压力容器基本检验标准.docx
《压力容器基本检验标准.docx》由会员分享,可在线阅读,更多相关《压力容器基本检验标准.docx(19页珍藏版)》请在冰豆网上搜索。
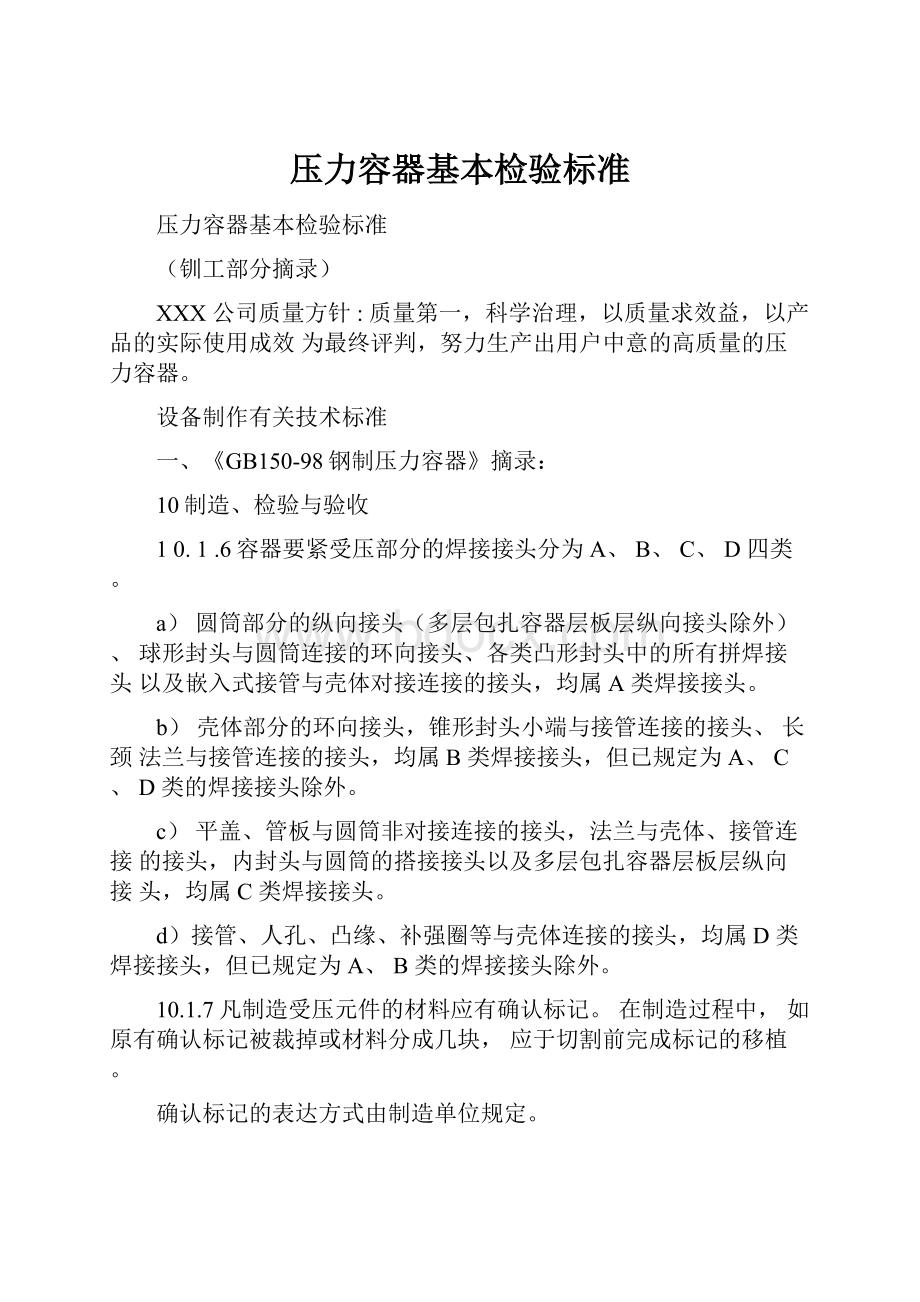
压力容器基本检验标准
压力容器基本检验标准
(钏工部分摘录)
XXX公司质量方针:
质量第一,科学治理,以质量求效益,以产品的实际使用成效为最终评判,努力生产出用户中意的高质量的压力容器。
设备制作有关技术标准
一、《GB150-98钢制压力容器》摘录:
10制造、检验与验收
10.1.6容器要紧受压部分的焊接接头分为A、B、C、D四类。
a)圆筒部分的纵向接头(多层包扎容器层板层纵向接头除外)、球形封头与圆筒连接的环向接头、各类凸形封头中的所有拼焊接头以及嵌入式接管与壳体对接连接的接头,均属A类焊接接头。
b)壳体部分的环向接头,锥形封头小端与接管连接的接头、长颈法兰与接管连接的接头,均属B类焊接接头,但已规定为A、C、D类的焊接接头除外。
c)平盖、管板与圆筒非对接连接的接头,法兰与壳体、接管连接的接头,内封头与圆筒的搭接接头以及多层包扎容器层板层纵向接头,均属C类焊接接头。
d)接管、人孔、凸缘、补强圈等与壳体连接的接头,均属D类焊接接头,但已规定为A、B类的焊接接头除外。
10.1.7凡制造受压元件的材料应有确认标记。
在制造过程中,如原有确认标记被裁掉或材料分成几块,应于切割前完成标记的移植。
确认标记的表达方式由制造单位规定。
对有防腐蚀要求的不锈钢以及复合钢板制容器,不得在防腐蚀面采纳硬印作为材料的确认标记。
10.2冷热加工成形
10.2.1按照制造工艺确定加工裕量,以确保凸形封头和热卷筒节成形后的厚度不小于该部件的名义厚度减去钢板负偏差。
冷卷筒节投料的钢板厚度Ss不得小于其名义厚度减钢板负偏差。
制造中幸免钢板表面的机械损害。
关于尖锐伤痕以及不锈钢容器防腐蚀表面的局部伤痕、刻槽等缺陷应予修磨,修磨范畴的斜度至少为1:
3。
修磨的深度应大于该部位钢材厚度Ss的5%,且不大于2mm,否则予以补焊。
关于复合钢板的成形件,其修磨深度不得大于复层厚度的3%,且不大于1mm,否则应予补焊。
10.2.2坡口表面要求:
a)坡口表面不得有裂纹、分层、夹渣等缺陷。
b)标准抗拉强度下限值(Tb>540MPa的钢材及Cr-Mo低合金钢经火焰切割的坡口表面,应进行磁粉或渗透检测。
当无法进行磁粉或渗透检测时,应由切割工艺保证坡口质量。
c)施焊前,应清除坡口及其母材两侧表面20mm范畴内(以离坡口的边缘的距离计)的氧化物、油污、熔渣及其它有害杂质。
10.2.3封头
10.2.3.1封头各种不相交的拼接焊缝中心线间距离至少应为封头钢材厚度Ss的3倍,且不小于100mm。
封头由成形的瓣片和顶圆板拼接制成时,焊缝方向只承诺是径向的和环向的。
先拼板后成形的封头,其拼接焊缝的内表面以及阻碍成形质量的拼接焊缝的外表面,在成形前应打磨与母材齐平。
1024圆筒与壳体
10.241A、B类焊接接头对口错边量b应符合表10-1的规定。
锻焊容器A、B类焊接接头对口错边量b应不大于对口处钢材厚度Ss的1/8,且不大于5mm。
复合钢板的对口错边量b不大于钢板复层厚度的5%,且不
大于2mm。
表10-1m
m
对口处钢材厚度Ss
按焊接接头类不划分对口错边量b
A
B
w12
w1/4Ss
w1/4Ss
>12~20
w3
w1/4Ss
>20~40
w3
w5
>40~50
w3
w1/8Ss
>50
w16/1Ss,且w10
w1/8Ss,且w20
注:
球形封头与圆筒连接的环向接头以及嵌入式接管与圆筒或封头对接连接的A类接头,按B类焊接接头的对口错边量要求。
10.2.4.2棱角度
焊接接头环向形成的棱角度E,用弦长等于1/6Di,且不小于300mm的内样板或外样板检查,其E值不得大于(Ss/10+2)mm,且不大于5mm。
焊接接头轴向形成的棱角度E,用长度不小于300mm的直尺检查,其E值不得大于(Ss/10+2)mm,且不大于5mm。
10.2.4.3B类焊接接头以及圆筒与球形封头相连的A类焊接接头,当两侧钢板厚度不等时,若薄板厚度w10mm,两板厚度差超过3mm;或薄板厚度〉10mm,两板厚度差大于薄板厚度的30%,或超过5mm时,均应按大于1:
3的斜度单面或双面削薄厚板边缘,或按同样要求采纳堆焊的方法将薄板边缘焊成斜面。
当两板厚度差小于上列数值时,则对口错边量b按10.2.4.1的要求,且对口错边量b以较薄板厚度为基准确定。
在测量对口错边量b时,不应计入两板厚度的差值。
10.2.4.4除图样另又规定外,壳体直线度允差应不大于壳体长度
的1%0。
当直立容器的壳体长度超过30m时,其壳体直线度允差应符合《JB4710-92钢制塔式容器》的规定。
注:
壳体直线度检查是通过中心线的水平和垂直面,即沿圆周0°、90°、180°、270°四个部位拉©0.5mm的细钢丝测量。
测量位置离A类接头焊缝中心线(不含球形封头与圆筒连接以及嵌入式接管与壳体对接连接的接头)的距离不小于100mm。
当壳体厚
度不同时,运算直线度时应减去厚度差。
10.2.4.5筒节长度应不小于300mm。
组装时,相邻筒节A类接头焊缝中心线间外圆弧长,以及封头A类接头焊缝中心线与相邻筒节A类接头焊缝中心线间外圆弧长应大于钢材厚度的3倍,且不小于100mm。
10.2.4.6法兰面应垂直于接管或圆筒的主轴中心线。
接管法兰应保证法兰面的水平或垂直,其偏差均不得超过法兰外径的1%(法兰外径小于100mm的,按100mm运算),且不大于3mm。
法兰的螺拴孔应与壳体主轴线或铅垂线跨中布置。
有专门要求时,应在图上注明。
10.2.4.7直立容器的底座圈、底板上地脚螺拴孔应跨中均布,中心圆直径允差、相邻两孔弦长允差和任意两孔弦长允差均不大于2mm。
10.248容器内件和壳体焊接的焊缝应尽量躲开筒节间相焊及圆筒与封头相焊的焊缝。
10.249容器上凡被补强圈、支座、垫板等覆盖的焊缝,均应打磨至与母材齐平。
10.2.4.10承担内压的容器组装完成后,按要求检查壳体的圆度。
a)壳体同一断面上最大的内径与最小的内径之差e,应不大于该
断面内径Di的1%(对锻焊容器为l%o),且不大于25mm;
b)当被检断面位于开孔中心一倍开孔内径范畴内时,则该断面最大直径与最小直径之差e,应不大于该断面内径Di的1%(对锻焊容器为l%o)与开孔内径的2%之和,且不大于25mm。
10.2.7机械加工和非机械加工表面的线性尺寸的极限偏差,分不
按GB/T1804-92中的m级和c级的规定。
线性尺寸的极限偏差数值
mm
公差等级
尺寸分段
0.5~3
3~6
6~30
30~
120
120~
400
400~
1000
1000~
2000
2000~
4000
f(周密级)
±0.05
±0.05
±0.1
±0.15
±0.2
±0.3
±0.5
m(中等级)
±0.1
±0.1
±0.2
±0.3
±0.5
±0.8
±1.2
±2
c(粗糙级)
±0.2
±0.3
±0.5
±0.8
±1.2
±2
±3
±4
v(最粗级)
±0.5
±1
±1.5
±2.5
±4
±6
±8
二、《JB4710-92钢制塔式容器》摘录:
7制造、检验与验收
7.1塔器的制造、检验及验收必须符合GB150-1998,且应遵守
本章规定
7.2外形尺寸偏差应符合下表的规定:
塔器外形尺寸承诺偏差mm
序号
检验项目
允许偏差
1
圆度
按GB150-1998
2
直线度
任意3000mm长圆筒段偏差<3mm;圆筒长度L<15000mm,偏差wL/1000;L
>15000mm时,偏差w(0.5L/1000+8)。
3
上、下两封头外侧之间的距离
士1.5mm/m,且不大于士50。
4
基础环底面至塔器下封头与塔壳连接焊缝距离
1000mm裙座长,偏差w
1.5mm,且最大值为6mm。
5
接管法兰至塔器外壁及法兰倾斜度
士5mm;倾斜度w0.5°
6
接管或人孔的标咼
接管
士6mm
人孔
士12mm
7
液面计对应接口间的距离
士3mm
8
接管中心线距塔盘面的距离
士3mm
9
液面计对应接口周向偏差
1mm
10
液面计法兰面的倾斜度
0.3mm
11
液面计两接管长度差
5mm
三、《压力容器安全技术监察规程》(99版)摘录:
第24条用于制造受压元件的材料在切割(或加工)前应进行材料标记移植。
第25条压力容器的筒体、封头(端盖)、人孔盖、人孔法兰、人孔接管、膨胀节、开孔补强圈、设备法兰;球罐的球壳板;换热器的管板和换热管;M36以上的设备主螺栓及公称直径大于等于250mm的接管和管法兰均作为要紧受压元件。
第69条压力容器的组焊要求如下:
1.不宜采纳十字缝。
相邻的两筒节间的纵缝和封头拼接焊缝与相邻筒节的纵缝应错开,其焊缝中心线之间的外圆弧长一样应大于筒体厚度的3倍,且不小于100mm。
2.在压力容器上焊接的临时吊耳和拉筋的垫板等,应采纳与压力容器壳体相同或在力学性能和焊接性能方面相似的材料,并用相适应的焊材及焊接工艺进行焊接。
临时吊耳和拉筋的垫板割除后留下的焊疤必须打磨平滑,并按图样规定进行渗透检测或磁粉检测,确保表面无裂纹等缺陷。
打磨后的厚度不应小于该部位的设计厚度。
3.不承诺强力组装。
4.受压元件之间或受压元件与非受压元件组装时的定位焊,若保留成为焊缝金属的一部分,则应按受压元件的焊缝要求施焊。
第75条筒体(含球壳、多层压力容器的内筒)和封头制造的要紧操纵项目如下:
1.坡口几何形状和表面质量。
2.筒体的直线度、棱角度,纵、环焊缝对口错边量,同一断面的最大最小直径之差。
3.多层包扎压力容器的松动面积和套合压力容器套合面的间
4.封头的拼接成形和要紧尺寸偏差。
5.球壳的尺寸偏差和表面质量。
6.不等厚的筒体与封头的对接连接要求。
第105条胀接的差不多要求:
1.柔性胀接的要求:
柔性胀接分为贴胀和强度胀接。
贴胀时管板孔内可不开槽。
强度胀接管板孔内应开矩形槽,开槽宽度为(1.1~1.3)(dt)1/2(d为换热管平均直径,t为换热管壁厚),开槽深度为0.5mm。
强度胀接应达到全厚度胀接,管板壳程侧承诺不胀的最大深度为5mm。
胀
接前,应通过运算胀接压力进行试胀,试胀的试样许多于5个,测试胀接接头的拉脱力q,贴胀应达到1Mpa,强度胀接应达到4Mpa。
胀接时可通过适当增加胀接压力使其达到规定的拉脱强度。
2.机械胀接的要求:
在进行正式胀接前,应进行试胀。
试胀时,应对试样进行比较性检查,检查胀口部分是否有裂纹,胀接过渡部分是否有突变,喇叭口根部与管壁的结合状态是否良好等,然后检查管板孔与管子外壁的接触表面的印痕和啮合状况。
按照试胀结果,实际确定合理的胀管率。
四、《HG20584-1998钢制化工容器制造技术要求》摘录:
3制造用原材料
3.0.4受压元件用钢板的表面质量应符合下列各条要求。
容器制成后的钢板表面也应符合此要求。
1、钢板表面承诺存在深度不超过厚度负偏差之半的划痕、轧痕、麻点、氧化皮脱落后的粗糙等局部缺陷。
2、深度超过上款规定的缺陷,以及任何拉裂、气泡、裂纹、结疤、折叠、压入氧化皮、夹杂、焊痕、打弧弧坑、飞溅等均应予以打磨清除。
清除打磨的面积应不大于钢板面积的30%,打磨的凹坑应与母材圆滑过渡,斜度不大于1:
3。
3、打磨后,如剩余厚度不小于设计厚度,且凹坑深度小于公称厚度的5%或2mm(取小者),承诺不作补焊。
如凹坑深度较深,但剩余厚度仍满足上述要求,应与设计者协商解决。
4、超出上述界限的缺陷应考虑进行补焊。
但承诺修补的面积和深度应符合下列要求:
⑴碳素钢、16Mn之类C---Mn钢:
单个修补面积小于等于200cm2,总计面积小于600cm2或3%(取小者);
⑵低合金高强度钢和低合金铬钼钢:
单个修补面积小于等于10
0cm2,总计面积小于等于300cmm2或2%(取小者);
⑶承诺补焊的深度应不大于板厚的1/5。
4加工和成形
4.0.1受压元件用材在加工过程中,标记应予保留。
必要时,应将标记转移到工件上,并保证转移标记的正确、无误、清晰、耐久。
4.0.7不锈钢设备在加工过程中应防止表面的划伤,并应注意加工器械造成的铁污染。
曾用于碳钢件的砂轮等工具,不得用于不锈钢设备。
4.0.8壳体上垫板、加大板等应至少开设1个©10或M10的排气、讯号孔。
加大板与壳体应紧密贴合,最大间隙为3mm。
加大板所覆盖的焊缝应磨平。
4.0.11蝶形封头由顶圆板和瓣片拼接时,顶圆板应不大于0.8DN(DN为封头外径)。
5焊接和切割
5.2焊缝位置
5.2.1壳体上的开孔应尽量不安排在焊缝及邻近区域,但符合下列情形之一者,承诺在上述区域开孔:
1.符合GB150开孔补强要求的开孔可在焊缝区域开孔。
2.符合GB150规定的承诺不另行补强的开孔,可在环焊缝区域开孔。
但现在应以开孔中心为圆心,对直径为3倍开孔直径长度的圆所包括的焊缝进行100%射线或超声波探伤,并符合要求。
凡因开孔而可予去除的焊缝可不受探伤质量的阻碍。
3.符合GB150规定的承诺不另行补强的开孔,当壳体板厚小于等于40mm时,开孔边缘距主焊缝的边缘应大于等于13mm。
但若按5.2.1条第一款对主焊缝进行射线或超声波探伤并符合要求者,可不受此限。
5.2.2外部附件与壳体的连接焊缝,如与壳体主焊缝交叉时,应在附件上开一槽口,以使连接焊缝跨过主焊缝。
槽口的宽度应足以使连接焊缝与主焊缝边缘的距离在1.5倍壳体壁厚以上。
五、《GB151-1999管壳式换热器》摘录:
6制造、检验与验收
6.2管箱、壳体、头盖
6.2.1圆筒内直径承诺偏差
6.2.1.1用板材卷制时,内直径承诺偏差可通过外圆周长加以操纵,其外圆周长承诺上偏差为10mm;下偏差为零。
6.2.1.2用钢管作圆筒时,其尺寸承诺偏差应符合GB/T8163或
GB/T14976的规定。
在遵循442规定时,附录C的奥氏体不锈钢焊接钢管也可用作圆筒。
6.2.2圆筒同一断面上,最大直径与最小直径之差为e<0.5%DN,且:
当DN<1200mm时,其值不大于5mm;
DN>1200mm时,其值不大于7mm。
6.2.3圆筒直线度承诺偏差为L/1000(L为圆筒总长),且:
当L<6000mm时,其值不大于4.5mm;
L>6000mm时,其值不大于8mm。
直线度检查,应通过中心线的水平和垂直面。
即沿圆周0°、9
0°、180°、270°四个部位测量。
6.2.4壳体内壁凡有碍管束穿入或抽出的焊缝均应磨至与母材表面齐平。
6.2.5在壳体上设置接管或其他附件而导致壳体变形较大,阻碍管束顺利穿入时,应采取防止变形措施。
6.2.6插入式接管、管接头等,除图样另有规定外,不应伸出管箱、壳体和头盖的内表面。
6.3换热管
6.3.1碳素钢、低合金钢换热管管端外表面应除锈,铝、铜、钛及其合金换热管管端应清除表面附着物及氧化层。
用于焊接时,管端清理长度应不小于管外径,且不小于25mm;用于胀接时,管端应出现金属光泽,其长度应不小于二倍的管板厚度。
632用于胀接的换热管,其硬度应满足5.822的要求,如不能满足时,制造单位应采取措施予以保证。
633换热管拼接时,应符合以下要求:
a)对接接头应作焊接工艺评定。
试件的数量、尺寸、试验方法按JB4708的规定;铝、铜、钛焊接接头可参照执行;
b)同一根换热管的对接焊缝。
直管不得超过一条;U形管不得超过二条;最短管长不应小于300mm;包括至少50mm直管段的U形管段范畴内不得有拼接焊缝;
c)管端坡口应采纳机械方法加工,焊前应清洗洁净;
d)对口错边量应不超过换热管壁厚的15%,且不大于0.5mm;直线度偏差以不阻碍顺利穿管为限;
e)对接后,应按下表选取钢球直径对焊接接头进行通球检查,以
钢球通过为合格:
换热管外径d
d<25
25vd<40
d>40
钢球直径
0.75di
0.8di
0.85di
注:
di---换热管内径。
f)对接接头应进行射线检测,抽查数量应许多于接头总数的10%,且许多于1条,以JB4730-94的III级为合格;若有一条不合格时,应加倍抽查;再显现不合格时,应100%检测;
g)对接后的换热管,应逐根进行液压实验,试验压力为设计压力的2倍。
6.3.4U形管的弯制
6.3.4.1U形管弯管段的圆度偏差,应不大于换热管名义外径的10%;但弯曲半径小于2.5倍换热管名义外径的U形弯管段可按15%验收。
6.3.4.2U形管不宜热弯。
6.3.4.3当有耐应力腐蚀要求时,冷弯U形管的弯管段及至少包括150mm的直管段应进行热处理。
碳钢、低合金钢钢管进行排除应力热处理;奥氏体不锈钢管可按供需双方商定的方法进行热处理。
6.3.4.4有色金属管一样不作排除应力热处理。
确有需要时,可按供需双方协商的方法及要求进行排除应力热处理。
6.4管板
6.4.1拼接管板的对接接头应进行100%射线或超声检测,按JB4730-94射线检测不低于II级,或超声检测中的I级为合格。
6.4.2除不锈钢外,拼接后管板应作排除应力热处理。
6.4.6管孔表面粗糙度
a)当换热管与管板焊接连接时,管孔表面粗糙度Ra值不大于25[1m;
b)当换热管与管板胀接连接时,管孔表面粗糙度Ra值不大于12.51m;
6.4.7胀接连接时,管孔表面不应有阻碍胀接紧密性的缺陷,如贯穿的纵向或螺旋状刻痕等。
6.4.8隔板槽密封面应与环形密封面平齐,或略低于环形密封面(操纵在0.5mm以内)。
6.5换热管与管板的连接
6.5.2胀接连接时,其胀接长度不应伸出管板背面(壳程侧),换热管的胀接部分与非胀接部分应圆滑过渡,不应有急剧的棱角。
6.6折流板、支持板
6.6.1折流板、支持板的管孔直径及允差按5.9.3的规定,但承诺超差0.1mm的管孔数不得超过4%。
662折流板、支持板外圆表面粗糙度Ra值不大于25卩m,外圆两侧的尖角应倒钝。
6.6.3应去除折流板、支持板上的任何毛刺。
6.7管束的组装
a)拉杆上的螺母应拧紧,以免在装入或抽出管束时,因折流板窜动而损害换热管;
b)穿管时不应强行敲打,换热管表面不应显现凹瘪或划伤;
c)除换热管与管板间以焊接连接外,其他任何零件均不准与换热管相焊。
6.8管箱、浮头盖的热处理
a)碳钢、低合金钢制的焊有分程隔板的管箱和浮头盖以及管箱的侧向开孔超过1/3圆筒内径的管箱,在施焊后作排除应力热处理,设备法兰密封面在热处理后加工。
b)除图样另有规定外,奥氏体不锈钢制管箱、浮头盖可不进行热处理。
6.11换热器的密封面应予爱护,不得因磕碰划伤、电弧损害、焊瘤、飞溅等而损坏密封面。
6.13补强圈的信号孔,应在压力试验前通入0.4~0.5Mpa的压缩
空气检查焊接接头质量
6.14重叠换热器须在制造单位进行重叠预组装。
重叠支座间的调整板应在压力试验合格后点焊于下台换热器的重叠支座上,并在重叠支座和调整板的外侧标有永久性标记,以备现场组装对中。
6.15换热器的组装
6.15.1换热器零、部件在组装前应认真检查和清扫,不应留有焊疤、焊接飞溅物、浮锈及其他杂物等。
6.15.2吊装管束时,应防止管束变形和损害换热管。
六、《JB/T4736-95补强圈》摘录:
5技术要求
5.1补强圈厚度按GB150有关要求运算决定,并按标准表1选取。
5.2补强圈与壳体、接管的连接焊缝应按照设计条件,结构要求,参考标准附录A,按表A1选用或自行设计。
用于低温压力容器的连接焊缝必须采纳全焊透结构。
5.3补强圈的材料一样与壳体材料相同,并应符合相应材料标准的规定。
补强圈应用整板制造,不得拼接。
5.4补强圈的形状应与补强部分壳体相符,并与壳体紧密贴合。
5.5安装补强圈时,应注意使螺孔位置在壳体的最低的位置。
5.6补强圈与壳体、接管的焊接,应采纳与壳体焊接相同的焊条与焊接工艺进行施焊。
施焊前应清除坡口内的铁锈、焊渣、油污、水气等赃物。
5.7补强圈焊接后,应对补强圈的角焊缝进行检查,不得有裂纹、气孔、夹渣等缺陷;必要时应作磁粉或着色检查。
焊缝的成形应圆滑过渡或打磨至圆滑过渡。
5.8由M10螺孔通入0.4~0.5MPa压缩空气,检查补强圈焊接质量,角焊缝不得有渗漏现象。
七、《JB/T4729-94旋压封头》摘录:
5制造技术要求
5.1材料
5.1.1用以制造封头的钢板应有材质证明,封头材料应符合GB150的有关规定和图样要求。
5.1.2封头材料不承诺存在裂纹、气泡、结疤、折叠、夹杂和分层等缺陷。
5.2制造
5.2.1坯料制备
5.2.1.1封头坯料宜采纳整板。
如需拼接,宜取同一炉批号板料。
并尽可能选用同一张板料。
5.2.1.2板料拼接时,其最外一条焊缝距板中心距离a<0.4Di,
且最小板宽b不得小于300mm。
5.2.1.3拼板组装的对口错边量不得大于坯料厚度的8%,且不大
于1.5mm。
5.2.1.4拼接焊缝的焊接及质量要求按GB150的有关规定。
拼接焊缝余高应打磨至与母材齐平。
521.5坯料割圆后,应将周边修磨圆滑,端面不得有裂纹、气泡、夹杂和分层等缺陷。
522成形
封头应采纳冷旋压一步法或二步法成形。
注:
通过一次旋压成形的方法称一步法,而通过压鼓、翻边两道工序成形的方法称二步法。
5.2.3冷成形后热处理
封头冷成形后应进行热处理。
当制造单位确保冷旋压成形后,材料性能符合设计、使用要求时,则不受此限。
除图样另有规定外,奥氏体不锈钢封头可不进行热处理。
5.2.4齐边及切坡口
5.2.4.1对碳钢及低合金钢制的封头,可采纳机械或气割方法进行齐边和切坡口;对不锈钢制封头应采纳机械或等离子切割方法进行齐边和切坡口。
5.242坡口型式按图样或定货合同的规定。
5.3尺寸及形状偏差
5.3.1内直径允差
封头内直径允差承诺通过外圆周长加以操纵,其外圆周长允差
按下表规定。
单位:
mm
名义厚度3n
内直径Di
外圆周长允差
3300WDiW2000
士93
2000+12士6
12800WDiW2000
士12士3
2000士9士6
4000