闪速炉余热锅炉清洗方案.docx
《闪速炉余热锅炉清洗方案.docx》由会员分享,可在线阅读,更多相关《闪速炉余热锅炉清洗方案.docx(19页珍藏版)》请在冰豆网上搜索。
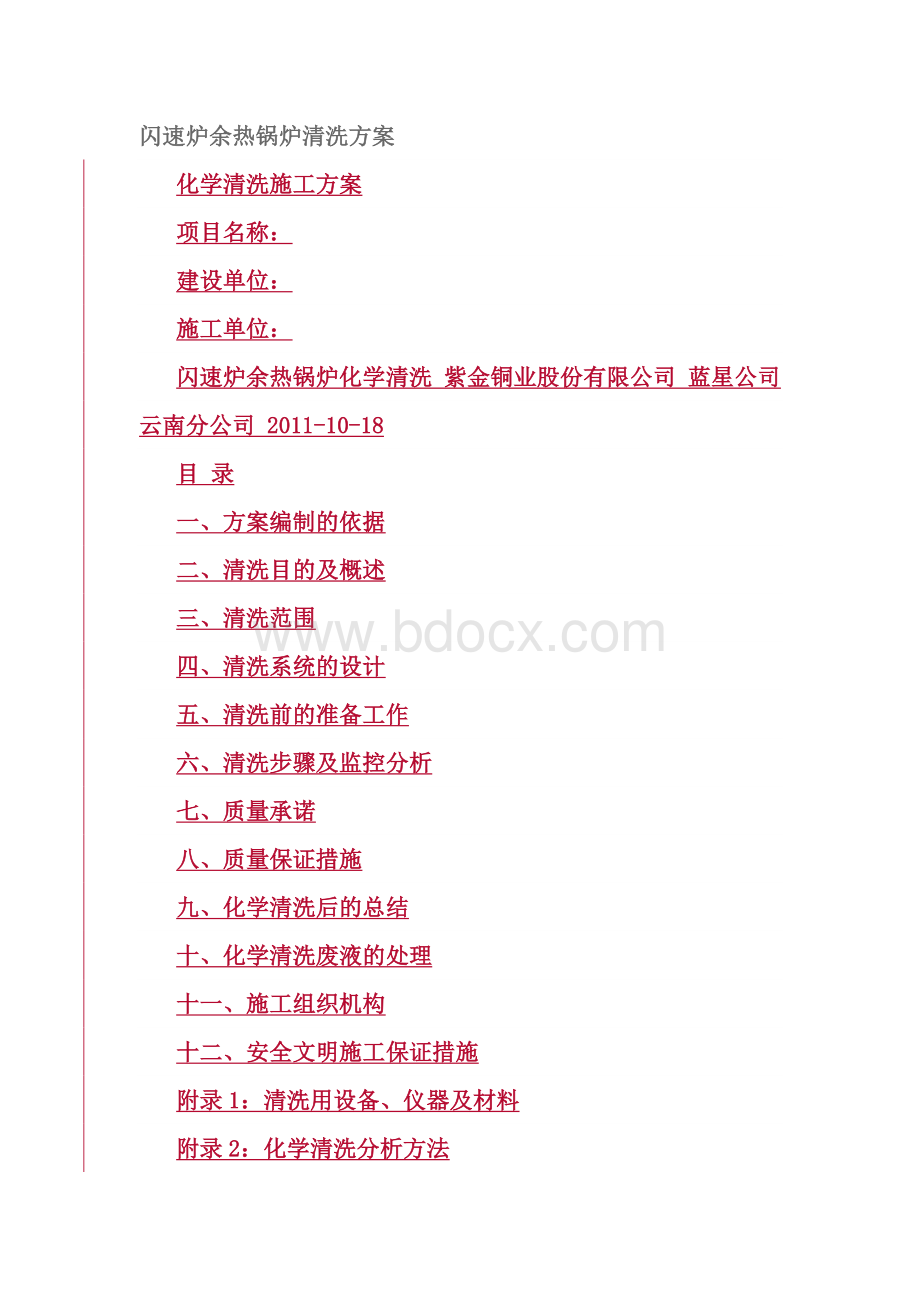
闪速炉余热锅炉清洗方案
化学清洗施工方案
项目名称:
建设单位:
施工单位:
闪速炉余热锅炉化学清洗紫金铜业股份有限公司蓝星公司云南分公司2011-10-18
目录
一、方案编制的依据
二、清洗目的及概述
三、清洗范围
四、清洗系统的设计
五、清洗前的准备工作
六、清洗步骤及监控分析
七、质量承诺
八、质量保证措施
九、化学清洗后的总结
十、化学清洗废液的处理
十一、施工组织机构
十二、安全文明施工保证措施
附录1:
清洗用设备、仪器及材料
附录2:
化学清洗分析方法
附录3:
临时配管材料表
附图:
清洗泵站示意图
一、方案编制的依据
1、厂方提供的锅炉图及相关资料;
2、国家质量技术监督局《锅炉化学清洗规则》;
3、甘肃科技出版社任建新《化学清洗》;
4、化学工业出版社窦照英《实用化学清洗技术》。
5、我公司《质量手册》、《程序文件汇编》;
6、中华人民共和国化工行业标准HG/T2387—2007《工业设备化学清洗质量标准》;
7、《驰宏公司曲靖分公司烟化炉余热锅炉化学清洗方案》;
8、《云铜铜业熔炼分厂艾萨炉余热锅炉、转炉余热锅炉清洗方案》;
二、清洗目的及概述
化学清洗是采用化学药剂与设备内表面的有机污物,铁锈、污垢进行反应、溶解过程而达到清洁去污的目的;
紫金铜业新建一套闪速炉余热锅炉用于冶炼铜过程中烟气的冷却和余热回收,产生的饱和蒸汽供发电和生产、生活使用。
根据开车前设计要求新锅炉系统内部必须清洁,而在开车前进行化学清洗可以达到如下结果:
?
除去制造过程中产生的氧化皮、铁锈及其他残余物;
?
除去制造过程中所采用的(例如用作保护的)油、润滑油及其他物质;?
除去在安装阶段留下的疏松颗粒物;
?
在管子、联箱及汽包内表面形成一层钝化膜,保证在锅炉运行前不会再次锈蚀。
总之,通过化学清洗能够清除锅炉内部各种沉积物及锈垢、杂质,使锅炉内表面清洁度达到要求。
为今后的发电、生产过程消除安全隐患,为保证正常生产创造良好条件。
余热锅炉设计参数
蒸发量:
50t/h;
工作压力:
5.0MPa;
蒸汽温度:
265℃;
排烟温度:
℃;
给水温度:
℃。
余热锅炉采用直通式强制循环锅炉,由辐射室和对流区两部分组成。
辐射室由膜式水冷壁组成,辐射室长度为mm,直段高度为mm,膜式壁由Ф38x5高压锅炉钢管和厚为5mm的扁钢焊接而成,管子间距为mm。
辐射室后部设有一块烟气挡板,为膜式壁结构。
辐射室出口烟气温度约℃。
对流区外壁也由膜式水冷壁组成,其膜式壁由Ф38x5高压锅炉钢管和厚度为5mm的扁钢焊接而成,管子间距为mm,对流区长度为mm。
对流区内部布置2组凝渣管屏,6组对流管束。
2组凝渣管屏为屏式结构的管束,6组对流管束均为顺列结构的管束。
余热锅炉设置汽包1台,汽包位于锅炉辐射室顶部,汽包内径mm,直段长度m,筒体壁厚为mm,封头壁厚为mm,材质为。
另余热锅炉所有入口联箱内水冷壁管处均设有限流控板。
因此,要对该余热锅炉进行成功清洗,必须解决好以下问题:
1、垢层必须是逐渐溶解和非溶物逐渐扩散,而非成片脱落堵在U型对流管束弯头部位,并且溶垢过程必须是在常温下完成.
2、流量和压头及清洗的具体操作必须能满足防止气阻的形成;
3、清洗系统的设计及清洗操作必须要防止节流孔的堵塞问题;
4、清洗系统的设计,应避免在锅炉本体割口,从而防止对锅炉本体造成伤害及大幅度降低因此造成的工作量。
5、选用的化学清洗剂能够满足常温清洗要求。
三、清洗范围
余热锅炉炉本体系统:
四、清洗系统的设计
清洗系统设计进、回路与锅炉循环系统基本一致,但清洗系统根据清洗需要可以实现逆向循环。
进液管由清洗泵站来,一支接强制循环泵出口阀门处,一支由清洗泵站接除盐水给水管线至气包,回液管一支接强制循环泵进液阀门处回到清洗泵站回液总管,一支由蒸汽管出口接至清洗泵站回液总管。
形成的各循环支路如下:
估计用水总量为:
清水≈1530M3;
(3)、低压蒸汽(现场如能提供):
5~10㎏,接入口径DN80~100
12、主要设备
清洗槽:
一个容积20M3
清洗泵站:
一台流量280M3/h扬程100M功率110KW
废液中和槽:
一个容积15M3
废液泵一台:
流量100M3/h
六、清洗步骤及监控分析
清洗步骤:
临时系统水冲洗→清洗系统水冲洗及检漏→碱洗→碱洗后水冲洗→酸洗→酸洗后水冲洗→漂洗→中和、钝化→人工清理检查
(以下为常温条件清洗工艺)
1、临时系统水冲洗
临时系统水冲洗的目的是冲出临时设备及管线的污物及其它杂质。
冲洗时将临时系统与待清洗设备断开,启动泵用清水将临时设备及管线冲洗干净。
当出口水澄清时,即可结束该步骤。
监控项目:
浊度/15分钟
2、清洗系统水冲洗及检漏
清洗系统水冲洗及检漏的目的是将待清洗系统内脱落的污垢用清水冲出系统,同时检查清洗系统中是否有泄漏及循环系统是否畅通。
临时系统冲洗完后,给系统注满水开始冲洗锅炉本体,在冲洗时,打开各排污点,将系统中的杂质污物彻底排干净,直至出口及各排放点的浊度与上水一致。
系统冲洗干净后,控制阀门保证清洗系统充满情况下,检查各回路及各法兰口、焊缝等是否有泄漏,若有泄漏,应及时补救。
当确定无误时,开始准备碱洗。
监控项目:
浊度/15分钟
3、碱洗
碱洗的目的是除去清洗系统中的有机污物和碱性可溶物,并对疏松的污垢和金属氧化物起到剥离作用,使下一步酸洗过程的作用更加完全、彻底。
水冲洗检漏结束后,给系统注满水后加入各种碱洗药剂,同时对进回液的碱
度进行监控,清洗时间为12~14小时左右。
当进回液浓度基本平衡且2小时内基本不变时,即可结束碱洗。
在碱洗过程中,应进行正反向切换。
药剂名称工艺条件
金属油污清洗剂5%
监控项目:
碱度1次/45分钟
4、碱洗后水冲洗
碱洗后水冲洗的目的是将系统内剩余的碱液用水冲出来,同时将脱落的垢冲出来。
碱洗结束后,打开系统总排污,将系统中的碱洗液排干净,然后用清水冲洗系统,并不断地打开各排污点检测PH值,当系统出口及排放点的PH值小于9,且浊度和上水一致时,即为终点。
监控项目:
浊度1次/30分钟
PH值1次/30分钟
5、酸洗
酸洗的目的是让酸与铁锈、污垢发生化学及电化学反应,从而将污垢彻底溶解除去。
为了防止垢层成片脱落,应从工艺上控制反应的速度,使可溶物逐渐溶解,不溶物成小颗粒状扩散在清洗液中,因此酸度应严格控制,并在清洗液中添加适量的助剂。
水冲洗结束后建立起循环,在常温下加入缓蚀剂,在其循环均匀后,逐步加入酸洗药剂及其他助剂,完成上述步骤后,将称重好的腐蚀试片及样管投入清洗循环槽中,同时酸洗前在汽包内也悬挂腐蚀试片,共同来测定清洗效果及腐蚀率。
在该过程中要保证定期排污。
当样管内锈垢清除干净,酸度及总铁离子浓度基本达到平衡后1小时不变即可结束酸洗,并取出腐蚀试片处理、称重,以测定腐蚀率。
药剂名称工艺条件
复合酸5%
缓蚀剂0.3%
促进剂M0.5%
还原剂0.5%
温度常温
监控项目:
酸度1次/45分钟
二价铁离子浓度1次/45分钟
三价铁离子浓度1次/45分钟
6、酸洗后水冲洗
酸洗后水冲洗的目的是冲出系统中残余的酸液和吸附在金属表面的残液,并将脱落的垢从系统中冲出。
排净系统中的酸洗液,然后用大量的水对全系统进行开路冲洗,并不断轮换各导淋排污以使系统中的颗粒、杂物及残液排净。
在冲洗过程中应打开高点放空。
当出口水的PH值大于5,且出口水与上水基本一致时,即可结束水冲洗。
监控项目:
PH值1次/10分钟
浊度1次/10分钟
7、漂洗
漂洗的目的是除去由于水冲洗过程中在金属表面形成的二次浮锈,并对铁离子进行络合,以保证最后的钝化效果。
水冲洗结束后建立起清洗循环系统,在常温下加缓蚀剂并循环均匀,然后开始加入漂洗药剂,控制PH值。
漂洗约3—6小时,在清洗过程中要不断监测铁离子浓度和PH值。
当监测项目基本不变即可结束漂洗。
控制铁离子浓度小于500PPM,若大于则应更换漂洗液。
药剂名称工艺条件
复合酸1%
缓蚀剂0.3%
监控项目:
漂洗液浓度1次/20分钟
铁离子浓度1次/20分钟
8、中和、钝化
通过酸洗、漂洗后,金属表面非常活泼,遇空气极易产生二次浮锈,通过钝化,使金属表面形成一层致密的钝化膜,从而防止锅炉在投运前的摆放期内遭受腐蚀。
漂洗结束后,直接用氨水调PH值至9-10,并对各排污点进行检查,使整个系统的PH值都要达到这一要求。
当达到要求时,可加入钝化药剂进行正反向循环。
钝化时间约为6~8小时。
钝化过程中应进行低点排污和高点排空,以确保钝化效果。
中和、钝化药剂工艺条件
氨水调PH值
复合钝化剂3%
监控项目:
PH1次/30分钟
9、人工清理检查
钝化结束后,排尽钝化液。
对锅炉的死角进行人工清理,并对可见部位进行直观检查,确定清洗效果。
(注:
如清洗后锅炉还需打压,试压进水时应给打压水加入锅炉保护剂,以保证钝化膜被破坏后锅炉免遭二次腐蚀.)
七、质量承诺
1、在该工程施工过程中不出现任何质量事故。
清洗质量要求如下:
(1)、被清洗金属表面应清洁,基本上无残留氧化物和焊渣,无明显金属粗晶析出的过洗现象,不允许有镀铜现象;
(2)、指示试片平均腐蚀率小于6g/m2h;
(3)、锅炉清洗表面应形成良好的钝化保护膜,金属表面不出现二次浮锈,无点蚀;
(4)、固定设备上的阀门等不应受到损伤。
2、保证按照合同要求按时竣工。
八、质量保证措施
1、公司质量管理体系
(1)、我公司于2005年9月通过ISO9001:
2000版质量管理体系认证。
建立、保持了持续改进的质量管理体系,完善了的各项规章制度,包括安全管理制度。
(2)、在本工程项目将按照我司ISO9001:
2000版质量管理体系文件要求对工程质量进行控制,以确保本工程项目质量目标的实现。
(3)、在本工程中,我方将按照公司《质量手册》、《程序文件》及公司相关的管理标准,建立以项目经理为第一责任人,技术负责人为直接责任人,施工负责人、施工操作人员及化验操作员全员参与的质量保证体系。
监督、检查。
3、质量方针和目标
(1)质量方针:
真诚的技术服务,永恒的质量追求。
(2)质量目标:
工程合格率达到100%,顾客满意度达到80%以上。
4、项目技术保证措施
(1)做好技术交底工作,由项目技术负责人向施工人员、施工负责讲述工程特点及现场要求;讲述施工规程、质量评定指标和容易造成质量问题的关键部位。
并对交底内容、过程进行记录。
(2)严把材料关。
对现场的材料进行严格把关,避免使用不合格的原材料。
(3)开展施工检查,做好技术复核工作。
施工准备必须完善,所以在施工前必须对施工过程中的重要技术进行复核,杜绝质量事故发生。
(4)认真做好“三检”工作。
“自检”、“互检”、“专检”是把好质量关的重要手段,按规范要求进行严格的工序交接制度,上道工序不验收合格决不进行下道工序,通过“三检”层层把关。
(5)施工机具保证。
根据需要,施工机具在数量、规格、品种及机具本身的质量上给予保证,确保工程质量。
(6)奖罚措施。
加强质量意识,严格执行有关规定进行奖罚。
(7)严格按照本公司的《质量手册》组织施工。
九、化学清洗后的总结
化学清洗工作全部结束后,整理有关分析测试数据及腐蚀速度数据,结合清洗过程提交《化学清洗总结报告》。
十、化学清洗废液排放
1、各阶段化学清洗废液进行中和处理后,排放至厂方污水系统;
2、碱性废液采用投药中和法进行处理。
中和剂选用氨基磺酸,调PH=6.0~9.0后进行排放;
3、酸性废液采用投药中和法进行处理。
中和剂选用氢氧化钠,调PH=6.0~9.0后进行排放;
4、化学耗氧量的处理