CNC弯管原理.docx
《CNC弯管原理.docx》由会员分享,可在线阅读,更多相关《CNC弯管原理.docx(20页珍藏版)》请在冰豆网上搜索。
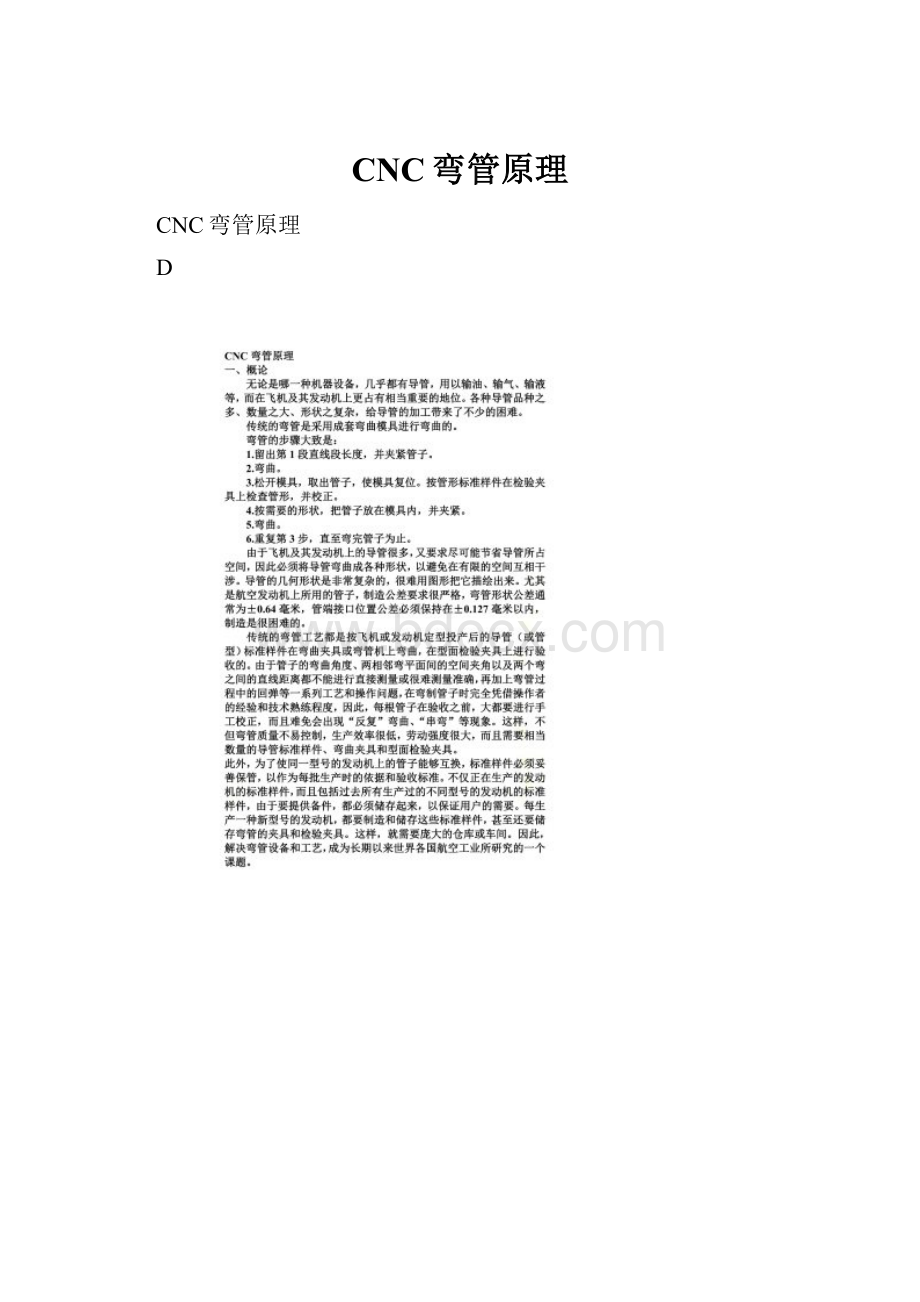
CNC弯管原理
CNC弯管原理
D
如果把管子放在空间坐标系中,并且管子上的直线段用其中心线表示,那么,管形即可由每段直线段中心线所表示。
相邻两中心线延长后产生了交点。
相邻两相交点连线的距离和方向,就表示了矢量的大小和方向。
将管形上的各直线段中心线以一系列的空间矢量来表示,求出它们的交点,进而求出“增量管形数据”,这就是矢量弯管的原始设想。
基于以上设想,美国伊顿·伦纳德公司制成了VECTOR1管形测量机。
如果一个管子有8个弯,那么,使用VECTOR1管形测量机测量管形时,测量点选择在9个直线段上任意一点(但两端的直线段需在端点处测量),而且每个直线段上只需测量一次。
因而,依次测量9次便可算出通过各测点的管形直线段中心线的方向余弦。
进而计算相邻两矢量的交点坐标数据,并存储在计算机的存储器内。
也就是说,VECTOR1管形测量机用a、b、c…j十个点的坐标数据来描述管形。
由于管形在空间的位置是比较复杂的,以若干点的坐标来描述管形,人们不易推想出管形的真实形状。
况且,弯管机所使用的数据不是坐标点数据,而是“增量弯管数据”。
因而,存储在计算机存储器内的坐标点数据还必须通过一系列矢量运算,计算出弯管所需要的“增量管形数据”。
1.两管间的送进距离DBB(DistanceBetweenBends)。
它是端点到直线与圆弧的切点之间的距离或直线与两圆弧的切点之间的距离。
对于弯管机来说,它是每一个弯之前的直线送进距离。
2.空间转角POB(PlaneOfBend)。
它是两个弯不在一个平面上,第二个弯所在的平面与第一个弯所在的平面的夹角。
对于弯管机来说,它是夹持管子的夹头的旋转角度。
夹头可作正向旋转运动,也可以作反向旋转运动。
3.弯曲角度DOB(DegreeOfBend)。
它是第二条直线段中心线相对于第一条直线段中心线的夹角。
对于弯管机来说,它是弯臂的转出角度。
管形的每一个弯都有这三个数据。
某一个弯的数据是依前一个弯的数据为基础而产生的,所以叫“增量管形数据”。
这种数据产生以后,还要经回弹数据修正,才成为弯管程序,用以控制矢量弯管机,进行弯管。
(三)矢量弯管技术
用测量机测出管形,取得必要的数据之后,还必须把管子弯出来。
因此和VECTOR1管形测量机配套的还有VECTORBEND弯管机,用这一台设备按测量所得数据弯曲管子。
所以矢量弯管技术的整个过程是:
1.使用VECTOR1管形测量机按管子标准样件测取(或按图纸输入)管形数据,编辑、修改管形数据;
2.测取回弹数据,编制弯管程序;
3.使用VECTORBEND弯管机弯管;
4.使用VERTOR1管形测量机进行自动检验,与标准样件管形数据相比较,算出差值,并用“差值”自动修正弯管程序;
5.再使用VECTORBEND弯管机弯出合格的管子。
本过程全由计算机控制完成。
也就是采用计算机数控(CNC)。
当然,这一过程中的第一步,测量管形数据也可以根据设计图纸,把管子各个直线段交点和两端点的数据直接输入到计算机中去,以此来确定管子的形状。
三、矢量弯管技术是弯管工艺的一个突破
采用矢量弯管技术制造管子具有重要的意义。
1.快速测取管形数据,按管形标准样件编程
前面已经说过,飞机及其发动机的导管的形状是很复杂的,它很难甚至不可能用设计图纸把它表达出来。
因此,在导管的加工中,许多导管的生产不是按照图纸,而是按照导管(或管形)标准样件来制造,在型面检验夹具上进行验收。
如果单纯的采用数控弯管,鉴于用通常办法测量管形数据很困难,即使测量出来,数据也不会准确,再加上影响回弹的因素很多,如管子的材料、直径、壁厚、弯曲半径和弯角大小等等,都没有一定的规律。
一系列的工艺问题,使得弯管程序的编制相当困难。
这就只能通过“逐个弯试弯—初记数据—试弯整个管形—修正数据—最后确定数据”的办法来编辑弯管程序。
然而,采用VECTOR1管形测量机,这个问题便迎刃而解了。
它通过对管形标准样件的测量,取得了管形数据,并经回弹修正后,自动编制VECTORBEND弯管机所需要的弯管程序。
这是一种“仿形”的方法,在实际生产中的用途很大。
特别是对于形状复杂的管形来说,大量的、复杂的计算工作均由计算机来完成,这就解决了一般测取管形数据的难题,从而使管形的计算机编程成为可能,并极大地减轻了编程人员的计算工作量。
2.快速综合检验管形
对于高质量、高效率的数控机床来说,如果没有与之相适应的快速检验方法,势必造成检验时间比弯管所需的时间长得多,以致影响数控弯管机床的高效率,造成“窝工”的现象,这是很不合理的。
VECTOR1管形测量机解决了这个问题。
它具有高效率综合检验管形的能力(一般7~8个弯的管子,从装夹、固定管子开始算起,到测量完毕、打印输出管形数据,3分钟以内可以完成),可对弯出的管子的形状进行快速检验,和对标准样件管形数据进行比较,确定误差值,并可打印出“检验报告单”。
这就有利于提高零件批量生产时的快速检验工效,有利于实现检验自动化。
同时,它还用“差值”自动修正弯管程序,得出新的弯管程序,再去弯管。
这种用“差值”修正的弯管程序,提供了一个新的弯管程序,使弯出的管形总是逼近管形标准样件,它实际上是一种“自适应”控制。
3.为导管的设计—制造一体化创造了条件
矢量弯管技术是管子弯曲生产自动化的基础,也为导管的设计—制造一体化创造了必要的条件。
美国麦克唐纳·道格拉斯飞机公司在导管的设计—制造一体化方面迈出了一步。
它将VECTOR系统与设计部门的大型计算机相连接,根据生产部门的安排,VECTOR系统接受存储在大型计算机存储器内的管形数据,并编制弯管程序,进行管子生产。
采用矢量弯管技术,从根本上改变了手工弯管的落后工艺面貌,使弯管技术面貌焕然一新。
它提高了弯管精度,使产品质量稳定、可靠。
对于形状复杂、手工弯管难以完成的棘手问题,可以比较容易的得到解决,其工效可提高几倍、几十倍。
可以说,矢量弯管技术是弯管技术的一个重大突破。
4.VECTOR1管形测量机可以按图纸尺寸输入“管形数据”,按管形标准样件测取管形数据或测量回弹数据,可以按需要编辑管形数据,如增加一个弯、撤消一个弯、移动一个弯、镜像、翻转管形数据;具有显示管形坐标数据、增量管形数据、回弹数据;存储和编制弯管程序等多种功能,其适应性大,操作简便,大大地缩短了生产准备周期,特别适应于新机研制过程中产品的形式和尺寸经常改变的需要。
而且,由于VECTOR1管形测量机能够获得准确的标准样件管形数据,并可存储保存;而在弯管之前测取回弹数据,编制弯管程序;再加上自动检验—修正弯管程序,VECTORBEND弯管机完全可以弯制符合要求的管形。
因此,从弯管的角度看,不需要保存大量的管形标准样件和型面检验夹具。
这样,既降低了生产费用,又节省了车间的庞大占地面积。
四、矢量弯管——CNC数控弯管系统介绍
如上所述,美国伊顿·伦纳德公司生产的CNC矢量弯管系统共分两部分,即VECTOR1管形测量机和VECTORBEND(简称VB)矢量数控弯管机。
VECTOR1管形测量机的功能有数十个,其主要功能是:
测取管形标准样件管形数据,将若干点的坐标数据变成增量管形数据;用增量管形数据来控制VB弯管机进行弯管,在一般情况下是不行的,还必须考虑管子的回弹修正问题。
在每批管子弯曲之前,用试验件在弯管机上做回弹试验,并在VECTOR1管形测量机上进行测量,以确定回弹数据。
而后修正增量管形数据,成为增量弯管程序,实现计算机编程。
VB数控弯管机接受来自VECTOR1管形测量机传送过来的增量弯管程序数据,并存储在控制柜的计算机中。
弯管机好象一个机械手,它按增量弯管程序数据和机床预定的弯管动作,将直管弯曲成所需要的形状。
下面对这套计算机控制的弯管系统作一些具体的介绍:
(一)VECTOR1管形测量机
VECTOR1管形测量机由工作台、测量臂、计算机、打印机、管子固定支撑架等组成。
1.测量臂
带计算机的VECTOR1管形测量机模仿人的手臂、手腕和手制成了测量臂。
测量臂的五个肘节处装有反映臂旋转角度的器件——编码器。
整个测量臂由臂Ⅰ、Ⅱ、Ⅲ、Ⅳ和探头组成。
臂Ⅰ是测量臂的立柱,它和坐标系统的z轴重合,并能绕z轴转动,其转角A由编码器A记录下来。
臂Ⅱ绕肘节B摆动,摆动角B由B处的编码器记录下来。
臂Ⅲ绕肘节C摆动,摆动角C由C处的编码器记录下来。
臂Ⅳ上装有探头,它除了可绕肘节E摆动,摆动角E由E处的编码器记录下来外,还可绕臂Ⅲ的轴线转动,转动的角度D由D处的编码器记录下来。
实际上,臂Ⅲ是由两段组成的,即下面的一段连同臂Ⅳ一起,可绕其臂Ⅲ轴线转动。
结构上保证了臂Ⅰ、Ⅱ、Ⅲ的中心线在一个平面上,臂Ⅲ、Ⅳ和由探头所决定的被测管子直线段中心线也在一个平面上,并且臂Ⅳ与探头所决定的管子直线段中心线相垂直。
整个测量臂上的五个肘节,使得测量臂能在空间任意转动,这就保证了探头能够比较方便的测量空间任意矢量。
同时,对于某一固定的测点来说,各肘节只有一个固定的转角,分别由五个编码器记录下来。
为了测取管形数据,应将管形标准样件固定在工作台面上的支架上,并用探头在管子各直线段上依次测量。
当测量完毕后,计算机把计算的管形数据存储在存储器内,并可用坐标点(x,y,z)的形式或增量管形数据(DBB、POB、DOB)的形式输出。
2.接口
设计这一系统的目的是收集五个编码器的数据,由计算机加以处理,完成各种测量的计算。
前面已经说过,VECTOR1管形测量机编制的弯管程序可经由专用电缆直接传送给VB弯管机的控制柜。
而且VECTOR1管形测量机上备有多个插座,可为多台弯管机服务。
数据的传输由VECTOR1上的弯管机接口板完成。
(二)VECTORBEND矢量数控弯管机
与VECTOR1管形测量机配套的VB弯管机是模块式弯管机,它是三坐标(DBB、POB、DOB)、点位闭环系统。
1.弯管机结构简要介绍
(1)床身。
床身由板材、型材焊接而成,被支撑在尾座和液压油箱上。
床身上装有导轨、弯管头、芯棒机构等。
在导轨上装有小车,床身上有行程开关。
(2)弯管头。
弯管头的功用在于完成“弯曲(DOB)”运动,把管子弯成需要的角度。
它由夹模机构、压模机构、助推机构、驱动回转机构等组成。
弯管头可以通过丝杠作横向运动,以便调整弯模中心线。
(3)小车。
小车由直流电机带动,以完成“直线送进(DBB)”运动。
小车上装有夹头,用气动操作。
夹头同样由直流电机带动,完成“空间转角(POB)”运动。
(4)芯棒机构。
芯棒机构装在床身的尾部,用其上面的螺母可前后调整芯棒,以保证芯棒在所需的位置上。
在自动弯管过程中,芯棒的前进、后退按计算机的指令,由液压操作完成。
2.液压系统
VB弯管机的液压系统比较简单。
它由带压力补偿的柱塞变量油泵、电液伺服阀、调压阀、压力表、油箱、油滤等组成。
应当指出的是,各液压执行元件(油缸)动作完成以后,反馈的信号不是由“微动开关”发出,而是在液压动作完成时,所需的液压油流量急剧减少,变量泵的斜盘倾角随之减小,连接在斜盘转轴上的液压臂,通过无触点开关发出反馈信号,使程序转入下一步。
因此,它简单、可靠。
3.弯管机的特点
VB弯管机在机械方面是比较完善的,有些地方是可以借鉴的。
机械方面的特点是:
(1)弯管头可沿导轨作横向移动,这是更换弯模后,调整弯模管槽对准机床中心线所必需的。
这样比用调整床身上的导轨和尾座来调整机床中心线简单。
(2)完成直线送进运动(DBB)的小车,在管子弯曲过程中,被管子拉着向前运动。
这样,去掉了“正推力”,从而去掉了小车与弯曲速度的同步问题,去掉了为增加“正推力”而设置的直流电机负反馈系统,简化了电气线路。
由于正推力对管子的弯曲有利,特别是在弯曲直径较大的管子时,正推力是必要的。
因而,VB弯管机增加了助推装置。
(3)弯曲时,由于小车作为负载,被管子拉着向前,为了改善弯曲,避免管子弯曲部分壁厚过分减薄,减少回弹,增加了助推装置。
弯曲时,压模不但压紧管子,而且被助推力推动向前,以形成一个助弯的侧推力。
(4)弯管臂和弯曲主轴连成一体、弯模轴可更换、夹模上下运动,这样不但结构合理,增加了机械部分强度,而且结构简单,从而使电气线路也简化了。
(5)当送进最后一个弯时,小车可能与压模相碰撞,这时可用“干涉区”功能,即压模退回→小车继续送进→弯管臂返回→空间转角(POB)→夹模夹紧→夹头松开,小车退出干涉区→压模压紧→弯曲管子。
这样,不但避免了小车同压模相碰撞,保证了最后一个弯的顺利完成,而且可以减少料头夹紧损失,降低生产成本。
(6)床身采用焊接结构,简单、紧凑。
五、增量管形数据的测取
欲测取管形数据,应该将管形标准样件固定在VECTOR1工作台面上的支架上。
将VECTOR1管形测量机接通电源,并复零。
根据VECTOR1管形测量机的检验报告,各臂的长度为:
臂Ⅰ34.053英寸
臂Ⅱ30.010英寸
臂Ⅲ23.984英寸
臂Ⅳ5.500英寸
六、回弹数据的测取
弯曲成型时,金属材料受力产生变形,而被弯曲成一角度。
当外力撤消后,被弯的管子部分恢复原来的状况,实测管子的弯曲角度比所需弯曲的角度小一些,这就是通常所说的管子的回弹。
弯曲不同的材料、不同的直径、不同的弯曲半径以及使用不同的工装和调整弯管机所用的工艺参数不同时,都会影响管子的回弹。
影响回弹的因素很多,这是一个比较复杂的问题。
但在机床调整好以后,工艺参数(弯曲半径、弯曲速度、夹紧力等)已经确定,而且又是在弯制某批材料管子的情况下,测定弯曲角度与回弹的关系,因此简化了一些影响回弹的因素,从而可把弯管机弯管臂的转角和管子的弯曲角度看成线性关系,这是确定回弹的一个简单而实用的办法。
测取回弹数据的大致步骤是:
1.调整好VB弯管机;
2.从被弯的管材中取一适当长度的试验管,按弯曲角度20°、120°弯曲管子;
3.在VECTOR1管形测量机上测量管形,计算回弹数据,并可打印输出回弹数据。
VB弯管机弯制管子时,也可以不预先测取回弹数据。
弯制好管子以后,在VECTOR1管形测量机上进行自动检验,并用“差值”修正弯管程序,得出新的弯管程序。
这样,VECTOR1便自动的将回弹因素考虑进去了。
七、增量弯管程序的编制
用于弯管的弯管程序要考虑到弯管机的具体情况、成形时管子的回弹和金属材料的拉伸。
实际上,用回弹数据把管形数据加以修正,编制出的弯管程序已经考虑到了这些问题。
弯管程序和增量管形数据的区别是:
1.弯管程序中已考虑了管子的回弹,即加大了弯曲角度。
加大了的弯曲角度就是弯管机弯管臂的转角。
2.弯管程序中已考虑了金属材料的拉伸,即用圆弧常数计算某弯曲角度下的材料需要量。
3.弯管程序中已考虑了具体弯管机的特性尺寸。
八、数控弯管的工艺过程
(一)使用VECTOR1测量机编程
使用VECTOR1测量机自动编辑管形数据,并经回弹修正,得出弯管程序的工艺过程如下:
1.按图纸数据输入管形数据
(1)坐标法
已知管子各直线段中心线延长线相交点间的距离时,用坐标法。
(2)增量法
当管子形状比较简单,可以从图纸上或通过计算得到所必需的尺寸时,用增量法。
2.按管形标准样件测取管形数据
在大多数情况下,由于导管的空间几何形状很复杂,很难用设计图纸把它准确的表达出来,而采用按管形标准样件测取管形数据的办法。
为了测取管形数据,应该将管形标准样件固定在VECTOR1工作台面上的支架上,并用探头在管子各直线段上依次测量。
VECTOR1测量机是以求直线段交点坐标而进行工作的。
因而它用空间若干点的坐标描述管形。
但这种方式不能被人们和弯管机所接受,还必须把它换算成管形数据,即用DBB—POB—DOB的格式表示。
3.测取回弹数据
弯曲不同的材料、不同的直径、不同的弯曲半径以及使用不同的工装和调整弯管机所用的工艺参数不同时,都会影响管子的回弹,因而每弯制一批管子都应测取回弹数据。
欲测取回弹数据,首先按所加工的管子调整好VB弯管机,并从被弯的管材中取一适当长度的试验管,按弯曲角度20°、120°弯曲管子。
而后在VECTOR1管形测量机上测量管形,计算回弹数据,
4.编辑弯管程序
按管形标准样件在VECTOR1测量机上测取的管形数据或按图纸数据从键盘输入的,都属于管形数据。
如前所述,由于回弹的存在,弯曲后的弯曲角度(DOB)将减小,弯曲半径将增大。
因此,必须用回弹数据对弯曲角度(DOB)和直线送进距离(DBB)进行修正,变管形数据为弯管程序。
1.弯管程序的输入
(1)从VECTOR1测量机直接输入
由于测量机与弯管机是配套产品,将弯管机通讯准备好,用测量机将弯管程序传输到弯管机。
(2)控制柜面板手工输入
按VECTOR1测量机已编辑好并打印输出的弯管程序,在控制柜面板手工输入。
2.弯管程序的修改
(1)当弯管程序有变动或有较大修改时,可在VECTOR1测量机上进行编辑,完毕后直接送给弯管机。
(2)如果局部修改某一段弯管程序,可直接在弯管机控制柜面板上,将要改的数据清除,并输入所需的数据。
3.机床、模具及调整
(1)机床液压系统的压力和弯曲速度的选择
弯曲不同直径、不同壁厚的管子以及使用的工装不同时,弯管各部位所需要的力也不同。
必须按材料、壁厚、直径等的不同,选择适当的系统压力(下面数据仅供参考)。
系统压力(最大)1500磅/英寸2
压模的系统压力(最大)1000磅/英寸2
助推的系统压力(最大)1000磅/英寸2
压模及助推的系统压力可按实际需要进行调节。
如直径为16毫米以上的管子,可选用:
系统压力1000磅/英寸2
压模的系统压力700磅/英寸2
助推的系统压力500磅/英寸2
弯管机有多种弯管速度。
在一般情况下弯制钢管,应在比较高速的情况下完成管子的弯曲。
对于直径大、弯曲半径小、壁薄的管子应采用较低的速度。
弯曲不同的材料、不同壁厚的管子以及弯曲半径不同时,都应选用不同的弯曲速度。
(2)弯模、夹模、压模、芯棒及其调整
弯模、夹模、压模及其芯棒等,对于弯管是非常重要的。
①弯模
弯曲时,弯模能防止管子扁平,并给出一个弯曲半径,以使管子弯曲成形。
弯模分组合式和整体式两种。
组合式弯模制造方便,但使用起来,由于弯模和镶块不是组合加工的,其半径槽不对中,或高低不平、不相切,或有间隙,使用感到不方便。
为了避免在接缝处产生压痕,方便现场使用,采用整体弯模为好,但整体弯模加工起来困难。
镶块的长度应大于2D(这里D=管子外径),特别是管子直径大时,这个数值应更大,否则夹不住管子,使弯曲无法进行。
当弯曲半径较小(如等于2D)时,由于管子椭圆的缘故,管子弯曲部分两侧有较严重的伤痕,故弯模槽的深度应比管子一半深些为好。
一般说来,直径在20毫米以下的钢管,弯曲半径等于管子直径的2倍,或2倍以上时,过分的椭圆和皱纹不应发生。
②夹模
夹模夹紧管子,同弯模一起转动,将管子弯曲成一定的角度。
夹模的宽度应不小于管子直径的2~3倍,特别是薄壁、较大直径的管子,其宽度更应大些。
如果太窄,则弯曲时夹不住管子,产生滑脱现象,并夹伤管子。
严重时,使弯曲无法进行。
从夹模夹紧来说,希望夹模宽些为好。
因此设计管子形状时,对两个弯之间的最小直线段距离必须给予足够的重视,以适应机弯的特点,保证最小夹紧长度。
夹模的宽度与镶块的宽度应一致,防止管子夹伤。
③压模
在弯曲过程中,压模压着管子到弯模上,并从助推得到向前的侧推力,使管子成形。
压模的压力应严格控制和调节。
如果压力不足,则弯曲半径内侧容易起皱纹;如果压力过大,又可使管子弯曲部分变细,并产生“内鹅头”。
当使用芯棒弯曲时,如果压力过大,管子在弯曲时容易前变形并与芯棒卡死,以致夹模夹不住管子而打滑,使弯曲无法进行。
压模压力不足还能引起弯曲部分椭圆度增大。
直径在16毫米以下的管子,如不使用芯棒,压模可以采用在弯曲前预先与弯曲变形相反的反变形措施,来保证弯曲后的椭圆度要求。
④芯棒
普通芯棒:
当弯曲直径为6、8毫米规格的管子时,由于直径小,自身的支撑力比较大,可以不使用芯棒,并保证弯曲处的椭圆度在直径的5%以内。
当管子直径增大时,为了防止弯管的椭圆度增大,应使用芯棒。
当管子被拉着向前时,由于芯棒作用,管子中心线外部的材料在切点处将被支撑,产生拉伸,并且硬化,以保证它的形状和不瘪。
芯棒的位置应在弯曲点上,并且切点的位置影响管子的椭圆度,影响管子的回弹。
如果芯棒太向前,容易使管子中心线外部的材料拉伸、变薄,长度增大,从而回弹变小,并且椭圆度也小,但有鹅头现象;有时还伴随着产生波纹。
如果芯棒太向后,管子中心线外部的材料没有足够的拉伸,而使管子塌下,椭圆度增大,甚至内侧产生皱纹。
因此,当弯曲半径增大时,芯棒应适当的向前些。
芯棒应该有一个(过切点的)提前量。
影响它的因素很多,例如:
芯棒前部R的大小;弯曲半径的大小;管子内径与芯棒之间的间隙;等等。
芯棒合适的位置首先应根据弯管经验粗略估计一下,而后通过试验调整,使其在合适的位置上,并保证管子无皱纹、鹅头小、椭圆度在管子外径的5%以内。
为了避免管子中心线外部材料上的波纹,除了正确的设计和调整芯棒外,应使芯棒杆有足够的刚性,免得颤抖引起波纹,并使用适当的润滑剂。
为了避免管子内壁划伤,芯棒应有足够的刚度,并经过仔细的去除毛刺、抛光;管子内腔也应经过认真的清洗,必要时进行湿吹砂。
芯棒与管子内径的径向间隙应不大于0.15毫米,如果间隙太大,尽管芯棒向前调整,但也可能产生皱纹。
由于管子壁厚公差较大,为了保证间隙,芯棒应分组,按管子内径选配。
使用芯棒时,由于管子中心线外部的材料受拉伸而变薄,但减薄量不得超过壁厚的10%。
允许有轻度皱纹,但不得超过壁厚的25%。
球芯棒:
在弯曲薄壁、直径大、弯曲半径小的情况下,应当使用球芯棒。
球芯棒的球体可在任意方向摆动。
使用球芯棒和普通芯棒一样,球芯棒的作用是保持管子在离开芯棒以后,仍支撑着管子周围,使管子不至于塌瘪。
球芯棒的调整和普通芯棒一样,不同的是球体部分应放在前面,后面的直杆部分按普通芯棒进行调整。
(3)助推的调整
在弯曲时用助推推动压模主动沿纵向移动,抵消弯曲时出现的阻力,这是机弯的一个特点。
使用助推,在弯曲时可以防止管壁过分冯减薄,减少管子回弹,同时抵消阻力,推动管子完成弯曲,减轻了夹模的负担,对弯曲是有利的。
一般来说,使用助推可以使夹紧长度减小,并使最小弯曲半径减小。
助推的速度可由装在助力缸上的调速阀来调节。
应调得略大于弯曲速度,以获得一定的侧推力。
(4)防皱模
在弯曲直径较大的管子,而弯曲半径较小、管壁又薄的情况下,应使用防皱模和球芯棒。
管子弯曲时,其中心线内侧的材料被压缩,当弯曲至一定角度时,由于材料压缩力大,将使材料被推回来,并超过切点,如果这个区域管壁未被弯模所支撑,就会形成皱纹。
即使以后被芯棒和弯模之间压平,但皱纹无法消除。
并当弯曲结束以后,管子上会形成一个大的皱纹。
使用防皱模,可以增加这个区域的支撑,使管壁在压缩后均匀增厚,不产生皱纹。
但由于调整不当,已经生成皱纹之后,防皱模不能消除皱纹。
防皱模的形状非常重要。
管子滑动通过的槽应略大于管子外径,其数值可为壁厚的10%,还应认真地抛光,以防止管子划伤。
防皱模的前端应制作得很薄很薄,伸到弯模的切点处,以弯模支撑,并加以固定,形成封闭腔。
为了减少弯曲时的阻力,防皱模在安装时,应略有一个很小的锥度。
压模的压力应调整得适当。
安装和调整防皱模时,最好使用“调整芯棒”,在夹模夹紧的情况下进行。
在弯曲