数控加工中心XY轴系统设计.docx
《数控加工中心XY轴系统设计.docx》由会员分享,可在线阅读,更多相关《数控加工中心XY轴系统设计.docx(34页珍藏版)》请在冰豆网上搜索。
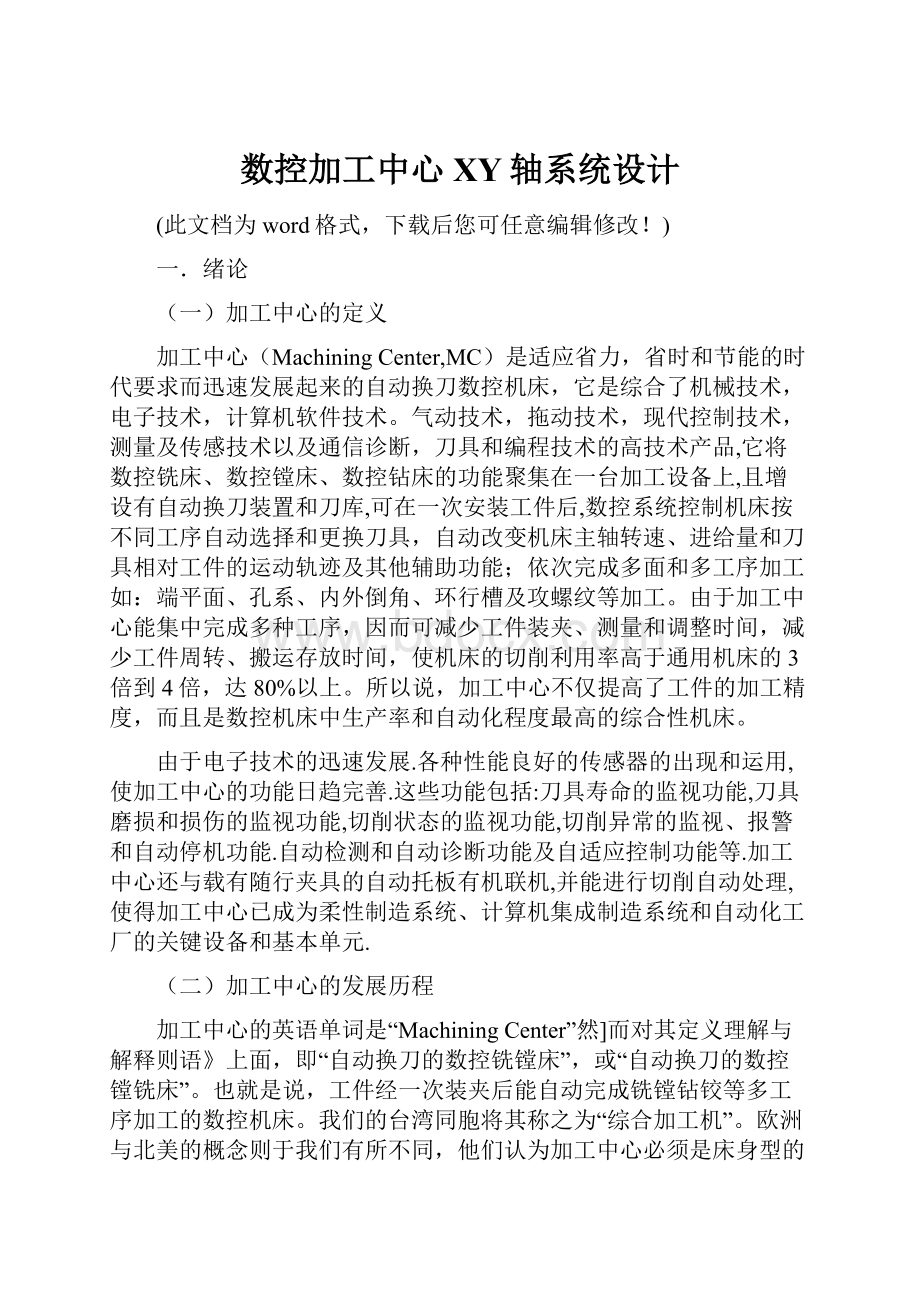
数控加工中心XY轴系统设计
(此文档为word格式,下载后您可任意编辑修改!
)
一.绪论
(一)加工中心的定义
加工中心(MachiningCenter,MC)是适应省力,省时和节能的时代要求而迅速发展起来的自动换刀数控机床,它是综合了机械技术,电子技术,计算机软件技术。
气动技术,拖动技术,现代控制技术,测量及传感技术以及通信诊断,刀具和编程技术的高技术产品,它将数控铣床、数控镗床、数控钻床的功能聚集在一台加工设备上,且增设有自动换刀装置和刀库,可在一次安装工件后,数控系统控制机床按不同工序自动选择和更换刀具,自动改变机床主轴转速、进给量和刀具相对工件的运动轨迹及其他辅助功能;依次完成多面和多工序加工如:
端平面、孔系、内外倒角、环行槽及攻螺纹等加工。
由于加工中心能集中完成多种工序,因而可减少工件装夹、测量和调整时间,减少工件周转、搬运存放时间,使机床的切削利用率高于通用机床的3倍到4倍,达80%以上。
所以说,加工中心不仅提高了工件的加工精度,而且是数控机床中生产率和自动化程度最高的综合性机床。
由于电子技术的迅速发展.各种性能良好的传感器的出现和运用,使加工中心的功能日趋完善.这些功能包括:
刀具寿命的监视功能,刀具磨损和损伤的监视功能,切削状态的监视功能,切削异常的监视、报警和自动停机功能.自动检测和自动诊断功能及自适应控制功能等.加工中心还与载有随行夹具的自动托板有机联机,并能进行切削自动处理,使得加工中心已成为柔性制造系统、计算机集成制造系统和自动化工厂的关键设备和基本单元.
(二)加工中心的发展历程
加工中心的英语单词是“MachiningCenter”然]而对其定义理解与解释则语》上面,即“自动换刀的数控铣镗床”,或“自动换刀的数控镗铣床”。
也就是说,工件经一次装夹后能自动完成铣镗钻铰等多工序加工的数控机床。
我们的台湾同胞将其称之为“综合加工机”。
欧洲与北美的概念则于我们有所不同,他们认为加工中心必须是床身型的,应带有交换工作台,一般用于批量生产,并容易组成FMC或FMS。
他们之所以强调批产,因为他们早在上世纪80年代就对刚性机床(专机)与柔性发展加工中心了。
之所以要指出这点,是因为许多欧美生产的
升降台式加工中心,或不带交换工作台的加工中心,尽管都带刀库可自动换刀,往往有悖中国国情而按他们的习惯,称之为数控镗铣床。
如果这样,这些机床若进口的话,在报关时往往因名称纠葛而引起麻烦,因为数控铣床和加工中心的税率是不同的。
当然也有少数人,他们喜欢借用定义进行混淆,以在报关时达渔利之目的。
随着机床制造技术的不断发展,同时也造成了对加工中心定义的不断挑战。
譬如美国G&L公司曾提出,要忘掉加工中心这个概念!
因此他们开发的当时被誉为未来机床的VARIAX,即国际上首台并联机床,只是六根滑动的柱塞联接上下两个平台,传统的机床床身、立柱等主关零件都被取消了,机床的三向
运动就靠这六根虚拟轴的自由度来控制。
上世纪90年代初瑞士MIKRON公司机床(数控)作过一番发明的Multistep机分析,当时认为,如果床,又体现了一种加工中心每年能制作8机床的新概念,它万个零件,那么选用是把组合加工机床的合理的,否则还是选专效率与加工中心的机。
而现在,随着机床柔性进行最佳结合。
高速加工的不断发展,这种机床的每个工加工中心可年产零件位有两根主轴,共20~25万件,甚至更多,24把刀具;集车、生命力非常旺盛,因此铣、钻、镗等功能于有许多原来擅长于专机一体,机床的每个工的制造商,也纷纷转而位是一个个独立的模块,可按需增加。
机械手可将工件作180°翻转,因此能完成5面加工,换刀速度低于1s,主轴转速可达15000r/min,工件实现全自动上下料。
1992年,德国EMAG创新开发成功的倒置立车,由于其集多种加工功能于一身,故将轻型盘类零件的加工概念,提升到了一个新的高度,因此被誉为“近十年最佳机床”。
90年代中后期发展起来的车、铣复合加工,将多工序复合变成了多工艺复合,从而把加工中心的概念上升到了一个新的层面,奥地利WFL公司的MILL-TURN,是一台既可车、铣、钻、镗,又具有测量功能的高效机床。
它能加工盘类、圆柱类、曲轴类零件,又可加工板类及箱体类零件。
机床卡盘除旋转外,还可分度定位及C轴功能。
装在刀架滑座上的主轴既可自动换刀进行铣削加工,又可装夹车刀直线进给,机床一般为6轴至9轴控制。
目前此类加工中心发展甚热,日本山崎、韩国大宇、奥地利EMCO、德国DMG以及中国沈阳机床等都不断推出新的机种。
山崎甚至认为,这种doneinone技术是技术发展的一大方向。
在不久前结束的日本JIMTOF2004国际机床展上,该公司INTEGREX100ⅢST复合加工中心备受观众青睐。
最近美国哈挺公司又开发了一种LeanMamufacturingCell的组合复合加工单元,将车床主轴系统、铣削的三轴滑台、动力刀架与刀库以及镗铣头结合在一起,来完成零件的复合加工。
总之,复合加工中心的开发正日新月异、层出不穷。
至于复合加工中心如何定义好,此问题我曾请教过当时中国机床工具工业协会总干事长于成廷先生。
他说“国外有人把以铣为主的加工中心称为第一代复合加工中心,以车为主的称为第二代复合加工中心。
这种提法是否妥当,大家可以商量,当然我们自己可以提出新的叫法”。
鉴于此,随着加工中心的不断发展,能否将集车、铣等两种以上工艺功能的自动换刀数控机床定义为综合加工中心。
当然,此粗浅想法仅仅为了抛砖引玉,亟盼专家、同仁们批评赐教。
至于加工中心的发展方向,我始终觉得大隈公司的SPACE提法很有意思。
日本大隈公司(OKUMA)是世界上著名的数控机床与数控系统的制造商。
他们所开发的MA-40、50、60系列卧式加工中心,自称是面向21世纪的SPACECENTER。
这个“SPACE”,不是来自太空这个意思,而是五个英文单词的词首组合。
S——Speed,表示高速度。
MA系列的主轴转速可达25000r/min,主轴启动从0~12000r/min,仅耗时1.9s。
切削速度40m/min,加速度0.5g,换刀速度1.3s。
实现了上述加工参数后,机床的切削时间可比原来缩短50%,非切削时间可缩短15%。
P——Power&Productivity,表示强劲与高效。
该系列机床布局通过FEM有限元分析法,结构采用坐标镗床床身形式,刚性及稳定性强,抗衰性好,特别适用于强力切削。
如切削S45C钢材,面铣金属切除量为705cm3/min;立铣为560cm3/min。
为了持续长时间稳定加工,机床在抑制热变形方面采取了不少措施,如加装可防热源生成的可伸缩盖板及凹槽集屑装置等。
A——Accuracy,表示高精度。
MA系列加工中心,系闭环控制,绝对光栅尺使机床精度胜任一筹。
其定位精度为±1μm;重复定位精度为0.2μm;圆度为
2μm。
交换工作台采用4锥定位机构,使重复定位精度能达到2.5μm。
为防止主轴长期运转所造成的热变形,机床附有V2补偿机构,使主轴30min运转后,主轴近端前轴承处的温升小于20°C。
主轴热变形值小于10μm。
C——Control&communication,表示控制与通讯。
MA系列机床,采用最新的OPS--U100M数控系统,其Hi-G控制功能使定位时间较原来缩短,使运行效率提高15%;由于该系统具有Hi-Cut功能,当高速切削在拐角突跳时,仍能保持良好的连续状态;机床带有绝对位置检测,除当前位置可置原点设定以外,同时不丢失OPS原点位置。
该系列的通讯能力也具有世界先进水平的通讯速度10Mbps数据传输,并可与局域网及广域网联络。
在线加工管理,在办公室内就能监测及管理车间加工状况;计算机DNC通讯能使工艺部门的加工程序编制直接输送到车间内的OSP数控系统上面去。
E——Eclogy,表示生态,即注重环保。
MA系列机床,已注重省资源及省能耗了,并使操作者处于舒适的环境之中。
该系列产品在停止主运行时,液压装置、冷却电机及电磁阀等都自动切断,从而使机床用电减少。
机床逐步采用干切削技术,使润滑油减少20%;油水分离装置使油被分离出来,以防止冷液腐蚀;油雾、粉尘回收装置使大气污染减小到最低程度。
观念是行动的先导,正确把握加工中心的定义,对促进其发展,或许会有些好处的。
(三)加工中心的工作原理
加工中心的工作原理是根据零件图纸,制定工艺方案,采用手工或者计算机自动编程零件加工程序,把零件所需要的机床各种动作及全部工艺参数变成机床的数控装置能接受的信息代码,并把这些代码储存在信息载体(穿孔带、磁盘等)上,将信息载体送到输入装置,读出信息并送入数控装置.信息载体为穿孔带时,输入装置为光电阅读机;磁带输入装置可用招待录音机;时信息载体为磁盘时,可用驱动器输入.以上是最常用的程序输入方法.另一种方法是利用计算机和加工中心直接进行通信,实现零件程序的输入和输出.
进入数控装置的信息,经过一系列处理和运算转变为脉冲信号.有的信号送到机床的伺服系统,通过伺服机构进行转换和放大,再经过传动机构,驱动机床有关零部件,使刀具和工件严格执行零件程序所规定的相应运动.还有的信号送到可编程序控制器中用以顺序控制机床的其它辅助动作,实现刀具自动更换.
(四)加工中心的组成及系列型谱
加工中心的组成随机床的类别、功能、参数的不同而有所不同。
机床本身分基本部件和选择部件,数控系统有基本功能和选用功能,机床参数有主参数和其他参数。
机床制造厂可根据用户提出的要求进行生产,但同类机床产品的基本功能和部件组成一般差别不大。
加工中心的系列型谱,我国尚未制定。
系列尺寸一般按优先数系取:
卧式加工中心,以分度工作台的边长尺寸为其主参数,如320×320,400×400,500×500,630×630,800×800,1000×1000,1250×1250等,其单位为㎜。
立式加工中心,工作台宽度一般取优先数系,长度按实际要求而定。
如320×1000,400×1000,500×1000,630×1200,800×1500,单位为㎜。
型谱一般按生产厂家的习惯或特长取。
如生产铣床的厂家,一般愿意套用铣床型谱,取名为XH×××,如XH754,XH716等;而生产镗床的厂家则愿意套用镗床型谱,取名为TH××××,如TH6350;与国外合作生产或供出口的加工中心,则直接采用国外厂家规定的名称,如SALON—3,RE5020等。
尽管出现了各种类型的加工中心,外型结构各异。
但从总体来看大体上由以下几大部分组成。
(1)基础部分由床身、立柱和工作台等大件组成,是加工中心的基础构件,它们可以是铸铁件,也可以是焊接钢结构件,均要承受加工中心的静载荷以及在加工时的切削载荷。
故必须是刚度很高的部件,亦是加工中心质量和体积最大的部件。
(2)主轴组件它由主轴箱、主轴电机、主轴和主轴轴承等零件组成。
其启动、停止和转动等动作均由数控系统控制,并通过装在主轴上的刀具参与切削运动,是切削加工的功率输出部件。
主轴是加工中心的关键部件,其结构优劣对加工中心的性能有很大的影响。
(3)控制系统单台加工中心的数控部分是由CNC装置、可编程序控制器、伺服驱动装置以及电机等部分组成。
它们是加工中心执行顺序控制动作和完成加工过程中的控制中心。
CNC系统一般由中央处理器、存储器和输入、输出接口组成。
中央处理器又由存储器、运算器、控制器和总线组成。
CNC系统主要特点是输入存储、数据的加工、插补运算以及机床各种控制功能都通过计算机软件来完成,能增加很多逻辑电路中难以实现的功能。
计算机与其他装置之间可通过接口设备联结。
当控制对象改变时,只需改变软件与接口。
(4)伺服系统伺服系统的作用是把来自数控装置的信号转换为机床移动部件的运动,其性能是决定机床的加工精度、表面质量和生产效率的主要因素之一。
加工中心普遍采用半闭环、闭环和混合环三种控制方式。
(5)自动换刀装置它由刀库、机械手和驱动机构等部件组成。
刀库是存放加工过程所使用的全部刀具的装置。
刀库有盘式、鼓式和链式等多种形式,容量从几把到几百把,当需换刀时根据数控系统指令,由机械手(或通过别的方式)将刀具从刀库取出装入主轴中,机械手的结构根据刀库与主轴的相对位置及结构的不同也有多种形式,如单臂式、双臂式、回转式和轨道式等等。
有的加工中心不用机械手而利用主轴箱或刀库的移动来实现换刀。
尽管换刀过程、选刀过程、刀库结构、机械手类型等各种不相同,但都是在数控装置及可编程序控制器控制下,由电机和液压或气动机构驱动刀库和机械手实现刀具的选择与交换。
当机构中装入接触式传感器,还可以实现对刀具和工件误差的测量。
(6)辅助系统包括润滑、冷却、排屑、防护、液压和随机检测系统等部分。
辅助系统虽不直接参加切削运动,但对加工中心的加工效率、加工精度和可靠性起到保障作用。
因此。
也是加工中心不可缺少的部分。
(7)自动托盘更换系统有的加工中心为进一步缩短非切削时间,配有两个自动交换工件托盘,一个安装在工作台上进行加工,另一个则位于工作台外惊醒装卸工件。
当完成一个托盘上的工件加工后,便自动交换托盘,进行新零件的加工,这样可减少辅助时间,提高加工工效。
(五)加工中心的分类
按主轴加工时的空间位置分类有:
卧式和立式加工中心。
卧式加工中心是指主轴轴线水平设置的加工中心。
卧式加工中心有多种形式,如固定立柱式或固定工作台式。
固定立柱式的卧式加工中心的立柱不动,其主轴箱在立柱上做上下移动,而工作台可在两个水平方向移动;固定工作台式的卧式加工中心的三个直线运动坐标方向的运动由立柱和主轴箱的移动来定位,安装工件的工作台是固定不动的(指直线运动)。
卧式加工中心一般具有3个~5个运动坐标轴,常见的是三个直线运动坐标轴和一个回转运动坐标轴(回转工作台),它能在工件一次装夹后完成除安装面和顶面以外的其余四个面的加工,最适合加工箱体类工件。
它与立式加工中心相比,结构复杂、占地面积大、质量大、价格也高。
立式加工中心立式加工中心主轴的轴线为垂直设置,其结构多为固定立柱式,工作台为十字滑台,适合加工盘类零件,一般具有三个直线运动坐标轴,并可在工作台上安置一个水平轴的数控转台(第四轴)来加工螺旋线类零件。
立式加工中心结构简单,占地面积小,价格低,配备各种附件后,可进行大部分工件的加工。
大型龙门式加工中心主轴多为垂直设置,尤其适用于大型或形状复杂的工件,像航空、航天工业及大型汽轮机上的某些零件的加工都需要用这类多坐标龙门式加工中心。
五面加工中心这类加工中心具有立式和卧式加工中心的功能,在工件一次装夹后,能完成除安装面外的所有五个面的加工,这种加工方式可以使工件的形状误差降到最低;省去二次装夹工件,从而提高生产效率,降低加工成本。
常见的五面加工中心有两中形式,一种是主轴可做90°旋转,而主轴不改变方向来完成五面加工。
但是,无论哪种形式的五面加工中心都存在结构复杂、造价高的缺点。
这类加工中心由于加工方式转换时,受机械结构的限制,使可加工空间受到一定限制,故其加工范围比同规格的加工中心要小,而机床的战地面积却大。
正是由于五面加工中心的制造技术复杂,成本高,所以它的使用和生产在数量上远不如其他类型的加工中心。
目前已有立、卧式加工中心;主轴或工作台可连续旋转的5坐标、6坐标或多坐标加工中心,工件一次装夹卡能完成除安装面外的全方位加工。
按工艺用途分类有;
镗铣加工中心镗铣加工中心分为立式镗铣加工中心、卧式镗铣加工中心和龙门镗铣加工中心。
其加工工艺以镗铣为主,用于箱体、壳类以及各种复杂零件特殊曲线和曲面轮廓的多工序加工,适合于多品种小批量生产。
复合加工中心复合加工中心主要指五面复合加工,主轴头可自动回转,进行立、卧加工,在主轴自动回转后,在水平和垂直方向实现刀具自动变换。
按功能特殊分类有:
单工作台、双工作台和多工作台加工中心;
单轴、双轴、三轴及可换主轴箱的加工中心;
立式转塔加工中心和卧式转塔加工中心;
刀库加主轴换刀加工中心;
刀库加机械手加主轴换刀加工中心;
刀库加机械手加双主轴转塔加工中心。
二.加工中心进给系统的机械转动机构
加工中心进给系统的机电传动部件主要有伺服电动机(简称电机)及检测元件、伺服电机与进给丝杠的联结、减速机构(齿轮副或带轮)、滚珠丝杠副(或齿轮齿条副)、死杠支承轴承、运动部件(工作台、主轴箱或立柱)等。
它承担了加工中心各直线坐标轴的定位和切削进给运动,因此将直接影响整机的运行状态和精度指标。
由于滚珠死杠、伺服电机及其控制单元性能提高,很多加工中心的进给系统中已去掉减速机构,采用伺服电机直接与滚珠丝杠连接,因而使整个系统结构简单,减少了产生误差的环节;同时,由于转动惯量减小,使伺服特性亦有所改善。
在整个进给系统中,除上述部件外,还有一个重要环节——导轨。
虽然从表面上看导轨似乎与进给系统关系不十分密切,实际上其运动摩擦力及负载这两个参数在进给系统中占有重要地位。
故导轨的性能对进给系统的影响是不容忽视的。
(一)伺服电机及检测元件
适用于加工中心的伺服驱动电机,有直流伺服电机及其控制单元和交流伺服
驱动电机及其控制单元。
有关直流伺服电机和交流伺服电机的型号及参数可参考有关手册和资料。
与伺服电机配套使用的完成采集移动部件反馈信息的检测元件有两种:
一类是位置检测元件,如旋转变压器、感应间步器、编码盘等;另一类是速度检测元件,一般采用测速发电机和光电脉冲编码器,光电脉冲编码器既可以用来测量位置,又可以用来测量转速。
(二)伺服电机与进给丝杠的连接
在加工中心进给驱动系统中,伺服电机与滚珠丝杠连接,要保证传动无间隙,
只有这样才能准确执行脉冲指令,而不丢掉脉冲。
为此在加工中心上,主要采用三种连接连接方式:
直接连接式、齿轮减速式、齿形带式。
齿轮减速型,则用于因结构上的原因不能直连时,或因负载力矩大,需要放大伺服电机输出扭矩的地方。
这时应特别注意齿轮竟的和啮合间隙状况。
(三)减速机构及齿隙消除
加工中心进给传动系统中的减速机构主要采用齿轮对或带论。
由于加工中心
进给系统经常处于自动变向状态,反向时如果驱动链中的齿轮等传动副存在间隙,酒会造成进给运动的反向运动滞后于指令信号,从而影响其驱动精度。
由于的齿轮的制造不可能达到理想的齿面要求,总是存在着一定的误差,故两个相啮合的齿轮,总有微量的齿侧隙。
因此,必须采取措施消除齿轮传动中的间隙,以提高加工中心进给系统驱动精度。
下面介绍几种在实践中行之有效的消除齿轮传动中侧隙的措施。
(1)圆柱齿轮传动
1)偏心轴套调整法图2—1所示为最简单的偏心轴套式消隙结构。
电机1
通过偏心轴套2装到壳体上,通过转动偏心轴套的转角,就能够方便地调整两啮合齿轮中的中心距,从而消除了圆柱齿轮正、反转时的齿侧隙。
2)锥度齿轮调整法图2—2是用带有锥度齿轮来消除间隙的结构。
在加工齿轮1和2时,将假象的分度圆柱面改变成带有小锥度的圆锥面,使其齿厚在齿轮的轴向略有变化(其外形类似于插齿刀)。
装配时只要改变垫片3的厚度就能调整两个齿轮的轴向相对位置,从而消除了齿侧间隙。
但如增大圆锥角的角度,则将使啮合条件恶化。
图2——2
上述两种方法的特点是结构简单,但齿侧隙调整后不能自动补偿。
3)双片薄齿轮错齿调整法在采用这种齿侧隙的一对啮合齿轮中,其中一个是宽齿轮,另一个是由两相同齿数的薄片齿轮套装而成,两薄片齿轮可相对回转。
装配后,应使一个薄片齿轮的齿左侧和另一个薄片齿轮的齿右侧,分别紧贴在宽齿轮的齿槽左、右两侧,这样错齿后就消除了齿侧隙,反向时不会出现死区。
通常采用的消除方法有两种。
①周向弹簧式图2—3为圆柱薄片齿轮周向弹簧错齿调整法。
在两个薄片齿轮1和2上各开了几条周向圆槽,并在齿轮1和2的端面上各压配有安装弹簧3的短柱4。
在弹簧3的作用下使薄片齿轮1和2错位而消除齿侧隙。
这种结构形式,弹簧3的张力必须足以克服驱动扭矩才能起作用,因而受到圆槽及弹簧尺寸限制,仅适用于读书装置而不适用于驱动装置。
图2—3
②可调拉弹簧图2—4为圆柱薄片齿轮可调拉簧错齿调整法。
在两个薄片齿轮1和2的端面均布着四个螺孔,分别装上凸耳3和8。
齿轮1的端面还有另外四个通孔,凸耳8可以在其中穿过。
弹簧4的两端分别钩在凸耳3和调节螺钉7上,通过螺母5调节弹簧4的拉力,调节完毕后螺母6锁紧。
弹簧的拉力使薄片齿轮错位,即两个薄片齿轮的左右面分别紧贴在宽齿轮齿槽的左右齿面上,从而消除了齿侧间隙。
(2)斜齿轮传动
斜齿轮传动齿侧隙的消除方法基本上与上述错齿调整法相同,也是用两个薄片齿轮和一个宽齿轮啮合,只是在两个薄片斜齿轮的中间隔开了一小段距离,这样它的螺旋线便错开了。
垫片错齿调整法中,薄片齿轮由平键和轴连接,互相不能相对回转。
斜齿轮3和4的齿形拼装在一起加工,并与键槽保持确定的位置。
加工时在两薄片齿轮之间装入已知厚度为t的垫片。
装配时,将垫片厚度增加或减少Δt,然后再用螺母拧紧。
这时两齿轮的螺旋线就产生了错位,其左右两齿面分别与宽齿轮的齿面贴紧,从而消除了间隙。
垫片厚度的增减量Δt可用下式计算出:
Δt=Δcotβ
式中Δ——齿侧隙;
β——斜齿轮的螺旋角。
垫片的厚度通常用试测法确定,一般要经过几次修磨才能调整好,故调整较费时,且齿侧隙不能自动补偿。
轴向压簧错齿调整法,其特点是齿侧隙可自动补偿,但轴向尺寸较大,结构不紧凑。
(3)锥齿轮传动
锥齿轮同圆柱齿轮一样,可用上述类似的方法来消除齿侧隙,通常采用的调整方法有下列两种:
1)轴向压簧调整法图2—5为锥齿轮轴向压簧调整法。
两个啮合的锥齿轮1和5,在其中的一个锥齿轮1的传动轴4上装有压簧2,该锥齿轮在弹簧力的作用下,可稍作轴向移动,从而消除齿侧隙,弹簧力的大小可用螺母3调节。
2)周向弹簧调整法图2—6为锥齿轮压力弹簧消除结构。
将一对啮合锥齿轮中的一个齿轮做成大小两片1和2,在大片锥齿轮1上制成有三个周向圆弧槽4,而在小片锥齿轮2的端面上制有三个凸爪8上,而另一端顶在镶块5上;螺钉7是装配时用的,安装完毕后需将螺钉7卸去,利用弹簧力使大片锥齿轮1和小片锥齿轮2稍微错开,从而达到消除齿侧隙的目的。
(4)双导程蜗杆传动
在数控装置中,常利用大减速比的传动副传动,以提高机床的分辨率。
为提高传动精度,可采用双导程蜗杆来消除间隙,或调整传动副的间隙。
双导程杆是具有微量差的左右侧不等螺距的蜗杆(同一侧仍是相等的),使得蜗杆的齿厚从原始计算剖面向一端线性地增厚,而相反的一端齿厚线性地减薄,因而可用轴向移动蜗杆的方法来消除或调整传动副的间隙。
按啮合原理不同,可分成两种不同的形式。
1)双导程蜗杆蜗轮传动双导程蜗杆蜗轮传动的啮合原理,与普通蜗杆蜗轮无本质差别。
其蜗杆可为阿基米德蜗杆或法向直廓蜗杆,它与普通蜗杆的区别在于左、右齿面具有不等的节距,而同侧齿面的节距则是相等的。
与之啮合的蜗轮则和普通蜗轮一样。
双导程蜗杆蜗轮之间的接触线仍为线接触。
但制造这种高精度的传动副需要专用的高精度双导程蜗轮滚刀。
同时,这种传动副对装配要求高,限制了这种传动副的应用。
2)双导程渐开线蜗杆齿轮传动双导程渐开线蜗杆齿轮传动副的本质是一对渐开线螺旋齿轮传动副。
它的小齿轮是一个渐开线蜗杆,并利用双导程变齿厚的原理,蜗杆左、右两侧的导程不相等(即其轴向模数不相等),而左、右两侧的分度圆柱螺旋角和基圆直径都相等,即它与普通斜齿轮没有什么区别。
这种传动副与普通的双导程蜗杆蜗轮副相比的优点是:
制造方便,用磨齿方法可得到高精度;由于渐开线齿轮传动可分性的特点,因而对箱体上轴线的中心距和轴交角误差不敏感。
但由于它是螺旋齿轮传动,齿面间为点接触,故承载能力不高。
因此,双导程渐开线蜗杆齿轮副仅适用于负载不大的精密数控装置中。
(四)传动装置
加工中心的进给传动链中,传动装置将旋转运动转换为直线运动并带动移动部件移动。
加工中心为提高进给系统的灵敏度、定位精度和防止爬行,必须降低摩擦并减少静、动摩擦系数之差。
通常采用滚珠丝杠螺母副。
(1)滚珠丝杠螺母副
滚珠丝杠螺母副是直线运动和回转运动相互转换的新型传动装置。
1)工作原