有机化工工艺学.docx
《有机化工工艺学.docx》由会员分享,可在线阅读,更多相关《有机化工工艺学.docx(18页珍藏版)》请在冰豆网上搜索。
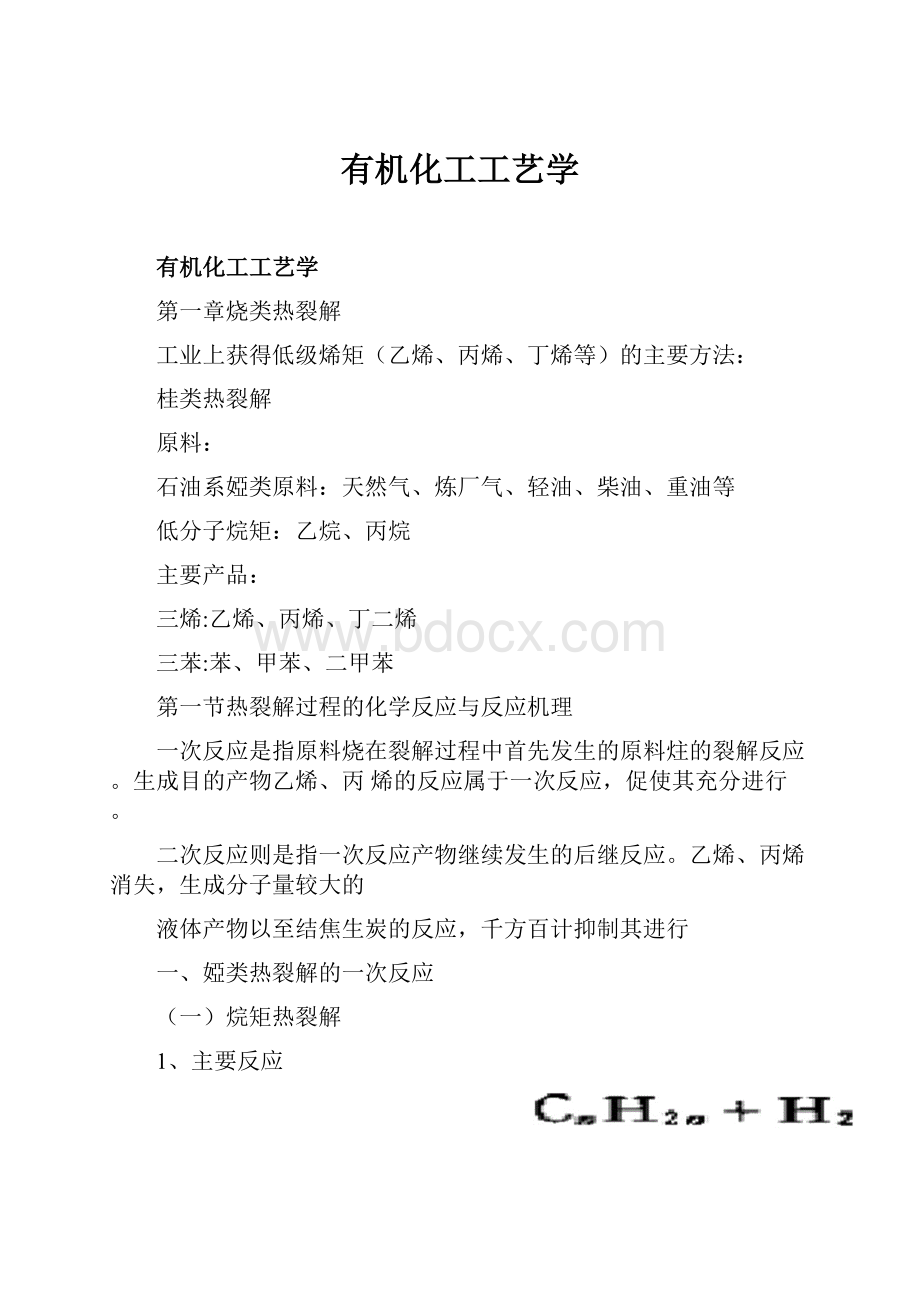
有机化工工艺学
有机化工工艺学
第一章烧类热裂解
工业上获得低级烯矩(乙烯、丙烯、丁烯等)的主要方法:
桂类热裂解
原料:
石油系婭类原料:
天然气、炼厂气、轻油、柴油、重油等
低分子烷矩:
乙烷、丙烷
主要产品:
三烯:
乙烯、丙烯、丁二烯
三苯:
苯、甲苯、二甲苯
第一节热裂解过程的化学反应与反应机理
一次反应是指原料烧在裂解过程中首先发生的原料炷的裂解反应。
生成目的产物乙烯、丙烯的反应属于一次反应,促使其充分进行。
二次反应则是指一次反应产物继续发生的后继反应。
乙烯、丙烯消失,生成分子量较大的
液体产物以至结焦生炭的反应,千方百计抑制其进行
一、婭类热裂解的一次反应
(一)烷矩热裂解
1、主要反应
1)脱氢反应
2)断链反应
2、脱氢和断链难易的判断
1•相同烷婭断链比脱氢容易
2.碳链越长越易裂解
3.叔氢〉仲氢〉伯氢
4.带支链的泾容易裂解或脱氢
3、烷烧热裂解的规律
1)斷链和脱氢均为热效应很大的吸热反应,脱氢比断链所需热量更多
2)断链是不可逆过程,脱氢是可逆过程
3)在分子两端断链的优势大
4)乙烷不发生断链反应,只发生脱氢反应生成乙烯,甲烷在一般裂解温度下不发生变化
主要产物:
氢、甲烷、乙烯、丙烯、C4烯婭
(二)环烷矩热裂解
1)斷链2)脱氢3)带侧链的环烷烧
2、反应规律
侧链烷基断裂比开环容易
脱氢生成芳炷优于开环生成烯婭
五环比六环烷矩难裂解
主要产物:
单环烷矩生成:
乙烯、丁二烯、单环芳婭
多环烷桂生成:
C4以上烯矩、单环芳烧
(三)芳香炷热裂解,一般不易芳环开裂
1)脱氢缩合
2)断侧链
3)脱氢
(四)烯矩热裂解
斷链、脱氢、芳构化等
主要产物:
乙烯、丙烯、丁二烯;环烯婭
特点:
烯炷在热裂解过程中生成小分子烯炷的裂解是不希望发生的,需要控制。
(五)各族婭类的热裂解反应规律
1)正构烷婭在各族矩中最利于乙烯、丙烯的生成。
2)环烷矩生成芳婭的反应优于生成单烯婭的反应。
3)无烷基的芳矩基本上不易裂解为烯婭,有烷基的芳矩,主要是烷基发生断碳键和脱氢反应,有结焦的倾向
4)大分子烯烧裂解为乙烯和丙烯
正构烷炷〉异构烷炷〉环烷炷(六碳环〉五碳环)>芳炷
二、婭类热裂解的二次反应
1、烯桧的裂解
2、烯疑的聚合、环化和缩合
3、烯婭的加氢和脱氢
4、婭分解生成碳
裂解过程的结焦生碳反应:
1200K以上经过烘桂中间阶段而生碳;
1200K以下经过芳婭中间阶段而结焦。
焦和碳的区别:
1.形成过程不同:
烯婭经过烘煙中间阶段而生碳;经过芳婭中间阶段而结焦
2.氢含量不同:
碳几乎不含氢,焦含有微量氢(0.1-0.3%)
三、泾类热裂解反应机理及动力学
链引发
断裂C—C键产生一对自由基
活化能高
链增长
自由基夺氢自由基分解,活化能不大
被夺走氢的容易顺序:
伯氢〉仲氢〉叔氢
自由基分解反应是生成烯矩的反应
链终止
两个自由基形成稳定分子的过程
活化能一般较低
(-)烷婭热裂解的自由基反应机理
自由基分解反应的规律
1)自由基分解为碳原子数较少的烯烧的反应活化能较小
2)自由基中带有未配对电子的碳原子,若所连的氢较少,就主要分解为氢自由基和同碳原子数的烯婭分子
3)链增长反应中生成的自由基碳原子数大于3,还可继续发生分解反应
4)自由基分解反应宜到生成氢自由基、甲基自由基为止
二)反应动力学
婭类裂解时的一次反应可按一级反应动力学处理
第二节炷类管式炉裂解生产乙烯
炷类热裂解的特点:
1)强吸热反应,反应温度一般高于750・C
2)存在二次反应,要求停留时间应很短,婭分压很低
3)产物为复杂混合物
一、原料矩组成对裂解结果的影响
(一)裂解原料性质及指标
烯烧0(olefin)
1、族组分(P(WA值)烷矩P(paraffin)
环烷婭N(naphthene)芳烧A(aromatics)
2、原料氢含量
原料中氢的质量百分含量
测定方法:
元素分析法
烷烧氢含量最高,环烷矩次之,芳矩则较低
氢含量越高,则乙烯产率越高
如Hf=ZgHg+Q—Zg)Hl
3、芳婭指数即美国矿务局关联指数(U・S.BureauofMinesCorrelationIndex),
简称BMCIo
用以表征柴油等重质馆分油中烧组分的结构特性
正构烷婭的BMCI值最小(正己烷为0.2),芳婭则相反(苯为99.8),因此炷原料的BMCI值越小,乙烯收率越高。
炬类化合物的芳香性愈强,则BMCI值愈大,不仅乙烯收率低,结焦的倾向性愈大。
1
4、特性因数表征石脑油和轻柴油等轻质油化学组成特性的一种因数,用K表示。
77土
匚=<£文小兀f
Z=1
K值以烷婭最高,环烷婭次之,芳炷最低。
原料短的K值越大则乙烯产率越高。
乙烯和丙烯
总体收率大体上随裂解原料K值的增大而增加。
(2)几种矩原料的裂解结果比较
1.原料由轻到重,相同原料量所得乙烯收率下降。
2.原料由轻到重,裂解产物中液体燃料又增加,产气量减少。
3.原料由轻到重,联产物量增大,而回收联产物以降低乙烯生产成本的措施,又造成装置
和投资的增加。
二、操作条件对裂解结果的影响
(-)衡量裂解结果的几个指标
1、转化率
转化率二参加反应的原料量/通入反应器的原料童(%)
2、产气率
产气率二气体产物总质量/原料质量(%)
3、选择性
选择性二转化为目的产物的原料量/反应掉的原料量(mol%)
4、收率和质量收率
收率二转化为目的产物的原料量/通入反应器的原料量(mol%)(wt%)
(二)裂解温度的影响
1.裂解温度影响一次反应的产物分布
2.裂解温度影响一次反应对二次反应的竞争
1、温度对一次反应产物分布的影响
按自由基链式反应机理分析,温度对一次产物分布的影响,是通过影响各种链式反应相对
量实现的。
在一定温度范围内,提高裂解温度有利于提高一次反应所得乙烯和丙烯的收率。
2、温度对一次反应和二次反应相互竞争的影响
烯矩脱氢、分解生碳和烯烧脱氢缩合结焦等
1)热力学分析
提高裂解温度有利于生成乙烯的反应,但更有利于乙烯脱氢生产乙烘,过高温度更有利于
碳的生产
2)动力学分析
温度升高,有利于提高kl/k2的比值,有利于提高一次反应对二次反应的相对速度,提高乙烯收率。
脱氢缩合也有同样规律。
但温度高时,一次和二次反应的绝对速度均加快,焦和乙烘的生产量会增加,因此相应减少停留时间以减少二次反应的影响
三)停留时间的影响
物料从反应开始到达某一转化率时在反应器内经历的反应时间。
1、表观停留时间
_*_S•乙
I
BVV
s、l一反应器容积、裂角举管截m积及管长V一气态反应物的实际容积宛率,
彳以"td-舞日寸
3、停留时间的影响
由于有二次反应,对每种原料都有一个最大乙烯收率的适宜停留时间,短停留时间对生成烯矩有利。
4、温度一留时间效应
不同温度-停留时间组合,裂解结果不同。
高温临停留时间最佳组合
提高温度,缩短停留时间的效应:
1•可以获得较高的烯婭收率,并减少结焦
2.抑制芳婭生成,所得裂解汽油的收率相对较低
3.使烘矩收率明显增加,并使乙烯/丙烯比及C4中的双烯矩/单烯矩的比增大,工业上利用此效应,适应市场需要。
(四)矩分压和稀释剂的影响
1、压力对平衡转化率的影响
降低压力有利于提高乙烯平衡组成有利于抑制结焦过程
2、压力对反应速度和反应选择性的影响
压力不能改变反应速度常数,但降低压力能降低反应物浓度
降低压力可增大_次反应对于二次反应的相对速度,提高一次反应选择性
3、稀释剂
目的:
降低炷分压
稀释剂种类:
水蒸气、惰性气体
优点:
1.设备在常压或正压操作,安全性高,不会对以后压缩操作增加能耗
2.易分离3.热容童大,使系统有较大的热惯性4.抑制硫对银链合金炉管的腐蚀
5、脱除结碳,抑制铁镰的催化生碳作用
五、动力学裂解深度函数KSF
单一炷类或低级婭类的裂解深度可由该单_婭类或其中一个有代表性的组分来衡量。
较重质原料,由于组成复杂,某一种婭在裂解过程中消失,而另一种炷在裂解时又可能生
成它,因此无法用转化率来衡量裂解深度,而采用动力学裂解深度函数KSF,
KSF值与产物分布(石脑油)
KSF=0^1浅度裂解区
原料饱和矩含量迅速下降,低级烯矩含量接近直线上升。
KSF=P2.3中度裂解区
乙烯含量继续上升
1.7处丙烯、丁烯含量出现峰值
KSF>2.3深度裂解区
一次反应已停止
乙烯峰值在3.5~6.5
三、管式裂解炉的工艺流程
(_)管式裂解炉
热裂解反应的特点:
强吸热反应高温
存在二次反应短停留时间低婭分压
反应产物是复杂的混合物
间接供热管式炉裂解
直接供热固体载热体法、气体载热体法、氧化裂解法
(二)裂解气急冷与急冷换热器
1、裂解气的急冷
终止裂解反应(主要是二次反应)回收废热
急冷方法:
直接急冷冷却介质(水、油)与裂解气直接接触,分离困难
间接急冷用急冷换热器回收大量的热量,冷却介质用高压水,产生高压水蒸汽
急冷方式比较
直接急冷
1.设备费少操作简单2.传热效果好3.产生大量含油污水,难分离4.不能回收高品位的热能
间接急冷
1.回收高品位的热能2.能量利用合理3.无污水4.不如直接方式中冷热物流接触空间大5.结焦比较严重6.压力损失大
控制急冷换热器结焦的指标:
1)停留时间<0.04s
2)裂解气出口温度>裂解气的露点
2、急冷换热器
工艺要求:
传热强度大827*0降到350〜600*C
能够承受很大的压差和温差
便于清焦
使裂解气在0.01"0.Is内骤冷至露点左右
(三)裂解炉的结焦与清焦
1、结焦原因:
二次反应
2、结焦的判断
1)在投料量不变的情况下,进口压力增大,压差增大
2)裂解管管壁出现光亮点
3)投料量及管出口温度不变,燃料消耗量增加
4)裂解气中乙烯的含量下降
3、清焦方法
1)停炉清焦:
切断进料及出口,用惰性气体或水蒸气清扫管线,再用空气和水蒸气烧焦
2)不停炉清焦:
重质轻质原料交替裂解法和水蒸气、氢气清焦法。
切换物料
3)其它方法:
加入助剂,起到抑制作用
(四)裂解工艺流程
原料油供给和预热系统
裂解和高压水蒸气系统
急冷油和燃料油系统
急冷水和稀释水蒸气系统
不包括压缩、深冷分离系统
(五〉管式裂解炉的优缺点
优点:
结构简单,易操作,连续生产,乙烯、丙烯收率较高,动力消耗小,热效率高等
缺点:
对重质原料的适应性还有一定限制;制造裂解管的材质要求高
四、裂解技术展望
第三节裂解气的净化与分离
一、概述
(-)裂解气的组成和分离要求
(二)裂解气分离方法简介
深冷分离法:
利用裂解气中各种矩的相对挥发度不同,低温下把除氢和甲烷以外的矩冷凝下来,再精馆分离
油吸收精馆分离法:
利用溶剂油对各组分的不同吸收能力,把除氢和甲烷以外的烧吸收下
来,在精馆分离
二、酸性气体的脱除
(一)酸性气体的来源C02,H2S和其他气态硫化物
1.气体裂解原料带入的气体硫化物和C02
2.液体裂解原料中所含的硫化物高温氢解生成的C02和H2S
3.结炭与水蒸气反应生成CO和C02
4.水蒸气与炷类反应生成C02
(二)酸性气体的危害
1.H2S:
腐蚀设备管道,使催化剂中毒
2.C02:
深冷时结成干冰,堵塞设备和管道
3.对下游产业也有危害
(三)脱除酸性气体的方法
多用化学吸收方法
UOnNZnCHZnaUOa+ZMLmO
-NZnOM:
ZnnS+
COS-H十ZdHUO.fNZMnO
KSK:
亠ZdOEi^丘BZd于:
(一)水的危害
分离在-1009以下进行在压缩系统、段间冷凝;
设备及管道
脱水要求
400〜700ppm-*lppm以下
吸附干燥
吸附剂:
A型分子筛、活性氧化铝、硅胶
(二)分子筛脱水
特点:
脱水效率
吸附选择性
离子型极性吸附剂
吸附容童与温度关系
脱附
(三)分子筛脱水与再生流程
需脱水:
裂解气、C2憎分、C3馆分、甲烷化后的氢气
四、脱烘
乙烘丙烘丙二烯
危害:
1.烘矩影响乙烯和丙烯衍生物生产过程2.影响催化剂寿命3.形成不安全因素4.恶化产品质ft
5.产生不希望的副产品
脱烘要求:
乙烘V10ppm>丙二烯VlOppm
脱烘方法:
催化加氢法和溶剂吸收法
(一)催化加氢脱乙烘
将裂解气中乙烘加氢成为乙烯或乙烷,由此达到脱除乙烘的目的
1、主副反应
2、前加氢和后加氢
前加氢在脱甲烷塔前,利用裂解气中H2进行加氢,又叫自给加氢
特点:
流程简单,投资少.但氢气过量,加氢选择性降低,对催化剂要求高
后加氢先分离出C2、C3后,再分别加氢
特点:
温度易控,选择性高,产品纯度高。
但流程较复杂。
3、加氢脱烘催化剂
要求:
选择性良好,尽可能使反应停留在生成乙烯的阶段。
常用催化剂:
Pd/a-A1203、Ni-Co/a-A1203
乙烘的吸附能力强于乙烯
(二)溶剂吸收法脱乙烘
1.吸收裂解气中的乙烘2.同时回收一定量的乙烘
常用的溶剂:
1.二甲基甲酰胺(DMF)2.N-甲基毗咯烷酮(NMP)3.丙酮
五、裂解气的压缩
裂解气各组分沸点都很低,常压下分离,则分离温度低,需大量冷量。
为使分离温度不太低,适当提高分离压力
第四节裂解气深冷分离流程
分离流程按脱甲烷脱乙烷脱丙烷的顺序
顺序分离流程前脱乙烷流程前脱丙烷流程
脱甲烷脱乙烷脱丙烷脱乙烷脱甲烷脱丙烷脱丙烷脱甲烷脱乙烷一、顺序分离流程
分离流程采取先易后难的分离顺序,再进行C2和C3的分离冷箱:
脱甲烷塔系统中某些冷凝器.换热器和气液分离器的操作温度甚低,为防止散冷,将这些冷设备集装在一起成箱。
前冷流程:
冷箱在脱甲烷塔之前
后冷流程:
冷箱在脱甲烷塔之前
二、脱甲烷塔及操作条件
脱除裂解气中的氢气和甲烷
需在-90C以下进行
温度最低、投资最大、能耗最多、工艺复杂
消耗的冷量占分离部分总冷量的42%
轻关键组分为甲烷
重关键组分为乙烯
塔顶分离出的甲烷轻馆分中应使其中的乙烯含童尽可能低,以保证乙烯的回收率塔釜产品则应使甲烷含量尽可能低,以确保乙烯产品质量
低压脱甲烷(0.6-0.7MPa):
a提高,分离效果好,能耗低于高压法,需耐低温钢材、多一套甲烷制冷系统、流程较复杂,发展方向
高压脱甲烷(3.0~3.2MPa):
Im
甲烷对乙烯a降低,温度较高,制冷系统简单,分离效果不如低压法,技术成熟三、乙烯塔和丙烯塔
(一)乙烯塔
C2馆分经过加氢脱烘之后,到乙烯塔进行精馆
塔顶得产品乙烯,塔釜液为乙烷
塔顶乙烯纯度要求达到聚合级
此塔设计和操作的好坏,对乙烯产品的产量和质量有直接关系
冷量消耗占总制冷量38%〜44%
1、操作条件
操作压力由制冷的能量消耗,设备投资,产品乙烯要求的输出压力以及脱甲烷塔的操作压力等因素来决定的。
高压法低压法
2.乙烯塔的改进
精馆段各塔板温度变化较小,乙烯浓度增大较慢提馆段温度变化较大,乙烯浓度下降较快精馆段塔板数较多,回流比大中间再沸器回收冷量
侧线出产品(避免甲烷影响乙烯产品纯度)
四、影响乙烯回收率诸因素
(一)影响乙烯回收率的因素分析
冷箱尾气2.25%关键因素
乙烯塔塔釜液0.40%
脱乙烷塔釜液0.284%
压缩段间凝液0.066%
影响冷箱尾气乙烯损失的主要因素
1、原料气的组成
T、P—定时,甲烷/氢气摩尔比越小,尾气中乙烯损失就越大
2、压力和温度
甲烷/氢气摩尔比一定时,增大压力或降温都利于减少乙烯损失,但有一定限制
P增大,甲烷/乙烯相对挥发度降低,分离困难,增加设备投资或冷量
甲烷难从塔釜液中蒸出
T降低,但受冷剂温度水平限制
(二)利用冷箱提高乙烯回收率
利用节流膨胀来获得低温
前冷是将脱甲烷塔顶憎分的冷量将裂解气预冷,通过分凝将裂解气中大部分氢和部分甲烷分离,这样使H2/CH4比下降,提高了乙烯回收率,同时减少了甲烷塔的进料量,节约能耗。
后冷仅将脱甲烷塔顶的甲烷氢憎分冷凝分离而获富甲烷馆分和富氢馆分,氢浓度较高
第五节裂解分离系统的能量有效利用
二、中间冷凝器和中间再沸器
精馆段:
中间冷凝器较廉价冷剂
提馆段:
中间再沸器较廉价热剂
三、深冷过程冷量的有效利用
四、
(一)冷冻剂的选择
就地取材
制冷温度越低,单位能量消耗越大。
不同温度级位的制冷,采用尽可能温度级位接近的冷剂。
沸点/9
制冷温度级位/弋
乙烯
-103.7
-100
丙烯
-47.7
-40
甲烷
-16L5
-120^-160
(二)
复迭制冷
制冷剂压缩制冷时,当其临界温度较低时,需用另一冷剂使其降至临界温度以下。
三)多级制冷提供多温度级位的冷剂
四、热泵
常规的精馅塔都是从塔顶冷凝器取走热量,由塔釜再沸器供给热量,通常塔顶冷凝器取走的热量是塔釜再沸器加入热量的90%左右,能量利用很不合理。
如果能将塔顶冷凝器取走的热量传递给塔釜再沸器,就可以大幅度地降低能耗。
但同一塔的塔顶温度总是低于塔釜温度,根据热力学第二定律,"热量不能自动地从低温流向高温”,所以需从外界输入功。
这种通过做功将热童从低温热源传递给高温热源的供热系统称为热泵系统。
该热泵系统是既向塔顶供冷又向塔釜供热的制冷循环系统。