润滑油冷却换热过程设计.docx
《润滑油冷却换热过程设计.docx》由会员分享,可在线阅读,更多相关《润滑油冷却换热过程设计.docx(41页珍藏版)》请在冰豆网上搜索。
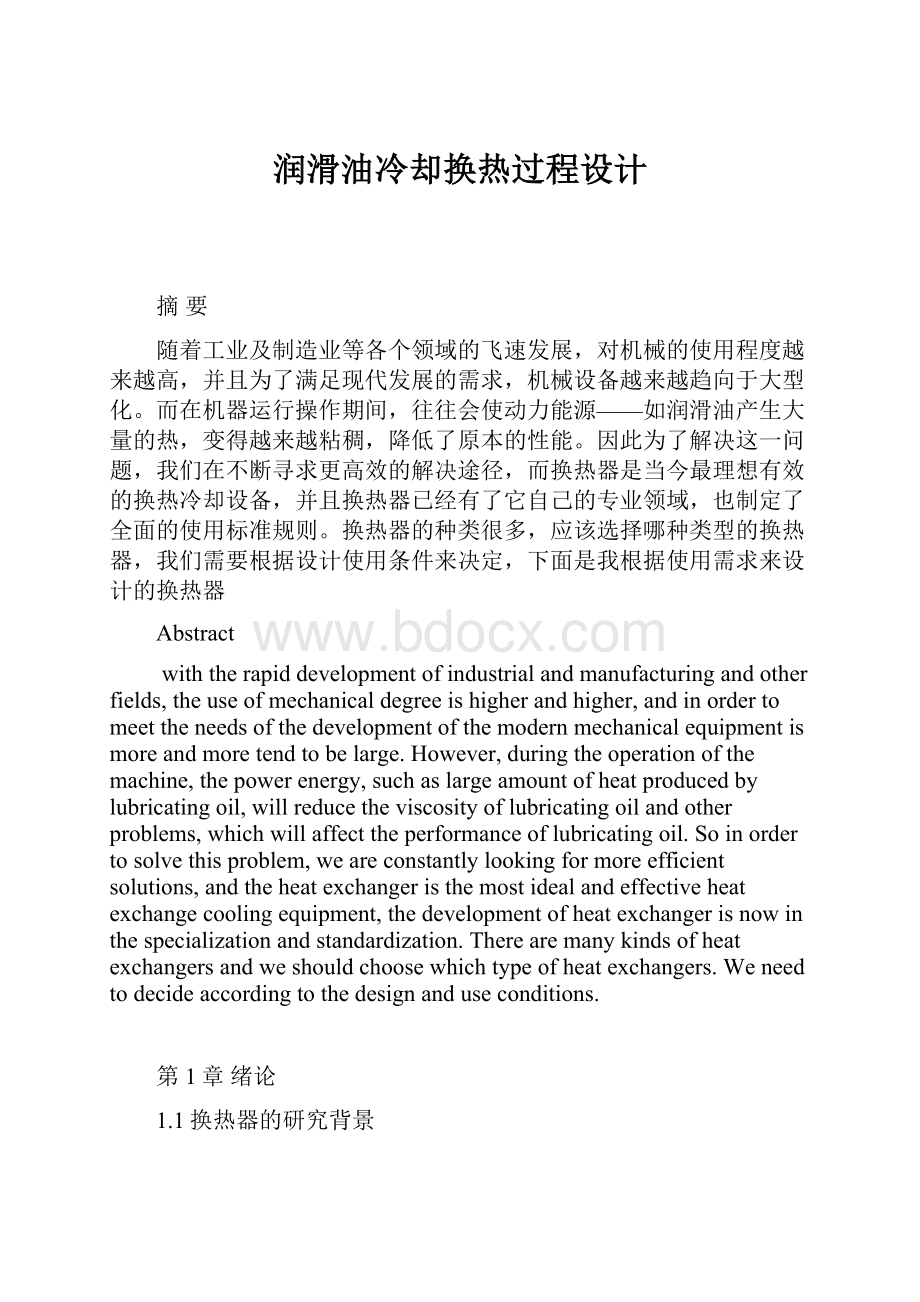
润滑油冷却换热过程设计
摘要
随着工业及制造业等各个领域的飞速发展,对机械的使用程度越来越高,并且为了满足现代发展的需求,机械设备越来越趋向于大型化。
而在机器运行操作期间,往往会使动力能源——如润滑油产生大量的热,变得越来越粘稠,降低了原本的性能。
因此为了解决这一问题,我们在不断寻求更高效的解决途径,而换热器是当今最理想有效的换热冷却设备,并且换热器已经有了它自己的专业领域,也制定了全面的使用标准规则。
换热器的种类很多,应该选择哪种类型的换热器,我们需要根据设计使用条件来决定,下面是我根据使用需求来设计的换热器
Abstract
withtherapiddevelopmentofindustrialandmanufacturingandotherfields,theuseofmechanicaldegreeishigherandhigher,andinordertomeettheneedsofthedevelopmentofthemodernmechanicalequipmentismoreandmoretendtobelarge.However,duringtheoperationofthemachine,thepowerenergy,suchaslargeamountofheatproducedbylubricatingoil,willreducetheviscosityoflubricatingoilandotherproblems,whichwillaffecttheperformanceoflubricatingoil.Soinordertosolvethisproblem,weareconstantlylookingformoreefficientsolutions,andtheheatexchangeristhemostidealandeffectiveheatexchangecoolingequipment,thedevelopmentofheatexchangerisnowinthespecializationandstandardization.Therearemanykindsofheatexchangersandweshouldchoosewhichtypeofheatexchangers.Weneedtodecideaccordingtothedesignanduseconditions.
第1章绪论
1.1换热器的研究背景
润滑油被广泛应用于各种大小型机械中,因为在机械运行过程中,各部件的运动会产生大量的热量,而润滑油在运转过程中会带走大部分的热量,使机械设备降温,润滑油冷却器可以延长润滑油的使用寿命,因为它们得到了有效的冷却,因此,润滑油冷却器是大型运转设备的重要组成部分[7]。
除了机械运转设备,润滑油冷却器还广泛应用于其他领域,例如:
核电厂、船舶动力装置等领域中。
其主要任务是发挥冷却润滑保护的作用,以防止由于润滑油高温而导致润滑剂的黏度降低。
这样润滑油将不能很好地附着于机器的摩擦表面,从而失去了润滑油本身的润滑作用和冷却作用,此时,如果继续使用该高温润滑油轻者会影响机械设备正常的稳定运行,重者将会触发安全保护系统动作。
所以,润滑油冷却器的主要目的是将润滑油冷却至适当的温度以维持设备系统安全稳定地运行。
多种类型的换热器为固定管板式、浮头式、U型管式、滑动管板式、填料式换热器等[1]。
其中,板式换热器起步晚,但在中国发展迅速。
其优点:
传热系数高,一般为管壳式换热器的两倍以上[10];末端温差小,可以在传热温差大的场合使用;结构紧凑,单位容积内传热面积大[10];价格成本低,金属材料耗量少且金属板材比管材的价格低,所以可以降低制造成本;并且清洗维修方便。
板式换热器所用的板材除了不锈钢外,还有锅板、铁板等,钎爆的绍合金板式换热器在国外最大可承受可适用于多种介质换热,比如冷凝器、蒸发器、油冷器等。
而管式换热器的优点有:
结构坚固、适应性好、可靠性高、用材范围广等,但其在结构紧凑、材料耗损价格以及换热效率等方面不及其他换热器。
因此,换热器的广泛应用使得其在国民经济中占有重要的地位[18]。
顺应生产制造的发展,当今,各国对换热器的生产正朝着大型化、高温化、高压化的方向发展。
1.2换热器的分类及特点
列管式换热器
夹套式换热器
间壁式换热器
沉浸式蛇管换热器
套管式换热器
混合式换热器
换热器
蛇管式换热器
喷淋式换热器
蓄热式换热器
板式换热器
1.按作用原理或传热方式分类
(1)混合式换热器
混合式换热器的主要原理是冷热流体通过互相接触和混合达到热交换的目的,其热交换效率关键影响因素是热流体和冷流体流体的接触面积。
所以为了提高其效率就要使冷热流体的接触面积尽可能增大。
为了获得更大的接触面积,可以防止装置中的阻隔填料,并且液体有时可以喷射成细小液滴,。
(2)蓄热式换热器
这是热流体和冷流体依次通过相同固体填料的表面,然后当冷流体通过时,热量被带走,使得填充物被加热和冷却,热流体和冷流体之间进行传热,当使用这种热交换器时,不可避免地会有少量的两种流体混合,并且必须成对使用[9]。
(3)间壁式换热器
间壁式换热器是使用最广泛的一种换热器,它是使冷热流体通过壁面进行传递,利用一种固体壁面将进行热交换的两种流体隔开[9]。
2.按照换热器传递热量的面积大小,以及其形式的不同可以分为:
按照换热器传递热量的表面积的形式分:
(1)通过管壁传热的换热器(称为“管式”)
①蛇管式换热器
②套管式换热器
③U型管式换热器:
它分为U型管和浮头型。
(2)通过换热器平板表面而进行热量交换的换热器(称为“板式表面”)
①螺旋板式换热器
②板式换热器
③伞板式换热器
④板翅式换热器
⑤板壳式换热器
(3)其它形式的换热器
这种换热器一般似乎满足一些特殊的要求,比如比较成熟的旋转换热器和热管,还有一些还处于开发阶段。
5.下面我们主要介绍列管式换热器。
列管式换热器主要由壳体、封头、换热管、管板、折流挡板、拉杆定距杆等组成,分为管程和壳程两种工艺,它们分别是管内和管外的热流体和冷流体的流动,它是化学及酒精生产中使用最广泛的换热器[2]。
优点:
稳定性好、材料类别丰富、易于使用等。
该装置的单位面积可以提供大的传热面积,良好的传热效果和较大操作灵活性,并且常用于大型装置。
有许多类型的管式换热器,根据其温度补偿结构目前广泛使用,主要有以下类别:
1)浮头式换热器
浮头就是它换热器首尾管板不和外壳体结合的区域。
为了去除因温差产生的作用力,在加热换热器管道时,沿管子垂直方向与浮头一起发生膨胀和收缩效应
新型浮头热交换器的浮头端部结构包括缸体、外盖侧法兰、浮头管板、钩环、浮头盖、外头盖、线孔、钢圈,在外盖侧法兰的内侧设有凹形或梯形的密封面,在密封面的外侧钻有多个螺旋均匀的布料并焊接在一起。
浮头上的钩头及相关部件被拆除,浮头管板的密封槽为原凹槽,另一端在管板中心的同一端面开口[12]。
半径稍大于管束外径的梯形槽,管板分割槽只与梯形槽联通,不与凹槽连通。
浮头式换热器的特点:
其管板一方面在换热器外壳部位和管子箱体中间部分固定,另一方面可以在壳体内部来回往复运动。
其优点是:
壳体和管束可以自由膨胀已消除热应力;为清洗全面清洗管道内外,可以将管子从壳体里面分离出来。
其缺点是:
结构复杂,造价高(比固定管板高20%);操作过程中容易在浮头上发生泄漏,并且不容易检查和处理。
通常在工作运行环境温度变化差异较大的情况下,浮头式换热器是首选换热器。
图1.1浮头式换热器结构
2)固定管板式换热器
固定管板式换热器的两端管板和壳体制成一体,管板固定不能移动,在冷热流体温差较大或壳体和管束热膨胀不同时,补偿环(或膨胀节)通常焊接在外壳上以补偿其温差应力,固定管板式换热器主要由管板、管壳、管头、管束组成,管板也称固定管板,是通过焊接或胀接的方式与壳体连接,不能移动,并且在壳体内设置有若干块折流板,折流板的数量是由管束的长度决定的,像这样的换热器可以用分程隔板分成任何程数[3]。
这类换热器的优点是:
结构比较简单、紧凑;造价便宜,其缺点是:
壳侧清洁困难,不应用于脏或腐蚀性介质。
另外,此类型的换热器还具有现实意义的特点,可以将管板和管道固定成一种特定的结构形式,两者之间所连接的一个结构形式是刚性的。
并且管的内部和外部是两种不同温度的流体,在流体之间的温度差极大时,管壁和壳壁(因热胀冷缩的物理效应)之间会发生巨大的形变,产生一种作用力,对管子产生危害。
为了防止温度差产生的作用力可能出现的安全隐患发生,例如,高温时管壁和壳壁之间发生形变,一般情况下都需要对换热器设置温度补偿装置。
(工业规定:
两者之间的温度差大于50度必须设置)
图1.2固定管板式换热器
固定管板式换热器的特点
1.旁路渗流较小;
2.造价低;
3.无内漏;
4.设备寿命低,不适用于壳体加工容易污染的场合。
3)U型管式换热器
U型管换热器主要由管板,U型管,壳体,封头等组成,它的特点是在同一块管板上将管子出入口部位结合在一起。
U型管式换热器的特点:
图1.3U型管换热器结构示意图
1.热补偿性能好:
其管子可以在壳体内来回往复移动的特点,即使存在管子和壳体之间的温度差异,也不会有很大的温度作用力。
2.传热性能较好:
双管程结构使工艺更长,流速更快,热交换更快;承压能力强;
3.便于检修和清洗:
管束可以从壳体中取出并且具有简单的结构和低成本。
4.但是,它最大的劣势是:
既不容易清洗又不方便更换管道,这给换热器工艺带来了很大的麻烦,而且在U型部分半径不能过小,不然有可能导致堵塞甚至发生断裂。
U型管式换热器影响其壳程换热的因素:
弯曲半径不能过小,为使排管紧凑则管子数目不能过多,并且管束中心部分存在间隙会使壳程流体容易短路,U型管换热器限制使用因素:
为了补偿弯管后管壁的减薄,直管段需要使用较厚的管道,所以只适用于管箱壁温差较大的场合[13]。
3)填料函式换热器:
该换热器在一个方向上可以任意胀起,温度性能较优,与浮头式相比,少了一个浮头结构,因此简单经济性很高,缺点是壳体中的介质可能泄漏出来,并且局限性很强。
1.3换热器的发展史
1.换热设备的发展概况
换热器的发展已有两百多年,主要可分为三个发展时期:
原始时期(20世纪以前);初步发展时期(20时间的前50年);迅速发展时期(近30余年)。
(1)原始时期
这段时间生产的换热器主要服务于冶金制造业、化学工业生产,以及发电厂,当时的换热器没有那么发达,几乎都是靠铸造形成的管子组装成的管式换热器。
当发展到19世纪50年代时蓄热室取代了管式换热器,是由于考贝尔和西门子发明的用于炼铁和炼钢炉的再生器比原来的管式换热器要热得多。
(2)初步发展时期
在1920s初期,换热器迎来了一个崭新的时期,发展非常迅速。
在科学理论指导下的初步发展时期。
在20世纪的前50年,换热器的发展情况如下:
①管式换热器发展迅速
在50年代初,管式换热器主导了所有的换热设备,各种管式换热器(U型管式、套管式、盘管式、蛇管式等)已经比较完善,许多国家也制定了相关标准,随后发展的冶金工业也使换热器在性能上更加优良,为了提高换热器的效率,翅片管换热器出现在20世纪30年代[16]。
②出现了多种板式结构换热器
顺应时代的发展需求,对换热提出了更高的要求,所以,此时板式换热器就诞生了,比管式换热器更加符合当时社会的需求,它在交换热量方面性能更加突出,而且不会损耗过多的材料,并且它的结构形式紧凑、简单,因此在当时它的发展备受关注。
之后,各种类型的板式换热器也出现在大家面前,带动生产制造等各个领域的发展。
(3)迅速发展时期
在1950s以后的时期,换热器开始了黄金发展时期,这段时间期间换热器的发展速度十分快,也得到了科学界技术研究方面和生产制造领域的充分认可。
①管式换热器的发展
随着强化传热的发展和新型材料的出现,使换热器的关键受力部件得到极大的改进,换热器也得到了飞速的发展。
同样,U型管换热器在某些方面也取得了很大的成就,具备板式换热器独有的优点,并且U型管换热器采用的是经过加强后的管子,性能更加优良。
当前,U型管换热器已经能承受高达1500℃(8MPa压力)的温度了。
②板式换热器的发展
随着工艺和传热的发展,板式换热器在过去的20年中发展迅速,在压力低,温度不高,流量不是很大的场合,各种板式换热器逐渐取代了管式换热器,其中,作为高效热交换装置的螺旋板式热交换器发展得特别迅速[15]。
2.换热器的发展趋势
当前换热器发展的基本趋势将是:
更大的体积、更严格的执行规定、更高的热量交换效益、更高的统一指标、结构更加紧凑。
U型管式换热器:
U型管式换热器的发展速度一直以来都很快,在于它在结构方面坚固的优势,以及制造U型管式换热器的材料丰富等优点使其具备在温度较高、压力较大的情景下使用。
电焊焊接式的翅片管的结构其传热效率更高,将会得到更广阔的发展前途。
自动化的日益需求、机械代替手动的趋势正在各科学技术领域上映,这会促使换热器起到更大的作用。
板式换热器:
这种热交换器的设计将通过提高工作温度和工作压力来提高其处理能力以进一步发展。
使它在更多领域发挥更多的作用,与此同时探索更加丰富的制造材料和制造方法。
其中,为提高工作温度和工作压力,扩大使用范围,开发新型垫片材料,改进密封结构,提高板材的刚度将成为未来发展的重点。
换热器在近代工业中的
1.4换热器应用情况
1.换热器在近代工业中的应用
化学生产制造领域对换热器的依赖也很大,通常换热器会为化学反应过程提供所需要的热量以及化学药剂相互反映都会产生大量的热(例如氮肥的生产)。
在生产活动结束后必须将药剂及反映环境回到室温状态,这时候,就必须通过换热器冷却、冷凝作用实现。
当然除了给化工生产降温,换热器还可以给化工生产提供反应所需要的温度,为化工生产环境加热,提供合适的反应温度。
由此以来可以更加充分地说明换热器为化学制造研究等领域提供反应条件的重要性。
在制冷领域中换热器也必不可少,比如用于制冷的制冷剂在被压缩机压缩后,需要用冷凝器冷凝成液体;相反,在液化的高压液体冷却剂经历绝热膨胀之后,它需要进入蒸发器以吸收热量并蒸发,然后以气态的形式再回到压缩机使用,这个双向的过程往复循环就是制冷过程。
火力发电厂设备配备有各种类型的热交换器(用于反应产品加热器、燃料加热器、整流冷凝器、空气预热器)。
其实,火电厂中最普遍的锅炉就可以看做一个大型复杂的换热器:
燃烧热量加热表面加热对流蒸发对工作流体进行加热,最后使工作流体汽化并加热,以满足可输送至汽轮机的过热蒸汽要求。
各种类型的换热器(加热器、蒸汽冷凝器、蒸汽发生器等)都应用在核电站中,为整个系统的反应条件和安全保障做后盾。
我们以蒸汽发生器为例:
核燃料裂变产生热量→传热给冷却剂→冷却剂再热→传递热量给反应产物→反应产物汽化→蒸汽带动汽轮发电机发电。
换热器存在于各个领域,如化学工程、电力和制冷。
例如,火力发电厂和石化公司可以将70%的热交换器投入使用,这是一个不容忽视的重要部分。
2.换热器在节能降耗中的应用
换热器在节约能源降低燃耗方面所做得贡献可以分为两个方向,一个是因换热器能够收集剩余温度不浪费释放掉,而做到节约能源的作用,另一个是,它可以提高热量交换的效益,从而达到降低燃耗的目的。
所以说,换热器在节能降耗方面发挥着巨大的作用。
根据调查显示,当前在回收废弃温度方面换热器是最有用的。
以锻造炉为例,普通加热炉每千克锻件的能耗为装有热交换器的加热炉每千克锻件能耗的4.7倍,在燃烧燃料的工业炉中,约60%至70%的热量被烟道气带走,并且热效率低[14]。
热交换器的安装利用烟气的余热来预热工业炉的入口空气,从而提高了工业炉本身的热效率,并且也节省了燃料。
使用普通热交换器将空气预热至三至四百摄氏度,通常可节省燃料的15%至25%。
使用高温换热器,可以获得更好的效果,节省高达40%的燃油。
燃烧低热量燃烧炉并将空气和气体预热至300摄氏度可以使升温速度提高1至2倍,并使产量增加20%至30%,我们必须尽快考虑外部需求,争取更大的经济效益[14]。
同时要把燃料综合利用的原则作为其他余热回收的核心。
1.5课题简介
换热器的本身工作原理其实就是不同温度流体之间相互交换热量而发生温度变化。
广泛应用于化工,炼油,电力和原子能以及许多工业部门,是确保工艺流程和条件,利用二次能源实现热量回收和节能的主要设备。
换热器主要完成将高温炉体的温度传递给低温流体,实现热量交换的工艺,在整个生产工艺中操作着包括冷却、冷凝、蒸发和加热等动作。
换热器占化学工业总投资的10-20%。
1.5.1U型管式换热器
换热器的种类是多种多样的,每种类型的换热器都因为它的结构及其材料特性具备不同的工作特性,换热器按结构形式分可分为板式换热器和管壳式换热器,今天我们着重介绍一下管壳式换热器,管壳式换热器分为:
固定管板式、U型管式换热器、浮头式换热器和填料函式换热器,每一个换热器都有自己独特的工作特性,使用于不同的场合[8]。
此类换热器的特点是:
①管子能够在壳体内部来回往复移动,因此即使管壁外部和壳体壁面的温度差异较大,也不会产生温度作用力,温度效应好;
②U型管的特别结构使得热量流通路径长,效益高;
③承压能力强;
④管子部分可以单独从壳体中分离出来,这样会给检修、清洗等带来更加便利的条件。
此类换热器缺点是:
①管内清洗不便;
②管束中间部分的管子难以更换;
③为了流体在U型位置畅通不发生堵塞等情况,所以设计制造的中间位置U型部分直径较大,导致排列管子稀疏;
④最内层的U型管所形成的大量的区域会影响壳体内流体的流动情况,很大可能会发生短路现象,这样会热量交换效果大大降低;
⑤在U型管笔直段和弯曲段的过渡部分,会出现笔直段管子厚度减小的情况,所以此时的管子厚度就很大,限制了它的使用范围。
图1.4U型管换热器结构简图
1.6工艺简述
1..6.1换热器的选型
传热设备的种类很多,在设计中,我们应采用哪种类型的换热设备,需要综合考量各种因素,其中包括设计条件的限制因素,比如流体的性质、温度、压力、流速等,以及预算成本等。
还包括换热设备本身的性能特征及适用场合和条件。
综合考虑内因和外因选择最佳的换热器型号。
选择型号应注意以下几点:
1)流体的性质;
2)流量及热负荷;
3)运行过程的温度、工作环境压力,以及执行标准规定的压力降区间;4)对清洗、维护的要求;
5)设备的结构材料,尺寸及空间的限制;
6)价格。
综合考虑,该设计最终选择了U型管式换热器。
1.6.2介质流动空间的确定
为工作流体选择路径时,应参考以下几点:
①对于容易结垢、不清洁或者黏度较大的流体应走易清洗的通道(比如油品等),U型管式换热器就属于此类,但是大型管板累管壳式换热器除外。
②如果需要增大对流传导系数的流体,通常采用提高流体的流动速度,单提高流体在管程内的流动速度有很多局限性,不可能一味地增加其表面积尺寸,所以一般通过串联壳体来达到增加对流传热系数。
③对于具有腐蚀性的流体,通常选择该流体走管程,这样就只需要对封头和管板采用耐腐蚀性的材料,大大降低了生产成本。
④如果高压流体分配在管子中,这样可以很有效地给外壳体减压。
⑤管子里的高温流体距离外界空气远,热量不会与气体发生交换。
⑥由于蒸汽清洁、传热系数和流速小一级便于冷夜排除的特点,一般使蒸汽走壳程。
⑦高粘度流体通常流入壳体空间。
当流体不能满足一个点,同时兼备多种特点的话,应根据具体的情况,举重就轻作出最适宜的选择。
1.6.3介质流动方向的选择
由公式
当热负荷Q和总传热系数K一定时,
A与成反比。
流体在换热器中流动的两种形式:
并流时:
并<逆
由A=Q/K得:
A并>A逆,
由上式分析可以得出,两端温度一定,并流的比逆流的小,所以相同的传热面积,逆流传热效率更高。
逆流在节省用料方面的成就也功不可没,逆流时所需的加热冷却药剂量较少。
并流时,
t总是低于T
逆流时,
t可以高于T
所以,
冷却剂(T1-T2)的温升可以大于比并流的温升。
同理
在相同条件下,逆流过程加热剂温降大于并流。
1.6.4管子排列方式的选择
换热管的排列主要有以下四种方式:
图1.5换热管排列形式
正三角形排列因为管间距都相等为正三角形的边长,因此在一块面积相同的管板上,三角形排列方式所排列的管子数最多。
若壳体内是易结垢或者黏度很大的流体,则壳体需要大强度的机械设备清洗,这时对空间体积的要求就比较大,所以正方形排列就是最佳方式。
图3.5.3中(a)和(d)以两种方式排列,具有相同的挡板间距,其流动截面小于(b)河(c)的流动截面,有利于提高流量,因此更为合理。
该设计中采取正三角形排列。
1.7U型管式换热器的设计综述
U型管式换热器的设计和分析最重要的是热力设计,它不仅使用于初始设计的新机器,而且使用于已为成品甚至是已投入使用的换热设备,起着重要作用[15]。
热力设计指根据用户的使用需求选择最适宜的设计运行参数,然后再运用传热知识进行传热计算检验是否符合要求或是最佳选择[15]。
流动设计实质是指压降的计算,也就是为换热器的动力设备的选择做准备(比如泵)。
并且热力设计和流动设计不是单一的个体,两者之间密切关联,尤其热力设计过程还需要在流动设计参数中得到[15]。
结构设计是指根据设计需求、热力计算、流动计算确定设备的结构框架与尺寸。
为了保证安全,在对换热设备时通常要对进行强度的校核,特别是对一些承压大或者受压不均匀的部件进行校核,处于高强度工作环境(高温高压)下的也要进行强度校核。
第二章U型换热器的传热设计
U型管式换热器的工艺设计包括以下内容:
1.根据要求确定设计方案;
2.初步确定换热器的结构和尺寸;
3.核算换热器的传热面积和流体阻力;
4.确定换热器的工艺结构
2.1设计条件
表2-1设计条件
壳程
管程
流体名称
可耐压齿轮油
冷却水
总流量(kg/h)
1000
13779.90
工作温度/进/出(℃)
T1=150;T2=30
t1=25;t2=25
压力/(MPa)
1.5
入口1.0;出口0.9
2.2确定物性参数
在以上条件下,查得其基本物性数据为:
表2-2物性数据
介质
密度(kg/m3)
比热容(KJ/kg×℃)
黏度(Pa×s)
导热系数(W/(m×℃))
冷却水
1000
4.18
0.735×10-3
0.6167
齿轮油
855
2.0
0.91×10-3
0.14
2.3符号说明
0——热流体的密度,kg/m3;
0——热流体的黏度,Pa×s;
0——热联体的导热系数,W/(m×℃);
——热流体的比热容,KJ/kg×℃;
——冷流体的比热容,KJ/kg×℃;
i——冷流体的密度,kg/m3
i——冷流体的黏度,
i——冷流体的导热系数,
——换热管数目。
2.4流体走向的确定
根据前述流体走向的选择条件,冷却水黏度小、清洁且易结垢,应走管程,可耐压齿轮油粘度大,且温度压力较高,不易清洗,所以可耐压齿轮油走壳程。
2.5传热计算
2.5.1