制造执行系统MES理论与应用研究.doc
《制造执行系统MES理论与应用研究.doc》由会员分享,可在线阅读,更多相关《制造执行系统MES理论与应用研究.doc(57页珍藏版)》请在冰豆网上搜索。
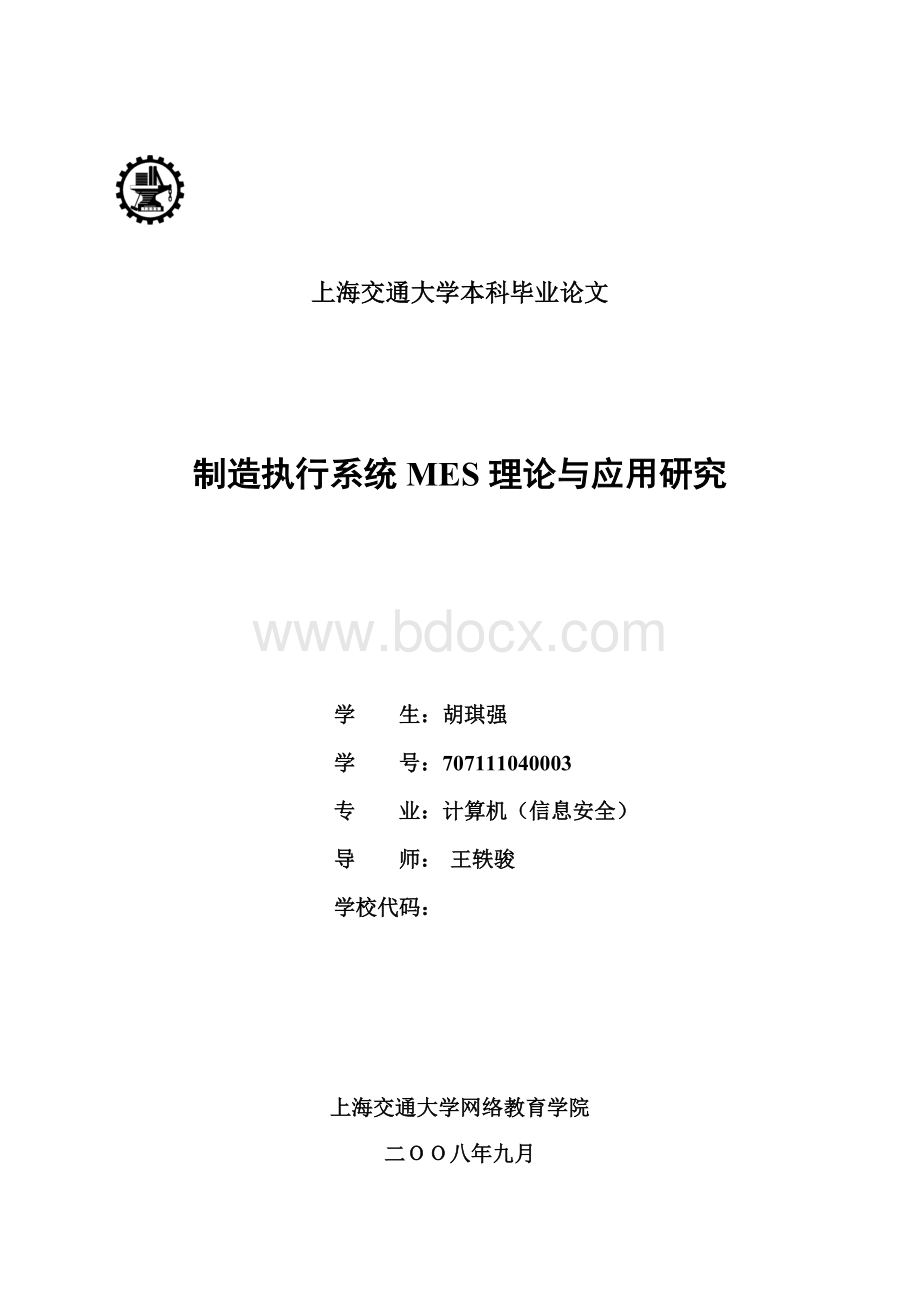
上海交通大学本科毕业论文 制造执行系统MES理论与应用研究
上海交通大学本科毕业论文
制造执行系统MES理论与应用研究
学生:
胡琪强
学号:
707111040003
专业:
计算机(信息安全)
导师:
王轶骏
学校代码:
上海交通大学网络教育学院
二OO八年九月
制造执行系统MES理论与应用研究
中文摘要
制造业是我国国民经济重要的支柱产业。
伴随中国加入WTO和经济全球化,中国正在成为世界制造业的中心。
中国的制造业企业面临日益激烈的国内外竞争,中国的半导体工业面临诸多挑战,如更加灵活的生产,更苛刻的质量要求以及具备竞争力的成本。
如何迅速提高企业的核心竞争力,就是以信息化带动工业化,加快信息化进程,通过投资具有成本效益的生产线,使用最新的科技。
走新型工业化道路。
制造执行管理系统(ManufacturingExecutionSystem:
MES)是企业CIMS信息集成的纽带,是实施企业敏捷制造战略和实现车间生产敏捷化的基本技术手段。
本论文主要以某半导体制造工厂计算机集成制造系统为背景,通过需求调研分析,根据企业的特定生产环境,提出了MES系统功能模块设计及实现架构,并且就系统模块的实现方法作了详细地阐述。
针对如何与企业其它信息系统进行有效地集成,本文提出基于OPC技术的MES与底层控制系统间集成,基于WEB技术的MES与上层信息系统间集成,并对如何实现MES系统与SAPERP系统的集成进行了个性化设计。
关键词:
MES,集成,OPC,Web
第13页共57页
ResearchandApplicationofManufacturingExecutionSystem(MES)
ABSTRACT
AsChinajoinstheWTO,theChineseenterprisesarefacingthechanceandchallenge.ItisimportantfortheenterprisestopromotetheirmodernizationwiththeManufacturingExecutionSystem,whichcanprovideflexibleandprecisemanufactory.ThisarticleusestheCIMSystemofSemiconductorIndustryasaflattoanalyzetheMESpracticeinChineseManufacturingenterprises.InthisarticletheMESistheperformerbetweentheprojectlayerandthebottomcontrollayer,whichisusedformanufacturingtrackingandcontrolthroughoutthemanufacturingprocessesinthefactory.
Keywords:
MES,Integration,OPC,Web
目录
第一章引言 6
1.1MES概述 6
1.1.1MES的产生 6
1.1.2MES的概念 7
1.1.3MES的国外发展 8
1.1.4MES的国内发展 10
1.2论文研究背景 11
1.3论文主要研究内容 12
1.4论文结构 13
第二章碧辟佳阳公司MES系统需求分析 14
2.1碧辟佳阳公司现状 14
2.2碧辟佳阳MES系统需求分析 15
第三章碧辟佳阳公司MES系统的功能模块设计与实现架构 25
3.1MES的设计原则 25
3.2MES系统的主要功能模块设计 26
3.3与MES有关的数据流分析 28
3.4MES的实现构架 28
3.4.1应用开发(管理)平台 28
3.4.2MES数据平台 29
第四章碧辟佳阳公司MES系统功能模块实现 31
第五章碧辟佳阳公司MES系统与现有系统间集成及实现 42
5.1MES在企业信息系统中的定位 42
5.2MES与底层控制系统的集成实现 42
5.2.1基于OPC-XML技术的MES/控制层集成的目标:
43
5.2.2基于OPC-XML技术的MES过程信息集成框架 45
5.3MES与上层ERP系统的集成实现 46
5.3.1集成内容 47
5.3.2集成模式的选择 47
5.4MES与SAPERP集成的接口实现 50
5.4.1SAP的接口类型 50
5.4.2MES与SAPPP-PI的集成 51
5.4.3接口实现代码示例 53
第六章结束语 55
6.1论文完成的工作 55
6.2改进意见 55
参考文献 56
致谢 57
第一章引言
1.1MES概述
1.1.1MES的产生
信息技术的飞速发展,将人类社会不可逆转地推进到知识经济时代。
现代企业若想在知识经济大潮中生存和发展,信息化是必然的选择。
许多企业通过信息系统的建设来加强管理,全面提高企业的竞争力。
随着制造业信息化工程的开展,许多企业实施了以物料需求计划(ManufacturingResourcesPlanning,MRPII)/企业资源计划(EnterpriseResourcePlanning,ERP)为代表的企业资源计划管理系统;以产品设计管理为主的产品数据管理系统PDM(ProductDataManagement);以监控和数据采集远距离控制与数据收集(SupervisoryControlandDataAcquisition:
SCADA)为代表的生产过程监控软件等。
这些系统虽然在企业中取得了一定成功,产生了一定的经济效益,然而出现了一些新的问题,形成了企业生产管理和制造单元控制软件之间的分离,使上层的MRP/ERP软件系统得不到精确的生产数据的支持,而制造单元又常常不能及时得到指令来调整工作状态,严重影响了制造业企业的生产和信息化进程。
随着企业信息化应用水平的不断提高,企业逐渐认识到将计划与制造过程统一起来的制造执行系统(ManufacturingExecutionSystem,MES)是解决这一问题的有效途径。
通过MES来实现企业信息的集成,形成实时化的ERP、MES、SFC车间层控制(ShopFloorControl,SFC)是提高企业整体管理水平的关键。
美国先进制造研究机构(AdvanceManufacturingResearch:
AMR)通过对大企业调查,在1990年提出MES概念。
AMR于1992年提出的三层的企业集成模型。
同年,一些有识之士开始意识到MES对制造业的重要性,发起并成立了国际性组织制造执行系统国际协会(ManufacturingExecutionSystemAssociationInternational,MESA)。
国际著名的软件厂商和企业界纷纷响应并加入这一非赢利性组织。
MEAS是以宣传MES思想和产品为宗旨,帮助其成员组织在企业界推广MES制定了一系列研究、分析和开发计划。
[1]
图1-1 AMR三层企业集成模型
1.1.2MES的概念
1)AMR将MES定义为:
“位于上层的计划管理系统与底层的工业控制之间的面向车间层的管理信息系统,就工艺本身指导工业控制。
”[1]
2)1992年MESA将MES定义为:
“MES能通过信息传递对从订单下达到产品完成的整个生产过程进行优化管理。
当工厂发生实时事件时,MES能对此及时做出反应、报告,并用当前的准确数据对它们进行指导和处理。
这种对状态变化的迅速响应使MES能够减少企业内部没有附加值的活动,有效地指导工厂的生产运作过程,从而使其既能提高工厂及时交货能力,改善物料的流通性能,又能提高生产回报率。
MES还通过双向的直接通讯在企业内部和整个产品供应链中提供有关产品行为的关键任务信息”。
[1]
3)国家863专家关于MES的定义:
制造执行系统(ManufacturingExecutionSystem,简称MES)是处于计划层和控制层之间的执行层,主要负责生产管理和调度执行。
它通过控制包括物料、设备、人员、流程指令和设施在内的所有工厂资源来提高制造竟争力,提供了一种系统地在统一平台上集成诸如质量控制、文档管理、生产调度等功能的方式。
制造执行系统的核心:
使用实时精确的生产过程数据,优化生产活动,对生产活动进行指导:
能够对生产过程的变化,实施快速反应,减少无附加值行为,提高工厂运行和事件处理的有效性。
MES定义的三个要点:
MES的优化目标是整个生产过程;MES需要收集生产过程中大量的实时数据,并且对实时事件能及时处理;MES需要同时对计划层和控制层保持双向通信能力,从上下层接受相应数据并反馈处理结果和生产指令。
其核心为“优化、快速反应、反馈控制”。
在企业信息集成系统中,MES处于ERP和过程控制系统之间,通过控制包括物料、设备、人员、流程指令和设施在内的所有工厂资源来提高制造竞争力,提供了一种系统地在统一平台上集成诸如质量控制、文档管理、生产调度等功能的方式,从而实现了实时化的EPR/MES/生产控制系统的集成一体化,它形成了一个信息交换的桥梁,使企业管理者能够实时地掌握生产信息,进行生产决策。
通过建立MES的系统结构,可以提供一个完整的生产管理系统与工业生产过程控制紧密集成的解决方案,提高企业的自动化水平和管理水平,提高企业的反应速度和竞争能力。
MES作为面向制造的系统必然要与企业其它生产管理系统切关系,MES在其中起到了信息集线器的作用,它相当于一个通讯工具为其它应用系统提供生产现场的实时数据。
[2]
MES使用实时、连续、自动、完整、精确的数据,优化从定单到产品完成的整个生产活动,通过对变化情况的快速反应,减少无附加值行为,提高工厂运行和处理的有效性。
MES是企业生产组织和管理的强有力的手段。
1.1.3MES的国外发展
MES发展的几个阶段:
图1-2 MES技术的发展历程
第一阶段:
专用MES(PointMES:
P-MES)――70年代
功能作用:
对某个单一的生产问题(如制造周期启发竞争力、在制品库存过大、产品质量得不到保证、设备利用率低、缺乏过程控制等)提供相应的软件系统加以解决,是自成一体的系统。
优点:
对特定的问题,能提供最恰当的解决问题的能力和易实现。
缺点:
不利于信息集成和共享
第二阶段:
集成MES一80――90年代
功能作用:
在P-MES基础发展起来,提供一套集成的应用软件来同时解决多个不同的生产问题。
具有丰富的应用功能,统一的逻辑数据库,单一的车间产品及过程模型等优点成为MES产品的主流。
是针对特定的、规范化的环境而设计的系统,如航空、装配、半导体、食品等行业,目前实现了三层的信息集成。
优点:
功能丰富,整体性强,在一定的范围内实现信息集成和共享。
缺点:
依赖于特定的车间环境,模块化、开发性、可重构性差,缺乏柔性,不宜修改和扩充,难以适应敏捷制造环境的要求。
第三阶段:
传统MES(TraditionalMES:
T-MES):
传统MES是在信息控制技术第一阶段上发展起来的信息系统,隐含较大的风险,如过程的微小变化就可能导致系统不能正常运行,系统稳定性差。
具体表现在:
通用性差、可集成性弱、缺乏互造作性、重构能力差、敏捷性(应变能力)差。
第四阶段:
可集成MES(1ntegratableMES