故障检测.docx
《故障检测.docx》由会员分享,可在线阅读,更多相关《故障检测.docx(17页珍藏版)》请在冰豆网上搜索。
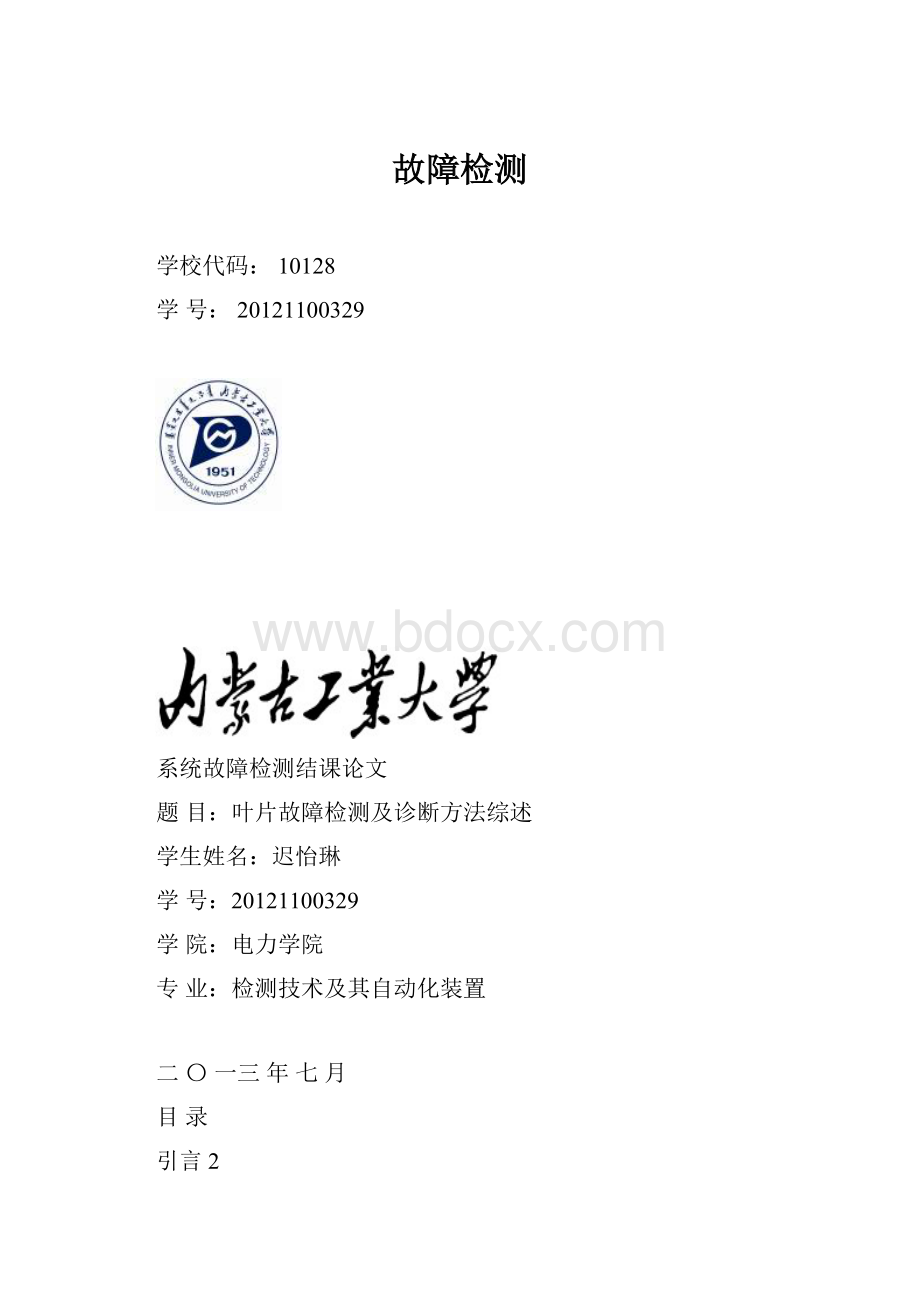
故障检测
学校代码:
10128
学号:
20121100329
系统故障检测结课论文
题目:
叶片故障检测及诊断方法综述
学生姓名:
迟怡琳
学号:
20121100329
学院:
电力学院
专业:
检测技术及其自动化装置
二〇一三年七月
目录
引言2
1风力机叶片损伤监测技术发展现状2
1.1国外发展现状2
1.2国内发展现状3
2.风力机叶片损伤机理以及识别方法4
2.1造成风力机叶片损伤的原因4
2.1.1运输、安装过程造成的损伤4
2.1.2自然环境造成的损伤5
2.1.3运行过程中造成的损伤5
2.2叶片常见的损伤类型5
2.2.1表面磨损5
2.2.2表面剥蚀与脱落5
2.2.3材料碳化6
2.2.4材料脆化7
2.2.5裂纹与开裂7
2.3叶片损伤产生的机理8
2.3.1砂眼产生的机理8
2.3.2裂纹产生的机理8
2.3.3雷击造成损伤的机理8
2.4叶片损伤识别的常用方法9
2.4.1声发射检测技术9
2.4.2超声波检测技术9
2.4.3红外热成像检测技术9
2.4.4振动检测技术9
2.4.5模糊理论检测技术10
2.4.5传感器检测技术11
2.5本章小结11
3研究展望11
参考文献13
摘要
叶片是风力发电机组的关键部件,承担将风的动能转换为风力机转子旋转机械能的任务。
叶片工作的安全可靠性和能量转换效率对整个风力机组有着十分重要的影响。
随着风力发电机组装机容量的不断增大,叶片故障对风力机组安全运行构成很大威胁,所以对叶片进行状态监测非常重要。
在对目前对叶片状态监测及故障诊断的文献进行理解和综合的基础上,对风力机叶片损伤的方式、常见损伤类型、损伤机理进行分析,对风力机叶片状态检测的常用方法,进行了比较研究综述,最后探讨了叶片故障检测及诊断技术的发展方向。
关键词:
叶片;状态监测;故障诊断
Abstract
Windturbinebladeisakeycomponentofthebearwillconvertthekineticenergyofthewind,tothewindturbinerotorrotatingmechanicalenergytask.Safety,reliabilityandenergyconversionefficiencyofbladehasanimportantinfluenceonthewholewindturbine.Withtheincreaseofwindpowercapacity,bladefaultposeagreatthreattothesafeoperationofwindturbine,soitisveryimportanttomonitortheworkingconditionoftheblade.Intheconditionmonitoringandfaultdiagnosisofleafliteraturebasingontheanalysisandsynthesisofwindturbineblades,thedamagemode,thecommontypesofinjury,injurymechanismwasanalyzed,thecommonlyusedmethodsofwindturbinebladestatedetection,comparisonresearch,finallydiscussesthedevelopmentdirectionoffaultdetectionanddiagnosistechnologyofblade.
Keywords:
blade;statemonitoring;faultdiagnosis
引言
风力发电机组中风机叶片是关键部件,承载着能量转化的重要作用,叶片工作的安全可靠性和能量转换效率对整个风力机组有着十分重要的影响,其性能好坏也直接影响着整机运行以及稳定【1,2】。
风力机叶片成本占整台风力发电机组的1/5,叶片的结构设计是整个风力机组设计的基础,它的设计应该根据气动设计中计算的载荷,并考虑机组实际运行环境的影响,如风沙、低温结冰等问题,使设计的叶片具有一定的强度与刚度,确保叶片在使用寿命周期内,并且在使用环境条件下运行而不发生损坏,叶片的设计要求
能承受50年一遇的极限风速【3,4】。
风力发电机的叶片损坏率较高,叶片损坏对风力发电造成了很大的经济损失,而且风力机叶片故障对风力机组安全运行构成很大威胁,所以,对叶片进行状态检测非常重要。
本文将简要概述风力机叶片监测技术在国内外最新进展及叶片损伤机理及其识别方法。
1风力机叶片损伤监测技术发展现状
1.1国外发展现状
为了验证叶片设计的正确性、可靠性和制造工艺的合理性,风力机叶片必须做到相关实验,如气动特性试验、静力和疲劳试验是风力机叶片全尺寸结构实验中的重要组成部分,目的是为了确保叶片所有部位都能够承受特殊的载荷情况,如五十年一遇的阵风等,这些测试不但能够验证风力机叶片在运行环境条件下能够承受较大载荷、暴露叶片的疲劳薄弱环节而且能够验证叶片长时间运行而不损坏。
当然,在试验过程中会有一些材料开裂的声音信号从叶片的某个部位发出,这些声音信号对于发现叶片损伤的位置和严重性具有非常重要的作用,对叶片设计和制造工艺的完善和改进有很大的指导作用。
2002年,P.A.Joosse,M.J.Blanch描述了声发射技术在风力机叶片静力试验和疲劳试验中的应用,对安装在叶片表面的传感器所采集的信号进行分析检测出叶片的故障和叶片损坏的区域,证明了声发射技术在静力试验和疲劳试验中能有效检测和测试叶片表面的破坏【5】。
2003年M.J.Blanch,A.G.Dutton将这种声发射技术应用到正在服役的风力发电机组叶片检测中,声发射监测能发现故障和描述叶片的破坏过程【6】
文献【7】【8】【9】【10】也描述了关于风力机叶片故障的声发射信号的分析问题。
2002年,Lars.Lading,Malcolm.McGugan等运用超声波对叶片进行无损检测,但是这种技术非常的费时118J。
上面文献中介绍的方法需要特定的检测条件,如需要约束叶片,安装复杂的测量仪器,施加静态载荷等等。
1999年,Beattie,A.GRumsey.M等介绍了一种数字照相能检测叶片表面的温度变化,这种方法能够有效地发现损伤,譬如裂纹等【11】。
当叶片出现裂纹时其振动频率等特性会发生改变,Ghoshal.A等介绍了四种振动方法用来检测一段由玻璃纤维构成的叶片的损坏,通过实验证明了方法的可行性【12】。
2000年,Chin-ShunTsai等介绍了将检测的振动信号用Meyer小波进行小波变换,得Nd,波系数,并计算其能量方差比,当大于某个设定值时判断叶片有损伤,这个设定值是经过研究得来的【13】。
2009年,L.Dolifiski等利用振动监测的方法检测风力机叶片损伤,该方法所用仪器为多点激光测振仪。
具体做法为:
将叶片根部固定,在根部用激振器进行激振,测得前几阶振型,然后采用小波分析对一阶振型模态进行连续小波变换,根据小波变换模极大值诊断结构的损伤【14】。
1.2国内发展现状
2006年,肖劲松等人运用红外线成像对风力机叶片进行了无损检测的数值研究,该文针对风力机叶片的典型材料中可能出现的典型缺陷(内部气孔),用脉冲红外线成像法进行检测,该方法的基本原理为:
先进行计算机模拟得到模型脉冲加热到冷却阶段任意时刻的温度场和热流场以及缺陷区对应的温度场以及温差的变化趋势,从理论上解释红外线成像检测内部缺陷的机理。
目前,该方法并没有在工程实际中运用,而且对于运行中的风力机组该方法很难实现在线的监测【15】。
2009年,赵光新等用声发射和小波分析对大型风力机叶片材料损伤进行识别研究,该文针对风力机叶片的监测问题,运用了声发射测试技术及分析手段和小波分析方法,提出了一个初步的运用声发射信号进行识别的思路,但该方法只是针对风力机叶片材料进行损伤识别,并没有对真实叶片做出判断,而且用声发射对已经出现的裂纹的材料进行信号分析就存在一定的缺陷性【16】。
2011年,徐玉秀等利用有限元分析方法建立了300W风力机发电机组的动力学模型,从风力发电机组的振动响应信号,应用程度分形维数理论,作为叶片偏心故障诊断识别的特征量,该方法只针对叶片的偏心故障进行检测,对于在运行当中出现叶片损伤情况并没有涉及到【17】。
2012年,李茫茫等采用理论计算和实验研究相结合的方法,对风力机叶片损伤前后的振动特性变化进行研究分析,找到了叶片损伤与其振动特性变化的定量关系,并开发出了基于振动信号检测的风力机叶片损伤动态监测(原型)系统。
基于振动的损伤识别方法在土木工程领域的梁类结构损伤识别上有很多研究。
2.风力机叶片损伤机理以及识别方法
随着风力发电机组装机容量不断增大,风力机叶片损伤对风机机组安全运行构成很大威胁,所以,风力机叶片损伤机理以及识别方法的探索对于风力机叶片监测研究显得尤为重要。
造成风力机叶片损伤的原因有很多,损伤的形式各种各样,本文通过比较造成风力机叶片损伤的原因,分析损伤的机理,从而科学地确定损伤识别方法。
2.1造成风力机叶片损伤的原因
2.1.1运输、安装过程造成的损伤
风力机发电机组的叶片长度有几十米,由于世界各国的铁路、公路管理部门对运载货物的长度和高度都有一定的限制,而且在叶片运输的过程中,进入现场的道路与正常公路又无法相比,很多风场的位置偏远、交通不便,有时候是山区、林区风场,因此叶片的叶尖与树木刮碰时有发生,叶尖与树枝刮磨会造成细小的伤痕。
同时,在安装叶片的过程中也有可能会造成叶片的损伤,其中绳具与夹具便是伤害叶片的一些装备,伤害叶片的主要部位为叶脊,吊装叶片时,无论是绳具还是夹具,只要吊起叶片的中心点与主梁角度有偏差,在叶片偏离地面时都会产生角度复位移动和摩擦复位现象,因此都会造成叶片表面受损。
吊装叶片使用的吊装宽带,有时也会损伤叶片表面【18】。
2.1.2自然环境造成的损伤
风力机组安装的位置地方不同,则风力机叶片叶所处的自然环境也不同,沙漠、海上或者沿海地区,山区,高原,平原,每个区域都伴随着不同的环境因素在这些自然环境下会对风力机叶片造成影响,风沙、低温、雨水、盐雾、雷电、冰雪等都有可能对风力机叶片造成一定的损伤。
2.1.3运行过程中造成的损伤
风力机组在运行过程中,受到方向不同、大小不同的风载荷的作用,由于风流方向不是一成不变的,并且叶片的结构不相同,这就使叶片产生不同方向、不同形式的运动,其中包括一些振动。
叶片受到的激振力越大并且激振力频率越接近叶片固有频率时,叶片变形就越明显,因此在运行过程中振动也会对叶片造成伤害【19】。
2.2叶片常见的损伤类型
2.2.1表面磨损
磨损是两物体表面接触随时间增加和载荷作用损伤的累积过程,两物体接触做复合运动时由于交变接触力的作用,使表面材料形成点蚀或剥落的现象。
在风力机叶片运行时,会与风沙之类的硬物相接触而产生摩擦,从而导致叶片表面逐渐被磨损。
还有种情况是由于风力机叶片暴露在自然环境中,受到雨雪冰霜等物质的化学作用而引起表面腐蚀,而摩擦中的机械作用又有加速了腐蚀的过程,从而造成表面磨损,这种情况称为氧化磨损和化学腐蚀磨损。
2.2.2表面剥蚀与脱落
大型风力机长期暴露在风沙、雨雪、温度骤变等恶劣环境,在风沙、雨雪的侵袭下,保护层会出现脱落(如图2.1所示)现象,而叶片表面磨损的地方经过一段时间后也容易会发生叶片的保护层脱落现象,保护层脱落后,叶片会变得比较脆弱,更容易在自然环境的影响下造成更进一步的损害,如出现小砂眼(如图2.2所示)。
2.2.3材料碳化
叶片在服役过程中会受到烈日高温、雷击、野火等不利因素的影响,在高温作用下叶片的表面会发生碳化现象。
世界每年有l%.2%的风轮叶片受到雷击袭击,叶片受雷击的损坏中,多数在叶尖是容易被修补,少数情况则要更换整个叶片,叶片遭受雷击后轻微的一般是表面碳化(如图2.3所示)或者后缘开裂,严重的会造成叶片击穿(如图2.4所示)。
2.2.4材料脆化
长期运行的风力发电机组叶片会有脆化现象,而且机组在太阳辐射作用下运行,叶片材料塑性会下降,脆性增加。
随着时间的增加,脆化会越来越严重,脆性的增加,有可能导致叶片发生断裂。
2.2.5裂纹与开裂
造成风力机叶片裂纹的主要原因是低温和机组振动。
叶片的振动和停车都会使裂纹加深加长,裂纹在扩张的同时空气中的污垢、风沙乘虚而入,使得裂纹加深加宽,风沙和污垢其实是扩张裂纹的作用。
裂纹可导致叶片的开裂,横向裂纹可导致叶片的断裂。
同时,风力发电机组他加上的风轮运转时,会对塔架系统产生激振力,塔架系统的运动反过来又对风轮产生激励,这样两者之间相互激励,就会使系统在耦合振动中变得不稳定,还会反作用在叶片上,也会使叶片出现断裂现象【20】。
叶片裂纹、开裂与断裂清醒如图2.5~图2.7所示。
2.3叶片损伤产生的机理
2.3.1砂眼产生的机理
风力机叶片长期在恶劣的环境中运行,避免不了受到雨雪、风沙等自然环境的影响,其表面在这些物体的侵袭下,叶片表面受到磨损,其保护层便开始脱落,风力机叶片出现砂眼是由于叶片没有了保护层引起的。
叶片的胶衣层破损后,被风沙抽磨的叶片首先出现的麻面,及一些小点点,其实就是叶片表面细小的砂眼,砂眼生成后它的演变的速度是惊人的,1.5毫米直径的砂眼二年后清洗已变成深度5毫米直径达10~12毫米的大砂眼【2l】。
2.3.2裂纹产生的机理
叶片在风的气流作用下会产生升力,叶片升力大小随攻角α而变,攻角α超过临界攻角时,α越大升力越小,α小于临界攻角时,α越大升力越大。
当叶尖作向上的于根部的弯曲运动时,于是流场中的流体会与叶片的新位置之间产生一个角度差,当α大于临界α,叶片升力是趋向增加的,升力的增加对于叶片的向上弯曲运动起到了的作用。
因此,气流提供给了叶片更多的能量,那么叶片的振动也就会更强烈。
这象称为“颤振”,而这种颤振是在叶片失速下形成的,因此又称为失速颤振。
通过颤生过程可以看出,颤振是由气动力、惯性力和弹性力交互作用的结果。
经过多次反振动,叶片材料会无法承受如此大振动应力,以至于在很短的时间内即出现裂纹或断裂[22]。
2.3.3雷击造成损伤的机理
叶片受到雷击,主要是由于叶片内进水所造成的,叶片进水主要类型有:
叶
脊迎风面出现通腔砂眼,风力机叶片叶尖处进水和叶片软胎现象。
雷击造成叶片
坏原因主要有两个:
一是当叶片被雷电击中时,叶片结构的温度会急剧升高,主
雷电因为产生的巨大能量,从而分解气体使气体温度升高并膨胀,当压力达到某一是造成叶片爆裂破坏;二是雷击造成的巨大声波,对叶片结构造成冲击破坏【23】。
2.4叶片损伤识别的常用方法
风力机叶片受到的损伤有些是无法避免的,如砂眼、开裂等。
但是,运行过程中由于机组振动造成的损坏如叶片的裂纹是各种损伤之一,也是非常严重的损伤,这是可以有效避免和检测出来的。
因此,对风力机叶片在运行过程中受交变载荷的影响以及自身振动作用下产生裂纹的监测很有必要,以下是风力机叶片损伤识别的常见几种方法。
2.4.1声发射检测技术
材料内部快速产生能量释放,产生瞬态弹性波的现象称为声发射。
声发射技术就是人们借助灵敏的电子仪器接收材料内部结构缺陷或潜在运动变化过程中材料本身发出声发射信号从而推断声发射源的技术,大多数材料变形和断裂时有声发射发生【24,25】,国外在对风力机桨叶进行静力试验和疲劳实验时就是应用声发射技术进行损伤检测的,从而找到风力机叶片在实验过程中的声发射特点。
2.4.2超声波检测技术
超声波检测主要是给探头一个电信号,激励探头压电晶片产生高频的超声场,超声场穿过风力机桨叶,在桨叶中传播,当遇到损伤位置时,超声场的部分能量便会反射回探头,探头将声信号转换成电信号给接受仪器【26】。
从而可以从信号中判断出桨叶是否损伤,以及损伤的具体位置。
2.4.3红外热成像检测技术
红外热成像检测技术是利用不可见的红外辐射转换成图像的损伤检测技术。
当对风力机桨叶施加均匀的热流时,材料表面的温度场应该是一致的,但是当风力机桨叶受到不同程度不同性质的损伤时,则损伤处相应表面的温度和红外辐射强度异常,所以根据红外成像图判断桨叶内部的损伤情况[27]。
2.4.4振动检测技术
在20世纪60年代,振动监测技术在航空航天、机械工程界就已经开始应用了,利用振动监测方法进行损伤检测的原理为:
当结构发生损伤时,其结构的物理参数(如刚度、质量、阻尼比)也会发生了变化,上述变化会改变结构的动力学特性(如频率、模态等),利用结构动力学特性的定量变化可以判断结构体的状态特征。
旋转机械最常用的状态监测方法就是振动监测,振动监测是大型设备状态监测与故障诊断中可靠、有效的分析方法之一,而且已经非常成熟,因此运用振动监测方法对风力机组设备进行状态监测有很大的实际应用价值。
风力机组在运行中存在着各种各样的大量的振动问题,造成风力机叶片的振动源也很多,叶片越长,叶片越容易发生变形而发生颤振,风力机叶片表面产生的剥落、裂纹会使振动进一步加剧,这样利用现有的振动问题对风力机叶片进行状态检测,是一种利用现有问题解决实际问题的有效方法。
基于风力机叶片振动的操作故障特征提取,通过对风机的数据采集,计算出的振动信号的关联维数,并将其作为特征参数,为叶片工作状态。
计算结果表明,关联维数有效地反映叶片的动态结构。
因此,叶片振动信号关联维数可以用来区分不同的工作状态。
实验还表明,该方法是特别有效的工作状态监测和故障诊断,在这些,可以达到较高的精度应用。
【28】
上述检测方法均可用于风力机叶片损伤检测。
但是,能够对风力机叶片进行实时在线动态监测,振动检测方法无疑成了最佳选择。
2.4.5模糊理论检测技术
在风机组的叶片存在的故障问题,根据传统的故障诊断方法,【29】介绍了模糊方法在风力涡轮机叶片的故障诊断,然后分析的模糊故障和症状。
同时,建立模糊综合评判模型,采用最大隶属度原则对风力机叶片的故障症状,结果表明它能迅速准确地找到故障症状,许多诊断对象的故障状态的模糊,模糊数学理论是这类故障诊断的一种有效方法。
它不需要基于模糊诊断方法建立精确的数学模型,充分运用隶属函数,模糊规则和模糊推理实现模糊诊断的智能化。
作为模糊逻辑具有相当强大的结构知识表达能力,它能正确表达的模糊或定性信息,推理过程接近人类的思维模式,同时模糊分类可以直接表达的描述性的发生与专家因此关联关系的编码,这是一个必然趋势将模糊理论引入风机故障诊断。
2.4.5传感器检测技术
在实际应用中的风力机组叶片的故障,【30】分析介绍了光纤传感布里渊传感器原理。
基于布里渊光时域监测系统对温度和应变力在线分析和建议(BOTDA)。
通过应用这技术,BOTDA传感器可以检测为1.5厘米裂纹,满足了风力机叶片的结构健康监测故障定位的要求。
LM公司在开发的叶片的复合材料铺设智能光纤传感器。
对叶片工作状态信息实时采集和处理,然后发送到控制系统。
一旦造成的环境负荷条件,如温度,风速,风荷载荷的临界值,监视器会自动提醒。
2.5本章小结
通过了解造成风力机叶片损伤的原因以及叶片在服役过程当中会受到的各种损伤及其特点,分析了风力机叶片各种损伤机理,表明:
风力机叶片在实际运行过程当中受到的损伤主要是裂纹,并且以横向裂纹为主,造成原因主要是由气动力、惯性力和弹性力交互作用的结果即失速颤振引发的,因此综合比较各种风力机叶片损伤监测方法,确定使用振动监测方法来对风力机叶片进行实时在线监测,其相对于其它方法具有很强的优越性以及实用性。
3研究展望
随着振动监测技术在各个工业检测领域的广泛应用,基于振动信号检测的风力机损伤动态监测技术必将成为解决风力机叶片在线监测的重要方法之一。
目前,国外在风力机叶片损伤监测的研究与开发方面取得了一定成果,但国内尚处于起步阶段,还有待进一步的研究和探索。
接下来主要可以从以下几方面进行深入研究:
(1)由于风电场的工作环境多变,风力机叶片结构的复杂性,采用什么样的传感
器、如何安装传感器而获得振动信号还有待进一步研究。
信号处理方面,仅仅运用模态分析方法进行处理比较有限,可以选择更先进的信号分析方法如小波分析对采集到的振动数据进行分析,获得更准确的损伤定量定位方法。
(2)本文提出的基于振动信号的损伤动态监测方法,由于实验室的条件有限,未
考虑风力机叶片旋转状态下的情况,而且其计算精确性还有待进一步的研究和认证。
(3)本文所研发的风力机叶片损伤动态监测系统,现正处于初级调试应用阶段,
系统结构和功能还有待进一步的优化和升级,如:
振型显示的优化、系统软硬件结构完善与优化、故障诊断功能的进一步研发和现场应用验证等。
【31】
参考文献
【1】王承煦,张源.风力发电[M】.北京:
中国电力出版社,2003
【2】乔燕虎,张春燕.风力发电机叶片振动失效机理分析阴.机械工程师,2007,4:
55.57
【3】王建录,郭慧文,吴雪霞.风力机械技术标准精编[M】.北京:
化学工业出版社,2010
【4】钱伯章.风能技术与应用[M】.北京:
科学出版社,2010,7
【5】EA.Joosse,M.J.Blanch,A.GDutton,et.AcousticEmissionMonitoringofSmallWind
TurbineBlandes.JournalofSolarEnergy.2002:
1-13
【6】M.J.Blanch,A.GDuRon.AcousticEmissionMonitoringofFieldTestsofanoperating
windTurbine[J].KeyEngineeringMaterials,2003,475-482
【7】AGDuRonl,MJBI.anch,PVionis,et.Acousticemissionconditionmonitoringofawind
turbinerotorblades[C].proceedingsofEWEC2003,Madrid,2003
【8】JensenFM,FalzonBG,AnkersenJ,StangH.Structuraltestingandnumericalsimulationofa34mcompositewindturbineblade.ComposStruct2006;76:
52–61.
【9】GieskeJ.H,RumseyM.A.Non-destructiveEvaluation(NDE)ofCompositeMetalBond
InterfaceofAWindTurbineBladeUsingAnAcoustic-ultrasonicTechnique[C].AIAA
AerospaceSciencesMeeting,1997,249-254
【10】DuRonA.QThermoelasticstressmeasurementandacousticemissionmonitoringinwind
turbinebladetesting[C].EuropeanWindEnergyConference.London,2004:
22.25
【11】LarsLading,M