240吨高温高压循环流化床锅炉运行规程大学毕设论文.docx
《240吨高温高压循环流化床锅炉运行规程大学毕设论文.docx》由会员分享,可在线阅读,更多相关《240吨高温高压循环流化床锅炉运行规程大学毕设论文.docx(145页珍藏版)》请在冰豆网上搜索。
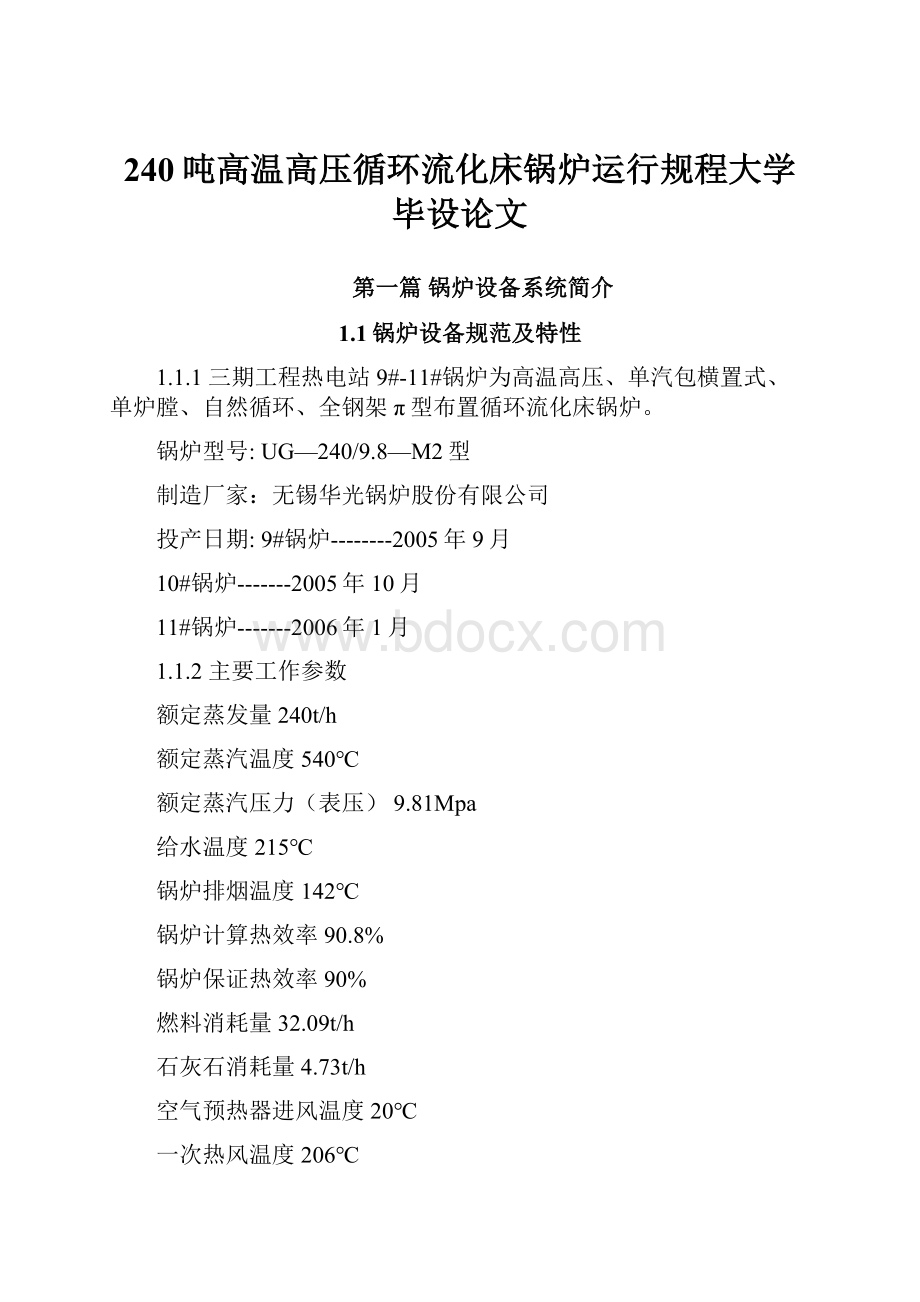
240吨高温高压循环流化床锅炉运行规程大学毕设论文
第一篇锅炉设备系统简介
1.1锅炉设备规范及特性
1.1.1三期工程热电站9#-11#锅炉为高温高压、单汽包横置式、单炉膛、自然循环、全钢架π型布置循环流化床锅炉。
锅炉型号:
UG—240/9.8—M2型
制造厂家:
无锡华光锅炉股份有限公司
投产日期:
9#锅炉--------2005年9月
10#锅炉-------2005年10月
11#锅炉-------2006年1月
1.1.2主要工作参数
额定蒸发量240t/h
额定蒸汽温度540℃
额定蒸汽压力(表压)9.81Mpa
给水温度215℃
锅炉排烟温度142℃
锅炉计算热效率90.8%
锅炉保证热效率90%
燃料消耗量32.09t/h
石灰石消耗量4.73t/h
空气预热器进风温度20℃
一次热风温度206℃
二次热风温度202℃
一、二次风量比60:
40
排污率≤1%
循环倍率25~30
锅炉飞灰份额70%
脱硫效率(钙硫摩尔比为2.3时)≥90%
1.2燃料特性
电厂燃用劣质烟煤与煤矸石的混煤,煤质分析资料见下表
名称
符号
单位
数值
设计煤种
校核煤种
收到基低位发热值
Qnet,ar
KJ/kg
21100(5024)
20060(4776)
干燥无灰基挥发分
Vdaf
%
21.00
27.87
全水分
Mar
%
6.00
4.3
收到基灰分
Aar
%
29.40
30.82
收到基碳
Car
%
53.43
54.6
收到基氢
Har
%
3.24
2.95
收到基氧
Oar
%
5.17
4.18
收到基氮
Nar
%
0.46
0.85
收到基全硫
Sar
%
2.30
2.30
灰变形温度
DT
℃
灰软化温度
ST
℃
灰熔化温度
FT
℃
1.2.1煤的入炉粒度要求:
粒度范围0~10mm,50%切割粒径d50=1.5mm,粒径分布详见附图。
1.2.2锅炉点火及助燃用油
锅炉点火及助燃用油:
0#轻柴油
序号
分析项目
单位
标准要求
实验方法
1
10%蒸余物残碳
%
≯4
GB/T268
2
水分
%
痕迹
GB/T260
3
运动粘度
mm2/S
3.0-8.0
GB/T265
4
闭口闪点
℃
<65
GB/T261
5
灰分
%
≯0.025
GB/T508
6
硫醇硫含量
%
≯0.01
GB/T380
7
机械杂质
%
无
GB/T511
8
硫含量
%
≯0.2
GB/T380
9
凝点
℃
≯0
GB/T510
1.3灰渣特性
(灰成分分析资料—来自技术开发部化验报告,脱硫投入时的灰样)
名称
符号
单位
数值
三氧化二铝
AI2O3
%
27.00
二氧化硅
SIO2
%
46.30
三氧化二铁
Fe2O3
%
5.46
二氧化钛
TiO2
%
0.88
氧化钠
Na2O
%
0.08
氧化钾
K2O
%
0.26
氧化钙、氧化镁
CaO+MgO
%
6.48
其它
/
%
2.99
烧失重(灼减)
/
%
10.55
1.4石灰石特性
石灰石的入炉粒度要求:
粒度范围0~1mm,50%切割粒径d50=0.3mm,粒径分布详见附图。
脱硫剂石灰石成分:
名称
符号
单位
数值
烧失重
\
%
43.47
氧化铝
AL2O3
%
0.85
氧化硅
SiO2
%
0.72
氧化镁
MgO
%
0.87
氧化钙
CaO
%
53.77
氧化铁
Fe2O3
%
0.32
1.5汽水品质
1.5.1给水品质
水源:
地下水
硬度:
0mg/l
PH值:
8.8~9.3
锅炉正常排污率:
≤1%
1.5.2蒸汽品质
钠:
≤10ug/l
二氧化硅:
≤20ug/l
导电度(25℃):
≤0.1uΩ/cm
1.6锅炉计算汇总表
热力计算汇总表1(100%额定负荷,设计煤质)
序号
项目名称
符号
单位
数据来源
结果
锅炉设计参数
1
额定蒸发量
D
t/h
设计数据
240
2
额定蒸汽压力
P
MPa
设计数据
9.81
3
额定蒸汽温度
T
℃
设计数据
540
4
汽包工作压力
Pd
MPa
设计数据
10.8
5
给水温度
tgs
℃
设计数据
215
锅炉设计煤质
1
收到基碳
Car
%
设计数据
53.43
2
收到基氢
Har
%
设计数据
3.24
3
收到基氧
Oar
%
设计数据
5.17
4
收到基氮
Nar
%
设计数据
0.46
5
收到基硫
Sar
%
设计数据
2.30
6
收到基灰分
Aar
%
设计数据
29.40
7
收到基水分
Mt,ar
%
设计数据
6.00
8
干燥无灰基挥发份
Vdaf
%
设计数据
21.00
9
收到基低位发热量
Qnet,ar
kcal/kg
设计数据
5024
锅炉各部件出口过剩空气系数
序号
项目名称
符号
单位
数据来源
结果
1
炉膛漏风系数
Δαl
设计数据
0
2
炉膛出口过量空气系数
α"l
计算结果
1.22
3
旋风筒漏风系数
Δαcl
设计数据
0
4
旋风筒出口过量空气系数
α"cl
计算结果
1.22
5
高过漏风系数
Δαgr
设计数据
0
6
高过出口过量空气系数
α"gr
计算结果
1.22
7
低过漏风系数
Δαdr
设计数据
0
8
低过出口过量空气系数
α"dr
计算结果
1.22
9
省煤器漏风系数
Δαsm
设计数据
0.02
10
省煤器出口过量空气系数
α"sm
计算结果
1.24
11
空预器漏风系数
Δαk
设计数据
0.03
12
空预器出口过量空气系数
α"k
计算结果
1.27
锅炉热效率
1
冷空气温度
tlk
℃
设计数据
20
2
一次热风温度
trk1
℃
设计数据
206
3
二次热风温度
trk2
℃
设计数据
202
4
排烟温度
θpy
℃
设计数据
142
5
排烟热损失
q2
%
计算结果
5.99
6
气体不完全燃烧损失
q3
%
计算结果
0.05
7
机械不完全燃烧损失
q4
%
计算结果
2.53
8
散热损失
q5
%
计算结果
0.55
9
灰渣物理热损失
q6
%
计算结果
0.07
10
总热损失
qe
%
计算结果
9.19
11
锅炉热效率
η
%
计算结果
90.81
12
保热系数
Φ
计算结果
0.994
13
锅炉有效利用热量
Qyx
kcal/kg
计算结果
1.46E+08
14
燃料消耗量
B
kg/h
计算结果
32095
15
计算燃料消耗量
Bj
kg/h
计算结果
31282
16
石灰石煅烧成CaO吸热
qx
%
计算结果
-1.09
17
CaO生成CaSO4放热
qf
%
计算结果
1.36
18
石灰石脱硫放热
qn
%
计算结果
0.27
19
锅炉修正热效率
qn
%
计算结果
91.08
锅炉热负荷
1
锅炉体积热负荷
qv
kw/m3
计算结果
115
2
锅炉截面热负荷
qs
kw/m2
计算结果
3485
锅炉第一级减温水(低温过热器出口)
1
减温器喷水量
Djw1
kg/h
计算结果
8244
2
蒸汽减温焓降
ip
kcal/kg
计算结果
18.70
3
减温器减温能力
Δt
℃
设计数据
26
锅炉第二级减温水(屏式过热器出口)
1
减温器喷水量
Djw2
kg/h
计算结果
3962
2
蒸汽减温焓降
ip
kcal/kg
计算结果
9.21
3
减温器减温能力
Δt
℃
设计数据
14
锅炉烟风流量
1
空预器出口烟气量
Qpy
Nm3/h
计算结果
229085
2
空预器进口一次风量
Q1
Nm3/h
计算结果
124118
3
空预器进口二次风量
Q2
Nm3/h
计算结果
85699
锅炉灰渣流量(不脱硫)
1
灰渣总流量
M
kg/h
计算结果
9436
2
炉膛底渣量占总灰量比例
R
计算结果
0.20
3
底渣流量
Ms
kg/h
计算结果
1887
4
飞灰流量
Mf
kg/h
计算结果
7549
锅炉灰渣流量(脱硫)
1
灰渣总流量
M
kg/h
计算结果
14970
2
炉膛底渣量占总灰量比例
R
计算结果
0.31
3
底渣流量
Ms
kg/h
计算结果
4654
4
飞灰流量
Mf
kg/h
计算结果
10316
锅炉SO2流量
1
原始排放
Eo
mg/Nm3
计算结果
6279
2
脱硫后的排放
E
mg/Nm3
计算结果
377
锅炉Nox排放
1
原始排放
Eo
mg/Nm3
计算结果
240
锅炉尾部粉尘排放浓度
1
不脱硫粉尘排放浓度
Eo
g/Nm3
计算结果
32.1
2
脱硫粉尘排放浓度
E
g/Nm3
计算结果
43.7
锅炉石灰石流量
1
脱硫石灰石流量
E
kg/h
计算结果
4733
2
钙硫摩尔比
Ca/S
/
计算结果
2.0
3
脱硫效率
η
%
计算结果
85.0
热力计算汇总表2(100%额定负荷,设计煤质)
序号
名称
符号
单位
炉膛
分离器
转向室
高过
屏过
低过
省煤器
一次风
二次风
1
管子外径
d
mm
60/51
38
51
38
42
38
32
40
40
2
管子壁厚
s
mm
5
6
5
5
6
5
4
1.5
1.5
3
横向节距
S1
mm
80
100
100
60
100
86
65
65
4
纵向节距
S2
mm
72
76
45
52
52
5
横向管子排数
Z1
排
144
80
22
80
92
121
121
6
纵向管子排数
Z2
排
24
33
86
58
40
7
受热面积
H
m2
956
99
151
957
144
1317
5456
3728
2563
8
附加受热面
Hfj
m2
71
137
9
烟气流速
Wy
m/s
10.38
8.77
8.19
8.54
8.48
10
工质流速
Wg
m/s
7.42
10.24
14.11
28.89
10.71
0.97
12.78
16.11
11
质量流率
D
kg/m2s
414
529
451
1054
428
12
烟气进口温度
θ'
℃
904
905
861
904
690
536.6
302.1
246
13
烟气出口温度
θ"
℃
904
905
861
690
904
536.6
302.1
142
184
14
工质进口温度
t'
℃
317.3
317.3
339.2
444.4
398.5
362.3
215
20
20
15
工质出口温度
t"
℃
317.3
339.2
362.3
540
458.4
424.5
286.1
206
202
16
传热系数
K
kcal/m2.h.℃
68.4
53.6
43.1
36
19.3
21.7
17
工质吸热量
Q
kcal/kg
2510.4
239.7
126.8
461.3
312.2
393.4
602.9
234.8
159.4
18
附加面工质吸热量
Qfj
kcal/kg
25.7
24.7
1.7炉膛水冷壁
炉膛断面尺寸为8770mm×5970mm,炉膛四周由管子和扁钢焊成全密封膜式水冷壁。
前后及两侧水冷壁分别各有109-φ60×5与74-φ51×5根管子。
前后水冷壁下部密相区处的管子与垂直线成一夹角,构成上大下小的锥体。
锥体底部是水冷布风板,布风板下面由后水冷壁管片向前弯与两侧墙组成水冷风室。
布风板至炉膛顶部高度为32.2m,炉膛烟气截面流速4.7m/s。
后墙水冷壁上部两侧管子在炉膛出口处向分离器侧外突出形成导流加速段,下部锥体处部分管子对称让出二只返料口。
前墙水冷壁下方有4只加煤口,侧墙水冷壁下部设置供检修用的专用人孔,炉膛密相区前、后墙水冷壁上还布置有二次风喷口(前墙两排,后墙三排)。
前、后、侧水冷壁分成四个循环回路,由汽包底部水空间引出3根φ325×25集中下降管,通过18根φ159×12的分散下降管向炉膛水冷壁供水。
其中两侧水冷壁下集箱分别由3根分散下降管引入,前、后墙水冷壁下集箱分别由6根分散下降管引入。
两侧水冷壁上集箱相应各有3根φ159×12连接管引至汽包,前、后墙水冷壁上集箱有12根φ159×12引出。
2片水冷屏则各有从汽包引出的一根φ219×16下降管供水,再分别由2根φ159×12的引出管引至汽包。
水冷壁系统的集箱除前后上集箱合并成φ325的集箱外,其余均为φ219×25。
炉膛水冷壁回路特性表:
回路
前、后水冷壁
侧水冷壁
水冷屏
上升管根数与规格
n-φ×s
2×109-φ60×5
2×74-φ51×5
2×24-φ60×5
水连接管根数与规格
n-φ×s
2×6-φ159×12
2×3-φ159×12
2×1-φ219×16
汽水引出管根数与规格
n-φ×s
12-φ159×12
2×3-φ159×12
2×2-φ159×12
下降管根数与规格
n-φ×s
3-φ325×25
水连接管与上升管截面之比
%
0.401
0.44
0.582
引出管与上升管截面之比
%
0.401
0.44
0.607
水冷壁、集箱、连接管的材料均为20G/GB5310。
水冷壁上设置有人孔、看火孔、温度测点、炉膛压力测量孔,水冷壁顶部设置了6只检修绳孔。
整个水冷壁重量由水冷壁上集箱的吊杆装置悬吊在顶板上,锅炉运行时水冷壁向下热膨胀,最大膨胀量158mm。
1.8高效蜗壳式汽冷旋风分离器
(1)分离器是循环流化床锅炉的重要组成部件,本锅炉采用的是中科院工程热物理研究所的高效蜗壳式汽冷旋风分离器专利技术,在炉膛出口并列布置两只汽冷旋风分离器,分离器直径φ5000mm,用φ38×6的管子和鳍片组成膜式壁作为旋风分离器的外壳,并采用蜗壳进口的方式形成结构独特的旋风分离器。
具有分离效率高和强化燃烧的优点。
旋风分离器将被烟气夹带离开炉膛的物料分离下来。
通过返料口返回炉膛,烟气则流向尾部对流受热面。
整个物料分离和返料回路的工作温度为930℃左右。
(2)包覆分离器的汽冷受热面能够有效吸收物料后燃所产生的热量,防止返料器内高温结焦,同时由于耐火层较薄还可以缩短锅炉的启动时间。
(3)分离器内表面焊有密排抓钉,并浇注一层60mm厚的特种耐磨可塑料,使整个分离器的内表面得到保护,从而使分离器具有较长的使用寿命。
(4)分离器出口管采用高温耐热合金钢制造,材质为1Cr25Ni20。
(5)分离器入口开设检修门,并保证其密封性。
(6)返料器和立管内设有热电偶插孔及观察窗,以监视物料流动情况。
(7)汽冷旋风分离器作为过热器受热面的一部分。
1.9汽包及汽包内部设备
汽包内径φ1600mm
厚度100mm
封头厚度100mm
筒身长12000mm
全长13800mm
材料P355GH(19Mn6)
汽包正常水位汽包中心线以下180mm(0水位)
水位正常波动值±50mm
汽包内采用单段蒸发系统布置有旋风分离器、清洗孔板和顶部百叶窗等内部设备。
汽包给水管座采用套管结构,避免进入汽包的给水与温度较高的汽包壁直接接触,降低汽包壁温温差与热应力。
汽包内装有44只直径φ315mm的旋风分离器,分前后两排沿汽包筒身全长布置,汽水混合物采用分集箱式系统引入旋风分离器。
每只旋风分离器平均负荷为6.0T/H。
汽水混合物切向进入旋风分离器,进行一次分离,汽水分离后蒸汽向上流动经旋风分离器顶部的梯形波形板分离器,进入汽包的汽空间进行重力分离,然后蒸汽通过清洗孔板以降低蒸汽中携带的盐份和硅酸根含量,经过清洗后的蒸汽再经过顶部百叶窗和多孔板进行二次汽水分离,最后通过汽包顶部饱和蒸汽引出管进入过热器系统。
清洗水量取百分之百的汽包给水,清洗后的水进入汽包的水空间。
为防止大口径下降管入口产生旋涡和造成下降管带汽,在下降管入口处装有栅格及十字板。
此外,为保证良好的蒸汽品质,在汽包内装有磷酸盐加药管和连续排污管。
为防止汽包满水,还装有紧急放水管。
汽包上设有上下壁温的测量点,在锅炉启动点火升过程中,汽包上下壁温差允许最大不得超过50℃。
同样,启动前锅炉上水时为避免汽包产生较大的热应力,进水温度不得超过90℃,并且上水速度不能太快,尤其在进水初期更应缓慢。
1.10燃烧设备
燃烧设备主要包括给煤装置、布风装置、排渣装置、给石灰石装置、点火装置、物料分离装置、返料回灰装置和一二次风及流化风供风装置。
1.10.1给煤装置
给煤装置包含4台称重式给煤机和4台刮板给煤机,称重式给煤机和刮板给煤机串联布置,构成4套给煤装置。
刮板给煤机与落煤管通过膨胀节相连,解决给煤机与炉膛水冷壁之间的膨胀差(膨胀值145mm)。
给煤装置的给煤量能够满足在2台给煤装置故障时,其余2台给煤装置仍能保证锅炉100%额定出力。
一定粒度的燃煤经给煤机进入布置在前墙的四根φ325×10间距为2m的落煤管,落煤管上端有送煤风,下端靠近水冷壁处有播煤风,给煤借助自身重力和引入的送煤风沿着落煤管滑落到下端,在距布风板1800mm处进入炉膛。
给煤量通过改变称重式给煤机的转速来调整。
给煤机内通入一次风冷风作为密封风(约有4000Pa的正压)。
播煤风管连接在每个落煤管的端口,并配备风门以控制入口风量。
1.10.2布风装置
风室由向前弯曲的后墙水冷壁及两侧墙水冷壁组成,风室内浇注100mm厚的中质保温混凝土。
防止点火时鳍片超温,并降低风室内的水冷度。
燃烧室一次风从左右两侧风道引入风室。
风室与炉膛被布风板隔开,布风板系水冷壁与扁钢焊制而成,布风板的横断面为8770×2800,其上均匀布置有903只风帽。
一次风通过这些风帽均匀进入炉膛,流化床料。
风帽采用耐磨耐高温合金,风帽横向纵向节距均为160mm。
为了保护布风板,布风板上的耐火浇注料厚度为150mm。
1.10.3排渣装置
底渣从水冷布风板上的三根φ219水冷放渣管排出炉膛,其中两根接滚筒冷渣机,每台冷渣机按6t/h冷渣量配置,另一根作为事故排渣管。
滚筒式冷渣器中的冷却水自化学除盐水来,换热后送入汽机低压除氧器。
底渣通过滚筒式冷渣器,可实现连续排渣。
出渣量以维持合适的风室压力为准。
通常运行时的风室压力约为8500~9500Pa。
定期排渣的大渣含碳量较低,能小于1.5%,而连续排渣的大渣含碳量会有所升高。
1.10.4给石灰石
锅炉添加石灰石(或生石灰)进行脱硫。
石灰石通过气力输送经二次风口送入炉膛。
脱硫的石灰石耗量每小时4.73吨,按钙硫比2.0计算,脱硫效率为85%。
1.10.5二次风装置
二次风通过分布在炉膛前、后墙上的二次风管喷口分别送入炉膛下部不同高度的空间。
前墙分两排共13根,后墙分三排共3根,合计26根。
喷口风速>70m/s。
运行时二次风压一般不小于6000Pa。
为了精确控制风量组织燃烧,一、二次风总管上装设电动风门及测风量装置。
1.10.6床下点火燃烧器
两台床下点火燃烧器并列布置在炉膛水冷风室后侧。
由点火油枪、高能电子点火器及火检装置组成。
点火油枪为机械雾化,燃料为0#轻柴油。
每支油枪出力900kg/h,油压2.5MPa,油枪所需助燃空气来自一次热风。
空气和油燃烧后形成850℃左右的热烟气。
从水冷风室上的布风板均匀送入炉膛。
为了便于了解油枪点火情况,点火燃烧器设有观察孔。
锅炉能满足程控点火要求,并有火检装置,其中火检探头的冷却采用仪用压缩空气吹扫。
点火用油量及风量:
点火油枪油压:
2.5MPa
每只油枪喷油量:
Q=900Kg/h
点火总风量55000m3/h
其中混合风17150m3/h
点火启动时,风室内温度监视采用直读式数字温度计,冷态启动时间一般6~8小时。
锅炉冷态启动顺序如下:
首先在流化床内加装启动惰性床料(通常为底渣),粒径0~5mm,并且使床料保持在微流化状态,启动高能点火器,把油点燃,850℃左右的热烟气通过水冷布风板进入流化床,加热床料。
床料在流化状态下升至550℃以上,维持稳定后开始投煤。
可先断续少量给煤,当床料温度持续上升后,加大给煤量并连续给煤直到锅炉启动完毕。
1.10.7返料回灰系统
旋风分离器下接有返料器,均由钢外壳与耐火材料衬里组成,耐火材料分内、外二层结构,里层为高强度耐磨浇注料,外层为保温浇注料。
返料器内的松动风与返料风采用高压冷风,由小风帽送入,松动风与返料风的风帽数量和风帽开孔数量有差别(每台返料器的小风帽总计140个,其中松动风74个,每只风帽开3个小孔;返料风66个,每只风帽开6个小孔),返料风大,松动风小,并采用分风室送风。
小风帽的材质为1Cr18Ni9Ti。
运行时总风量581Nm3/h,其中返料风量372Nm3/h,松动风量209Nm3/h。
启动时设计风量1221Nm3/h,其中返料风量784Nm3/h,松动风量437Nm3/h。
返料器上设置一个启动床料加入口,尺寸φ219×5,必要时(如改进锅炉效率)也可以作为飞灰再循环管路中飞灰的加入口,返料器的布风板还设有一根φ108×6放灰管。
1.11过热器系统及其调温装置
本锅炉采用辐射和对流相结合,并配以二级喷水减温器的过热器系统。
饱和蒸汽从汽包由4根φ159×12的管子引至分离器前导流加速段包墙的入口集箱,经过管径φ51的包墙管至出口集箱,再由导汽管引入旋风分离器下环行集箱,蒸汽经膜式壁上行到上环行集箱后,引至尾部两侧包墙的上集箱,随后