现场管理者的十个方法.docx
《现场管理者的十个方法.docx》由会员分享,可在线阅读,更多相关《现场管理者的十个方法.docx(9页珍藏版)》请在冰豆网上搜索。
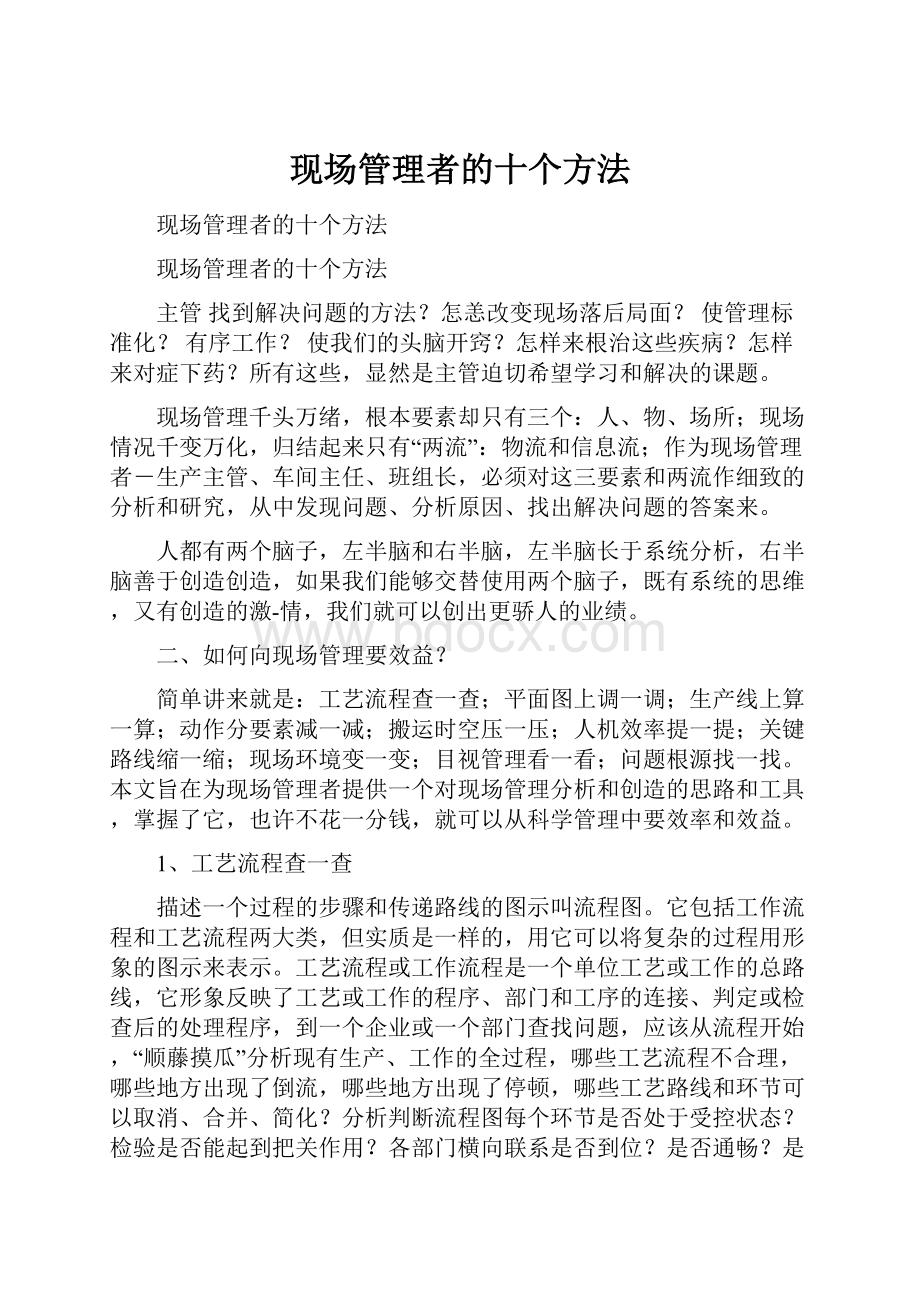
现场管理者的十个方法
现场管理者的十个方法
现场管理者的十个方法
主管找到解决问题的方法?
怎恙改变现场落后局面?
使管理标准化?
有序工作?
使我们的头脑开窍?
怎样来根治这些疾病?
怎样来对症下药?
所有这些,显然是主管迫切希望学习和解决的课题。
现场管理千头万绪,根本要素却只有三个:
人、物、场所;现场情况千变万化,归结起来只有“两流”:
物流和信息流;作为现场管理者-生产主管、车间主任、班组长,必须对这三要素和两流作细致的分析和研究,从中发现问题、分析原因、找出解决问题的答案来。
人都有两个脑子,左半脑和右半脑,左半脑长于系统分析,右半脑善于创造创造,如果我们能够交替使用两个脑子,既有系统的思维,又有创造的激-情,我们就可以创出更骄人的业绩。
二、如何向现场管理要效益?
简单讲来就是:
工艺流程查一查;平面图上调一调;生产线上算一算;动作分要素减一减;搬运时空压一压;人机效率提一提;关键路线缩一缩;现场环境变一变;目视管理看一看;问题根源找一找。
本文旨在为现场管理者提供一个对现场管理分析和创造的思路和工具,掌握了它,也许不花一分钱,就可以从科学管理中要效率和效益。
1、工艺流程查一查
描述一个过程的步骤和传递路线的图示叫流程图。
它包括工作流程和工艺流程两大类,但实质是一样的,用它可以将复杂的过程用形象的图示来表示。
工艺流程或工作流程是一个单位工艺或工作的总路线,它形象反映了工艺或工作的程序、部门和工序的连接、判定或检查后的处理程序,到一个企业或一个部门查找问题,应该从流程开始,“顺藤摸瓜”分析现有生产、工作的全过程,哪些工艺流程不合理,哪些地方出现了倒流,哪些地方出现了停顿,哪些工艺路线和环节可以取消、合并、简化?
分析判断流程图每个环节是否处于受控状态?
检验是否能起到把关作用?
各部门横向联系是否到位?
是否通畅?
是否需要构建或增加新的通路?
由流程图的各个环节及传递路线,分析现有各部门的工作职能是否到位,是否要对现有机构进行调整或重组?
有道是“框框、菱形加线条组成,但是运用起来是个宝,任你工序多复杂,透视清楚别想跑!
加一加,严格把关更牢靠;通一通,部门职能不落空。
减一减,换来效率大提高,定一定,有规有矩不争吵!
”
2、平面图上调一调
有些在建厂初期就没有对工地布置和设备布置进行过精心设计,或是由于生产的不断开展,设备的不断添置,打乱了布局,或是由于产品结构的变化,造成了厂房或设备布置不合理,从而使产品和工件在生产时运输路线过长,这是每时每刻都在制造浪费的隐患,必须下决心改变。
在工艺流程图上是看不到平面路线的,流程图上一个箭头实际可能走几十米,所以还要进一步在平面布置图上去找效益。
通过分析作业方式和设备、设施的配置,按生产流程的流动方向,有无重复路线和倒流情况,找出不合理的局部,合理调整和设计一种新的布局,来缩短工艺路线和操作者的行走距离,减少不必要的资源浪费。
有时,一台设备的移动会带来几十米甚至上百米距离的节省。
有时会节省出更多的空间。
3、流水线上算一算
生产线和流水线应该按照一致的节拍进行,生产才能均衡。
有的企业生产常常出现“前面干,后面看,前面提前走,后面在”的局面。
造成的原因一个是移动方式不合理,另一个就是节拍不均衡。
如果采用顺序移动方式,每干完一批活以后再移到下一个工序,这就会造成下工序的等待和窝工。
如果以平行移动方式传递,即干好一个就往下工序传递一个,往往会使效率提高一倍。
一个由许多块长短不同的木板箍成的木桶,决定其容量大小的并非其中最长的那块木板,而是其中最短的那块木板。
同样,在流水线上,干得最慢的人就是决定流水线最终效率的人。
生产线或流水线的平衡效率=各工序净作业时间的总和/最长工序的作业时间×人员数。
很多生产流水线的平衡率常常不到50%,如果把时间长的工序通过简化,提速、换人、或拆分的方法,对时间短的工序通过裁并、增加等等手法来平衡流水线。
整个生产线的生产效率就会大大提高,个别工序缓慢而导致的窝工和堆积就会消除。
4、动作要素减一减
任何操作都是以人工的动作为根本单元,特别是劳动密集型企业,组装工序、加工工序等这些以手工劳动为主体的工序,动作是产生效益的一个非常重要的因素。
进行动作分析,最主要的目的就是消除多余的动作、无效动作或缓慢动作,如弯腰作业、站在凳子上作业、蹲着作业、作业场所不畅、没有适合的工位器具、人与物处于寻找状态等,以最省力的方法实现最大的工作效率。
这个研究几乎不花一分钱,就可以大大提高生产效率。
例如在现实生活中,为什么有的人包饺子会比一般人快很多?
为什么有的人插秧会比一般人快很多?
那都是因为他们掌握了一定的诀窍,以最经济的动作来完成任务。
试以包饺子为例,不少人会用八个以上的动作甚至几十个动作来包一个饺子,如果你将勺子夹在右手小拇指上不放下来,按以下程序包饺子:
左手拿皮子-右手挖馅放到皮子上-两手合拢捏饺子成型-左手放饺子。
这样,只要4个动作就可以包好饺子,效率比一般人提高一倍!
动作分析要遵循以下几个最重要的动作经济原那么:
●能用脚或左手做的就不要用右手做,尽可能双手同时作业,同时开始,同时结束
●使双手同时朝着相反方向进行对称动作。
●材料和工具要尽量放在伸手就能拿到的地方,并按照根本作业要素的顺序确定适当的位置。
●减少一切不必要的动作,要知道:
没有效益的工作只能叫动作,而有效益的动作才是工作!
动作距离要最短,尽量提高效率。
●尽量利用惯性、重力、自然力和动力装置,而不是依靠,当然可以减少人的疲惫,从而有助于工作效率的提高。
●为了减轻疲劳,作业点要保持适当的高度,而这个高度是可以测出来的。
通过测量和精心计算,就能够使动作尽量地舒服一点,也能够减轻工作的疲劳。
●站立式走动作业。
从精益生产的角度来讲,为了调整生产节拍,有可能需要一个人同时操作两个或多个设备,这就要求作业人员不能坐着工作,而应该采用站立走动的作业方式,从而提高工作效率。
5、搬运时空压一压
据统计,加工费的25%到40%是搬运费;工序的时间,有70%到80%是搬运和停顿的时间;工厂的灾害,又有85%是在搬运过程中发生的。
可见对搬运进行压缩是非常重要的。
改善搬运要对搬运进行优化,从搬运数量、搬运空间、搬运时间上改善。
第一,要减少搬运的数量和搬运的次数;第二在搬运空间上要尽可能缩短搬运距离、减少搬运路线和次数;第三在搬运时间上要缩短时间、减少次数;在方法上要注意管理协调,尽量采用非动力如利用重力在斜坡滑行或在输送带上搬运。
搬运合理化的原那么是要做到对被搬运物料几乎无损耗;搬运方法要科学、文明、杜绝野蛮粗暴;搬运环境平安、适可、杜绝冒险;减少暂时放置现象的发生时机,尽可能做到一次到位;合理规划工厂布局,可以有效缩短搬运距离。
在工厂规划已经定局时,通过合理化规划流程,也可有效缩短搬运距离。
6、人机效率提一提
人和设备是一对矛盾,处理不好,就会发生不是人等机器就是机器等人。
人和设备构成了人机工程的关系,在分析时要分析作业者和机器在同一时间内的工作情况,有无窝工、等待、无效时间,通过调整工作顺序改良人机配合,寻求合理的方法,使人的操作和机器的运转协调配合,将等待时间减少到最大限度,充分发挥人和机器的效率。
就象挤水分一样将互相等待的时间挤出去,这就是向人机联合作业要效益。
7、关键路线缩一缩
几乎任何一个产品都是由假设干零件组成,通常要分几条线或几个工序生产,而且到后期都要把零件一点一点组装起来,在形成零件、部件过程中,不可防止地会发生各工序工作量大小不一的情况。
这就会在后期的生产中带来互相制约,工作量小的工序的就会有很多空闲时间,而工作量大的工序就会没有一刻休息时间,换句话说就是时差为零,成了生产上的瓶颈。
时差为零的工序就叫关键路线,它制约了企业或车间的产能和交货期,我们在找出关键路线后,要从非关键路线上抽调人财物,加强关键路线,或采用平行作业、交叉作业等等形式,缩短关键路线,不断修改和优化方案、到达缩短日程节省费用的最正确目标。
生产主管的根本功一是能根据方案和生产能力推算和找出关键路线。
二是不断压缩关键路线和其它路线,到达时间、费用的综合优化。
这里有两种方法:
1、时间优化。
就是在人力、设备、资金等有保证的条件下,寻求最短的工作周期。
它可以争取时间,迅速发挥投资效果。
利用时差,从非关键路线上抽调局部人力、物力集中用于关键路线,或分解作业,增加作业之间的平行交叉程度,增加投入的人力和设备,采用新工艺,新技术来缩短关键路线的延续时间;
2、时间—费用优化。
工程工程的费用支出可以分为直接费用和间接费用两局部。
直接费用是指与各项作业直接有关的费用如材料费、水电费,间接费用是指管理费用等不与各项活动直接有关,但随时间变动而变动的费用,工程周期越短,间接费用越小。
时间—费用优化就是寻求直接费用和间接费用之和最低时的工程周期。
8、场所环境变一变
分析生产、工作环境是否满足生产、工作需要和人的生理需要,分析现场还缺少什么物品和媒介物,针对不同类别场所的问题,分别提出改良建议,开展“、整顿、清扫、清洁、素养、平安”六项活动,做到永远保持A状态,不断改善B状态,随时去除C状态,使保持旺盛的斗志和良好的技能,所需物品随手可取,不需要之物随时得到去除,现场环境通畅、整洁、美化、平安、文明,使场所和环境在时间和空间上实现整体优化。
9、目视管理看一看
人类大脑视觉方面的信息高达80%。
因此用视觉来沟通和指挥的方法更为直接了当。
利用形象直观、色彩适宜的各种视觉感知信息来组织现场生产,以图表、图画、照片、文字注解、标志、符号、作为目视管理的工具。
可以轻而易举地到达解释、认知、警告、判断、行动等功能。
所以目视管理也可称之为“看得见的管理”、“可视化管理”。
10、问题根源找一找
每日寻找差距,以求第二天干得更好———这是海尔模式独创性中非常重要的一点,不断寻找问题、分析问题、永不休止地对现场进行改良,这是质量改良、8D工作法、CIP等活动的共性。
正是这一点推动着管理运作过程,使企业处于不断向上的良性循环中。
这些现场改善的十大利器,如果你实实在在利用它,你就会发现,这些利器神力非凡、所向披靡,你会惊喜地看到:
工艺路线顺畅了、平面布置合理了,流水线上窝工消失了,节拍更均匀了、工人操作效率高了、搬运便捷了、生产均衡了、人机结合密切了,管理简单了,一个更快、更好、更短、更顺、更爽的精益生产局面已悄然降临!
现场管理方法,降低本钱xx-09-0820:
37|#2楼
“改善”,意指持续不断地改良,它的步线是一小步一小步,阶梯式的,但随着时间的'演进,它会带来戏剧性的重大成果。
“改善”与创新不同,创新是一触即发式,令人瞩目,感受到实质的成果,但它的成果经常有争议,“改善”是运用常识的方法及低本钱的“改善”手法,即能确保阶梯式的持续进步。
它还是一种低风险方式。
因爲在改善的过程中,如果觉察有不妥当之处,管理人员随时都可回复到原来的工作方法,而无需消耗大本钱。
一、现场改善要遵循PDCA回圈/SDCA回圈;在“改善过程”中,首先要建立方案执行核查处置,即PDCA回圈,以此作爲改善持续运作的工具,以达成“维持标准”和“改良标准”的目标。
“方案”是指建立改善的目标。
“执行”是指依方案推行。
“核查”是指确认是否按方案的进度在实行,以及是否达成预定的方案。
“处置”是指新作业程式的实施及标准化。
以防止原来的问题再次发生,或者是再设定新的改良目标。
PDCA不断地在回圈。
一旦到达改善的目标,改善後的现状便随即成爲下一个改善的目标。
PDCA的意义就是永远不满足现状,因爲员工通常较喜欢停留在现状,而不会主动去改善。
所以管理人员必须持续不断地设定新的挑战目标,以带动PDCA回圈。
任何一个新的工作流程,在初期都是呈不稳定状态。
开始进行PDCA改善时,必须先将任何现有的流程稳定下来,此一稳定的过程称之爲:
标准化执行查核处置,即SDCA回圈。
二、主要的改善活动
1.及时生産方式:
及时生産方式的目的是要消除各种没有附加价值的动作和程式,同时达成一个去芜存菁的生産体系,以便更具弹性地去适应顾客的需求变化。
要实现理想的及时生産方式,必须持续不断地实施一系列的改善活动,以消除现场中没有附加价值的工作。
及时生産方式能够急速地大幅度降低本钱,缩短交货周期,增强公司的获利能力。
2.全员生産保全:
全员生産保全着重於设备质量的改良。
它通过总体的预防保养来延长设备的寿命,以追求设备效率的最大化。
3.设定目标:
管理部门应设定明确的改善目标,以指引每一位员工,同时能正确领导所有的改善活动,向既定目标迈进,最高管理部门要有一个到达目标的方案,往下传达至下一管理层,直至到达现场爲止。
而现场围绕目标展开一系列的工作。
4.提案建议制度:
它的功能着重在鼓励员工的叁与来提高士气,激发员工对现场改善的兴趣,提出自己的建议。
无论他们的建议有多小,管理者都应给予鼓励并有选择的付诸实施。
管理阶层不期望能从每一个建议中获得很大的经济利益。
着重培养,开发具有改善意识及自律化的员工,日积月累到很大的经济效益。
三、现场改善
1.现场与管理:
在现场,生産顾客满意的産品才能使公司生存和兴隆。
常规组织的各个阶层高级管理阶层、中级管理阶层、工程师职员及现场督导人员,都是爲了提供现场必要的支援而存在。
进一步而言,现场不仅是所有改善的活动场所,也是所有资讯的。
因此,爲了解决现场发生的大小问题,管理阶层必须密切接触现场的实情。
换句话说,不管管理阶层提供什麽样的
协助,都应是源自现场的特定需求。
一旦管理阶层不尊重,不珍视现场时,便会经常下达一些不适当的指示,要求和其他支援效劳给现场造成错误。
2.维护厂房良好环境的5S
5S是代表5个日文字词,它是厂房现场维持的构成要项。
(1)(seini)将现场需要与不需要的东西,区别出来。
并将後者处理掉。
(2)整顿(seiton)将後需要的东西,安排成爲有秩序的状态。
(3)清扫(seiso)保持机器及工作环境的乾净。
(4)清洁(seikesu)延伸乾净的概念至更,并且持续执行上述3个步骤。
(5)教养(sh-itsuke)以设立目标的方式,来建立自律以及养成从事5S的习惯。
厂房良好环境的维持,表示员工士气高昂及纪律严谨。
任何公司都可以在短期内达成一个高水准有纪律的公司。
然而要长久维护下去,可就是一件极富挑战性的工作了。
而且,5S一旦消失不见,就会显现出一个杂乱无章的现场。
3.检查现物
一有问题或异常的状况时,管理人员应该到现场去检查现物。
借着在现场详细检视现物,重复地问着“爲什麽”而确认出问题的原因,而用不着使用那些高深复杂的科技。
改善是从问题认定开始,一旦认识清楚了,那就已经成功了一半。
管理人员的工作之一,应当是经常保持注视行动的现场。
而且依据现场和现场的原那么来认定问题。
而不是在会议室聚集在一起讨论问题。
4.现场管理的金科玉律
大多数的管理人员,较喜欢把办公室当做工作的场所,而且希望自己能远离发生事件的生産现场。
仅通过每天、每周、甚至每月一次的报告和会议,来接触、了解现场的实情。
与现场保持密切的接触及了解,是效率化管理的第一步骤。
因此有5项现场管理的金科玉律:
(1)当问题(异常)发生时,要先去现场。
(2)检查现物(有关的物件)。
(3)当场采取暂行处置措施。
(4)开掘并将之排除。
(5)标准化以防止同样错误再发生。
模板,内容仅供参考