壳形塑料件的注射模设计.docx
《壳形塑料件的注射模设计.docx》由会员分享,可在线阅读,更多相关《壳形塑料件的注射模设计.docx(29页珍藏版)》请在冰豆网上搜索。
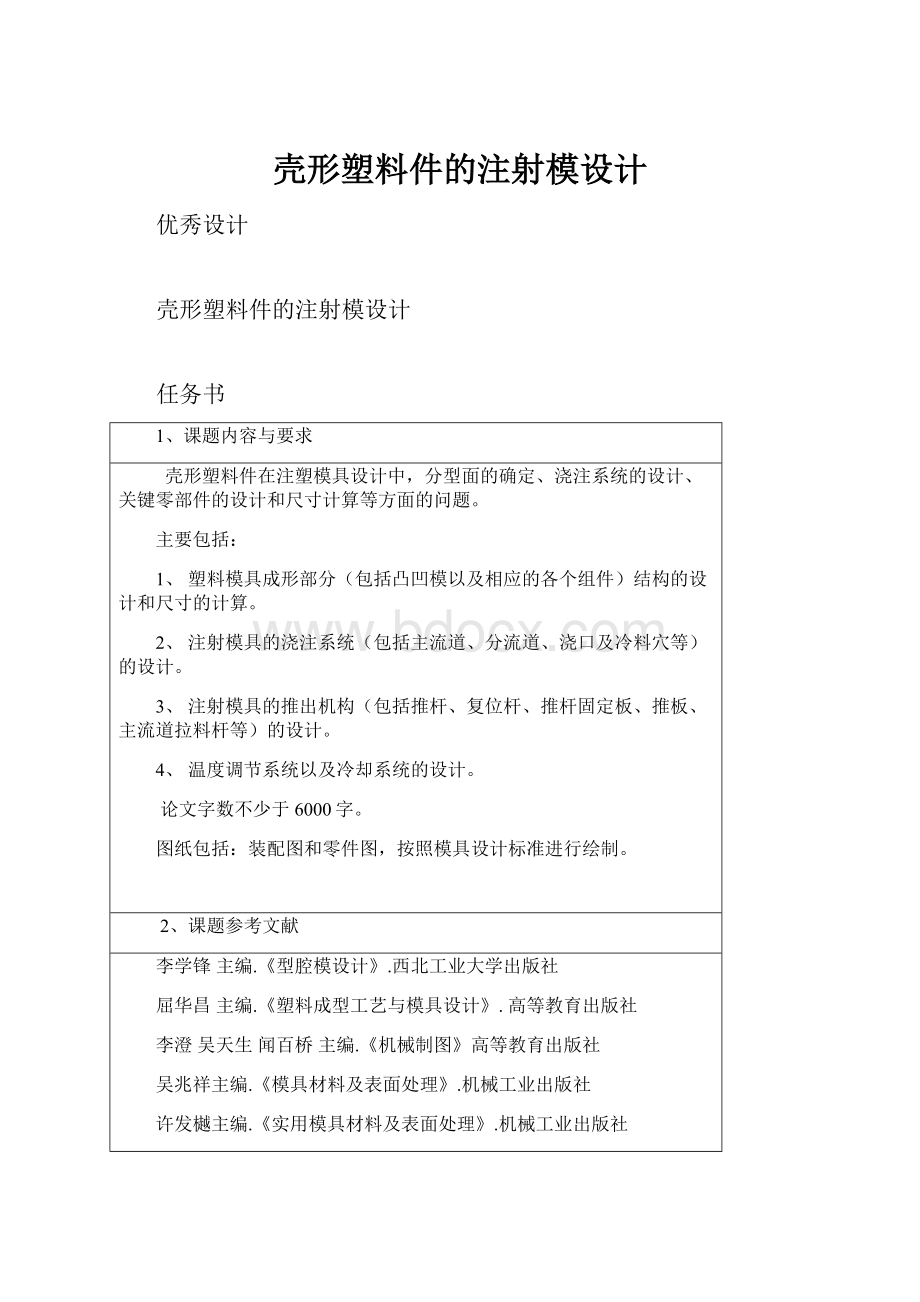
壳形塑料件的注射模设计
优秀设计
壳形塑料件的注射模设计
任务书
1、课题内容与要求
壳形塑料件在注塑模具设计中,分型面的确定、浇注系统的设计、关键零部件的设计和尺寸计算等方面的问题。
主要包括:
1、塑料模具成形部分(包括凸凹模以及相应的各个组件)结构的设计和尺寸的计算。
2、注射模具的浇注系统(包括主流道、分流道、浇口及冷料穴等)的设计。
3、注射模具的推出机构(包括推杆、复位杆、推杆固定板、推板、主流道拉料杆等)的设计。
4、温度调节系统以及冷却系统的设计。
论文字数不少于6000字。
图纸包括:
装配图和零件图,按照模具设计标准进行绘制。
2、课题参考文献
李学锋主编.《型腔模设计》.西北工业大学出版社
屈华昌主编.《塑料成型工艺与模具设计》.高等教育出版社
李澄吴天生闻百桥主编.《机械制图》高等教育出版社
吴兆祥主编.《模具材料及表面处理》.机械工业出版社
许发樾主编.《实用模具材料及表面处理》.机械工业出版社
党根茂骆志斌李集仁编.《模具设计与制造》.西安电子科技大学出版社
3、课题任务进度安排
第4周-第9周:
相关资料的查阅
塑件的分析、型腔数的确定和分型面的确定
浇注系统的设计
成型零部件的设计与计算
其它零部件的设计
冷却系统的设计
利用AutoCAD绘制模具零件图和装配图
毕业论文的撰写
答辩电子课件的制作
第10周:
毕业答辩
教研室主任意见:
教研室主任(签名):
年月日
开题报告
1、课题研究的现状和意义
80年代以来,在国家产业政策和与之配套的一系列国家经济政策的支持和引导下,我国模具工业发展迅速,年均增速均为13%,1999年我国模具工业产值为245亿,至2000年我国模具总产值预计为260-270亿元,其中塑料模约占30%左右。
在未来的模具市场中,塑料模在模具总量中的比例还将逐步提高。
我国塑料模工业从起步到现在,历经半个多世纪,有了很大发展,模具水平有了较大提高。
在大型模具方面已能生产48英寸大屏幕彩电塑壳注射模具、6.5kg大容量洗衣机全套塑料模具以及汽车保险杠和整体仪表板等塑料模具;精密塑料模具方面,已能生产照相机塑料件模具、多型腔小模数齿轮模具及塑封模具。
成型工艺方面,多材质塑料成型模、高效多色注射模、镶件互换结构和抽芯脱模机构的创新设计方面也取得较大进展。
塑料模具在基础工业中的地位和对国民经济的影响显得日益重要。
2、课题要解决的问题或研究的基本内容
壳形塑料件在注塑模具设计中,分型面的确定、浇注系统的设计、关键零部件的设计和尺寸计算等方面的问题。
主要包括:
5、塑料模具成形部分(包括凸凹模以及相应的各个组件)结构的设计和尺寸的计算。
6、注射模具的浇注系统(包括主流道、分流道、浇口及冷料穴等)的设计。
7、注射模具的推出机构(包括推杆、复位杆、推杆固定板、推板、主流道拉料杆等)的设计。
8、温度调节系统以及冷却系统的设计。
3、课题研究拟采用的手段和工作路线
本课题采用的是注射成型工艺。
一模2腔。
1、查询有关塑料制件、成型工艺、成型设备等相关资料,以备模具设计时使用
2、初步选择成型设备
3、进行必要的计算,拟定模具结构方案
4、方案论证
5、绘制模具图纸
6、编写设计说明书
4、课题研究进程计划
第4周-第9周:
相关资料的查阅
塑件的分析、型腔数的确定和分型面的确定
浇注系统的设计
成型零部件的设计与计算
其它零部件的设计
冷却系统的设计
利用AutoCAD绘制模具零件图和装配图
毕业论文的撰写
答辩电子课件的制作
第10周:
毕业答辩
5、课题成果
论文□图纸□产品或作品□应用程序□
其它:
指导教师意见:
同意
指导教师(签名):
年月日
教研室主任意见:
教研室主任(签名):
年月日
一、前言………………………………………………………………………………1
二、塑件工艺分析…………………………………………………………………1
2.1塑件选用材料分析及工艺特性…………………………………………1
2.2分析塑件的结构工艺性…………………………………………………2
三、确定注射机的型号…………………………………………………………2
3.1塑件体积计算………………………………………………………………2
3.2注射机型号的确定…………………………………………………………3
3.3注射量的校核……………………………………………………………3
3.4锁模力的校核………………………………………………………………3
3.5开模行程校核………………………………………………………………4
四、模架设计………………………………………………………………………4
4.1根据型腔数目的确定模架尺寸……………………………………………4
4.2型腔尺寸的分析……………………………………………………………4
五、模具结构与设计………………………………………………………………4
5.1主流道、分流道设计………………………………………………………4
5.2分流道的布置……………………………………………………………5
5.3冷料穴和拉料杆的设计…………………………………………………6
六、支承零部件的设计…………………………………………………………6
6.1支承板设计………………………………………………………………6
6.2垫块设计…………………………………………………………………6
6.3动模座板、定模座板的设计……………………………………………6
七、成型零部件设计………………………………………………………………7
7.1成型零件工作尺寸的计算……………………………………………7
7.2成型零部件的强度与刚度计算……………………………………………9
八、推出机构的设计………………………………………………………………10
8.1采用推杆推出………………………………………………………………10
8.2推杆位置的选择……………………………………………………10
九、合模导向机构的设计…………………………………………………10
9.1导柱的设计…………………………………………………………10
9.2推杆的设计…………………………………………………………11
9.3复位杆的设计………………………………………………………11
十、温度调节系统…………………………………………………………12
结束语…………………………………………………………………………13
参考文献………………………………………………………………………14
【摘要】:
塑料件的模具结构设计,应根据企业实际生产的具体要求来进行模具结构设计。
浇注系统采用普通流道,进行一模两腔注射。
【关键词】:
塑料注射模导柱复位杆
一前言
随着注射成型技术的不断发展,塑料制品已经深入到日常生活中的每—个角落。
由于塑料件具有重量轻.生产方便,价格便宜,放大到成人用品,小到儿童玩具,几乎全部采用塑料件生产。
塑料件的模具结构设计,应根据企业实际生产的具体要求来进行模具结构设计。
二塑件工艺分析
2.1塑件选用材料分析及工艺特性
该材料为丙烯腈-丁二烯-苯乙烯共聚物(ABS)
基本特征:
ABS是由丙烯腈、丁二烯、苯乙烯共聚而成的。
这三种组分各自的特性,使ABS具有良好的综合力学性能。
丙烯腈使ABS有良好的耐化学腐蚀及表面硬度,丁二烯使ABS坚韧,苯乙烯使它有良好的加工性和染色性能。
ABS无毒、无味、呈微黄色,成型的塑料有较的光泽。
密度为0.9~0.23g/cm。
ABS有极好的抗冲击强度,且在低温下也在不迅速下降。
ABS有良好的机械强度和一定的耐磨性、耐寒性、耐油性、耐水性、化学稳定性和电气性能。
水、无机盐类对ABS几乎无影响,但在酮、醛、酯、中会溶解或形成乳浊液。
ABS不溶于大部分醇类,ABS塑料表面受冰醋酸、植物油等化学药品引起开裂。
ABS有一定的硬度和尺寸稳定性,易于成型加工,经过调色可配成任何颜色。
ABS的缺点就是耐热性不高,连续工作温度为70℃左右,热变形温度93℃左右,且耐气候性差,在紫外线作用先易变硬发脆。
塑料件性能:
(1)力学性能:
屈服强度为50Mpa、拉伸强度38Mpa、断裂伸长率35%、拉伸弹性模量1.8、弯曲弹性模量1.4、弯曲强度80Mpa、布氏硬度9.7HBS、密度1.02—1.16g/cm3、比体积1.02—1.16、吸水性0.2—0.4、熔点130—160℃。
2.2分析塑件的结构工艺性
塑件相对一般塑料件较大,其整体结构简单,尺寸测量方便,符合一般塑件的设计要求,主要设计特征是内外抽芯机构。
三确定注射机的型号
根据塑料件的体积及主流道、分流道的容量来确定注射机的型号。
3.1塑件体积计算
根据Pro\e自带的测量工具测得该塑件的体积是:
47.123cm3
塑件重量为:
GS=V﹒r
=47.123x1.2g=57g
式中r为塑料容重(ABS的容种r=1.2g/cm3)
根据塑件的计算重量或体积,选择设备型号规格,确定型腔数当未限定设备时,须考虑以下因素:
机额定注射量GB,每次注射量不超过最大注射量的80%
即n=(0.8GB-Gj)/GS式中n—型腔数
Gj—浇注系统重量(g)
GS—塑件重量(g)
GB—注射机额定射量(g)
浇注系统估算结果:
Vj=6.2x(0.5/2)2π+12x(0.2/2)2π+2x9x(0.2/2)2π
=1.85cm3
设n=2则得
GB=(nGS+Gj)/0.8
=(2x57+1.85x1.2)/0.8g
=145.28g
从计算结果,并根据塑料注射机技术规格表2-40
根据塑件精度,因为该塑件精度一般,故采用一模两腔,即n=2
生产批量该塑件属大批量生产,故选了一模两腔。
3.2注射机型号的确定
根据塑件注射量大小故选择注射机额定注射量125㎝3;型号为XS-ZY-125。
注射机的规格和性能:
额定注射量125cm3、注塞直径42mm、注射压力120Mpa、注射方式:
螺杆式、锁模力900KN、最大开合模行程300mm、模具最大厚度300mm、喷嘴孔圆弧半径12mm、喷嘴孔的直径4mm
3.3注射量的校核
根据塑件注射量大小来选择额定注量
最大注射量的校核公式
nm+m1≤kmp=2*25+4.15≤0.8*125
其中n—型腔的数量k—注射量最大注射量系数取0.8
m—单个塑件体积mp—注射机最大注射量
m1—浇注系统所需塑料体积
3.4锁模力的校核
锁模力的校核公式
Fz=P(nA+A1)=120*%80(2*8.103+0.26)<9.0*105
其中Fz=熔融塑件分型面上的涨开力N
P=塑件熔体对型腔的成型压力,其大小为注射压力的80%
A=单个塑件在模具上的投影面积
A1=浇注系统在模具上的投影面积
3.5开模行程校核
S≥H1+H2+(5~10)mm
S—注射机最大开模行程为180mmH1为45mmH2为94mm取105mm
即合格
H1—推出距离(脱模距离)H2—包括浇注系统在内的塑件高度mm
四模架设计
4.1根据型腔数目的确定模架尺寸
根据最大注射量的大小确定型腔数目n=(km-m2)/m1=(0.8*120-4.15)/25=3.674,取2
其中n——型腔的数目
k——注射机的最大注射量系数,取0.8;
m1——单个塑件体积;
m2——浇注系统所有塑件体积;
m——注射机最大注射量;
4.2型腔尺寸的分析
平衡式布置
计算相关尺寸确定模架尺寸L≥75*2+38+25*2=230
B≥117+53+25*2=220
按标准选取模架为250*315。
五模具结构与设计
5.1、主流道、分流道设计:
主流道是连接注射机的喷嘴与分流道的一段通道,通常和注射机的喷嘴在同一轴线上,断面为圆形,带有一定的锥度。
(1)、为便于从主流道中拉出浇注系统的凝料以及考虑塑料熔体的膨胀,主流道设计成圆锥形,其锥度为2°—4°,取4°。
对流动性差的塑料,也可取3°——6°,过大会造成流速减慢,易成涡流。
内壁粗糙度为Ra0.63。
(2)、主流道大端呈圆角,其半径常取r=1——3mm,以减少料流转向过渡时的阻力。
R取2mm。
(3)、在保证塑件成型良好的情况下,主流道的长度尽量短,否则将会使主流道的凝料增多,且增加压力损失,使塑料熔体降温过多而影响注射成型。
(4)、为了使熔融塑料从喷嘴完全进入主流道而不溢出,应使主流道与注射机的喷嘴紧密对接,主流道对接处设计成半球形凹坑,其半径r2=r1+(1~2mm)。
其小端直径D=d+(0.5~1mm),凹坑深度常取3~4mm,取4mm。
分流道设计:
分流道是主流道与浇口之间的通道,一般分设在分型面上,起分流和转向的作用。
(1)、分流道的长度和断面尺寸
分流道的长度取决于模具型腔的总体布置方案和浇口位置,从输送熔体时的减少压力损失和热量损失及减少浇道凝料的要求出发,应力求缩短。
L取15.5mm分流道断面尺寸ABS取4.8~9.5取6mm。
(2)、分流道的断面形状为梯形(如图)
要减少流道没的压力损失,流道的截面积大、表面积小,以减少传热损失。
H/d=0.9,h=6*0.9=5.4,x/d=0.7,x=6*0.7=4.2.
5.2、分流道的布置
1)分流道的布置取决于型腔的布局,两者相互影响。
采用平衡式布置平衡式布置要求从主流道至各个型腔的分流道,其长度、形状、截面尺寸等都必须对应相等,达到各个型腔的热平衡和塑料流动平衡。
2)分流道与接口的连接:
分流道与接口的连接处于加工成斜面并用圆弧过度,有利于塑料容体的流动及填充。
5.3、冷料穴和拉料杆的设计(如图)
冷料穴是浇注系统的结构组成之一。
一般位于主流道对面的动模板上或处于分流道的末端。
作用是:
1)注系统道中料流的前锋冷料,以免这些冷料注入型腔。
这些冷料既影响熔体的冲填速度,又影响了成型塑件的质量。
2)便于在该处设置主流道拉料杆的功能。
拉料杆采用Z字型固定在推杆固定板上,工作时依靠Z字型钩将主流道凝料拉出浇口套,推出后由于钩子的额方向性而不能自动脱落,需要人工取料。
六支承零部件的设计
6.1支承板设计
支承板是垫在动模型腔下面的一块平板,其作用是承受成型时塑料熔体对动模型腔或型芯的作用力,以防止型腔底部产生过大的挠曲变形或防止主型芯脱出型芯的固定板。
其中相关尺寸根据模架而定
6.2垫块设计
用于支承动模成型部分并形成推出运动空间的零件。
其中相关尺寸根据模架而定
6.3定模座板、动模座板的设计
定模座板使定模固定在注射机的固定工作台面上的模板。
动模座板使动模固定在注射机的移动工作台面上的模板。
其中相关尺寸根据模架而定
七成型零部件设计
7.1成型零件工作尺寸的计算
确定主要零件结构及尺寸
经过初步设计,预选300x294x230模架。
各板厚数值都是根据公司要求的(非国标),其强度足够。
参考资料:
《塑料成型工艺与模具设计》
a、板厚及侧壁厚计算
对于面板属于矩形型腔,故可采用矩形整体式来计算板厚及侧壁厚。
1)按钢度条件计算侧壁厚:
2)s≥(cpH14/E[δ])1/3
式中c—由H1决定的系数查表6.6,取c=0.93
p—型腔内熔体的压力,据注射机取p=100Mpa
H1—承受熔体压力的侧壁高度,H1=2mm
[δ]—允许变形量,PC的值为≤0.06-0
则s≥(0.93x100x24/2.06x105x0.07)1/3
=2mm
因此可取型腔之间的壁厚为2mm,其它侧壁厚均取>7mm.
b、按钢度条件计算型腔底板厚度
h≥(c`pb4/E[δ])1/3
式中c`—由型腔边长比1/b决定的系数,查表取值为0.01251
b—塑件短边长度为42.3mm,其它同上。
h≥(0.0251x100x42.34/2.06x105x0.07)1/3
=13.174mm
由于是一模两腔,故底版厚28mm,总板厚30mm.
通过对定模型腔的侧壁厚和板厚的尺寸计算,故选用模架300x294x230。
其导柱等件皆从模架中选取。
c、型腔尺寸计算
1)塑件的平均收缩率计算:
S=(Smax+Smin)/2%
=(05+0.8)/2%=0.65%
2)各尺寸计算由型腔径向尺寸计算公式:
(Lm)+δ0z=[(1+S)Ls-xΔ]+δ0z
因塑件精度要求不高,故取:
x=0.5
得
40+δ0z=[(1+0.65%)x40–0.5x0.0.38]+00.38/5=40.278+00.076
36+δ0z=[(1+0.65%)x36–0.5x0.28]+00.28/5=36.1525+00.056
68+δ0z=[(1+0.65%)x68–0.5x0.28]+00.28/5=68.1265+00.056
46+δ0z=[(1+0.65%)x46–0.5x0.44]+00.44/5=46.3195+00.088
由型腔深度公式
(Hm)+δ0z=[(1+S)Hs-xΔ]+δ0z
得:
5+δ0z=[(1+0.65%)x200–0.5x0.74]+00.74/5=200.93+00.148
d、型芯尺寸计算
1)塑件的平均收缩率、及精度要求和型腔一致。
即S=0.65%x=0.5
2)各尺寸的计算由型芯径向尺寸计算公式:
(Lm)-δ0z=[(1+S)Ls+xΔ]-δ0z
36-δ0z=[(1+0.65%)x36+0.5x0.38]-0.038/5=36.6255-o0.076
46-δ0z=[(1+0.65%)x46+0.5x0.5]-0.05/5=46.991-o0.1
100-δz=[(1+0.4%)*10+0.75*0.28]0-0.093=ø10.3980-0.093
40-δz=[(1+0.4%)*4+0.75*0.12]0-0.04=R4.1020-0.04
50-δz=[(1+0.4%)*5+0.75*0.12]0-0.046=ø5.5740-0.046
由型芯深度公式:
(Hm)-δ0z=[(1+S)Hs+xΔ]-δ0z
28-δ0z=[(1+0.65%)x28+0.5x0.12]-0.012/5=28.57625-o0.024
7.2成型零部件的强度与刚度计算
整体式矩形型腔结构与组合式型腔相比刚性大。
底板与侧壁为一整体,这样型腔底部不会出现溢料间隙,所以在计算型腔时,变形量的控制主要是为了保证塑件尺寸精度和顺利脱模。
1、体式矩形型腔侧壁和底板厚度计算
整体式矩形型腔侧壁厚度计算
(1)按刚度条件计算
S=25≥{CPH14/E[δ]}1/3≥{0.57*30*424/2.06*105*0.04}1/3≥5.56合格
式中C——由H1/l决定的系数,查《塑料成型工艺与模具设计》表6.6
p——型腔内容体的压力50MPa
E——钢的弹性模量2.06*105Mpa
[δ]——允许变形量,mm
(2)按强度条件计算侧壁厚度S=25≥{PL4(1+Wa)/2*[σ]}1/2≥{30*1174(1+0.197)/2*160}1/2≥10.52合格
式中Wa——抗弯截面系数,见《塑料成型工艺与模具设计》表6.6
[σ]——许用应力160Mpa
a——矩形成型型腔的边长比,a=b/l
2、整体式矩形型腔底板厚度的计算
3按刚度条件计算
h=21≥{C,Pb4/E[δ]}1/3≥{0.0251*30*75/2.06*0.04}1/3≥10.4合格
式中c,——由型腔边长比l/b决定的系数,查《塑料成型工艺与模具设计》表6.7。
(2)按强度条件计算底板厚度整体式矩形型腔底板的最大应力发生在短边与侧壁交界处,按强度条件,底板厚度的计算为:
h=21≥{a,Pb2/[σ]}1/2≥[0.4256*50*452/160]1/2≥16.41合格
式中a,——由模脚(垫块)之间距离和型腔短边长度l/所决定的系数,查《塑料成型工艺与模具设计》表6.8。
八推出机构的设计
8.1采用推杆推出
截面成圆形,在推杆固定板上的孔应为d+1mm,推杆台肩部分常为d+5mm;推杆工作部分与模板或型芯上推杆孔的配合常采用H8/f的间隙配合,视推杆直径的大小与不同的塑件品种而定;推杆的材料采用T8A热处理要求HRC50~54,推杆工作端配合部分的粗糙度Ra取0.8μm;
圆形推杆直径的d=6
8.2推杆位置的选择
1)推杆的位置应选择在脱模阻力最大的地方。
2)塑件各处的推模阻力相等时需均匀布置,以保证塑件推出时受力均匀,塑件推出平稳和不变形。
应考虑推杆本身的强度和刚度。
九合模导向机构的设计
9.1导柱的设计
用于动模与定模间或推出机构零件的定位与导向。
导柱导向部分的长度应比凸模端面的高度高出8~12mm,以免出现导柱末导正方向而型芯先进入型腔的情况。
导柱为国家标准GB4169.4——84带头导柱的规格,导柱的材料为T8A淬硬到HRC50~55;
尺寸如图所示
9.2、推杆的设计
推杆的形状采用直通式推杆,尾部采用台肩固定;
推杆的工作端面形状采用圆形;
推杆的材料采用T8A热处理要求HRC50~55,推杆工作端配合部分的粗糙度Ra取0.63μm;
尺寸如图所示
9.3、复位杆的设计
复位杆的形式及尺寸如图,材料T8A;
十温度调节系统
冷却水道的布置应做到回路系统内流动的介质能充分吸收成型塑件所传导的热量,使模具成型表面的温度稳定地保持在所需的温度范围内,并且要做到使冷却介质在回路系统内流动畅通,无滞留部位。
1、冷却水道应尽量多、截面尺寸应尽量大
2、冷却水道离模具型腔表面的距离一般取10—15mm
3、冷却水道出入口的布置
4、冷却水道应沿着塑料收缩方向设置
5、冷却水道的布置应避开塑件易产生熔接痕的部位及避开导柱孔、螺钉孔、销钉孔。
经综合考虑在定模板设置两条直通式2-ø8的冷却水道,其水嘴如图:
结束语
三年的大学生涯伴随着这次设计的结束而划上了句号,在设计的一个多月里,一个又一个问题的困饶,一次又一次的修改,最终在一张张的图纸出笼时候让我感到了成功的喜悦。
在绘制零件图的过程中,同学一次次的帮助让我非常感动,但是所有这些热心的人们都将要离去了。
至此,感谢让我度过了三年金色阳光般日子的学校,感谢我所有的任课老师在这三年时间里对我无微不至的关心和谆谆教诲,让我在这三年里遨游在知识的海洋,在我人生的过程中你们的教导会使我终身受用。
我会在今后的工作中更加的努力的!
!
!
参考文献
1、党根茂骆志斌李集仁编.《模具设计与制造》.西安电子科技大学