高纯硅的制备与硅烷法doc 10页.docx
《高纯硅的制备与硅烷法doc 10页.docx》由会员分享,可在线阅读,更多相关《高纯硅的制备与硅烷法doc 10页.docx(20页珍藏版)》请在冰豆网上搜索。
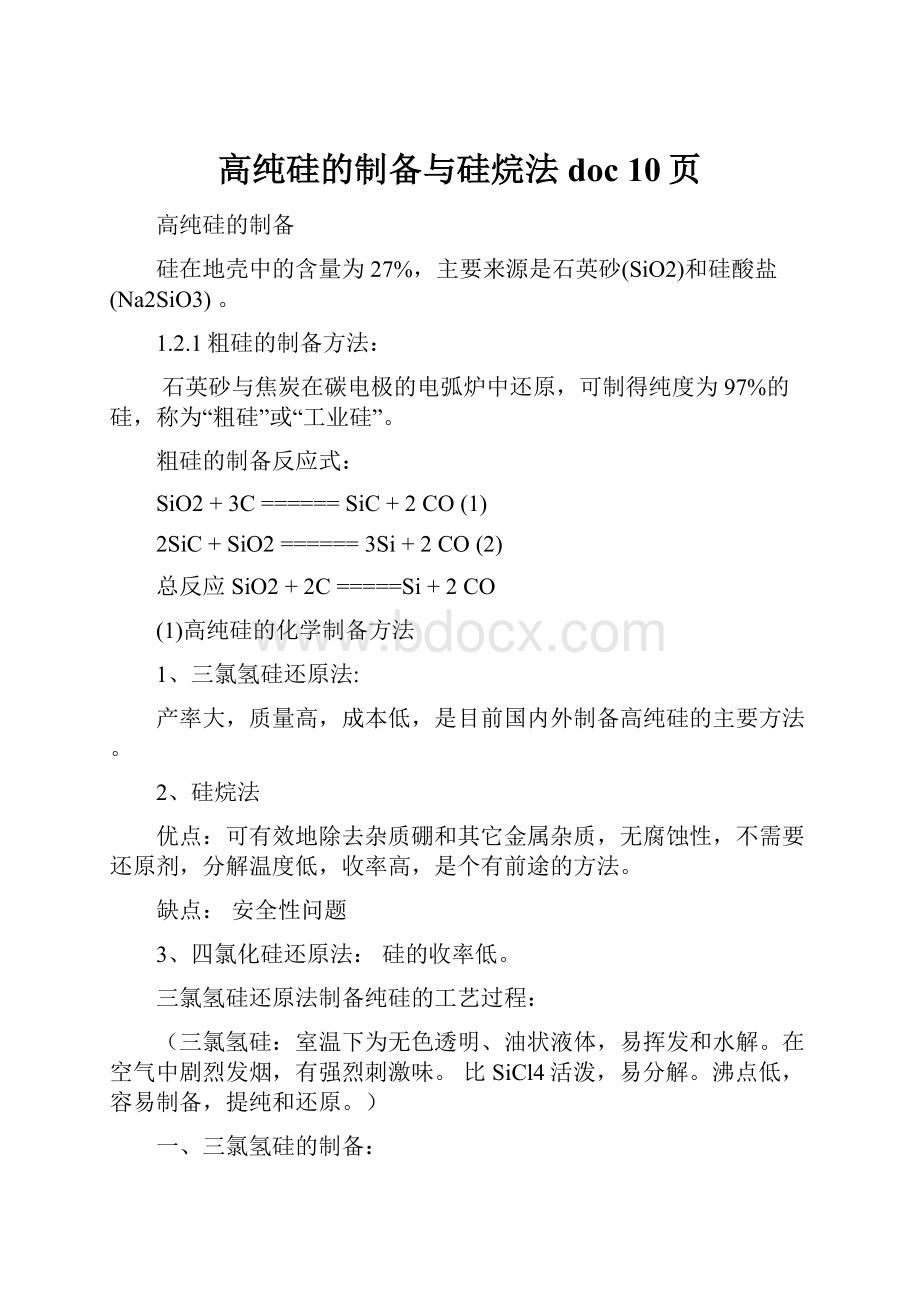
高纯硅的制备与硅烷法doc10页
高纯硅的制备
硅在地壳中的含量为27%,主要来源是石英砂(SiO2)和硅酸盐(Na2SiO3)。
1.2.1粗硅的制备方法:
石英砂与焦炭在碳电极的电弧炉中还原,可制得纯度为97%的硅,称为“粗硅”或“工业硅”。
粗硅的制备反应式:
SiO2+3C======SiC+2CO
(1)
2SiC+SiO2======3Si+2CO
(2)
总反应SiO2+2C=====Si+2CO
(1)高纯硅的化学制备方法
1、三氯氢硅还原法:
产率大,质量高,成本低,是目前国内外制备高纯硅的主要方法。
2、硅烷法
优点:
可有效地除去杂质硼和其它金属杂质,无腐蚀性,不需要还原剂,分解温度低,收率高,是个有前途的方法。
缺点:
安全性问题
3、四氯化硅还原法:
硅的收率低。
三氯氢硅还原法制备纯硅的工艺过程:
(三氯氢硅:
室温下为无色透明、油状液体,易挥发和水解。
在空气中剧烈发烟,有强烈刺激味。
比SiCl4活泼,易分解。
沸点低,容易制备,提纯和还原。
)
一、三氯氢硅的制备:
原料:
粗硅+氯化氢
流程:
粗硅→酸洗(去杂质)→粉碎→入干燥炉→通入热氮气→干燥→入沸腾炉→通干HCl→三氯氢硅
主反应:
Si+3HCl=SiHCl3+H2
(副反应生成的杂质1、SiCl42、SiH2Cl2)
为增加SiHCl3的产率,必须控制好工艺条件,使副产物尽可能的减少。
较佳的工艺条件:
1、反应温度280-300℃
2、向反应炉中通一定量的H2,与HCl气的比值应保持在1:
3~5之间。
3、硅粉与HCl在进入反应炉前要充分干燥,并且硅粉粒度要控制在0.18-0.12mm之间。
4、合成时加入少量铜、银、镁合金作催化剂,可降低合成温度和提高SiHCl3的产率。
二、氯氢硅的提纯
目的:
除去SiHCl3中含有的SiCl4和多种杂质的氯化物。
提纯方法:
精馏
精馏提纯:
是利用混合液中各组分的沸点不同来达到分离各组分的目的。
三、三氯氢硅还原
主反应:
SiHCl3+3H2→Si+3HCl
副反应:
4SiHCl3+3H2=Si+3SiCl4+2H2
SiCl4+H2=Si+4HCl
升高温度,有利于SiHCl3的还原反应,还会使生成的硅粒粗大而光亮。
但温度过高不利于Si在载体上沉积,并会使BCl3,PCl3被大量的还原,增大B、P的污染。
反应中还要控制氢气量,通常H2:
SiHCl3=(10-20):
1(摩尔比)较合适。
硅烷法
主要优点:
1、除硼效果好
2、无腐蚀性
3、分解温度低,不使用还原剂,效率高
有利于提高纯度
4、产物中金属杂质含量低,(在硅烷的沸点-111.8℃下,金属的蒸气压低)
5、外廷生长时,自掺杂低,便于生长薄外廷层。
缺点:
安全性
一、硅烷的制备
原料:
硅化镁、氯化铵
Mg2Si+4NH4Cl====SiH4+4NH3+2MgCl2+Q
条件:
液氨中。
液氨作溶剂、催化剂
(1)Mg2Si:
NH4Cl=1:
3
(2)Mg2Si:
液氨=1:
10
(3)反应温度:
-30℃~-33℃
二、硅烷的提纯
可用方法:
1、低温精馏(深冷设备,绝热装置)、2、吸附法(装置简单)主要用吸附法,使用分子筛吸附杂质。
(分子筛的作用:
1、工业用于做吸附剂。
2、催化剂分类:
分为微孔≤2nm,介孔2-50nm,超大孔≥50nm
吸附流程
1、4A分子筛吸附NH3,H2O,部分PH3、AsH3、C2H2、H2S等
2、5A分子筛吸附余下的NH3,H2O,PH3、AsH3、C2H2、H2S及B2H6,Si2H6
3、13X分子筛吸附烷烃,醇等有机大分子
4、常温和低温活性炭吸附B2H6、AsH3、PH3)
吸附后,在热分解炉中加热至360℃,除去杂质的氢化物
三、硅烷热分解
SiH4=Si+2H2
工艺条件:
1、热分解的温度不能太低,载体的温度控制在800℃
2、热分解的产物之一氢气必须随时排队,保证反应用右进行。
高纯锗的制备
流程:
锗精矿→GeCl4→精馏(萃取提纯)→水解→二氧化锗→区熔提纯→高纯锗
1、GeCl4的制备
反应式:
GeO2+4HCl→GeCl4+2H2O
1)反应时盐酸浓度要大于6mol/L,否则GeCl4水解,一般使用10mol/L的盐酸,可适当加硫酸增加酸度。
2)加入氧化剂(氯气)以除去砷。
2、GeCl4的提纯(萃取法、精馏法)
采用萃取法,利用AsCl3与GeCl4在盐酸中溶解度的差异,萃取分离。
GeCl4在浓盐酸中几乎不溶,AsCl3的溶解度可达200-300g/L
3、GeCl4水解
反应式:
GeCl4+(2+n)H2O——GeO2·H2O+4HCl+Q
1、可逆反应,酸度大于6mol/L,反应向左进行。
因为在盐酸浓度为5mol/L时,GeO2的溶解度最小,所以控制GeCl4:
H2O=1:
6.5。
2、使用超纯水,用冰盐冷却以防止受热挥发。
3、过滤后的GeO2经洗涤后在石英器皿中以150-200℃下脱水,制得的GeO2纯度可达5个“9”以上。
4、GeO2氢还原
GeO2+2H2=Ge+2H2O
1、为防止中间产物GeO在700℃以上完全挥发,还原温度控制在650℃左右。
2、尾气无水雾标志着完全还原。
3、还原完后升温将锗粉熔化成锗锭。
冰盐是指冰和盐类的混合物。
用冰盐制作制冷剂可以获得更低的温度。
工业上应用最广的冰盐是冰块与工业食盐NaCl的混合物。
冰盐冷却是利用冰盐融化过程的吸热。
冰盐融化过程的吸热包括冰融化吸热和盐溶解吸热这两种作用。
分凝现象:
将含有杂质的晶态物质熔化后再结晶时,杂质在结晶的固体和未结晶的液体中的浓度是不同的,这种现象称分凝现象或偏析现象。
区熔提纯:
就是利用分凝现象将物料局部深化形成狭窄的熔区,并令其沿锭长一端缓慢地移动到另一端,重复多次使杂质尽量集中在尾部或头部,进而达到使中部材料提纯的目的。
平衡分凝系数:
在一定温度下,平衡状态时,杂质在固液两相中浓度的比值,以此来描述该体系中杂质的分配关系。
(K0=CS/CL)
能使材料熔点下降的杂质,K0<1,熔融再凝固结晶时固相中的浓度小于液相中的浓度,所以提纯时杂质向尾部集中
能使材料熔点上升的杂质,K0>1,提纯时杂质向头部集中
对于K<1的杂质,当结晶速度大于杂质由界面扩散到熔体内的速度,杂质就会在界面附近的熔体薄层中堆积起来,形成浓度梯度加快杂质向熔体内部的扩散。
最后达到一个动态平衡,形成稳定的界面薄层,这个杂质较高的薄层称杂质富集层(或扩散层)。
对于K>1的杂质,结晶时固相界面会多吸收界面附近熔体中的杂质,就会使界面附近的熔体薄层中杂质呈缺少状态,这一薄层称杂质贫乏层。
有效分凝系数:
通常把固相杂质浓度CS与熔体内部的杂质浓度CL0的比值定义为有效分凝系数Keff。
(Keff=CS/CL0)
当界面不移动或移动速度f趋于零时,CL0→CL,则Keff→K0
结晶过程有一定速度时,Keff≠K0,此时,Cs=KeffCL0
BPS公式:
讨论了平衡分凝系数与有效分凝系数的关系:
Keff=K0/[(1-K0)e-fδ/D+K0]
有效分凝系数Keff,是平衡分凝系数K0,固液界面移动速度f,扩散层厚度δ,和扩散系数D的函数
如果固液界面移动速度很快,则f值很大,杂质在熔体中的扩散速度较慢,f>>D/δ,有效分凝系数接近1,则达不到利用分凝效应使杂质向一边集中,从而提纯的效果。
为使分凝效应显著,应使凝固速度f采用电磁搅拌熔体,会使扩散层中积累的杂质加速输运到整个熔体中。
扩散层厚度δ变小,有助于Keff趋向于K0
区熔原理
正常凝固:
将一锭条全部熔化后,使其从一端向另一端逐渐凝固的方式称正常凝固。
由于存在分凝现象,正常凝固后锭条中的杂质分布不再均匀,会出现三种情况:
1、K<1的杂质,越接近尾部浓度越大,杂质向尾部集中
2、K>1的杂质,越接近头部浓度越大,杂质向头部集中
3、K≈1的杂质,基本保持原有的均匀分布的方式。
固相中杂质浓度CS沿锭长的分布公式:
CS=Ks/(1-g)=ks0(1-g)k/(1-g)=kC0(1-g)k-1
杂志的分布规律:
K≈1的杂质,分布曲线接近水平,即浓度沿锭长变化不大
K<0.1,K>3的杂质,随锭长变化较快,越是K偏离1的杂质,向锭的一端集中的趋势越明显,提纯效果越好。
注意:
在尾部(K<1)因杂质浓度太大,K不再是常数,所以上式不再适用。
如杂质浓度过大,会形成合金状态,更不符合分凝规律。
一次区熔与正常凝固的比较:
就一次提纯而言,正常凝固比一次区熔提纯的效果好。
熔区越宽,提纯效果越好最后一个熔区属于正常凝固,不服从区熔规律。
极限分布:
经过多次区熔后,杂质分布状态将达到一个相对稳对且不再改变的状态,这种极限状态叫做极限分布或最终状态。
原因:
在凝固界面,由于分凝作用,部分杂质将被排斥到熔区,并向后携带。
在熔化界面,由于锭料熔化又带入新的杂质,它们将从熔化界面向凝固界面运动,运动方向与分凝出来的杂质运动方向相反,称杂质倒流。
使整个熔区的杂质浓度增加。
在最初几次区熔时,由于尾部杂质浓度还不太大,熔化界面熔入的杂质量也比较少,杂质倒流的作用不明显,此时分凝占主导地位。
杂质总的流向是从头部流到尾部,对材料起提纯作用。
多次区熔后,尾部的杂质越来越多,杂质倒流越来越严重,最终杂质分布达到平衡,出现极限分布状态。
规律:
影响杂质浓度极限分布的主要因素是杂质的分凝系数和熔区长度。
对不同K值的杂质,K<1时,K值越小,杂质分布卓越头部杂质浓度越小,熔区长度越小,极限分布时CS越小。
影响区熔提纯的主要因素:
1、熔区长度
一次区熔时,由CS=C0[1-(1-K)e-kx/L]
L→大,CS→小,提纯的效果越好,由此考虑,熔区长度L越大越好。
极限分布的时,熔区长度越大,CS越大,提纯的效果越差,所以从极限分布的角度来看,L→小较好。
实际区熔时,应取最初几次用大熔区,后几次则用小熔区的工艺条件。
2、熔区移动速度
根据BPS公式,熔区的移动速度越小,Keff→K0,有利于杂质的分凝与提纯。
但区熔速度过慢会降低生产效率。
反之,区熔速度越大,所次区熔用时少,但提纯效果由于Keff的增大而降低。
要想在最短时间内,最有效的提纯材料,必须同时考虑区熔次数n与区熔速度f,使n/f的比值最小。
即用尽可能少的区熔次数和尽量快的区熔速度来区熔,达到预期的效果。
经验公式:
一般区熔时,可按fδ/D≈1的条件近似计算f
3.区熔次数的选择
多次区熔后,锭中的杂质会达到极限分布,所以无限增加区熔次数是无效的。
一般情况下,不论K值的大小,达到极限分布的区熔次数不是很多,并且相差也不大。
可使用一个半经验公式,计算n值
n=(1~1.5)L/l
通常取L/l=10,计算出n最大为15,通常区熔次数取20左右。
4.质量输运
质量输运或质量迁移:
区熔时,物质会从一端缓慢地移向另一端的现象。
产生的原因:
物质熔化前后材料密度变化,对某一物质,区熔时其质量输运的多少和输运的方向取决于熔化密度变化的大小与符号。
熔化时体积缩小,输运的方向与区熔的方向一致,例如锗、硅;
熔化时体积增大,输运的方向与区熔的方向相反。
质量输运的结果,会使水平区熔的材料锭纵向截面变成锥形,甚至引起材料外溢,造成浪费。
晶体长大的动力学模型
完整突变光滑面模型
层生长理论(KosselW.,1927):
在晶核的光滑表面上生长一层原子面时,质点在界面上进入晶格“座位”的最佳位置是具有三面凹入角的位置。
质点在此位置上与晶核结合成键放出的能量最大。
因为每一个来自环境相的新质点在环境相与新相界面的晶格上就位时,最可能结合的位置是能量上最有利的位置,即结合成键时成键数目最多,放出能量最大的位置。
层生长理论的局限:
按层生长理论,晶体在气相或在溶液中生长时,过饱和度要达到25%以才能生长,而且生长不一定会连续.实际上,某些生长体系,过饱和度仅为2%时,晶体就能顺利生长。
螺旋生长理论(FrankF.C.1949):
在晶体生长界面上螺旋位错露头点所出现的凹角及其延伸所形成的二面凹角可作为晶体生长的台阶源,促进光滑界面上的生长。
可解释层生长理论所不能解释的现象,即晶体在很低温的过饱和度下能够生长的实际现象。
位错的出现,在晶体的界面上提供了一个永不消失的台阶源。
位错是晶体中的一维缺陷,它是在晶体某一列或若干列原子出现了错位现象,即原子离开其平衡位置,发生有规律的错动。
模型认为晶体是理想不完整的,其中必然会存在一定数量的位错,如果一个纯螺型位错和一个光滑的相面相交,在晶面上就会产生一个永不消失的台阶源,在生长过程中,台阶将逐渐变成螺旋状,使晶面不断向前推移。
生长硅、锗单晶的方法很多,目前:
锗单晶主要用直拉法,硅单晶常采用直拉法与悬浮区熔法
坩埚直拉法(CZ)的优点是,可拉制大直径和高掺杂低阻单晶。
缺点是由于熔硅与石英坩埚(SiO2)熔接以及石墨的污染,将使大量的O、C及金属杂质进入硅单晶,故CZ法不能制备高阻单晶。
无坩埚区熔法(FZ)采用高频感应加热,通过熔区移动生长单晶,由于工艺不接触石英坩埚(SiO2)和石墨加热,可拉制高纯度、长寿命单晶。
缺点是单晶掺杂极为困难。
直拉单晶制造法(乔赫拉尔斯基法,CZ法)是把原料多硅晶块放入石英坩埚中,在单晶炉中加热融化,再将一根直径只有10mm的棒状晶种(称籽晶)浸入融液中。
在合适的温度下,融液中的硅原子会顺着晶种的硅原子排列结构在固液交界面上形成规则的结晶,成为单晶体。
直拉法生长单晶的电阻率的控制
1.直拉法单晶中纵向电阻率均匀性的控制
变速拉晶法。
此法基于Cs=KCL这一基本原理,因为在拉晶时,若杂质K实际上,K应为Keff,它随拉速和转速而变。
当拉速f小时,Keff→K0,f增大,Keff也增加。
若在晶体生长初期用较大的拉速,随后随着晶体的长大而不断减小拉速,保持CL与Keff乘积不变,这样拉出来的单晶纵向电阻率就均匀了。
一般变拉速比较方便,但改变拉速f是有一定范围的,f太大晶体易产生缺陷,f大小,生产时间过长。
双坩埚法(连通坩埚法、浮置坩埚法)。
在拉制锗单晶时对于K<1的杂质(但K<<1的杂质不能用),用连通坩埚法可控制单晶纵向电阻率的均匀性。
连通坩埚的结构是在一个小坩埚外面再套上一个大坩埚,且内坩埚下面有一个连通孔与外面大坩埚相连。
所掺杂质放在内坩埚里,并从内坩埚内拉晶(浮置坩埚是在一个大坩埚内放一个有孔的小坩埚)。
基本原理:
由Cs=KCL可知,在拉晶时,若杂质K使用双坩埚,当拉出部分单晶,内坩埚的CL变大时,外坩埚中的锗液进入内坩埚,又使CL变小。
当锗熔化后,内外坩埚中的熔体液面相同。
拉晶时,内坩埚内熔体减少,液面降低,外坩埚中的纯锗液通过连通孔流入,保持内坩埚中液体体积不变,而杂质则不易通过连通小孔流到大坩埚中。
但当晶体生长得较长,内坩埚中杂质量变少时,晶体电阻率也会上升。
如果K较小时,生长的晶体所带走的杂质少,内坩埚熔体中杂质浓度变化是缓慢的,晶体纵向电阻率就比较均匀。
水平布里奇曼法
水平布里奇曼法,又叫横拉法。
它与锗单晶生长常用的水平区熔法很相似。
两温区横拉法法生长GaAs设备有。
加热炉分为低温炉与高温炉,它们分别供电、测温和控温。
高温炉外部有一个开有观察孔的保温炉,它装在区熔传动机构上,可以左右移动。
反应室为圆柱形石英管,中间有石英隔窗,一端放有用金刚砂打毛后清洗干净的石英舟,另一端则装砷。
合成GaAs工艺:
1、将纯Ga盛于石英舟内,放在石英反应管一端,纯砷放到另一端。
为了使整个体系能保持有9
×104Pa的砷蒸气,装砷量要比按化学计量计算的量要多一些。
2、高真空下分别加温除去氧化膜。
Ga在700℃,1.3×10-3Pa下恒温处理2h除去氧化膜。
砷在280℃,1.3×10-3Pa真空下恒温处理2h除去氧化膜。
3、在真空条件下分别用氢氧焰封闭石英管。
为了便于操作将Ga用干冰或液N2冷冻凝固,用石英撞针(或用固体As)撞破石英隔窗。
4、将反应管放人炉中,镓舟置于高温炉中,砷端置于低温炉中,通电升温。
砷:
低温炉恒温于617℃,镓:
高温炉恒温1250℃
5、开动区熔机,使熔区由锭的一端移到另一端,这时GaAs便合成好了。
6、GaAs合成后,将保温炉退回锭的前端,即可进行晶体生长。
生长晶体时可利用预先放人的籽晶引晶,并可以应用缩颈技术,以降低位错密度。
横拉法的缺点:
用横拉法生长GaAs单晶的主要问题是“粘舟”,即GaAs与石英舟粘在一起不易分开。
解决办法:
1、将石英舟喷砂打毛,或将喷砂后的石英舟用Ga在1000~1100℃高温下处理10h。
2、脱氧时真空度要高。
3、合成及拉晶时严格控制温度并防止Ga与As化学比的偏离。
目前用这种方法可拉制截面最大直径为75mm的GaAs单晶。
液态密封法也称LEP法或称LEC法,它是目前拉制大直径Ⅲ一V族化合物晶体的最重要的方法。
它是在高压炉内,将欲拉制的化合物材料盛于石英坩埚中,上面覆盖一层透明而黏滞的惰性熔体,将整个化合物熔体密封起来,然后再在惰性熔体上充以一定压力的惰性气体,用此法来抑制化合物材料的离解,用这种技术可拉制(GaAs、InP、GaP等的大直径单晶。
密封化合物熔体的惰性熔体应具备以下条件:
①密度比化合物材料小,熔化后能浮在化合物熔体上面。
②透明,便于观察晶体生长的情况。
③不与化合物及石英坩埚反应,而且在化合物及其组分中溶解度小。
④易提纯,蒸气压低,易熔化,易去掉。
目前采用的B2O3
MOVPE技术是生长化合物半导体薄层晶体的方法,最早称为MOCVD。
近年来从外延生长角度出发,称这一技术为MOVPE。
它是采用Ⅲ族、Ⅱ族元素的有机化合物和V族、Ⅵ族元素的氢化物等作为晶体生长的源材料,以热分解方式在衬底上进行外延生长Ⅲ一V族,Ⅱ一Ⅵ族化合物半导体以及它们的多元化合物的薄层单晶。
MOVPE具有下列的特点:
(1)可以通过精确控制各种气体的流量来控制外延层的性质
(2)反应器中气体流速快,可以迅速改变多元化合物组分和杂质浓度
(3)晶体生长是以热分解方式进行,是单温区外延生长,需要控制的参数少,设备简单。
便于多片和大片外延生长,有利于批量生长。
(4)晶体的生长速度与金属有机源的供给量成正比,因此改变其输入量,可以大幅度地改变外延生长速度。
(5)源及反应产物中不含有HCl一类腐蚀性的卤化物,因此生长设备和衬底不被腐蚀,自掺杂比较低。
此外,MOVPE可以进行低压外延生长,比上述常压MOVPE的特点更加显著。
MOVPE设备分为卧式和立式两种,有常压和低压,高频感应加热和辐射加热,反应室有冷壁和热壁的。
组成:
(1)源供给系统、
(2)气体输运和流量控制系统,(3)反应室加热及温度控制系统,(4)尾气处理,(5)安全防护报警系统,(6)自动操作及电控系统。
分子束外延(MBE)是在超高真空条件下,用分子束或原子束输运源进行外延生长的方法。
在超高真空中,分子束中的分子之间以及分子束的分子与背景分子之间几乎不发生碰撞。
优点:
①源和衬底分别进行加热和控制,生长温度低,如GaAs可在500℃左右生长,可减少生长过程中产生的热缺陷及衬底与外延层中杂质的扩散,可得到杂质分布陡峭的外延层;②生长速度低(0.1-1nm/s),利用快门可精密地控制掺杂、组分和厚度,是一种原子级的生长技术,有利于生长多层异质结构;③MBE生长不是在热平衡条件下进行的,是一个动力学过程,因此可以生长一般热平衡生长难以得到的晶体;④生长过程中,表面处于真空中,利用附设的设备可进行原位(即时)观测,分析、研究生长过程、组分、表面状态等。
缺点:
MBE设备比较复杂,价格昂贵,使用时消耗大量液氮。
某些元素如Zn的粘附系数较小,用这类元素掺杂尚有困难。
MBE设备主要由真空系统、生长系统及监控系统等组成。
在异质外延层和衬底或相邻的两个外延层之间,如果存在晶格常数的差异,称之为晶格失配。
当这种应变较大时,即存储在晶体中的应变能量足够大时,将通过在界面处形成位错而释放,所形成的位错称为失配位错。
异质结:
两种不同晶体接触处所形成的结。
由两种半导体单晶联结起来构成。
可分为同型(NN+,PP+)和异型(PN)两种
超晶格是一种新型结构的半导体化合物,它是由两种极薄的不同材料的半导体单晶薄膜周期性地交替生长的多层异质结构,每层薄膜一般含几个以至几十个原子层。
1.半导体的主要特征:
1.电阻率大体在10e-3∼10e9Ωcm2.电阻率的温度系数是负的3.通常具有很高的热电势。
4.具有整流效应。
5.对光具有敏感性。
2.半导体材料:
第一代为Si、第二代为GaAs、第三代微GaN。
4.Si的三种制备:
SiCL4氢还原、SiHCL3氢还原、SiH4法
5.精馏的原理:
精馏提纯是利用混合液中各组分的沸点不同来达到分离各组分的目的。
精馏的目的:
SiHCL3提纯的主要方法。
6.硅烷法的优点:
1.除B效果好2.无腐蚀性3.分解温度低4.沸点低5.外延时自掺杂低
7.分凝现象:
将含有杂质的结晶态物质熔化后再结晶时,杂质在结晶的固体和未结晶的液体中浓度是不同的,这种现象就叫分凝现象。
8.熔区提纯:
利用分凝现象将物料局部熔化形成狭窄的熔区,并令其沿锭长从一端缓慢的移动到另一端,重复多次使用杂质尽量被集中在尾部或头部,进而达到使中部材料被提纯的技术。
9.平衡分凝系数:
在一定温度下,平衡状态时,杂质在固液两相中浓度的比值,以此来描述该体系中杂质的分配关系。
(K0=CS/CL)
10.有效分凝系数:
通常把固相杂质浓度CS与熔体内部的杂质浓度CL0的比值定义为有效分凝系数Keff。
(Keff=CS/CL0)
11.BPS:
Keff=K0/[(1-K0)e-fδ/D+K0]
条件:
1.f>>D/δ时,Keff趋于1。
2.当f<3.当f≈D/δ时,Keff变化最大。
12.分凝现象使杂质浓度分布不均匀:
1.对于K<1的杂质,其浓度越接近尾部越大,向尾部集中。
2.对于K>1的杂质,其浓度越接近头部越大,向头部集中。
3.对于K≈1的杂质,基本保持原有的均匀分布的方式。
13.极限分布:
经过多次区熔提纯后,杂质分布状态将达到一个相对稳定且不再改变的状态,把这种极限状态叫做极限分布。
14.影响杂质浓度极限分布主要因素:
1.杂质的分凝系数2.熔区长度
15.影响熔区提纯的因素:
1.熔区长度2.熔区移动速度3.区熔次数的选择4.质量运输(n=(1
∼1.5)L/l,n为区融次数、L为锭长、l为熔区长度经常使L/l=10使用,n最大值是15,区融次数以20词左右为宜)
16.Ge的区融提纯结果:
17.晶体生长的三种方式:
固相生长、液相生长、气相生长
转换条件:
在气固相转变过程时,P1>P0;在溶液中生长晶体时,C1>C0,即有一定的过饱和度;在熔体中生长晶体时,∆T<0,即有一定过冷度时,其自由能变化∆G,∆gV