摘果式拣选和播种式分拣比较.docx
《摘果式拣选和播种式分拣比较.docx》由会员分享,可在线阅读,更多相关《摘果式拣选和播种式分拣比较.docx(13页珍藏版)》请在冰豆网上搜索。
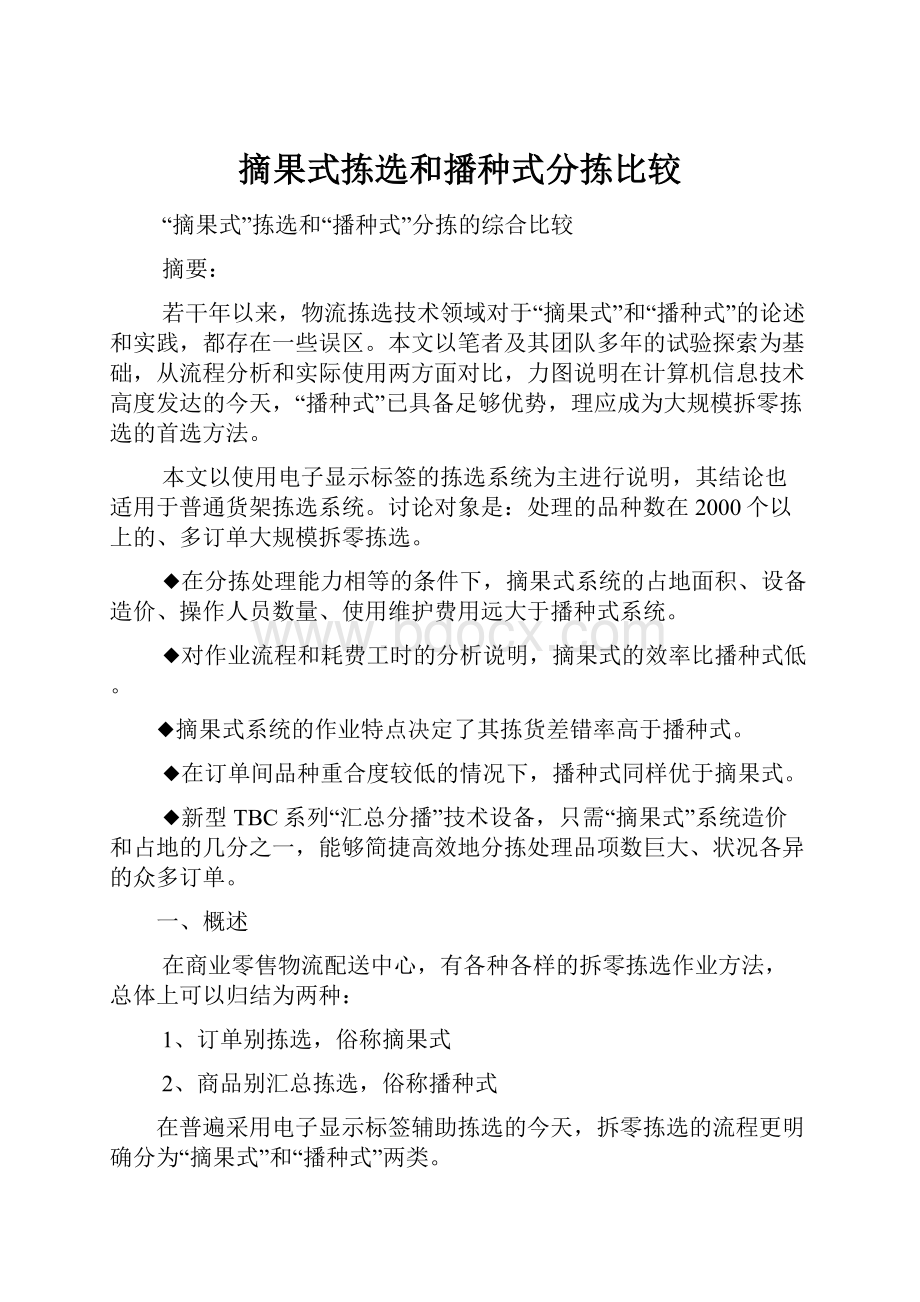
摘果式拣选和播种式分拣比较
“摘果式”拣选和“播种式”分拣的综合比较
摘要:
若干年以来,物流拣选技术领域对于“摘果式”和“播种式”的论述和实践,都存在一些误区。
本文以笔者及其团队多年的试验探索为基础,从流程分析和实际使用两方面对比,力图说明在计算机信息技术高度发达的今天,“播种式”已具备足够优势,理应成为大规模拆零拣选的首选方法。
本文以使用电子显示标签的拣选系统为主进行说明,其结论也适用于普通货架拣选系统。
讨论对象是:
处理的品种数在2000个以上的、多订单大规模拆零拣选。
◆在分拣处理能力相等的条件下,摘果式系统的占地面积、设备造价、操作人员数量、使用维护费用远大于播种式系统。
◆对作业流程和耗费工时的分析说明,摘果式的效率比播种式低。
◆摘果式系统的作业特点决定了其拣货差错率高于播种式。
◆在订单间品种重合度较低的情况下,播种式同样优于摘果式。
◆新型TBC系列“汇总分播”技术设备,只需“摘果式”系统造价和占地的几分之一,能够简捷高效地分拣处理品项数巨大、状况各异的众多订单。
一、概述
在商业零售物流配送中心,有各种各样的拆零拣选作业方法,总体上可以归结为两种:
1、订单别拣选,俗称摘果式
2、商品别汇总拣选,俗称播种式
在普遍采用电子显示标签辅助拣选的今天,拆零拣选的流程更明确分为“摘果式”和“播种式”两类。
1)摘果式拣选(订单别拣选)
摘果式拣选法,是针对每一份订单(每个客户),拣货人员或设备巡回于各个货物储位,将所需的货物取出(形似摘果)。
其特点是每人每次只处理一份订单(或一个客户)。
应用电子显示标签进行摘果式拣选,一般要求每一品种货物(货位)对应一个电子标签,控制计算机系统可根据货物位置和订单数据,发出出货指示并使货架位上的电子显示标签亮灯,操作员根据电子标签所显示的数量及时、准确地完成商品拣货。
下图是使用电子显示标签的摘果式拣选系统示意图。
下图是某配送中心的摘果式分拣线作业场景。
该线的拣选品项数约1000个。
2)播种式分拣(商品别汇总拣选)
播种式分拣,是把多份订单(多个客户的要货需求)集合成一批,把其中每种商品的数量分别汇总,再逐个品种对所有客户进行分货(形似播种)。
所以,称其为“商品别汇总分播”更为恰当。
应用电子显示标签的播种式分拣系统,其每个电子标签货位代表一张订单(一个客户),操作员先通过条码扫描把将要分拣货物的信息输入系统中,需要货物的(客户)分货位置所在的电子标签就会亮灯,同时显示出该位置所需分货的数量。
载有一个品种货物的拣货人员或设备,巡回于各个客户的分货位置,按显示数量分货。
下图是使用电子显示标签的播种式分拣系统示意图
下图是某配送中心播种式分拣线的作业场景。
该线采用“货到人”方式,一次分拣客户数最多为60个。
二、“摘果式”和“播种式”系统的平面布局
下面给出了摘果式系统和播种式系统在配送中心的平面布局图,参照条件是分拣处理的品种数和分拣输出能力大致相等。
上图——摘果式系统的平面布局图
上图中间的拆零拣选区安装了摘果式分拣线,线的长度通常大于200米。
上图——播种式系统的平面布局图
上图中间的拆零拣选区安装了四条播种分拣线,每条线长度10米。
由这两种系统的平面布局图可以看出,播种式系统的占地面积小很多,因此可以获得更多的仓储容积和作业区域。
三、两种方法的硬件设备和成本分析
应用电子显示标签的摘果式和播种式分拣系统,其硬件组成主要有:
装有电子显示标签的货架,以及配套的流水(输送)线。
从外观形式看,这两种分拣系统的硬件的主要区别是:
摘果式系统货架和流水线的长度远远大于播种式,宽度的差别不大。
1、摘果式
摘果式分拣系统,一般要求每一品种货物占用一个货位,对应使用一个电子标签。
国内现有的摘果式系统货架,一般每米长度可设置10个左右(8-12)的货位,因此2000个品种的摘果式系统,其货架长度约为200米。
配套的流水线长度一般会大于货架的长度。
2、播种式
应用电子显示标签的播种式分拣系统,其每个电子标签(货位)代表一张订单(一个客户),因此货架长度和分拣的品种多少无关,用很短的货架分拣线就可以处理品种数巨大的订单。
例如TBC型播种分拣线,可以单班处理2000个品项40个客户,其货架长度仅有10米,是前述摘果式分拣线的二十分之一。
如果四条播种式分拣线组合,长度也只有四十多米,仅为摘果式的五分之一。
3、硬件设备成本
摘果式和播种式系统,粗略估算它们的硬件造价,其每一个货位的成本、每米流水线的成本,两种系统是基本相等的。
因此,在分拣处理能力相等的条件下,由于摘果式的货架、流水线长度远大于播种式,所以摘果式系统在占地面积、设备造价、操作人员数量、使用费用等方面,将远大于播种式系统。
下图是一次分拣40份订单的播种式分拣线,长度十米。
三、作业流程和耗费工时分析:
注:
◆以含有若干份订单的一个波次为例
◆讨论范围是订单间品种重合度较高的情况
◆请与前述平面布局图对照理解
1、摘果式拣选的作业流程:
①补货:
从仓储区向拆零拣选区送货,并且逐个货位放上货架。
②沿线拣选:
周转箱沿着分拣流水线移动,分拣人员从货架上取货,放入周转箱。
③复核装箱:
对已经装入周转箱的货物进行核对(品种、数量等),有时还需要换箱装货。
④集货待运:
把已经复核装箱完毕的货箱送到发货区,等待运出。
2、播种式分拣的作业流程
①汇总拣货:
从仓储区将该波次所需货物全部拣出,送到拆零分拣区,逐个放到分拣线上。
②沿线分货(含复核装箱):
待分货箱沿着流水线移动,分拣人员从箱中取货,放入货架箱内。
间歇性复核、装箱。
③集货待运:
把已经复核装箱完毕的货箱送到发货区,等待运出。
3、作业量和耗时比较
下面按照作业流程的顺序,对两种方式的各个阶段进行比较:
(为便于理解,下面比较忽略了一些细节。
)
①摘果式的“补货”——播种式的“汇总拣货”
摘果式的补货作业,包括从仓储区将该波次所需货物拣出,以及按品项巡行于数千个货位,逐个放到拣选货位上。
播种式的汇总拣货,包括从仓储区将该批次所需货物全部拣出,以及逐个放到分拣线上。
两种方式比较,摘果式的补货作业,多出了需要巡行数千个货位的行走动作距离。
这个距离通常是几百米长度。
此外,摘果式对每个货位的放货操作,其动作量也大于播种式的放货。
由于拣选货架空间有限,对出货量较大的商品货位,摘果式往往需要进行多次补货。
而播种式只需一次。
因此,这个作业时段,摘果式的作业量、耗时要远大于播种式。
此外,摘果式大量补货时通常要暂停分拣作业,这就很难实现连续分拣,造成时间利用不充分。
播种式则没有这个问题。
②摘果式的“沿线拣选”——播种式的“沿线分货”
摘果式的沿线拣选,是从货架上取货放到流水线上;
播种式的沿线分货,是从流水线上取货放到货架上。
这两个互逆的拣货动作,耗时基本相当。
可是,摘果式的流水线长度远大于播种式,并且摘果式的货位多、转换多,周转箱移动的阻碍也多,造成摘果式分拣线的周转箱移动速度往往低于播种式(不考虑空行程)。
每当货架上货箱装满以后,播种式分拣需要做一个换箱动作;此外,播种式分拣还要间歇性进行数量复核。
完成这两件事情所需的时间,大约等于10%的拣货动作时间。
综合而论,在这个作业时段,两种方式的工效大致相当。
③摘果式的“复核装箱”
这个动作是摘果式独有多出的,就是要对流水线上下来的货箱内的品种数量进行逐一核对,有时还要重新装箱。
可见,摘果式的“沿线拣选”与“复核装箱”的作业时间之和明显超过播种式的“沿线分货”。
有些摘果式分拣线,为缩短作业时间而免去了这个“复核“动作,其后果是增加了差错率。
差错率:
播种式在分拣货物时,可以通过核对剩余数量发现前面作业的差错,因此可以明显减少差错。
摘果式则很难在作业中核对。
所以同等条件下摘果式的差错率高于播种式。
④集货待运
在这个阶段,两种方式作业量基本相等。
分析结论:
对于同样的分拣量,摘果式的行走距离较大、动作多、耗时长、差错率高。
因此播种式优于摘果式。
从另一方面说,尽管摘果式对单个订单的响应速度较快,但是播种式可以高效处理成批订单,其完成一份订单的平均时间要少于摘果式(在本文设定的条件下)。
“现代物流网”网站显示的信息,某物流专家研究结论如下:
播种式(商品别)的差错率仅为摘果式(商店别)的十分之一。
各种拣货方式的错误率对比表
拣货方式
错误率
备注
拣货单拣货
0.1%——0.5%
商店别
DPS拣货
0.01%——0.05%
商店别
RF拣货
0.01%——0.05%
商店别
DPS拣货
0.001%
商品别
四、低重合度品项分拣作业分析
在一个波次的订单里,对其中每个品种的货物,可以按照需要该品种的客户数的多少进行分类。
要货客户数超过该波次客户总数50%的品种,一般称为高重合度品种(品项)。
前面文章对于摘果和播种两种分拣方式的分析,主要适用于重合度较高的货物品项。
对于低重合度品项的分拣,是否播种式仍然具有优势?
这是一个诸多专家、教科书都没有说清楚的问题。
对于摘果式拣选,当该货物要货重合度较低时,就意味着拣货箱在流水线上巡回时,多数经过的是不需拣货的货位,即空行程。
这些空行程占用的时间、空间、操作、人员都是无效益的。
播种式分拣也有类似的情况。
为了解决这个问题,目前摘果式大多采取分区拣选策略,用减小拣货区域来减少空行程。
下图为分区摘果示意图。
其中黄色区域为输送线,黑色方块为周转箱,红色箭头表示了周转箱的移动方向。
在采用了分区策略的情况下,摘果式的作业效率又是怎样呢?
1、拣货行走距离概略分析:
一个特例:
假定对于一个2000个品项、40个客户的分拣批次,其中有30个品项是单客户要货品项。
这30个品项的拣货行走距离是:
摘果式——应用分区策略,将2000个品项的拣选区分为4个小区(参见上图),每个小区的品项货位数是500个,因此每个单客户品项的拣货行走距离为500个货位(不计主通道),30个品项总拣货行走距离为15,000个货位。
播种式——使用每线40个客户(货位)的播种式分拣线,每个单客户品项的最大拣货行走距离是40个货位,30个品项总拣货行走距离为1200个货位。
可见,摘果实的行走距离同样远大于播种式。
对于要货客户数大于1的、低重合度品项,也有类似的结论。
2、播种式的空行程问题
如前所述,对于低重合度的品项,早期播种式分拣也存在空行程的人员时间浪费问题。
上述数据表明,空行程对播种式的影响远远小于摘果式。
深圳市托贝克公司最新设计的“并行分类”播种式分拣系统,针对不同的重合度采用不同的播种流程,并行上线方案,使得高重合与低重合品项并行分拣,很好地解决了空行程问题,也缩短了订单的响应时间。
3、摘果式高低频分类并行拣选的分析
为了缩短摘果式拣选的行走距离和时间,有专家设计了高低频分类并行拣选方案,典型案例为上海可的。
实地考察发现,这个方案也有明显的缺陷:
◆高低频分类的补货、拣选作业流程比较复杂,容易出错。
◆市场要货的高低频是每天都在变化的,分拣货位很难及时跟随调整。
◆中频和低频区域没有使用机械流水线,拣货人员行走距离长,作业强度较大,差错多。
所以高低频分类并不能改变摘果式的固有缺点。
忽略两种方式的技术细节,用工业工程的一般原理分析,由于播种式采用了汇总订单成批处理的方法,必然可以省略单店处理作业的若干重复动作,效率自然要高于摘果式。
分析结论:
播种式的拣货行走距离远远小于摘果式。
行走距离长无论对于人员行走或是自动输送机都是弊端。
对于低重合度的品项分拣,播种式仍然优于摘果式。
五、提高自动化程度后的比较
摘果式和播种式分拣,在全面实现机械自动化以后,会产生什么新的情况呢?
1、这两种分拣系统,由于其处理的对象是相同的,机械动作是类似的,因此实现自动化的难度差别是不大的。
2、在全面采用自动机械输送线以后,尽管行走距离很长,摘果式拣选的工作效率得到明显提升。
但是随之而来的是:
◆分拣输送系统造价大幅提高◆使用维护费用大幅提高◆系统的复杂程度提高,可靠性降低
播种式就不存在这些问题。
3、对于补货——汇总拣货,摘果式的补货是在多个补货位进行,而播种式的补货(汇总拣货)在一个上线点进行,因此摘果式实现自动补货的成本将会大大高于播种式。
4、如果不设置复核工序,提高自动化程度很难降低摘果式的分拣差错率。
但是设置复核工序必然增加作业时间、降低效率。
5、提高自动化程度很难增加摘果式拣选的货箱容积利用率。
可见,提高自动化程度后,播种式依然优于摘果式。
六、一组数据的比较(按实测数据估算)
1、某便利店配送中心的摘果式分拣线(可的高低频并行分类型):
总分拣品项2000个,采用ABC分类分区,分拣之后不复核。
A区分拣品项1000个,分拣线长84米,人员34人,分拣速度每小时5600次。
BC区分拣品项1000个,分拣线长40米,人员12人,分拣速度每小时1600次。
共计:
分拣线长124米,人员46人,分拣速度7200次/小时。
如果分拣之后进行复核,就需要更多的人员和时间。
(此处未计摘果式比播种式多出的补货人员和工作量。
)
2、某药品配送中心播种式分拣线
总分拣品项2000个,用四条五工位分拣线,每线人员9人,分拣速度单线每小时1650次。
共计:
分拣线长40米,人员36人,分拣速度6600次/小时。
比较结论:
采用了优化分区策略的摘果式分拣系统,其占地面积(造价)约为TBC系列播种式分拣的三倍,人效比播种式低40%。
托贝克公司最新的“并行分类”播种式分拣系统,实测数据表明分拣效率比原TBC系列提升约30%。
七、TBC“汇总分播”拣选技术的新进步
播种式分拣并非十全十美,也存在一些不足:
1、订单的响应时间较长
由于播种式分拣是集合一批客户订单进行分拣,对于个别客户的紧急订单就不能很快响应。
可以采用多线并行、急货先出等方法缩短订单响应时间。
对于个别紧急订单,可以采用RF辅助人工拣货方式给予解决。
2、分拣线的操作难度稍大
实际情况表明,由于播种式分拣需要同时处理许多订单,订单间存在各种差别(品种重合度、包装体积、数量、物理状态等),因此分拣流程的整体操作难度大于摘果式。
这个问题可以通过改善控制流程、加强操作培训来解决。
3、流程的管理要求较高
摘果式分拣的工作失误只影响一个客户,播种式影响的是一批客户。
因此使用播种式分拣对流程管理的要求更高,对管理信息系统、人员、规章制度
都有更高的要求。