站场旅客地道安全快速施工工艺创新解析.docx
《站场旅客地道安全快速施工工艺创新解析.docx》由会员分享,可在线阅读,更多相关《站场旅客地道安全快速施工工艺创新解析.docx(9页珍藏版)》请在冰豆网上搜索。
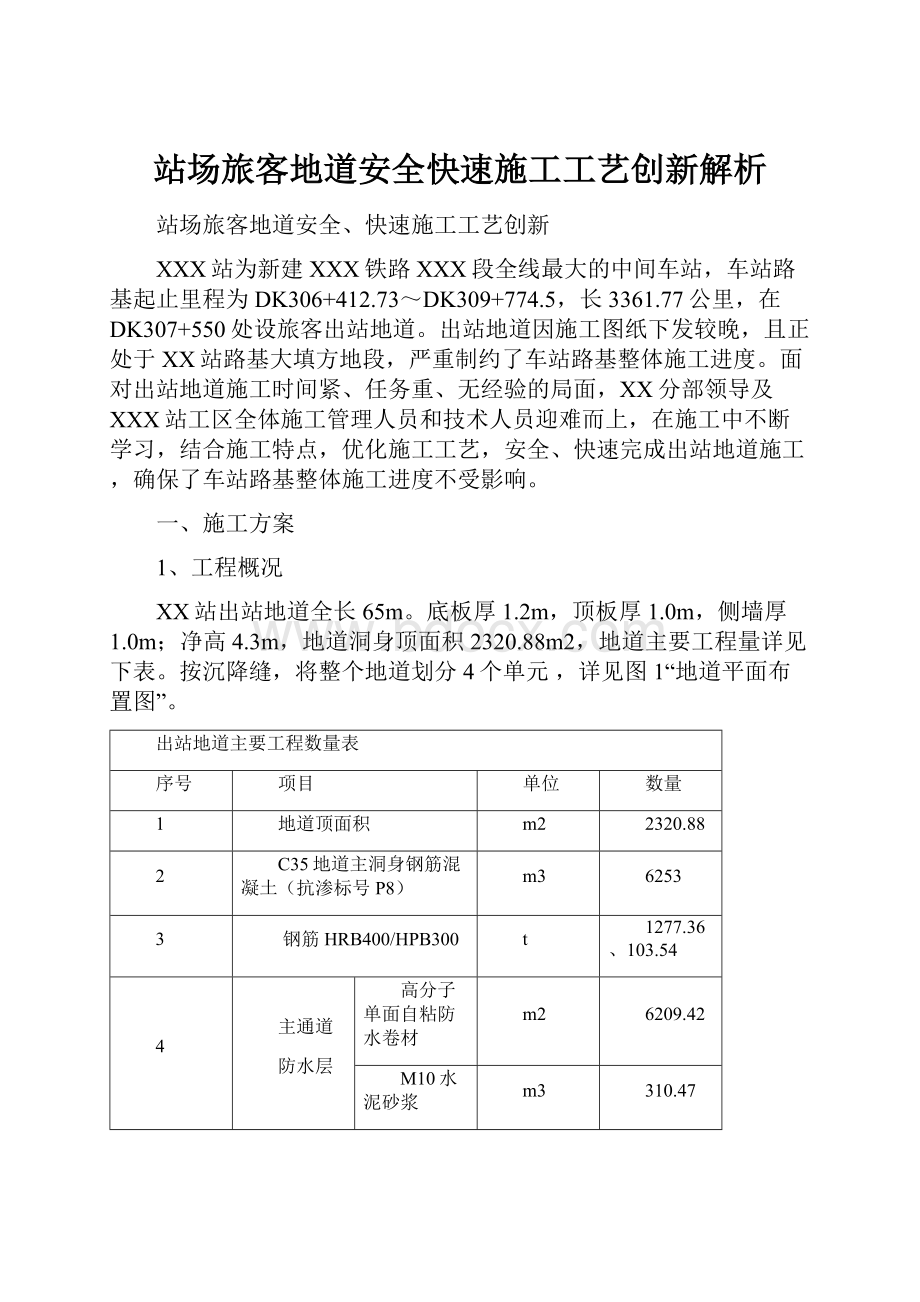
站场旅客地道安全快速施工工艺创新解析
站场旅客地道安全、快速施工工艺创新
XXX站为新建XXX铁路XXX段全线最大的中间车站,车站路基起止里程为DK306+412.73~DK309+774.5,长3361.77公里,在DK307+550处设旅客出站地道。
出站地道因施工图纸下发较晚,且正处于XX站路基大填方地段,严重制约了车站路基整体施工进度。
面对出站地道施工时间紧、任务重、无经验的局面,XX分部领导及XXX站工区全体施工管理人员和技术人员迎难而上,在施工中不断学习,结合施工特点,优化施工工艺,安全、快速完成出站地道施工,确保了车站路基整体施工进度不受影响。
一、施工方案
1、工程概况
XX站出站地道全长65m。
底板厚1.2m,顶板厚1.0m,侧墙厚1.0m;净高4.3m,地道洞身顶面积2320.88m2,地道主要工程量详见下表。
按沉降缝,将整个地道划分4个单元,详见图1“地道平面布置图”。
出站地道主要工程数量表
序号
项目
单位
数量
1
地道顶面积
m2
2320.88
2
C35地道主洞身钢筋混凝土(抗渗标号P8)
m3
6253
3
钢筋HRB400/HPB300
t
1277.36、103.54
4
主通道
防水层
高分子单面自粘防水卷材
m2
6209.42
M10水泥砂浆
m3
310.47
砼保护层
m3
232
5
地基
处理
碎石垫层
m3
696
C20砼垫层
m3
464
6
集水井
个
2
图1地道平面布置图
2、主要施工方案及方法
地道洞身施工时以沉降缝为界限整体分四个单元施工,依次顺序为:
第三节、第一节、第二节、第四节。
混凝土分三次分层浇筑。
第一次浇筑至底板以上0.5m,总浇筑高度1.7m。
第二次浇筑侧墙,总浇筑高度为2.1m。
第三次浇筑顶板。
施工过程中,为了进一步缩短工期,经研究后决定加大资源投入,对施工顺序进行优化调整,三、一节同步施工,完成后再同步施工二、四节。
3、具体施工步骤
3.1基底处理
基坑开挖采用人工配合挖掘机开挖,将地道位置已填筑的级配碎石填料和CFG桩间土清除干净。
基坑开挖过程中,应严格控制坑边堆载,坡顶边2m范围内不得大于5KN/㎡,开挖完成后,基坑上部四周设安全护栏。
基坑四周设截水沟,排截地面水,地面采用10cm厚C15混凝土硬化场地,防止地表水渗入基坑。
基底采用小型夯机夯实。
对地基承载力进行测试,满足设计要求地基承载力不小于150KPa,局部地区不满足此设计要求的进行换填碎石填料。
待基底报检合格后方可进行回填30cm厚砂加碎石,再在其上铺筑20cm的C20的混凝土垫层,四周加宽20cm。
3.2地道施工
3.2.1地道施工
(1)地道施工以沉降缝为单位进行施工
待垫层混凝土达到一定强度后,精确放线定出地道身中、边孔线位置。
先绑扎第三段地道底板及下侧墙钢筋,钢筋连接采用机械连接,注意机械连接区段长度为35d,同一连接区段内钢筋接头百分率不大于50%。
底板钢筋绑扎按照设计要求,以钢筋骨架为截面,依次绑扎。
立下侧墙内模及外模,支撑牢固。
第一次浇筑至底板以上0.5m,总浇筑高度1.7m。
模板采用钢模板,每次使用模板前要进行清理、擦油处理。
钢模板使用过程中,检查模板变形情况,发现变形严重,影响砼外观质量的,要随时进行更换;横带采用Φ48×3.5mm钢管,间距50cm;竖带采用双排Φ48×3.5mm钢管,间距50cm;采用Φ12mm光圆钢筋作为拉筋进行底板和侧墙模板的加固,拉筋竖向和横向间距均为0.5m;另外在侧墙外侧采用Φ48×3.5mm钢管和[10cm槽钢支架作为斜撑杆。
待混凝土强度达到拆模强度时,拆除下侧墙内模,安装侧墙模板。
侧墙采用定型钢模板,使用特制止水螺杆进行对拉和钢管外支撑加固。
钢筋模板安装完成后进行侧墙浇筑。
侧墙混凝土浇筑完成达到拆模强度后、安装地道顶板模板,顶部设有可以调节高度的U托,上部用木方做分配梁,支撑顶板内模。
模板采用112×244×1.8cm竹胶板;横带采用10×10cm方木,间距25cm;纵带采用双排Φ48×3.5mm钢管,间距50cm。
另外在侧墙内侧搭设Φ48×3.5mm满膛钢管支架,纵向、横向间距为60cm,竖向间距(步距)为100cm;外侧采用Φ48×3.5mm钢管作为斜撑杆。
当顶板混凝土强度达到设计强度后,才能拆除支撑及顶板底模。
(2)施工工艺
地道洞身钢筋施工
a钢筋加工
地道主钢筋接头采用机械连接,注意机械连接区段长度为35d,同一连接区段内钢筋接头百分率不大于50%。
钢筋接头不得设置在弯起位置和跨中的位置,且接头距弯起点达到10d以上距离。
b钢筋安装
首先绑扎底层钢筋,然后放置5.0cm高的垫块,每平方米不少于4块。
为保证钢筋绑扎时钢筋骨架的整体性,要在底层钢筋绑扎完毕后安装架立钢筋,然后绑扎上层钢筋。
安装钢筋时为确保钢筋的混凝土保护层厚度满足设计要求。
为此,在钢筋与模板之间采用垫块支垫,垫块采用高强度细石混凝土预制。
强度、密实度不低于本体混凝土的设计强度和密实度。
垫块互相错开,梅花型布置。
绑扎钢筋网架,在安装和浇筑混凝土过程中不能有变形、松脱现象。
在钢筋的交叉点处,用直径1.0mm的铁丝扎结,按照梅花形绑扎。
地道模板施工
地道底板、侧墙采用钢模板,顶板采用112×244×1.8cm竹胶板;另外在侧墙内侧搭设Φ48×3.5mm满樘钢管支架,纵向、横向间距为60cm,竖向间距(步距)为100cm;外侧采用Φ48×3.5mm钢管作为斜撑杆。
支架搭设前进行受力检算,确保搭设支架满足承载力要求。
支架搭设好后进行3遍检查验收,确保支架稳固安全。
首先架子队及现场管理人员进行初验,检查整改无误后报工区;工区组织分部各部门及工区生产、技术负责人共同对支架进行验收,检查整改无误后报监理;监理最后检查无安全隐患方可进行下一道工序施工。
地道洞身混凝土施工
地道混凝土由混凝土搅拌站生产供应,混凝土运输车运输,汽车泵泵送入模,当侧墙内混凝土浇筑高度大于2m时,须加串筒。
混凝土应分层进行浇筑,不得随意留置施工缝。
其分层厚度为300mm。
混凝土浇筑过程中,随时对混凝土进行振捣使其均匀密实,振捣采用插入式振捣器垂直点振,插入式振捣器的移动间距不大于振捣器作用半径的1.5倍,且插入下层混凝土内的深度为50~100mm,与侧模保持50~100mm的距离。
当振捣完毕需变换振捣棒在混凝土拌和物中的水平位置时,应边振动边竖向缓慢提出振动棒,不得将振捣棒放在拌和物内平拖,不得用振捣棒驱赶混凝土。
避免碰撞模板钢筋及其他预埋部件。
混凝土较黏稠时,应加密振点分布。
每一振点的振捣延续时间宜为20~30s,以混凝土不再沉落、不出现气泡、表面呈现浮浆为度,防止过振、漏振。
混凝土振捣完成后,及时抹平混凝土裸露面,待定浆后再抹第二遍并压光。
抹面时严禁洒水,防止过度操作影响表层混凝土的质量。
混凝土振捣过程中,避免重复振捣,防止过振,加强检查模板支撑的稳定性和接缝的密合情况,防止在振捣混凝土过程中产生漏浆。
并应符合下列规定:
混凝土生产由试验室进行监控,监控内容包括水泥、砂石料、配合比、坍落度、含气量等。
3.2.2地道封闭端板施工
地道封闭端端板为宽1.0m,高5.3m,沿线路纵向长度31.4m。
其端板采用就地灌注,与主动身采用配件相连。
主洞身施工时与端板相邻处顶、底板及侧墙须预留防水凹槽,顶板及侧墙安设配件,拆模后在其端头涂刷一层石油沥青马蹄酯,然后按封闭端板钢筋布置图,绑扎钢筋,浇筑封闭端板。
3.3防水层及沉降缝施工
3.3.1底板处理
基底处理完之后,在其上铺设200mm厚的C20砼垫层,再抹20mm厚的M10水泥砂浆找平层,并要求找平层平整密实。
当找平层达到足够强度后方可施工3mm厚高分子单面自粘防水卷材,在防水卷材施工前应将找平层清洗干净,无明水。
在铺好的防水卷材上抹50mm后M10水泥砂浆保护层,待强度达到强度后,方可进行底板钢筋施工。
3.3.2侧墙或顶板处理
施工缝不得留在侧墙与底板的交接处,应留在底板上≥500mm处为宜,施工缝仅允许水平缝,不得留垂直缝。
侧墙或顶板拆模后即可抹20mm厚M10水泥砂浆找平层,待找平层达到足够强度后方可施工3mm厚高分子单面自粘防水卷材。
地道侧墙防水层经检查合格后在其外侧设120mm厚砖保护墙。
洞身和出入口顶板待M10水泥砂浆保护层达到足够强度后浇筑10cmC15素混凝土保护层。
3.3.3沉降缝处理
钢边橡胶缝止水带:
施工支模时应注意检查钢边橡胶缝带位置是否端正,必须保证缝带的伸缩孔中心线与沉降缝中轴线重合并平整的置于砼的中间部分,模板固定位置,然后在一侧灌注砼将止水带一半埋入砼中,拆模后将中密度聚乙烯板贴在已浇筑完毕砼上,继续浇筑另一侧砼时把中密度聚乙烯板留在原位置不得损坏,沉降缝中应填塞聚硫双组份密封膏。
二、优化前后方案相比
1、施工难易程度对比
工艺基本相同,难易程度无明显差异。
2、施工周期对比
优化前计划完成时间:
9月30日
优化后实际完成时间:
8月21日
提前时间40天。
3、安全度对比
①优化后减少了吊车吊材料进入施工场地更换架车地点的次数,提高了安全系数。
②优化后,同步施工使支架搭设工人没有空闲时间从事其它工种作业,一直从事支架搭设,保证了其专业性和熟练度,搭设支架安全性更有保障。
4、经济对比
优化前后施工前期投入相同,以7月12日开始搭设支架为节点出现差异,7月12日至优化前计划完成时间9月30日时间为80天,至优化后实际完成时间8月21日时间为40天,按以上时间分人、材、机三方面对优化前后经济对比如下:
①人员投入对比
人员投入对比详见下表:
项目
优化前
优化后
平均每天施工人员数量(人)
80
120
工人平均工资(元/天·人)
120
120
工作时间(天)
80
40
总人工费(万元)
76.8
57.6
优化前-优化后(万元)
19.2
②材料投入对比
投入材料主要为竹胶板、架子管、扣件等,经物资部门折算,材料投入对比详见下表:
项目
优化前
优化后
竹胶板(元)
758.33
1112.22
架子管(元)
9695.78
16187.73
扣件(元)
1750.00
2333.33
总材料费(万元)
1.22
1.96
优化前-优化后(万元)
-0.74
③机械投入对比
投入机械主要为吊车,机械投入对比详见下表:
项目
优化前
优化后
吊车数量(台)
4
4
吊车平均租赁费(元/天·台)
1400
1400
工作时间(天)
80
40
总机械费(万元)
44.8
22.4
优化前-优化后(万元)
22.4
综合经济对比:
优化前-优化后=19.2-0.74+22.4=40.86(万元),工期提前40天,节约人工费和设备折旧费(或租赁费)约120万,优化后就比优化前节省160.86万元;若从全局考虑,优化后使为车站路基填筑创造了有利条件,大大缓解了车站整体施工的工期压力,避免了后期抢工期的大规模人员机械等资源的投入,创造的经济价值无法估量。
三、车站地道施工的重难点
⑴安全,支架搭设必须事前检算,事后检查,确保搭设支架稳定可靠方可进入下道工序作业。
⑵快速,人员、材料、机械到位,工序衔接紧密,协调配合得当,避免出现窝工、互相阻碍等问题。
四、未来的展望
由于XX站旅客地道是我处和XX集团修建的第一座大跨度车站地道,施工经验不足,尽管在施工过程中兢兢业业、小心谨慎,仍不可避免的造成了很多资源浪费,同时车站地道外观质量也差强人意。
如果我XX处将来再承建车站地道等类似大体积构造物,我们有信心精益求精,以更少的投入、更短的时间打造一座内在质量与外观质量均无可挑剔的精品工程。