第九章基本光刻工艺流程显影到最终检验.docx
《第九章基本光刻工艺流程显影到最终检验.docx》由会员分享,可在线阅读,更多相关《第九章基本光刻工艺流程显影到最终检验.docx(42页珍藏版)》请在冰豆网上搜索。
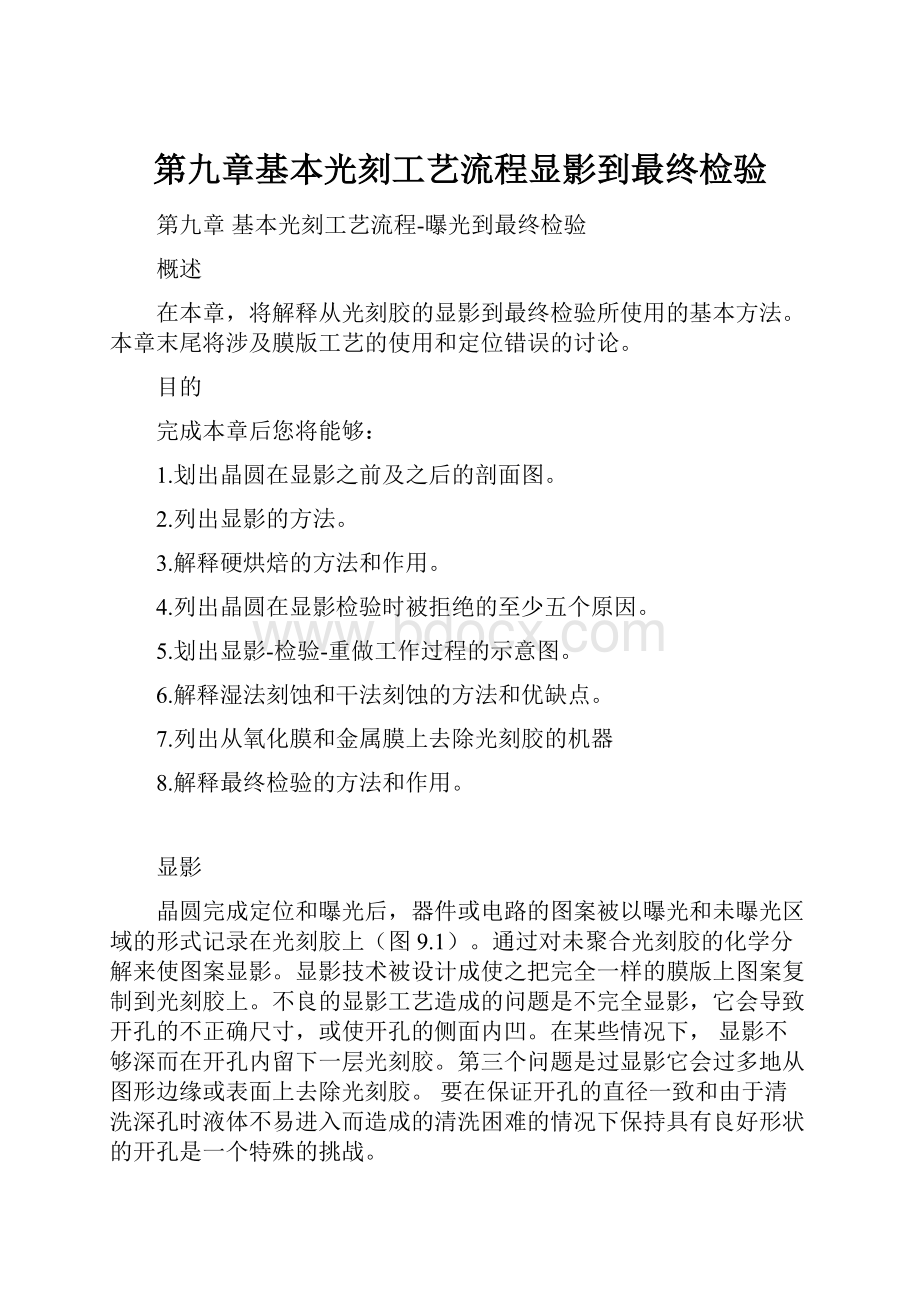
第九章基本光刻工艺流程显影到最终检验
第九章基本光刻工艺流程-曝光到最终检验
概述
在本章,将解释从光刻胶的显影到最终检验所使用的基本方法。
本章末尾将涉及膜版工艺的使用和定位错误的讨论。
目的
完成本章后您将能够:
1.划出晶圆在显影之前及之后的剖面图。
2.列出显影的方法。
3.解释硬烘焙的方法和作用。
4.列出晶圆在显影检验时被拒绝的至少五个原因。
5.划出显影-检验-重做工作过程的示意图。
6.解释湿法刻蚀和干法刻蚀的方法和优缺点。
7.列出从氧化膜和金属膜上去除光刻胶的机器
8.解释最终检验的方法和作用。
显影
晶圆完成定位和曝光后,器件或电路的图案被以曝光和未曝光区域的形式记录在光刻胶上(图9.1)。
通过对未聚合光刻胶的化学分解来使图案显影。
显影技术被设计成使之把完全一样的膜版上图案复制到光刻胶上。
不良的显影工艺造成的问题是不完全显影,它会导致开孔的不正确尺寸,或使开孔的侧面内凹。
在某些情况下,显影不够深而在开孔内留下一层光刻胶。
第三个问题是过显影它会过多地从图形边缘或表面上去除光刻胶。
要在保证开孔的直径一致和由于清洗深孔时液体不易进入而造成的清洗困难的情况下保持具有良好形状的开孔是一个特殊的挑战。
负和正的光刻胶有不同的显影性质并要求不同的化学品和工艺。
负光刻胶显影
在光刻胶上成功地使图案显影要依靠光刻胶的曝光机理。
负光刻胶暴露在光时会有一个聚合的过程它会导致光刻胶聚合在显影液中分解。
在两个区域间有足够高的分解率以使聚合的区域只失去很小部分光刻胶。
对于大多数的负光刻胶显影二甲苯是受欢迎的化学品。
它也在作负光刻胶中作溶液使用。
显影完成前还要进行冲洗。
对于负光刻胶,通常使用n-丁基醋酸盐作为冲洗化学品,因为它既不会使光刻胶膨胀也不会使之收缩,从而不会导致图案尺寸的改变。
用光刻机刻图案的晶圆,可能使用一种性质较温和的STODDART溶剂。
俯视
表层光刻胶
曝光后显影后
正确曝光曝光不足
不完全曝光严重过曝光
(a)(b)
图9.1光刻胶显影(a)过程(b)问题
正光刻胶负光刻胶
显影剂NaOHXylene
TMAHStoddard溶剂
冲洗水n-醋酸丁酯
图9.2光刻胶显影剂和冲洗用化学品
冲洗的作用是双重的。
第一,它快速地稀释显影液。
虽然聚合的光刻胶不会被显影液分解,但在曝光的边缘总会有一个过度区其中包含部分聚合的分子。
如果显影液留在表面上便会溶解这部分区域而改变图案尺寸。
第二,冲洗可去除在开孔区少量部分聚合的光刻胶。
开发全部为水成分的负光刻胶显影系统一直是半导体工业的一个目标。
从工厂中消除有机溶剂减少安全系统和减少处理或排放化学品的费用。
到目前,只取得了很小的可接受的成功。
正光刻胶显影
正光刻胶有不同的显影条件。
两个区域,聚合的和未聚合的区域,有不同的溶解率约1:
4。
这意味着在显影中总会从聚合的区域失去一些光刻胶。
使用过度的显影液或显影时间过长可以导致光刻胶太薄而不能使用。
结果有可能导致在刻蚀中翘起或断裂。
有两种类型的化学显影液用于正光刻胶,碱-水溶液和非离子溶液。
碱-水溶液可以是氢氧化钠或氢氧化钾。
因为这两种溶液都含有离子污染物,所以在制造敏感的电路时不被使用。
大多数用正光刻胶的制造厂使用叠氮化四甲基铵氢氧化物的溶液(TMAH)。
有时要添加表面活性剂来去除表面张力使溶液更易亲合晶圆表面。
正光刻胶水的性质使它们在环保上比有机溶液的负光刻胶更具吸引力。
掩膜版
反光刻胶层
晶圆
聚合的光刻胶
部分聚合的光刻胶
未聚合的光刻胶
图9.3在光刻胶图案边缘的过度区
正光刻胶的显影工艺比负光刻胶更为敏感。
1影响结果的因素是软烘焙时间和温度、曝光度、显影液浓度、时间、温度、及显影方法。
显影工艺参数由所有变量的测试决定。
图9.4显示了对于一个特定的工艺参数对线宽的影响。
湿法显影
有几个方法用于光刻胶显影(图9.5)。
方法的选择依据光刻胶极性、特征图形尺寸、缺陷密度的考虑、要刻蚀层的厚度及产能。
20-S曝光
16-S曝光
12-S曝光
8-S曝光
光刻胶厚度
持续曝光时间:
50S
(基于68华氏度的8秒曝光)
显影剂浓度:
50%
曝光后烘焙:
无
线宽变化
显影剂温度(华氏)
图9.4显影剂温度和曝光关系与线宽变化的比较
**沉浸
**喷射
**PUDDLE
图9.5显影方法
沉浸。
沉浸是最古老的显影方法。
在耐化学腐蚀的传输器中的晶圆被放进盛有显影液的池中呆上一定的时间然后再被放入加有化学冲洗液的池中进行冲洗(图9.6)。
这种方法的问题如下:
1.液体的表面张力阻止了化学液体进入微小开孔区。
2.部分溶解的光刻胶块儿会粘在晶圆表面。
3.很多晶圆处理过后化学液池会被污染
4.当晶圆被提出化学液面时会被污染
5.显影液(特别是正显影液)随着使用会被稀释
6.为了消除1,2,3的问题需要经常更换化学液从而增加了成本。
7.室温的拨动改变溶液的显影率
8.晶圆必须迅速地送到下一步进行干燥这就增加了一个工艺步骤。
经常在化学液池上增加附属方法来提高显影工艺。
用通过使用机械搅动的办法来辅助增加均匀性和对微小开孔区的渗透。
一种流行的系统是使用置于池内的TEFLON密封的磁体与池外可产生旋转磁场的装置构成。
显影剂冲洗烘干
图9.6沉浸显影步骤
搅动也可用向液体施加超声波或磁声波的方法实现。
超声波可产生气穴现象。
波中的能量使液体分离成微小的空洞随即空洞会破裂。
成千上万个微小空洞的快速产生和破裂会产生均匀显影并有助于液体渗透进微小的开孔区。
在磁声波范围的声波能量会减小粘在晶圆表面的STAGNENT界线层。
2另外也通过对液体池进行加热和温度控制来增强显影率。
喷射显影。
受欢迎的化学显影方法是用喷射。
事实上,通常有很多原因使喷射工艺对于任何湿法工艺(清洁、显影、刻蚀)来讲比沉浸工艺更受欢迎。
例如,用喷射系统可很大地降低化学品的使用。
工艺的提高包括由于因喷射压力的机械动作而限定光刻胶边缘和去除部分光刻胶块儿而带来较好的图案清晰度。
因为每个晶圆都是用新的化学显影液所以喷射系统总是较沉浸系统清洁。
喷射工艺可在单一或批量系统完成。
在单一晶圆配置中(图9.7),晶圆被真空吸在吸盘上并旋转同时显影液和冲洗液依次地喷射到晶圆表面。
冲洗之后晶圆吸盘高速旋转使晶圆被甩干。
在外观和设计上,单晶圆喷射系统和点胶机一样只是通入不同的化学品。
单晶圆喷射系统具有可集成显影和硬烘焙工艺而实现自动化的优点。
这个工艺的一个主要优点是均匀性的提高。
冲洗
显影剂
真空
图9.7喷射显影和冲洗
许多年来喷射显影一直是对负光刻胶的一个标准工艺因为负光刻胶对显影液的温度不算敏感。
对于温度敏感的正光刻胶来说,喷射系统不是很有效。
问题在于液体在压力下从喷嘴喷出后便很快冷却。
称为隔热冷却(adiabaticcooling),用于正光刻胶的喷射显影系统通常由加热的晶圆吸盘或加热的喷嘴来控制温度。
用于正光刻胶的喷射显影所遇到的其它问题是当使用碱显影液和水基的显影液喷出时产生的泡沫而造成机器的老化。
批量显影系统有两种形式,单批和多批。
这些机器是甩-冲洗-干燥这在第7章有所描述。
显影系统要求额外的管道来供应显影化学品。
多批显影系统一般上较直喷射,单晶圆系统的均匀性低因为它不是喷射到晶圆表面上并且在正光刻胶的工艺上温度控制更复杂。
混凝显影。
喷射显影因其均匀性和产能而非常有吸引力。
混凝显影是用以获得正光刻胶喷射显影工艺优点的一种工艺的变化。
该系统使用一个标准的单晶圆喷射装置。
正常的喷射显影和混凝显影的区别是用于晶圆的显影化学品的不同。
工艺开始时在静止的晶圆表面上覆盖一层显影液。
(图9.8)。
表面张力使显影液在晶圆表面上不会流散到晶圆外。
显影液会在晶圆表面上停留一定的时间,通常是在以吸盘加热的晶圆上,这时绝大部分的显影会发生。
混凝显影是单晶圆只有晶圆表面沉浸的工艺。
要求的时间过后,更多的显影液被喷到晶圆表面上并冲洗,干燥,然后送去下一个工序。
等离子体去除浮渣。
不完全显影造成的一个特殊的困难是叫做浮渣(scumming)的情形。
浮渣可以是留在晶圆表面上的未溶解的光刻胶块儿或是干燥后的显影液3。
膜很薄并很难直观检验。
为解决这问题,在微米和微米以下的ULSI生产线中,在化学显影后用氧等离子体来去除(descum)这种薄膜。
干法(或等离子)显影
液体工艺的消除一直是一个长期目标。
它们难于集成到自动生产线并且化学品的采购、储存、控制和处理费用高。
取代液体化学显影液的途径是使用等离子体刻蚀工艺。
干法等离子体刻蚀对于刻蚀晶圆表面层已经是完善的工艺。
(参见“干法刻蚀”)。
在离子体刻蚀中,离子,由离子体场而得到能量,以化学形式分解暴露的晶圆表面层。
干法光刻胶显影要求光刻胶化学物的曝光或未曝光的部分二者之一易于被氧等离子体去除。
换句话说,图案的部分从晶圆表面上氧化掉。
一种干法显影叫做DESIRE的工艺将在第10章中描述,它使用甲基硅烷和氧等离子体。
硬烘焙
硬烘焙是在掩膜工艺中的第二个热处理操作。
它的作用是实质上和软烘焙是一样的:
通过溶液的蒸发来固化光刻胶。
而硬烘焙的目的是使光刻胶和晶圆表面有良好的粘贴。
这个步骤有时称为刻蚀前烘焙。
硬烘焙的方法
硬烘焙在设备和方法上与软烘焙相似。
对流炉、在线及手动热盘,红外线隧道炉,移动带传导炉,真空炉都用于硬烘焙中。
对于自动生产线,轨道系统受到青睐。
参见第8章软烘焙一段。
硬烘焙工艺
硬烘焙的时间和温度的决定与在软烘焙工艺是一样的。
起始点是由光刻胶制造商推荐的工艺。
之后,工艺在被精确调整来达到粘贴和尺寸控制的要求。
一般使用对流炉的硬烘焙的温度是从130到200度进行30分钟。
对于用其它的方法时间和温度都有所不同。
设定最低温度使光刻胶图案边缘和晶圆表面达到良好粘贴。
热烘焙增强粘贴的机理是脱水和聚合。
加热使水份脱离光刻胶,同时使之进一步聚合,从而增强了其耐刻蚀性。
硬烘焙温度的上限以光刻胶流动点而定。
光刻胶有象塑料的性质当加热时会变软并可流动(图9.9)。
当光刻胶流动时,图案尺寸便会改变。
当在显微镜下观察光刻胶流动是明显的增厚的光刻胶边缘。
极度的流动会在沿图案边缘处显示出边缘线。
边缘线是自光刻胶流动后在光刻胶中留下的斜坡来的光学影响。
正常温度高温
图9.9光刻胶在高温下流动
硬烘焙工艺流程
显影显影/烘焙显影/烘焙
检验检验检验
硬烘焙刻蚀重新烘焙
刻蚀刻蚀
图9.10硬烘焙工艺流程的几个选择
硬烘焙是立即在显影后或是马上在开始刻蚀前来进行的,如图9.10所示。
在大多数生产情况中,硬烘焙是由和显影机并排在一起的隧道炉来完成的。
当使用此种操作规程时,把晶圆存放在氮气中或是立即完成检验步骤以防止水份重新被吸收到光刻胶中,这一点非常重要。
显影检验
在显影和烘焙之后就是要完成光刻掩膜工艺的第一个质检。
适当地来说应叫显影检验(developinspect)或DI。
检验的目的是区分那些有很低可能性通过最终掩膜检验的晶圆;提供工艺性能和工艺控制数据;及分拣出需要重做的晶圆。
这时的检验良品率,也就是通过这第一个质检的晶圆数量,不会计入最终良品率的计算。
但是有两个主要原因使之成为很受关注的良品率。
光刻掩膜工艺对于电路性能的的关键性会在本文点强调。
在显影检验工艺,工程师有第一个判断工艺的性能机会。
显影检验步骤的第二个重要性与在检验时作的拒收有关。
首先,一部分晶圆会从上一步留下来问题而要停止工艺处理。
这些晶圆在显影检验时会被拒绝接受并进行处理。
其它在光刻胶上有光刻图案问题的晶圆可被通过去掉光刻胶的办法而进行重新工艺处理。
几乎没有工厂不发生这种一般性的重新工艺处理。
晶圆被返回掩膜工艺称为重新工艺处理(rework或redo)。
工艺工程师的目标是保持尽可能低的重新工艺处理率,应小于10%而5%是一个受欢迎的水平。
一个原因是去过重新工艺处理的晶圆在最终工艺完成时有较低的分选良品率。
重新工艺处理会造成粘贴问题并且再次的传输操作会导致晶圆污染和损坏。
如果太多的晶圆进行重新工艺处理则整个分选良品率会受到严重的影响。
保持低重新工艺处理率的第二个原因与在进行重新工艺处理晶圆时要求另外的计算和区分有关。
去水合物
点胶
烘焙光刻胶去除
定位和曝光
显影检验拒收的晶圆
合格晶圆
图9.11重做过程
显影检验良品率和重新工艺处理率随掩膜水平而变。
总体上,在掩膜次序中的第一级有较宽的特征图形尺寸、较平的表面和较低的密度,所有这些会使掩膜良品率更高。
在晶圆到了关键的接触和连线步骤时,重新工艺处理率会有上升趋势。
显影检验的方法
在这一段将解释检验方法,工艺流程和检验的参数。
检验设备的描述会将在第14章进行。
总体上有四类晶圆上的问题适用于显影检验和最终检验。
在图案尺寸(关键尺寸测量)上会有偏差。
有定位不准的图案,有表面问题如光刻胶的污染、空洞或划伤及污点和其它的表面不规则。
人工检验
图9.12的流程图显示了一个典型的人工显影检验次序。
第一步是用眼睛直观检验晶圆表面。
由于没有使用放大镜,所以这种检验有时又叫做1倍检验(1倍放大等于眼的视觉水平)。
检验可在正常的室内光线下进行,但是更多时候晶圆要在直射的白光或高密度紫外线下进行。
检验时晶圆与光线成一定的角度。
用这种方法可以非常有效地检查出膜厚的不规则,粗显影问题、划伤及污染,特别是污点。
通过1倍检验的晶圆将在显微镜下检查。
大多数工业上的作法是用基于概率原理的随机取样(randomsampling)的方法。
这个原理决定必须要精确探测出缺陷水平的区域大小。
这样的检验系统是基于操作员随机选取检查区域的。
步骤
检查内容
方法
1
污点/大的污染
裸眼/UV光
2
污点/大的污染
图案不规则性
定位不准
100-400倍显微镜
SEM/AFM/自动检验设备
3
微观尺寸
显微镜/SEM/AFM
图9.12显影检验次序
人工检验中不采用随机取样。
随着缺陷密度的下降并对于VLSI集成电路如果要得到满意的缺陷采样检查的区域就需要扩大。
然而,随着芯片密度的增大每个芯片上的器件也在减小这就倍数更大的显微镜来检查。
放大倍数的增加会使视景减小,这又会造成操作员用更多的时间来检查晶圆。
统计地去采样一个大直径低缺陷的晶圆的方法因其所要求的时间长而被禁止。
通常的规程是选择一些具体的区域来检查。
假设被选定的芯片在地理上代表晶圆表面。
这个方法也假设一般的问题会出现在表面上。
这个方法对于一般晶圆上的问题是适当的并提醒工艺工程师在掩膜工艺中的问题。
通常显微镜会装有可驱动的/编程的平台以自动进行对晶圆表面的区域检查。
除了芯片采样的问题,还有晶圆采样的问题。
晶圆检查的数量随着具体掩膜级别的难度与敏感性变化。
越敏感和有难度的光刻胶层,可能越要检查更多的晶圆。
每批晶圆中要检查的数量可从几个到全部。
在每个掩膜级别,有一些尺寸对于整个电路是非常关键的一个区域或一组图案。
对每个级别有一个代表性的图案被选出来作为关键尺寸(CriticalDemension,CD)。
在显影检验过程中,要使用人工或自动显微镜的方法来测量这些图案的尺寸。
自动检验。
随着芯片尺寸增大和元件尺寸的减小,工艺变得更加繁多并精细,人工检验的效力也到了极限。
可探测表面和图案失真的自动检验系统成为了在线和非在线检验的选择。
这些系统将在第14章中描述。
自动检验系统提供了更多数据,这又令工艺工程师能够特性化和控制工艺。
它们的一致性好,而人会在能力上发生变化并因做重复性的工作而产生疲劳。
显影检验拒收的原因
有很多原因可使晶圆在显影检验时被拒收。
一般地,要找的仅是那些在光刻掩膜步骤中增加的缺陷。
每一片晶圆都会带有一些缺陷和问题并且晶圆到达当前步骤时有可接受的质量,在这一原理下,从上一步留下的缺陷一般地被忽略掉。
如果一片晶圆有严重的问题而在上一步未被发现它就会被从批料中拿掉。
这种检验一般是一个“首先-不足原理(first-failbasis)”就是说操作员或机器检验晶圆直到达到一个拒收的水平。
“首先-不足”系统节省时间但不会给工艺工程师一个晶圆图案质量的估计。
每片晶圆的信息被记录在清单上以做累计和分析用。
自动和半自动光学检验仪有电子记忆用来累积和收集拒收数据。
在一些先进的生产线上把检验单编程到PC中,这会提高检验步骤和数据分析的速度。
大多数拒收的原因已讨论过。
但还有一个涉及的问题是搭桥(图9。
14)。
它是指两个图案被一曾薄光刻胶相联的情况。
搭桥是因曝光过度、光刻掩膜版清晰度不良、或光刻胶层太厚造成的。
搭桥是一个特殊的棘手问题。
批号
碎晶圆
划伤
污染
小孔
MIA
搭桥
光刻胶翘起
曝光不足
无光刻胶
光刻胶流动
不正确掩膜版
C。
D
拒收
图9.13典型的显影检验单
刻蚀
在完成显影检验步骤后,掩膜版的图案就被固定在光刻胶膜上并可准备刻蚀。
在刻蚀后图案就会被永久地转移到晶圆的表层。
刻蚀就是通过光刻胶暴露区域来去掉晶圆的最表层的工艺。
刻蚀工艺主要有两大类:
湿法和干法刻蚀(图9.21)。
两种方法的主要目标是将光刻掩膜版上的图案精确地转移到晶圆的表面。
其它刻蚀工艺的目标包括一致性、边缘轮廓控制、选择性、洁净度和所有权成本最低化。
湿法刻蚀
历史上的刻蚀方法一直是使用液体刻蚀剂沉浸的技术。
规程类似于氧化前清洁-冲洗-干燥工艺(第7章)和沉浸影。
晶圆沉浸于装有刻蚀剂的槽中过一定的时间,传送到冲洗设备中去除残余的酸,再送到最终冲洗和甩干。
湿法刻蚀用于特征图形尺寸大于3微米的产品。
低于此水平时,由于控制和精度的需要就得使用干法刻蚀。
刻蚀一致性和工艺控制由附加的加热器和搅动设备来提高,例如,搅拌器或带有超声波和磁声波的槽。
长槽湿法刻蚀被与第7章所描述的喷射系统相似。
对于刻蚀,化学成分和计时非常关键。
对于晶圆被刻蚀剂污染的担忧由增加出口过滤器(point-of-usefilter)来解决。
这些特殊的过滤器安装在自动化学分配系统的最终出口处以使在化学液体进入槽前被过滤干净。
这种方式可阻挡住从化学品、泵和管道系统来的微粒。
光刻胶图案搭桥短路
图9.14搭桥的连线
被选择的刻蚀液要有可均匀地去掉晶圆表层而又不伤及下一层的材料(良好的选择性)的能力。
刻蚀时间的变化性是一个工艺参数,它受料盒和晶圆在槽中到达温度平衡的过程中温度变化的影响,和在晶圆被送入冲洗槽过程中持续刻蚀的影响。
一般地,工艺被设置在最短时间并保持与均匀刻蚀和高生产力。
最大时间受限于光刻胶在晶圆表面的粘贴时间。
图案复制的精度依靠几个工艺参数。
它们包括:
过刻蚀、内切、选择性和侧边的各向异性/各向同性刻蚀。
不完全刻蚀
不完全刻蚀是指表面层还留在图案孔中或表面上的情况(图9.15)。
不完全刻蚀的原因是太短的刻蚀时间,出现可减慢刻蚀时间的表面层,或是一个薄厚不均匀的表层也可导致在厚的部分产生不完全刻蚀。
光刻胶层
晶圆
图9.15不完全刻蚀
如果使用化学湿法刻蚀,过低的温度或弱的刻蚀液会导致不完全刻蚀。
如果是干法刻蚀,不正确的混合气体或不当的系统运行可导致相同的影响。
过刻蚀和底切
与不完全刻蚀相反的是过刻蚀(overetch)。
在任何的刻蚀工艺中,总会有一定程度的有计划的过刻蚀以便允许表层厚度的变化。
有计划的过刻蚀还可用以来突破最外表层的缓慢刻蚀层。
理想的刻蚀应在表层中形成垂直的侧边(图9.16)。
产生这种理想结果的刻蚀技术叫做各向异性刻蚀(anisotropic)。
然而,刻蚀剂会从各个方向去掉材料,这种现象叫做各向同性(isotropic)。
在从最外表面刻蚀到表层底部的过程中刻蚀也会在最外表面进行。
结果会在侧边形成一个斜面。
这种作用因在光刻胶边缘下被底切所以称为底切(undercutting)(图9.17)。
一个持续的刻蚀目标是把底切水平控制在一个可接受的范围内。
电路布置的设计者在计划电路时会把底切考虑在内。
相邻的图案必须要分开一定的距离以防止短路。
在图案设计的时候必须要计算底切量。
各向异性刻蚀可用等离子体刻蚀的方法可以得到,它用于刻蚀高级的电路时受到青睐。
底切的减少可允许制作更密的电路。
各向异性刻蚀各向同性刻蚀
图9.16各向异性刻蚀和各向同性刻蚀
正常
过刻蚀
过刻蚀和光刻胶翘起
图9.17底切的程度
当刻蚀时间过长,刻蚀温度太高,或是刻蚀剂混合物太强便会发生严重的底切(或过刻蚀)。
当光刻胶和晶圆表面粘接力较弱也会发生底切。
这是一个持续令人担心的问题。
干燥脱水、PRIME、软烘焙和硬烘焙的目的就是来防止这种问题。
在刻蚀开孔的边缘光刻胶粘接力的失效会导致严重的底切。
如果粘接力非常弱,光刻胶会翘起而导致极为严重的底切。
选择性
在刻蚀工序的另一个目标是保护被刻蚀层下的表面。
如果晶圆的下层表面被部分刻蚀掉,则器件的物理尺寸和电性能会发生改变。
和保护表面相关的刻蚀工艺的性质是选择性(selectivity)。
它由被刻蚀层的刻蚀速率与被刻蚀层下面表层的刻蚀速率的比来表示。
以不同的刻蚀方法氧化硅/硅的选择性从20到40。
4高选择性意味着下表层很少或没有被刻蚀。
在刻蚀形状比大于3:
15的小接触孔时良好的选择性也会成为一个问题。
选择性还适用于光刻胶去除。
这在干法刻蚀中考虑较多。
在表层被刻蚀去的同时一些光刻胶也会同时被去除。
选择性必须要足够高来保证光刻胶不会在被刻蚀层之前被去除掉。
硅湿法刻蚀
典型的硅刻蚀是用硝酸与氢氟酸的混合水溶液。
这一配比规则在控制刻蚀中成为一个重要的因素。
在一些比率上,刻蚀硅会有放热反应。
放热反应所产生的热可加速刻蚀反应,接下来又产生更多的热,这样进行下去而导致工艺无法控制。
有时醋酸和其它成分被混合进去来控制放热反应。
一些器件要求在晶圆上刻蚀出槽或沟。
刻蚀规则要进行调整以使刻蚀速率依靠晶圆的取向。
<111>取向的晶圆以45度角刻蚀,而<100>取向的晶圆以“平”底刻蚀。
6其它取向的晶圆可得到不同形状的沟槽。
多晶硅刻蚀也用基本相同的规则。
二氧化硅湿法刻蚀
最共同的刻蚀层是热氧化形成的二氧化硅。
基本的刻蚀剂是氢氟酸(HF),它有刻蚀二氧化硅而不伤及硅的优点。
然而,饱和浓度的氢氟酸在室温下的刻蚀速率约为300纳米/秒。
7这个速率对于一个要求控制的工艺来说太快了。
(3000纳米厚的膜仅要10秒)。
在实际中,氢氟酸(49%)与水或氟化胺与水混合。
以氟化胺(NH(INF/4F)来缓冲会加速刻蚀速率的氢离子的产生。
这种刻蚀溶液称为缓冲氧化物刻蚀(bufferedoxideetches)或BOEs。
它们以不同的浓度混合来达到合理的刻蚀时间(图9.18)。
一些BOE公式包括一个湿化代理物(表面活化剂如TRITONX-100或等同物)用以减小刻蚀表面的张力,以使其均匀地进入小开孔区。
铝膜湿法刻蚀
有选择的铝和铝合金刻蚀溶液基于磷酸。
不幸的是铝与磷酸反应的副产物是微小的