起重机伤害事故分析及预防正式.docx
《起重机伤害事故分析及预防正式.docx》由会员分享,可在线阅读,更多相关《起重机伤害事故分析及预防正式.docx(8页珍藏版)》请在冰豆网上搜索。
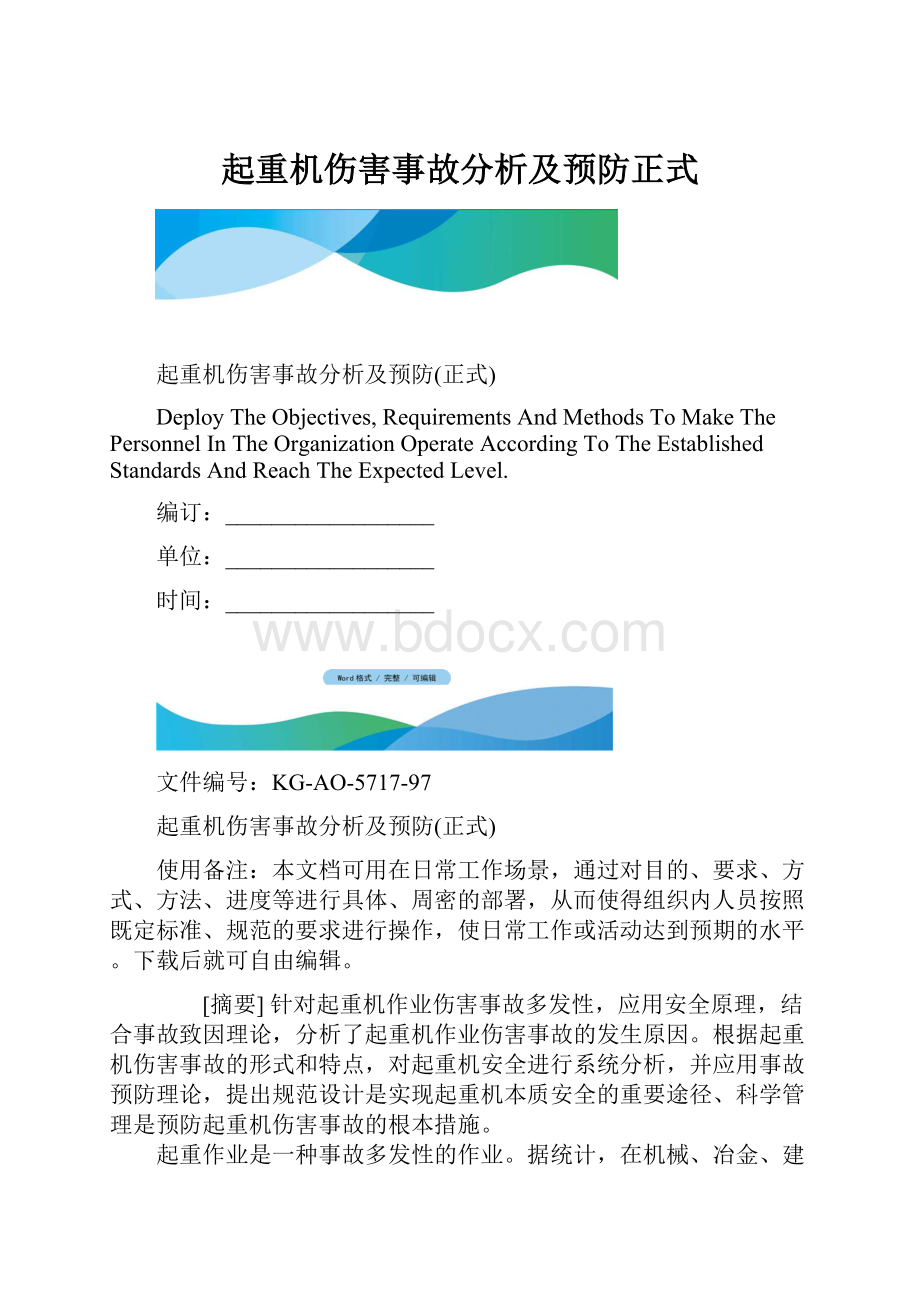
起重机伤害事故分析及预防正式
起重机伤害事故分析及预防(正式)
DeployTheObjectives,RequirementsAndMethodsToMakeThePersonnelInTheOrganizationOperateAccordingToTheEstablishedStandardsAndReachTheExpectedLevel.
编订:
__________________
单位:
__________________
时间:
__________________
文件编号:
KG-AO-5717-97
起重机伤害事故分析及预防(正式)
使用备注:
本文档可用在日常工作场景,通过对目的、要求、方式、方法、进度等进行具体、周密的部署,从而使得组织内人员按照既定标准、规范的要求进行操作,使日常工作或活动达到预期的水平。
下载后就可自由编辑。
[摘要]针对起重机作业伤害事故多发性,应用安全原理,结合事故致因理论,分析了起重机作业伤害事故的发生原因。
根据起重机伤害事故的形式和特点,对起重机安全进行系统分析,并应用事故预防理论,提出规范设计是实现起重机本质安全的重要途径、科学管理是预防起重机伤害事故的根本措施。
起重作业是一种事故多发性的作业。
据统计,在机械、冶金、建筑、海港和铁路等产业中,起重机伤害事故占这些产业事故的30%左右,占总事故的7%~12%,这些事故的发生造成了严重的人员伤亡和经济损失。
随着工业生产的发展,起重机的起重量、工作速度和安全防护措施都不断地提高,事故发生率自20xx年以来已连续8年下降,但是由于多年来对起重机械的设计、制造、安装、使用维修等缺乏严格、科学化的系统安全管理,致使发生在起重机作业中的伤亡事故总数仍然居高不下,重大事故时有发生。
因此,必须运用科学的方法,分析产生故障的原因,采取切实可行的预防措施,排除故障,确保设备的完好率,提高安全使用水平和效率。
起重机作业过程中造成的伤害事故,究其原因不外乎两种,即人为因素和设备因素。
人为因素主要有未履行职能、错误地履行职能、执行未赋予的分外职能、按错误程序执行职能和执行职能时间不对等;设备的因素主要有重物坠落、起重机失稳倾翻、挤压、高处跌落和触电等。
本文从事故致因理论出发,详细地分析起重机伤害事故的发生原因,有针对性地提出相应的预防措施,有利于起重机作业安全的提高。
1 起重机伤害事故的形式
1.1重物坠落
吊具或吊装容器损坏、物件捆绑不牢、挂钩不当、电磁吸盘突然失电、起升机构的零件故障(特别是制动器失灵、钢丝绳断裂)等都会引发重物坠落。
重物坠落或起重机的金属结构件破坏、坠落,都可能造成严重的后果。
常见的重物坠落的原因主要有脱绳、断绳、脱钩、吊钩破断、溜钩和车轮脱轨等。
除此之外,钢丝绳两端的固定也是十分重要的,如辽宁铁岭4.18钢水包倾覆事故的原因之一就是起重机上用于固定钢丝绳的压板螺栓松动。
1.2起重机失稳倾翻
起重机失稳有两种类型:
一是由于操作不当(例如超载、臂架变幅或回转过快等)、支腿未找平或地基沉陷等原因使倾翻力矩增大,导致起重机倾翻;二是由于坡度或风载荷作用,使起重机沿路面或轨道滑动,导致脱轨翻倒。
1.3金属结构的破坏
金属结构是各类桥架起重机、塔式起重机和门座起重机的重要构成部分,作为整台起重机的骨架,不仅承载起重机的自重和吊重,而且构架了起重作业的立体空间。
由于起重机的金属结构组成不同,金属结构破坏形式往往也不同,例如,桥式起重机和门式起重机的主梁下挠度超标或支腿垮塌;塔式起重机和门座起重机的坠臂、倒塔等。
金属结构的破坏常常会导致严重伤害,甚至群死群伤的恶果。
1.4挤压
起重机挤压伤害事故是指人受到挤压而造成的人身伤亡事故,挤压事故经常发生在运行起重机或回转起重机与周围固定物之间。
如桥式起重机的端梁与周围建筑物的立柱、墙之间发生的伤害事故;门式起重机的支腿与场地堆放物或其他临时设施之间发生的挤压伤害事故;塔式起重机、流动式起重机回转时,其尾部与建筑物、堆放物或其它设施之间发生的事故。
运行机构的操作失误或制动器失灵引起溜车,造成碾压伤害等均为挤压伤害事故。
1.5高处跌落
起重机的机体高大,一般车间作业的桥架型起重机的主梁离地高度都在6m以上,室外作业的主梁离地高度都在10m以上,塔式起重机和门座起重机甚至高达几十米。
为了获得作业现场清楚的观察视野,司机室往往设在金属结构的高处,很多设备也安装在高处,塔式起重机转移场地时的拆装作业、起重机高处设备的维护和检修,以及安全检查测量,这些需要人员登高的场所和作业环节,都存在人员从高处跌落伤害的危险。
1.6触电
大多数起重机都是电力驱动,或通过电缆,或采用固定裸线将电力输入,起重机的任何组成部分或吊物,与带电体距离过近或触碰带电物体时,都可以引发触电伤害。
即使是流动式起重机,在输电线附近作业时,触碰高压线的事故也时有发生。
直接触电或由于跨步电压会造成电伤、电击事故。
1.7其他伤害
其他伤害是指人体与运动零部件接触引起的绞、碾、戳等伤害;液压起重机的液压元件破坏造成高压液体的喷射伤害;飞出物件的打击伤害;装卸高温液体金属、易燃易爆、有毒、腐蚀等危险品,由于坠落或包装捆绑不牢破损引起的伤害等。
2起重机伤害事故的特点
起重伤害事故有如下特点:
(1)事故大型化、群体化,一起事故有时涉及多人,并可能伴随大面积设备设施的损坏。
(2)事故后果严重,只要是伤及人员,往往是恶性事故,一般不是重伤就是死亡。
(3)伤害涉及的人员可能是司机、起重工和作业范围内的其他人员,其中起重工被伤害的比例最高。
文化素质低的人群是事故高发人群。
(4)在安装、维修和正常起重作业中都可能发生事故。
其中,起重作业中发生的事故最多。
(5)事故高发行业中,建筑、冶金、机械制造和交通运输等部门较多,这与这些部门起重设备数量多、使用频率高、作业条件复杂有关。
(6)起重事故类别与机种有关,由于任何起重机都具有起升机构,所以重物坠落是各种起重机共同的易发事故。
此外还有桥架式起重机的夹挤事故,汽车起重机的倾翻事故,塔式起重机的倒塔折臂事故,室外轨道起重机在风载作用下的脱轨翻倒事故以及大型起重机的安装事故等。
从安全技术角度看:
起重机械通常结构庞大、机构复杂,操作技术难度大;所吊运的重物种类多,载荷是变化的,吊运过程复杂而危险;大多数起重机械活动空间范围较大,一旦造成事故影响的范围也较大;与吊运人员直接接触的活动的零部件(如吊钩、钢丝绳等)较多,存在潜在的偶发危险因数;需要多人配合作业,存在较大的难度;作业环境复杂,高温、高压、易燃易爆、输电线路、强磁等危险因数对作业人员构成威胁。
由于上述工作特点、特殊功能和特殊的结构形式,使起重机和起重作业方式存在着诸多危险因素,从而国家将起重机定为特种(危险)设备。
因此研究事故的致因理论和预防理论,进而预防起重机伤害事故的发生是很有必要的。
3事故致因及预防理论
3.1海因里希的事故因果连锁理论
该理论的核心思想是:
伤亡事故的发生不是一个孤立的事件,而是一系列原因事件相继发生的结果,即伤害与各原因之间具有连锁关系。
海因里希提出的事故因果连锁过程包括:
(1)遗传及社会环境;
(2)人的缺点;(3)人的不安全行为和物的不安全状态;(4)事故;(5)伤害。
对于上述事故因果连锁关系,可以用5块多米诺骨牌来形象地加以描述。
如果第一块骨牌倒下(即第一个原因出现),则发生连锁反应,后面的骨牌相继被碰倒(相继发生)。
如果因果连锁中的一块骨牌被移去,则连锁反应中断,不会引起后面骨牌的倒下,即事故过程不能连续进行。
海因里希认为,企业安全工作的中心就是移去中间的骨牌(不安全行为、不安全状态),即采取防止人的不安全行为和物的不安全状态的措施,从而中断事故连锁的进程,避免伤害发生。
海因里希的理论曾被称作“工业安全公理”。
3.2轨迹交叉论
该理论的基本思想是:
伤害事故是许多相互联系的事件顺序发展的结果。
这些事件概括起来不外乎是人的原因和物的原因。
当人的不安全行为和物的不安全状态在各自发展过程中延伸,在时间、空间上相接触(交叉)时,就会发生事故。
轨迹交叉论认为人的因素和物的因素在事故致因中占有同样重要的地位。
按照该理论,可以通过避免人与物两种运动轨迹交叉,即避免人的不安全行为和物的不完全状态同时、同地出现,来预防事故的发生。
3.3能量意外释放论
该理论认为事故是一种不正常的或不希望的能量释放,各种形式的能量是构成伤害的直接原因。
从能量意外释放论出发,预防伤害事故就是防止能量或危险物质的意外释放,防止人体与过量的能量或危险物质接触。
于是,我们应该通过控制能量或控制作为能量达及人体媒介的能量载体来预防伤害事故。
在工业生产中经常采用的防止能量意外释放的屏蔽措施主要有:
(1)用安全的能源代替不安全的能源;
(2)限制能量;(3)设置屏蔽设施;(4)在人、物与能源之间设置屏障,在时间或空间上把能量与人隔离;(5)信息形式的屏蔽。
3.4系统致因理论
系统中存在的、可能发生意外释放的能量或危险物质称作第一类危险源;导致约束、限制能量措施失效或破坏的各种不安全因素称作第二类危险源。
一起事故的发生是两类危险源共同起作用的结果,第一类危险源的存在是事故发生的前提,第二类危险源的出现是第一类危险源导致事故的必要条件。
在事故的发生、发展过程中,两类危险源相互依存、相辅相成。
3.5现代因果连锁理论(管理失误论)
人的不安全行为或物的不安全状态是工业事故的直接原因,必须加以追究。
但是,它们只不过是其背后的深层原因的征兆和管理缺陷的反映。
只有找出深层的、背后的原因,改进企业管理,才能有效地防止事故。
博德(FrankBird)在海因里希事故因果连锁理论的基础上,提出了现代事故因果连锁理论。
该理论认为管理者的失误造成了人的不安全行为和物的不安全状态,是事故的根本原因。
尽管遗传因素和人员成长的社会环境对人员的行为有一定的影响,却不是影响人员行为的主要因素。
在企业中,如果管理者能够充分发挥管理机能中的控制机能,则可以有效地控制人的不安全行为和物的不安全状态。
博德模型包括以下几点:
(1)事故因果连锁中一个重要的因素是安全管理。
安全管理人员应该充分认识到,他们的工作要以得到广泛承认的企业管理原则为基础,即安全管理者应该懂得管理的基本理论和原则,控制是管理机能(计划、组织、指导、协调及控制)中的一种机能。
安全管理中的控制是指损失控制,包括对人的不安全行为和物的不安全状态的控制,这是安全管理工作的核心。
(2)为了从根本上预防事故,必须查明事故的基本原因,并针对查明的基本原因采取对策。
基本原因包括个人原因及与工作有关的原因。
个人原因包括:
缺乏知识或技能、动机不正确、身体上或精神上的问题等;工作方面的原因包括:
操作规程不合适,设备、材料不合格,通常的磨损及异常的使用方法以及温度、压力、湿度、粉尘、有毒有害气体、蒸汽,通风、噪音、照明、周围的状况(容易滑倒的地面、障碍物、不可靠的支持物、有危险的物体等)等环境因素。
只有找出这些基本原因,才能有效地预防事故的发生。
(3)不安全行为和不安全状态是事故的直接原因,这一直是最重要的、必须加以追究的原因。
但是,直接原因不过是基本原因的征兆,是一种表面现象。
在实际工作中,如果只抓住作为表面现象的直接原因而不追究其背后隐藏的深层原因,就永远不能从根本上杜绝事故的发生。
另一方面,安全管理人员应该能够预测及发现这些作为管理缺欠的征兆的直接原因,采取恰当的改善措施;同时,为了在经济上及实际可能的情况下采取长期的控制对策,必须努力找出其基本原因。
(4)从实用目的出发,往往把事故定义为最终导致人员身体损伤、死亡、财产损失等不希望的事件。
但是,越来越多的学者从能量的观点把事故看作是人的身体或构筑物、设备与超过其阈值的能量的接触或人体与妨碍正常生活活动的物质的接触。
于是,防止事故就是防止接触。
为了防止接触,可以通过改进装置、材料及设施,防止能量释放,通过训练、提高工人识别危险的能力,佩戴个人保护用品等来实现。
4 起重机伤害事故的预防
根据轨迹交叉理论,只要砍断物的事件链,可完全避免伤亡事故的发生。
因此采用可靠性高、结构完整性强的安全装置、防护系统和信号系统及高度自动化和遥控装置来控制起重机物的因素的发展,控制起重机事故的发生。
根据能量意外释放论,起重机自身就是一种能量,它所吊起的重物也是一种能量,在驾驶室中工作的司机由于处于高位也是一种能量,由于这些能量在一定程度上是客观存在的,因此,必须采取有效的措施来让这些能量按照人们预先为其设定好的路径流动,预防能量的意外释放。
可靠性在安全系统工程中占有很重要的位置,而起重机安全系统的可靠性直接关系到起重机整个系统运行过程中可靠性和安全性。
据经验可知:
设计阶段的技术对起重机固有可靠性的影响程度达到40%以上,所以说,可靠性工作的重点就在起重机的设计阶段。
在构建起重机安全系统方面,尤其要重视设计人员的设计方法和设计工作。
用机器部分地代替人,针对可能发生危险的环节,强调应设置能自动动作的安全装置来替代人的工作,如起重量限制器和限位开关等;用机器代替人操作是防止人失误发生的最可靠措施,机器的故障率比人的失误率要低100倍以上,从而可以大大提高系统的可靠性。
在人—机—环境系统设计中,对人与机合理分工的原则是系统的效率、可靠性和成本。
在经济合理的情况下应尽可能让机器更多地代替人的工作以减轻人的劳动强度,确保安全和健康,建立人—机—环境并行的冗余系统,当人员操作失误时由自动控制系统来纠正,以提高人的可靠性。
5结论
通过对起重机伤害事故形式和特点的分析,结合事故致因理论,得到以下几点启发:
(1)事故是可以预防的。
事故虽不可能根除,但可以通过采取多种措施使其降低到可接受的程度,这就使得事故的预防成为可能。
(2)在起重机伤害事故因果链中,人的不安全因素与物的不安全因素具有同等重要的地位。
在日常使用中,操作人员大多只注重设备的质量、性能及安全防护装置,而很少注意自身存在的缺点,给起重机作业埋下了无形的不安全隐患。
(3)提高安全管理是预防起重机伤害事故的最根本的措施。
管理者的失误造成了人的不安全行为和物的不安全状态,是事故的根本原因。
(4)避免人的不安全行为和物的不安全状态同时、同地出现,是预防起重机伤害事故发生的最基本的措施。
在起重机作业中应避免存在不安全因素的人操作存在安全隐患的起重机,这样至少可以减小事故发生的可能性。
请在这里输入公司或组织的名字
EnterTheNameOfTheCompanyOrOrganizationHere