质检班工作流程.docx
《质检班工作流程.docx》由会员分享,可在线阅读,更多相关《质检班工作流程.docx(10页珍藏版)》请在冰豆网上搜索。
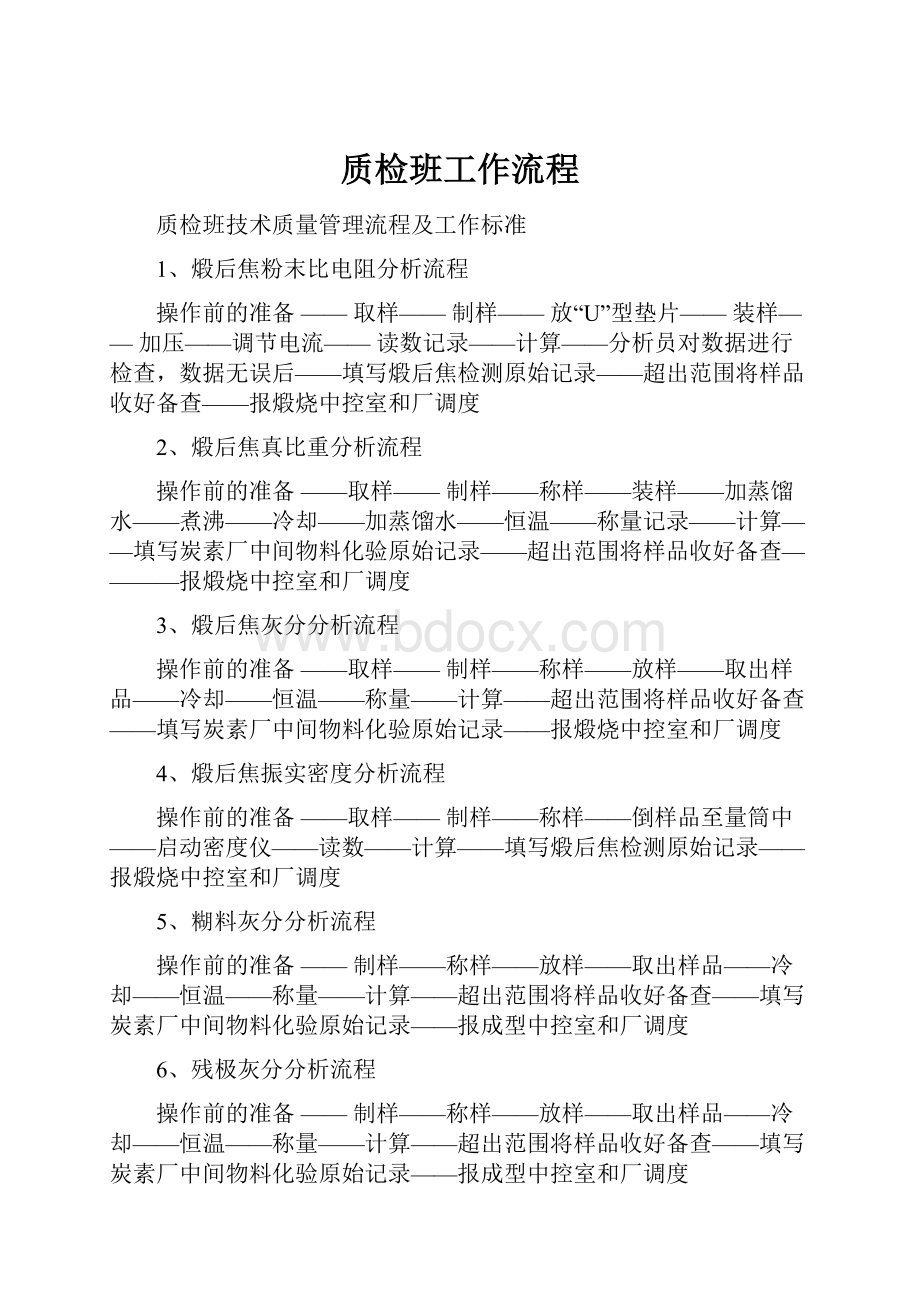
质检班工作流程
质检班技术质量管理流程及工作标准
1、煅后焦粉末比电阻分析流程
操作前的准备——取样——制样——放“U”型垫片——装样——加压——调节电流——读数记录——计算——分析员对数据进行检查,数据无误后——填写煅后焦检测原始记录——超出范围将样品收好备查——报煅烧中控室和厂调度
2、煅后焦真比重分析流程
操作前的准备——取样——制样——称样——装样——加蒸馏水——煮沸——冷却——加蒸馏水——恒温——称量记录——计算——填写炭素厂中间物料化验原始记录——超出范围将样品收好备查————报煅烧中控室和厂调度
3、煅后焦灰分分析流程
操作前的准备——取样——制样——称样——放样——取出样品——冷却——恒温——称量——计算——超出范围将样品收好备查——填写炭素厂中间物料化验原始记录——报煅烧中控室和厂调度
4、煅后焦振实密度分析流程
操作前的准备——取样——制样——称样——倒样品至量筒中——启动密度仪——读数——计算——填写煅后焦检测原始记录——报煅烧中控室和厂调度
5、糊料灰分分析流程
操作前的准备——制样——称样——放样——取出样品——冷却——恒温——称量——计算——超出范围将样品收好备查——填写炭素厂中间物料化验原始记录——报成型中控室和厂调度
6、残极灰分分析流程
操作前的准备——制样——称样——放样——取出样品——冷却——恒温——称量——计算——超出范围将样品收好备查——填写炭素厂中间物料化验原始记录——报成型中控室和厂调度
7、成型物料筛分析流程
操作前的准备——称样——放样——启动振筛机——分别称量记录——填写筛分析记录——报成型中控室和厂调度
8、生块外观检查流程
检查前的准备——确认待检的生阳极块——在每列炭块的两头端面清楚标注质检日期、班次、过检列数——依次测量生阳极块的长、宽、高尺寸——检查生阳极块麻面情况——检查生阳极块有无掉角——检查碳碗有无裂缝——检查阳极的上部表面有无裂缝——检查棒孔的凹陷缺损和裂纹长度——检查四个侧面裂纹——检查大面有无弯曲——检查生块两边高度差——在每块炭块顶面打上过检标示,合格标示“√”,不合格标示“×”并标明作废原因——与成型、堆垛三方交割清楚生阳极过检数及合格数——废品集中时通知成型悬链人员及班长——向炭素厂调度报过检数及合格数
1、煅后焦粉末比电阻工作标准
操作前的准备:
1)、穿戴好相关的劳保用品(工作服、工作鞋、安全帽、防护口罩、劳保手套)
2)、确认所用的设备(颚式破碎机、顶击式振筛机、粉末电阻率测定仪)正常。
3)、准备好所用的工器具(取样桶、取样缸、取样勺、试样袋)
操作标准:
取样:
到煅烧车间煅烧窑冷却机下料口取样1000克左右。
制样:
1)、将试样用四分法缩分至500g,放入颚式破碎机中进行破碎。
2)、将破碎好的干燥试样倒入顶击式振筛机中筛分成三部分(I、IIa和III),如下:
第一部分﹥0.5mm;第IIa部分0.3-0.5mm;第三部分﹤0.5mm。
将第I部分破碎成以0.3-0.5mm为主的颗粒,筛分出0.3-0.5mm作为IIb部分。
将IIa和IIb部分彻底混合,于110℃±5℃烘干2h,贮存在干燥器中备用。
测定:
称取15g-20g试样
1)、在模筒与电极间放上垫片,2)、将试样缓慢倒入模筒中,装满后,将其放在加压架上,3)、缓慢加压至0.04MPa,取下垫片。
然后再缓慢加压至0.64MPa。
加压过程中不要超过设定加压值,等压力充分稳定后(一般调整两次),将选择开关打向电流侧,4)、调节电流输出旋钮,使电流输出至300mA,5)、再将选择开关打向电阻率测量侧,数字显示为该试样电阻率值。
6)、独立地进行两次测定,两个平行试样的绝对误差不应小于5μΩ·m,取其平均值,。
分析员对数据进行检查,数据无误后,填写煅后焦检测原始记录。
7)、超出范围将样品收好备查。
8)、报煅烧中控室和厂调度。
2、煅后焦真比重工作标准
操作前的准备:
1)、穿戴好相关的劳保用品(工作服、工作鞋、安全帽、防护口罩、劳保手套)
2)、确认所用的设备(颚式破碎机、密封化验制样粉碎机、电子天平、电炉、恒温水浴锅)正常。
3)、准备好所用的工器具(取样桶、取样缸、取样勺、比重瓶、滴瓶、洗瓶、短颈漏斗、排笔、表面皿、试样袋)
操作标准:
取样:
到煅烧车间煅烧窑冷却机下料口取样500g左右。
制样:
1)、将试样放入颚式破碎机中破碎。
2)、将破碎好的干燥试样用四分法缩分,取50~60g放入密封化验制样粉碎机进行细碎,全部通过0.15mm的标准筛网。
测定:
1)、称取过100网目的经吸铁后的干燥试样2.0000g(准确至0.0002g)两个。
2)、经漏斗倒入25mL清洁干燥的比重瓶中,用毛刷扫净盘和漏斗上的试样,加蒸馏水至瓶的2/3处。
3)、煮沸3min(不允许有试样溅出),加入蒸馏水,4)、同注入蒸馏水的滴瓶一同放入恒温水浴锅内放入恒温水浴锅内保温30min(水浴锅内水位应与瓶内水位相平)记录水浴锅的温度,用同温度之蒸馏水注满。
5)、塞上玻璃塞,使塞上毛细管充满水柱,并迅速擦掉外溢多余的水滴,用干布擦瓶,用滤纸吸干瓶塞间的水份。
迅速称量。
比重瓶先制定好常用各个温度的水值重量表,测定水值的操作同上。
6)、计算:
真比重={试样重/[(装水瓶重+试样重)-装水和试样的瓶重]}×水的比重。
测定误差:
同一化验室不超过±0.01g/cm3。
不同化验室不超过±0.02g/cm3。
做平行样取其平均值。
7)、分析员对数据进行检查,数据无误后,填写炭素厂中间物料化验原始记录——超出范围将样品收好备查————报煅烧中控室和厂调度。
石油焦经煅烧后密度的测定
1范围
本标准规定了石油焦经煅烧后密度测定方法。
本标准适用于石油焦经煅烧后密度测定。
2方法原理
煅后石油焦在蒸馏水中排气后,用比重瓶法测定其密度。
3仪器和设备
3.1恒温水浴
3.2比重瓶:
25mL
4真密度的测定
称取过100网目的经吸铁后的干燥试样2.0000g(准确至0.0002g)。
经漏斗倒入25mL的比重瓶中,用毛刷扫净盘和漏斗上的试样,加蒸馏水至瓶的2/3处。
加热煮沸后再加少许蒸馏水煮沸3min取下用煮沸过的蒸馏水注满。
放入恒温水浴锅内保温30min(水浴锅内水位应与瓶内水位相平)记录水浴锅的温度,用同温度之蒸馏水注满。
塞上玻璃塞,使塞上毛细管充满水柱,并迅速擦掉外溢多余的水滴,用干布擦瓶,用滤纸吸干瓶塞间的水份。
迅速称量。
比重瓶先制定好常用各个温度的水值重量表,测定水值的操作同上。
5计算
真比重={试样重/[(装水瓶重+试样重)-装水和试样的瓶重]}×水的比重
注:
3.1真比重试样结果以20℃为标准,其他温度须经校正后报出。
a)计算结果时,由试样测定时的温度选用同温度的比重瓶的水值来计算。
并经温度校正后报出。
b)比重瓶各温度的水值需定期(两个月)校正检查。
c)保温温度应在15~20℃之间,以减少因温度差别进行换算和校正时带入的误差。
d)需用酒精法定期进行对照检查,必要时以酒精法来校正结果。
e)当煅后焦挥发份排除不尽,试样易漂浮在水面。
这时应延长煮沸时间以防漂浮物中的空气占据瓶内体积造成偏差。
当煅烧质量不好,真比重指标差时,易出现漂浮现象,此时最好用酒精法作试验。
6测定误差
同一化验室不大于0.01g/cm3。
不同化验室不大于0.02g/cm3。
3、煅后焦灰分工作标准
操作前的准备:
1)、穿戴好相关的劳保用品(工作服、工作鞋、安全帽、防护口罩、劳保手套)
2)、确认所用的设备(颚式破碎机、密封化验制样粉碎机、电子天平、电炉)正常。
3)、准备好所用的工器具(取样桶、取样缸、取样勺、方瓷舟、表面皿、试样袋)
操作标准:
取样:
到煅烧车间煅烧窑冷却机下料口取样500g左右。
制样:
1)、将试样放入颚式破碎机中破碎。
2)、将破碎好的干燥试样用四分法缩分,取50~60g放入密封化验制样粉碎机进行细碎,全部通过0.15mm的标准筛网。
测定:
1)、在预先已恒重的瓷方舟内,称取2g试样精确至0.1mg,薄薄铺平,2)、放在850±20ºC高温炉前边缘上进行预热,以后逐渐将瓷方舟移入恒温区内,灼烧2h,3)、取出放在石棉网上,在空气中冷却5~10min,再放入干燥器内,冷却至室温,称量。
4)、恒重检查:
每次灼烧不少于30min,直至两次称量误差小于0.001g为止。
计算时取最小数值。
结果的计算
试样中灰份含量按下式计算
Am(%)=(m2-m1)×100/m0
式中:
Am——试样灰份值,%;
m0——试样的质量,g;
m1——瓷方舟的质量,g;
m2——灼烧后灰份和瓷方舟的质量,g。
计算值取小数点后两位。
误差
灰份值
误差,%
同一化验室
不同化验室
小于1
0.05
0.1
大于或等于1
0.3
0.5
炭素材料灰份含量测定方法
1范围
本标准规定了炭素材料灰分含量的测定。
本标准适用于炭素材料灰分含量的测定。
2原理
灰份式炭素材料在850±20ºC灼烧至恒重得残余物占原试样量的百分含量。
3仪器和设备
3.1分析天平:
感量0.1mg。
3.2瓷方舟
3.3玻璃干燥器:
内装变色硅胶。
3.4坩埚钳
3.5高温炉
3.5.1带有调温装置,能保持850±20ºC,并附有热电偶和温度指示仪表。
3.5.2高温炉后壁具有插入热电偶的圆形孔。
孔的位置应使热电偶的热接触点在炉中恒温区内,炉门有一圆孔(直径ø15~20mm)。
4试样
4.1干燥的试样:
粒度不大于20mm,重量不小于0.5kg。
4.2试样用四分法缩分,取50~60g进行破碎,全部通过0.15mm网孔的标准筛网。
5试验步骤
5.1在预先已恒重的瓷方舟内,称取3g试样精确至0.1mg,薄薄铺平,放在850±20ºC高温炉前边缘上进行预热,以后逐渐将瓷方舟移入恒温区内,灼烧3h,取出放在石棉网上,在空气中冷却5~10min,再放入干燥器内,冷却至室温,称量。
5.2恒重检查:
每次灼烧不少于30min,直至两次称量误差小于0.001g为止。
计算时取最小数值。
注:
(1)多灰试样灰份大于1时,称取1g试样。
(2)炭糊试样粒度为0.5mm。
(3)电解后的底块试样,制样时需清除掉表面电解质,粒度为0.3mm,称3g试样,在温度760±10ºC灼烧至
恒重。
6结果的计算
6.1试样中灰份含量按下式计算
Am(%)=(m2-m1)×100/m0
式中:
Am——试样灰份值,%;
m0——试样的质量,g;
m1——瓷方舟的质量,g;
m2——灼烧后灰份和瓷方舟的质量,g。
6.2计算值取小数点后两位。
7实验误差
灰份值
误差,%
同一化验室
不同化验室
小于1
0.05
0.1
大于或等于1
0.3
0.5
4、煅后焦振实密度工作标准
操作前的准备:
1)、穿戴好相关的劳保用品(工作服、工作鞋、安全帽、防护口罩、劳保手套)
2)、确认所用的设备(颚式破碎机、顶击式振筛机、散料振实密度仪)正常。
3)、准备好所用的工器具(取样桶、取样缸、筛具)
操作标准:
取样:
到煅烧车间煅烧窑冷却机下料口取样4kg克左右。
制样:
1)、将试样放入颚式破碎机中进行破碎。
2)、将破碎好的试样按照所需粒级进行筛分。
3)、分别称取样品500g。
测定:
1)、将称好的样品倒入密度仪的量筒中,将料面拨平。
2)、打开密度仪的电源开关
3)、调整密度仪的冲程数到要求值。
4)、按下启动键C。
5)、待冲程结束后,将料面拨平,读取样品的体积值。
6)、根据:
密度=质量/体积,计算结果。
7)、分析员对数据进行检查,数据无误后,填写煅后焦检测原始记录。
8)、报煅烧中控室和厂调度。
9)、结果超出范围四小时重新取样检测。
5、糊料灰分工作标准
6、残极灰分工作标准
7、成型物料筛分工作标准
称样——放样——启动振筛机——分别称量记录——填写筛分析记录——报成型中控室和厂调度
操作前的准备:
1)、穿戴好相关的劳保用品(工作服、工作鞋、安全帽、防护口罩、劳保手套)
2)、确认所用的设备(电子天平、顶击式振筛机)正常。
3)、准备好所用的工器具(取样勺、表面皿)
操作标准:
1)、用电子天平分别准确称量各种试样100g,放置好待用。
2)、将筛具按所需的顺序放好,将称好的物料倒入振筛机中,拧紧筛顶。
3)、打开振筛机电源,设定好时间,启动振筛机。
(细焦、细残筛分10分钟,粉料筛分15分钟)4)、振筛机停止后,打开筛顶,确认拧紧后取出筛具。
5)、用电子天平分别称取各筛具上的物料,并作好记录。
6)、根据所记录的数据计算误差值(在±0.5g)7)、分析员对数据进行检查,数据无误后,填写筛分记录。
将结果反馈至成型车间。
8、生块外观检查工作标准