数控铣床孔类零件加工.docx
《数控铣床孔类零件加工.docx》由会员分享,可在线阅读,更多相关《数控铣床孔类零件加工.docx(23页珍藏版)》请在冰豆网上搜索。
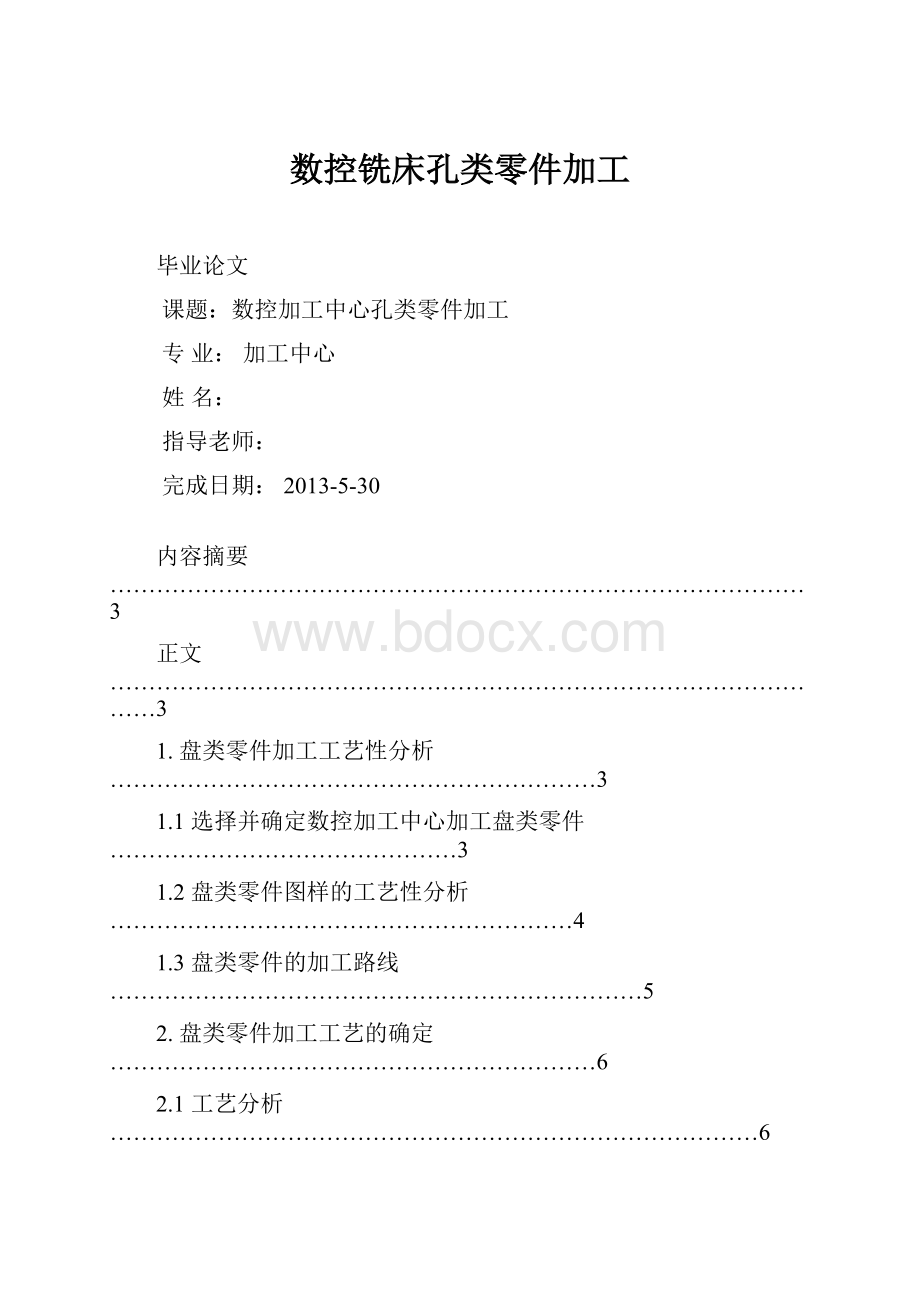
数控铣床孔类零件加工
毕业论文
课题:
数控加工中心孔类零件加工
专业:
加工中心
姓名:
指导老师:
完成日期:
2013-5-30
内容摘要………………………………………………………………………………3
正文……………………………………………………………………………………3
1.盘类零件加工工艺性分析………………………………………………………3
1.1选择并确定数控加工中心加工盘类零件………………………………………3
1.2盘类零件图样的工艺性分析……………………………………………………4
1.3盘类零件的加工路线……………………………………………………………5
2.盘类零件加工工艺的确定………………………………………………………6
2.1工艺分析…………………………………………………………………………6
2.2工艺卡片…………………………………………………………………………7
2.3刀具卡片…………………………………………………………………………8
2.4走刀路线…………………………………………………………………………8
2.5程序的编制……………………………………………………………………13
3.误差分析…………………………………………………………………………17
4.结论………………………………………………………………………………17
参考文献……………………………………………………………………………18
盘类零件的加工
内容摘要
盘类零件是由多个端面、深孔、螺纹孔、曲面、沟槽、外轮廓组合而成的较复杂的盘形零件。
其特点是零件基本形状呈盘形块状,零件表面汇集了多种典型表面。
加工时,装夹次数一般较少,但所用刀具一般较多,编制程序较繁琐。
加工前需要做好充分的准备,包括图纸分析、确定加工工艺、选用机床型号、选用毛坯大小、确定走刀路线与加工顺序等,其前期的准备工作比较复杂。
关键词:
盘类零件图纸分析确定加工工艺机床
正文:
数控加工过程中需要考虑多方面的因素,包括图纸的分析、选择适合加工该零件的数控机床、选择加工中将要用到的刀具规格、选择良好的切削用量等等。
由此看出,数控加工实践是一门复杂的技术。
需要多学习、多熟练才能在保证安全的情况下完成任务。
所以,我作为数控行业的一份子要努力的提高自身的专业水平,不断的锻炼自己的实践技能,成为一个全方面发展的数控技术人才。
1盘类零件加工的工艺性分析
盘类零件加工工艺性分析是编程前的重要工艺准备工作之一,根据实际加工,利用数控加工中心具有高精度、高柔性、高效率,且适合加工具有复杂轮廓、端面的零件等特点。
通过对使用BV75型数控加工中心加工盘类零件,来阐述以下几个方面的问题:
1.1选择并确定数控加工中心加工盘类零件
在选择加工盘类零件的设备时,应充分发挥数控加工中心适用于加工复杂端面这一加工优势。
选择BV75数控加工中心的主要依据如下:
BV75立式加工中心采用专业化厂家提供的数控系统,各直线运动轴、主轴及追加旋转轴均采用伺服电机驱动,三轴或四轴联动,可进行各种铣削、镗孔、钻铰孔、刚性攻丝等一般机械加工,并实现数字化精确定位,通过运动轴插补联动可实现旋切大螺纹、多种曲面加工,且同一台机床上可实现工件一次装夹过程中多种工序的粗、精加工。
同时,数控系统中配备了多种典型循环程序供加工过程中编程选用。
机床工作过程中的切削加工、冷却液提供、刀具交换等均由预编制程序控制,且换刀过程中自动实施主轴中心吹气,保持刀柄及主轴锥孔清洁。
机床切削过程中产生的切屑根据配置不同或者由冲刷系统及排屑器等定向排送到集屑小车,或者人工清理。
BV75立式加工中心主要技术参数如下:
机床行程范围
X轴mm
762
Y轴mm
510(带A轴为450或490)
Z轴mm
560
工作台参数
工作台尺寸mm
610*900
T型槽尺寸mm
5-18*100*125
工作台最大承载能力(均布)kg
500
主轴端面直工作台面距离mm
152~712
主轴中心至立柱导轨面距离mm
563.4
移动速度
快速移动速度mm/min
24000
切削进给速度mm/min
3~15000
主轴参数
主轴锥孔
7:
24
主轴轴径mm
φ70
刀库参数
斗笠式刀库
机械手式刀库
刀库容量(把)
21
24
换刀方式
任选
随机
换刀时间(秒)
6
2.5
最大刀具直径mm
φ80
φ75
相邻无刀最大刀具直径mm
φ160
φ120
最大道具长度mm
304
290
最大单刀重量kg
6.8
6
刀库承载能力kg
68
80
1.2盘类零件图样的工艺性分析
根据BV75数控加工中心加工盘类零件的特点,对零件图纸进行工艺分析时,应着重考虑如下几点:
(1)盘类零件图纸的尺寸分析
根据盘类零件图纸的分析,应首先确定零件上各端面的相互位置、相距尺寸,保证加工时刀具的走刀路线不会干涉到零件的各个端面。
例如,在加工时刀具直径为10mm,零件两端面距离为9mm,若在加工前发现这一点便会在保证加工精度的情况下更换合适的刀具。
相反,如果在实际加工前对图纸的分析不够透彻,便有可能出现上述错误,造成零件加工失败,不仅浪费时间,还提高了加工成本,得不偿失。
(2)顺铣和逆铣对加工的影响
在铣削加工盘类零件时,采用顺铣还是逆铣方式是影响加工表面粗糙度的重要因素之一。
逆铣时切削力F的水平分力FX的方向与进给运动Vf方向相反,顺铣时切削力F的水平分力FX的方向与进给运动Vf的方向相同。
铣削方式的选择应视零件图样的加工要求,工件材料的性质、特点以及机床型号、刀具规格等条件因素综合考虑。
通常,由于数控加工中心传动采用滚珠丝杠结构,其进给传动间隙很小,顺铣的工艺性就优越于逆铣。
为了降低表面粗糙度值,提高刀具的耐用度,对于铝镁合金、钛合金和耐热合金等材料,尽可能采用顺铣加工。
但如果盘类零件的毛坯为黑色金属锻件或铸件,表皮较硬而且余量一般较大,这时采用逆铣较为合理。
1.3盘类零件的加工路线
(1)z轴方向走刀路线
在加工盘类零件时,Z轴的切削深度尤为重要。
必须要看清图纸的标注,并在深度上也要保证高精度。
铣削外轮廓时,尽量选择在工件外下刀。
铣削内轮廓时,要选好下刀点,必须保证不能干涉工件的尺寸精度。
(2)x、y轴方向走刀路线
在加工盘类零件时,x、y轴方向走刀路线是否正确直接影响到零件加工的质量。
x、y轴方向在走刀路线正确的情况下基本能保证零件成型正确。
若x、y轴方向走刀路线错误,则直接导致工件作废,成为废品。
如果走刀路线偏差较大,不仅会导致零件作废,更会威胁到操作人员的人身安全。
(3)对于二维轮廓加工通常采用以下几个步骤:
(1)从起刀点下刀到下刀点;
(2)沿切向切入工件;
(3)轮廓切削;
(4)刀具向上抬刀,退离工件;
(5)返回起刀点。
2盘类零件加工工艺的确定
2.1工艺分析
图1盘类零件
需要加工的盘类零件如图1所示,零件的材料为45号钢,毛坯选为100mm×80mm×27mm的方形毛坯料。
且底面和四个轮廓面均已加工好,要求在BV75立式加工中心上加工顶面及孔。
(1)加工部位分析
①加工顶面;
②加工Φ32孔;
③加工Φ60沉孔;
④加工4×M8-7H螺纹孔;
⑤加工2×Φ12孔;
⑥加工3×Φ6孔
(2)工步设计
工步号
工步内容
刀具号
刀具规格
1
粗铣顶面
T1
端面铣刀Φ125
2
钻Φ32、Φ12孔中心孔
T2
中心钻Φ2
3
钻Φ32、Φ12孔至Φ11.5
T3
麻花钻Φ11.5
4
扩Φ32孔至Φ30
T4
麻花钻Φ30
5
钻3×Φ6孔至尺寸
T5
麻花钻Φ6
6
粗铣Φ60沉孔
T6
立铣刀Φ18,2刃
7
钻4×M8底孔至Φ6.8
T7
麻花钻Φ6.8
8
镗Φ32孔至Φ31.7
T8
镗刀Φ31.7
9
精铣顶面
T1
端面铣刀Φ125
10
铰Φ12孔至尺寸
T9
铰刀Φ12
11
精镗Φ32孔至尺寸
T10
微调精镗刀Φ32
12
精铣Φ60沉孔至尺寸
T11
立铣刀Φ18,4刃
13
Φ12孔口倒角
T13
倒角刀Φ20
14
3×Φ6、M8孔口倒角
T3
麻花钻Φ11.5
15
攻4×M8螺纹
T12
丝锥M8
2.2工艺卡片
序号
加工工序
刀具
刀具名称
主轴速度
r.p.m
进给速度
mm/min
刀具长度
补偿
刀具半径补偿
刀具补偿值
1
粗铣顶面
T1
端面铣刀Φ125
240
300
H01
实测值
2
钻Φ32、Φ12孔中心孔
T2
中心钻Φ2
1000
100
H02
3
钻Φ32、Φ12孔至Φ11.5
T3
麻花钻Φ11.5
550
110
H03
4
扩Φ32孔至Φ30
T4
麻花钻Φ30
280
85
H04
5
钻3×Φ6孔至尺寸
T5
麻花钻Φ6
1000
220
H05
6
粗铣Φ60沉孔
T6
立铣刀Φ18,2刃
370
1000
H06
D06
30.5
7
钻4×M8底孔至Φ6.8
T7
麻花钻Φ6.8
950
140
H07
8
镗Φ32孔至Φ31.7
T8
镗刀Φ31.7
830
120
H08
9
精铣顶面
T1
端面铣刀Φ125
320
280
H01
10
铰Φ12孔至尺寸
T9
铰刀Φ12
170
42
H09
11
精镗Φ32孔至尺寸
T10
微调精镗刀Φ32
940
75
H10
12
精铣Φ60沉孔至尺寸
T11
立铣刀Φ18,4刃
460
1000
H11
D11
30
13
Φ12孔口倒角
T13
倒角刀Φ20
300
50
H13
14
3×Φ6、M8孔口倒角
T3
麻花钻Φ11.5
300
50
H03
15
攻4×M8螺纹
T12
丝锥M8
100
125
H12
2.3刀具卡片
刀具选择与加工目的
转速r/min
进给量mm/min
背吃刀量mm
端面铣刀Φ125
240
300
中心钻Φ2
1000
100
2
麻花钻Φ11.5
550
110
30
麻花钻Φ30
280
85
35
麻花钻Φ6
1000
220
15
立铣刀Φ18,2刃
370
1000
10
麻花钻Φ6.8
950
140
30
镗刀Φ31.7
830
120
27
铰刀Φ12
170
42
30
微调精镗刀Φ32
940
75
27
立铣刀Φ18,4刃
460
1000
10
倒角刀Φ20
300
50
麻花钻Φ11.5
300
50
丝锥M8
100
125
27
2.4走刀路线
1)粗铣顶面
2)钻Φ32、Φ12孔中心孔
3)钻Φ32、Φ12孔至Φ11.5
4)扩Φ32孔至Φ30
5)钻3×Φ6孔至尺寸
6)粗铣Φ60沉孔
7)钻4×M8底孔至Φ6.8
8)镗Φ32孔至Φ31.7
9)精铣顶面
10)铰Φ12孔至尺寸
11)精镗Φ32孔至尺寸
12)精铣Φ60沉孔至尺寸
13)Φ12孔口倒角
14)3×Φ6、M8孔口倒角
15)攻4×M8螺纹
2.5程序的编制
如图所示为本文数控程序编制的流程图。
加工工艺参数输入部分以人机交互对话方式输入盘类零件铣削加工的有关工艺参数,如刀具半径,起刀点、加工走向,主轴转速、进给速度等。
NC数据处理部分根据几何形状数据及加工工艺参数,对数据文件中的实体(直线、圆弧、列表点)的数据重新排序,列表点先以三次B样条曲线进行拟合,再用双圆弧法进行插补,形成标准的G代码格式。
刀具轨迹仿真部分主要是检验数控程序语法错误,加工时是否有干涉现象或刀具轨迹不合理等,可以减少实际加工中试切次数和防止设备、刀具、工件的损坏。
加工程序编制如下:
O0001;
N3G17G90G40G80G49G21;
G91G28Z0.;
N5M06T01;
N8G90G54G00X120.Y0.;
N9M03S240;
N10G43Z100.H01;
N11Z0.5;
N12G01X-120.F300;
N13G00Z100.M05;
N14G91G28Z0.M05;
/M00;
N16M06T02;
N19G90G54G00X0.Y0.;
N20M03S1000;
N21G43Z100.H02;
N22G99G81Z-5.R5.F100;
N23X-36.Y26.;
N24G98X36.Y-26.;
N25G80G91G28Z0.M05;
/M00;
N27M06T03;
N30G90G54G00X0.Y0.;
N31M03S550;
N32G43Z100.H03;
N33G99G81Z-30.R5.F110;
N34X-36.Y26.;
N35G98X36.Y-26.;
N36G80G91G28Z0.M05;
/M00;
N38M06T04;
N41G90G54G00X0.Y0.;
N42M03S280;
N43G43Z100.H04;
N44G98G81Z-35.R5.0F85;
N45G80G91G28Z0.M05;
/M00;
N47M06T05;
N50G90G54G00X40.Y0.;
N51M03S1000;
N52G43Z100.H05;
N53G99G81Z-15.R5.F220;
N54Y15.;
N55G98Y30.;
N56G80G91G28Z0.M05;
/M00;
N58M06T06;
N61G90G54G00X0.Y0.;
N62M03S370;
N63G43Z5.H06;
N64G01Z-10.F1000;
N65G41X8.Y-15.D06F110;
N66G03X23.Y0.R15.;
N67I-23.;
N68X8.Y15.R15.;
G00G40X0Y0;
N69G01G41X15.Y-15.D06;
N70G03X30.Y0.R15.;
N71I-30.;
N72X15.Y15.R15.;
N73G01X-16.Y0.;
N74Z-4.7F1000;
N75X-61.F110;
N76X-56.5Y-41.586;
N77X-12.213Y-16.017;
N78X15.Y-15.F1000;
N79G03X30.Y0.R15.F110;
N80G01Y51.;
N81X0.;
N82Y16.;
N83G40Y0.F1000;
N84G00Z100.M05;
N85G91G28Z0.;
/M00;
N87M06T07;
N88G90G54G00X23.Y0.;
N91M03S950;
N92G43Z100.H07;
N93G98G81Z-30.R5.F140;
N94X0.Y23.;
N95X-23.Y0.;
N96G98X0.Y-23.;
N97G80G91G28Z0.M05;
/M00;
N9M06T08;
N102G90G54G00X0.Y0.;
N103M03S830;
N100G43Z100.H08;
N101G98G76Z-27.R5.Q0.1F120;
N102G80G91G28Z0.M05;
/M00;
N106M06T01;
N107G90G54G00X120.Y0.;
N108M03S320;
N109G43Z100.H01;
N110Z0;
N111G01X-120.F280;
N112G00Z100.M05;
N113G91G28Z0.;
/M00;
N115M06T09;
N118G90G54G00X-36.Y26.;
N119M03S170;
N120G43Z100.H09;
N121G99G82Z-30.R5.P1000F42;
N122G98X36.Y-26.;
N123G80G91G28Z0.M05;
/M00;
N9M06T10;
N102G90G54G00X0.Y0.;
N103M03S940;
N100G43Z100.H10;
N101G98G76Z-27.R5.Q0.1F75;
N102G80G91G28Z0.M05;
/M00;
N134M06T11;
N137G90G54G00X0.Y0.;
N138M03S460;
N139G43Z5.H11;
N140G01Z-10.F1000;
N141G41X8.Y-15.D11F80;
N142X15.;
N143G03X30.Y0R15.;
N144I-30.;
N145X15.Y-15.R15.;
N146G01X-16.Y0.;
N147Z-5.F1000;
N148X-61.F110;
N149X-56.5Y-41.586.;
N150X-12.213Y-16.017;
N151X15.Y-15.F1000;
N152G03X30.Y0R15.F150;
N153G01Y51.;
N154X0.;
N155Y16.;
N156G40Y0.F1000;
N157G00Z100.M05;
N158G91G28Z0;
/M00;
N185M06T12;
N187G90G54G00X23.Y0.;
N188M03S100;
N190G43Z100.H12;
N192G98G84Z-27.R10.F125;
N193X0.Y23.;
N194X-23.Y0.;
N195X0.Y-23.;
N196G80G91G28Z0.;
N198G28X0.Y0.;
M30;
3误差分析
在数控加工的整个过程中,经常会产生以下几种误差:
(1)近似计算误差:
主要产生在加工列表曲线、曲面轮廓时,采用近似计算法所发生的逼近误差。
(2)插补误差:
这是由于用直线段或圆弧段逼近零件轮廓曲线所产生的误差。
减少插补误差的方法是密化插补点,但这会增加程序段数目,增加计算和编程的工作量。
(3)尺寸圆整误差:
这是将计算尺寸换算成机床的脉冲当量时由于圆整化所产生的误差。
数控机床能反映出的最小位移量是一个脉冲当量,小于一个脉冲当量的数据只能四舍五入,于是就产生了误差。
(4)操作误差
在加工过程中,操作者在操作过程中,工件的安装引起的误差和寻找工件坐标原点过程中容易引起误差。
首先安装过程中,可能会产生工件面与定位面之间靠不紧,解决办法:
在安装过程中四个压板要同时压紧,不能其中某个压紧。
先让四个螺栓稍微拧一下但是不要彻底拧紧,并且用尼龙棒或者木棒在工件上轻轻敲打,使工件底面与定位面之间靠实。
并且拧紧顺序为对角拧紧。
寻找坐标原点过程中,由于使用的设备的精度不同,会带来不同的误差。
解决办法:
使用精度高的仪器,如:
千分表、寻边器等等。
4结论
通过对盘类零件的工艺分析,合理制定了其加工工艺过程,选择了合适的加工刀具及切削参数,合理的编制了加工盘类零件的数控程序,经过独立的分析、计算及改善加工过程,避免了可能产生的各种误差,使用BV75数控加工中心加工出的盘类零件,精度较高,尺寸符合图纸要求。
即提高了产品的加工质量和效率,又降低了工人的劳动强度。
对我个人的数控技术及独立完成加工的技能有了很大的帮助,并且使我更加喜欢数控技术专业。
是我充分看到了自己的不足,是我的技术有了一次跨越性的提高。
参考文献
徐宏海数控加工工艺化学工业出版社,2003,7-5025
徐嘉元、曾家驹机械制造工艺学机械工业出版社,1999,7-111
华茂发数控机床加工工艺械工业出版社,2000,7-111
陈日曜金属切削原理机械工业出版社2002.4
李善树数控机床及其应用机械工业出版社2001.1
延波加工中心的数控编程与操作技术机械工业出版社2001.1