放空洞混凝土施工.docx
《放空洞混凝土施工.docx》由会员分享,可在线阅读,更多相关《放空洞混凝土施工.docx(7页珍藏版)》请在冰豆网上搜索。
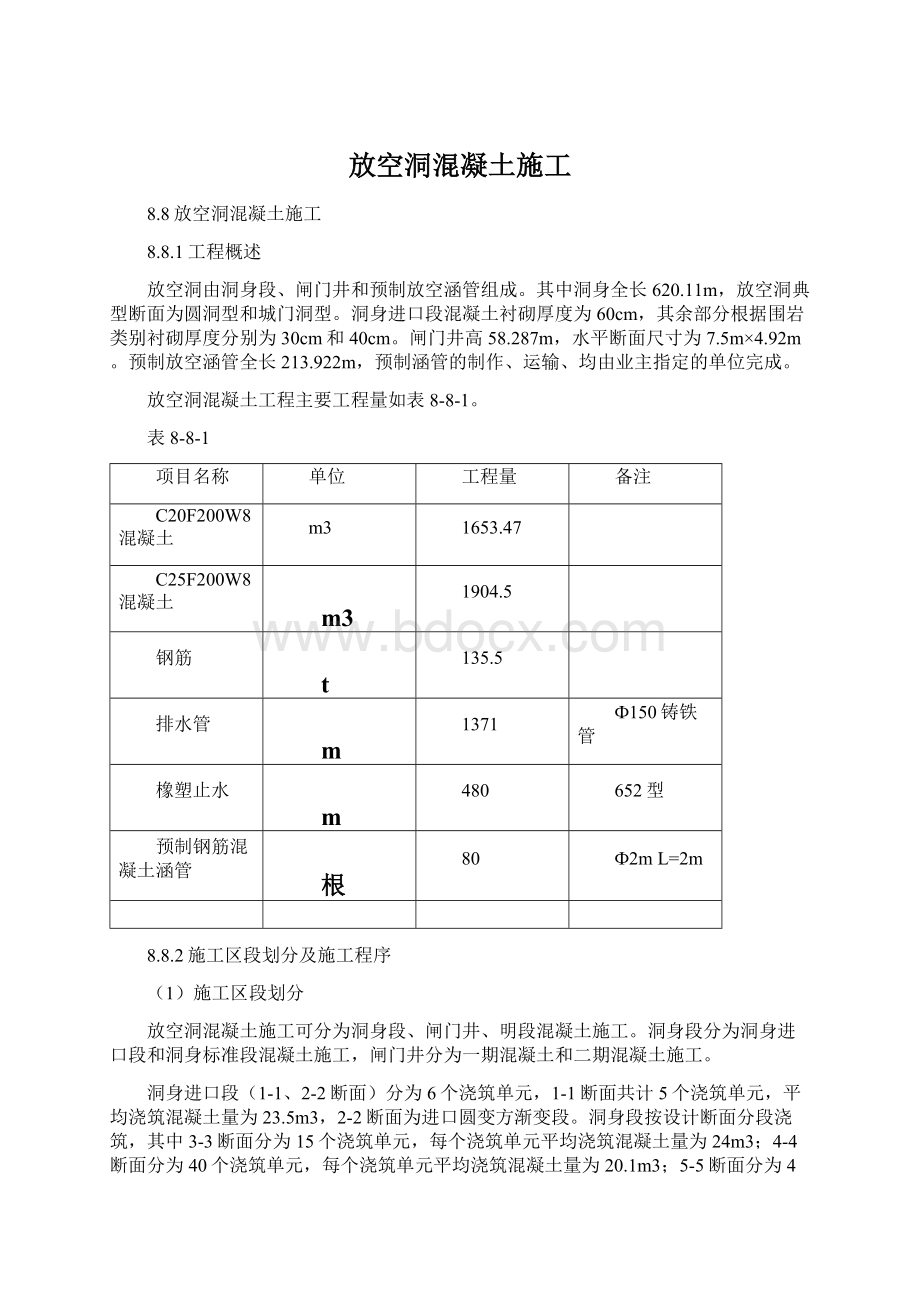
放空洞混凝土施工
8.8放空洞混凝土施工
8.8.1工程概述
放空洞由洞身段、闸门井和预制放空涵管组成。
其中洞身全长620.11m,放空洞典型断面为圆洞型和城门洞型。
洞身进口段混凝土衬砌厚度为60cm,其余部分根据围岩类别衬砌厚度分别为30cm和40cm。
闸门井高58.287m,水平断面尺寸为7.5m×4.92m。
预制放空涵管全长213.922m,预制涵管的制作、运输、均由业主指定的单位完成。
放空洞混凝土工程主要工程量如表8-8-1。
表8-8-1
项目名称
单位
工程量
备注
C20F200W8混凝土
m3
1653.47
C25F200W8混凝土
m3
1904.5
钢筋
t
135.5
排水管
m
1371
Ф150铸铁管
橡塑止水
m
480
652型
预制钢筋混凝土涵管
根
80
Ф2mL=2m
8.8.2施工区段划分及施工程序
(1)施工区段划分
放空洞混凝土施工可分为洞身段、闸门井、明段混凝土施工。
洞身段分为洞身进口段和洞身标准段混凝土施工,闸门井分为一期混凝土和二期混凝土施工。
洞身进口段(1-1、2-2断面)分为6个浇筑单元,1-1断面共计5个浇筑单元,平均浇筑混凝土量为23.5m3,2-2断面为进口圆变方渐变段。
洞身段按设计断面分段浇筑,其中3-3断面分为15个浇筑单元,每个浇筑单元平均浇筑混凝土量为24m3;4-4断面分为40个浇筑单元,每个浇筑单元平均浇筑混凝土量为20.1m3;5-5断面分为4个浇筑单元,每个浇筑单元平均浇筑混凝土量为48.5m3。
洞身混凝土浇筑分段、混凝土浇筑示意见图XLC/C—CC—03—8—8—1。
闸门井按3m/层进行分层浇筑,平均每层浇筑混凝土量为73.8m3,共有30个浇筑单元。
明段混凝土浇筑量为403m3。
(2)施工程序
放空洞在开挖完成后进行洞身段和闸门井混凝土施工。
放空洞洞身段采用先底板(Ⅰ区)后侧墙顶拱(Ⅱ区)的施工程序,底板施工穿插在侧墙顶拱施工中,不占用直线工期。
闸门井在底板浇筑完成后,按3m/层的分层高度向上浇筑。
闸门井每层混凝土施工程序为:
基岩验收(可同时验收20m)—→测量放线—→安装钢筋—→安装模板—→模板复测调整就位并加固—→仓号验收—→混凝土浇筑—→拆除模板并修整—→进行下一道工序。
8.8.3施工布置和主要施工机械
放空洞混凝土施工所用风、水、电均采用开挖时的供给系统,施工道路使用开挖时施工道路(由2号公路修施工支路至放空洞出口工作面)。
洞身进口段和闸门井底板混凝土浇筑所用混凝土泵布置在放空洞进口,由于洞身标准段施工时闸门井也进行混凝土施工,故洞身标准段混凝土施工从出口向进口进行施工。
为便于闸门井混凝土施工,在EL480高程设一活动值班房。
放空洞闸门井混凝土水平运输采用6m3混凝土搅拌车运至EL840高程,由MY-BOX管入仓,混凝土振捣采用Ф50软轴振捣棒和Ф100变频振捣器振捣。
由于放空洞洞身每段混凝土浇筑量较少,洞径小的特点,洞内混凝土水平运输采用0.5m3自卸翻斗车运输,泵送入仓,选用HB60混凝土泵能满足排水洞混凝土施工。
放空洞侧墙混凝土采用Ф50软轴振捣棒振捣,底板混凝土振捣采用Ф50软轴振捣棒和平板振捣器振捣,顶拱混凝土采用附着式振捣器振捣,并在模板窗口处辅以Ф50软轴振捣棒振捣。
8.8.4放空洞混凝土施工
(1)钢筋工程
钢筋安装前施工人员应按钢筋料单逐一对照,确认无误后方可安装,钢筋的焊接和钢筋绑扎应按GB50204—2002中的有关规定和施工图的要求进行。
放空洞洞身钢筋安装程序为:
打插筋孔—→安装插筋—→测量放线—→安装外层架力筋—→外层钢筋安装—→安装内层架力筋—→内层钢筋安装—→检查合格进行下一道工序。
闸门井钢筋安装过程中,要特别注意埋件和二期混凝土插筋的位置,不能漏埋和错埋。
所有钢筋安装完后,施工单位自检,发现问题及时处理,经监理工程师验收合格后方可进行下一工序作业。
(2)模板工程
a.洞身段
洞身进口段混凝土采用先底拱后侧墙顶拱的施工程序,进口段底拱直接做样架人工抹面施工,侧墙、顶拱采用定型组合钢模板,Ф48钢管承重体系支模,局部补缝采用现立木模,面板为3cm厚松木或杉木板,外刷模板漆。
进口斜直面混凝土采用定型组合钢模板,R为60cm的园弧斜面采用定性异型钢模板施工。
进口圆形变方形渐变段模板应进行专门设计,初步设定按四块进行拼装,模板加工时,严格控制加工精度,加工成型后,进行拼装,测量检查合格后送至工地安装。
模板见图XLC/C—CC—03—8—8—2、3。
洞身段混凝土采用先底板后侧墙顶拱的施工程序,底板采用刮轨法施工,侧墙顶拱模板采用定型组合钢模板,Ф48钢管架为承重体系的模板方案,其堵头模板为木模板采用插板法支设,外设插筋顶撑、内设拉杆加固。
洞身渐变段模板采用定型组合钢模板,钢管架为承重体系的模板方案,局部补缝采用现立木模,面板为3cm厚松木或杉木板。
模板详见图XLC/C—CC—03—8—8—4。
b.闸门井
闸门井混凝土模板采用定型组合钢摸板现场安装,2[100(槽钢)做围檩,Ф14拉杆加固。
施工脚手架随浇筑高度而升高。
混凝土浇筑完成后,施工脚手架成为灌浆施工脚手架。
混凝土模板见图XLC/C—CC—03—8—8—5。
混凝土分层见图XLC/C—CC—03—8—8—6。
c.明段
明段现浇混凝土模板采用定型组合钢模板Ф48钢管架为承重体系的模板方案。
预制放空洞出口挑流鼻坎侧墙模板采用定型组合钢模板,钢围檩拉杆、钢管架加固,顶面由测量放出样轨,人工抹面。
d.模板质量保证措施
每个仓号在立模前,必须有足够的、满足精度要求的测量控制点和仓内高程点,对于结构、形体比较复杂的部位要适当加密控制点;负责安装模板的班组长,必须熟悉设计图纸和有关规范,并严格按设计图纸和规范要求施工;每次安装模板前,将模板表面粘结的杂物清理干净并刷涂脱模剂,为保证混凝土外表面的光度,对所有永久面模板的表面贴膜或拆模后进行打磨处理;承重模板的承重体系必须牢固可靠,施工过程中作好“盯、查、看、防”工作;加强模板现场管理,随时修补、保养模板。
(3)止水
止水材料的材质、规格及安装按“技术规范”和“设计要求”执行。
止水铜片在车间加工,分类堆放。
铜止水直线接头在现场采用搭接双面焊接,搭接长度不小于20mm,橡塑止水在现场焊接,采用搭接热焊方式,先将搭接的一面削平,然后用加热器加热,最后加压搭接,搭接长度10cm。
止水安装要用止水固定卡固定,以防在混凝土浇筑中止水移位。
混凝土浇筑过程中,要派专人盯看止水,不能冲着止水直接下料,以免损坏止水。
对于水平止水,要先将止水下部浇筑完毕并振捣密实后才可进行止水上部浇筑,防止止水下部脱空。
安装止水部位必须振捣密实。
(4)混凝土浇筑
施工段内各项工作完成后,认真冲洗仓号,清除各种杂物,割除伸入保护层中的钢筋头,清除仓内松动、尖角岩石,并保证浇筑设备的数量和质量,待监理工程师检验合格后方可开始浇筑。
混凝土浇筑完成后要及时进行洒水养护。
a.闸门井混凝土浇筑
闸门井混凝土由混凝土搅拌车运至EL840高程,然后由MY-BOX管入仓。
仓内混凝土采用平铺法施工,每层铺料厚度不大于50cm,混凝土入仓后,及时振捣,振捣采用Ф50软轴振捣棒和Ф100振捣器振捣,不能出现不振、漏振、欠振、过振情况,以保证混凝土浇筑质量。
闸门井混凝土在浇筑过程中,应使仓内混凝土均匀上升,并保护好仓内的预埋件。
仓内混凝土不得堆积,应随浇随平仓,仓内若有粗骨料堆积时,应均匀地分布于砂浆较多处,不得用水泥浆覆盖,以免造成内部蜂窝。
b.放空洞洞身混凝土浇筑
底板混凝土采用刮轨法施工,由测量放线控制,用Φ22钢筋作样轨,轨距1~1.2m,混凝土浇筑振捣后,由人工按刮轨控制体形,原浆压光抹面后拆除样轨并修复混凝土表面,即可保证设计体形。
放空洞侧墙混凝土(4-4断面)采用平铺法施工,每层平均铺料厚度为30cm,Ф50软轴振捣棒振捣,浇筑侧墙混凝土时,要保证左、右侧墙均匀下料。
顶拱混凝土入仓后采用附着式振捣器振捣,并在模板窗口处辅以Ф50软轴振捣棒振捣。
混凝土浇筑过程中,注意承重支架有无异常情况,发现情况及时处理。
c.明段混凝土浇筑
预制涵管安装完成后即进行此段混凝土浇筑。
此段混凝土浇筑方法与洞内基本一致。
(5)混凝土施工中应注意的问题
1)仓面施工质量控制
a.浇筑方案控制
为了确保混凝土的质量,每个浇筑单元在开仓浇筑前,向监理工程师提交一份施工方案。
内容包括:
浇筑部位、起止坐标、起止高程、分层分块顺序及其工程量、混凝土类别、施工线路、入仓方式、施工手段(包括混凝土供料强度,各种必备机械的型号、数量)等,并附简要的施工平面图、剖面图和说明。
b.浇筑前仓面检查
混凝土的仓面(主要指仓面清理、模板安装、钢筋、止水等)按设计要求进行检查。
表面要用高压水冲毛。
此外,对于老混凝土面或岩石的边缘斜坡尖角必须凿除或打毛。
c.砂浆摊铺
铺设砂浆的作用是使岩石与混凝土或混凝土层间紧密结合,提高防渗性能与抗剪强度。
首先控制砂浆的配合比,其水灰比为混凝土的水灰比减少0.03~0.05。
仓面检测工作度在10cm左右,均匀摊铺厚度控制在2~3cm,一般摊铺与混凝土浇筑速度相匹配。
d.混凝土入仓及摊铺
混凝土入仓前应检查混凝土的和易性是否符合要求,混凝土入仓后要及时平仓、及时振捣。
2)现场质量问题处理
a.混凝土出现发白、干硬、初凝现象,应停仓处理。
b.混凝土被严重污染,如外来水、泥浆、油污等带入仓内所污染的混凝土,均需挖除重新浇筑。
c.混凝土浇筑过程中严禁向成品混凝土中加水。
3)混凝土表观质量控制
标书要求,放空洞进口段混凝土表面凹凸度不能超过3mm,并应磨成不大于1:
30的斜坡;一般过水面混凝土凹凸度不能超过6mm,并应磨成不大于1:
20的斜坡;闸门底槛混凝土表面要求光滑,与施工图纸所示理论线的偏差不大于3mm。
为满足设计和规范要求,特采取以下措施来确保混凝土浇筑的表观质量。
a.模板安装前制订模板安装方案,在施工中认真落实模板安装方案,测量盯检模板。
b.底板混凝土抹面严格按样架控制混凝土体型,在混凝土浇筑过程中先用木杆抹平,混凝土浇筑完成后、混凝土初凝前再用铁抹利用混凝土原浆摸平压实、压光,并拆除样架。
c.模板拆除后应仔细检查混凝土浇筑质量,发现混凝土缺陷应及时通知监理工程师并提出修补方案,进行修补。
对于混凝土模板缝,应及时用磨光机进行打磨。
4)安全问题及解决方案
放空洞混凝土施工均在开挖完成后进行施工,洞内围岩在外暴露时间较长,容易发生掉块现象。
在洞身每段混凝土施工前应派专人检查此段围岩情况,发现危石及时处理,避免危石掉落伤人。
放空洞闸门井高度高,施工人员在施工中应系好安全带、带好安全帽。
专职安全员应随时在施工工作面巡查,发现不安全因素及时处理。
(6)施工进度计划
开挖交面后,即依次展开钢筋混凝土施工的各分项工作。
a.闸门井
闸门井EL786.313以下共浇筑混凝土160m3,共需31天;EL786.313—EL831.313共浇筑混凝土1032m3,共需80天;ELEL831.313—EL840.00共浇筑混凝土208m3,共需20天;二期混凝土共浇筑混凝土152m3,共需31天。
闸门井混凝土施工共需162天。
b.放空洞
洞身段共有浇筑单元55个,进口段共浇筑混凝土322.5m3,共需30天;洞身标准段共浇筑混凝土1623.4m3,共需250天;
洞身混凝土施工共需280天。
c.明段
明段混凝土浇筑安排在洞身浇筑完成后,总浇筑方量为403m3,预计工期为45天。
具体工期安排详见表8-8-2。
(7)资源配制
混凝土工程所需劳动力见表8-8-3,混凝土施工材料见表8-8-4,施工设备用量见表8-8-5。