粉末冶金复习资料.docx
《粉末冶金复习资料.docx》由会员分享,可在线阅读,更多相关《粉末冶金复习资料.docx(15页珍藏版)》请在冰豆网上搜索。
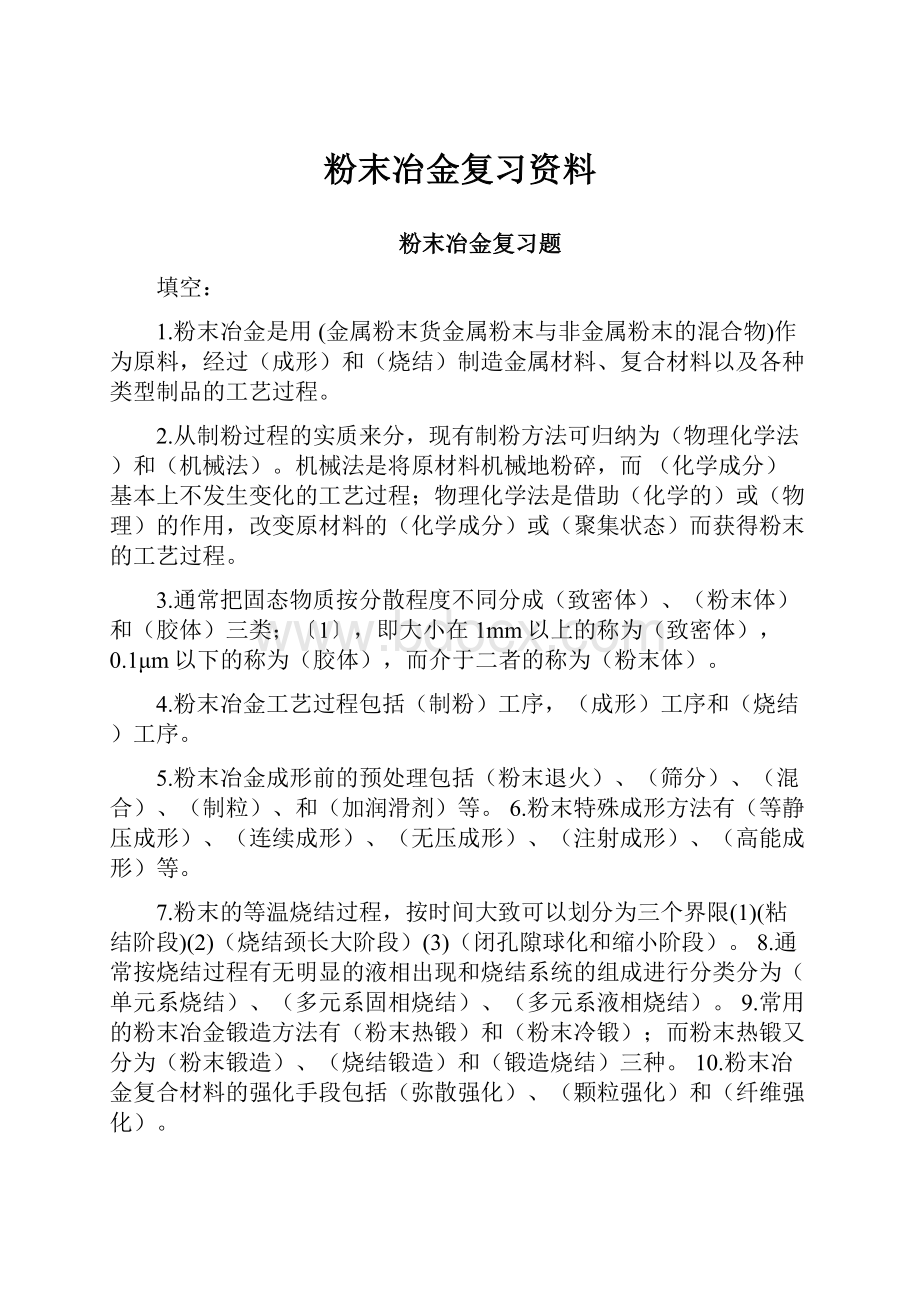
粉末冶金复习资料
粉末冶金复习题
填空:
1.粉末冶金是用 (金属粉末货金属粉末与非金属粉末的混合物)作为原料,经过(成形)和(烧结)制造金属材料、复合材料以及各种类型制品的工艺过程。
2.从制粉过程的实质来分,现有制粉方法可归纳为(物理化学法)和(机械法)。
机械法是将原材料机械地粉碎,而 (化学成分)基本上不发生变化的工艺过程;物理化学法是借助(化学的)或(物理)的作用,改变原材料的(化学成分)或(聚集状态)而获得粉末的工艺过程。
3.通常把固态物质按分散程度不同分成(致密体)、(粉末体)和(胶体)三类;〔1〕,即大小在1mm以上的称为(致密体),0.1μm以下的称为(胶体),而介于二者的称为(粉末体)。
4.粉末冶金工艺过程包括(制粉)工序,(成形)工序和(烧结)工序。
5.粉末冶金成形前的预处理包括(粉末退火)、(筛分)、(混合)、(制粒)、和(加润滑剂)等。
6.粉末特殊成形方法有(等静压成形)、(连续成形)、(无压成形)、(注射成形)、(高能成形)等。
7.粉末的等温烧结过程,按时间大致可以划分为三个界限
(1)(粘结阶段)
(2)(烧结颈长大阶段)(3)(闭孔隙球化和缩小阶段)。
8.通常按烧结过程有无明显的液相出现和烧结系统的组成进行分类分为(单元系烧结)、(多元系固相烧结)、(多元系液相烧结)。
9.常用的粉末冶金锻造方法有(粉末热锻)和(粉末冷锻);而粉末热锻又分为(粉末锻造)、(烧结锻造)和(锻造烧结)三种。
10.粉末冶金复合材料的强化手段包括(弥散强化)、(颗粒强化)和(纤维强化)。
11.粉末是颗粒与颗粒间的空隙所组成的分散体系,因此研究粉末体时,应分别研究属于(单颗粒)、(粉末体)及(粉末体的孔隙)等的性质。
12.粉末在压制过程中,粉末的变形包括(弹性变形)、(塑性变形)和(脆性变形)。
13.通常等静压按其特性分成(冷等静压)和(热等静压)。
14. 烧结过程有自动发生的趋势。
从热力学的观点看,粉末烧结是(系统自由能减小)的过程,即烧结体相对于粉末体在一定条件下处于(能量较低)状态。
15.典型的烧结机构包括(粘性流动)、(蒸发与凝聚)、(体积扩散)、(表面扩散)、(晶界扩散)、( 塑性流动)和(综合作用烧结理论)等。
16. 多孔预成形坏的变形特性是研究粉末冶金锻造过程塑性理论的基础。
锻造时,与致密金属坯的塑性变形相比,多孔预成形坯具有以下(质量不变条件)、(低屈服强度和低拉伸塑性)、(小的横向流动)、(变形和致密的不均匀性)变形特性。
17. 一般粉末治金材料是金属和孔隙的复合体,其孔隙度范围很广,有低于l~2%残留孔隙度的(致密材料),有10%左右孔限度的(半致密材料),有>15%孔隙度的(多空材料),也有高达98%孔隙度的(泡沫材料)。
简答题:
一、还原法制取铁粉的过程机理是什么?
影响铁粉还原过程的因素有哪些?
发展复合型铁粉的意义有哪些?
答:
铁氧化物的还原过程是分段进行的,即从高价氧化铁到低价氧化铁,最后转变成金属:
Fe2O3→Fe3O4→Fe。
固体碳还原金属氧化物的过程通常称为直接还原。
当温度高于570°时,分三阶段还原:
Fe2O3→Fe3O4→浮斯体(FeO·Fe3O4固溶体)→Fe
3Fe2O3+CO=2Fe3O4+CO2 Fe3O4+CO=3FeO+CO2 FeO+CO=Fe+CO2 当温度低于570°时,由于氧化亚铁不能稳定存在,因此,Fe3O4直接还原成金属铁 Fe3O4+4CO=3Fe+4CO2
影响因素:
(1)原料①原料中杂质的影响②原料粒度的影响
(2)固体碳还原剂①固体碳还原剂类型的影响②固体还原剂用量的影响
(3)还原工艺条件①还原温度和还原事件的影响②料层厚度的影响③还原罐密封程度的影响
(4)添加剂①加入一定的固体碳的影响②返回料的影响③引入气体还原剂的影响④碱金属盐的影响⑤海绵铁的处理 高密度、高强度、高精度粉末冶金铁基零件需要复合型铁粉。
二、电解法可生产哪些金属粉末?
为什么?
影响电解铜粉粒度的因素有哪些?
1、1)水溶液电解法:
可生产铜、镍、铁、银、锡、铅,铬、锰等金属粉末,在一定条件下可使几种元素同时沉积而制得Fe-Ni、Fe-Cu等合金粉末。
2)熔盐电解法:
可以制取Ti、Zr、Ta、Nb、Th、U、Be等纯金属粉末,也可以制取如Ta-Nb等合金粉末以及各种难熔化合物(如碳化物、硼化物和硅化物等)
2、
(1)电解液的组成
1)金属离子浓度的影响。
2)酸度(或H+浓度)的影响;
3)添加剂的影响
(2)电解条件
1)电流密度的影响;
2)电解液温度的影响;
3)电解时搅拌的影响;
4)刷粉周期的影响;
5)关于放置不溶性阳极和采用水内冷阴极问题
三、粉末颗粒有哪几种聚集形式?
它们之间的区别在哪里?
1、一次颗粒,二次颗粒(聚合体或聚集颗粒),团粒,絮凝体
2,通过聚集方式得到的二次颗粒被称为聚合体或聚集颗粒;团粒是由单颗粒或二次颗粒靠范德华引力粘结而成的,其结合强度不大,用磨研、擦碎等方法或在液体介质中就容易被分散成更小的团粒或单颗粒;絮凝体是在粉末悬浮液中,由单颗粒或二次颗粒结合成的更松软的聚集颗粒
四、压制前粉末需要进行哪些预处理?
其作用如何?
预处理包括:
粉末退火、筛分、混合、制粒、加润滑剂
预先退火:
使氧化物还原,降低碳和其他杂质的含量,提高粉末的纯度;消除粉末的加工硬化,稳定粉末的晶体结构 混合:
将两种或两种以上不同成分的粉末混合均匀 筛分:
把颗粒大小不同的原始粉末进行分级
制粒:
将小颗粒的粉末制成大颗粒或团粒,改善粉末的流动性。
在硬质合金生产中,为了便于自动成形,制粒使粉末能顺利充填模腔
加润滑剂:
降低成形时粉末颗粒和模冲间摩擦,改善压坯的密度分布,有利于脱模
五、影响压制过程的因素有那些?
1、粉末性能对压制过程的影响
1)粉末物理性能的影响
(1)金属粉末本身的硬度和可塑性;
(2)金属粉末的摩擦性能
2)粉末纯度(化学成分)的影响
3)粉末粒度及粒度组成的影响
4)粉末形状的影响
5)粉末松装密度的影响
2、润滑剂和成形剂对压制过程的影响
1)润滑剂和成形剂的种类 2)润滑剂和成形剂的用量 3)振动压制的影响 4)磁场压制的影响
六、粉末冶金技术中的特殊成型包括哪些?
与一般压制法相比有什么特点?
1、等静压成型,粉末连续成型,粉浆浇注成型,粉末注射成形,爆炸成形
2、
(1)等静压成型:
1)能够压制具有凹形、空心等复杂形状的杆件;
2)压制时,粉末体与弹性模具的相对移动很小,所以摩擦损耗也很小。
单位压制压力较钢模制法低;
3)能够压制各种金属粉末及非金属粉末。
压制坯件密度均匀,对难熔金属粉末及其化合物尤其有效;
4)压坯强度较高,便于加工和运输;
5)模具材料是橡胶和塑料,成本较低廉;
6)能在较低的温度下制得接近完全致密的材料
(2)粉末连续成型:
1)能够生产一般轧制法难于或无法生产的板带材;
2)能够轧制出成分比较精确的带材;
3)粉末轧制的板带材料具有各向同性;
4)工艺过程短、解约能源;
5)粉末轧制法成材率比熔铸轧制法高;
6)不需大型设备,减少大量投资
(3)、粉浆浇注成型:
制取某些新型特殊材料;生产羰基铁粉制品,适当烧结处理后,材料机械性能接近锻造材料;生产设备简单,生产费用低
(4)、粉末注射成形:
制造形状复杂的坯块
(5)、爆炸成形:
能够压出相对密度极高的压坯
八、热等静压技术适宜加工什么样的材料?
同热压法比较,它的特点是什么?
热等静压法制取的制品密度比热压法要高些,尤其在压制难熔金属时,差别更为明显。
同一材料的热等静压制温度比热压法低。
考虑到低的压制温度有利于获得细晶粒的合金材料,有利于制取一般方法难于制取的熔点相差悬殊的层叠复合材料,所以,热等静压材料性能普遍高于热压法制取的材料性能。
十、粉末等温烧结的三阶段是怎样划分的?
实际烧结过程包括哪些现象?
答:
粉末的等温烧结过程,按时间大致可划分为三个界限不十分明显的阶段:
(1)粘结阶段-烧结初期,颗粒间的原始接触点或面转变成晶体结合,即通过成核、结晶长大等原子过程形成烧结颈。
(2)烧结颈长大阶段-原子向颗粒结合面的大量迁移使烧结颈扩大,颗粒间距离缩小,形成连续的孔隙网络。
(3)闭孔隙球化和缩小阶段-当烧结体密度达到90%以后,多数孔隙被完全分隔,闭孔隙数量大为增加,孔隙形状趋近球形并不断缩小。
实际烧结过程可能出现的现象例如粉末表面气体或水分的挥发、氧化物的还原和离解、颗粒内应力的消除、金属的回复和再结晶以及聚晶长大等。
十一、分析影响互溶多元系固相烧结的因素。
答:
影响因素:
(1)烧结温度。
(2)烧结时间 在相同温度下,烧结时间越长,扩散越充分。
(3)粉末粒度 合金化的速度随着粒度减小而增加。
(4)压坯密度 增大制压力,将使粉末颗粒间接触面积增大,扩散界面增大,加快合金化过程。
(5)粉末原料 采用一定数量的预合金粉或复合粉同完全使用混合粉比较,达到相同的均匀化程度所需的时间将缩短,因为这时扩散路程缩短,并可减少要迁移的原子数量。
(6)杂质 有些杂质会存在于粉末表面或在烧结过程的杂质阻碍颗粒间的扩散进行。
十七、说明烧结的概念及烧结过程。
答:
烧结是粉末或粉末压坯,在适当的温度和气氛条件下加热所发生的现象或过程。
烧结的结果是颗粒之间发生粘结,烧结体的强度增加,而且多数情况下,密度也提高。
烧结过程:
粉末烧结后,烧结体的强度增加,首先是颗粒间的联结强度增大,即联结面上原子间的引力增大。
在粉末或粉末压坯内,颗粒间接触面上能达到的原子引力作用范围的原子数目有限。
但是在高温下,由于原子振动的振幅加大,发生扩散,接触面上才有更多的原子进入原子作用力的范围,形成粘结面,并且随着粘结面的扩大,烧结体的强度也增加。
烧结面扩大进而形成烧结颈,使原来的颗粒界面形成晶粒界面,而且随着烧结的继续进行,晶界可以向颗粒内部移动,导致晶粒长大。
名词解释
松装密度:
粉末试样自然的充满规定容器时,单位容积的粉末质量。
松装密度可以用漏斗法、斯科特容量计法来测量。
氢损:
把金属粉末的试样在纯氢气气流中煅烧足够长的时间, 粉末中的氧被还原生成水蒸气,某些元素与氢气生成挥发性化合物,与挥发性元素一同排出,测得试样粉末的质量损失称为氢损。
熔浸:
将粉末压坏与液体金属接触或埋在液体金属内,让压坏的空隙被金属液体填充,冷却下来就得到致密材料或零件,这种工艺称为熔浸。
熔浸必须具备的基本条件:
(1)骨架材料与熔浸材料的熔点相差较大,不致造成零件变形。
(2) 熔浸金属应能很好溶湿骨架材料,即润湿角小于90度。
(3)骨架与熔浸金属之间不发生互溶或溶解度不大,以避免在熔浸过程中产生新相而致使液相消失。
(4) 熔浸金属的量应以填满压坏中的空隙为限度,过多或过少均为不利。
活化烧结:
采用化学或物理的措施,使烧结温度降低,烧结过程加快,或使烧结体密度和其他性能得到提高的方法称为活化烧结。
活化烧结从方法上可以分为两种类型:
(1) 依靠外界因素活化烧结过程。
如加活性剂等。
(2)提高粉末活性。
活化烧结与预氧化烧结,添加少量合金元素,在气氛或填料中添加活化剂。
电火花烧结:
利用粉末间火花放电所产生的高温,并且同时受外应力作用的一种特殊烧结法。
压缩性:
是金属粉末在规定的压制条件下被压紧的能力。
成形性:
指粉末压制后,压坏保持既定形状的能力。
强化机理:
使金属基体中含有高度分散的第二相质点而达到提高
致密化过程:
1快速致密化阶段——即在热压初期发生相对滑动,破碎和塑形变形,类似成形时的颗粒重排
2致密化减速阶段——以塑形流动为主要机构,类似于烧结后期的闭孔收缩阶段 3趋近终极密度阶段——受扩散控制的蠕变为主要机构,此时的晶粒长大使致密化速度大大降低,达到终极密度后,致密化过程完全停止
制取铁粉的主要还原方法有那些?
比较其优缺点
碳还原:
可以还原很多金属氧化物,但容易被碳污染
气体还原:
可以制取合金粉,制取的铁粉比碳还原制取的纯,生产成本低 金属热还原:
可以制取生产无碳金属,用于稀有金属
模压成型工艺的特点是什么?
(1)模压成型工艺的优点。
模压成型工艺有以下几方面优点 ①与挤出和注射等成型工艺相比,模压成型工艺所需设备结构简单、制造精度不髙、制造费用低,所以投资少、见效快,为发展多品种、小批量的生产提供了有利条件,这也是模压成型工艺目前还在大量运用的原因之一。
②在模压成型过程中,由于塑料的流动距离很短,受填料的定向影响小,所以塑件的尺寸变动小,不易变形,尺寸稳定性好,机械性能稳定。
③相同吨位的压机可以成型较大平面的制品。
④模压成型工艺成熟,生产过程易于控制。
⑤模压成型中没有浇注系统,原材料浪费相对较少。
对于不能重复利用的热固性材料来讲,节约原料尤为重要。
⑥模压成型基本上适合于加工各种塑料。
尤其像氨基树脂、环氧树脂和聚酰亚胺等材料,用注射成型既困难又会影响制品外观质量;对于用石棉或玻璃纤维等增强的塑料,在注射和挤出成型中,纤维易在浇口部分断裂,使制品的机械强度特别是冲击强度降低,失去增强的意义;聚酯团状和片状模塑料若采用注射成型,则需特殊的强迫加料装置,导致设备费用昂贵。
模压成型是制造高强度塑件最有效的方法。
(2)模压成型工艺的缺点。
模压成型的缺点表现在以下三方面。
①生产周期长,生产效率低。
②较难实现生产自动化,因而劳动强度大。
③因为飞边厚,塑件厚度方向的尺寸难以控制,所以模压成型不能模压尺寸精度要求较的制品。
1. 什么是弹性后效其主要影响因素有哪些
答 当压力去除之后和将压坯脱拱之后由于内应力作用压坯产生的膨胀现象称为弹性后效。
弹性后效的大小取决于残留应力的高低 主要影响因素
a.压制压力压制压力高弹性内应力高
b.粉末颗粒的弹性模量弹性模量越高弹性后效越大
c.粉末粒度组成越合理产生的弹性应力越小粒度小弹性后效大
d.颗粒形状形状复杂弹性应力大弹性后效大
f.粉末混合物的成份
烧结气氛的两个作用是什么
答 1保护功能控制烧结体与环境之间的化学反应如氧化和脱碳 2净化功能及时带走烧结坯体中润滑剂和成形剂的分解产物
致密化:
压力作用下松散状态→拱桥效应的破坏(位移→颗粒重排)+颗粒塑性变形→孔隙体积收缩→致密化
等静压成型
定义:
粉末装于弹性(柔性)模具(包套)中,以流体为传压介质,各向均匀受压。
分类:
冷等静压(CIP):
常温下进行的等静压 常温下,粉末装于弹性模具中,以液体为传压介质,粉末体各向均匀受压而密实成压坯 热等静压(HIP):
高温下进行的等静压 高温下,粉末或压坯装于包套中,在高压容器内,以气体为传压介质,使粉末同时承受高温和等静压力作用而获得致密材料或制品.
等静压的一般特点:
压坯形状、尺寸范围大,尤大尺寸、形状复杂压坯或制品;
压坯密度高且均匀 形粉末广,尤难熔金属化合物、陶瓷、高合金钢等 工艺简单,可不加润滑剂 设备:
冷等静压机分类:
螺纹式、拉杆式、框架式
热等静压机分类:
螺纹式、框架式
HIP特点:
① 压制、烧结同时进行,能消除粉末坯体中的所有孔隙,相对密度可达0.9999 ② 压力作用,使HIP的烧结温度低于通常的烧结温度 ③ HIP所需压制压力比CIP低
④ 晶粒细小、组织均匀,无成分偏析 ⑤ 材料综合性能好,是PM高新技术之一 ⑥ 设备投资大,成本
粉末冶金定义
制取金属及化合物粉末,采用成形和烧结工艺制
成金属材料、复合材料、陶瓷材料及其它们的制品
的技术科学。
粉末压制成形-致密化现象
Ø致密化:
压力作用下松散状态→拱桥效应的
破坏(位移→颗粒重排)+颗粒塑性变形→
孔隙体积收缩→致密化;
Ø拱桥效应:
颗粒间由于摩擦力的作用而相互
搭架形成拱桥孔洞的现象;
Ø影响因素:
与粉末松装密度、流动性存在一
定联系。
脱模压力
脱模压力指把坯块从模具内取出所需的压力。
什么是弹性后效?
它对压坯有何影响?
加载(或卸载)后经过一段时间应变才增加(或减小)到一定数值的现象。
压制过程中,当卸掉压制力并把坯块从模具内取出后,由于弹性内应力的作用,坯块发生弹性膨胀,这种现象称为弹性后效
弹性后效:
在去除P压后,压坯所产生的胀大现象。
弹性后效危害:
压坯及压模的弹性应变是产生压坯裂纹的主要原因之一,由于压坯内部弹性后效不均匀,脱模时在薄弱部位或应力集中部位就会出现裂纹。
影响压坯密度分布的因素(P182)
实验证明,增加压坯的高度会使压坯各部分的密度差增大,而
加大直径则会使密度的分布更加均匀。
压坯中密度分布的不均匀
性,在很大程度上可以用双向压制来改善。
在双向压制时,与上
、下模冲接触的两端密度较高
粒度:
颗粒在空间范围所占大小的线性尺度.
粒度组成(粒度分布):
不同粒径的颗粒占全部粉末的百分含量.
平均粒度:
粉末颗粒粒径的统计平均值.
什么是松装密度和振实密度?
松装密度的控制有何重要意义?
松装密度:
自然充填容器时,单位体积的质量
振实密度:
粉末在振动容器中, 在规定条件下经过振动后测得的粉末密度
意义:
压制过程中, 采用容量装粉法, 即用充满形腔的粉末体积来控制压坯的密度和单重. 用松装密度和振实密度来描述粉体的这种容积性质.
如何提高粉末的ρ松和流动性?
松装密度高的粉末流动性也好,方法:
粒度粗、形状规则、粒度组成用粗+细适当比例、表面状态光滑、无孔或少孔隙
压坯中密度分布不均匀的状况及其产生的原因是什么?
如何改善密度分布?
密度分布不均匀的状况:
一般,高度方向和横断面上都不均匀. ① 平均密度从高而低降低.
② 靠近上模冲的边缘部分压坯密度最大; 靠近模底的边缘部分压坯密度最小. ③ 当H/D(高径比)较大时,则上端中心的密度反而可能小于下端中心的密度. 产生的原因:
压力损失 改善压坯密度不均匀的措施:
① 在不影响压坯性能前提下, 充分润滑; ② 采用双向压制;
③ 采用带摩擦芯杆的压模; ④ 采用浮动模;
⑤ 对于复杂形状采用组合模冲, 并且使各个模冲的压缩比相等; ⑥ 改善粉末压制性(压缩性、成形性)— 还原退火; ⑦ 改进模具构造或适当变更压坯形状 .
⑧ 提高模具型腔表面硬度和光洁度. HRC58~63,粗糙度9级以上.
什么是等静压成形?
它有什么优缺点?
其基本原理是什么?
等静压成形是指,借助于高压流体的静压力作用,使弹性模套内的粉末在同一时间内各个方向上均衡地受压而获得密度分布均匀和强度较高的压坯的成形方法。
优点:
① 能成形凹形、空心等复杂形状.
② 粉末与弹性模具间相对移动很小、摩擦损耗小,压制压强较钢模低. ③ 能压制各种金属粉末及非金属粉末; 压坯密度分布均匀. ④ 压坯强度较高.
⑤ CIP模具材料是橡胶、塑料, 成本低廉.
⑥ 能在较低温度下制得接近完全致密的材料. —HIP 缺点:
① 压坯尺寸精度和表面光洁度都比钢模压制低; ② 生产效率低于自动钢模压制;
③ CIP中使用的橡胶或塑料包套寿命比金属压模要短得多;
④ HIP中使用的包套都为一次性、消耗大,且包套材料种类受到限制. 基本原理(帕斯卡原理)
流体在密闭容器内任何一点所受的压应力,将无保留地传递到流体(或容器)的各处.
1流体内任意处的静压应力相等,称为准静力等静压,否则为非准静力等静压. ②流体通过液-固(气-固)界面对固体施加压力.
2③HIP在加压同时还要加热,使成形和烧结过程同时完成
简述热等静压的过程和特点。
过程:
将装于包套内的粉体置于充满气体介质的高温压力容器内,使粉体在压缩的同时经历高温烧结, 成为致密制品.
特点:
粉末体(粉末压坯或包套内的粉末)在等静压高压容器内同一时间经受高温和高压的联合作用,强化了压制与烧结过程,降低了制品的烧结温度,改善了制品的晶粒结构,消除了材料内部颗粒间的缺陷和孔隙,提高了材料的致密度和强度。
烧结
1.什么是烧结?
如何分类?
一定气氛下, 粉末或压坯, 在低于主要组分熔点温度下的加热处理过程. 分类:
1)按有无液相分和烧结系统的组成分:
单元系烧结、多元系固相烧结和多元系液相烧结。
烧结推动力
粉体颗粒尺寸很小,比表面积大,具有较高的表面能,即使在加压成型体中,颗粒间接触面积也很小,总表面很大而处于较高能量状态。
根据能量最低原理,它将自发地向最低能量状态变化,并伴随使系统的表面能减少。
可见,烧结是一个自发的不可逆过程,系统表面能降低是推动烧结进行的基本动力。
粉状物料的表面能大于多晶烧结体的晶界能,这是烧结过程的推动力,粉体经烧结后,晶界能取代了表面能,这是烧结后多晶材料稳定存在的原因。
什么是液相烧结?
有哪些液相烧结技术?
各有什么应用?
烧结温度下,低熔点组元熔化或形成低熔共晶、产生可流动液相的烧结. 在近现代, 液相烧结的应用领域迅速扩大, 涉及电触头、工具钢、超合金、硬质合金、高密度合金、金刚石-金属复合材料、绝缘材料、难熔材料、磁性材料、汽车结构零件和高强度陶瓷等.
液相烧结的优点和缺点各有哪些?
优点:
① 由液相引起的物质迁移要比固相扩散快;② 液相产生的毛细力促使液相流动和颗粒发生适位的位移(重排),提高烧结速度;③ 最终,液相将填满烧结体内的孔隙,可以获得密度高、性能好的产品.
局限性:
① 尺寸控制较固相烧结难.因为液相烧结的材料尺寸变化大,有的线收缩可>20%; 有些材料烧结过程会发生膨胀.② 可能出现变形、开裂和坍塌. 液相烧结过程中压坯强度较低,同时,压坯的密度不均匀,在液相烧结过程中会造成收缩不均匀,可能引起较大的变形、甚至造成开裂.当液相量过多时,则可能出现坍塌.通常,大的压坯容易发生开裂, 压坯的悬臂部分容易发生坍塌.一般要求严格控制加热速度(保证刚度和均匀收缩).
液相烧结的三个基本条件是什么?
良好的润湿性;固相在液相中有一定溶解度;适当的液相数量.
液相烧结可以分为哪三个阶段?
各阶段基本特点是什么?
(1)液相流动与颗粒重排阶段:
颗粒在液相内近似呈悬浮状态,受液相表面张力推动,颗粒可发生位移、相对滑动.烧结体密度迅速增大.
(2) 固相溶解-再析出阶段:
该过程一般特征是显微组织粗化,固相在液相中的溶解度随温度和颗粒形状、大小而变化.
小颗粒、颗粒表面凸起、棱角因具有较高饱和溶解度,将优先溶解,使小颗粒趋向减小、颗粒表面趋向平整光滑;同时,液相中一部分过饱和原子在大颗粒表面沉析,使大颗粒趋于长大.结果:
颗粒外形逐渐趋于球形、小颗粒逐渐缩小或消失,大颗粒更加长大, 从而使颗粒更加靠拢,烧结体发生收缩.这阶段致密化速度已显著减慢、气孔已基本消除. 颗粒间距更加缩小,液相流进孔隙更加困难. 3)固相烧结阶段
经前两阶段,颗粒间互相靠拢、接触、粘结并形成连续骨架,剩余液相充填于骨架间隙.刚性骨架阻碍颗粒更进一步重新排列,使该阶段致密化速率明显减慢.液相不完全润湿固相或液相数量较少时,该阶段将表现得更为突出.固相骨架形成后的烧结过程与固相烧结相似.扩散作用会导致固体颗粒间接触长大,故,大多数液相烧结材料性能将随该阶段时间延长而降低
(此文档部分内容来源于网络,如有侵权请告知删除,文档可自行编辑修改内容,供参考,感谢您的配合和支持)