进料检验手册管理.docx
《进料检验手册管理.docx》由会员分享,可在线阅读,更多相关《进料检验手册管理.docx(27页珍藏版)》请在冰豆网上搜索。
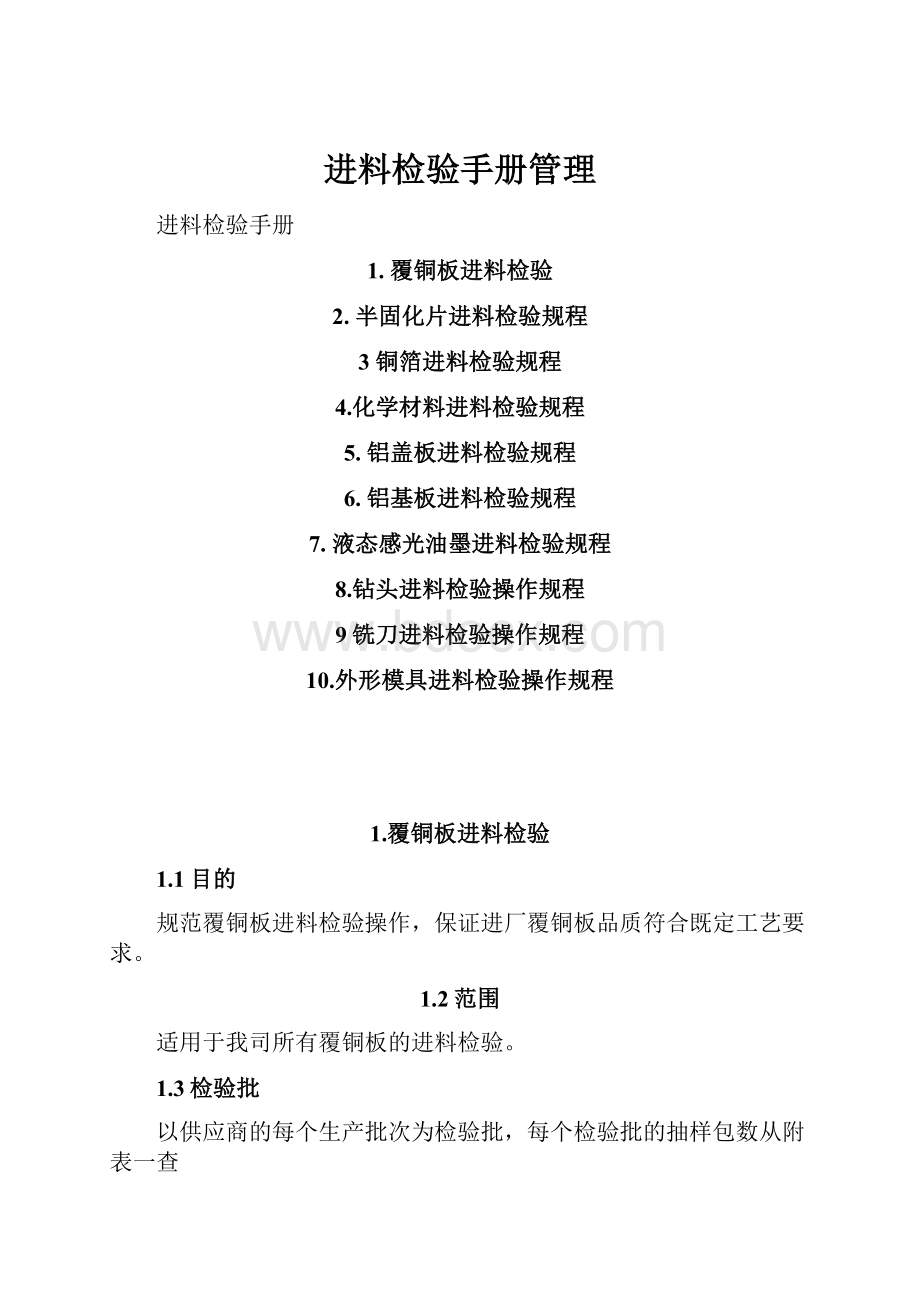
进料检验手册管理
进料检验手册
1.覆铜板进料检验
2.半固化片进料检验规程
3铜箔进料检验规程
4.化学材料进料检验规程
5.铝盖板进料检验规程
6.铝基板进料检验规程
7.液态感光油墨进料检验规程
8.钻头进料检验操作规程
9铣刀进料检验操作规程
10.外形模具进料检验操作规程
1.覆铜板进料检验
1.1目的
规范覆铜板进料检验操作,保证进厂覆铜板品质符合既定工艺要求。
1.2范围
适用于我司所有覆铜板的进料检验。
1.3检验批
以供应商的每个生产批次为检验批,每个检验批的抽样包数从附表一查
取。
1.4检验内容
1.4.1常规检验项目
检验项目
检验频率
样本容量(C=0)
检验
工具
检验方法
品质要求
一般抽样
加强抽样
标签
1次/检验批
AQL=4.0
AQL=2.5
目视
《检验标准》4.1
包装
1次/检验批
AQL=4.0
AQL=2.5
目视
《检验标准》4.2
尺寸
整张板
1次/检验批
AQL=4.0
AQL=2.5
卷尺
5.1
《检验标准》4.3
剪切板
IPC-41013.8.4.1.1
板厚
1次/检验批
AQL=4.0
AQL=2.5
千分尺
5.2
《检验标准》4.3
铜箔厚度
1次/检验批
AQL=4.0
AQL=2.5
铜箔测厚仪
5.3
《检验标准》4.4
外观
1次/检验批
AQL=4.0
AQL=2.5
5.4
《检验标准》4.5
1.4.2周期性检验项目
检验项目
检验频率
样本容量
检验工具
检验方法
品质要求
剥离强度
1/2oz
1次/季度/供应商
2块
TA631
剥离仪
5.5
《检验标准》4.7
1oz
注:
《检验标准》--《覆铜板及半固化片检验标准》
1.5检验方法
1.5.1尺寸检验
用卷尺测量样本的长、宽及对角线,并记录测量数据。
1.5.2板厚检验
用千分尺对样本的厚度进行测量,对其中5个样本各测5个点(测量
点要求如附图一所示),其余样本每一样本任选测一个点,并记录下测量结果。
1.5.3铜箔厚度
用铜箔测厚仪对样本的正反面各测量一个点,并记录下测量结果。
1.5.4外观检验
用正常视力观察样本正反两面的外观是否正常,如发现表面有污垢,须用
抹布蘸水轻轻擦拭,观察是否很容易擦去,记录检验结果。
1.5.5剥离强度
见WI-PL-022《印制板导线铜箔抗剥强度测试方法》。
1.6判定原则
所有检验后的判定按照“零缺陷”的原则进行,对判定为不合格品的以《进料不合格品处理规程》处理。
1.7支持文件与表格
《IPC-4101》
《覆铜板及半固化片检验标准》
《TA631剥离仪操作规程》
《印制板导线铜箔抗剥强度测试方法》
《进料不合格品处理规程》
《IQC检验记录》
附表一
检验批大小(SH)
1~50
51~280
281~500
501~1200
>1201
抽样包数(包)
1
2
3
4
5
附图一48”方向(板材纬向)
123
54
4
注:
所取的测量点距板边距离为1英寸
2.半固化片进料检验规程
2.1目的
对半固化片执行进料检验,保证生产用半固化片品质符合既定工艺要求。
2.2范围
适用于我司所有半固化片的进料检验。
2.3说明
检验批:
以供应商的每个生产批次作为一个检验批;
一般抽样:
IQC正常进料检验所采用的抽样方案;
加强抽样:
使用方法见《进料不合格品处理规程》。
2.4检验内容
2.4.1常规检验项目
检验项目
检验频率
样本容量
检验工具
检验方法
品质要求
一般抽样
加强抽样
标签
1次/检验批
1箱
全检
目检
《检验标准》5.2
包装
1次/检验批
1箱
全检
目检
《检验标准》5.3
尺寸
1次/检验批
1箱
2箱
卷尺
5.1
IPC-41013.8.4.1.3
凝胶化时间
1次/检验批
1箱
2箱
凝胶机
5.2
《检验标准》附页
压制厚度
1次/检验批
1箱
2箱
千分尺
5.3
《检验标准》5.6
2.4.2周期性检验项目
检验项目
检验频率
样本容量
检验工具
检验方法
品质要求
树脂含量
1次/规格/供应商/季度
1箱
分析天平
WI-IQC-15
《检验标准》
附页
注:
《检验标准》--深南电路有限公司《覆铜板及半固化片检验标准》
2.5检验方法
2.5.1尺寸检验
用卷尺测量宽度,共测量两次,计算其平均值。
2.5.2凝胶化时间
2.5.2.1取样
在半固化片上切取足够搓1000mg树脂粉的样片,将样片折叠或揉搓,并
用清洁的蜡纸收集半固化片上的树脂粉,将收集到的树脂粉用钢筛筛选处理,将过筛的树脂粉用蜡纸收集作为凝胶实验树脂粉。
2.5.2.2测量
按《凝胶机操作规程》对样本进行凝胶化时间测试,实验重复5次,去掉最大值及最小值,计算其余三个数值的平均值为此样本的凝胶化时间。
2.5.3压制厚度
2.5.3.1取样
在半固化片长度方向上切取约30”左右的样品,由层压准备工序下成两张
相同尺寸的半固化片,并按铜箔-半固化片-半固化片-铜箔的结构请层压工序以正常压制参数进行层压,压完之后将铜箔蚀去。
2.5.3.2测量
在距板边纤维至少1英寸处取12个点进行测量,所取点的位置如附图二
所示,将测量结果记录于《IQC检验记录》中。
2.5.3.3判定
用12个测量结果的平均值的1/2作为单张半固化片的平均压制厚度,判定
压制厚度是否合格时以该平均压制厚度是否在公差范围以内为准。
2.6接收原则
所有检验后的判定按照“零缺陷”的原则进行,不符合验收标准的以《进
料不合格品处理规程》处理。
2.7支持文件与表格
《进料不合格品处理规程》,《凝胶机操作规程》,《覆铜板及半固化片
检验标准》,《半固化片树脂含量测定规程》,《IQC检验记录》。
附图二长方向
3铜箔进料检验规程
3.1目的
规范铜箔进料检验操作,保证进厂铜箔品质符合既定工艺要求。
3.2检验类别
使用检验。
3.3检验批
以相同规格的每个进料批做为一个检验批。
3.4抽样方案:
以铜箔的卷数做为样本数,按C=0,AQL=10进行取样。
3.5检验项目及验收标准
检验项目
检验工具
检验方法
检验标准
宽度
卷尺
用卷尺测量整卷铜箔宽度,要求测量两次,计算其平均值。
测量值的平均值在铜箔标称宽度±3mm以内。
单位面积的铜箔重量
分析天平
按照《铜箔单位面积测量操作规程》,从待检铜箔中取样,测量铜箔单位面积的重量,计算其平均值。
测量值的平均值在附表一的规定范围之内。
外观
必要时用10倍放大镜。
目视
凹点与压痕
不能存在直径大于1.0MM的凹点或压痕;在任300*300MM面积内小于1.0MM的凹点不得超过2个
不能有永久性的皱折存在。
划痕
深度超过铜箔标称厚度20%的划痕不得存在,300*300MM范围内不允许超过3个。
夹杂物
尺寸大于0.002MM的杂质不得存在。
破洞、针孔
不允许存在破洞、针孔
6、清洁度
铜箔不得有污垢、烟渍、氧化点、盐类污迹、油脂、指印、外来物等存在。
3.6支持文件及表格:
《进料质量控制规程》;《铜箔单位面积测量操作规程》;《IQC检验记录》
附表一
铜箔规格
单位面积重量(g/m2)
1/4OZ(9m)
80.3±10%
3/8OZ(12m)
107±10%
1/2OZ(18m)
153±10%
1OZ(35m)
305±10%
2OZ(70m)
610±10%
4.化学材料进料检验规程
4.1目的
对化学材料执行入厂检验,保证进厂化学材料品质符合工艺要求。
4.2范围
双氧水、氨蚀刻液、甲醛、黑化药水、光亮剂。
4.3检验批
以生产批作为一个检验批。
4.4抽样方案
从每个检验批中任意抽取一个样本对相应的检验项目进行1次检验。
4.5送检流程
4.5.1流程图
:
4.5.2化学实验室按照以下检验依据对化学材料进行检验
材料名称
检验规程
样本容量
合格范围
双氧水
标称含量50%
《过氧化氢溶液分析方法》
80ml
双氧水含量≥50%
标称含量27.5%
双氧水含量≥27.5%
氨蚀刻液
《碱性溶液蚀刻方法》
80ml
PH>9.6,Cl离子浓度≥160g/l
黑化药水
《黑化药水进料分析方法》
80ml
PTL-103A浓度:
8.41~9.29N
PTL-103B碱强度:
7.13~7.87N
PTL-101碱强度:
2.29~2.52N
PTL-104浓度:
5.25~6.08N
甲醛
《甲醛溶液纯度分析方法》
80ml
甲醛含量>37%
光亮剂
《镀铜光亮剂分析方法》
600ml
UV分析值≥0.8,Hull试片合格,PH<2.0,比重1.025~1.035
注:
双氧水的标称含量指入库单上注明的双氧水规格含量。
4.5.3注意事项
常规情况下,IQC只对以上化学材料执行以上项目的检验,当生产线或工
艺部有其它材料的检验要求或增加检验项目时,则以生产线或工艺研发部门反馈的书面通知为准。
4.6支持文件
《过氧化氢溶液分析方法》
《碱性溶液蚀刻方法》
《黑化药水进料分析方法》
《甲醛溶液纯度的分析方法》
《镀铜光亮剂分析方法》
《化学材料检验单》
《进料不合格品处理规程》
5.铝盖板进料检验规程
5.1目的
规范铝盖板进料检验操作,保证进厂铝盖板品质符合生产要求。
5.2范围
适用于我司所有铝盖板的进料检验。
5.3检验批
以同规格的每个进料批作为一个检验批。
5.4抽样方案
5.4.1检验频率:
1次/检验批。
5.4.2样本容量:
AQL=4.0的C=0抽样方案。
5.5检验项目
5.5.1外观
5.5.1.1检验方法:
目视;
5.5.1.2检验标准
①不允许出现明显黑条、纵横向条纹、擦划伤;
②不允许出现凹坑、黑点;
③不允许有油污;
④平整性良好,无明显翘曲。
5.5.2厚度
5.5.2.1检验方法
用百分尺(或千分尺)依照覆铜板厚度的测量方法进行测量,并记录测量
结果。
5.5.2.2检验标准:
0.2±0.02mm;
5.6不合格品的处理
当检验员在检验中发现不合格时,应立即将不合格品隔离作好标识,并报
告IQC工程师按《进料不合格品处理规程》处理。
5.7支持文件与表格
《覆铜板进料检验操作规程》;《进料不合格品处理规程》;《IQC检验
记录》。
6.铝基板进料检验规程
6.1目的
规范铝基板的进料检验项目,保证生产用铝基板品质符合既定工艺要求。
6.2检验工具
千分尺,铜箔测厚仪,卷尺,放大镜,读数显微镜。
6.3检验批
以供应商的交货批作为一个检验批。
6.4抽样方案
按C=0,AQL=4.0抽样方案进行抽样。
6.5外观检查
6.5.1外观检查时目检,必要时用放大镜或读数显微镜;
6.5.2铝基板表面应平整,不应有分层、裂纹及毛刺;
6.5.3铝板面平整、氧化膜均匀,不能有影响使用的凹陷、裂纹、划痕等缺陷;
6.5.4铜箔面不应有影响使用的气泡、折皱、针孔、划痕、麻点和胶点。
任何变
色和污垢应能被浓度为5%盐酸溶液或丙酮擦去;
6.5.5铝基板不能有摔伤、撞伤、变形等缺陷。
6.6尺寸要求
6.6.1尺寸及偏差
板面尺寸
允许偏差
18”×24”
±3mm
6.6.2标称厚度及公差
标称厚度t(mm)(不含铜箔)
公差(mm)
0.5<t≤0.8
±0.06
0.8<t≤1.0
±0.10
1.0<t≤1.7
±0.13
1.7<t≤2.6
±0.18
2.6<t≤3.6
±0.23
6.6.3铜箔厚度检测
用铜箔测厚仪对样本铜箔的厚度进行测量,并记录测量结果。
6.6.4厚度检测方法
用千分尺测量样本厚度,当抽样数不小于5件时,至少对其中的5件每件
有4点测量值,其余每件只需测量一件;当进料数小于5件时,对每个样本测量4点,4点测量位置如附图一所示,所有测量点位置距板边10mm以外。
并记录测量结果。
6.7注意事项
6.7.1测量时应戴干净手套,防止铝板面出现氧化。
6.7.2板与板之间应隔纸(可用干净的白纸或牛皮纸),防止板面擦花。
6.8不合格品的处理
不合格品按《进料不合格处理规程》进行处理。
6.9支持文件及表格
《进料不合格品处理规程》;《IQC检验记录》;《进料不合格处理
单》。
7.液态感光油墨进料检验规程
7.1目的
规范液态感光油墨进料检验操作,保证进厂液态感光油墨品质符合既定工
艺要求。
7.2检验批
以供应商的每个生产批为一个检验批。
7.3抽样方案
在每个检验批中任意抽取1kg油墨对所有检验项目进行1次检验。
7.4检验标准
检验项目
检验标准
粘度
200±30ps(测量温度:
25±2℃)
硬度
油墨表面不能划伤。
附着力
不允许有油墨粘在胶面上的痕迹,并且油墨无脱落现象。
耐酸性
油墨层不允许出现变色、起泡、脱落、溶解等现象。
耐碱性
耐溶剂
耐焊剂
备注:
粘度项目的检验只需对PSR-4000Z100/Z26与DSR-2200C-7BS型
号的油墨进行。
7.5检验操作
7.5.1准备试验板
从废品板中选取一块面积不小于200mm×200mm的未印油墨的半成品板。
7.5.2请托丝印工序印制试验板
7.5.2.1油墨配制
由丝印工序在1kg油墨样本中称取适量的主剂和固化剂,并按《丝印液态
感光油墨工艺操作规程》对称取的油墨进行配制,配制完后对油墨粘度进行测量,并将测量结果填在《使用检验跟踪单》上交IQC。
7.5.2.2油墨印刷
由丝印人员按《丝印液态感光油墨工艺操作规程》对试验板进行印刷、预
烘、曝光、显影、后固化。
7.5.3检验员职责
由IQC检验员用剪床从试验板上剪取面积约为50mm×50mm的8块试片,分别用作检验油墨的耐酸性、耐碱性、耐溶剂和耐焊剂性;用试验板的剩余部分分别对油墨的硬度和附着力进行检验。
7.5.4检验方法
检验项目
检验方法
粘度
判断《使用检验跟踪单》上的测量结果是否在规定范围以内。
硬度
用6H铅笔与板面成45°用力在试验板上印有油墨的表面上划两道痕迹,观察油墨层有无划伤。
记录下试验结果。
附着力
先将试验板用乙醇洗净并晾干,在板上选取至少2处油墨面积不小于1cm2的表面,用手指把测试所用的3M1/2”胶带的胶面压在被测部位上,用力排除胶带内的空气并放置约10s,然后在与被测面垂直的方向上均匀地施加一个拉力,迅速把胶带拉起。
观察胶带上是否有油墨粘覆痕迹及板面状况,并记录结果。
耐酸性
取2块试片,浸入10%(质量比)的盐酸中,30分钟后取出。
观察油墨层有无出现变色、起泡、脱落、溶解等现象,记录下试验结果。
耐碱性
取2块试片,浸入10%(质量比)的氢氧化钠溶液中,60分钟后取出。
观察油墨层有无出现变色、起泡、脱落、溶解等现象,记录下试验结果。
耐溶剂
取2块试片,依照《助焊膜及字符耐焊剂和耐溶剂试验方法》进行耐溶剂试验,记录下试验结果。
耐焊剂
取2块试片,依照《助焊膜及字符耐焊剂和耐溶剂试验方法》进行耐焊剂试验,记录下试验结果。
7.6不合格品的处理
IQC检验员在检验中如果发现不合格情况,应对不合格油墨做好标识,并
报告IQC工程师按《进料不合格品处理规程》进行处理。
7.7支持文件
《进料不合格品处理规程》,《丝印液态感光油墨工艺操作规程》,《助
焊膜及字符耐剂和耐溶剂试验方法》,《使用检验跟踪单》。
8.钻头进料检验操作规程
8.1目的
规范钻头进料检验操作,保证进厂钻头品质符合既定工艺要求。
8.2检测工具
千分尺,游标卡尺,显微镜,OPTECH-M1钻头直径测定器,指套,钻头中
转盒。
8.3检验批
以供应商的每个生产批次为一个检验批。
8.4抽样方案
一般抽样方案按C=0中AQL=1.0进行抽样,加强抽样方案按C=0中
AQL=0.65进行抽取。
样本数以钻头支数为单位,尽量在每盒中平均取样。
8.5检验标准
检测项目
检验标准
钻径检测
钻径符合附表一内的公差要求
柄径检测
柄径符合附表一内的公差要求
全长检测
全长符合附表一内的公差要求
外观检验
螺旋槽内无杂物;符合附图《钻头常见的外观缺陷和控制标准》。
8.6验收原则
零缺陷验收。
8.7检验方法
检测项目
检测工具
检测方法
钻径检测
OPTECH-M1钻头直径测定器
1.拿钻头的手戴上指套;
2.将钻头轻轻从钻头盒中抽出,并放置于钻头直径测定器上;
3.大拇指压住钻头轻轻旋转,同时中指压住测定开关;
4.待显示盘上的数据稳定后,读取其数据,即为此钻头
钻径;
5.将钻头轻轻放回预备的中转盒中,待测其它数据。
6.记录数据。
柄径检测
千分尺
1.对千分尺先校零;
2.拿钻头的手戴上指套;
3.另一只手拿千分尺;
4.轻轻从中转盒中拿出钻头;
5.对一处柄径进行测量;
6.读取数据,并将钻头依顺序放回中转盒,待测量全长;
7.记录数据。
全长测量
游标卡尺
1.拿钻头的手戴上指套;
2.另一只手拿游标卡尺;
3.轻轻依顺序从中转盒中拿出钻头;
4.用游标卡尺测量其全长;
全长测量
游标卡尺
1.读取数据,并将钻头依次放回中转盒中,待下步使用;
2.记录数据。
外观检验
----
目视检测钻柄有倒角,无损伤,整个钻头清洁并有金属光泽。
显微镜
1.将样本钻头钻尖朝上,放在显微镜下;
2.钻径≥1.6mm的钻头,选用20倍放大系数检验;
3.钻径<1.6mm的钻头,选用大于20倍的放大系数检验。
4.检验完毕将钻头放入相应的原盒中。
8.8检验员职责
按8.7的检验项目逐一进行检验,按8.5的检验标准和8.6的验收原则
判定抽样批是否合格。
抽样检验合格后,由IQC印《进料检验合格证》印章;抽检不合格的按《进料不合格处理规程》处理。
8.9注意事项
8.9.1操作中接触钻头需戴指套作业;
8.9.2检验过程中钻头顺序不能放混,必须将相应钻头放回原盒中;
8.9.3操作中轻拿轻放防止损伤钻头。
附表一
项目
公差(mm)
钻径φ1(mm)
φ1+0–0.02
柄径φ2(mm)
φ2+0-0.02
全长L(mm)
L+0.30-0.20
9.铣刀进料检验操作规程
9.1目的
规范铣刀进料检验操作,保证进厂铣刀品质符合既定工艺要求。
9.2检测工具
千分尺,游标卡尺,显微镜,指套,中转盒。
9.3检验批
以供应商的每个生产批次为一个检验批。
9.4抽样方案
一般抽样方案按C=0中AQL=0.65进行抽样,加强抽样方案按C=0中
AQL=0.4进行抽取。
样本数以铣刀支数为单位,尽量在每盒中平均取样。
9.5检验标准
检测项目
检测标准
铣径检测
铣径符合附表一内的公差要求
柄径检测
柄径符合附表一内的公差要求
全长检测
全长符合附表一内的公差要求
外观检验
槽内无杂物;刀刃无崩刃、破损等严重的外观缺陷。
9.6验收原则
零缺陷验收。
9.7检验方法
检测项目
检测工具
检测方法
铣径检测
千分尺
1.对千分尺先校零;
2.拿铣刀的手戴上指套;
3.另一只手拿千分尺;
4.将铣刀轻轻从铣刀盒中抽出;
5.对一处铣刀直径进行测量;
6.读取数据,并将铣刀依顺序放回中转盒,待测量其它数据;
7.记录数据。
柄径测量
千分尺
1.拿铣刀的手戴上指套;
2.另一只手拿千分尺;
3.轻轻依顺序从中转盒中拿出铣刀;
4.用千分尺测量其柄径;
5.读取数据,并将铣刀依顺序放回中转盒,待测量其它数据;
6.记录数据。
全长测量
游标卡尺
1.拿铣刀的手戴上指套;
2.另一只手拿游标卡尺;
3.轻轻依顺序从中转盒中拿出铣刀;
4.用游标卡尺测量其全长;
5.读取数据,并将铣刀依次放回中转盒中,待下步使用;
6.记录数据。
外观检验
----
目视检测铣刀刀柄有倒角,无损伤,整个铣刀清洁并有金属光泽。
显微镜
1.将样本铣刀铣尖朝上,放在显微镜下;
2.铣径≥1.6mm的铣刀,选用20倍放大系数检验;
3.铣径<1.6mm的铣刀,选用大于20倍的放大系数检验。
4.检验完毕将铣刀放入相应的原盒中。
9.8检验员职责
按9.7的检验项目逐一进行检验,按9.5的检验标准和9.6的验收原则判
定抽样批是否合格。
抽样检验合格后,由IQC印《进料检验合格证》印章;抽检不合格的按《进料不合格处理规程》处理。
9.9注意事项
9.9.1操作中接触铣刀需戴指套作业;
9.9.2操作中轻拿轻放防止损伤铣刀。
附表一
项目
公差(mm)
铣径
φ1=3.175mm
φ1-0.02–0.05
φ1≠3.175mm
φ1+0.01–0.02
柄径φ2(mm)
φ2+0-0.02
全长L(mm)
L+0.50-0.50
10.外形模具进料检验操作规程
10.1目的
规范外形模具进料检验操作,保证进厂外形模具品质符合既定工艺要求。
10.2工作程序
10.2.1由工程部填写《生产工具检验通知单》,连同模具一起交品检部IQC。
10.2.2IQC检验员对模柄尺寸、定位销尺寸及定位销的松动情况进行检验,并
记录到《生产工具检验通知单》中。
10.2.3尺寸检验合格后,IQC检验员将模具交外形班班长或工艺工程师,由其安排人员按《外形模具使用规程》对模具进行安装、调试、试冲及自检,并将安装、调试情况记录到《生产工具检验通知单》中。
10.2.4由操作者将冲好后的零件交IQC,由IQC对冲压零件进行检验。
10.2.5检验合格后,IQC检验员负责在模具上贴上《进料检验合格证》标签,并将外形模具交工程部。
10.3检验方案
对于所有进厂外形模具,需按2.0款规定的程序进行全检。
10.4检验操作
10.4.1外形模具模柄尺寸、定位销尺寸检验及定位销的松动情况检查
10.4.1.1用卡尺检查模柄尺寸及定位销尺寸
60T冲床模具模柄尺寸要求为:
不加模套尺寸
φ50.8±0.1mm
加模套尺寸为
φ40+0.1/-0mm
10.4.1.2用手来回拧模具上的定位销两次,观察有无松动。
10.4.2冲压零件检验需检项目
10.4.2.1试冲件的尺寸是否符合MI的要求,有无漏冲孔槽情况;
10.4.2.2板面有无压伤、特别注