超声波塑料焊接工艺.docx
《超声波塑料焊接工艺.docx》由会员分享,可在线阅读,更多相关《超声波塑料焊接工艺.docx(16页珍藏版)》请在冰豆网上搜索。
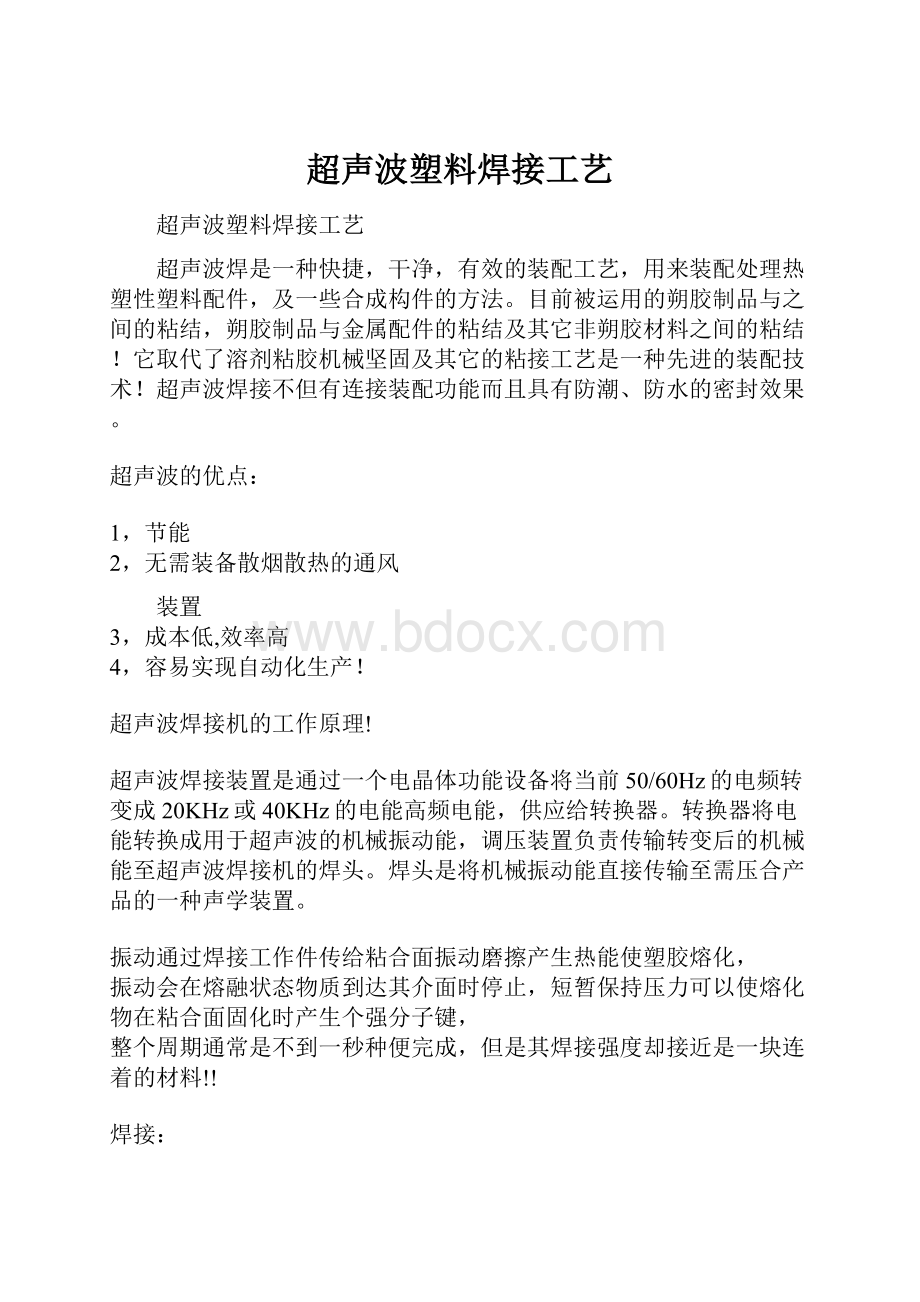
超声波塑料焊接工艺
超声波塑料焊接工艺
超声波焊是一种快捷,干净,有效的装配工艺,用来装配处理热塑性塑料配件,及一些合成构件的方法。
目前被运用的朔胶制品与之间的粘结,朔胶制品与金属配件的粘结及其它非朔胶材料之间的粘结!
它取代了溶剂粘胶机械坚固及其它的粘接工艺是一种先进的装配技术!
超声波焊接不但有连接装配功能而且具有防潮、防水的密封效果。
超声波的优点:
1,节能
2,无需装备散烟散热的通风
装置
3,成本低,效率高
4,容易实现自动化生产!
超声波焊接机的工作原理!
超声波焊接装置是通过一个电晶体功能设备将当前50/60Hz的电频转变成20KHz或40KHz的电能高频电能,供应给转换器。
转换器将电能转换成用于超声波的机械振动能,调压装置负责传输转变后的机械能至超声波焊接机的焊头。
焊头是将机械振动能直接传输至需压合产品的一种声学装置。
振动通过焊接工作件传给粘合面振动磨擦产生热能使塑胶熔化,
振动会在熔融状态物质到达其介面时停止,短暂保持压力可以使熔化物在粘合面固化时产生个强分子键,
整个周期通常是不到一秒种便完成,但是其焊接强度却接近是一块连着的材料!
!
焊接:
指的是广义的将两个热塑性塑料产品熔接的过程。
当超音停止振动时,
固体材料熔化,完成焊接。
其接合点强度接近一整块的连生材料,
只要产品的接合面设计得匹配,
完全密封是绝对没有什么问题的,
碟合:
熔化机械锁形成一个材质不同的塑料螺栓的过程。
嵌入:
将一个金属无件嵌入塑料产品的预留孔内。
具有强度高,成型周期短安装快速的优点!
!
类似于模具设计中的嵌件!
UltrasonicWelding1
UltrasonicWelding2
塑料件超声波焊接设计
塑料与塑料加工2010-12-0922:
53:
48阅读34评论0 字号:
大中小 订阅
现代注塑方式能有效提供比较完美的焊接用塑胶件。
光我们决定用超声波焊接技术完成熔合时,塑料件的结构设计必须首先考虑如下几点:
1焊缝的大小(即要考虑所需强度)2是否需要水密、气密3是否需要完美的外观4避免塑料熔化或合成物的溢出5是否适合焊头加工要求
焊接质量可能通过下几点的控制来获得:
1材质2塑料件的结构3焊接线的位置和设计4焊接面的大小5上下表面的位置和松紧度6焊头与塑料件的妆触面7顺畅的焊接路径8底模的支持
为了获得完美的、可重复的熔焊方式,必须遵循三个主要设计方向:
1最初接触的两个表面必须小,以便将所需能量集中,并尽量减少所需要的总能量(即焊接时间)来完成熔接。
2找到适合的固定和对齐的方法,如塑料件的接插孔、台阶或企口之类。
3围绕着连接界面的焊接面必须是统一而且相联系互紧密接触的。
如果可能的话,接触面尽量在同一个平面上,这样可使能量转换时保持一致。
下面就对塑料件设计中的要点进行分类举例说明:
整体塑料件的结构
1.1塑料件的结构
塑料件必须有一定的刚性及足够的壁厚,太薄的壁厚有一定的危险性,超声波焊接时是需要加压的,一般气压为2-6kgf/cm2。
所以塑料件必须保证在加压情况下基本不变形。
1.2罐状或箱形塑料等,在其接触焊头的表面会引起共振而形成一些集中的能量聚集点,从而产生烧伤、穿孔的情况,在设计时可以罐状顶部做如下考虑○1加厚塑料件○2增加加强筋
○3焊头中间位置避空
1.3尖角
如果一个注塑出来的零件出现应力非常集中的情况,比如尖角位,在超声波的作用下会产生折裂、融化。
这种情况可考虑在尖角位加R角。
1.4塑料件的附属物
注塑件内部或外部表面附带的突出或细小件会因超声波振动产生影响而断裂或脱落,例如固定梢等。
通过以下设计可尽可能减小或消除这种问题:
○1在附属物与主体相交的地方加一个大的R角,或加加强筋。
○2增加附属物的厚度或直径。
1.5塑料件孔和间隙
如被焊头接触的零件有孔或其它开口,则在超声波传递过程中会产生干扰和衰减,根据材料类型(尤其是半晶体材料)和孔大小,在开口的下端会直接出现少量焊接或完全熔不到的情况,因此要尽量预以避免。
1.6塑料件中薄而弯曲的传递结构
被焊头接触的塑件的形状中,如果有薄而弯曲的结构,而且需要用来传达室递超声波能量的时候,特别对于半晶体材料,超声波震动很难传递到加工面,对这种设计应尽量避免。
1.7近距离和远距离焊接
近距离焊接指被焊接位距离焊头接触位在6mm以内,远距离焊接则大于6mm,超声波焊接中的能量在塑料件传递时会被衰减地传递。
衰减在低硬底塑料里也较厉害,因此,设计时要特别注意要让足够的能量传到加工区域。
远距离焊接,对硬胶(如PS,ABS,AS,PMMA)等比较适合,一些半晶体塑料(如POM,PETP,PBTB,PA)通过合适的形状设计也可用于远距离焊接。
1.8塑料件焊头接触面的设计
注塑件可以设计成任何形状,但是超声波焊头并不能随意制作。
形状、长短均可能影响焊头频率、振幅等参数。
焊头的设计需要有一个基准面,即按照其工作频率决定的基准频率面。
基准频率面一般占到焊头表面的70%以上的面积,所以,注塑件表面的突超等形状最好小于整个塑料面的30%。
一滑、圆弧过渡的塑料件表面,则比标准可以适当放宽,且突出位尽量位于塑料件的中部或对称设计。
塑料件焊头接触面至少大于熔接面,且尽量对正焊接位,过小的焊头接触面,会引起较大损伤和变形,以及不理想的熔接效果。
在焊头表面有损伤纹,或其形状与塑料件配合有少许差异的情况下,焊接时,会在塑料件表面留下伤痕。
避免方法是:
在焊头与塑料件表面之间垫薄膜(例如PE膜等)。
焊接线的设计
2焊接线的设计
焊接线是超声波直接作用熔化的部分,其基本的两种设计方式:
○1能量导向○2剪切设计
2.1能量导向
能量导向是一种典型的在将被子焊接的一个面注塑出突超三角形柱,能量导向的基本功能是:
集中能量,使其快速软化和熔化接触面。
能量导向允许快速焊接,同时获得最大的力度,在这种导向中,其材料大部分流向接触面,能量导向是非晶态材料中最常用的方法。
能量导向柱的大小和位置取决于如下几点:
○1材料○2塑料件结构○3使用要求
当使用较易焊接的材料,如聚苯乙烯等硬度高、熔点低的材料时,建议高度最低为0.25mm。
当材料为半晶体材料或高温混合树脂时(如聚乙碳),则高度至少要为0.5mm,当用能量导向来焊接半晶体树脂时(如乙缩荃、尼龙),最大的连接力主要从能量柱的底盘宽带度来获得。
没有规则说明能量导向应做在塑料件哪一面,特殊情况要通过实验来确定,当两个塑料件材质,强度不同时,能量导向一般设置在熔点高和强度低的一面。
根据塑料件要求(例如水密、气密性、强度等),能量导向设计可以组合、分段设计,例如:
只是需要一定的强度的情况下,分段能量导向经常采用(例如手机电池等)。
2.2能量导向设计中对位方式的设计
上下塑料件在焊接过程中都要保证对位准确,限位高度一般不低于1mm,上下塑料平行检动位必须很小,一般小于0.05mm,基本的能量导向可合并为连接设计,而不是简单的对接,包括对位方式,采用能量导向的不同连接设计的例子包括以下几种:
插销定位:
,插销定位中应保证插销件的强度,防此超声波震断。
台阶定位:
如h大于焊线的高度,则会在塑料件外部形成一条装饰线,一般装饰线的大小为0.25mm左右,创出更吸引人的外观,而两个零件之间的差异就不易发现。
○1企口定位:
采用这种设计的好处是防止内外溢料,并提供校准,材料容易有加强密封性的获得,但这种方法要求保证凸出零件的斜位缝隙,因此使零件更难能可贵于注塑,同时,减小于焊接面,强度不如直接完全对接。
○2底模定痊:
采用这种设计,塑料件的设计变得简单,但对底模要求高,通常会引致塑料件的平行移位,同时底模固定太紧会影响生产效果。
○3焊头加底模定位:
采用这种设计一般用于特殊情况,并不实用及常用。
○4其它情况:
A:
为大型塑料件可用的一种方式,应注意的是下支撑模具必须支撑住凸缘,上塑料件凸缘必须接触焊头,上塑料件的上表面离凸缘不能太远,如必要情况下,可采用多焊头结构。
B:
如连接中采用能量导向,且将两个焊面注成磨砂表面,可增加摩擦和控制熔化,改善整个焊接的质量和力度,通常磨砂深度是0.07mm-0.15mm。
C:
在焊接不易熔接的树脂或不规则形状时,为了获得密封效果,则有必要插入一个密封圈,需要注意的是密封圈只压在焊接末端。
薄壁零件的焊接,比如热成形的硬纸板(带塑料涂层),与一个塑料盖的焊接。
2.3剪切式设计
在半晶体塑料(如尼龙、乙缩醛、聚丙烯、聚乙烯和热塑聚脂)的熔接中,采用能量导向的连接设计也许达不到理想的效果,这是因为半晶体的树脂会很快从固态转变成融化状态,或者说从融化状态转化为固态。
而且是经过一个相对狭窄的温度范围,从能量导向柱流出的融化物在还没与相接界面融合时,又将很快再固化。
因此,在这种情况下,只要几何原理允许,我们推荐使用剪切连接的结构。
采用剪切连接的设计,首先是熔化小的和最初触的区域来完成焊接,然后当零件嵌入到下起时,继续沿着其垂直壁,用受控的接触面来融化。
这样可能性获得强劲结构或很好的密封效果,因为界面的熔化区域不会让周围的空气进来。
由于此原因,剪切连接尤其对半晶体树脂非常有用。
剪切连接的熔接深度是可以调节的,深度不同所获得的强度不同,熔接深度一般建议为0.8-1.5mm,当塑件壁厚及较厚及强度要求高时,熔接深度建议为1.25X壁厚。
几种基本的剪切式结构:
剪切连接要求一个塑料壁面有足够强度能支持及防止焊接中的偏差,有需要时,底模的支撑高于焊接位,提供辅助的支撑。
UltrasonicWelding3
UltrasonicWelding4.
弯曲/生成
音波将配件的一部分熔化再组成一个塑料的突起部位或塑料管或其它挤出配件。
这种方式的优势在于处理的快速,较小的内压,良好的外观及对材料本性的克服。
点悍
点焊是对没有预留也或能源控制的两个热塑塑料组件的局部焊接。
点焊也能产生一个强有力的粘合构造,尤其适合一些大型配件、有突起的塑料片或浇注的热塑塑料以及那些结构复杂、难以进入接合面的产品。
剪切
切和封口一些有序与无序的热塑材料的超音波工艺。
用这种方法密封的边缘不开裂,且没有毛边、卷边现象。
纺织品/胶片的密封纺织品品及一些胶片的密封也可用到超音波。
它可对胶片实行紧压合,还可对纺织品进行整洁的局部剪切与密封。
缝合的同时也起到了装饰的作用。
影响超音波焊接的因素
说起热塑塑料的可焊接力,不能不说到超音波压合对各种树脂的要求。
其最主要的因素包括聚合物结构,熔化温度、柔韧性(硬度)、化学结构。
聚合物结构
非结晶聚合物分子排列无序、有明显的使材料逐步变软、熔化及至流动的温度(Tg玻璃化温度)。
这类树脂通常能有效传输超音速振动并在相当广泛的压力/振幅范围内实现良好的焊接。
半结晶型聚合物分子排列有序,有明显的熔点(Tm熔化温度)和再度凝固点。
固态的结晶型聚合物是富有弹性的,能吸收部分高频机械振动。
所以此类聚合物是不易于将超声波振动能量传至压合面,帮要求更高的振幅。
需要很高的能量(高熔化热度)才能把半结晶型的结构打断从而使材料从结晶状态变为粘流状态,这也决定了这类材料熔点的明显性,熔化的材料一旦离开热源,温度有所降低便会导致材料的迅速凝固。
所以必须考虑这类材料的特殊性(例如:
高振幅、接合点的良好设计、与超音夹具的有效接触、及优良的工作设备)才能取得超声波焊接的成功。
聚合物:
热塑性与热固性
将单体结合在一起的过程称为“聚合”。
聚合物基本可分为两大类:
热塑性和热固性。
热塑性材料加热成型后还可以重新再次软化和成型,基所经历的只是状态的变化而已-这种特性使决定了热塑性材料超音波压合的适应性。
热固性材料是通过不可逆反的化学反应生成的,再次加热或加压均不能使已成型的热固性产品软化,所以传统上一直认为热固性材料是不适合使用超音波的。
熔化温度
聚合物的熔点越高,其焊接所需的超音波能量越多.
硬度(弹力系数)
材料的硬度对其是否能有效传输超音速振动是很有影响的。
总的说来,愈硬的材料其传导力愈强。
超声波熔接:
以超声波频率振动的焊头,在预定的时间及压力下,磨擦生热,令塑胶接面相互熔合,既牢固,又方便快捷
超声波埋插:
由焊头送到金属及塑胶间的超声波震动,磨擦生热令塑胶接触面熔化,使金属椿挤入塑胶孔内。
超声波铆接,成形包覆:
塑胶件上的梢子,通过金属件的孔,以高震幅焊头震动梢端,使其熔解,顺着焊头的接触面变为铆钉形状,将金属板铆住
超声波点焊
将两层塑胶板焊接,焊头中央的导梢以超波震动攒穿上层塑胶板,由于震动能产生离析,塑胶接面间接产生磨擦热,令两层塑胶板熔接。
二.超声波塑料焊接的相容性和适应性:
热塑性塑料,由于各种型号性质不同,造成有的容易进行超声焊接,有的不易焊接.如图表中黑方块表示两种塑料的相容性好,容易进行超声焊接,圆圈表示在某些情况下相容,焊接性能尚可,空格表示两种塑料相容性很差,不易焊接.
超声波焊接的焊口设计:
两个热塑性塑料零件的超声波焊接要求超声波振动通过焊接头传递到组合件的上半部,最后传至两半的结合处或界面上.在此,振动能量转换成热能,用以熔化塑料.当振动停止后,塑料在压力下固化,在结合面上产生焊接.
两个结合表面的设计,对于获得最佳焊接结果来说是非常重要的.有各种各样的连接设计,每一种都有特色和优点.各种设计的使用取决于许多因素,例如塑料类型、零件几何形状、焊接的要求(即粘性、强度、密封等).
夹具装置:
塑料超声波焊接的一个重要因素是夹具装置.夹具装置的主要用途是固定零件,使之与焊接头对准,同时对组合件提供适当的支撑.被焊接的材料、零件几何形状、壁厚和零件的对称性均可影响能量向界面的传递,因此设计夹具时必须加以考虑.
某些用途,例如铆接和嵌插,要求在焊接头接触区下面有坚硬的承托装置.铝质的夹具装置可提供必要的刚度,可以镀铬来防止零件出现疤痕和提高耐磨性.
在一些用途中,夹具必须具有一定程度的弹性以保证在连结区产生异相状态.异相状态一般在最差的结合处出现,这是待焊接的范围;不过,由于某些零件材料和几何形状,结合的两半可能合成一整体,上下同时振动,如果这种状态出现,将承槽由刚性材料改为弹性材料,或者将硬度计由软性材料改为另一种材料,往往足以在连结区重新建立异相状态.
简单的实验性夹具可用木料、环氧树脂或熟石膏建造.对于更精密、更长寿命的夹具将要用铝、钢、黄铜、铸塑尿烷,或其它的弹性材料.夹具设计范围广,从快速拆卸夹具到简单的金属板均有.应用的要求和生产率通常决定夹具的设计。
上图表示简单的对接焊连接和有能量导向部分的理想连接的时间--温度曲线.能量导向部分允许迅速焊接,同时达到最大的强度.在导向部分的材料如图示在整个结合区内流动.
上图表示焊前按要求比例设计能量导向部分改进对接焊与导致的材料流动.工件尺寸的选择应是如图示能量导向部分熔化后足够分布于结合面之间,通常,对于易焊的树脂能量导向部分最小高度为0.010英寸(0.25毫米).对于某些需要高能量的树脂,即结晶型、低刚度或高熔化温度的非晶型(例如聚碳酸酯、聚砜)树脂,需要较大的能量定向部分,其最小高度为0.020英寸(0.5毫米)。
在工件之间对齐的方法,例如销钉和插口,应包括在工件设计中。
必须指出,为熔剂焊封所作的设计一般可以修改,以符合超声波焊接的要求。
要避免:
能量导向部分设计的典型错误是将结合面削成45度的斜面.
上图表示这样做的结果.
上图表示便于对齐的阶梯式连接.这种连接设计适合于在侧面不宜有过多的熔体或溢料之场合
榫槽连接法:
主要用于焊接和防止内外烧化.不过,需要保持榫舌两侧的间隙使模制较困难.锥度可根据模塑实践经验进行修改,但必须避免在零件之间产生任何障碍。
上图表示适用于超声波焊接的各种基本能量导向连接法,这些可作为典型连接部分的参考,对具体用途应稍作修改。
上图表示需要严密封接时所用的剪切连接法,特别适合于晶型树脂(尼龙、聚甲醛、热塑性聚酯、聚乙烯、聚丙烯和聚苯硫).因为晶型树脂从固态到熔化改变迅速、温度范围窄、能量导向式连接就不是最佳方法,原因是来自导向部分的熔融树脂在它能与相结合的表面熔合之前会迅速凝固.