门护板设计指南.docx
《门护板设计指南.docx》由会员分享,可在线阅读,更多相关《门护板设计指南.docx(18页珍藏版)》请在冰豆网上搜索。
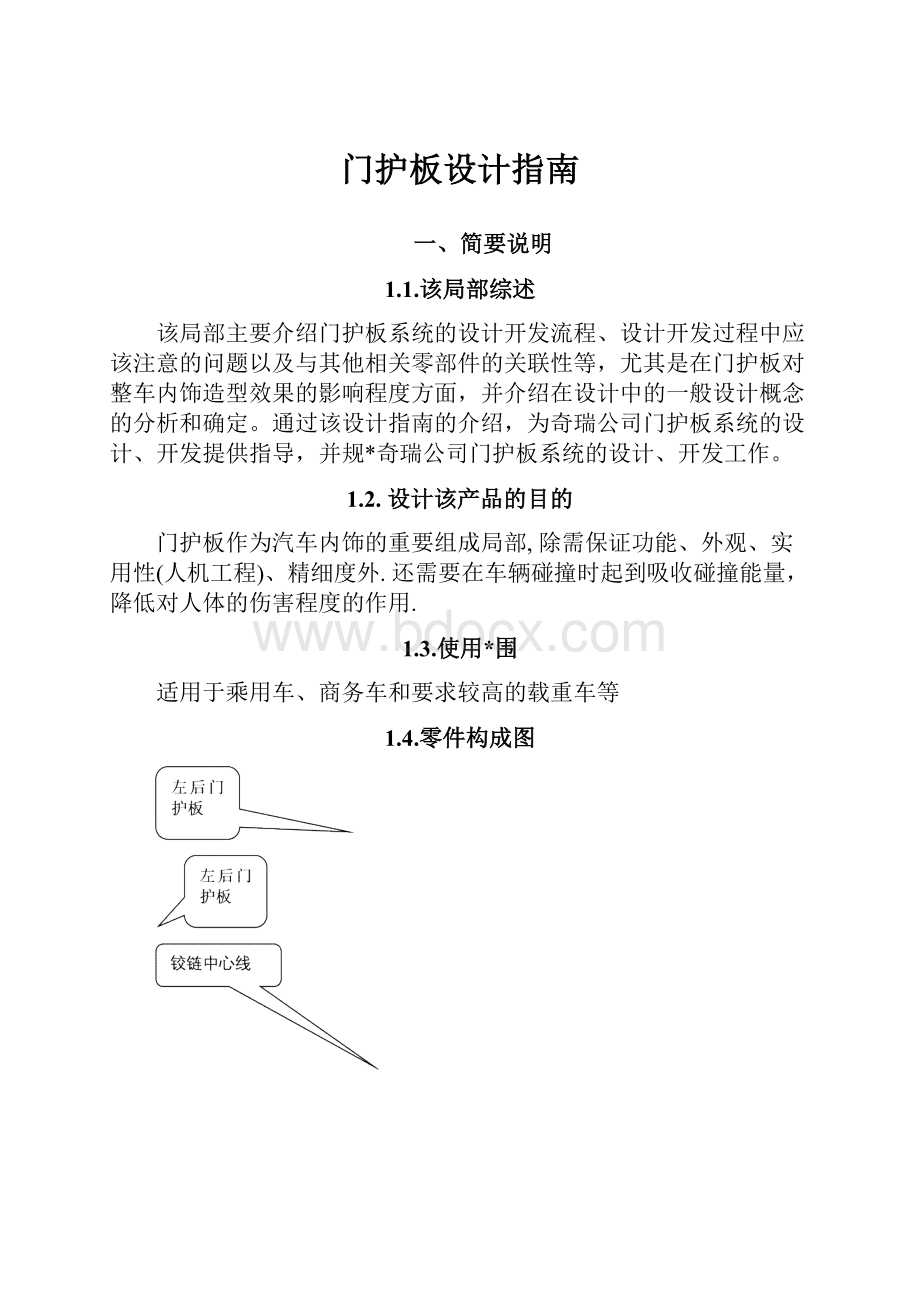
门护板设计指南
一、简要说明
1.1.该局部综述
该局部主要介绍门护板系统的设计开发流程、设计开发过程中应该注意的问题以及与其他相关零部件的关联性等,尤其是在门护板对整车内饰造型效果的影响程度方面,并介绍在设计中的一般设计概念的分析和确定。
通过该设计指南的介绍,为奇瑞公司门护板系统的设计、开发提供指导,并规*奇瑞公司门护板系统的设计、开发工作。
1.2.设计该产品的目的
门护板作为汽车内饰的重要组成局部,除需保证功能、外观、实用性(人机工程)、精细度外.还需要在车辆碰撞时起到吸收碰撞能量,降低对人体的伤害程度的作用.
1.3.使用*围
适用于乘用车、商务车和要求较高的载重车等
1.4.零件构成图
序号
零件名称
一般料厚
一般材料
1
前门护板
2.5—3m
PP+EPDM+T15
2
后门护板
2.5—3m
PP+EPDM+T15
3
后背门护板
2.5mm
PP6
二、设计设想〔思想、理念〕
2.1概述
门护板在设计时一般主要考虑外观上的整体效果,一般来说,ACLASS冻结后就不允许改动,所以在CAS阶段就需要定义门护板与周边零件、各分块之间的间隙,同时作初步的人机工程及法规进展校核.校核后须对INSIDEHANDLE,ARMREST,GRIPHANDLE,WINDOWCRANKASSY,MAPPOCKET重新进展布置(如果需要),如果可能,在此阶段还需要考虑右舵车,尽量做到左、右件对称,减少右舵件开发投入;CLASS制作完成后,进入MATERIAL阶段,此阶段须定义各分块材料;完成后进入SECTION阶段,在此阶段须对工艺、脱模方向、配合方式进展初步的定义,同时最重要的是门护板的运动校核,确定CALSSA面在运动时是否与周边件有干预现象;SECTION阶段;完成后进入FRAME阶段,此阶段须考虑装配可行性、定位、碰撞吸能块及强度,对构造进展细化。
假设单从门护板考虑,一般来说,与门护板配合的钣金面应尽量平整,门内钣金应尽量为一体式〔不要前后分块〕,且钣金上所有门护板固定孔应在同一道工序中冲出。
受边界、空间、工艺及其他因素的影响,门护板在设计过程中必然会不断修改.
2.2开展方向
、轻量化
、NVH
、侧碰平安
、多功能
2.3开发周期
门护板正向开发周期表
工作内容
时间(工作日)
累计
设计
300
300
模具开发
90-180
390-480
整改
240
630-710
实验
90
720-810
认可
10
730-820
2.4数据制作
CAS阶段.
此阶段需要确定整车对门护板的配置要求,建立零件清单,并初步确认零件材料、厚度、各分件的工艺(注塑,吸塑,搪塑,吹塑)、检查CAS是否满足相关法规(GB8410、FMVSS201),如果需要,还需考虑右舵,尽量减少右舵需要开发的零件和开发费用.
.1法规要求
.1.1内部凸出物要求
所有零部件的设计,都需要满足国家相关法规的要求,这是设计的根底。
Title
Territory
Number
Remark
InteriorFittings
内部凸出物
ECE
EEC
Australia
GB
USA
ECER21/01
EEC74/60-78/632
ADR21/01
GB1152-1999
FMVSS201
R>3.2
Height≤25,
regulatorhandle≤35
OccupantProtection
乘员保护
Weshouldhave50×50areawithinthepelvicarea
SideImpactProtection
侧碰保护
USA
GB
ECE
FMVSS214
GB-20071-2006
95
Doortrimshould`tkeep
Sharpwhencarbeside
HIC
≤1.000
CHEST
G
≤60G
DEFLECTION
≤42mm
PELVICSYMPHYSISLOAD
≤6KN
ABDOMINALLOAD
≤2.5KN
VISCOUSCRITERION
≤1.0m/s
SHAPE
NOSHARPEDGE
.1.2燃烧特性要求
Title
Territory
Number
Remark
Flammability
USA
EEC
FMVSS302
95/28
≤102mm/min
GB
8.410
≤100mm/min
奇瑞公司目前要求小于等于75MM/MIN
.2人机工程的校核及功能件的布置
.2.1INSIDEHANDLE布置
INSIDEHANDLE的布置要方便操作,同时又要防止误操作,一般来说,INSIDEHANDLE的布置*围见下列图:
为保证内开手柄的操作空间,手柄和护框上缘应保证30mm间隙,手柄和底座应保证20mm间隙,假设为2手指操作,保证以上间隙的手柄长度应大于40mm,3手指操作的手柄长度应大于50mm。
.3ARMREST布置
ARMREST布置要求高度及前后位置适宜,使驾驶员或乘客手臂得到放松.常见布置*围见下列图:
另外:
为使驾驶员或乘客手臂舒适,ARMREST的总宽度须大于60mm?
,平面区域大于40mm。
ARMREST倾斜角度≤6°,〔注:
受整车造型影响,ARMREST布置通常无法到达理想状态,此时须评审决定〕
.4WINDOWCRANKASSY布置
WINDOWCRANKASSY应尽量布置在人方便操作的*围内〔参见INSIDEHANDLE的布置区域〕,同时,为方便操作,手指区域间隙应大于40,背手区域间隙应大于50,座和门板的间隙应大于55。
.5MAPPOCKET布置
此局部布置受造型影响较大,通常由造型决定,但如果条件允许,MAPPOCKET应尽量保证280mm*70mm*100mm的空间。
.6GRIPHANDLE布置
掌握式
手握处周长应不大于100mm,内侧距门护板本体间隙应大于35mm
盒式
宽度应大于25mm,深度应大于30mm,长度大于80mm。
.7REGULATORHANDLE布置
REGULATORHANDLE应尽量布置在人方便操作的*围内〔参见INSIDEHANDLE的布置区域〕手摇柄在玻璃关闭状态的位置,应该避开人体腿部,以防止侧碰时对人体造成伤害。
且手摇柄的外部倒角尺寸应该满足法规要求〔R>3.2mm〕。
手摇柄旋转轴线应该尽量接近Y方向。
前门的布置应该考虑与仪表板、地图带、内开手柄及门护板扶手的间隙,保证在手摇柄旋转的过程中不与其发生干预。
后门的布置应该考虑与前排座椅、后排座椅、内开手柄及门护板扶手的间隙,保证在手摇柄旋转的过程中不与其发生干预
位置比拟紧凑的允许与前座椅有微量干预,不影响功能。
但不能与座椅坐垫干预。
MATERIAL阶段.
此阶段须明确各分件所用的材料,现我司大局部门护板本体材料为PP+EPDM-T15,后背门护板材料采用PP6,其中EPDM使门护板具有一定的弹性,填加15%的滑石粉可以对门护板起到增强作用,防止零件变形.因PP材料的附着力较差,故一般喷漆件及电镀件不用此材料,现我司门护板上常用喷漆件及电镀件材料为PC+ABS(电镀级).此材料有较好的强度和耐高温性能,可以防止零件在喷漆或电镀时变形.当分块为吸附或搪塑时,考虑到本钱及工艺,其骨架我司大局部采用ABS材料.假设零件为长而细的注塑零件时,应选用抗变形较好的材料.
SECTION阶段.
.1脱模方向的定义
在此阶段首先应根据CAS初步确定各注塑件的脱模方向.一般来说,本体因前后下侧均有翻边,故脱模方向常为Y向.在做SECTION的时候必须考虑零件的工艺性及门板与钣金的配合方式、各分件之间的配合方式.
.2截面线位置的定义
与门护板配合的相关件:
内挡水条,门内钣金,门槛压板,立柱护板,门洞条、锁、升降器、导轨、三角块、内开拉手、开关面板、扬声器
一般制作截面线的位置都是能表达件与件的配合特征。
.3主截面线
主截面线一般是能总体表达门护板内部构造
DETAILA:
上板体与中饰板配合关心
DETAILB:
本体与开关面板的配合关系
开关面板与门护板的配合方式:
1.开关面板与门护板平面同齐,此种配合如上图,一般门护板此位置为包复面料时,可用该种配合,如B11,A11
2.B14、S21、S12、A21类型,此种配合如果门护板没有包复面料,最好不要把拉手布置到开关面板上,间隙不好控制。
3.S22、S18类型
DETAILC:
杂物盒与下本体的配合关系
.4内开拉手的配合
内开拉手分类
与边界的配合关系
.5与内挡水条的配合
S12:
翻边贴合式
此设计中挡水条门门护板配合翻边在设计时应有0.5mm的干预量,门护板与挡水条配合的R角应大于挡水条的R角。
S22:
插入式
此设计多应用与门护板上板体为吸附或搪塑工艺的情况下。
〔注:
假设上板体为注塑,分模线将可见,影响外观质量,故不可采用此配合方式〕
B12:
覆盖式,此设计内挡水安装的钣金止口应与内挡水有1mm间隙。
以防止门护板和内挡水干预
.6与仪表板的配合
.7与立柱的配合
.8与三角块的配合
一般来说,为改善门护板与钣金配合,卡扣坐与钣金固定孔间隙设计值应校实际值大,设计值=实际值+〔0.5~1〕。
.9与保险手柄座的配合
工程参考面制作
工程面的制作
.1工程面的根本要求
工程参考面制作的目的,是为了A面调整更能符合工程要求。
如果有CAS数据,根本就不需要制作工程参考面了。
护板的工程参考面,最重要的是要做好与边界配合的参考面。
如下列图所示:
图示工程参考面,是根据截面线、B-R线制作的,该面定义了护板的边界、与密封条的配合等,A面在调整是,不允许超过该参考面。
.1工程面的运动校核
门护板的A面与门框密封条在运动过程中干预,在实际装车的过程中会出现将门框密封条刮伤或刮掉,运用校核如下列图所示:
一般来说,门护板与门框密封条干预一般出现在15度以内,一般是局部干预,所以在做运动校核的时候初始角度应该多切几个断面,保证运动过程无干预现象。
2.4.4FRAME阶段.
此阶段需要着重考虑定位、固定、装配可行性、碰撞能量吸收、强度.及常见质量问题的排除.
1、定位、固定:
为保证门护板装配位置的准确行,通常需在门护板后上侧设一定位孔,前上侧设一辅助定位的长孔。
其他固定孔则应有1mm的调整量。
另外,为保证门护板与钣金的配合,沿门护板周边应200-250mm有一个固定点,固定点应在门护板与钣金配合翻边内侧25~75mm处。
后端距门护板顶部100mm内应设一固定点。
对卡扣的拨出力要求在89~111.25N之间〔20~25磅〕,使用人工手指按压方式装配的卡扣插入力在22.25N〔5磅〕,使用拍入方式装配的卡扣插入力在44.5N〔10磅〕之间;且卡扣必需保证至少插拨三次不损坏。
下列图是借用我司现生产的局部车型卡扣时,一些设计参数。
〔非定位卡扣〕
A(mm)
B(mm)
C(mm)
Dma*(mm)
E(mm)
F(mm)
A11
6.5-7
4.2
2
8.5
5.5
7
B11
S11
3.3
2.5
9.5
5.5
7
T11
碰撞能量吸收:
为提高侧碰的平安性,通常在门护板与钣金之间增加缓冲块。
需增加缓冲块的区域及缓冲块尺寸见下列图:
法规要求〔FMVSS201〕:
FMVSS201中规定:
在下列图所示区域内,Y向最突出点必须被一51mm*51mm的正方形平面区域〔上下或前后切线夹角小于20°〕所包括。
2.5失效问题库:
车型
失效问题
原因分析
解决措施
1.
四门护板与门内板钣金配合间隙大
2
门护板下方固定孔偏
3
车门内护板布织物缺陷
4
仪表板与门护板子配合处,装饰条过度不平顺,配合不好
5
与玻璃升降开关配合不良,松动或难装配
6
四门护板与呢槽配合间隙大
7
门内护板处钣金孔外露
三各种加工工艺及优缺点的比照
3.1加工工艺
各种加工工艺都要尽量减少与视觉方向垂直的配合间隙,减小配合间隙〔如下列图所示〕;并尽量将分模线至于不可见处;如必需将分模线外露,分型线处公差不得大于0.5mm。
高压注塑工艺
材料经过螺杆加热后注入闭合的模具,冷却定型后开模取出。
主要产品质量问题及影响因素:
序号
质量问题
影响因素
1
缩印〔缩痕〕
加强筋位置、模具浇口设计等
2
变形
产品构造、材料、周转或摆放方法等
3
熔接痕
产品构造、浇口位置、材料流动性等
低压注塑工艺
材料经螺杆加热后注入微闭合的模具,模具经过二次闭合加压,冷却定型后开模取出。
低压注塑工艺主要用于生产外表有装饰面料〔织物/表皮〕的产品---产品变型较小。
优点:
1、成型效率高:
2、面料与骨架不用胶粘剂;
缺点:
1、本钱高:
设备模具工装本钱高〔相对于高压注塑模〕:
2、面料本钱高,相对于二次复合工艺的材料〔即包复工艺〕。
吸塑
.1阳模吸塑成型工艺
阳模真空吸塑表皮:
将外表已有花纹的片材进展加热,当表皮到达拉伸成型温度要求时,上升阳模,使加热表皮与阳模开成直空腔,开启阳模真空抽吸系统,使表皮贴于阳模外表,冷却后脱模,制得定型的表皮,成型表皮即可转入下道发泡成型工序。
优点:
1、模具投资小,寿命长;2、生产效率高;3、设备投资只有搪塑设备的1/3或1/4。
缺点:
1、由于外表花纹是预制的,花纹损失随着表皮的拉伸度增大而增大。
当拉伸较大时,细皮纹就会使皮纹消失,粗皮纹会淡化形成明显的视觉差,影响美观。
2、由于阳模真空成型的工艺特征,决定了阳模吸塑加工对产品阴阳角尺寸的局限性,一般R角都要设计在R1.5以上,给产品外观设计带来了局限。
面料:
要点:
需在注塑工艺上考虑面料压缩及拐角处的实际复合效果,减少须根据面料或表皮的拉伸率。
.2阴模吸塑成型工艺
阴模吸塑成型技术是阳模真空吸塑与搪塑技术的有机的结合,它是一种模热成型技术。
热的不带皮纹的片材〔0.8mm表皮TPO+2.0mm泡沫〕被放置在发泡层与阴模的型腔之间,通过真空吸附使片材与模具型腔〔模具型腔已制作皮纹〕接触成型,由于冷却时片材收缩离开与发泡层吸覆贴合成型,此种工艺和伟统的成型和复合工艺相比拟的话,不会出现皮纹拉伸变形现象,而且可以在一个零件上实现不同的皮纹形式,皮纹均匀清晰手感好,与搪塑效果相当。
聚氨酯〔PU喷涂〕
聚氨酯〔PU〕喷涂工艺是近几年迅速开展起来的一种新工艺,相对搪塑工艺而言有许多优点。
见3.2成型工艺性和本钱的比拟综合比拟。
制作PU喷涂的表皮主要工艺:
在模具上喷脱膜剂→喷漆〔颜色〕→喷PU原料形成表皮〔由机械手控制在不同地方的厚薄〕→冷却→取出表皮。
发泡与切割工艺
除了表皮制造工艺与搪塑不同以外,阴模成型和PU喷涂在制作门护板后续工艺上〔如发泡等〕与搪塑都是一样的。
发泡工艺是将聚醚和异氰酸酯充分混合后,注入模具中的表皮与骨架中间,交联固化,在其间形成具有要求形状泡沫的加工工艺。
该泡沫既连接了表皮与骨架,又大大改善零件的手感。
该工艺是软质门护板生产的必须工艺。
搪塑
要点:
搪塑可制作出比拟复杂的状态,可防止面料复合及拉伸率对造型的影响。
3.2各种表皮成型工艺和本钱综合比拟
价格比拟
阳模吸塑、阴模吸塑、搪塑综合比拟
各成型工艺比拟
搪塑与PU喷涂工艺和本钱比拟
搪塑与PU喷涂工艺和本钱比拟
搪塑
PU喷涂
再生利用
较难
可以
成品加工生产周期
300秒
120-250秒
设计自由度
大
更大一点
外表最小外半径
R1
R1
外表厚度
1-1.2
1-1.2
原材料浪费〔边角料等〕
浪费稍大
浪费相对小
表皮手感〔硬度〕调整
余地小,偏硬
可调整
颜色的选择
比拟自由〔主要是黑色或深蓝色〕
更自由〔可实现浅色和一件多色〕
生产效率与灵活性
有限
灵活性好
耐照射能力
好
好
耐低温能力
一般
好
市场占有率
主流
逐步兴起
设备本钱
110-115%
100%
模具本钱
120-130%
100%
模具寿命
2-4万套
40-50万套
能源消耗
相当高〔280°C)
很低〔65°C)