董斌模具失效分析.docx
《董斌模具失效分析.docx》由会员分享,可在线阅读,更多相关《董斌模具失效分析.docx(10页珍藏版)》请在冰豆网上搜索。
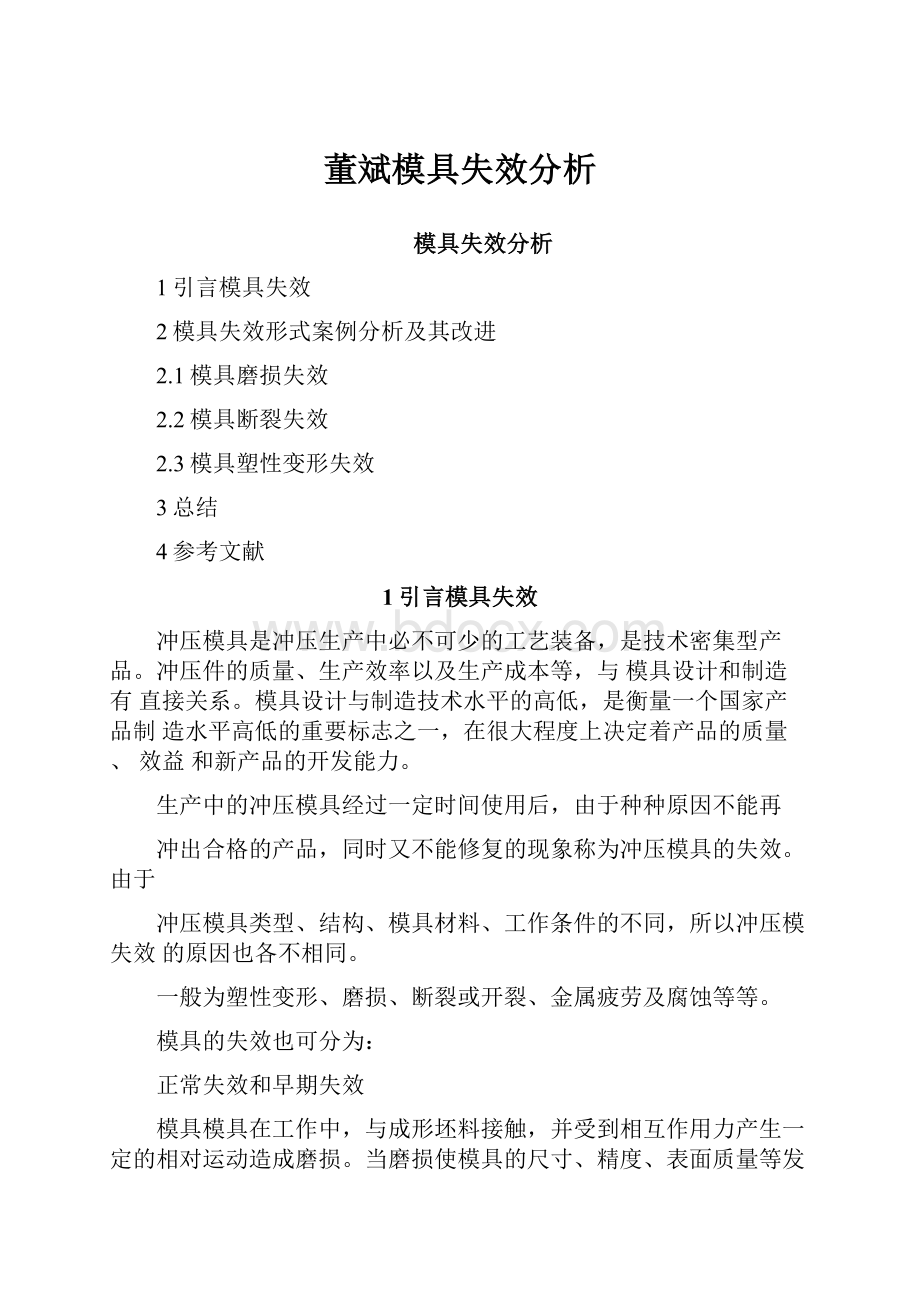
董斌模具失效分析
模具失效分析
1引言模具失效
2模具失效形式案例分析及其改进
2.1模具磨损失效
2.2模具断裂失效
2.3模具塑性变形失效
3总结
4参考文献
1引言模具失效
冲压模具是冲压生产中必不可少的工艺装备,是技术密集型产品。
冲压件的质量、生产效率以及生产成本等,与模具设计和制造有直接关系。
模具设计与制造技术水平的高低,是衡量一个国家产品制造水平高低的重要标志之一,在很大程度上决定着产品的质量、效益和新产品的开发能力。
生产中的冲压模具经过一定时间使用后,由于种种原因不能再
冲出合格的产品,同时又不能修复的现象称为冲压模具的失效。
由于
冲压模具类型、结构、模具材料、工作条件的不同,所以冲压模失效的原因也各不相同。
一般为塑性变形、磨损、断裂或开裂、金属疲劳及腐蚀等等。
模具的失效也可分为:
正常失效和早期失效
模具模具在工作中,与成形坯料接触,并受到相互作用力产生一定的相对运动造成磨损。
当磨损使模具的尺寸、精度、表面质量等发生变化而不能冲出合格的产品时,称为磨损失效,磨损失效是模具的主要失效形式,为冲模的正常失效形式,不可避免。
按磨损机理,模具磨损可分为磨粒磨损、黏着磨损、疲劳磨损、腐蚀磨损。
1磨粒磨损硬质颗粒存在于坯料与模具接触表面之间,或坯料表面的硬突出物,刮擦模具表面引起材料脱落的现象称为磨粒磨损。
2黏着磨损坯料与模具表面相对运动,由于表面凹凸不平,黏着部分发生剪切断裂,使模具表面材料转移或脱落的现象称为黏着磨损。
3疲劳磨损坯料与模具表面相对运动,在循环应力的作用下,使表面材料疲劳脱落的现象称为疲劳磨损。
4腐蚀磨损在摩擦过程中,模具表面与周围介质发生化学或电化学反应,引起表层材料脱落的现象称为腐蚀磨损。
在模具与坯料相对运动过程中,实际磨损情况非常复杂。
工作中可能出现多种磨损形式,它们相互促进,最后以一种磨损形式失效。
冲裁模的工作条件
冲裁模具主要用于各种板料的冲切。
从冲裁工艺分析中我们已经
得知,板料的冲裁过程可以分为三个阶段:
弹性变形阶段
塑性变形阶段
剪裂阶段
对于薄板冲裁模,由于模具受到的冲击载荷不大,在正常的使用
过程中,模具因摩擦产生的刃口磨损是主要的失效形式
磨损过程可分为初期磨损,正常磨损和急剧磨损三个阶段
町b)c)
團11.i.1冲裁时刃口的损伤过榨
a)局部塑变h)摩撼酣物c)疲劳抽坏
(阴期牌损阶段)(正常哪损阶段)f急剧陋损阶田)
初期磨损阶段
模具刃口与板料相碰时接触面积很小,刃口的单位压力很大,造成了刃口端面的塑性变形,一般称为塌陷磨损,其磨损速度较快•正常磨损阶段
当初期磨损达到一定程度后,刃口部位的单位压力逐渐减轻,同时刃口表面因应力集中产生应变硬化。
这时,刃口和被加工坯料之
间的摩擦磨损成为主要磨损形式。
磨损进展较缓慢,进入长期稳定的正常磨损阶段,该阶段时间越长,说明其耐磨性能越好。
急剧磨损阶段
刃口经长期工作以后,经受了频繁冲压会产生疲劳磨损,表面出现了损坏剥落。
此时进入了急剧磨损阶段,磨损加剧,刃口呈现疲劳破坏,模具已无法正常工作。
模具使用时,必须控制在正常磨损阶段以内,出现急剧磨损时,要立即刃磨修复。
2.1.2造成模具磨损失效原因
1、模具间隙选用不符合标准,模具间隙小,严格要求模具总间隙为板材厚度的20%-25沱间。
2、凹凸模具的对中性不好,包括模座和模具导向组件及砖塔镶套由于长期使用磨损或偏位而造成精度不足等原因造成模具对中性不好,应定期采用对芯棒对机床和安装座进行对中性检查调整。
3、凸模温度过高,主要是由于同一模具连续长时间冲压造成冲头过热或模具刃磨方法不当,造成模具退火而导致模具强度不够。
注:
(所有模具应要有专人刃磨,以免刃磨不当而造成模具损坏或减短模具寿命)
4、局部的单边冲切,如步冲,冲角或剪切时侧向力会使冲头偏向一边,该边的的间隙减小而造成模具磨损严重,如果机床模具安装
精度不高,严重的会使冲头偏过下模而造成凸模和凹模损坏。
2.1.3预防模具的磨损失效措施
1.合理进行冲模设计
冲模设计是否合理是预防模具磨损提高冲模耐用度的基础。
因
此在设计冲模时应设法对产品成形中的不利条件采取有效措施。
对于
易磨损的凸、凹模,要设计成互换性好的零件,以便凸、凹模磨损后能随时进行更换,使冲模始终保持良好的工作状态。
对弯曲模和拉深模,凸、凹模的间隙最好设计成可调的,以便当冲模磨损后经表面磨光和抛光后,对间隙值进行微调,即可使用。
对冲裁模,冲模的间隙值要选择合理,其间隙值不可太小,否则会直接影响冲模的使用寿命及耐用度,若过大,又会使工件形成拉长的毛刺。
2.正确选择冲模材料
不同的冲模材料具有不同的强度、韧性和耐磨性,应根据被加工工件的种类、形状、数量和大小及硬度高低来选取冲模材料。
对于生产批量大,磨损较严重的冲模,可采用耐磨的硬质合金来制造模具。
在一定的条件下使用较高级材料会使冲模耐用度提高好几倍。
3.合理进行冲模零件的锻造及热处理
在选择优质冲模钢材的同时,对不同的材料要进行合理的锻造和热处理,这是预防磨损、提高冲模耐用度的主要途径之一。
例如在淬火时,若在加热时产生过热不但会使此工件造成过大的脆性,而且
在冷却时容易引起变形和开裂。
另外还可采用一些表面强化工艺(真
空热处理、离子氮化处理、气体软氮化工艺、渗硼处理等)来提高表
面硬度、耐磨性及抗腐蚀性等。
4•保证被冲压板材和坯件的质量严格检查被冲压板材和坯件的质量,使其材质一定要均匀,厚薄一致,表面平整,不应有明显的凸起或凹坑,材料表面光洁,无毛刺和其它杂物等。
5•保持凸、凹模刃口的锋利及适当的润滑对冲裁模应经常刃磨凸、凹模刃口,使其始终保持刃口锋利性,而对弯曲、拉深等成形模具应经常将凸、凹模表面磨光保持较低的表面粗糙度值。
在冲压时,还
应经常在模具工作部位和毛坯件表面涂以适当的润滑油,使其在模具或坯件表面形成润滑膜,减少凸、凹之间的直接磨损。
6.选用合适的设备及加强模具维护
在冲压加工中应选用较高精度和较高刚性的压力机进行冲压,以减少由于压力机的精度而造成的凸、凹模单面磨损。
同时,操作者必须合理地使用及维护冲模,对冲模应经常进行检修;随时清除凸、凹模工作部位的废渣或杂物,保持工作台面的整洁,安全文明生产。
模具出现较大裂纹或分离为数部分而丧失工作能力,称为断裂效。
不
热应力和组织应力作用,有些热作模具的工作温度较高,又采用一定
的强制冷却方式,形成较大的内应力,且其内应力又远远大于机械应力,因此,较多热作模具零件断裂失效的主要原因与内应力过大有关。
模具断裂失效因果图见图1
根据断裂失效机理分析,按断裂原因可分为:
过载断裂、疲劳断裂等
当模具零件外加载荷超过其危险截面所能承受的极限应力时,零件
将发生断裂,这种断裂称为过载断裂。
过载断裂的断口宏观特征与材料拉伸断口形貌雷同。
当材料塑性较好时,宏观断口显示出较大的塑
性变形,而材料较脆时,零件断口呈脆性。
模具零件经过一定次数的循环载荷或交变应力作用
后引发的断裂现象称为疲劳断裂。
疲劳断裂过程一般经历三个阶段:
疲劳裂纹的萌生,疲劳裂纹的扩展,最终断裂或瞬间断裂。
典型的疲劳断口主要特征为:
按照断裂过程形成三个形貌不同的区域。
①疲劳
核心区,它是疲劳断裂的源区,断口呈光滑、细洁的狭小区域。
②疲
1防止材质不良引起裂纹
模具材料内部缺陷,如疏松、缩孔、夹杂物、成分偏析、碳化物分布不均,及材料的表面缺陷,如氧化、脱碳、折叠、疤痕等均会影响钢材性能,并造成锻造或热处理产生裂纹,引起断裂失效。
针对上述情况,常采取以下预防措施:
①加强原材料的质量检验,严格控制钢材中碳化物不均匀度级别要求。
②钢材在锻轧时,模具坯料应反复多方向锻造,从而使钢中共晶碳化物击碎得更为细小、均匀。
③选用淬透性良好的材料,使其淬火后能获得均匀的应力状态,以避免开裂或变形。
例如冲裁模,通常凹模应选淬透性好的材料,而凸模则要求相应低些。
2防止锻造裂纹
选择合理的锻造工艺参数,是保证模具锻件质量的重要条件。
坯料加热过程中应避免发生过热或过烧现象。
因加热温度过高会引起晶粒迅速长大,使坯料塑性下降,影响锻件力学性能。
过烧则会使金属晶粒边界出现氧化及形成易溶氧化物。
过烧的坯料,塑性很差,强度严重降低,一经锻打即破碎成废料。
因此,锻造过程中应严格控制加热温度,防止发生过烧现象,并防止加热过程中坯料氧化。
预防措施为:
锻件加热时,装炉温度不宜过高及加热速度不可过快,否则锻件心部与表层温差过大而造成内应力过大,导致内部产生裂纹。
尤其是大型模具锻件加热时,坯料应采取预热措施,避免温差过大。
锻件的冷却方式也将影响锻件的质量。
终锻后应将锻件放置在500到700C加热炉中,随炉缓慢冷却。
一般情况下,锻件中含碳量、合
金元素含量越高,体积越大,形状越复杂,冷却速度应越缓慢[4]
模具锻后应及时退火。
一般可采用球化退火,如CrWMn钢采用等温球化退火工艺,将锻件加热至780C左右,保温2到3h,随炉冷至680到720C保温4到5h,再随炉冷却(冷却速度小于25C/h)至500C出炉空冷,以获得均匀的球化退火组
织,硬度<229HBS
3防止淬火裂纹
消除内应力退火,防止过热或过烧,防止氧化和脱碳,防止淬火变
形与裂纹,防止回火裂纹等。
塑料模具在服役时承受很大的应力,而且不均匀。
当模具的某个部位的应力超过了当时温度下模具材料的屈服极限时,就会以晶格滑移、孪晶、晶界滑移等方式产生塑性变形,改变了几何形状或尺寸,而且不能修复再服役时,叫塑性变形失效。
塑性变形的失效形式表现为镦粗、弯曲、形腔胀大、塌陷等。
模具的塑性变形是模具金属材料的屈服过程。
是否产生塑性变形,起主导作用的是机械负荷以及模具的室温强度。
在高温下服役的模具,是否产生塑性变形,主要取决于模具的工作温度和模具材料的高温强度。
出现塑性变形失效的主要原因有:
1.模具材料的强度水平不高;
2.模具材料虽选择正确,但热处理工艺不正确,未能发挥模具钢的强韧性
3.冲压操作不当,发生意外的超载。
预防措施:
产生塑性变形失效的主要原因是模具材料强度不足,表面硬化层太薄以及工作温度高于回火温度而导致回火软化等。
这种失效属于非正常失效,一般可通过选用较好的模具材料或适当的热处理强化方法予以避免。
生产中,无论采用何种模具钢,为保证型腔表面具有足够的强度和硬度,一般都要对它们进行淬火处理(针对碳素结构钢),
渗碳层厚度通常大于0.8mm
常见模具失效形式有磨损、断裂、塑性变形。
模具失效是个综合性问题,与模具结构、工作条件、模具材料、加工方法、维护与管理等多方面因素有关,必须针对具体问题具体分析,针对不同的影响因素,采取不同措施来预防模具的早期失效。
对模具进行失效形式分析和改进措施非常有必要,对延长模具寿命,减少成本很有作用。
[1]邓明,胡亚民,彭威允.模具技术讲座[J].机械工人:
冷加工,2001(3),55〜57.
[2]曾珊琪,丁毅.模具寿命与失效[M].北京:
化学工业出版社,2005,16〜28,81〜122.
[3]孙凤勤.冲压与塑压设备[M].北京:
机械工业出版社,2003,26〜27.
[4]刘晋春,赵家齐,赵万生.特种加工[M].北京:
机械工业出版社,2004,10〜12.