生产计划APS高级自动排程思想.docx
《生产计划APS高级自动排程思想.docx》由会员分享,可在线阅读,更多相关《生产计划APS高级自动排程思想.docx(11页珍藏版)》请在冰豆网上搜索。
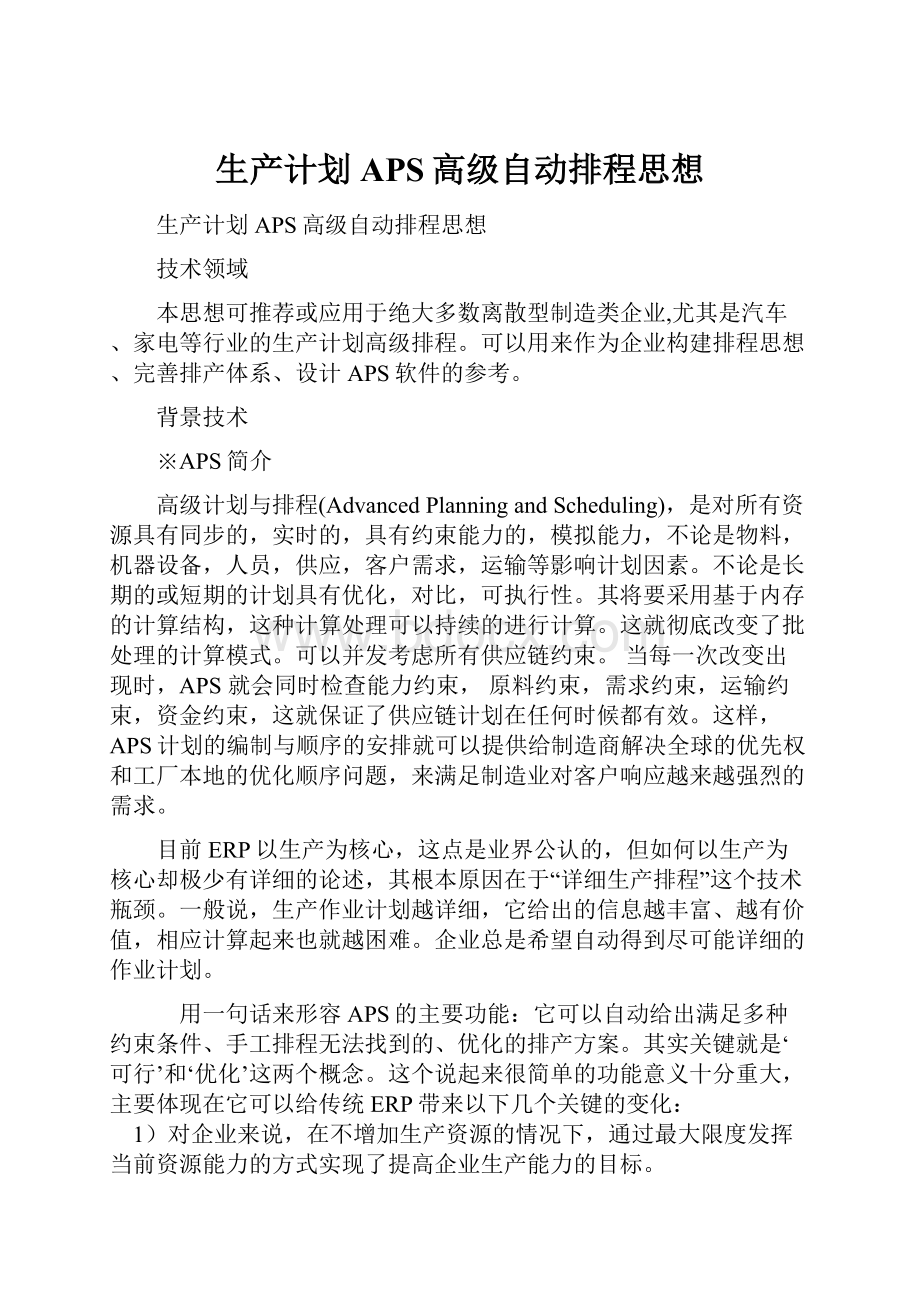
生产计划APS高级自动排程思想
生产计划APS高级自动排程思想
技术领域
本思想可推荐或应用于绝大多数离散型制造类企业,尤其是汽车、家电等行业的生产计划高级排程。
可以用来作为企业构建排程思想、完善排产体系、设计APS软件的参考。
背景技术
※APS简介
高级计划与排程(AdvancedPlanningandScheduling),是对所有资源具有同步的,实时的,具有约束能力的,模拟能力,不论是物料,机器设备,人员,供应,客户需求,运输等影响计划因素。
不论是长期的或短期的计划具有优化,对比,可执行性。
其将要采用基于内存的计算结构,这种计算处理可以持续的进行计算。
这就彻底改变了批处理的计算模式。
可以并发考虑所有供应链约束。
当每一次改变出现时,APS就会同时检查能力约束,原料约束,需求约束,运输约束,资金约束,这就保证了供应链计划在任何时候都有效。
这样,APS计划的编制与顺序的安排就可以提供给制造商解决全球的优先权和工厂本地的优化顺序问题,来满足制造业对客户响应越来越强烈的需求。
目前ERP以生产为核心,这点是业界公认的,但如何以生产为核心却极少有详细的论述,其根本原因在于“详细生产排程”这个技术瓶颈。
一般说,生产作业计划越详细,它给出的信息越丰富、越有价值,相应计算起来也就越困难。
企业总是希望自动得到尽可能详细的作业计划。
用一句话来形容APS的主要功能:
它可以自动给出满足多种约束条件、手工排程无法找到的、优化的排产方案。
其实关键就是‘可行’和‘优化’这两个概念。
这个说起来很简单的功能意义十分重大,主要体现在它可以给传统ERP带来以下几个关键的变化:
1)对企业来说,在不增加生产资源的情况下,通过最大限度发挥当前资源能力的方式实现了提高企业生产能力的目标。
2)APS排程的结果给出了精确的物料使用和产出的时间、品种、数量信息,用这些信息可以把很多相关企业或者分厂、车间联合在一起组成一个'SCM供应链'系统,最大限度减少每个企业的库存量。
3)APS可以用来做为生产决策的依据,它的排程计算结果不光可以作为生产计划,还可以通过不断whatif的'试算'的方式为企业提供生产决策依据。
4)根据自动生成的作业计划还可以自动生成质检、成本、库存、采购、设备维护、销售、运输等计划。
带动企业各个不同管理模块围绕生产运转,改进这些模块的运转方式,大大提高这些模块的运转效率,提升企业整体管理水平。
APS系统的开发难度很大,需要融合最前沿数学理论和最先进管理理论,专业人才很少,投资见效很慢,在国外的价格非常昂贵。
但APS的思想却可以在排产领域和生产管理过程中给人以高度的启发。
APS要解决的两个问题:
如何不断缩短运算时间和如何不断提升次优解的优化程度。
前者偏重数学、硬件;而后者更偏重APS思想或者APS算法,它也直接体现了不同厂商核心技术的水平高低。
※应用案例
安徽宁国中鼎密封件有限公司(简称“中鼎公司”)是全国橡胶密封件行业的龙头企业,其技术力量、工艺装备以及产量和效益居全国同行领先水平,其主导产品主要是为国内各大汽车制造厂和国际著名汽车制造商提供橡胶制品等。
根据企业的生产经营特点和现存管理技术问题,为了根据企业的资源约束条件合理地确定生产作业计划,减少制造提前期,满足快速多变的主机市场需求,从而进一步提高企业的管理水平和综合竞争力,以适应汽车配套件市场的竞争环境,中鼎公司决定实施ERP系统,并在ERP系统中引入了先进的计划与排程——APS技术
中鼎公司应用APS技术的主要特点在于:
建成一个符合企业个性化特点的生产管理系统,即在传统ERP的基本框架之上,对计划层进行必要的“瘦身”,并将粗能力计划功能嵌入到主生产计划模块中;在执行层进行必要的“胖体”,即将物料需求计划、细能力计划、车间任务、车间作业溶入到APS模块中,形成一个有限能力顺排生产管理系统。
APS子系统的主要作用:
各事业部利用该系统对不同的产品进行不同的产能定义和产能计算;确定提前期和生产批量;对生产任务进行排程和调度。
APS系统的功能特点:
集成了物料需求和细能力需求及车间任务和车间作业功能,使生产计划—物料需求计划—能力平衡—车间执行—生产调度一气呵成。
APS技术在中鼎公司ERP系统中的应用,反映在生产管理方面的效果主要体现在以下诸方面:
1、提高了企业的市场应变能力
使传统的先制造出产品再推向市场的“推”式经营方式,被按市场需求安排生产的“拉”式经营方式所取代,公司能够以最快、最经济的方式安排设计、工艺、生产,缩短了供货周期,提高了企业的市场应变能力。
2、提高了企业的生产计划管理精度
建成的生产管理系统是闭环反馈控制系统,它通过对能力和物料等资源的模拟排程,完成产品计划(MPS),零部件计划(MRP),工序级计划(PAC)之间的无缝衔接,使生产作业计划变得更合理可行,从而压缩了无效时间和提前期,使产品制造周期缩短将近一半。
3、提高了企业的装配和用户服务水平
中鼎ERP系统可迅速、准确地反映原材料和零部件的存储、成套和缺件情况,从而可预先进行监督和控制,保证在降低库存的条件下无缺件生产。
由于零部件能准时交付,使得企业装配车间的劳动生产率提高了20%~40%,准时交付率平均提高55%,误期率平均降低35%;由于消除了缺件,保证了均衡生产,减少了突击性加班,并保证了产品的质量,有效地提高了企业的装配和用户服务水平。
发明内容
本发明所提供的是一种关于离散型制造类企业进行生产计划高级自动排程的思想。
该思想所围绕的核心目标分解如下:
1.杜绝人工排产造成的资源浪费;
2.减少半成品库存
3.降低工厂平均生产周期
4.提高设备利用率
5.提高订单承诺交期的履约率、提高客户满意度。
6.通过共享精确的排程结果,实现按计划拉动原料备货、原料配送、成品配车、成品发货等环节。
7.排产经验固化、沉淀,过程规范化、标准化。
以下以离散型制造企业的家电行业为例,针对不同的生产模式,在外协物料非企业排产瓶颈资源的前提下,如何有效的进行高级计划排程,加以简述:
1.通过工艺模型找出瓶颈工序
工厂的型号都有固有的工艺模型,模型定义了生产该型号所经历的一道道工序。
对于洗衣机、空调类家电,产品差异化较小,瓶颈工序不在前工序,影响排程的因素主要体现在事业部生产线的日产能、订单的交货期、外协物料的产能等。
此类排产相对简单,可以直接从成品入手,以产品交期、成品库存、日产能作为主要考虑因素,结合事业部、物流的评审即可排定计划。
对于冰箱类家电,生产过程则复杂的多,产品型号差异化较大,排程主要受箱体发泡、门体发泡等前工序产能的制约,因此应从前工序入手,应该更多的考虑产品交期、发泡模位、发泡模具产能限制等条件。
图一为某事业部发泡线体示意图
图一发泡线体示意图
2.搜集基础信息
确认瓶颈工序的同时,努力搜集自动排程过程用到的基础数据。
如果将排产算法形容为一个人大脑,那么基础数据就是骨架,下面列出了APS不可获取的基本信息:
a)型号主数据
b)型号分类
c)物料BOM
d)生产线信息
e)工艺模型
f)模具
g)工序
h)工厂日历
基本信息可以根据企业的情况通过ERP软件获取到,否则通过人工来整理。
3.定义排产约束参数
通过头脑风暴法或启发引导等方式,搜集各排产员排产所考虑的约束条件。
将搜集到的约束条件进行归纳汇总。
下面列出了部分排产的约束条件。
图二约束条件归总
4.非前工序瓶颈_自动排产过程
4.1需求处理:
此步骤首先对于市场部一段时间内的所有销售订单,按照系统能处理的统一格式,进行加工整理。
比如将销售订单依照型号、工贸、日期进行汇总数量。
4.2通过型号或所属分类,找到其所属的工艺模型并得到瓶颈工序、可产线体、线体优选顺序和生产节拍等信息。
4.3整体分线:
通过得到的第一优选线体进行分线处理,分线是指将订单分配到生产线。
图三总体分线
4.4生产订单总体均衡:
分别计算每条线体的实际耗时,与标准耗时做减法,从正差异的线体向负差异的线体移单。
图四总体均衡
4.5将处理后的需求按照交期由早到晚排序
4.6按4.5的排序结果,以日为单位,将枚举所有订单以此占用日期时间轴。
4.7在提前期允许的范围内,前提后面符合条件的订单,前提时遵循型号的优先级、工贸的优先级约束条件。
4.8考虑到日的线与线之间的均衡移单,逻辑同4.4
4.9考虑拆单补足空余时间轴,拆单不能盲目,遵循连续的原则,既时间上要连续或模具使用的连续。
4.10运算每个订单时,时刻要校验以下约束:
型号日最大产能、线体库存容量、工序库存容量、同工厂同工贸同日最大发货体积
4.11到日到线的排产完成后,考虑按照节拍快慢拍排列各线体订单的时间顺序。
4.12自制样机按照提前期、生产台数自动插空。
4.13输出成品总装生产时序计划
4.14通过物料BOM分解,按照工艺树推出半成品/前工序生产时序计划
5.前工序瓶颈_自动排产过程
5.1需求处理:
此步骤首先对于市场部一段时间内的所有销售订单,按照系统能处理的统一格式,进行加工整理。
比如将销售订单依照产品分类、工贸、日期进行汇总数量。
5.2通过型号分类,找到其所属的工艺模型并得到总装工序、线体、线体优选顺序和生产节拍等信息。
5.3整体分线:
通过得到的总装第一优选线体进行分线处理,分线是指将订单分配到生产线。
同4.3
5.4生产订单总体均衡:
分别计算每条线体的实际耗时,与标准耗时做减法,从正差异的线体向负差异的线体移单。
同4.4
5.5通过型号分类,找到其所属的工艺模型并得到箱体发泡(瓶颈)工序工序、线体、线体优选顺序和生产节拍等信息
5.6通过系列的需求、日产能和模具数量,计算所有系列的单模日程
系列号
T+1周
周6
周日
周1
周2
周3
周4
周5
周6
合计
模具数
模日
产能
2009-9-5
2009-9-6
2009-9-7
2009-9-8
2009-9-9
2009-9-10
2009-9-11
2009-9-12
日程
BCD-195
1
400
40
130
243
488
353
606
113
0
1973
4.9325
BCD-216
3
500
600
1581
1514
1849
1624
1000
513
0
8681
17.362
BCD-218
3
500
118
140
19
54
5
8
344
0.688
BCD-228
1
400
200
431
387
398
311
213
151
309
2400
6
BCD-248
1
300
200
258
256
221
61
52
53
112
1213
4.0433333
BCD-258
1
200
20
84
83
85
25
20
7
10
334
1.67
BCD-278
1
200
20
101
96
84
19
5
23
348
1.74
BCD-301
1
200
60
244
190
352
74
118
263
480
1781
8.905
BCD-331
1
200
80
35
20
58
21
55
113
228
610
3.05
BCD-401
1
200
3
5
2
5
1
16
0.08
合计
1223
2987
2931
3559
2543
2069
1226
1162
17700
48.470833
图五系列需求单模日程表
5.7上模:
将系列模日数能被生产天数整除的作为集合A,不能被整除的作为集合B:
其中A和B都按照模日由大到小排列,并且现循环A再循环B,以尽量占用天数多占用模位少为原则,从有需求日期的前一天开始成矩形连续的占用时间轴,占用模位,以此循环各系列;每占用一个,计算日产能和日需求的结存情况。
每日向前累计产能要大于累计需求;如果不足要增加模位;剩余不满单日模产能安排空余模位。
补充空余模位的逻辑过程参照4.7~4.9。
系列:
1,2,3,4,5,6,7,8
系列需求:
Ni(i=1,2,3,…,8)
最晚交货期
Ki(i=1,2,3,…,8)
日期1
日期2
日期3
日期4
日期5
模位1
模位2
模位3
模位4
安排每个系列需求时,占用单元格不能为不规则图形,必须为矩形
5.8根据型号交货期、型号优先级,将系列匹配到型号,从而确定型号的关键工序的具体生产时间和顺序。
5.9通过工艺模型和线体分组的概念,将发泡线体映射到总装线体
5.10输出成品总装生产时序计划
5.11通过物料BOM分解,按照工艺树推出半成品/前工序生产时序计划