压铸件结构设计规范.docx
《压铸件结构设计规范.docx》由会员分享,可在线阅读,更多相关《压铸件结构设计规范.docx(18页珍藏版)》请在冰豆网上搜索。
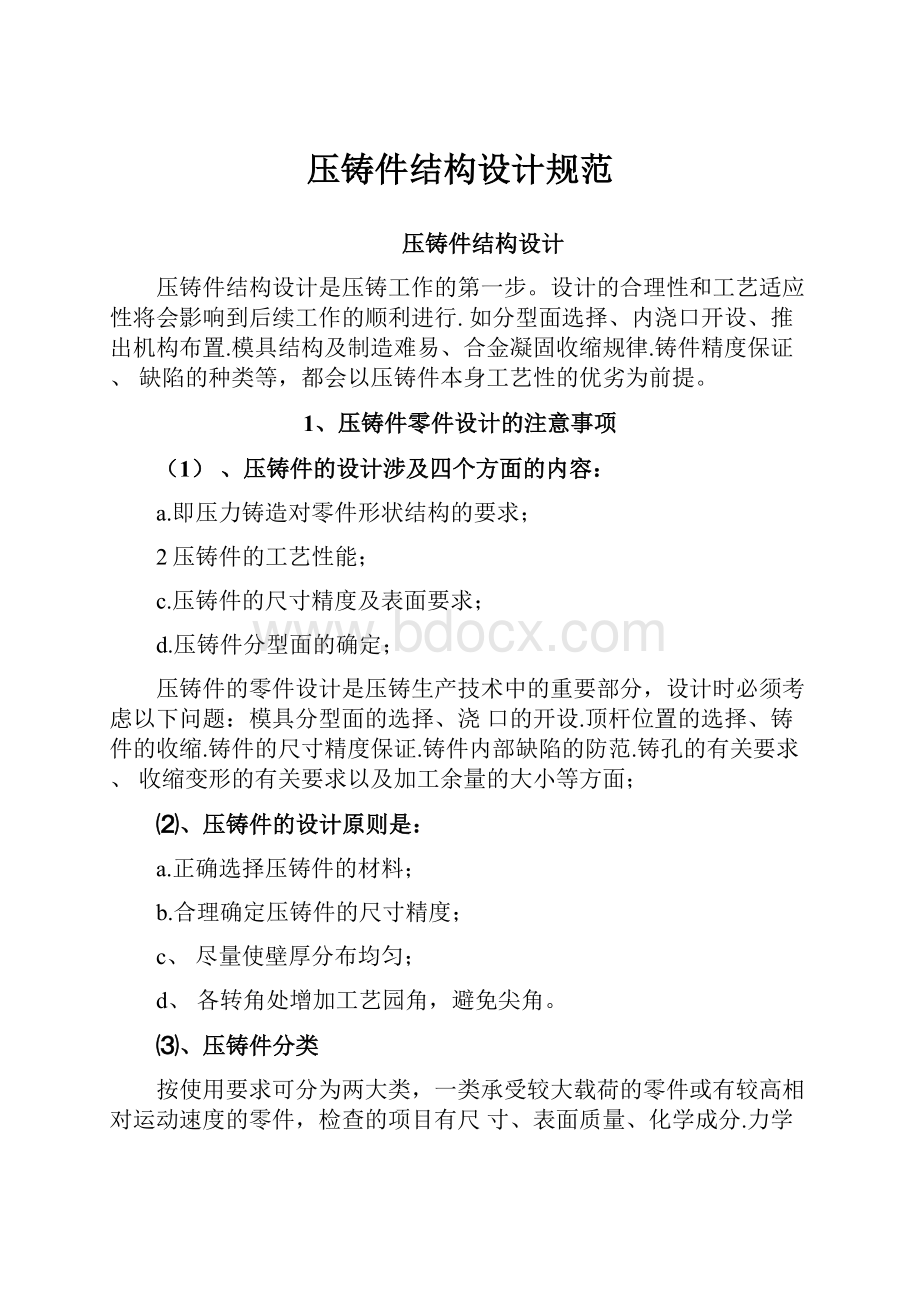
压铸件结构设计规范
压铸件结构设计
压铸件结构设计是压铸工作的第一步。
设计的合理性和工艺适应性将会影响到后续工作的顺利进行.如分型面选择、内浇口开设、推出机构布置.模具结构及制造难易、合金凝固收缩规律.铸件精度保证、缺陷的种类等,都会以压铸件本身工艺性的优劣为前提。
1、压铸件零件设计的注意事项
(1)、压铸件的设计涉及四个方面的内容:
a.即压力铸造对零件形状结构的要求;
2压铸件的工艺性能;
c.压铸件的尺寸精度及表面要求;
d.压铸件分型面的确定;
压铸件的零件设计是压铸生产技术中的重要部分,设计时必须考虑以下问题:
模具分型面的选择、浇口的开设.顶杆位置的选择、铸件的收缩.铸件的尺寸精度保证.铸件内部缺陷的防范.铸孔的有关要求、收缩变形的有关要求以及加工余量的大小等方面;
⑵、压铸件的设计原则是:
a.正确选择压铸件的材料;
b.合理确定压铸件的尺寸精度;
c、尽量使壁厚分布均匀;
d、各转角处增加工艺园角,避免尖角。
⑶、压铸件分类
按使用要求可分为两大类,一类承受较大载荷的零件或有较高相对运动速度的零件,检查的项目有尺寸、表面质量、化学成分.力学性能(抗拉强度、伸长率、硬度);另一类为其它零件,检查的项目有尺寸、表面质量及化学成分。
(
在设计压铸件时,还应该注意零件应满足压铸的工艺要求。
压铸的工艺性从分型面的位置、顶面推杆的位置.铸孔的有关要求、收缩变形的有关要求以及加工余疑的大小等方面考虑。
合理确定压铸面的分型面,不但能简化压铸型的结构,还能保证铸件的质量。
(4)、压铸件结构的工艺性:
1)尽量消除铸件内部侧凹,使模具结构简单。
2)尽量使铸件壁厚均匀,可利用筋减少壁厚,减少铸件气孔、缩孔、变形等缺陷。
3)尽量消除铸件上深孔、深腔。
因为细小型芯易弯曲、折断,深腔处充填和排气不良。
4)设计的铸件要便于脱模、抽芯。
5)肉厚的均一性是必要的。
6)避免尖角。
7)注意拔模角度。
8)注意产品之公差标注。
9)太厚太薄皆不宜。
10)避免死角倒角(能少则少)。
11)考虑后加工的难易度。
12)尽量减少产品内空洞。
13)避免有半岛式的局部太弱的形状。
14)太长的成形孔,或太长的成形柱皆不宜。
'2、压铸件零件设计
⑴、压铸件的形状结构
a、消除内部侧凹;
b、避免或减少抽芯部位;
c、避免型芯交叉;合理的压铸件结构不仅能简化压铸型的结构,降低制造成本,同时也改善铸件质量。
(2).璧星
压铸件的壁厚对铸件质量有很大的影响。
以铝合金为例,薄壁比厚壁具有更高的强度和良好的致密性。
因此,在保证铸件有足够的强度和刚性的条件下,应尽可能减少其壁厚,并保持壁厚均匀一致。
铸件壁太薄时,使金属熔接不好,影响铸件的强度,同时给成型带来困难;壁厚过大或严重不均匀则易产生缩瘪及裂纹。
随着壁厚的增加,铸件内部气孔.缩松等缺陷也随之增多,同样降低铸件的强度。
压铸件的壁厚一般以〜4mm为宜,壁厚超过6mm的篆件不宜采用压铸。
推荐釆用的最小壁厚和正常壁厚见表lo
表1压铸件的最小壁厚和正常壁厚
h
3
夕
壁厚处的面积aX
b(cm2)
锌合金
铝合金
镁合金
铜合金
壁厚h(mm)
最小
正常
最小
正常
最小
正常
最小
正常
W25
>25〜100
>100〜500
>500
最大壁厚与最小壁厚之比不要大于3:
1(应设计壁厚均匀,保证足够强度与刚度的前提)。
压铸件壁厚度(通常称壁厚)是压铸工艺中一个具有特殊意义的因素,壁厚与整个工艺规范有着密切关系,如填充时间的计算.内浇口速度的选择.凝固时间的计算、模具温度梯度的分析.压力(最终比压)的作用、留模时间的长短、铸件顶出温度的高低及操作效率;
a.零件壁厚偏厚会使压铸件的力学性能明显下降,薄壁铸件致密性好,相对提高了铸件强度及耐压性;
b、铸件壁厚不能太薄,太薄会造成铝液填充不良,成型困难,使铝合金熔接不好,铸件表面易产生冷隔等缺陷,并给压铸工艺带来困难;
压铸件随壁厚的增加,其内部气孔、缩孔等缺陷增加,故在保证铸件有足够强度和刚度的前提下,应尽量减小铸件壁厚并保持截面的厚薄均匀一致,为了避免缩松等缺陷,对铸件的厚壁处应减厚(减料),增加筋;对于大面积的平板类厚壁铸件,设置筋以滅少铸件壁厚。
1)压铸件壁厚与性能有关。
2)压铸件壁厚影响金属液填充型腔状态,最终影响铸件表面质量。
3)压铸件壁厚影响金属料消耗及成本。
在设计压铸件时,往往为保证强度和刚度的可靠性,以为壁越厚性能越好;实际上对于压铸件来说,随着壁厚增加,力学性能明显下降。
原因是在压铸过程中,当金属液以高压、高速的状态进入型腔,与型腔表面接触后很快冷却凝固。
受到激冷的压铸件表面形成一层细晶粒组织。
这层致密的细晶粒组织的厚度约为0.3m左右,因此薄壁压铸件具有更高的机械性能。
相反,厚壁压铸件中心层的晶粒较大,易产生内部缩孔、气孔,外表面凹陷等缺陷,使压铸件的机械性能随着壁厚的增加而降低。
9随着壁厚的增加,金属料消耗多,成本也增加。
但如果单从结构性计算出最小壁厚,而忽略了铸件的复杂程度时,也会造成液态金属充填型腔状态不理想,产生缺陷。
在满足产品使用功能要求前提下,综合考虑各后工序过程的影响,以最低的金属消耗取得良好的成型性和工艺性,以采取正常、均匀的壁厚为佳。
⑶、铸造圆角
压铸件各部分相交应有圆角(分型面处除外),使金属填充时流动平稳,气体容易排出,并可避免因锐角而产生裂纹。
对于需要进行电镀和涂饰的压铸件,圆角可以均匀镀层,防止尖角处涂料堆枳。
压铸件的圆角半径R—般不宜小于1伽,最小圆角半径为0.5mm,见表2。
铸造圆角半径的计算见表
3。
说明:
①.对锌合金铸件,K=l/4;对铝.镁.合金铸件,K二1/2。
②.计算后的最小圆角应符合表2的要求。
表2压铸件的最小圆角半径(ran)
压铸合金
圆角半径R
压铸合金
圆角半径R
锌合金
铝、镁合金
铝锡合金
铜合金
表3铸造圆角半径的计算(mm)
压铸件上凡是壁与壁的连接,不论直角、锐角或钝角、盲孔和凹槽的根部,都应设计成圆角,只有当预计确定为分型面的部位上,才不采用圆角连接,其余部位一般必须为圆角,圆角不宜过大或过小,过小
压铸件易产生裂纹•过大易产生疏松缩孔,压铸件圆角一般取:
1/2壁厚WRW壁厚。
圆角的作用是有助于金属的流动,减少涡流或湍流;避免零件上因有圆角的存在而产生应力•集中而导致开裂;当零件要进行电镀或涂覆时,圆角可获得均匀镀层,防止尖角处沉积;可以延长压铸模的使用寿命,不致因模具型腔尖角的存在而导致崩角或开裂。
圆角可使金属液流动顺畅,改善充型持性,气体容易排出。
同时,避免尖角产生应力集中而导致裂纹缺陷。
'穆别是压铸件需要电镀处理时,圆角对于保证其良好的电镀效果是十分必要的。
⑷、拔模斜度
设计压铸件时,就应在结构上留有结构斜度,无结构斜度时,在需要之处,必须有脱模的工艺斜度。
斜度的方向,必须与铸件的脱模方向一致。
推荐的脱模斜度见表4。
表4脱模斜度
<1
说明:
①.由此斜度而引起的铸件尺寸偏差,不计入尺寸公差值内。
合金
配合面的最小脱模斜度
非配合面的最小脱模斜度
外表面a
内表面B
外表面a
内表面[3
锌合金
or10*
•
0°15’
0°15’
0°45’
铝、镁合金
0R15’
0°30’
0°30z
1°
铜合金
0。
30z
0°45’
r
1°30’
2、表中数值仅适用型腔深度或型芯高度W50mni,表面粗糙度在,大端与小端尺寸的单面差的
最小值为0.03mmo当深度或高度〉50mm,或表面粗糙度超过时,则脱模斜度可适当增加。
斜度作用是减少铸件与模具型腔的摩擦,容易取出铸件;保证铸件表面不拉伤;延长压铸模使用寿命,铝合金压铸件一般最小铸造斜度如下:
铝合金压铸件最小的铸造斜度
外表面
内表面
型芯孔(单边)
r
r3(r
2°
为了顺利脱模,减少推出力、抽芯力,减少模具损耗,在设计压铸件时,应在结构上有尽可能大的斜度。
从而减少压铸件与模具的摩擦,容易取出铸件,也使铸件表面不被拉伤,保证表面光洁。
⑸、加强趣
加强筋的设置可以増加零件的强度和刚性,同时改善了压铸的工艺性。
但须注意:
1分布要均匀对称;
2与铸件连接的根部要有圆角;
3避免多筋交叉;
4筋宽不应超过其相连的壁的厚度。
当壁厚小于1・5初时,不宜采用加强筋;
5加强筋的脱模斜度应大于铸件内腔所允许的铸造斜度。
一般采用的加强筋的尺寸按表5选取:
大于或等于mm,会降低抗拉强度,易产生气孔,缩孔。
设计原则:
1.受力大,减小壁厚,改善强度。
2、对称布置,壁厚均匀,避免缩孔气孔。
3、与料流方向一致,避免乱流。
4.避免在肋上设置任何零部件。
筋的作用是壁厚改薄后,用以提高篆件的强度和刚性,防止减少铸件收缩变形.以及避免工件从模具内顶出时发生变形,填充时用以作用辅助回路(金属流动的通路),压铸件筋的厚度应小于所在壁的厚度,一般取该处的厚度的2/3、3/4。
压铸件倾向采用均匀的薄壁,为了提高其强度和刚性,防止变形,不应单纯用增加壁厚的方法,而应釆用适当的薄壁加强筋达此目的。
加强筋应对称布置,厚度均匀,避免新的金属堆聚。
为减少脱模时的阻力,加强筋应有铸造斜度。
⑹、压铸孔和孔到边缘的最小距离
1)铸孔
压铸件的孔径和孔深,对要求不髙的孔可以直接压出,按表5。
表5最小孔径和最大孔深
\孔径合类别、
最小孔径d(mm)
最大孔深(mm)
孔的最小斜度
一般的
技术上可能的
盲孔
通孔
d>5
d<5
d>5
d<5
锌合金
6d
4d
12d
8d
0〜%
铝合金
4d
3d
8d
6d
%〜1%
镁合金
s
5d
4d
lOd
8d
0〜%
铜合金
3d
2d
5d
3d
2%〜4%
说明:
①.表内深度系指固定型芯而言,,对于活动的单个型芯其深度还可以适当增加。
②.对于较大的孔径,精度要求不高时,孔的深度亦可超出上述范围。
铸件的孔应尽量铸出,这不仅可使壁厚均匀,减少热节,节约金属,而且可节省机加工工时。
压铸件可压铸出的孔的最小尺寸和深度,受到形成孔的型芯在型腔中的分布位置的制约。
细型芯在抽出时易弯曲或折断,因此孔的最小尺寸和深度受到一定限制。
其深度应带有一定斜度,以便于抽芯。
对于压铸件自攻螺钉用的底孔,推荐采用的底孔直径见表6。
2)铸孔到边缘的最小距离
为了保证铸件有良好的成型条件•铸孔到铸件边缘应保持一定的壁厚,见图2。
图2
b$(l/4〜l/3)t
当tV时,bM1.5mm
3)长方形孔和槽
压铸件上的长方形孔和槽的设计推荐按表7采用。
表7长方形孔和槽(mm)
•f
合金类别
铅锡合金
锌合金
铝合金
镁合金
铜合金
最小宽度b
最大深度H
210
心12
心10
宀12
210
厚度h
心10
心12
心10
心12
心8
说明:
宽度b在具有铸造斜度时.表内值为小端部位值。
⑺、文字、标志、图案
1)诂压铸铸A应翼用凸纹。
凸纹高度大于0.3叫以适应模具制造的特点。
2)采用目前开始流行的新技术:
“转移彩膜”,可将彩色的文字、标志.图案彩膜转印到压铸件表面。
3)压铸出铸件后,用激光在铸件表面打出文字、标志、图案,可以打出非常细微的文字。
例:
平行纹(直纹)高0.7MM,间距1MM,角度。
外径034.5nm共104牙。
⑻、收缩率
—收缩率通常称为缩水。
它是指合金由液态凝固为固态,并冷却至室温时尺寸缩小的百分数,可用下式
(K=(L模-L件)/L件
式中:
L模为模腔尺寸,L件为铸件尺寸。
收缩率的大小与压铸件的结构特点、壁厚、合金的化学成分和工艺因素等有关。
锌合金的线收缩率一般为:
自由收缩时取%〜%,受阻收缩时取%〜%。
表5为有型芯的锌合金压铸件不同壁厚时的线收缩率参考值。
⑼.螺纹
1)外螺纹可以铸出,由于铸件或模具结构的需要,采用两半分型的螺纹型环时,需留有^0.3mm加工余to可铸出的最小螺距为0.75mm,最小螺纹外径6mm,最大螺纹长为螺距的8倍。
2)内螺纹虽然可以铸出,但要通过使用机械装置转动压铸模中的型芯,使模具结构更复杂,而増加成本。
所以一般先铸出底孔,再由机械加工成内螺纹。
合金
最小螺距(P)
最小螺纹外径
最大螺纹长度
锌
外
内
外
内
6
10
8P
5P
铝
1
]
10
20
6P
4P
Q叭齿轮
齿轮可以铸出,锌合金压铸齿轮最小模数m为。
对要求高的齿轮齿面应留有"0.3mm的加工余量。
0D.表皮
铸态零件其外表面有致密的激冷表皮层比铸件其它部分有较高的力学性能。
因此设计者应避免机械加工去掉铸件表皮致密层,尤其是对要求耐磨的铸件。
■⑫、嵌件
压铸件內采用嵌件的目的:
1改善和提高铸件上局部的工艺性能,如强度、硬度、耐磨性等;
2铸件的某些部分过于复杂,如孔深.内侧凹等无法脱出型芯而采用嵌件;
3可以将几个部件铸成一体。
设计带嵌件的压铸件的注意事项:
1嵌件与压铸件的连接必须牢固,要求在嵌件上开槽、凸起、滚花等;
2嵌件必须避免有尖角,以利安放并防止铸件应力集中;
1③必须考虑嵌件在模具上定位的稳固性,满足模具内配合要求;
4外包嵌件的金属层不应小于〜2mm;
5铸件上的嵌件数量不宜太多;
6铸件和嵌件之间如有严重的电化腐蚀作用,则嵌件表面需要镀层保护;
7有嵌件的铸件应避免热处理,以免因两种金属的相变而引起体积变化,使嵌件松动。
当设计要求将不同材料的零件组合成一个部件时,可采用插入件压铸,先把嵌件装放到压铸模型腔内,然后在嵌件周围压铸成形锌合金部件。
Q9、功能组合
在进行产品设计中,降低成本最有效的方法是将几个零件组合成一个压铸件。
图4是一个设计典范,原设计的部件由一个钢冲压件和两个带螺纹的机加工钢件组成。
新设计是一个压铸件。
人4俎合功能
Q0、压铸件的加工余量
压铸件由于尺寸精度或形位公差达不到产品图纸要求时,应首先考虑釆用精整加工方法,如校正、拉光.挤压、整形等。
必须釆用机加工时应考虑选用较小的加工余量,并尽量以不受分型面及活动成型影响的表面为毛坯基准面。
推荐采用的机加工余疑及其偏差值见表8。
较孔余疑见表9。
表8推荐机加工余量及其偏差(伽)
机加工余量一般取〜0.5mmo
基本尺寸
W100
>100〜250
>250〜400
>400〜630
>630〜1000
毎面余量
卜
+
+
+
1
+1
表9推荐较孔加工余t(mm)
公称孔径D
£6
>6-10
>10〜18
7
>18〜30
>30〜50
>50〜60
较孔余量
3.压铸件的公差等级与精度
一般压铸件精度为IT11级;高精度压铸件为IT13级。
压铸件公差等级CT:
4、6(见表8)。
«8■件尺寸公SKAGe/T6414-1997fISO6062:
1994mm
铸件墓本尺寸
公筮符级
CT4CT5CT6
1076
16-25
25-40
40〜2
2-100
100-160
160〜250250-400
0.
0.
0.
0.
2830323640445056
38
O.
42
4650
56.62.70.78
0.66U.
5458.64707888.02
楮密压铸件的尺寸分类由产品图要求的合理性,
压铸技术保证的可能性,实现批量生产的经济性这三
方面考虑,从压铸毛坯到成品零件的全过程来择定各个尺寸公差。
通常认为,精密压铸件也应当对同一个铸件上的各种尺寸,按照压铸达到各个尺寸公差数值等级的不同而区分为3种类型,即一般尺寸.严格尺
寸和高精度尺寸(见图5)。
§0.2
毎本尺寸/mm
N
①
SS分型面及活动用显对压度的关系示例
①同一半棋囲定邯分的尺寸②受分割面形响的尺寸③受活动成型形响的尺寸
4、镁-铝-锌合金压铸成本和性能对比
压铸类型
合金材料价格/吨浮动
合金比重
压铸件成本对比
单位毛坯件
单位毛坯件
表面处理单
气体保护
压铸耗材
单位压铸件成
对比
重量
材料成本
位成本
成本
成本
本价(不含表面处理成本)
镂合金压
铸
:
万
100g
、—兀
増加10~40%
、元/模次
、元/模次
、元/个
铝合金压
铸
'万
148.9g
、元
装饰件同上结构件无
无
衣于镂合
金
、元/个
锌合金压
铸
、万
394.4g
、元
装饰件同上k构件无
无
低于镂合
金
~元/个
备注:
铝、锌合金结构划
•可以不作身
总面处理,但装饰件表面处理成本与镁合金一样。
SF6气体价格:
8000元/瓶(50公升),24小时开机可用半年;氮气:
22~32元/瓶,可用12小时。
物理性$
总数值比校
材料名称
比重g/cms
融点
X:
导热系数
W/mk
抗拉强度
Mpa
屈服板限
Mpa
延伸率%
抗拉强度与比重之比
杨氏模量
GPa
镂合金(压铸成形)
AZ91
596
72
280
160
8
151
45
AM60
615
62
270
14()
15
151
45
铝合金(压铸成形)
380
595
100
315
160
3
117
71
钢铁
碳素钢
1520
42
517
400
22
66
200
塑料
APS
90仃g)
35
*
40
34
PC
160(Tg)
104
♦
3
85