能源介质管道施工方案讲解.docx
《能源介质管道施工方案讲解.docx》由会员分享,可在线阅读,更多相关《能源介质管道施工方案讲解.docx(40页珍藏版)》请在冰豆网上搜索。
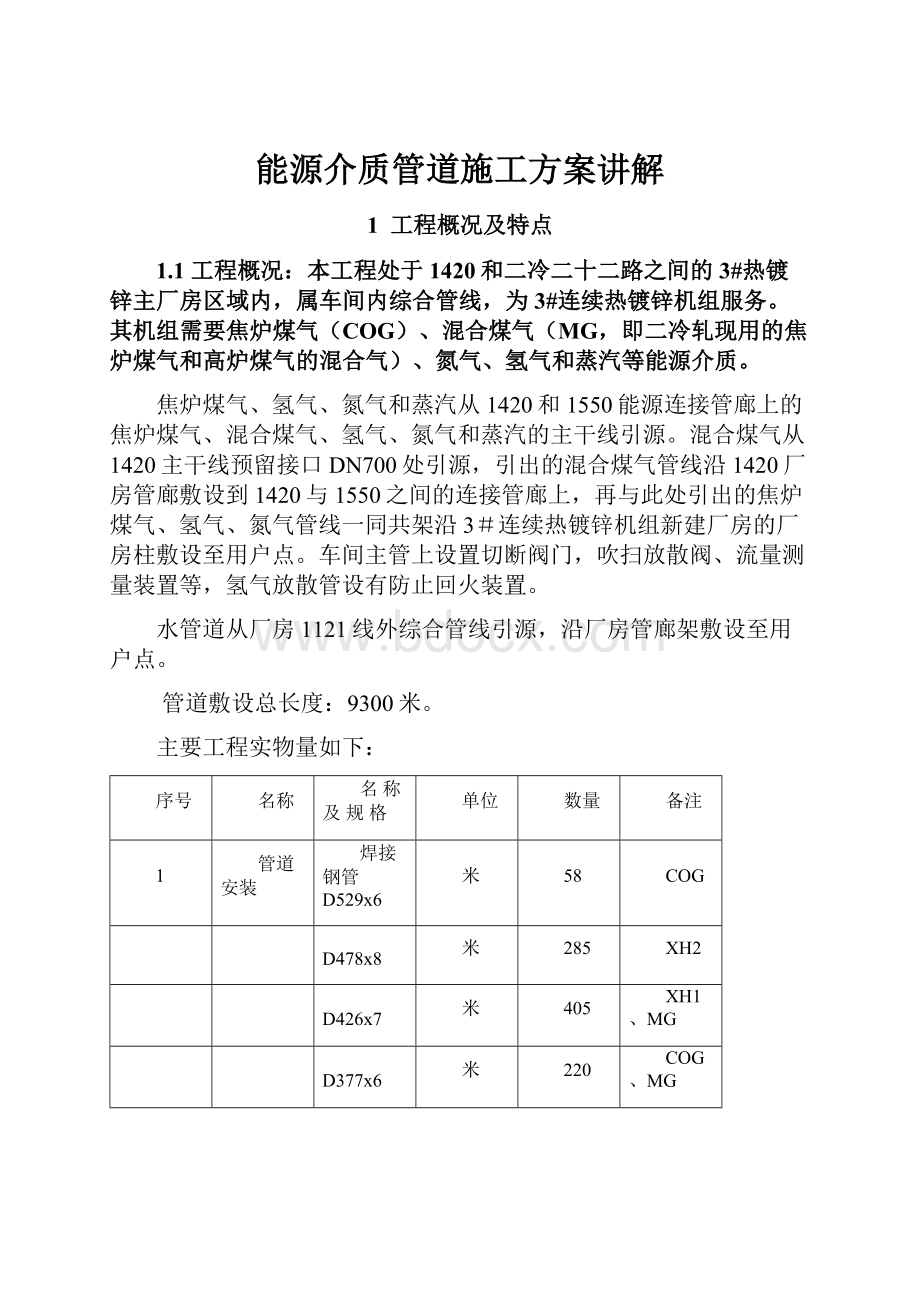
能源介质管道施工方案讲解
1工程概况及特点
1.1工程概况:
本工程处于1420和二冷二十二路之间的3#热镀锌主厂房区域内,属车间内综合管线,为3#连续热镀锌机组服务。
其机组需要焦炉煤气(COG)、混合煤气(MG,即二冷轧现用的焦炉煤气和高炉煤气的混合气)、氮气、氢气和蒸汽等能源介质。
焦炉煤气、氢气、氮气和蒸汽从1420和1550能源连接管廊上的焦炉煤气、混合煤气、氢气、氮气和蒸汽的主干线引源。
混合煤气从1420主干线预留接口DN700处引源,引出的混合煤气管线沿1420厂房管廊敷设到1420与1550之间的连接管廊上,再与此处引出的焦炉煤气、氢气、氮气管线一同共架沿3#连续热镀锌机组新建厂房的厂房柱敷设至用户点。
车间主管上设置切断阀门,吹扫放散阀、流量测量装置等,氢气放散管设有防止回火装置。
水管道从厂房1121线外综合管线引源,沿厂房管廊架敷设至用户点。
管道敷设总长度:
9300米。
主要工程实物量如下:
序号
名称
名称及规格
单位
数量
备注
1
管道安装
焊接钢管D529x6
米
58
COG
D478x8
米
285
XH2
D426x7
米
405
XH1、MG
D377x6
米
220
COG、MG
无缝钢管D325X6
米
5
MG
D219X6
米
680
S、XH1、XH2
D168X5.5
米
662
Hj1、SGS
D159x4.5
米
2000
YS、N2、S2
D140X5
米
800
XH1、L1、L2
D114x5
米
1450
SGS、S1、
L1、L2
D108X4
米
680
S、HY
D76X4.5
米
70
YS、CS
D76X3.5
米
200
YS
D60X4
米
95
XH1、XH2、YS
D57X3.5
米
220
H2
D48X3.5
米
53
HY
D27X2.8
米
35
S1
D25X2.5
米
150
配管
D21X2.8
米
60
YS
钢塑复合管[热滚塑PO(聚烯烃)]D168X5.5
米
318
Hj2
钢塑复合管(内衬PP)D89X4
米
165
HX
钢塑复合管(内衬PE)D108X4
米
340
CS
钢塑复合管(内衬PE)D76X4.5
米
300
CS
2
管道保温
岩棉管壳δ=70~110
米3
24
用与蒸汽
橡塑海棉管壳δ=30
米3
14
用于冷冻水
3
设备安装
阀门、阻火器、补偿器
套
165
支座、托座、滑动支架等设备
套
300
1.2工程特点:
1.2.1本工程中焦炉煤气、混合煤气、氮气、氢气、压缩空气、废水、蒸汽管道为压力管道,焊接要求高,技术含量大。
1.2.2管道焊缝射线照相检验量大,须边施工边检验,以及早发现问题并处理。
1.2.3施工场地狭窄,工期短,节点多,高空作业多,多数集中在管廊架上,增加了施工难度。
1.2.4管道试压,吹扫介质由甲方提供,施工时必须在能源部及项目组的管理协调下采取切实有效的安全技术保障措施,加强安全管理,确保试压、吹扫的顺利进行。
1.3工程开、竣工时间
开工时间:
2003.6.20
竣工时间:
2003.9.20
2编制依据及适用范围
2.1编制依据
1.《工业金属管道工程施工及验收规范》GB50235-97;
2.《现场设备、工业管道焊接工程施工及验收规范》GB50236-98;
3.《工业金属管道工程质量检验评定标准》GB50184-93
4、《钢结构涂装工程施工及验收规程》BZQ(GJ)0011-94
5.《压力管道安全管理与监察规定》1996;
6.《钢结构、管道涂装技术规程》YB/T9256-96;
7、压力管道安装质量保证手册(第一版)2000.6.1
8.图纸及有关技术文件上的技术、质量要求;
2.2适用范围
本方案适用于宝钢1800冷轧3#热镀锌机组工程中的能源介质管道安装工程。
3施工平面布置图
4施工进度计划
上海五冶冶金建设有限公司
编制人
陈峰
1800冷轧3#热镀锌能介管道工程施工计划
编制日期
2003.5.10
日期
工程项目
计划绝对工期
5
10
15
20
25
30
35
40
45
50
55
60
65
70
75
80
85
90
95
1、施工
准备
2、管道支、托架制安
3、管道敷
设、焊接
4、管道试
压、吹扫
5、测试
6、管道
油漆
7、管道
保温
5质量保证措施及预防措施
5.1施工过程质量控制流程图
5.2质量控制管理规程
5.2.1管道施工过程中的质量控制是由质量流转卡完成的,它由三部分组成:
材料流转卡、焊接流转卡、工艺流转卡。
5.2.2材料流转卡从材料进货标识发放再发放使用剩余材料回收进行全过程控制,确保所有材料的正确使用和可追溯性。
材料流转卡的签发由材料责任工程师负责。
所有材料必须有材质证明或合格证。
{注:
压力管道安装用主材:
(管材、钢材)都由甲方(宝钢厂)提供,其材质质量由甲方保证,但所供材料经检验不合格时应拒绝使用}。
5.2.3焊接流转卡从焊接工艺评定焊接工艺评定报告焊接作业指导书现场焊接控制焊后处理焊接检验焊口返修进行全过程控制,并确保每一过程的可追溯性。
焊接流转卡的鉴发由焊接责任工程师负责。
5.2.4工艺流转卡对除“材料”和“焊接”以外的工艺过程进行控制,确保对重要工序和特殊工序的重点控制。
将相关见证记录编号并在工艺流转卡上登记。
工艺流转卡的鉴发由工艺责任工程师负责。
本工程重要工序和特殊工序为:
1)氢气、氮气管线系统中的钢管、阀门、管件等脱脂;2)管道试验;3)管道吹扫
5.3质量预防措施
5.3.1为了确保管道安装质量,防止质量事故以及习惯性质量通病的发生特制定以下预防措施。
5.3.1.1针对工程特点,定期对工人进行质量意识教育,提高工人的质量意识,杜绝质量通病的发生。
5.3.1.2技术人员提前作好充分的施工技术准备,有针对性地对施工人员进行技术交底。
5.3.1.3特别是在压力管道施工中,应严格按照压力管道的施工要求进行施工,材料的管理必须严格按照压力管道材料流转程序进行,防止错用。
5.3.1.4施工过程控制:
工程技术人员必须跟作业认真巡查施工状况,及时发现问题。
上道工序施工完毕后必须经质检员确认合格后方能进行下道工序施工。
5.3.1.5利用经济杠杆,确保施工质量受控,对施工质量的好坏,特别是习惯性质量通病与施工班组的收入相挂钩,奖好罚劣,并且落实到人头。
5.4压力管道安装用焊工的资格确认
5.4.1本次管道安装用焊工全部持有锅炉压力容器焊工证,其项目符合本工程管道安装的要求。
6管道安装工程保证体系
6.1管道安装工程质量保证体系及劳动力构成
质量保证工程师尚修明
质量保证工程师助理曹正思
质量管理工程师胡泽江
检验责任工程师
李建全
探伤责任工程师
陈向阳
计量责任工程师
倪
蔓
测量责任工程师
倪
蔓
安全责任工程师
马
莉
筠
焊接责任工程师
杨
凡
理化责任工程师
林
强
热处理责任工程师
蔡静
设备责任工程师
杨
庆
材料责任工程师
王
晓
林
庆
工艺责任工程师
匡礼毅
设计责任工程师
陈希圣
项目责任工程师陈红武
持证氩弧焊工:
8名
持证起重工:
6名
管工:
25名
气割工:
6名
保温:
15名
其他:
7名
6.2管道安装工程现场质量、技术管理体系
五冶3#热镀锌项目部总工:
汤守权
五冶十五规划项目质检站站长:
徐卫坚
机电项目总工:
陈红武
工长:
刘明勇
设备员:
隋坤
材料员:
王道彬
技术员:
刘中兴
质检员:
陈峰
施工班组
6.3管道安装工程安全管理体系
监理公司
上海五冶机电公司安全部
机电项目部
经理:
聂丁未
副经理:
陈贻
安全员:
何建华
技术员:
刘中兴
技术员:
陈峰
工长:
刘明勇
施工班组
7管道安装主要施工方法及要求
7.1本工程所使用管道的技术参数见下表
管道
名称
设计压力(MPa)
管道
材质
管件材质
管道
保温
管道类别
焊缝检验
(设计要求)
氢气
0.7
20#
20#
无
压力管道
100%射线照相检验,GB3323Ⅱ级合格。
焦炉
煤气
0.04
20#
20#
无
压力管道
固定焊口:
10%,转动
焊口:
5%,
GB3323Ⅲ级合格。
混合
煤气
0.04
20#
20#
无
压力管道
氮气
0.7
20#
20#
无
压力管道
蒸汽
1.0
20#
20#
有
压力管道
含油
废水
0.55
20#
20#
无
压力管道
浓碱
废水
0.55
20#
20#
无
压力管道
压缩
空气
1.0
20#
20#
无
压力管道
循环供回水
0.65
20#
20#
无
消防水
0.65
20#
20#
无
事故水
0.45
20#
20#
无
冷冻水供回水
1.0
20#
20#
有
工业水
0.4
20#
20#
无
纯水
0.4
钢塑复合管(热滚塑PE)
钢塑复合管(热滚塑PE)
无
稀碱
废水
0.55
钢塑复合[热滚塑PO(聚烯烃)]
钢塑复合[热滚塑PO(聚烯烃)]
无
压力管道
含锌
废水
0.55
钢塑复合[热滚塑PO(聚烯烃)]
钢塑复合[热滚塑PO(聚烯烃)]
无
压力管道
7.2施工准备
7.2.1材料管理:
A)工程所需物资在投入使用前,均由物资供应部门组织验证或检验,以确保未经检验或检验不合格的物资不得入库和不得用于工程,并按〈〈不合格处理程序〉〉处理。
B)保证压力管道安装工程全过程中采购物资及工程产品(包括中间产品和最终产品)的质量在搬运、储运、入库、发放直至竣工交付的各个环节受到保护而不被损坏、混存和错用。
所有物资在搬运过程中均应有标识,并保护予以识别。
C)所有物资按贮存要求保管和入库,对有特殊要求的物资应予以隔离。
未经验收、检验的物资不得入库。
要求库房帐物一致,并做好物资发放记录。
D)阀门检测:
凡在出厂前已作过耐压强度试验,持有出厂合格证,且在安装前并无任何损伤疑点存在时,在接入系统管路前,只作单体阀门状态下的气密性检验。
本工程中焦炉煤气、混合煤气、氮气、氢气、压缩空气、废水、蒸汽阀门抽检比例皆为100%检查。
7.2.2管道组成件的检验:
管道组成件必须具有制造厂的质量证明书,其质量不得低于国家现行标准的规定;管道组成件的材质、规格、型号、质量应符合设计文件的规定,并应按国家现行标准进行外观检验,不合格者不得使用。
7.2.3对管道及各类附件进场后均应进行外观检查,有重皮、裂缝的管子及附件不得使用。
7.2.4管道的防腐
7.2.4.1氢气、氮气管道的防腐
1)管道的除锈,采用槽式浸泡酸洗除锈并达到B0级,其常用工艺流程见下图:
钝化废液处理
2)管道酸洗时要严格遵守操作规程,以防止酸洗件产生过蚀、氢脆,酸洗液的温度及酸洗时间应在规定的控制范围内,各工序之间须连续进行,不得中途停顿,钝化后应在48小时内涂完底漆,在涂底漆之前,如已返锈则应重新进行酸洗和钝化,其酸洗、钝化常用工艺参数见下表:
工艺参数
工序
介质
浓度(%)
PH值
压力(Mpa)
时间(hr)
温度
(℃)
脱脂
氢氧化钠
8~10
4
60~80
脱脂剂
0.5~2
酸洗
盐酸
5~10
8
常温
氢氟酸氨
0.5
缓蚀剂
0.5
漂洗
柠檬酸
1~5
0.5
常温
中和
氨水
25
10~11
0.5
常温
钝化
亚硝酸钠
0.5~5
8~10
0.5
常温
3)氢气、氮气管道浸泡除锈处理后,管内无油迹可不用再脱油,若检查管内有油时,须进行脱脂,其工艺程序如下:
风干
4)管道经酸洗除锈合格后涂刷底漆一遍,其油漆品种为C53-31红丹醇酸防锈漆。
7.2.4.2除氢气、氮气外其他管道的防腐
a、循环供回水、消防水、事故水、冷冻水供回水、工业水、含油废水、浓碱废水、蒸汽管道皆采用喷砂除锈,其质量等级为Sa2.5;
b、焦炉煤气、混合煤气、压缩空气管道采用喷砂除锈,其质量等级为Sa2.5;
c、蒸汽管道外壁涂刷E06-28无机硅酸锌耐热底漆一遍;
d、循环供回水、事故水、冷冻水供回水、工业水、含油废水、浓碱废水管道钢管内壁喷涂环氧煤沥青涂料[消防水(消火栓系统)喷涂无毒环氧涂料;消防水(水喷雾系统)喷涂环氧煤沥青涂料],厚0.2mm。
e、除蒸汽管道外其他管道外壁涂刷C53-31红丹醇酸防锈漆一遍;
7.3管道安装一般规定
7.3.1严格按照设备、管道安装、管道焊接工艺流程组织施工,并使用相关的专用表格进行过程和质量记录,在保证记录真实性、及时性、完整性和符合性的基础上确保其“可追溯性”,从而使施工质量处于受控状态。
7.3.2严格按施工图纸进行安装。
管道组成件的规格、型号、材质应符合设计规定,管道支承件的规格、型号必须符合设计规定,管道的走向、标高等应严格按图纸进行,支撑件的位置、固定方式不得随意变更。
7.3.3各种检验、试验、图纸、专用资料有明确规定的就按规定进行,如无明确规定时应按国家现行规范、规程、标准进行,其质量标准不应低于我国的现行规定。
7.4管道安装通用规定
7.4.1法兰与管道连接采用焊接时,法兰的内外两面都必须与管子焊接,法兰面与管子轴线倾斜度应小于或等于管外径的1/100。
7.4.2法兰连接时要严格对中,轴向最大允许偏差不大于2mm,不得用强紧螺栓的方法清除歪斜,拧紧螺栓分两次进行,第一次均匀对称拧一遍,然后再拧紧螺栓。
7.4.3法兰连接用垫片插入时要使垫片和法兰密封面无损伤、无划痕和其他异物。
7.4.4管道连接时不得用强力对口、加偏垫等方法来消除接口端面的空隙、偏斜或不同心等。
7.4.5
管道对口时管道同轴平直度须符合以下要求:
管径<100mm,α允许偏差不大于1mm,全长不超过10mm。
管径≥100mm,α允许偏差不大于2mm,全长不超过10mm。
7.4.6法兰连接时,须保证法兰间的平行度不得大于法兰外径的1.5‰且不大于2mm,不得用强紧螺栓的方法消除歪斜。
7.4.7法兰连接需保证与管道同心,螺栓穿入方向一致并能自由穿入。
7.4.8管道安装的极限允许偏差见表1。
表1
序号
项目
允许偏差(mm)
1
坐标
室外25
室内15
2
标高
室外±20
室内±15
3
水平管平直度
DN≤100
2L/1000最大50
DN>100
3L/1000最大80
4
立管铅垂度
5L/1000最大30
5
管道组对内壁错边量
不大于壁厚的10%,
且不大于2
7.5管道安装特殊规定
7.5.1用于氢气、氮气管线系统中的钢管、阀门、管件等,在安装前应按图纸有关要求进行脱脂处理,并出具相关脱脂检验报告。
7.5.2氢气、氮气管道、阀门、管件及仪表,在安装过程中及安装后,应采取有效措施防止受到油脂污染,防止铁屑、焊渣、砂土及其他杂物进入或遗留在管内,并应进行严格的检查。
7.5.3氢气、氮气管道的连接,应采用焊接,但与设备、阀门连接处按设计要求可采用法兰或螺纹连接。
螺纹连接处应采用聚四氟乙烯薄膜作为填料,严禁铅油麻丝等含油脂的材料。
7.5.4氢气、氮气管道内壁除锈必须彻底除去毛刺、锈斑、鳞片、浮渣,直至管道内壁出现金属光泽为合格。
7.5.5氮气、氢气管道应有防雷及防静电接地装置。
车间内部可与本车间的静电干线相连接,室外氢气、氮气管道在进出有爆炸危险的建筑物处、不同爆炸危险的边界、管道分支处应设防静电接地装置,接地电阻小于10欧。
管道每对法兰或螺纹接头间电阻值超过0.03欧时,应用导线跨接。
静电接地安装完毕后必须经过测试,电阻值超过规定时应进行检查与调整。
7.5.6水管需设排气阀,DN400及DN450管道采用DN50单口排气阀,DN400(不包含DN400)以下管道采用DN25单口排气阀,在排气阀前需加设一截止阀,纯水及含锌废水、稀碱废水管道上的排气阀截止阀及其支管要求衬塑,与纯水及废水管道所用管材一致。
7.5.7管道切割采用机械方法切割,当采用气焊切割时,切割表面要修磨平整,管端的切割粉沫、毛刺等用锉刀或磨光机清除干净。
7.5.8管道焊接皆采用坚固的“V”型坡口对焊连接。
管道名称
厚度T(mm)
坡口形式
坡口尺寸
间隙c(mm)
钝边p(mm)
坡口角度α(°)
主管焊接
3~9
0~2
0~2
65~75
支管焊接
1~2.5
1~2
40~50
7.6管道焊接
7.6.1管道焊接应符合《现场设备、工业管道焊接工程施工及验收规范》(GB50236-98)的要求。
根据施工图纸设计的管道组成件规格、材质和焊接要求选用适当的“焊接作业指导书”及焊工。
当施工图纸出现新材料、新工艺,公司现有“焊接作业指导书”不能覆盖时,必须进行“焊接工艺评定”,根据“焊接工艺评定报告”编制“焊接作业指导书”,指导焊接工作正确进行。
7.6.2管道焊接方法
7.6.2.1循环水供回水、消防水、事故水、冷冻水供回水、工业水、管道采用手工电弧焊。
7.6.2.2氢气、氮气、焦炉煤气、混合煤气、蒸汽、压缩空气、含油废水、浓碱废水管道:
管外径D≥100mm采用氩弧焊打底,电焊盖面;D<100mm的管道采用全氩弧焊。
7.6.2.3各项焊接工作都必须严格按相关的“焊接作业指导书”进行,不允许出现例外。
焊接过程精心操作,确保设计资料或规范所要求的焊接质量;及时、真实的填写各种相关记录,各种记录应全部反映在“管道单线图”上。
7.6.3管道焊接时焊缝区15~20mm内的污染物采用机械方法进行清理,焊接电弧1m范围内的相对湿度不得大于90%,焊接时的风速不得超过2m/s,当超过规定时,现场焊接应采取有效的防风措施,并加大氩气流量。
7.6.4管道焊接后,必须对焊缝进行外观检查,焊缝表面不得有裂纹、气孔、夹渣等缺陷。
焊缝检查合格后,须对焊缝进行射线照相检验,其检验标准见管道的技术参数表。
7.6.5经探伤检查发现不合格者,应对被抽查焊工所焊焊缝,按原规定数量加倍探伤,如仍有不合格者,则应对该焊工在该管道上所焊全部焊缝进行无损探伤检查。
7.6.6无损探伤的焊缝,其不合格部位必须返修,返修后仍按原规定方法探伤。
同一焊缝允许返修次数不超过三次。
7.7管道试压
7.7.1气体管道压力试验
管道
名称
设计压力P(MPa)
强度试验
气密性试验
泄漏量试验
试验
介质
试验
压力
试验介质
试验压力
试验介质
试验
压力
氢气
0.7
N2
1.15P
N2
1.05P
N2
1.0P
焦炉
煤气
0.04
N2或压缩空气
1.15P
N2或压缩空气
1.0P
混合
煤气
0.04
N2或压缩空气
1.15P
N2或压缩空气
1.0P
氮气
0.7
N2
1.15P
N2
1.0P
N2
1.0P
蒸汽
1.0
无油洁净水
1.5P
无油洁净水
1.5P
压缩
空气
1.0
无油洁净水
1.5P
无油洁净水
1.5P
1)氢气、氮气管道安装射线照相检验合格并经检查确认后,按强度试验和严密性试验、泄漏量的顺序进行试压。
2)气压试验:
先以0.2MPa压力进行预试压后进行强度试验,试验压力应逐级缓升,直到升至试验压力的50%进行检查,如无泄漏及异常现象,继续按试验压力的10%逐级升压,直至强度试验压力,每级稳压3分钟,达到试验压力后稳压10分钟再降至设计压力,停压时间应根据查漏工作需要而定,以发泡剂检验无泄漏,焊缝、法兰、支架、托座等无明显变形和破裂为合格。
3)水压试验:
先缓慢升压,待达到试验压力后,稳压10分钟,在将试验压力降至设计压力,停压30分钟,以压力不将、无泄漏为合格。
在试验过程中发现泄漏时,不得停压处理。
消除缺陷后,应重新进行试验。
试验结束后,应及时拆除盲板、膨胀节限位设施,排尽积液。
排液时应防止形成负压,并不得随地排放。
4)泄漏量试验:
管道的泄漏量试验应包括阀门、管件等在内,试验时的测压、测温点应有代表性。
泄漏试验压力等于设计压力,时间为24小时。
平均小时泄漏率对室内管道应以不超过0.25%为合格;室外管道应以不超过0.5%为合格。
全系统每小时平均泄漏率按下式计算:
100P2T1
A=——(1-——)×K%
tP1T2
式中:
A——每小时平均泄漏率%;
P1——试验开始时的绝对压力MPa;
P2——试验结束时的绝对压力MPa;
T1——试验开始时气体的绝对温度°K;
T2——试验结束时气体的绝对温度°K;
t——试验时间小时;
K——校正系数当DN<300mm时,K=1;
当DN≥300mm时,K=300/DN
DN——管道公称直径mm。
注:
试验用压力表已经检验并在周检期内,其精度不低于1.5级,表的满刻度值为被测最大压力的1.5~2倍,且压力表不得低于2块。
7.7.2循环供回水、消防水、事故水、纯水、冷冻水供回水、工业水、废水管道水压试验
1)水管道施工完毕后应进行水压试验,其试验压力为设计压力的1.5倍。
2)管道试压时升压、降压速度≤0.03MPa/min。
3)试压时,应逐步缓慢增加压力,管道升压至80%设计压力时,停止升压,检查无泄漏及异常现象时