PVC管材生产中常见问题及解决办法.docx
《PVC管材生产中常见问题及解决办法.docx》由会员分享,可在线阅读,更多相关《PVC管材生产中常见问题及解决办法.docx(21页珍藏版)》请在冰豆网上搜索。
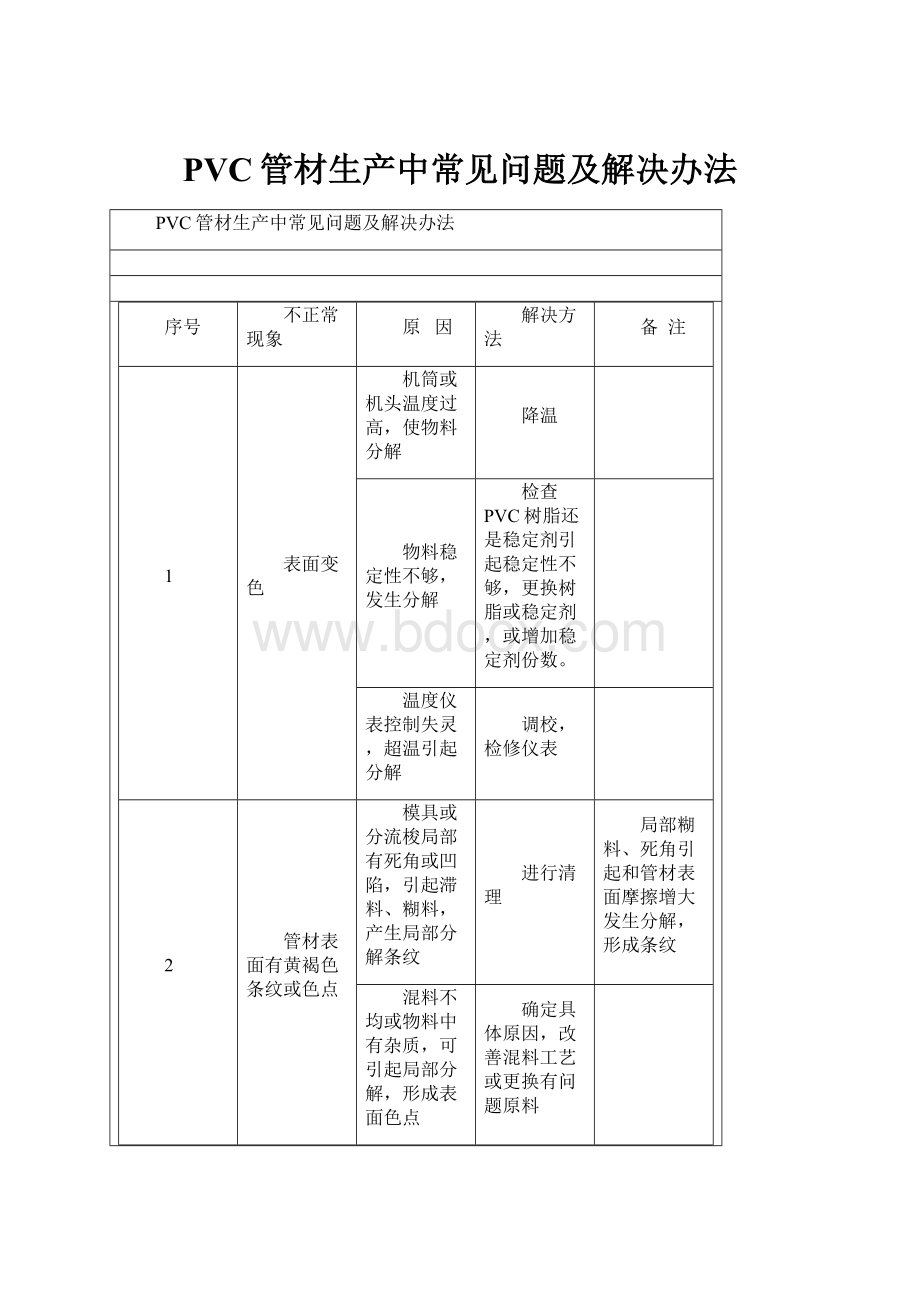
PVC管材生产中常见问题及解决办法
PVC管材生产中常见问题及解决办法
序号
不正常现象
原 因
解决方法
备 注
1
表面变色
机筒或机头温度过高,使物料分解
降温
物料稳定性不够,发生分解
检查PVC树脂还是稳定剂引起稳定性不够,更换树脂或稳定剂,或增加稳定剂份数。
温度仪表控制失灵,超温引起分解
调校,检修仪表
2
管材表面有黄褐色条纹或色点
模具或分流梭局部有死角或凹陷,引起滞料、糊料,产生局部分解条纹
进行清理
局部糊料、死角引起和管材表面摩擦增大发生分解,形成条纹
混料不均或物料中有杂质,可引起局部分解,形成表面色点
确定具体原因,改善混料工艺或更换有问题原料
3
外表无光泽
口模温度低
提高口模温度、增加ACR用量以提高剪切
光亮型ACR加工助剂即使在较低温度下仍可显著改善表面光洁度
剪切速率太大,熔体破裂
适当提高料温、提高ACR用量或降低牵引速度
口模温度过高或内表面光洁度差
降温,降低粗糙度
塑化不良
提温、增加加工助剂
外润滑剂含量过低
在保证物料塑化的前提下,适当增加外润滑剂
外滑剂过少,使物料易粘结模具金属表面,影响表面光泽
CaCO3的粒度过大或粒径分布过宽
更换适用的碳酸钙
4
管材表面起皱纹
口模四周温度不均匀
检查加热圈
冷却不良
开大冷却水或降低却水温度
牵引太慢
加快牵引
料内有杂质
调换原料
芯模温度太低
提高芯模温度
机身温度过低
提高机身温度
牵引速度太快
减速
5
内壁毛糙
芯模温度太低
提高模芯温度或增加工助剂
温度低造成塑化不良,内壁在模头处难以升温,故产生毛糙现象
机筒温度过低,塑化不良
提高温度
提温会使后段温度难以控制时,可增加ACR加工助剂,而不提温,能得到相同效果
螺杆温度太高
加强螺杆冷却
6
管壁起泡
料过潮
干燥
机筒二段后真空排气孔处真空度过低或堵塞
检查泵工作状况,管路有无堵塞(抽粉子引起)
有分解(机头温度过高)
降低温度
7
管壁厚度不均匀
口模、芯棒不同心
调模
机头温度不均,出料有快慢
检查加热圈,检查螺杆有无脉动现象
牵引速度不稳
检查维修牵引机
真空槽真空度有波动
检查真空泵及其管路
8
内壁凹凸不平
螺杆温度过高
降螺杆温度
螺杆转速过快,引起融体破裂
降螺杆转速
9
管材弯曲
管壁厚度不均
同7
机头四周温度不均
检查电热圈
机身、定径槽、牵引不在一条轴线上
调节至一条轴线上
冷却槽两端孔不在一条直线上
调节至一条轴线上
冷却槽喷头出水不均匀
调节、更换喷头
10
断面有气泡
物料水份高
干燥或换喷头
混料温度低,水份未排出
提高混料温度
排气孔真空度低或管道堵塞
检查真空泵及其管路
机身或模头温度过高
降低温度
混配料热稳定性差
检查修改配方
11
管材冲击强度不全合格
加工温度低
提高加工温度或增加ACR加工助剂
原铺料质量差
更换原料
背压低
改变工艺条件
如因模具引起背压低,不能通过工艺调节时,只能修模
配方不良
改进配方
加工温度高(塑化,过度或有分解)
降低温度
使用CPE抗冲改性时,螺杆转速太快,剪切率过高使CPE分散不均,呈堆集状态,搞抗冲作用下降
降低螺杆转速
降低螺杆转速会使产能下降,改用ACR作为抗冲改性剂最佳解决办法,ACR对温度高低、剪切速率大小均有良好的适应性
冷却水温度过低(多生在冬天),因骤冷产生过大内应力
调节冷却水温度
排气不良,使管材产生气孔
调节排气孔真空度,有堵塞时予以消除
缺陷性粒子,在管壁中形成微裂纹,使管材抗冲强度下降
缺陷性粒子可能来自杂质,团聚的CaCO3、滑剂、未塑化的PVC颗粒等,根据具体原因采取对措施,如将干混料过筛
缺陷性粒子是指颗粒较大,影响材料强度的颗粒.缺陷性粒子同样会使管材液压试验不合格
12
管材液压试验不合适
塑化不良,拉伸强度降低
提高或增加工加工助剂份数
PVC树脂质量不好,聚合度低或分子量分布过宽,或分子结构有缺陷
更换PVC
改性剂抗拉强度低,从而降低了管材的抗拉强度
更换较高抗拉强度的抗冲改性剂,ACR和CPE来说,对管材抗拉强度影响要小得多
11条中诸因素,同样会引起管材抗拉强度低,使液压试验不合格
13
二氯甲烷浸渍试验不合格
塑化不良
提高加工温度或增加ACR加工助剂
对碳酸钙、炭黑等填充组份高的配方,仅靠提高加工温度来提高塑化度往往是难以凑效的,此时需要增加ACR加工助剂
14
纵向回缩率不合格
配方中弹性橡胶体等高回缩率物质组份过高,如CPE
更换配方中的回缩率过高的组份
挤出速度与索引速度不匹配,牵引速度过快
降低牵引速度
冷却不良
降低冷却水温度或加大冷却水量
机头温度过高
降低温度
PVC型材生产中常见问题及解决办法
序号
不正常现象
原因
解决办法
备注
1
型材弯曲或翘曲
定型材模具、牵引机与机头不在一条直线上
调整定型模具、牵引机的位置
机头出料不均匀
调节或修整模具
冷却不均匀,产生内应力
调整冷却水量或冷却水发布
口模温度不均匀,产生内应力
调整温度
挤出速度过快,使型材冷却不良
降低挤出速度
2
型材表面不平
牵引速度过快,型材在定型模中不能贴壁
降低牵引速度
真空定型模真空度小
检查是否有漏气或真空泵系统有无堵塞
定型模离机头距离过大
调节定型模与机头之间的距离
定型模位置偏高可偏低
调整定型模上下位置
冷却不好
加强冷却效果
3
型材表面有划伤
口模内有异物
清理机头
定型模表面有水垢或真空槽内有异物
清理定型模
4
型材断面有气泡
加工温度过高,物料分解产生气体
降低加工温度
料筒冷却装置失灵
检查料筒冷却装置在超过设定温度时,是否起冷却作用
国产挤出机一般均采用风冷,风扇有时会失灵
原料中挥发物太多
调整配方
抽真空系统出故障
检查真空系统工作是否正常,管道有无堵塞
配方中新更换的某种原料不合适
更换有问题原料
混料温度低,水份和挥发物得不到排除
提高混料温度
5
型材表面粗糙,光泽差,有云状现象
口模内壁不光滑,沾有析出物
清理口模
物料混合不均匀
检查混料机搅拌浆,混料时间是否正常,采取相应措施
定型模真空度不够,型材贴模不紧
提高真空度
温度太低,塑化不良
提温或增加ACR加工助剂
光亮型加工ACR更为有效
挤出速度过快,塑化不良
降速
6
口模内发生分解,型材表面出现分解黄线
出现黄线的原因是因为局部发生分解,以下原因:
1.模头流道局部抛光不好,存在滞料
对模具粗糙处进行抛头
2.模具中有死角
修模
7
型材有明显的熔结线
温度太低,塑化不良
提高温度或增加加工助剂份数
挤出速度快,物料塑化不良
降低螺杆转速
熔结部位原料分解
清理机头
配方不全格(滑剂过量或滑剂性能不好,易析出等)
调节配方
模具设计或结构不良
增加机头定型长度
8
型材尺寸不稳定
温度波动大
稳定温度
挤出速度或牵引速度不稳定
稳定挤出速度或牵引速度
物料混合不均匀(高混机搅拌浆磨损或工艺条件变化)
根据具体原因采取措施,确保物料混合均匀
冷却定型模具尺寸不当或冷却效率不高
修整模具或调整冷却工艺
配方中润滑剂过量,背压低
调整配方,减少滑剂用量
定型模真空度低,型材不能贴壁
调节真空度
定型模处阻力不平衡,产生内应力
调节口模出量料,使各部分挤出速度尽量一致
冷却不均匀
调节冷却水或改进定型模冷却系统
供料不稳定,可能因料斗架桥、加料螺旋沾料等原因引起
查找供料不稳的原因,采取相应措施
9
型材收缩率高
冷却不好
增强冷却效果
牵引速度过快
降低牵引速度
机头温度过高
降低机头温度
配方中收缩率较高的组份过高
更换配方中收缩率大的部份,用添加份数少或收缩率较低的助剂代替
例如用ACR取代CPE
10
型材加强筋变形
冷却效果不好
增强冷却效果
牵引速度过快或过慢
调节牵引速度
定型模与机头间距离不适当
调节定型模与机头之间的距离
牵引机履带夹紧力过大
调节夹紧力
真空度太小或真空波动
调节或稳定定型模的真空压力
11
型材强度降低(冲击强度、弯曲弹性模量)
塑化不良(温度低或加工助剂不够,配方中填料组份高)
提高温度,或增加加工助剂量,降低配方中CaCO3含量
主要影响冲击强度
配方不合理
调节配方
物料混合不均匀或预塑化不良
改善高混机性能或工艺
挤出温度过高(引起过塑化或物料分解)
降低温度
熔体压力低
调节配方(例如增加大分子量加工助于提高熔体压力),改进模具,降低模具温度
抗冲剂选择不当(例如填写CPE份数多时会引起弹性模量大幅度下降,填加量少时抗冲强度下降)
改换抗冲性剂,例如改用抗冲ACR
ACR填加份数比CPE少,即可达到同样抗冲效果,但对弹性模量影响较小
牵引速度过快,产生分子链趋向性
降低牵引速度
冷却太快
定型要缓冷,不能骤冷
骤冷引起型材内应力,降低强度
12
可焊性不良
润滑剂过量或熔点过低,易析出,使焊缝强度下降
调节润滑剂含量或更换润滑剂
配方中有对焊缝强度影响大的组份
调节配方
焊接工艺不良
焊接时的加热时间、加热温度、对接压力等工艺条件均对焊缝强度产生影响,试验、调节到适宜的焊接工艺条件
13
型材焊角强度试验时,在焊缝以外型材断裂
型材断面和结构不合理
改进模具
型材强度不够
根据地1条,查找影响强度的原因
pvc管材变色问题
2010-08-0817:
53
型材在加工时就发现色泽不统一(如色泽有轻微偏差是允许的);
(2)加热变形后型材明显黄变;
(3)加热后状态良好,但型材制成门窗时间不长就变灰。
型材正常生产中不发黄,而在后来的成窗制品时发黄。
在型材生产过程中,当原料及模具等基本条件无变化时,如果将其塑化段及均化段的温度提高5℃左右,所产生的型材发生黄变倾向,也说明其热稳定效率不足,应增加热稳定剂的加入量,尤其是配方中加入荧光增白剂等增白助剂时,热稳定剂不足,增白效果不明显。
PVC分子结构与颜色的关系
(1)因PVC树脂是一种热敏性塑料,其光稳定性较差,在热和光的作用下,支链发生脱HCI反应、多烯结构分子,当主链出现共扼双键数量不太多时产生微量色差,氯化氢首先会与周围潜在的对酸活性的物质发生反应,而共扼双键成为PVC分子链内新的活性位置,被光引发成大分子游离基后,PVC就容易遭受氧化,产生色变。
(2)PVC树脂中存在一定数量偏低低分子量组分,降低了聚合物的热稳定性,PVC分解的机理有游离基机理、离子机理、单分子机理等,PVC分解除稳定剂外还有可能受到PVC树脂本身质量的影响,如PVC树脂内是否存有残留过多的引发剂。
(3)聚合物中如存在某种杂质,例如在聚合过程中加人的引发剂、催化剂、酸、碱等去除不尽,或在储运过程中吸收水分,都会降低聚合物的稳定性。
因为这些物质能引起分子-离子降解反应,CPE中含有较多Cl2、HCl等低分子物,易加速树脂热分解。
因此对稳定不好的PVC+CPE体系,通过增加稳定剂用量也可消除一些型材泛黄问题。
(4)硬PVC结构型材,它是由PVC作连续相的多相聚合物与混合物捏合热稳定剂、光稳定剂润滑剂、填充剂与颜料构成的混合体系,当PVC异型材曝露在自然环境时,一旦PVC组分脱氯化氢后,碳酸钙原组分会转化成氯化钙新组分,它分散在氧化降解物层内,并形成潜在的吸水位置,这是户外型材发黄的原因之一。
(5)除了温度还有应力,塑料在成型之前,在高搅、冷搅、挤出等过程中,受到剪切应力和拉伸应力的作用而引起热降解。
解决色差时,单一的方法并不能较理想处理问题,如从以下4个方面全盘考虑,解决起来更快捷些:
(1)降低加工温度比不降低加工温度色泽变白些;
(2)在复合稳定剂中单纯加单铅盐效果不比增加复合稳定剂效果好;
(3)单纯加稳定剂又不如既选用部分稳定剂,又选用增白母料或高白度填料、增加钛白粉效果快;
(4)单纯加钛白粉再适度增加一些内润滑剂效果更佳。
一般认为低分子物质对聚合物有增塑作用,机理之一是大分子与小分子之间的相互作用代替大分子之间的相互作用,从而使大分子链段运动容易得多。
上述措施会从不同程度上阻止PVC分解,减少型材加工中色泽不一致现象,笔者认为最有效途径是从稳定体系优化设计,从根本上抑制PVC共扼多稀发色结构。
生产实践中用自制的紫外灯管对型材进行紫外老化12小时,有明显颜色变化。
及时对产品进行自然气候暴露老化试验无疑是必要的,以便从小料方面筛选出具有优良耐候性的配方。
铅硫污染变色据报道:
“PVC型材在室外经雨淋和强阳光照射后,型材局部表面发生变色,有的是同一窗上有一根型材上在残存雨点的地方变色程度更厉害,表面色泽呈淡灰色或浅灰色”。
除其他原因外,群青作为淡青色作色剂分散下均是其原因之一,群青一一硅酸铝的含硫复合物,耐碱不耐酸,在PVC型材中使用量过大或大量积聚,从理论上讲,与含硫化合物作用可能生成黑色的硫化铅,变色的现象已在不少型材门窗厂出现,这是使用铅盐系列稳定剂同时加入较低质量钛白粉和群青的型材厂值得注意的问题。
也有厂家报告与橡胶密封条接触的型材亦有明显变色,且变色向周围扩延,除劣质密封条中含有易析出的机油类材料等,其另外原因有橡胶密封条中残存的硫与铅作用生成硫化铅的结果。
填料对PVC管材生产的影响及解决方案
作者:
新疆屯河节水科技有限公司王建国
填料虽然只占PVC管材配方的很小一部分,但对提高PVC管材的性能和质量发挥着重要的作用,而且会对PVC管材生产的各个环节产生很大的影响。
因此,填料增加后应及时调整润滑体系予以平衡,否则会对PVC管材的生产造成极大的破坏作用。
填料又称填充剂,是一类添加到塑料中能增加体积、降低制品成本的物质。
填料不但降低了塑料制品的生产成本,提高了树脂的利用率,同时也扩大了树脂的应用范围,而且一些填料的应用还可赋予或提高管制品某些特定的性能,如尺寸稳定性、阻燃性、电气绝缘性、防粘性、不透明性和刚性。
有些填料还能提高管材的拉伸强度和冲击强度。
本文以采用了碳酸钙填料的、用于110规格管材的0#~4#配方(各配方的配比情况如表中所示)为例,通过6项测试实验来讨论在管材生产过程中填料是如何影响PVC管材生产的,并就其中出现的各种问题提出了相应的解决方案。
填料对PVC管材生产的影响
1、混料工艺
在PVC管材配方中增加填料后,首先会对混料电流造成较大影响。
如图1所示,在混料初期,0#~4#配方样品中的混料电流值差较小。
在55℃~65℃之间,各配方的电流值差为5A,当混料温度上升至65℃~75℃时,混料电流值差只有2~3A。
这是由于在此温度范围内,配方中的外润滑剂开始溶解,发挥润滑作用,从而使电流保持在一定范围内。
随着混料温度不断升高,混料电流呈现较大的差异,且填料含量越高,混料电流相对越低。
这表明填料比例增加后,由于润滑剂的润滑作用,使其具有较低的切导热系数,从而极大地降低了物料与混料机桨叶之间的摩擦热,并同时降低了马达的负载,导致混料电流呈下降趋势。
图1填料对混料电流的影响
如图2所示,随着填料含量的增加,混料时间呈上升趋势。
增加1倍的填料,混料时间可延长22%左右。
这也与混料电流下降相对应,当电流值为67~76A时,混料电流处于一个较低的曲线,而增加改质剂后,降低了物料混合过程中的摩擦热,同时由于高混锅排料温度的升高,延长了混料时间,从而为配方中各组分提供了充分的混合时间,显著提高了PVC树脂的包覆效果和干混料的混合均匀性。
图2填料对混料时间的影响
图3所示为填料的增加对干混料表观密度的影响示意图。
从图中可以看出,填料的增加对表观密度的影响很小,只有1%左右。
这是由于填料的流动性比较好,尤其是在高温时流动性能更好,所以在混料过程中由于CaCO3的加入降低了PVC颗粒之间、PVC颗粒与机械表面之间的摩擦,从而使得物料的总摩擦力减少,而且CaCO3的加入量越多,现象越明显。
图3填料对干混料表观密度的影响
总之,填料的增加会大大降低混料工序的效率,但不会对干混料的质量造成较大影响。
2、管材的加工性能
有研究表明,填料的含量对管材的加工性能影响显著。
当填料含量较低时,由于填料分散于PVC粒子之间,妨碍了PVC粒子的熔融,从而减缓了物料的塑化速度,延长了塑化时间,但可有效提高PVC管材的刚性。
填料加量过多则会提高物料的粘性,平衡转矩也会随之升高。
研究发现,在实际的应用过程中,在不改变挤出成型模具的情况下增加填料,管材的外径出现了偏大的问题,并同时伴随着壁厚尺寸出现误差等问题。
这是因为填料颗粒的加入限制了PVC分子链的旋转和移动功能,因而对那些与PVC分子链有关的材料性能均有影响。
提高材料的模量会降低离模膨胀率和热收缩率,这样处于高温下的管坯在进入真空定径装置冷却定型的过程中,收缩比例减小,从而导致管坯的壁厚有所减小,出现壁厚达不到原有标准,甚至低于标准下限的现象。
图4填料对扭矩和熔体压力的影响
3、管材挤出设备
填料含量的增加对挤出工艺的要求大为不同。
随着填料含量的增加,在挤出过程中物料的扭矩值增大,导致在原有的挤出工艺条件下管材生产出现过塑化问题,且管材的挤出量随之下降,造成产量的降低。
如图4所示,在相同的挤出工艺条件下,随着填料含量的增加,扭矩值和熔体压力呈逐步上升趋势。
随着填料含量的增加,螺杆中物料的密度也随之增大,使得物料在挤压、剪切过程中的摩擦力增加,摩擦热因此急剧增加,从而导致螺杆、机筒4区(均化挤出段)的温度远远超出设定温度(如图5所示),而此时设备自身的冷却系统已达到满负荷状态,无法使该区温度继续下降,通常会高出设定温度15℃~25℃。
这时若要缓解物料的过塑化问题,必须将实际温度降低至130℃以下,而在如此低的温度下生产管材,由于物料对螺杆磨损以及扭矩的上升对设备的安全运行极为不利,而且此时物料塑化所需的热能需要大量的机械能来转换,这样长时间的挤出运转势必会加剧螺杆及设备传动系统的损坏。
图5填料对挤出工艺控制方面(工艺温度)的影响
另一方面是填料本身对管材挤出设备的磨损。
一般,各矿物性填料的莫氏硬度为~3,即便是硬度低于钢材的填料,其尖角也会对设备有影响。
从机筒抽真空处观察到的塑化情况与螺杆扭矩曲线上表现出的塑化情况对比发现,粒径大小以及粒径分布均匀程度直接影响混料的塑化时间和螺杆扭矩的变化,甚至颗粒大小、分布和形状相同的填料,若硬度较高,对料筒、螺杆、混料机桨叶,甚至是模具都会有较大的磨损。
综上所述,在实际生产过程中,填料增加后的情况:
试样0#~4#的液压实验时间从23min~60min不等。
试样0#~3#主要是剪切热大,物料有过塑化现象,均出现了韧性变形:
试样0#的液压时间为23min,此时物料并未出现塑化过度的现象,但存在螺槽中物料填充不足的现象;试样1#降低了主机速度,由于塑化效果不充分,出现了脆爆现象;试样2#的机身2区和机头2区温度比1#高5℃,虽进一步改善了塑化效果,大大延长了液压实验时间,但仍然达不到国标要求。
这4次工艺调整使得物料的塑化状态逐渐由条状转变为絮状,扭矩值和熔体压力也逐渐恢复到原有水平,液压实验逐渐好转,但仍然达不到质量标准要求。
这样我们对试样4#的滑剂种类进行了调整,适当的增加了内润滑剂的比例,对比发现该试样有效提高了填料的分散性,改善了塑化效果,而且所获得的混料电流值最高,液压实验性能最好。
图6液压实验对比图
解决方案
一般,可以通过提高管材的挤出速度和增加模具压缩段的压力来提高离模膨胀率,从而使管材的壁厚达到标准范围。
通过降低真空箱的真空度可以将管材的外径维持在标准的范围内,如果仍无法达到预期的目的,那么就必须通过更换定型模具来解决该问题。
在实际生产过程中,可以通过降低管材的挤出速度或喂料量来缓解高扭矩和高摩擦热的问题,但随之而来的是设备产能的下降和单位管材能耗的增加,不利于管材稳定高效的生产。
在增加填料的同时,应尽可能地将扭矩值和熔体压力保持在原有水平:
一方面,可适当调整工艺温度。
但这通常要降低机身温度,适当提高模具以及合流芯的温度,以减少物料在机身部分的受热程度,缓解过塑化问题。
另一方面,要改进管材生产的整个生产流程源头,即调整配方组份。
调整配方组份其实主要是指调整配方中的润滑体系,使其最终达到润滑平衡的状态。
在生产PVC硬管时,所需的热量来自管材挤出机的外部加热和物料与物料、物料与螺杆和料筒之间的剪切摩擦,后者是主要的供热源。
由于混料在加工时受到一定的剪切力会产生大量的剪切热,这就要求混料配方具有控制塑化速率及熔体粘度的特性。
虽然润滑剂对混料的影响不大,但润滑剂可调节物料分子之间的作用力和物料与机械表面的摩擦力,其中内润滑剂能促进塑化并降低塑化扭矩,而外润滑剂可延迟塑化并防止树脂熔体粘附在加工设备的金属表面。
可通过调整内外润滑剂的比例来调控树脂混合物的塑化时间,以满足特定加工设备及工艺所要求的塑化速率。
表各配方的配比情况
在管材生产的过程控制中,需要结合干混料的性能检测结果对配方中的润滑体系进行调配。
调配主要以硬脂酸、石蜡和改质剂为主,保证混料电流值趋于偏中下水平,混料时间必须达到8min以上,表观密度达到。
在工艺调试过程中,并不调整工艺温度,而是增加喂料量,提高物料的剪切、混炼效果,从而增加管材的密实度,改善液压实验性能。
随着挤出工艺温度控制逐步下降,接下来应尽可能下调工艺温度,包括机头温度的控制。
若调试过程中管材挤出速度变大,出现韧性变形的次数越频繁,说明调整不适宜,干混料的加工性能欠缺。
如果加工设备的剪切力过大,生成的摩擦热过多,在加工较易分解的树脂时就必须降低加工温度,以避免树脂内部局部过热而造成热分解。
由于树脂都是热的不良导体,单靠降低加热温度来调节很有限,最可靠的方法是降低树脂粘度,从根本上减少摩擦热。
这时,可适当地按比例增加内、外润滑剂用量来降低树脂的熔体粘度,使润滑体系能适应特定的加工设备及工艺的要求。
反之,加工设备的剪切力较小,则应适当减少内、外润滑剂的用量。
(end)