常规分析的质量管理与控制图.ppt
《常规分析的质量管理与控制图.ppt》由会员分享,可在线阅读,更多相关《常规分析的质量管理与控制图.ppt(30页珍藏版)》请在冰豆网上搜索。
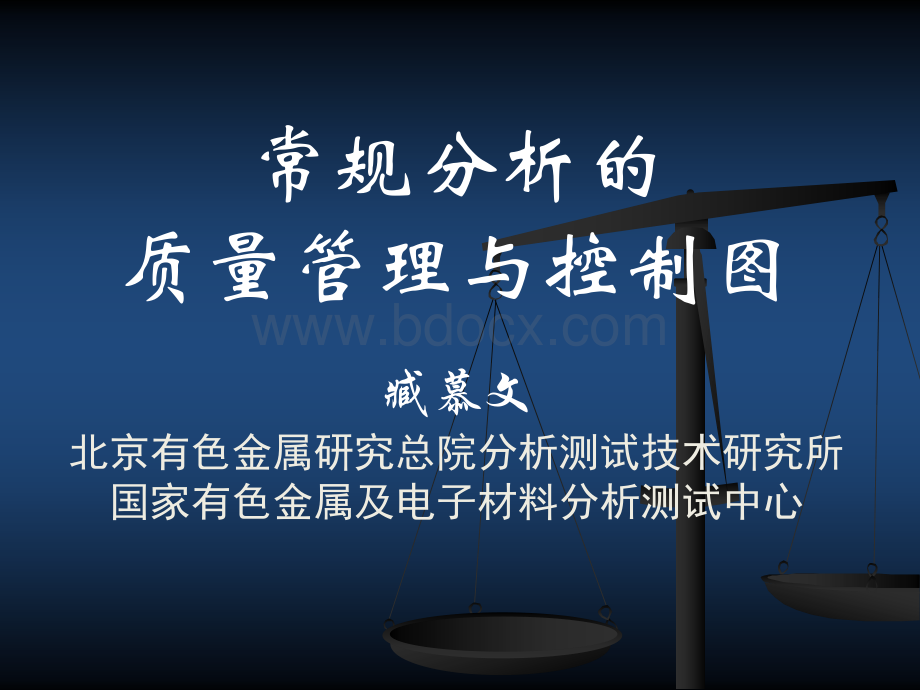
常规分析的质量管理与控制图臧慕文北京有色金属研究总院分析测试技术研究所国家有色金属及电子材料分析测试中心1994年,美国著名质量管理学家J.M.Juran曾在美国质量管理学会年会上指出:
20世纪以“生产力的世纪”载入史册,未来的21世纪将是“质量的世纪”。
科学研究、资源开发、环境保护、产品质量控制和商业贸易等等各方面都离不开分析测试。
如何保证分析测试的质量,使分析结果既正确又精密,即准确度高?
影响分析测试质量的五大因素是:
人(人员)、机(仪器)、料(试剂)、法(方法)、环(环境)。
在正常的情况下,应该对这五大方面有良好的管理和控制,使测试质量获得重要保证。
统计分析测试数据并检验测试数据的可靠性也是测试质量的重要保证:
正确度计算:
平均值,中位值;正确度检验:
标准物质对照、标准方法比对、加标回收试验并用t检验和方差分析进行统计检验。
精密度计算:
极差R,标准偏差s,不确定度u,重复性限r,再现性限R,标准四分位距NormIQR等;精密度检验:
检验、F检验、Cochran检验等方差检验;但是,这些保证测试质量的办法、措施,都是“离线”的、“静态”的,没有起到“全过程的监控”作用。
20世纪20年代美国的休哈特(W.A.Shewhart)提出了“统计过程控制(StatisticalProcessControl)”简称SPC的概念。
SPC就是应用统计技术对过程中的各个阶段进行监控,是用控制图法(或质量管理图法)进行质量管理,从而达到保证与改进质量的目的。
SPC强调全过程的预防,首先在生产管理中采用,以后推广应用到其它方面,常规分析质量管理也可采用常规分析质量管理也可采用控制图控制图。
1.简述SPC及其发展SPC是利用统计技术(控制图)对生产(管理)过程中的各个阶段进行监控,科学地区分出生产过程中产品质量的偶然波动与异常波动,以便采取措施,消除异常,恢复过程的稳定。
作用预防判断过程的异常,及时告警。
缺点不能告知异常是由什么因素引起的和发生于何处,即不能进行诊断。
SPD(StatisticalProcessDiagnosis)即统计过程诊断,是是SPCSPC的的进进一步一步发发展。
上世展。
上世纪纪8080年代开始,年代开始,张公绪教授提出选控控张公绪教授提出选控控制图系列、两种质量诊断理论,开辟了统计质量诊断的新方制图系列、两种质量诊断理论,开辟了统计质量诊断的新方向,向,9090年代又提出两种多元诊断理论,解决了多工序、多指年代又提出两种多元诊断理论,解决了多工序、多指标系统的质量控制与诊断问题。
标系统的质量控制与诊断问题。
目前目前SPDSPD已已进进入入实实用性用性阶阶段。
段。
SPA(StatisticalProcessAdjustment)即统计过程调整,是SPD的进一步发展,这方面国外刚刚起步,目前尚无实用性的研究成果。
SPCSPDSPASPC、SPD、SPA三者构成一个闭环,循环不已。
2质量控制图控制图(ControlChart)是对过程质量特性值进行测定、记录、评估以及监察过程是否处于控制状态的一种用统计方法设计的图。
控制图显示质量特性值随时间变化的波动曲线,并分析和判断是由于偶然原因抑或由于系统原因所造成的质量波动,从而告警,提醒操作者作出准确判断和提出有效对策,消除系统性原因产生的影响,使操作程序处于稳定并得到动态控制。
2.1控制图原理及形式在正态分布密度函数曲线中可以看到,在正态分布密度函数曲线中可以看到,正正态态分布分布由由两个参数,即两个参数,即总总体均体均值值和和总总体体标标准差准差来决定的。
来决定的。
这对质量管理很有用,即无论总体均值和总体标准差取何值,产品质量特性值落在之间的概率为99.73%,落在之外的概率为100%-99.73%=0.27%,而超过一侧,即大于或小于的概率为0.27%/2=0.135%。
图1正态分布在3区间的概率Shewhart根据正态分布的这一特性,提出了控制图。
将图1先按顺时针方向转90即成图2(a),再上下翻转180即成图2(b)。
以测量值为纵坐标,以日期或测量顺序为横坐标,即得图3单值控制图,也叫x控制图。
该图纵坐标为质量特性值,横坐标为抽样时间或样本序号。
三条线:
上面一条虚线叫上控制界限线(简称上控制线),相应于,用符号UCL表示,中间一条实线是中心线,相应于用符号CL表示,下面一条虚线叫下控制界限线(简称下控制线),相应于,用符号号LCLLCL表示。
表示。
图3单值控制图(x控制图)图2由正态分布概率密度曲线演变的控制图t/h为什么用控制图的控制界限?
质量指标值落在以外的概率只有0.27%,这是一个小概率。
按照小概率事件原理,在一次实践中超出按照小概率事件原理,在一次实践中超出范围的范围的小概率事件几乎是不会发生的。
小概率事件几乎是不会发生的。
若发生了小概率事件,说明过程已处于不稳定状态。
利用控制图来判断过程是否处于稳定和受控状态就是进行统计推断。
统计推断就会产生两种错误。
第一类错误是将正常判为异常,即测试本来并没有发生异常,只是由于偶然原因的影响,使质量波动过大而超过了界限线,却判为存在系统原因造成分析数据异常,从而因“虚告警”造成损失。
第二类错误是将异常判为正常。
即虽然已经存在系统因素的影响,但因某种原因,质量波动并没有超过界限线,因此认为测试仍处于控制状态而没有采取相应的措施加以改进。
这样因“漏告警”而造成损失。
根据数理统计学原理,放宽控制界限线范围固然可以减少犯第一类错误的机会,但却会增加犯第二类错误的可能,反之,压缩控制界限线范围可以减少犯第二类错误的机会,但却会增加犯第一类错误的可能。
显然,控制图的控制界限线范围的确定应以两类错误的综合总损失最小为原则。
方法确定的控制图控制界限,被认为是经济合理的方法因此,大多数国家都采用这个方法,并称为“原理”。
20世纪80年代Motorola.Co.将控制方式由过去的控制方式改为控制方式。
控制方式下的稳态不合格品率为,控制方式下的稳态不合格品率为,后者比前者降低了:
即135万倍!
2.2常规分析中常用的控制图常规分析中常用的控制图2.2.12.2.1单值单值控制控制图图实例:
某管理某管理样样中中铜铜的的测测定。
在一段定。
在一段时间时间里穿插在日常分析里穿插在日常分析工作中,用常工作中,用常规规方法独立方法独立测测定定2020次以上,次以上,计计算算标标准偏差,准偏差,积积累累结结果,果,绘绘制控制制控制图图。
测测定定结结果如表果如表11。
月月日日2月月1347111216202123样品编号12345678910w/%0.2510.2500.2500.2630.2350.2400.2600.2900.2620.234月月日日2月月25283月月2581215182330样品编号11121314151617181920w/%0.2290.2500.2830.3000.2620.2700.2250.2500.2560.250该系列测定值的平均值为该系列测定值的平均值为,标准偏差,标准偏差绘图绘图如如图图44。
图图中中心中中心线线,即,即0.256%0.256%;UCLUCL和和LCLLCL分分别别在在CL(CL(均均值值)的上下两的上下两边边()和和()处处,而上下警告,而上下警告限限则则分分别别在在()和和()处处,用虚,用虚线线表示之。
表示之。
联结各测定值的曲线,虽然有起伏,但除23#点,各点都在控制限内。
有了这张控制图,以后再进行此管理样中铜的测定时,就可以利用图对分析质量进行监控。
UCLLCLCL测定值顺序号图4控制图的打点监控办法:
只要在分析未知样时,附带分析这份管理样。
把管理样的分析结果接着“打点”到这张控制图上。
如果“打点”未出界,表示分析的各种条件正常。
影响结果的,无系统因素,仅偶然性因素,反映分析过程处于稳定或控制状态。
因此,同时进行的未知样的分析结果也是可靠的。
若“打点出界”,如图4上的23#结果,就可判断那一天分析条件有异常。
因为在正常情况下,打点出界的可能性为0.1%左右。
根据小概率事件原理,在正常情况下,一次分析结果不应超出置信区间。
现在一次独立实验中,发生了“打点出界”事件,说明对结果产生影响的,除经常存在着的偶然性因素外,还有系统因素在起作用,使正态分布曲线发生位移。
23#测定值所遵循的是另一正态分布,测定值x对于而言,出现的概率就不再是0.1%,而是xx%。
由此可见,控制图上“打点出界”,能及时指出分析过程有异常。
找出系统原因,并消除,保证不再犯。
这样逐个除去系统因素,就会使分析过程逐步趋近并最终达到控制状态。
怎样判断分析过程是否处于控制状态?
根据“小概率原理”,若点子在控制限内,原则上可以看作分析过程处于控制状态;若点子超出控制限外或恰在控制限上,则可以看作过程处于失控状态。
还有一些依据“小概率原理”的规则:
(1)点子基本随机排列,符合3种情况时,过程处于控制状态:
i)连续25点全部都在界限内;ii)连续35点,在界限外的点不超过1点;iii)连续100点;在界限外的点不超过2点;对于界外点,需找出异常原因。
(2)图5中,在中心线一侧连续出现的点叫做链。
其点数叫做链长。
当链长不小于7时,则判断有异常(以往采用7点链判异,现国外已改为9点链判异,使犯第一种错误的概率)0=0.0027图5控制图中出现的链长为7的链(异常)(3)(3)点子逐点子逐渐渐上升或下降的状上升或下降的状态态称称为倾为倾向。
向。
图图66中,当有中,当有连续连续不不少于少于77点的上升或下降的点的上升或下降的倾倾向向时时,则则判断有异常。
判断有异常。
图6控制图中出现的倾向(4)中心线一侧点子连续出现,属以下情况,判断有异常:
i)连续11点中,至少有10点;ii)连续14点中,至少有12点(图7);iii)连续17点中,至少有14点;iv)连续20点中,至少有16点。
图7中心线一侧点子连续出现(5)(5)点子屡屡超出警告限而接近控制限点子屡屡超出警告限而接近控制限(图图8),8),下述情况均有异常:
下述情况均有异常:
i)i)连续连续33点中,至少有点中,至少有22点;点;ii)ii)连续连续77点中,至少有点中,至少有33点;点;iii)iii)连续连续1010点中,至少有点中,至少有44点。
点。
图8点子屡屡接近控制限UCLCLLCL上警告限上警告限下警告限下警告限(6)(6)所有点都集中在中心所有点都集中在中心线线附近,判断有异常附近,判断有异常(图图9)9)。
所有点都集中在中心线附近,数据似乎“特别好”,但是不要被良好的“外貌”所迷惑,而应该注意到所隐含的非随机性。
造成此现象的原因可能是数据有误或数据虚假。
图9点子集中在中心线附近2.2.2R控制图(均值极差控制图均值极差控制图)R控制图是均值()和极差(R)控制图,为两者联用的综合控制图。
对于计量值数据,这是最常用、最基本的控制图。
均值控制图用来观察分析数据平均值的变化,极差控制图用来观察分析数据分散程度的变化。
两图同时使用,可以综合地了解质量特性数据的分布形态。
实例:
光电直读光谱法测定某管理样中碳,绘制R控制图。
(1)搜集数据1)搜集近期质量数据,将数据按组号(或分析时间)顺序分组。
2)每次抽取的样本个数n=35个,搜集数据一般为N=100个(最少50个以上),并分成K组。
3)搜集到的每组数据,按次序填入控制图数据记录表2中。
样号号x1x2x3x4x5Rsi10.750.910.920.970.930.8960.220.08520.830.800.780.810.880.8200.100.03830.910.880.880.850.780.8600.130.04940.830.830.810.830.750.8100.080.03550.810.860.910.780.840.8400.130.04960.970.730.710.670.780.7720.300.11870.850.910.830.760.800.8300.150