QC七大手法在QC活动中的应用.docx
《QC七大手法在QC活动中的应用.docx》由会员分享,可在线阅读,更多相关《QC七大手法在QC活动中的应用.docx(12页珍藏版)》请在冰豆网上搜索。
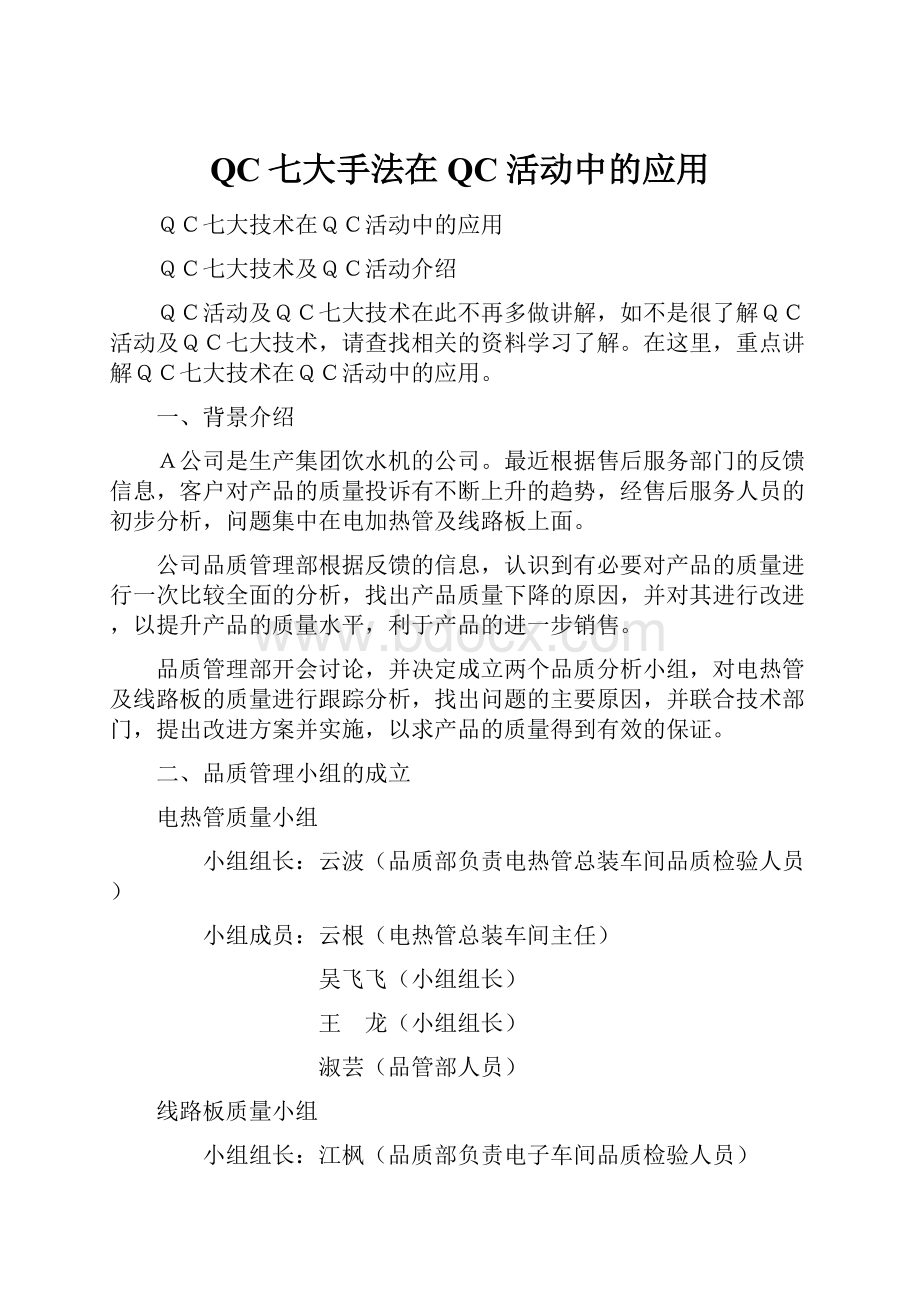
QC七大手法在QC活动中的应用
QC七大技术在QC活动中的应用
QC七大技术及QC活动介绍
QC活动及QC七大技术在此不再多做讲解,如不是很了解QC活动及QC七大技术,请查找相关的资料学习了解。
在这里,重点讲解QC七大技术在QC活动中的应用。
一、背景介绍
A公司是生产集团饮水机的公司。
最近根据售后服务部门的反馈信息,客户对产品的质量投诉有不断上升的趋势,经售后服务人员的初步分析,问题集中在电加热管及线路板上面。
公司品质管理部根据反馈的信息,认识到有必要对产品的质量进行一次比较全面的分析,找出产品质量下降的原因,并对其进行改进,以提升产品的质量水平,利于产品的进一步销售。
品质管理部开会讨论,并决定成立两个品质分析小组,对电热管及线路板的质量进行跟踪分析,找出问题的主要原因,并联合技术部门,提出改进方案并实施,以求产品的质量得到有效的保证。
二、品质管理小组的成立
电热管质量小组
小组组长:
云波(品质部负责电热管总装车间品质检验人员)
小组成员:
云根(电热管总装车间主任)
吴飞飞(小组组长)
王 龙(小组组长)
淑芸(品管部人员)
线路板质量小组
小组组长:
江枫(品质部负责电子车间品质检验人员)
小组成员:
叶双(电子车间主任)
郁(小组组长)
瑞杰(小组组长)
明华(品管部人员)
小组目标:
两个临时QC小组,利用一个月的时间,对两种配件产品进行全过程检验,找出产生产品问题的主要原因,并协同相关部门,制订解决方案并尽快实施,并使质量水平降低到品质体系的目标或更低!
三、小组计划
主计划:
9月1日到9月9日,跟踪产品,全检产品,利用品质七大技术找出问题的主要原因。
9月10日到9月12日,协同技术部门、采购部门,对问题的主要原因进行再次分析,并制定改进方法和实施计划。
9月16日到9月25日,实施改进计划,并全程跟踪产品的生产过程,利用品质七大技术对改进的效果进行分析、确认。
9月26日,总结本次QC活动,并对相关措施进行标准化。
分计划:
(略)
四、电热管QC小组活动过程
小组在组长的组织下,从9月1日起到9月8日,对全部的电热管产品进行了全检,将检测的数据进行分析,得到了下图的初步结果:
(数据收集表)
从上表中,我们初步可以看出每天的不良数及不良率,不良总数为50根,不良率达到了2.8%,比品质体系的质量目标1%高了1.8%
所以,小组人员认为,电热管确实存在问题,以前的抽检样本太小,不能反映出整体的质量状况。
所以,在以后的抽样检验中,应当增加样本的大小,或者进行全检!
对上表进行进一步的分析,可以得到查检表,如下图:
从查检表中,可以发现各不良项目的影响度大小。
但为了更直观的观察各不良项目的影响度大小,绘制出了柏拉图,如下图:
从上图中,就可以非常明显的看出,前四项不良项目占了总不良的大部分,所以,小组人员一致认为,要改进电热管的质量,必须有效的解决这四项的不良项目,必须对这四项进行再分析,找出产生这四项不良的主要原因。
小组人员在9月9日,利用晚上的时间,在生产现场开了一次不良分析的会议,对找出的四项不良项目进行深入的讨论分析,利用鱼刺图的方法,找出产生不良的真正原因。
结论:
造成电热管螺母打滑的主要原因是:
1)电动螺丝刀力矩未调整好(以前未作规定,大部分都调的太大);
2)螺杆螺纹不标准(螺杆与螺母的螺纹不相配);
3)螺母材料不符要求(螺母为不锈钢材料,而电热管螺杆为铜质材料)。
运用相同的方法,对其他三项的不良项目进行了分析,并都找到了相关的原因。
9月10日晚上,在品管部的组织下,将相关的技术部人员、采购部人员、生产部人员集中到一起,对产生各项不良的原因进行了再次分析讨论,基本确定了这些原因是造成电加热管不良的主要原因。
然后,以技术部为主导,根据这些原因,制订出了相关的改进方法。
最后,在品管部的组织下,制订出了改进方法的实施计划。
实施计划如下(略)
9月11日到9月15日,在品管部的协调之下,对实施计划进行了准备。
9月16日开始进行改进计划,持续到9月23日。
并对全部的电加热管进行是全检。
然后对收集的数据进行了计算分析。
数据灌入表:
从上表中,可看出,不良率已经下降到了1.3%,但尚未达到品质体系的1%标准,所以,虽然不良率经过这次的改进,并达到了很大的下降。
但还需进一步的分析。
下一步,由软件自动生成查检表:
再绘制出柏拉图:
从柏拉图中可看出,各不良项的不良率已比较的低了。
但如果要进一步的分析,可从ABC三项入手,进行下一步的改善活动!
再来看看改善前后的推移图。
改善前:
改善后:
可看出,改善后的推移图,不仅不良率得到了有效的降低,而且不良率的有明显的下降趋势,非常直观!
9月26日晚上,品管部、技术部、生产部、采购部等相关人员,集中在会议室,对本次的活动进行了一次总结。
由组长作了活动的过程讲解,并将各图表利用投影的方式,对与会人员用作了详细说明。
然后,由组长主持,对实施的措施做了标准化,并作了分解实施计划,以使不良率维持在现在的良好水平。
五、线路板QC小组的活动过程
线路板的不良根据售后服务人员的反馈信息,主要在于输出电压不稳定,从而影响了其他部件的工作。
所以,小组人员针对线路板的输出电压,作了专题改善活动。
第一步,连续全检100个线路板的输出电压。
获得相关数据。
计算出后两项的值,就可绘制出直方图:
从直方图中,可以明显直观的看出了问题。
一是在合格线之外的区域比较的多,二是分布也不是最好的。
平均值管制图中,100个值里面竟有2个超出下限不符管制,所以,可以得出结论,生产过程并没有得到很有效的控制。
点的分布还是比较正常的。
再来看看R管制图:
R管制图点的分布来看,还算比较的好。
分析其中的不良数:
9
不良率达到了9%
分析这9块不良的原因,只有一块是由于调节输出电压的电位器没有调节好的原因引起的外,其他的8块均是由于变压器输出电压输出不合格造成的。
对此,小组人员讨论决定,将所用的变压器进行全检,然后再对100块线路板进行全检。
改进后的相关数据及图表如下:
直方图如下:
从改善后的直方图可直观的看出,品质已得到很大的改善。
所检产品全部在合格线之,柱形分布也是很理想。
平均值管制图如下:
从上图中可看出,各点分布都是比较好的。
生产过程没有异常情况。
组距管制图如下:
从9月1日到9月10日,线路板QC小组,完成了改善前后的检测活动。
取得了满意的效果。
9月12日晚,品管部组织了技术部、采购部、生产部的相关人员,对此次活动作了详细的汇报说明。
并要求采购部对变压器配套厂家提出相关的要求,必须满足我们提出的质量要求,否则要另外选择厂家。
对生产的作业标准和检验标准作了一些改善,并进行了再标准化。
以将此次活动的效果得到维持。
六、活动总结
两个QC小组活动都结束后,在9月27日晚,品管部开了个部会议,对此次活动作了总结,并由两个小组的组长写出总结报告,报总经理室备案。