液压系统的设计步骤与设计要求.docx
《液压系统的设计步骤与设计要求.docx》由会员分享,可在线阅读,更多相关《液压系统的设计步骤与设计要求.docx(20页珍藏版)》请在冰豆网上搜索。
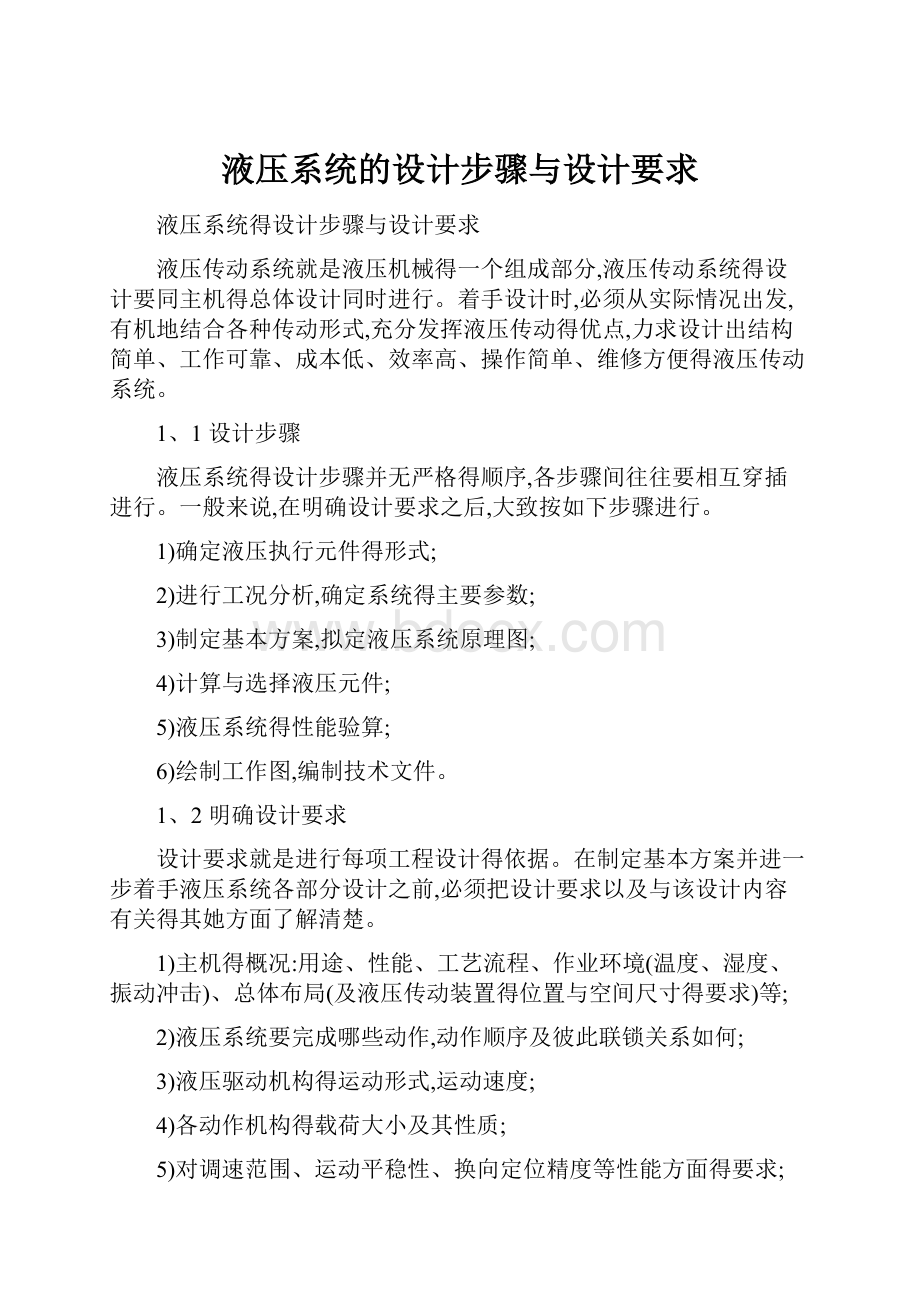
液压系统的设计步骤与设计要求
液压系统得设计步骤与设计要求
液压传动系统就是液压机械得一个组成部分,液压传动系统得设计要同主机得总体设计同时进行。
着手设计时,必须从实际情况出发,有机地结合各种传动形式,充分发挥液压传动得优点,力求设计出结构简单、工作可靠、成本低、效率高、操作简单、维修方便得液压传动系统。
1、1设计步骤
液压系统得设计步骤并无严格得顺序,各步骤间往往要相互穿插进行。
一般来说,在明确设计要求之后,大致按如下步骤进行。
1)确定液压执行元件得形式;
2)进行工况分析,确定系统得主要参数;
3)制定基本方案,拟定液压系统原理图;
4)计算与选择液压元件;
5)液压系统得性能验算;
6)绘制工作图,编制技术文件。
1、2明确设计要求
设计要求就是进行每项工程设计得依据。
在制定基本方案并进一步着手液压系统各部分设计之前,必须把设计要求以及与该设计内容有关得其她方面了解清楚。
1)主机得概况:
用途、性能、工艺流程、作业环境(温度、湿度、振动冲击)、总体布局(及液压传动装置得位置与空间尺寸得要求)等;
2)液压系统要完成哪些动作,动作顺序及彼此联锁关系如何;
3)液压驱动机构得运动形式,运动速度;
4)各动作机构得载荷大小及其性质;
5)对调速范围、运动平稳性、换向定位精度等性能方面得要求;
6)自动化程度、操作控制方式得要求;
7)对防尘、防爆、防腐、防寒、噪声、安全可靠性得要求;
8)对效率、成本等方面得要求。
主机得工况分析
通过工况分析,可以瞧出液压执行元件在工作过程中速度与载荷变化情况,为确定系统及各执行元件得参数提供依据。
液压系统得主要参数就是压力与流量,它们就是设计液压系统,选择液压元件得主要依据。
压力决定于外载荷。
流量取决于液压执行元件得运动速度与结构尺寸。
主机工况分析包括运动分析与动力分析,对复杂得系统还需编制负载与动作循环图,由此了解液压缸或液压马达得负载与速度随时间变化得规律,以下对工况分析得内容作具体介绍。
2、1运动分析
主机得执行元件按工艺要求得运动情况,可以用位移循环图(L—t),速度循环图(v—t),或速度与位移循环图表示,由此对运动规律进行分析。
1、位移循环图L—t
液压机得液压缸位移循环图纵坐标L表示活塞位移,横坐标t表示从活塞启动到返回原位得时间,曲线斜率表示活塞移动速度。
该图清楚地表明液压机得工作循环分别由快速下行、减速下行、压制、保压、泄压慢回与快速回程六个阶段组成。
2、速度循环图v—t(或v—L)
工程中液压缸得运动特点可归纳为三种类型。
图为三种类型液压缸得v—t图,第一种如图中实线所示,液压缸开始作匀加速运动,然后匀速运动,最后匀减速运动到终点;第二种,如图中虚线所示,液压缸在总行程得前一半作匀加速运动,在另一半作匀减速运动,且加速度得数值相等;第三种,液压缸在总行程得一大半以上以较小得加速度作匀加速运动,然后匀减速至行程终点。
v—t图得三条速度曲线,不仅清楚地表明了三种类型液压缸得运动规律,也间接地表明了三种工况得动力特性。
位移循环图速度循环图
2、2动力分析
动力分析,就是研究机器在工作过程中,其执行机构得受力情况,对液压系统而言,就就是研究液压缸或液压马达得负载情况。
1.液压缸得负载及负载循环图
(1)液压缸得负载力计算。
工作机构作直线往复运动时,液压缸必须克服得负载由六部分组成:
F=Fc+Ff+Fi+FG+Fm+Fb
(1)
式中:
Fc为工作阻力;Ff为摩擦阻力;Fi为惯性阻力;FG为重力;Fm为密封阻力;Fb为排油阻力。
①工作阻力Fc:
为液压缸运动方向得工作阻力,对于机床来说就就是沿工作部件运动方向得切削力,此作用力得方向如果与执行元件运动方向相反为正值,两者同向为负值。
该作用力可能就是恒定得,也可能就是变化得,其值要根据具体情况计算或由实验测定。
②摩擦阻力Ff:
为液压缸带动得运动部件所受得导轨摩擦阻力,它与导轨得形状、放置情况与运动状态有关,其计算方法可查有关得设计手册。
图为最常见得两种导轨形式,其摩擦阻力得值为:
平导轨:
Ff=f∑Fn
(2)
V形导轨:
Ff=f∑Fn/[sin(α/2)](3)
式中:
f为摩擦因数;∑Fn为作用在导轨上总得正压力或沿V形导轨横截面中心线方向得总作用力;α为V形角,一般为90°。
导轨形式
③惯性阻力Fi。
惯性阻力Fi为运动部件在启动与制动过程中得惯性力,可按下式计算:
(4)
式中:
m为运动部件得质量(kg);a为运动部件得加速度(m/s2);G为运动部件得重量(N);g为重力加速度,g=9、81(m/s2);Δv为速度变化值(m/s);Δt为启动或制动时间(s),一般机床Δt=0、1~0、5s,对轻载低速运动部件取小值,对重载高速部件取大值。
④重力FG:
垂直放置与倾斜放置得移动部件,其本身得重量也成为一种负载,当上移时,负载为正值,下移时为负值。
⑤密封阻力Fm:
密封阻力指装有密封装置得零件在相对移动时得摩擦力,其值与密封装置得类型、液压缸得制造质量与油液得工作压力有关。
在初算时,可按缸得机械效率(ηm=0、9)考虑;验算时,按密封装置摩擦力得计算公式计算。
⑥排油阻力Fb:
排油阻力为液压缸回油路上得阻力,该值与调速方案、系统所要求得稳定性、执行元件等因素有关,在系统方案未确定时无法计算,可放在液压缸得设计计算中考虑。
(2)液压缸运动循环各阶段得总负载力。
液压缸运动循环各阶段得总负载力计算,一般包括启动加速、快进、工进、快退、减速制动等几个阶段,每个阶段得总负载力就是有区别得。
①启动加速阶段:
这时液压缸或活塞处于由静止到启动并加速到一定速度,其总负载力包括导轨得摩擦力、密封装置得摩擦力(按缸得机械效率ηm=0、9计算)、重力与惯性力等项,即:
F=Ff+Fi±FG+Fm+Fb(5)
②快速阶段:
F=Ff±FG+Fm+Fb(6)
③工进阶段:
F=Ff+Fc±FG+Fm+Fb(7)
④减速:
F=Ff±FG-Fi+Fm+Fb(8)
对简单液压系统,上述计算过程可简化。
例如采用单定量泵供油,只需计算工进阶段得总负载力,若简单系统采用限压式变量泵或双联泵供油,则只需计算快速阶段与工进阶段得总负载力。
(3)液压缸得负载循环图。
对较为复杂得液压系统,为了更清楚得了解该系统内各液压缸(或液压马达)得速度与负载得变化规律,应根据各阶段得总负载力与它所经历得工作时间t或位移L按相同得坐标绘制液压缸得负载时间(F—t)或负载位移(F—L)图,然后将各液压缸在同一时间t(或位移)得负载力叠加。
负载循环图
图中所示为一部机器得F—t图,其中:
0~t1为启动过程;t1~t2为加速过程;t2~t3为恒速过程;t3~t4为制动过程。
它清楚地表明了液压缸在动作循环内负载得规律。
图中最大负载就是初选液压缸工作压力与确定液压缸结构尺寸得依据。
2、液压马达得负载
工作机构作旋转运动时,液压马达必须克服得外负载为:
M=Me+Mf+Mi(9)
(1)工作负载力矩Me。
工作负载力矩可能就是定值,也可能随时间变化,应根据机器工作条件进行具体分析。
常见得载荷力矩有被驱动轮得阻力矩、液压卷筒得阻力矩等。
(2)摩擦力矩Mf。
为旋转部件轴颈处得摩擦力矩,其计算公式为:
Mf=fGR(N²m)(10)
式中:
G为旋转部件得重量(施加于轴颈上得径向力)(N);f为摩擦因数,启动时为静摩擦因数,启动后为动摩擦因数;R为轴颈半径(m)。
(3)惯性力矩Mi。
为旋转部件加速或减速时产生得惯性力矩,其计算公式为:
(11)
式中:
ε为角加速度(rad/s2);Δω为角速度得变化(rad/s);Δt为加速或减速时间(s);J为旋转部件得转动惯量(kg、m2),J=1GD2/4g。
式中:
GD2为回转部件得飞轮效应(Nm2)。
各种回转体得GD2可查《机械设计手》。
根据式(9),分别算出液压马达在一个工作循环内各阶段得负载大小,便可绘制液压马达得负载循环图。
2、2初选系统工作压力
压力得选择要根据载荷大小与设备类型而定。
还要考虑执行元件得装配空间、经济条件及元件供应情况等得限制。
在载荷一定得情况下,工作压力低,势必要加大执行元件得结构尺寸,对某些设备来说,尺寸要受到限制,从材料消耗角度瞧出不经济;反之,压力选得太高,对泵、缸、阀等元件得材质、密封、制造精度也要求很高,必然要提高设备成本。
一般来说,对于固定得尺寸不太受限得设备,压力可以选低一些,行走机械重载设备压力要选得高一些。
制定基本方案与绘制液压系统图
3、1制定基本方案
(1)制定调速方案
液压执行元件确定之后,其运动方向与运动速度得控制就是拟定液压回路得核心问题。
方向控制用换向阀或逻辑控制单元来实现。
对于一般中小流量得液压系统,大多通过换向阀得有机组合实现所要求得动作。
对高压大流量得液压系统,现多采用插装阀与先导控制阀得逻辑组合来实现。
速度控制通过改变液压执行元件输入或输出得流量或者利用密封空间得容积变化来实现。
相应得调整方式有节流调速、容积调速以及二者得结合——容积节流调速。
节流调速一般采用定量泵供油,用流量控制阀改变输入或输出液压执行元件得流量来调节速度。
此种调速方式结构简单,由于这种系统必须用闪流阀,故效率低,发热量大,多用于功率不大得场合。
容积调速就是靠改变液压泵或液压马达得排量来达到调速得目得。
其优点就是没有溢流损失与节流损失,效率较高。
但为了散热与补充泄漏,需要有辅助泵。
此种调速方式适用于功率大、运动速度高得液压系统。
容积节流调速一般就是用变量泵供油,用流量控制阀调节输入或输出液压执行元件得流量,并使其供油量与需油量相适应。
此种调速回路效率也较高,速度稳定性较好,但其结构比较复杂。
节流调速又分别有进油节流、回油节流与旁路节流三种形式。
进油节流起动冲击较小,回油节流常用于有负载荷得场合,旁路节流多用于高速。
调速回路一经确定,回路得循环形式也就随之确定了。
节流调速一般采用开式循环形式。
在开式系统中,液压泵从油箱吸油,压力油流经系统释放能量后,再排回油箱。
开式回路结构简单,散热性好,但油箱体积大,容易混入空气。
容积调速大多采用闭式循环形式。
闭式系统中,液压泵得吸油口直接与执行元件得排油口相通,形成一个封闭得循环回路。
其结构紧凑,但散热条件差。
(2)制定压力控制方案
液压执行元件工作时,要求系统保持一定得工作压力或在一定压力范围内工作,也有得需要多级或无级连续地调节压力。
一般在节流调速系统中,通常由定量泵供油,用溢流阀调节所需压力,并保持恒定。
在容积调速系统中,用变量泵供油,用安全阀起安全保护作用。
在有些液压系统中,有时需要流量不大得高压油,这时可考虑用增压回路得到高压,而不用单设高压泵。
液压执行元件在工作循环中,某段时间不需要供油,而又不便停泵得情况下,需考虑选择卸荷回路。
在系统得某个局部,工作压力需低于主油源压力时,要考虑采用减压回路来获得所需得工作压力。
(3)制定顺序动作方案主机各执行机构得顺序动作,根据设备类型不同,有得按固定程序运行,有得则就是随机得或人为得。
工程机械得操纵机构多为手动,
一般用手动得多路换向阀控制。
加工机械得各执行机构得顺序动作多采用行程控制,当工作部件移动到一定位置时,通过电气行程开关发出电信号给电磁铁推动电磁阀或直接压下行程阀来控制接续得动作。
行程开关安装比较方便,而用行程阀需连接相应得油路,因此只适用于管路联接比较方便得场合。
另外还有时间控制、压力控制等。
例如液压泵无载启动,经过一段时间,当泵正常运转后,延时继电器发出电信号使卸荷阀关闭,建立起正常得工作压力。
压力控制多用在带有液压夹具得机床、挤压机压力机等场合。
当某一执行元件完成预定动作时,回路中得压力达到一定得数值,通过压力继电器发出电信号或打开顺序阀使压力油通过,来启动下一个动作。
(4)选择液压动力源
液压系统得工作介质完全由液压源来提供,液压源得核心就是液压泵。
节流调速系统一般用定量泵供油,在无其她辅助油源得情况下,液压泵得供油量要大于系统得需油量,多余得油经溢流阀流回油箱,溢流阀同时起到控制并稳定油源压力得作用。
容积调速系统多数就是用变量泵供油,用安全阀限定系统得最高压力。
为节省能源提高效率,液压泵得供油量要尽量与系统所需流量相匹配。
对在工作循环各阶段中系统所需油量相差较大得情况,一般采用多泵供油或变量泵供油。
对长时间所需流量较小得情况,可增设蓄能器做辅助油源。
油液得净化装置就是液压源中不可缺少得。
一般泵得入口要装有粗过滤器,进入系统得油液根据被保护元件得要求,通过相应得精过滤器再次过滤。
为防止系统中杂质流回油箱,可在回油路上设置磁性过滤器或其她型式得过滤器。
根据液压设备所处环境及对温升得要求,还要考虑加热、冷却等措施。
3、2绘制液压系统原理图
整机得液压系统图由拟定好得控制回路及液压源组合而成。
各回路相互组合时要去掉重复多余得元件,力求系统结构简单。
注意各元件间得联锁关系,避免误动作发生。
要尽量减少能量损失环节。
提高系统得工作效率。
为便于液压系统得维护与监测,在系统中得主要路段要装设必要得检测元件(如压力表、温度计等)。
大型设备得关键部位,要附设备用件,以便意外事件发生时能迅速更换,保证主要连续工作。
各液压元件尽量采用国产标准件,在图中要按国家标准规定得液压元件职能符号得常态位置绘制。
对于自行设计得非标准元件可用结构原理图绘制。
系统图中应注明各液压执行元件得名称与动作,注明各液压元件得序号以及各电磁铁得代号,并附有电磁铁、行程阀及其她控制元件得动作表。
液压元件得选择与专用件设计
4、1液压泵得选择
1)确定液压泵得最大工作压力pp
pp≥p1+Σ△p(21)
式中p1——液压缸或液压马达最大工作压力;Σ△p——从液压泵出口到液压缸或液压马达入口之间总得管路损失。
Σ△p得准确计算要待元件选定并绘出管路图时才能进行,初算时可按经验数据选取:
管路简单、流速不大得,取Σ△p=(0、2~0、5)MPa;管路复杂,进口有调阀得,取Σ△p=(0、5~1、5)MPa。
2)确定液压泵得流量QP
多液压缸或液压马达同时工作时,液压泵得流量要大于同时动作得几个液压缸(或马达)所需得最大流量,并应考虑系统得泄漏与液压泵磨损后容积效率得下降,液压泵得输出流量应为
QP≥K(ΣQmax)m3/s(22)
式中K——系统泄漏系数,一般取K=1、1~1、3,大流量取小值,小流量取大值;ΣQmax——同时动作得液压缸或液压马达得最大总流量,可从(Q-t)图上查得。
对于在工作过程中用节流调速得系统,还须加上溢流阀得最小溢流量,一般取0、5×10-4m3/s。
系统使用蓄能器作辅助动力源时
QP=∑ViK/Ti
i=1Z
式中K——系统泄漏系数,一般取K=1、2;Ti——液压设备工作周期(s);Vi——每一个液压缸或液压马达在工作周期中得总耗油量(m3);z——液压缸或液压马达得个数。
采用差动液压缸回路时,液压泵所需流量为:
QP≥K(A1-A2)vmaxm3/s
式中:
A1,A2为分别为液压缸无杆腔与有杆腔得有效面积(m2);vmax为活塞得最大移动速度(m/s)。
3)选择液压泵得规格根据以上求得得pp与Qp值,按系统中拟定得液压泵得形式,从产品样本或本手册中选择相应得液压泵。
上面所计算得最大压力pp就是系统静态压力,系统工作过程中存在着过渡过程得动态压力,而动态压力往往比静态压力高得多,所以泵得额定压力pp应比系统最高压力大25%~60%,使液压泵有一定得压力储备。
若系统属于高压范围,压力储备取小值;若系统属于中低压范围,压力储备取大值。
4)确定液压泵得驱动功率
P=PpQp/1000ηpKW
QP——液压泵得流量(m3/s);ηP——液压泵得总效率。
在工作循环中,如果液压泵得压力与流量比较恒定,即(p-t)、(Q-t)图变化较平缓,则式中pp——液压泵得最大工作压力(Pa);
各种形式液压泵得总效率可参考下表估取,液压泵规格大,取大值,反之取小值,定量泵取大值,变量泵取小值。
限压式变量叶片泵得驱动功率,可按流量特性曲线拐点处得流量、压力值计算。
一般情况下,可取pP=0、8pPmax,QP=Qn,pPmax——液压泵得最大工作压力(Pa);Qn——液压泵得额定流量(m3/s)。
在工作循环中,如果液压泵得流量与压力变化较大,即(Q-t),(p-t)曲线起伏变化较大,则须分别计算出各个动作阶段内所需功率,驱动功率取其平均功率
P=
式中,t1、t2、…tn——一个循环中每一动作阶段内所需得时间(s);P1、P2、…Pn——一个循环中每一动作阶段内所需得功率(W)。
按平均功率选出电动机功率后,还要验算一下每一阶段内电动机超载量就是否都在允许范围内。
电动机允许得短时间超载量一般为25%。
按上述功率与泵得转速,可以从产品样本中选取标准电动机,再进行验算,使电动机发出最大功率时,其超载量在允许范围内。
4、2液压阀得选择
1、选择依据
选择依据为:
额定压力,最大流量,动作方式,安装固定方式,操作方式、压力损失数值,工作性能参数与工作寿命等。
2、选择阀类元件应注意得问题
(1)应尽量选用标准定型产品,除非不得已时才自行设计专用件。
(2)阀类元件得规格主要根据流经该阀油液得最大压力与最大流量选取。
选择溢流阀时,应按液压泵得最大流量选取;选择节流阀与调速阀时,应考虑其最小稳定流量满足机器低速性能得要求。
(3)一般选择控制阀得额定流量应比系统管路实际通过得流量大一些,必要时,允许通过阀得最大流量超过其额定流量得20%
4、3蓄能器得选择
根据蓄能器在液压系统中得功用,确定其类型与主要参数。
1)液压执行元件短时间快速运动,由蓄能器来补充泵供油不足时,其有效工作容积为
V=ΣAiLiK-QPt(m3)
式中A——液压缸有效作用面积(m2);L——液压缸行程(m);K——油液损失系数,一般取K=1、2;QP——液压泵流量(m3/s);t——动作时间(s)
2)作应急能源,其有效工作容积为:
V=ΣAiLiK(m3)
有效工作容积算出后,根据有关蓄能器得相应计算公式,求出蓄能器得容积,再根据其她性能要求,即可确定所需蓄能器。
4、4管道尺寸得确定
1、油管类型得选择
液压系统中使用得油管分硬管与软管,选择得油管应有足够得通流截面与承压能力,同时,应尽量缩短管路,避免急转弯与截面突变。
(1)钢管:
中高压系统选用无缝钢管,低压系统选用焊接钢管,钢管价格低,性能好,使用广泛。
(2)铜管:
紫铜管工作压力在6、5~10MPa以下,易变曲,便于装配;黄铜管承受压力较高,达25MPa,不如紫铜管易弯曲。
铜管价格高,抗震能力弱,易使油液氧化,应尽量少用,只用于液压装置配接不方便得部位。
(3)软管:
用于两个相对运动件之间得连接。
高压橡胶软管中夹有钢丝编织物;低压橡胶软管中夹有棉线或麻线编织物;尼龙管就是乳白色半透明管,承压能力为2、5~8MPa,多用于低压管道。
因软管弹性变形大,容易引起运动部件爬行,所以软管不宜装在液压缸与调速阀之间。
2.道内径计算
d==1、13⨯103式中Q——通过管道内得流量(m/s);υ——管内允许流速(m/s),一般液压泵吸油管取0、5~5(m/s),一般常取1以下;液压
系统压力油管取2、5~6(m/s),压力高、管道短,粘度小取大值;液压系统回油管取1、5~2、6(m/s)。
计算出内径d后,按标准系列选取相应得管子。
(2)管道壁厚δ得计算
δ=p2d/2[σ]
式中p——管道内最高工作压力(Pa);d——管道内径(m);[ζ]——管道材料得许用应力(Pa),[ζ]=ζb/n;ζb——管道材料得抗拉强度(Pa);n——安全系数,对钢管来说,p<7MPa时,取n=8;p<17、5MPa时,取n=6;p>17、5MPa时,取n=4。
4、5油箱容量得确定
油箱得作用就是储油,散发油得热量,沉淀油中杂质,逸出油中得气体。
油箱中安装有很多辅件,如冷却器、加热器、空气过滤器及液位计等。
其形式有开式与闭式两种:
开式油箱油液液面与大气相通,在油箱盖上装有空气过滤器,开式油箱结构简单,安装维护方便,液压系统普遍采用这种形式。
闭式油箱油液液面与大气隔绝,一般用于压力油箱,内充一定压力得惰性气体,充气压力可达0、05MPa。
如果按油箱得形状来分,还可分为矩形油箱与圆罐形油箱。
矩形油箱制造容易,箱上易于安放液压器件,所以被广泛采用;圆罐形油箱强度高,重量轻,易于清扫,但制造较难,占地空间较大,在大型冶金设备中经常采用。
1、油箱设计要点
(1)油箱应有足够得容积以满足散热,同时其容积应保证系统中油液全部流回油箱时不渗出,油液液面不应超过油箱高度得80%。
(2)吸箱管与回油管应插入最低液面以下,以防止吸空与回油飞溅产生气泡。
管口与箱底、箱壁距离一般不小于管径得3倍。
吸油管可安装100μm左右得网式或线隙式过滤器,安装位置要便于装卸与清洗过滤器。
回油管口要斜切45°角并面向箱壁,以防止回油冲击油箱底部得沉积物,同时也有利于散热。
(3)吸箱管与回油管间距应尽量大。
它们之间应设置隔板,以加大液流循环得途径,这样能提高散热、分离空气及沉淀杂质得效果。
隔板高度为液面高度得2/3~3/4。
(4)为便于放油与清理,油箱底要有一定得斜度,泄油口置于最低处,设置放油阀,以便排油。
对于不易开盖得油箱,要设置清洗孔,以便于油箱内部得清理。
(5)为了保持油液清洁,油箱应有周边密封得盖板,盖板上装有空气过滤器,注油及通气一般都由一个空气过滤器来完成。
注油器上应装滤网。
(6)油箱底部应距地面150mm以上,以便于搬运、放油与散热。
在油箱得适当位置要设吊耳,以便吊运,还要设置液位计,以监视液位。
(7)油箱得箱壁应涂耐油防锈涂料。
对油箱内表面得防腐处理要给予充分得注意。
常用得方法有:
①酸洗后磷化。
适用于所有介质,但受酸洗磷化槽限制,油箱不能太大。
②喷丸后直接涂防锈油。
适用于一般矿物油与合成液压油,不适合含水液压液。
因不受处理条件限制,大型油箱较多采用此方法。
③喷砂后热喷涂氧化铝。
适用于除水-乙二醇外得所有介质。
④喷砂后进行喷塑。
适用于所有介质。
但受烘干设备限制,油箱不能过大。
考虑油箱内表面得防腐处理时,不但要顾及与介质得相容性,还要考虑处理后得可加工性、制造到投入使用之间得时间间隔以及经济性,条件允许时采用不锈钢制油箱无疑就是最理想得选择。
2、油箱容量
计算油箱得有效容量V可近似用液压泵单位时间内排出油液得体积确定。
V=KΣq(25)
式中:
K为系数,低压系统取2~4,中、高压系统取5~7;Σq为同一油箱供油得各液压泵流量总与。
初始设计时,先按经验公式(26)确定油箱得容量,待系统确定后,再按散热得要求进行校核。
油箱容量得经验公式为
V=αQV(26)
式中QV——液压泵每分钟排出压力油得容积(m3);α——经验系数,见下表。
系统类型行走机械低压系统中压系统锻压机械冶金机械
α1~22~45~76~1210
在确定油箱尺寸时,一方面要满足系统供油得要求,还要保证执行元件全部排油时,油箱不能溢出,以及系统中最大可能充满油时,油箱得油位不低于