位移随曲柄运动的角度的变化曲线如下图所示
以曲柄19的角速度为2.541rad/s时为例,画出滑枕20的加速度,速度以及位移随时间的变化曲线如下图所示: