组合零件三维建模及数控加工工艺设计及编程制定.docx
《组合零件三维建模及数控加工工艺设计及编程制定.docx》由会员分享,可在线阅读,更多相关《组合零件三维建模及数控加工工艺设计及编程制定.docx(18页珍藏版)》请在冰豆网上搜索。
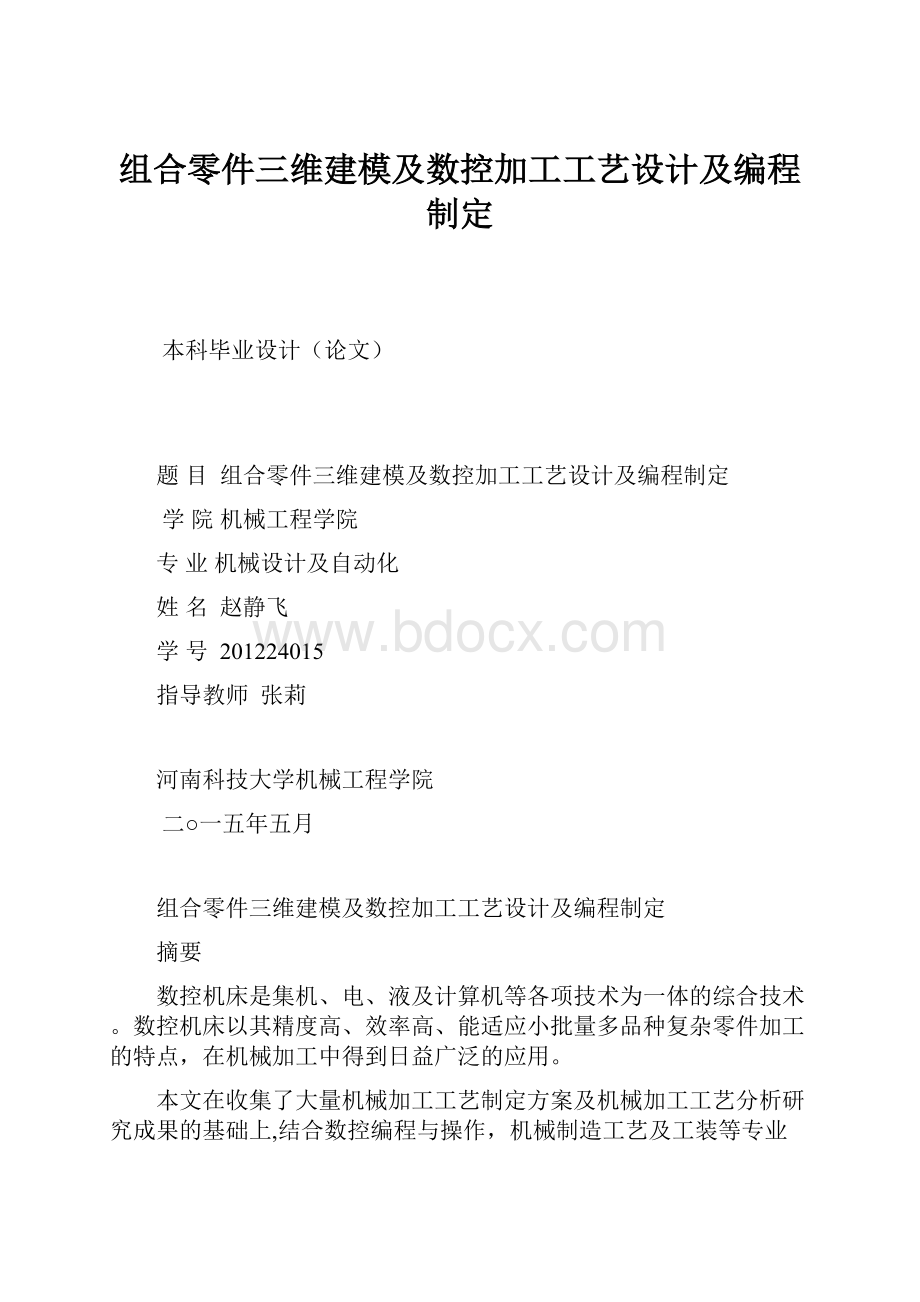
组合零件三维建模及数控加工工艺设计及编程制定
本科毕业设计(论文)
题目组合零件三维建模及数控加工工艺设计及编程制定
学院机械工程学院
专业机械设计及自动化
姓名赵静飞
学号201224015
指导教师张莉
河南科技大学机械工程学院
二○一五年五月
组合零件三维建模及数控加工工艺设计及编程制定
摘要
数控机床是集机、电、液及计算机等各项技术为一体的综合技术。
数控机床以其精度高、效率高、能适应小批量多品种复杂零件加工的特点,在机械加工中得到日益广泛的应用。
本文在收集了大量机械加工工艺制定方案及机械加工工艺分析研究成果的基础上,结合数控编程与操作,机械制造工艺及工装等专业课的学习与操作实践活动中习得的经验,选择正确的加工方法,设计合理的工艺过程,充分发挥数控加工的特点。
以数控车床车削轴类组合零件为例。
对数控加工工艺过程及其加工工序进行了具体的描述。
首先,对零件图样作详细的分析,对刀具、切削用量、加工设备及装夹方式进行具体的选择。
然后,编制完整的数控加工工艺过程卡、工序卡、刀具量具卡。
最后确定零件加工程序。
写出本次毕业设计总结。
关键词:
数控加工;轴类组合零件;工艺设计;切削用量;数控编程
COMPOSITEPARTSTHREE-DINENSIONALMODELINGANDNCMACHININGPROCESSDESIGNANDPROGRAMMING
Abstract
NCmachinetoolisthecollectionmachine,electricity,liquidandthetechnologysuchascomputerintegratedtechnology.NCmachinetoolwithhighprecision,highefficiency,abletoadapttothecharacteristicsofthesmallbatchmorevarietiesofcomplexpartsprocessing,totheincreasinglyextensiveapplicationinthemechanicalprocessing.
Makeplanbasedonthecollectedalargenumberofmachiningprocessandmachiningprocessanalysisandresearch,onthebasisofcombiningtheCNCprogrammingandoperationofmachinerymanufacturingtechnologyandequipmentandotherspecializedcourselearningandoperationexperienceofpracticeintheacquisition,toselectthecorrectprocessingmethods,designreasonableprocess,givefullplaytothecharacteristicsofncmachining.
BytheNClatheturningaxleassemblypartasanexample.IntheNCmachiningprocessanditsprocessingprocessdescribedindetail.Firstofall,makedetailedanalysisonpartsdesign,thecutter,cuttingdosage,theprocessingequipmentandtheclampingwaychoice.Then,completetheNCmachiningprocessCARDS,processcard,cuttingtoolmeasuringtool.Finallydeterminethepartsprocessingprogram.Writethesummaryofgraduationdesign.
Keywords:
TheNCmachining;Combinationofaxialparts;Processdesign;Cuttingparameter;CNCprogramming
前言
设计的目的:
毕业设计是教学计划中安排的最后一个教学环节,是前期教学的拓展和延伸,是对过去所学理论和实践经验的一次总结和检验。
基于本身对所学知识的熟练程度及今后发展方向的却定。
特通过本次设计,对自己进行工程设计过程进行学习和体验,为今后的岗位过渡打下基础。
因此本次毕业设计选题为:
《组合零件三维建模及数控加工工艺设计及编程制定》,此题的类型是生产实践型,是以运用所学的数控技术方面的专业知识,解决生产实践中的重要问题为目的的设计过程。
其中的特色是突出体现了,把毕业设计的选题与企业的生产实际紧密联系在一起,使其所做的毕业设计课题也更加具备了生产实用性。
因此能在此次毕业设计中收获知识、提高能力、完善自己是最大的目的。
设计的意义:
通过经历毕业设计这一过程,了解、掌握企业生产工艺制定的方法,产品生产的技术要求,组织生产的运营模式。
从而深化了所学的数控方面专业知识和能力。
培养了自身如何建立科学的设计思想,如何运用专业知识解决问,分析数控加工范围内的一般工程技术问题的能力,如何提高独立获得新知识、新技术和新信息的水平。
对自身今后的学习和发展具有一定的重要意义。
设计的概述:
此次毕业设计是建立在数控技术发展的基础之上,因此对数控技术的发展状况和遇到亟需解决的问题应有一个全面的了解。
数控机床就是将加工规程所需的各种操作和步骤以及工件的形状尺寸用数字代码表示,通过手工输入或传输等方式将数字信息送入数控装置,数控装置对输入的信息进行处理运算,发出各种控制信号,控制机床的伺服系统或其它驱动元件,使机床自动加工出所需要的工件。
数控机床的诞生与发展,有效的解决了一系列的生产上的矛盾,为单件、小批量精密复杂零件的加工提供了自动化加工手段。
随着计算机技术的高速发展,传统的制造业开始有了根本性变革,各工业发达国家投入巨额资金,对现在的制造技术行业研发提出了全新的发展制造模式,在现代制造系统中,数控技术是关键技术,它是集微电子、计算机、自动检测自动控制等高新技术于一体,具有高精度,高效率,柔性化的特点。
由专用型封闭式开环控制模式,向通用型开放式实时动态全闭环控制模式发展。
在集成化基础上,数控系统实现了超薄型、超小型化;在智能化基础上,综合了计算机、多媒体、模糊控制、神经网络等多学科技术,数控系统实现了高速、高精、高效控制,加工过程中可以自动修正、调节与补偿各项参数,实现了在线诊断和智能化故障处理;在网络化基础上,CAD/CAM与数控系统集成为一体,机床联网,实现了中央集中控制的群控加工。
长期以来,我国的数控系统为传统的封闭式体系结构,CNC只能作为非智能的机床运动控制器。
加工过程变量根据经验以固定参数形式事先设定,加工程序在实际加工前用手工方式或通过CAD/CAM及自动编程系统进行编制。
CAD/CAM和CNC之间没有反馈控制环节,整个制造过程中CNC只是一个封闭式的开环执行机构。
在复杂环境以及多变条件下,加工过程中的刀具组合、工件材料、主轴转速、进给速率、刀具轨迹、切削深度、步长、加工余量等加工参数,以至于无法在现场环境下根据外部干扰和随机因素实时动态调整,更无法通过反馈控制环节随机修正CAD/CAM中的设定量,因而影响CNC的工作效率和产品加工质量。
由此可见,传统CNC系统的这种固定程序控制模式和封闭式体系结构,限制了CNC向多变量智能化控制发展,已不适应日益复杂的制造过程,因此,对数控技术实行变革势在必行。
如今数控技术性能正朝着高速高精高效化、柔性化、工艺复合性和多轴化、实时智能化;其功能发展朝着用户界面图形化、科学计算可视化、插补和补偿方式多样化、内装高性能PLC;体系结构的发展朝着集成化、模块化、网络化、的技能指标方向发展。
1机械加工工艺规程的制定
工艺规程是用来指导生产的主要技术文件,制定工艺规程的基本要求是在保证产品质量的前提下,尽量提高生产效率和降低成本,使经济效益最大化。
另外,还应在充分利用本企业现有生产条件的基础上,尽可能采用国内外先进工艺技术和经验,并保证工人具有良好而安全的劳动条件。
1.1组合零件加工工艺分析
组合零件加工时既要考虑到单件工件的尺寸公差,也要考虑到组装后的配合要求,一个尺寸不合格会影响到几个尺寸的配合,尺寸之间的关联性很强。
掌握尺寸精度、形状位置公差和表面粗糙度的控制,从而保证零件间的配合精度。
加工图1-1组合零件1和图1-2组合零件2。
通过组合零件1右端的M30外螺纹与组合零件2左端的M30内螺纹的旋合,最终成为图1-3所示的组合件。
图1-1组合零件1
图1-2组合零件2
图1-3组合件
1.1.1组合零件结构工艺性分析
在制订零件的机械加工工艺规程之前,对零件进行工艺性分析,以及对产品零件图提出修改意见,是制定工艺规程的一项重要工作。
此次设计的是一个轴类组合零件,此件几何要素间的相互关系明确,条件充分,采用一个主视图和一个剖视图完整的表达零件,尺寸标注完整,符合国家制图标准,所设计的零件结构便于在数控机床上加工成形。
检查零件结构要素工艺性要体现,各要素规格统一和标准,以减少加工时刀具调整的次数。
能采用普通设备和标准刀具进行加工,刀具容易进入和顺序通过,避免端面加工,防止碰撞已加工工面。
加工面与非加工面应明显分开,应使加工时刀具有良好的切削条件,以提高刀具的寿命和保证加工质量。
在加工时还应保证零件有足够的刚性,防止加工中在高速和多刀切削是的变形,影响加工精度。
1.1.2零件形状分析
该组合零件表面由圆柱、圆弧、外槽、螺纹、内孔、锥面、外螺纹等表面组成,其中组合零件1的尺寸精度主要有φ520-0.02、φ400-0.03、φ2000.02、φ46-0.020350+0.03mm、200+0.03mm、92±0.03mm。
内圆锥面和外圆柱面的表面粗糙度值Ra为1.6um,要求较高。
组合零件2的尺寸精度主要有φ520-0.02、φ2400.02、1500.03mm、40±0.03mm内圆柱面和外圆柱面的表面粗糙度值Ra为1.6um,要求较高。
图中零件尺寸标注完整,符合数控加工尺寸标注要求,轮廓描述清晰完整。
1.2零件技术要求分析
1.2.1工艺要求
制定零件机械加工工艺过程是生产技术准备工作的一个重要组成部分。
一个零件可以采用不同的工艺过程制造出来,但正确与合理的工艺过程应满足以下基本要求:
(1).保证产品的质量符合图纸和技术要求条件所规定的要求;
(2).保证提高生产率和改善劳动条件;
(3).保证经济性的合理。
1.2.2技术依据
(1).产品零件图和装配图,技术条件;
(2).毛坯生产和供应条件;
(3).年生产纲领;
(4).本车间生产条件(包括设备,工人技术等级,劳动场合条件等);
(5).工艺技术条件,手册等。
1.2.3生产类型的确定
生产纲领是指企业在计划期内应当生产产品的产量和计划进度。
通常包括零件备品和废品在内的年产量就是生产纲领。
计算零件生产纲领的公式:
式中:
件/年(产品的年产量)
件/个(每个机器该零件的数量)
(零件的备品率)
(零件的废品率)
则
(件)
根据生产纲领确定该零件为批量生产。
(1)批量生产条件编程,不准用砂布和锉刀修饰平面,这是对平面高精度的要求,未注公差尺寸按GB1804-M,调质处理,硬度要求为220-250HBS,无热处理要求,未注粗糙度部分光洁度按Ra6.3。
(2)加工难点及处理方案
分析图纸可知,此零件对平面度的要求高,左端更有内轮廓加工,为提高零件质量,采用以下加工方案:
1.对图样上给定的几个精度要求较高的尺寸,编程时采用中间值。
2.在轮廓曲线上,有一处既过象限又改变进给方向的轮廓曲线,因此在加工时应进行机械间隙补偿,以保证轮廓曲线的准确性。
3.零图纸中含有圆柱度,为保证其形位公差,应尽量一次装夹完成左端面的加工以保证其数值。
4.本设计图纸中的各平面和外轮廓表面的粗糙度要求可采用粗加工---精加工加工方案,并且在精加工的时候将进给量调小些,主轴转速提高。
5.螺纹加工时,为保证其精度,在精车时选择改程序的方法,将螺纹的大径值减小0.18-0.2mm,加工螺纹时利用螺纹千分尺或螺纹环规保证精度要求。
选择以上措施可保证尺寸、形状、精度和表面粗糙度。
1.1.3零件材料、毛坯的分析
零件材料的选用是很重要的,材料的不当选择会使制成的零件不能满足使用要求,过早的损伤和破坏产生不良影响或经济效益差等。
机械零件的选材的一般原则是:
首先应满足使用性能的要求,同时兼顾工艺性、经济性和环保性。
对于轴类零件的选材应具备以下几点要求:
优良的综合力学性能,既要求有高的强度和韧性,以防止过载和冲击造成断裂。
高的疲劳极限,防止疲劳断裂。
良好的耐磨性。
(1)材料的分析
该轴零件加工中,刀具与工件之间的切削力较大。
工件材料的可切削性能。
强度、硬度、塑性、提供冷切削加工、机械性能都跟工件的材料有关。
所以选择45钢为该轴类零件的材料。
45钢的化学成分中含C0.42%~0.50%,Si0.17%~0.37%,Mn0.50~0.80%,P≤0.035%,S≤0.035%,Cr≤0.25%,N≤0.25%,Cu≤0.25%.45钢在进行冷加工时硬度要求,热轧钢,压痕直径不小于3.9,布氏硬度不小于241HB,退火钢压痕直径不小于4.4,布氏硬度不小于187HB,45钢的机械性能:
δs≥335Mpa,δb≥600Mpa,∮≥40%,AK≥47J。
45钢相对切削性硬质合金刀具1.0,高速钢刀具1.0,45钢经济合理对加工刀具的要求也合理,45钢用途广泛,主要是用来制造汽轮机、压缩机,泵的运动零件制造齿轮、轴活塞销等零件。
根据以上数据适合该轴的加工。
(2)毛坯的分析
轴类零件的毛坯有型材、锻件和铸件三种。
锻件:
适用与零件强度较高,形状较简单的零件。
尺寸大的零件因受设备限制,故一般用自由锻;中、小型零件可选模锻;形状复杂的刚质零件不宜用自由锻。
铸件:
适用于形状复杂的毛坯。
本零件的毛坯宜采用型材,由圆钢锯割,,使钢材经过热轧,获得均匀的纤维组织,提高其力学性能,同时也提高零件与毛坯的比重,减少材料消耗
根据零件图样可知该零件为一对组合零件,生产类型为小批量生产。
分别定义为组合零件1和组合零件2,材料皆为45钢。
大部分加工表面是回转体表面,考虑其复杂程度,所以本零件毛坯种类为热轧型中的圆钢,因为圆钢的经济性好,加工余量小,成本较低。
根据本零件的结构特征和尺寸要求及考虑到数控机床加工性能,所以组合零件1的毛坯圆钢尺寸为100mm×φ63mm,组合零件2的毛坯圆钢尺寸为45mm×φ63mm。
1.1.4零件三维图的建立
根据分析完正确的零件图后,通过UG三维绘图软件确定三维模型。
图1-4组合零件1的三维图
图1-5组合零件2的三维图
图1-6组合件的三维图
2零件加工工艺规程的设计
根据生产纲领确定该零件为成批生产。
在制定零件加工的工艺规程时,正确的选择工件的定位基准有着十分重要的意义。
定位基准的选择好坏,不仅影响零件加工的位置精度,而且对零件个别表面的加工顺序也有很大的影响。
基准有粗基准和精基准之分,选择定位基准时是从保证工件的精度要求出发,因而分析定位机准选择的顺序就应从精基准到粗基准。
合理的选择定位基准是保证零件加工精度的前提,还能简化加工工序,提高加工效率。
2.1定位基准的选择
定位基准是指工件在加工时用于定位的基准。
定位基准是零件获得加工尺寸的直接基准。
定位基准进一步可分为粗基准和精基准。
粗基准就是把未加工的定位基准面成为粗基准。
精基准是把经过机械加工的定位基准成为精基准。
2.1.1粗基准选择原则
(1)为了保证不加工表面与加工表面之间的位置要求,应选不加工表面作粗基准的原则;
(2)合理分配各加工表面的余量,应选择毛坯外圆作粗基准的原则;
(3)粗基准应避免重复使用,便于工件装夹的原则;
(4)选择粗基准的表面应平整,没有浇口、冒口或飞边等缺陷,以便定位可靠的原则。
2.1.2精基准选择原则
(1)基准重合原则:
选择已加工表面的设计基准为定位基准;
(2)基准统一原则;
(3)自为基准原则;
(4)互为基准原则;
(5)便于装夹的原则。
2.1.3定位基准的确定
综上所述,根据粗、精基准选择原则,由于这个工件是个实心轴,组合零件1末端要镗一个Φ30的锥孔,因轴的长度不是很长,所以采用工件的右端面和Φ52的外圆作定位基准,使用普通三爪卡盘夹紧工件,第一次装夹时取工件的左端面中心为工件坐标的原点,对刀点在(100.100)处。
第二次装夹时取工件的右端面中心为工件坐标的原点,对刀点在(100.100)处。
同理组合零件2是一个空心轴套,采用工件的右端面和Φ52的外圆作定位基准,使用普通三爪卡盘夹紧工件。
,第一次装夹时取工件的右端面中心为工件坐标的原点,对刀点在(100.100)处。
第二次装夹时取工件的左端面中心为工件坐标的原点,以外圆作为精基准,最终加工内孔。
对刀点在(100.100)处。
由于此零件全部表面都需加工,应选用外圆及一端面为粗基准,然后通过“互为基准的原则”进行加工。
遵循“基准重合”的原则。
加工左端时选择在毛坯外圆柱段的右端外圆表面,加工右端时选择在Φ38mm外圆柱段的表面,以体现定位基准是轴的中心线。
在数控车床上只需用三抓卡盘装夹定位,定位基准应选在零件的轴线上,组合零件1以毛坯φ520-0.02mm圆钢的轴线和左端面为定位基准。
再掉头以φ46mm外圆的轴线为定位基准。
组合零件2以毛坯φ520-0.02mm圆钢的轴线和右端面为定位基准。
2.2装夹方式的选择
机床夹具是指安装在机床上,用以装夹工件或导引刀具,使工件和刀具具有正确的相互位置关系的装置。
为了工件不至于在切削力的作用下发生位移,使其在加工过程始终保持正确的位置,需将工件压紧压牢。
合理的选择加紧方式十分重要,工件的装夹不仅影响加工质量,而且对生产率,加工成本及操作安全都有直接影响。
2.2.1车床常用的装夹方式
1)在三爪自定心卡盘上装夹。
三爪自定心卡盘的三个爪是不同步运动的,能自动定心,一般不需要找正,该卡盘装夹工件方便、省时,但夹紧力小,适合装夹外形规则的中小型工件。
2)再两顶尖之间装夹,对于尺寸较大或加工工序较多的轴类工件,为了保证每次装夹时的装夹精度,可用两顶尖,该装夹方式适用于多工序加工或精加工。
3)用卡盘和顶尖装夹。
当车削质量较大的工件时要一端用卡盘夹住,另一端用后支撑,这种方式比较安全,能承受较大的切削力,能装刚性好,轴向定位基准,应用较广泛。
4)用心轴装夹。
当装夹面为螺纹时再做个与之配合的螺纹进行装夹,叫心轴装夹。
这种方式比较安全,能承受较大的切削力,安装刚性好。
在数控车床上工件定位安装的基本原则与普通机床相同。
工件的装夹方法影响工件的加工精度和效率,为了充分发挥数控机床的工作特点,在装夹工件时,应考虑以下几种因素:
1.尽可能采用通用夹具,必须时才设计制造专用夹具;
2.结构设计要满足精度要求;
3.易于定位和装夹;
4.易于切削的清理;
5.抵抗切削力由足够的刚度。
2.2.2装夹方式确定
装夹方法:
组合零件1必须分两次装夹。
由于右端外表面为螺纹,不适于做装夹表面,所以第一次装夹工件右端,加工左端,把左端加工到φ520-0.02外圆处,为了防止由于切削力的作用而产生轴向位移,必须在卡盘内装一限位支撑,或者利用工件的台阶面进行限位。
此处利用工件台阶面进行定位。
使用三爪自定心卡盘夹持零件的毛坯外圆,确定零件伸出合适的长度(应将机床的限位距离考虑进去)。
零件需要加工两端,因此需要考虑两次装夹的位置,考虑到右端的Φ63mmx35mm的台阶可以用来装夹,因此先加工左端,然后调头夹住Φ40mmx30mm的台阶加工右端。
,同样组合零件2也分两次装夹,由于零件左端有锥面,不适合做装夹表面,所以第一次装夹工件的左端的Φ63mmx15mm,加工工件右端。
为了防止工件表面夹伤所以应在被装夹的零件表面垫紫铜片。
2.2.3零件设备的选择
设备的选择一般应考虑下列问题:
1.机床的精度与工序要求的精度相适应。
2.机床的规格与工件的外形尺寸、本工序的切削用量相适应。
3.机床的生产效率与被加工的零件或产品的生产类型相适应。
4.选择的设备应尽可能与工厂现有的条件相适应。
数控车床能对轴类或盘类等回转体零件自动地完成内外圆柱面、圆锥表面、圆弧面等工序的切削加工,并能进行切槽、钻、扩等的工作。
根据零件的工艺要求,可以选择经济型数控车床,一般采用步进电动机形式半闭环伺服系统。
此类车床机构简单,价格相对较低,这类车床设置三爪自定心卡盘、普通尾座或数控液压尾座,适合车削较长的轴类零件。
根据主轴的配置的要求选择卧式数控车床。
数控车床具有加工精度高,能做直线和圆弧插补,数控车床刚性良好,制造和对刀精度高,能方便和精确地进行人工补偿和自动补偿,能够加工尺寸精度要求较高的零件。
能加工轮廓形状特别复杂的表面和尺寸难于控制的回转体,而且能比较方便的车削锥面和内外圆柱面螺纹,能够保持加工精度,提高生产效率。
所以对加工是非常有利的。
这对配合件是典型的轴类零件,主要加工面有内外圆柱面,内外圆锥面、内外螺纹、和圆弧面的加工,故选择选择卧式数控车床即可完成所有加工面的加工要求。
具体来说,加工组合零件1和零件2有粗精车外形、车槽、车螺纹、镗内孔、车内槽、车内螺纹等工步。
所需要刀具不超过八把。
故选择国产卧式数控车床数控系统为FANUC0i的数控车床即可满足上述要求。
该机床规格为Φ460mmx500mm,X轴行程为225mm,Z轴行程为600mm,尾座体行程380mm,推力为9000N,主轴转速范围为30-4000r/min。
X/Z定位精度和重复定位精度分别为0.005mm和0.003mm刀架容量为8把。
工件依次装夹即可完成外圆、车槽、车螺纹、镗孔等工步的加工。
3刀具及切削用量
3.1数控车床刀具的选择
刀具的选择确定是数控加工工艺中的重要内容,它不仅影响数控机床的加工效率,而且直接影响加工质量。
数控机床主轴转速比普通机床高1-2倍,且主轴输出功率大,因此与传统加工方法相比,数控加工刀具的要求更高。
应根据机床的加工能力、工件材料的性能、加工工序的内容、切削用量以及其它相关因素,合理的选择刀具的类型、结构、几何参数等。
3.1.1选择数控刀具的原则
刀具寿命与切削用量有密切的关系。
在制定切削用量时,应首先选择合理的刀具寿命,而合理的刀具寿命则应根据优化的目标而定。
一般分最高生产率刀具寿命和最低成本刀具寿命两种,前者根据单件工时最少的目标确定,后者根据工序成本最低的目标确定。
选择刀具寿命时可考虑如下几点根据刀具复杂程度、制造和磨刀成本来选择。
复杂和精度高的刀具寿命应选的比单刃刀具高些。
对于机夹可转位刀具,由于换到时间短,为了充分发挥其切削性能,提高生产效率,刀具寿命可选的低些,一般取15-30min。
对于装刀、换刀和调刀比较复杂的多刀机床、组合机床与